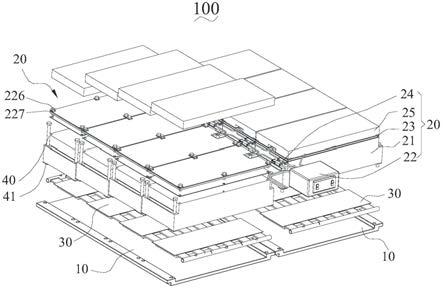
[0001]
本实用新型涉及新能源汽车动力电池测试技术领域,尤其是涉及一种动力电池的热管理测试系统。
背景技术:[0002]
随着生活水平的不断提高,人们对于环保的认识以及意识也越来越强。新能源汽车也得到了大力的发展,而新能源汽车中动力电池是重要部件。动力电池的使用温度直接影响电池的工作性能、寿命及安全性,而动力电池的热管理系统测试实验是对于动力电池性能的重要实验。
[0003]
现有的动力电池的热管理系统都是采用真电池包做实验,需要借助电池模拟器对电池包进行充放电,根据不同充放电来模拟电池的发热,然后同步在电池冷却泵内通入冷却液等不同的冷媒来带走热量。现有的测试实验系统存在诸多不便,例如在新能源汽车的开发前期,往往没有成熟的电池包可供实验,并且动力电池包价格昂贵,拥有电池模拟器设备的测试机构不多,造成测试价格昂贵、测试周期长的问题。
技术实现要素:[0004]
本实用新型的目的在于解决现有的动力电池的热管理测试系统需要使用真电池包测试实验,价格昂贵、用于测试的电池模拟器设备稀缺,测试周期长的缺点,提供一种动力电池的热管理测试系统。
[0005]
本实用新型解决其技术问题采用的技术方案是:一种动力电池的热管理测试系统,包括至少一个支撑壳体、至少一个固定于所述支撑壳体上的假体发热模块,以及设置于所述假体发热模块底部的冷却系统,所述冷却系统通过第一锁紧件固定于所述支撑壳体与所述假体发热模块之间,所述假体发热模块包括与动力电池的导热系数以及热容相同的假体电池、设置于所述假体电池上方的发热部件以及设置于所述假体电池与所述发热部件之间的第一导热垫。
[0006]
进一步地,所述发热部件包括设置于所述假体电池上方的铝板、设置于所述铝板上的加热膜以及与所述加热膜电连接的正极、负极,所述假体电池与其上方的所述发热部件、所述第一导热垫一一对应设置。
[0007]
具体地,相邻的所述发热部件通过快接插头相互串联。
[0008]
具体地,所述发热部件还包括设置于所述加热膜上的温控系统。
[0009]
具体地,所述温控系统包括设置于所述加热膜上的温度感应器以及与所述温度感应器电连接的温控器。
[0010]
具体地,所述假体发热模块还包括设置于所述加热膜顶面的隔热垫。
[0011]
具体地,所述铝板和所述加热膜上均设置有与所述假体电池连接的通孔,所述铝板和所述加热膜通过穿过所述通孔的第二锁紧件锁紧于所述假体电池的顶面。
[0012]
具体地,所述发热部件还包括绝缘垫,所述绝缘垫设置于所述第二锁紧件上,并位
于所述加热膜与所述第二锁紧件之间。
[0013]
进一步地,所述冷却系统包括电池冷却板、设置于所述电池冷却板与所述支撑壳体之间的弹性支撑垫以及设置于所述假体电池与所述电池冷却板之间的第二导热垫。
[0014]
本实用新型所提供的一种动力电池的热管理测试系统的有益效果在于:该热管理测试系统是一个独立完整的测试系统,不需要真电池包也不需要电池模拟器对真电池包进行充放电,通过不同功率的加热膜接口实现电池的不同发热效果,并且输入电压不限,非常方便。该动力电池的热管理测试系统选用了与动力电池的热容以及导热系数相同的假体电池取代了传统测试中使用的真电池包,利用发热部件来模拟真电池包的发热过程取代了传统测试中使用的电池模拟器,可以根据需要改变发热部件中的加热膜的功率,从而模拟不同的假体电池的发热效果;并且还通过第一锁紧件将冷却系统固定于支撑壳体上,保证了该假体电池与冷却系统的接触面积跟真电池包与冷却系统的接触面积一致,保证了假体发热模块与冷却系统中的热传导路径以及热阻与真电池包均是一致的,从而通过本实用新型所提供的动力电池的热管理测试系统来验证电池冷却板的开发设计,该假体发热模块可以接入不同电压的直流或者交流电,无需真电池包即可完成测试,取代了传统的测试所需的铜排、线束、pdu、bms等硬件,也无需使用bms软件即可进行测试,结构简单,测试系统中的假体电池的成本仅是真电池包的5%,可以在新能源汽车的开发前期进行测试实验,无需等到真电池包数据冻结、电池其他硬件、软件到位后才进行测试实验,可以有效地节约新能源汽车的动力电池的研发时间和研发成本。
