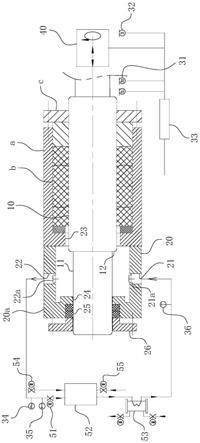
1.本发明涉及柱塞及其往复密封使用寿命检测技术领域,具体涉及一种阶梯式柱塞往复密封试验装置及阶梯式柱塞设计方法。
背景技术:2.由于寿命试验成本、验证方法等各种因素限制,绝大多数情况下尚无有效获得柱塞及其往复密封使用寿命的方法与手段。目前,柱塞及其往复密封副的寿命数据多数通过现场测试法,或实物样机测试法等方法得到。
3.应用现场测试法全程借助于往复泵应用现场,利用泵使用现场具备的生产装置和便利条件,在流程生产用泵过程中,对泵配柱塞及其往复密封的寿命及工作状态进行跟踪、记录并最终获得它们寿命测试数据。然而,在流程应用现场,前提和目标是保障安全生产,柱塞及其往复密封寿命测试只是附加任务。在实践中,生产工艺总是不停在变化,决定泵的运行工况(流量、压力、转速、温度、输送介质)也都在处于变化之中,导致测试过程的边界条件常偏离预设工况但又不能调整,测试结果就不能客观反映特定工况的实际情况。甚至由于条件的制约,往往这种变化还缺乏有效的统计记录,分析数据时,缺乏必要的实际运行工况和运行边界条件作为变化分析基础。同时,由于受制于现场操作者专业能力、专业技术人员难以系统参与、现场生产型仪器设备精度不够等诸多因素的影响,增加了这种测试数据的不确定性。以至于很多时候,相同柱塞,不同渠道得到数据差别很大,甚至有成倍的偏差。所以,许多通过这种方式获得的寿命数据,由于缺乏许多准确的工况参数数据支撑,仅能作为寿命数据定性参考,不能作为精确定量的寿命指标依据。此外,生产线意外停机检修会带来较大的经济损失。未经试验验证直接用于实际生产进行试验验证,很容易造成意外故障停机。因此多数情况下,未经试验验证的柱塞及其往复密封是不允许直接在生产现场进行试验测试的。
4.实物样机测试法是将装配有被试柱塞及其往复密封的实物样机安装在专用试验台架系统上,在设计工况下,对泵进行连续运行试验,测试泵配柱塞及其往复密封的实际运行寿命。然而,实物样机测试法的劣势也极其明显:即高耗低效,对于大功率机组这种缺陷愈加明显。高耗方面,实物样机测试法需要将柱塞及其往复密封装配在实物样泵中,在泵实际工况下连续运行,直至柱塞及其往复密封损坏为止。以中等功率的315kw柱塞泵为例,如果柱塞寿命按时间2000h、电费率按0.75元/kw.h估算,试验电费约为:315*2000*0.75/10000=47.25万元。以上估算仅是对1种柱塞、1种工况,如果柱塞需要进行多种工况的对比测试,那试验费用无疑将是巨大的支出。低效是指:实物样机测试法是柱塞与整泵一起试验,根据往复泵的结构和工作原理,泵的转速与泵的流量和功率是1次方关系。如果提高转速,势必提高泵的流量和驱动功率,受制于功率及柱塞强度影响这是不可能试验的,因此寿命试验只能是原速或降速试验。此外,由工程经验可知,往复泵柱塞寿命一般在1~6个月左右,大泵柱塞寿命相对短一点。如果大功率、原速试验,多数企业的测试能力仅能保证一台大泵试验,将导致大量的泵正常试验无法试验。因此实物样机测试法不仅试验数据获取周
期长,企业也无法承担;同时,柱塞生产企业也不具备稍大功率的测试条件。
技术实现要素:5.本发明的其中一个目的是克服上述现有技术的不足,提供一种结构合理而实用的阶梯式柱塞往复密封试验装置,本装置具备节能高效的工作特点,既能体现与往复泵实际工况相一致的柱塞与往复密封之间的摩擦磨损状态,同时又不需要泵在实际工况即大功率工况下长期运行,从而在保证测试准确、可靠、快速、智能进行的前提下,大幅降低试验成本。本发明的另一个目的是提供一种基于上述阶梯式柱塞往复密封试验装置的柱塞设计方法,以确保装置快速高效运行。
6.为实现上述目的,本发明采用了以下技术方案:
7.一种阶梯式柱塞往复密封试验装置,包括填料函以及配合于填料函筒腔内的柱塞,其特征在于:填料函的一端布置液缸体而另一端布置可使柱塞产生轴向往复动作的动力源,所述液缸体密封面状的贴合于填料函端面处,液缸体的缸腔构成可供介质暂存的容纳腔;所述柱塞前端设置附加柱塞杆使整体外形呈阶梯轴状,液缸体的靠近填料函的一侧缸壁贯穿布置可供柱塞穿行的配合孔,配合孔孔径小于或等于填料函的密封筒径,液缸体的远离填料函的一侧缸壁轴向贯穿布置同轴孔,附加柱塞杆与所述同轴孔间构成孔轴插接式动密封关系,此时柱塞的位于容纳腔区域的轴肩构成用于抽拉及泵压容纳腔内介质的所述工作端;
8.本装置还包括用于监控柱塞往复运动次数的冲次信号传感器和/或监控动力源转轴转速的转速信号传感器;所述冲次信号传感器和/或转速信号传感器的信号输出端连通采集与控制模块的信号输入端。
9.优选的,所述液缸体包括外形呈桶体状的主缸,所述同轴孔贯穿布置在主缸的桶底处,主缸桶口与填料函的函底间构成面贴合的密封配合。
10.优选的,同轴孔外形呈二段式阶梯孔状,且位于主缸桶底处的同轴孔的孔端孔径大于位于容纳腔处同轴孔的孔端孔径;同轴孔的大孔径段处同轴布置有填料环,并以副填料压盖压紧填料环于大孔径段内,填料环的内环面与附加柱塞杆外壁间构成孔轴插接式动密封关系。
11.优选的,液缸体外壁处开设有连通容纳腔的带有进口阀的介质进口及带有出口阀的介质出口,介质经由介质进口进入并由介质出口流出;本装置还包括介质循环组件,介质循环组件的循环管路分别连通介质进口与介质出口;介质经由介质进口进入容纳腔后再由介质出口流出,并在柱塞的轴肩的泵压作用下依序经过压力信号传感器、第二温度信号传感器、压力调节阀后进入储液罐,储液罐内的介质则经由冷却模组及第一温度信号传感器后流入介质进口;压力信号传感器、第二温度信号传感器及第一温度信号传感器的信号输出端同样连通采集与控制模块的信号输入端。
12.优选的,介质出口与储液罐进口之间还布置有并联分支管路,并联分支管路上布置有起平衡水压作用的旁通阀。
13.优选的,储液罐上布置补液管,补液管上布置补液阀。
14.优选的,所述冷却模组为水冷换热器。
15.优选的,一种应用所述阶梯式柱塞往复密封试验装置的阶梯式柱塞设计方法,其
特征在于:
16.根据以下公式获得二段式阶梯轴状的柱塞的附加柱塞杆长度l1与直径d1:
17.l1=(1.5~2)s
18.d1=(0.9~0.95)d219.式中,s为柱塞行程,d2为原柱塞直径。
20.本发明的有益效果在于:
21.1)、由于填料函处填料密封的磨损是柱塞的直接的往复运动造成,而在正常状态下运行时,柱塞承担着泵送介质的任务,因此需要与之相匹配的功率驱动其运动。故倘若采取某种形式的柱塞,使其在对少量介质做功的情况下还能还原柱塞在实际运行中与函体表面的运动状态,则可以快速高效的对柱塞寿命进行检测。
22.基于上述观点,本发明另辟蹊径地设计了可轴向贯通式的阶梯型的附加柱塞杆与柱塞配合结构,通过在柱塞顶端布置附加柱塞杆进而使得整个轴体呈现阶梯型,使得柱塞仅依靠部分横截面也即轴肩对介质做功;既能完全模拟柱塞与填料密封作往复运动时的受力和工作状态,又能保证柱塞在仅受很小轴向力的作用下以远小于正常柱塞的驱动功率下完成其检测。该结构搭配全自动测试系统、关键参数自纠错系统来进行柱塞及其往复密封测试,既保证了柱塞及其往复密封测试的准确性同时也具备了高效、快速及智能化的特点。
23.介质循环组件的布置,目的则在于提供介质以往复循环的载体,以确保介质的正常循环使用。更具体而言,一方面,通过本发明的柱塞处轴肩来对少量介质做功,完全的模拟了柱塞与填料函之间的相对运动情形,相较于原始柱塞形式其试验所需驱动功率得到极大的减小,同时节约了试验成本,为企业实现了节能降负的目标;另一方面,由于试验所用介质的需要量的减少,对一些特殊、稀有、贵重试验介质来说也是一种极大的节约。此外的,由于柱塞仅对少量介质做功,因此其泵送流量和轴向载荷也随之减小,这使得柱塞的加速运动变的可行,在一定基础上可以通过加快泵转速快速获得柱塞的寿命数据,缩短试验周期,并有效的节省时间成本,一举多得。