附图说明
[0015]
图1是本实用新型提供的一种动力电池的热管理测试系统的立体分解结构示意图;
[0016]
图2是本实用新型提供的一种动力电池的热管理测试系统的假体发热模块中假体电池的立体结构示意图;
[0017]
图3是本实用新型提供的一种动力电池的热管理测试系统的假体发热模块中发热部件的立体结构示意图;
[0018]
图4是本实用新型提供的一种动力电池的热管理测试系统的冷却系统的立体结构示意图。
[0019]
图中:100-热管理测试系统、10-支撑壳体、20-假体发热模块、21-假体电池、22-发热部件、221-铝板、222-加热膜、2221-通孔、223-正极、2224-负极、225-温控系统、2251-温度传感器、2252-温控器、226-第二锁紧件、227-绝缘垫、24-快接插头、25-隔热垫、30-冷却系统、31-电池冷却板、32-弹性支撑、33-第二导热垫、40-第一锁紧件、41-隔热垫。
具体实施方式
[0020]
为了使本实用新型的目的、技术方案及优点更加清楚明白,以下结合附图及实施例,对本实用新型进行进一步详细说明。应当理解,此处所描述的具体实施例仅仅用以解释本实用新型,并不用于限定本实用新型。
[0021]
参见图1-图4,为本实用新型所提供的一种动力电池的热管理测试系统100。该测试系统100利用假体电池21来模拟动力电池的实际使用过程中的发热情况,并通过调试测
试系统100中的冷却系统30,使得其能够满足动力电池的散热需求,达到在新能源汽车中的使用需求。该测试系统100主要用于进行动力电池热管理系统设计前期的测试验证,基于不同电池发热量进行电池冷却板的设计开发验证,对测试系统100中的冷却系统30内通入冷却液或冷媒带走热量,从而验证冷却系统对假体电池21的降温性能和温度均匀性。
[0022]
参见图1,为本实用新型所提供的一种动力电池的热管理测试系统100的立体分解结构示意图。该热管理测试系统100包括至少一个支撑壳体10、至少一个固定于支撑壳体10上的假体发热模块20以及设置于假体发热模块20底部的冷却系统30。该支撑壳体10的结构不限,只要可容纳冷却系统30以及固定假体发热模块20即可。在本实施例中,热管理测试系统100中具有两个支撑壳体10和两套冷却系统30,每套冷却系统30可以覆盖一个支撑壳体10上的所有假体发热模块20,从而通过冷却系统30带走假体发热模块20所传导的热量。该假体发热模块20的数量与需要测试的动力电池中电池模组的数量对应。在本实施例中,每个支撑壳体10内均设置有四个假体发热模块20。本实用新型所提供的热管理测试系统100中,该假体发热模块20可以取代传统的测试实验中所需的真电池包以及为真电池包进行充放电的电池模拟设备。通过该假体发热模块20不仅可以模拟真电池包的结构和导热性能,还可以模拟真电池包的自发热过程和通过冷却系统30的散热过程。因此,在动力电池的研发前期即可运用该假体发热模块20开展测试实验,无需等到真电池包的数据冻结、电池其他硬件、软件都到位之后才进行热管理开发设计,可以节约动力电池的研发时间和研发成本。
[0023]
具体地,如图1所示,本实用新型所提供的假体发热模块20包括与动力电池的导热系数以及热容相同的假体电池21、设置于假体电池21上方的发热部件22以及设置于假体电池21与发热部件22之间的第一导热垫23。该假体电池21根据实际动力电池的热容进行等效设计,且该假体电池21与冷却系统30的热阻以及传热路径均与真电池包一致。该假体电池21与其上方的发热部件22及第一导热垫23一一对应设置。在本实施例中,一个冷却系统30上方设置有四个假体电池21,对应的,就具有四个第一导热垫23设置于发热部件22和假体电池21之间,每个假体电池21上均设置有与其匹配的一个发热部件22为其提供所需的热量。
[0024]
进一步地,为了保证该假体发热模块20与冷却系统30之间的接触面积以及导热垫的导热性能能够与真电池包一致,需要通过第一锁紧件40将冷却系统30固定于支撑壳体10与假体发热模块20之间。如图2所示,该假体电池21包括与动力电池体积相同的主体部分以及设置于主体部分两侧用于与支撑壳体10连接的连接部分,在连接部分上均匀分布有多个可供第一锁紧件40穿设的通孔。该第一锁紧件40穿过该通孔将假体电池21锁紧于支撑壳体10上,并且将冷却系统30压紧于假体电池21与支撑壳体10之间。
[0025]
具体地,如图2所示,为了阻隔假体电池21上的热量传递至支撑壳体10上,保证该假体电池21上的热量全部传导至冷却系统30中,该热管理测试系统100还包括设置于第一锁紧件40上,位于假体电池21与支撑壳体10之间的隔热垫25。通过该隔热垫25阻隔了假体电池21与支撑壳体10之间的热量传递。在本实施例总,该第一锁紧件40为螺栓。
[0026]
进一步地,如图4所示,为本实用新型所提供的一种动力电池的热管理测试系统100中的冷却系统30的立体结构示意图。该冷却系统30包括电池冷却板31、设置于电池冷却板31与支撑壳体10之间的弹性支撑垫32以及设置于假体电池21与电池冷却板31之间的第
二导热垫33。该电池冷却板31的结构不限,口琴管形式或者冲压板形式均可,可以为该电池冷却板31内通入冷却液或者冷媒把冷却系统30上方所传递来的热量带走。该弹性支撑垫32的结构也不限,发泡硅橡胶或者板簧均可。通过调节第一锁紧件40,可以调节该弹性支撑垫32的压缩量,保证该弹性支撑垫32的压缩量与真电池包设置于冷却系统30上是一致的。该第二导热垫33与假体发热模块20中的第一导热垫23的结构和材质均一致,一般为长方形硅胶垫。该第二导热垫33可根据该第一锁紧件40调节压缩量,同时达到传递热量的目的。
[0027]
进一步地,如图3所示,为本实用新型所提供的一种动力电池的热管理测试系统100中发热部件22的立体结构示意图。该发热部件22包括设置于假体电池21上方的铝板221、设置于铝板221上的加热膜222以及与加热膜222电连接的正极223、负极224。通过该铝板221支撑加热膜222,通过正极223和负极224位加热膜222供电,从而实现加热膜222的通电发热。该铝板221上的加热膜222可以根据不同动力电池的发热需求而选用不同的功率,例如1500w、2000w不等。不同功率的加热膜222可以模拟不同动力电池的发热效果。在本实施例中,该加热膜222可以是pi或pet加热膜,尺寸根据电池加热膜设计。并且该加热膜222可以连接不同的电压,家用220v交流电压、商用380v交流电压或者其他直流电压,使用方便,不需要使用电池模拟器即可实现假体电池21的发热效果。因此,该发热部件22可以取代传统测试系统中的电池模拟器实现假体电池21的发热过程。
[0028]
具体地,相邻的假体发热模块20中的发热部件22通过快接插头24相互串联。在本实施例中,同一个支撑壳体10上设置有四个假体发热模块20,其中每个假体发热模块20中的发热部件22相互串联,在串联时使用快接插头24进行相互之间的连接。通过设置快接插头24,可以方便该不同功率的加热膜222的快速拆装。
[0029]