24.本发明已在全自动测试系统、关键参数自纠错系统的辅助下进行了柱塞寿命的现场测试;实践证明,本发明具备节能高效的工作特点,可保证寿命测试的准确、可靠、快速及自动化进行,尤其适合大功率机组内的柱塞及其往复密封使用寿命检测所使用。
25.2)、对于液缸体而言,其主体结构由主缸构成,通过将主缸的桶口直接通过螺纹配合等压紧密封在填料函相应端面处,从而既保证了介质能在柱塞处轴肩的泵压作用下,经由容纳腔及介质进口和介质出口来产生正常循环;同时,容纳腔内介质也能经由配合孔而渗入柱塞与填料函之间的配合间隙处,从而模拟现实状况下的介质对密封副的润滑现象。而对于同轴孔而言,其设计功能在于始终确保附加柱塞杆与自身的密封配合性,以避免介质沿同轴孔产生外泄状况。
附图说明
26.图1为本发明的工作状态剖视图。
27.本发明各标号与部件名称的实际对应关系如下:
28.a
‑
填料函 b
‑
密封填料 c
‑
填料压盖
29.10
‑
柱塞 11
‑
附加柱塞杆 12
‑
轴肩
30.20
‑
液缸体 20a
‑
主缸
31.21
‑
介质进口 21a
‑
进口阀 22
‑
介质出口 22a
‑
出口阀
32.23
‑
配合孔 24
‑
同轴孔 25
‑
填料环 26
‑
副填料压盖
33.31
‑
冲次信号传感器 32
‑
转速信号传感器 33
‑
采集与控制模块
34.34
‑
压力信号传感器 35
‑
第二温度信号传感器
35.36
‑
第一温度信号传感器 40
‑
动力源
36.51
‑
压力调节阀 52
‑
储液罐 53
‑
冷却模组
37.54
‑
旁通阀 55
‑
补液阀
具体实施方式
38.为便于理解,此处对本发明的具体结构及工作方式作以下进一步描述:
39.本发明的具体实施例结构参照图1所示,主要结构包括三大部分,也即阶梯型柱塞运动组件、介质循环组件以及采集控制组件。其中:
40.一、阶梯型柱塞运动组件
41.本发明的一个主要发明点是创新性的设计了阶梯型轴向贯通减小容积变化式柱塞组合构造及其往复密封机构。具体而言,在被测试的柱塞10的前端部分设置作为阶梯段的附加柱塞杆11,形成阶梯型结构。被测试的柱塞10的尺寸参数按照柱塞实际大小确定,整体布置主副密封机构。主密封机构即是需要试验的实际密封机构,由填料函a、密封填料组件也即密封填料b与支撑环及填料压盖c等组成,其结构、尺寸等完全按实际被测试泵的密封结构尺寸,确保柱塞10与密封填料b之间的运动形式与实际相符;副密封机构由填料压盖26与液缸体20组成,主要用来密封柱塞10的附加柱塞杆11,确保该部位无介质泄漏即可。
42.该结构中,由于轴向是一个闭合贯通式容腔且附加柱塞杆11的长度大于液缸体的长度,使得阶梯段的附加柱塞杆11无法对介质做功。相较于传统泵腔,柱塞10真正对介质做功的部分只有其环状部位,大大减小了泵送流量,从而降低泵配功率与柱塞轴向力,达到在较小功率下对柱塞及密封进行检测的目的。
43.柱塞10的驱动端采用通用的往复泵动力端形式即曲柄连杆结构,将如电动机或柴油机等的动力源40输出的旋转运动转换为柱塞10的往复运动,驱动端转速可调。
44.由于驱动力只要提供克服柱塞10和附加柱塞杆11运动与各自密封填料的摩擦力以及对少量介质做功的功率即可,所以驱动端动力通常可以在一定范围内用于多种型号柱塞及其往复密封的试验驱动。同时,由于驱动力小,只要适当提高驱动功率就可实现柱塞高速往复运动,可达实际运行泵速的5~10倍,可显著提高试验效率。