具体地,如图3所示,在本实施例中,该发热部件22还包括设置于加热膜222上的温控系统225。该温控系统225根据不同温度阈值实现整个发热部件22电路的通断,通过电路的通断来保护加热膜222不会过热,防止测试过程中出现安全事故。该温控系统225包括设置于加热膜222上的温度感应器2251以及与温度感应器2251电连接的温控器2252。该温度感应器2251可灵活布置在加热膜222的任意位置上,用于探测加热膜222的最高温度。该温控器2252通过设置预定的极限温度,当温度感应器2251实时监测的温度达到该极限温度时,通过温控器2252实现电路断开,防止测试过程中出现安全事故。
[0030]
具体地,如图1所示,本实用新型所提供的假体发热模块20还包括设置于加热膜222顶面的隔热垫25。该隔热垫25用于阻挡发热部件22中加热膜222工作时的热辐射,使得加热膜222上所产生的热量往假体电池21上传递,确保整个测试系统100中热传递的路径与真电池包一致。
[0031]
具体地,如图1和图3所示,在发热部件22中,铝板221和加热膜222上均设置有与假体电池21连接的通孔2221,第二锁紧件226穿过通孔2221将铝板221和加热膜222锁紧于假体电池21的顶面。每个铝板221和加热膜222上所设置的通孔的位置与数量均与假体电池21上的连接孔的位置一致。通过第二锁紧件226可以将发热部件22固定至假体电池21上,发热部件22通电发热后,将热量传递至假体电池21上模拟动力电池的充放电发热过程。为了防止该第二锁紧件226直接与加热膜222接触发生导电的问题,该发热部件22还包括设置于第二锁紧件226上,位于加热膜222与第二锁紧件226之间的绝缘垫227。在本实施例中,该第二锁紧件226为螺栓。
[0032]
本实用新型所提供的一种动力电池的热管理测试系统100中,通过对假体发热模块20进行通电,使得假体发热模块20中的加热膜222发热并且将热量通过假体电池21传递至冷却系统30中,再通过注入冷却系统30的冷冻液或者冷媒将热量带走。该发热部件22中的加热膜222发热,将热量传递至铝板221上,并通过铝板221下方的第一导热垫23将热量传递至假体电池21上,通过假体电池21再传递至冷却系统30。该冷却系统30通过第二导热垫33将热量传递至电池冷却板31上散热。通过假体发热模块20和冷却系统30实现热量的传递过程,从而验证假体电池21的温降和温度均匀性。
[0033]
本实用新型所提供的一种动力电池的热管理测试系统100是一个独立完整的测试系统,不需要真电池包也不需要电池模拟器对真电池包进行充放电,通过不同功率的加热膜222接口模拟电池的不同发热效果,并且输入电压不限,非常方便。该动力电池的热管理测试系统100选用了与动力电池的热容以及导热系数相同的假体电池21取代了传统测试中使用的真电池包,利用发热部件22来模拟真电池包的发热过程,取代了传统测试中使用的电池模拟器,可以根据需要改变发热部件22中加热膜222的功率,从而模拟不同的假体电池21的发热效果;并且还通过第一锁紧件40将冷却系统30固定于支撑壳体10上,保证了该假体电池21与冷却系统30的接触面积跟真电池包与冷却系统30的接触面积一致,保证了假体发热模块20与冷却系统30中的热传导路径以及热阻与真电池包均是一致的,从而通过本实用新型所提供的动力电池的热管理测试系统100来验证电池冷却板31的开发设计,该假体发热模块20可以接入不同电压的直流或者交流电,无需真电池包即可完成测试,取代了传统的测试所需的铜排、线束、pdu、bms等硬件,无需使用bms软件即可进行测试,结构简单,测试系统中的假体电池的成本仅是真电池包的5%。
[0034]
以上仅为本实用新型的较佳实施例而已,并不用以限制本实用新型,凡在本实用新型的精神和原则之内所作的任何修改、等同替换和改进等,均应包含在本实用新型的保护范围之内。