45.由上可知,本发明的核心点就是在柱塞10前端设置附加柱塞杆11使整体外形成阶梯型,从而使得仅利用柱塞10的轴肩12部位来形成泵压面,来减小其对介质的做功面积,以达到降低功率与轴向力的作用,从而在较小的功率下模拟柱塞10在密封填料b表面的运动情况。因此,柱塞10前端的附加柱塞杆11参数设计就显得尤为重要。
46.以l代表整根柱塞10的长度;l1代表附加柱塞杆11长度;d2代表原柱塞10直径,也即图1中的柱塞10的大轴径段直径;d1代表附加柱塞杆11直径。上述参数中需要确定的是柱塞10前端的附加柱塞杆11长度l1与直径d1,根据以下公式获得二段式阶梯轴状的柱塞10及附加柱塞杆11长度l1与直径d1:
47.l1=(1.5~2)s
48.d1=(0.9~0.95)d249.式中,s为柱塞行程,d2为原柱塞直径,也即传统所用柱塞的直径。
50.参数的取值可考虑对于小功率泵取小值,大功率泵取大值。
51.此时,原柱塞泵送理论流量q和本发明的柱塞10的泵送流量q1分别为:
[0052][0053][0054]
现假设对某一柱塞,取d1=0.9d2,由此可以发现阶梯式柱塞组合结构的泵送流量仅为原柱塞泵送流量的19%。相应地,泵配功率与轴向柱塞力也仅为原泵的19%,大大降低试验所需功率与驱动端强度要求。
[0055]
二、介质循环组件
[0056]
介质循环组件主要由循环管路、压力调节阀51、储液罐52、冷却模组53也即水冷换热器等部件组成。由于柱塞10在容纳腔内的往复运动使得腔体内的容积发生变化。当容纳腔内容积逐渐变大时,介质进口21处进口阀21a开启,介质出口22处出口阀22a关闭,从而使得介质通过介质进口21被吸入容纳腔内;反之,当容纳腔内容积逐渐变小时,介质进口21处进口阀21a关闭,介质出口22处出口阀22a开启,从而使得介质通过介质出口22排出容纳腔。通过压力调节阀51可调节液缸体20也即泵的出口压力,使其出口背压符合实际工况下的压力。液缸体20的进出口管路均连接在储液罐52中,使得介质可以被循环使用。由于柱塞10在运动过程中会产生大量的热能使得介质温度升高,因此需要在储液罐52中接入冷却模组53,也即如图1所示的水冷换热器,对介质进行冷却,以确保介质的物态属性与实际情况相符,从而降低试验误差。
[0057]
介质循环组件是本发明的通用系统,一般设计一到两组基本可以满足所有试验需要。
[0058]
三、采集与控制组件
[0059]
采集与控制组件是本发明的电气与自动控制部分,主要由数据采集子系统和电力拖动及自动控制子系统两部分组成。
[0060]
数据采集子系统主要包括压力信号传感器34、第一温度信号传感器36、第二温度信号传感器35、冲次信号传感器31、转速信号传感器32等多个传感器和采集与控制模块33等构成。电力拖动及自动控制子系统主要有变频调节器、电控柜、电气元件执行器等组成。
[0061]
采集与控制组件是通用系统,一套系统通过简单修正某些设计参数,基本也可以满足所有试验需要。
[0062]
实际工作时,系统压力、介质温度、冲次等试验数据由采集与控制模块33来采集并控制;系统压力由压力信号传感器34采集,并通过控制压力调节阀51来确保压力始终能调整到试验需要压力。由于泵在运行中可能存在压力波动的情况,因此规定一个压力值偏差,当采集压力值大于该偏差值时,报警停车分析差值原因,解决问题后继续试验。
[0063]
试验介质温度由第一温度信号传感器36和第二温度信号传感器35测得,第一温度信号传感器36永远小于第二温度信号传感器35。两者温度都不能高于柱塞10的试验要求温
度,当两者温度高于要求温度时,通过水冷换热器来调节保证第一温度信号传感器36和第二温度信号传感器35的平均值满足试验介质要求温度。
[0064]
通过两组冲次信号传感器31来记录柱塞10的往复运行次数;而柱塞10往复运行次数是柱塞及其往复密封寿命的最直接体现。一般情况下,通过时间来表征零件寿命,时间即是柱塞在填料表面往复次数的累积。在柱塞与填料密封副未失效前,柱塞在填料表面往复次数越多,则柱塞及密封使用寿命越长,因此测得柱塞及其往复密封失效前往复次数即可获得其寿命数据。
[0065]
本发明通过冲次信号来记录柱塞10的往复次数并累计,此信号非常关键,不容出错,本发明采用同源异源双比对方法进行自校纠错:柱塞10的起始位置安装两个同源的冲次信号传感器31,测量记录柱塞10往复次数作为试验有效冲次数并自检;在与柱塞10连接无减速低速旋转处安装转速信号传感器32,转速信号传感器32可转换成冲次信号,与冲次信号传感器31异源,将其记录并与冲次信号传感器31的记录进行对比,以相互校验。
[0066]
动力源40采用变频驱动方式,转速可调,柱塞10每单位时间内的往复次数亦随之变化。由于本发明的二段阶梯式的柱塞10搭配附加柱塞杆11的组合结构设计方式,使得本发明的柱塞10所需要的功率及轴向力较原始柱塞大大降低,因此可以在原始柱塞寿命的转速基础上相应提高泵的转速,实际运行可达原泵速的5~10倍,从而大大减少试验所需时间。甚至在必要时,可同时对两个相同的柱塞
‑
填料结构进行相同或不同对比试验,以增加试验的透明度,降低试验的偶然性。
[0067]
综上可知,本发明相对于传统的填料函a寿命试验方式,存在以下优点:
[0068]
1)节能降耗
[0069]
本发明采用阶梯型柱塞组合结构形式,在完全模拟柱塞及其往复密封实际工作状态情况下,介质排量大大减少,驱动柱塞运动的功率与柱塞所受轴向力大幅下降,极大降低了试验所需和介质用量。
[0070]
2)试验周期短
[0071]
本发明使得柱塞运动所需要的功率及轴向力大大降低,因此能大幅提高试验转速,极大缩短柱塞及其往复密封寿命试验并快速获得寿命数据,缩短试验周期,节省时间成本。
[0072]
3)智能化程度高
[0073]
本发明试验边界条件通过数据控制系统自动控制,试验记录自动记录、自动控制,消除了人为因素干扰,符合企业面向智能化转型需求。
[0074]
4)精确度高
[0075]
本发明试验系统中,关键数据如压力、往复次数等都采用多参数相互校验,保证试验边界始终处于设计状态,确保试验条件的一致性和试验数据的准确,提高了试验准确性。
[0076]
本发明结构设计便于同时无差别多柱塞试验,无差别同时获得多样本数据,便于对试验结果准确性进行进一步甄别,提高试验准确性的实际效果。
[0077]
由于成本低,实现容易,更便于广泛开展针对性、多样性试验,可以针对诸多影响柱塞及其往复密封因素进行针对性试验,使得不同种柱塞数据更为精准。
[0078]
5)实用性超强,便于实现推广
[0079]
综上,本发明的柱塞及往复密封试验系统,便于更低成本、低能耗、更快速、更广泛
的试验开展,便于柱塞与密封生产企业、整泵生产企业装备该系统,为柱塞及其往复密封试验大规模开展带来可能,为柱塞及其往复密封科研带来方便,可快速、大幅提高柱塞及其往复密封的可靠性,进而提高整体设备使用寿命。
[0080]
实践可知,本发明节能80%左右,同时能将原试验周期缩短至原周期的20%以内,成效极为显著。
[0081]
当然,以上为本发明的其中一种具体的实施例。实际操作时,对作为动力源的变频电机的动力结构进行常规性替换,如将齿轮齿条机构来取代曲柄摇杆结构,使用柱塞缸来取代变频电机等;以及对主缸的外形作适应性变化,对常用电学件作常规性的替换,甚至将本发明的方案常规性的辐射至相邻的缸体寿命测试领域等等,这类在已知本发明的技术方案的基础上所作的常规变化,均应当作为等同或相似设计而落入本发明的保护范围内。