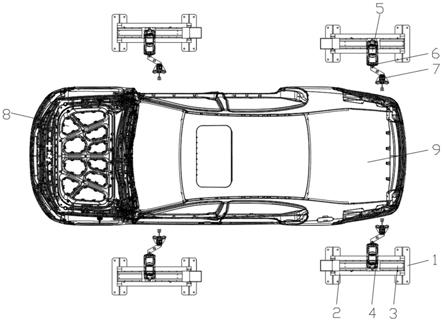
1.本发明涉及汽车制造表面质量检测装置技术领域,具体领域为一种车身表面间隙断差自动测量设备。
背景技术:2.汽车的装配是汽车产品制造过程中最重要工艺环节之一,是把经检验合格的数以百计、或数以千计的各种零部件按着一定的技术要求组装成整车及发动机、变速器等总成的工艺过程,在对汽车装配完成后,需要对装配后的整车进行各组成部件间间隙断差的测量和检验工作,通常总装车间完成整车装配后采用人工使用塞尺、游标卡尺及断差尺对车身各零部件总成间的间隙面差进行测量和检验,这样容易因为人工测量的主观性和人工测量较大的测量误差对车身表面间隙断差检测的结果产生较大的影响,导致检测结果可能无法真实有效的反映车身真实的情况,不利于整车质量保障和监督,且培养一名经验丰富、技术过硬的车身表面间隙断差检测师需要多年的实践和积累,需要投入大量的资源和费用,不利于降低人工成本,提高检测效率,且目前常见的表面间隙断差自动检测设备采用工业机器人带检测测头进行测量,需要设置安全围栏,无法实现人机协同作业及本工位本地人工复检等任务,不利于节省操作工位,浪费工时。
技术实现要素:3.本发明的目的在于提供一种车身表面间隙断差自动测量设备,以解决上述背景技术中提出的通常总装车间完成整车装配后采用人工使用塞尺、游标卡尺及断差尺对车身各零部件总成间的间隙面差进行测量和检验,这样容易因为人工测量的主观性和人工测量较大的测量误差对车身表面间隙断差检测的结果产生较大的影响,导致检测结果可能无法真实有效的反映车身真实的情况,不利于整车质量保障和监督,且培养一名经验丰富、技术过硬的车身表面间隙断差检测师需要多年的实践和积累,需要投入大量的资源和费用,不利于降低人工成本,提高检测效率,且目前常见的表面间隙断差自动检测设备采用工业机器人带检测测头进行测量,需要设置安全围栏,无法实现人机协同作业及本工位本地人工复检等任务,不利于节省操作工位,浪费工时的问题。
4.为实现上述目的,本发明提供如下技术方案:一种车身表面间隙断差自动测量设备,包括机器人底座,所述机器人底座的上端设有机器人控制柜存放箱,所述机器人控制柜存放箱的上表面中间位置左右方向设有滑动机构,所述滑动机构的上端设有机器人固定机构,所述机器人固定机构的上表面通过螺栓连接有机器人,所述机器人的工作端通过螺栓设有测头固定机构,所述测头固定机构的内部通过螺栓连接有缝隙尺寸检测头,四组所述缝隙尺寸检测头之间设有输送机构,所述输送结构的内部设有车身本体。
5.优选的,所述机器人底座包括地面固定板,所述地面固定板的四角处通过化学锚栓固定在地面上,所述地面固定板的上表面中间位置前后方向设有竖直支撑板,所述竖直支撑板的前后表面下端与所述地面固定板之间焊接有倾斜加固板,所述竖直支撑板为一整
块上端拐角处设有直角倒角的长方形不锈钢板,所述竖直支撑板的左右侧表面上下端贯穿开设有一号窗口及二号窗口,所述一号窗口的内部卡接有机器人控制柜存放箱,两块所述竖直支撑板之间且在所述一号窗口及所述二号窗口之间焊接有支撑板。
6.优选的,所述滑动机构包括固定板,所述固定板通过螺栓与所述机器人控制柜存放箱的上表面固定连接,所述固定板的上端通过螺栓固定连接有滑道,所述滑道的右端且在所述机器人控制柜存放箱的右端外部设有控制箱,所述控制箱的左端且在所述滑道的上端设有线缆收集盒,所述滑道的左端设有限位板,所述滑道的内部后端设有齿条,所述滑道与所述机器人固定机构滑动连接。
7.优选的,所述机器人固定机构包括滑块,所述滑块与所述滑道滑动连接,所述滑块的内部通过螺栓连接有一号伺服电机,所述一号伺服电机的输出端贯穿所述滑块的下壁伸入到所述滑道的内部,所述一号伺服电机的输出端通过连接键连接有齿轮,所述齿轮与所述齿条啮合,所述滑块的上表面开设有供所述机器人连接的螺纹孔。
8.优选的,所述机器人包括机器人连接座,所述连接座通过螺栓与所述滑块的上表面连接,所述机器人连接座的上端通过转轴转动连接有一号动力关节,所述一号动力关节的左端通过转轴转动连接有二号关节,所述二号关节的上端设有一号臂的下端,所述一号臂的上端设有三号动力关节,所述三号动力关节的右端通过转轴转动连接有四号关节,所述四号关节的上端设有二号臂的下端,所述二号臂的上端设有五号动力关节,所述五号动力关节的左端通过转轴转动连接有六号动力关节,所述六号动力关节的上端通过转轴转动连接有七号动力关节,所述七号动力关节的左端通过螺栓与所述测头固定机构固定连接。
9.优选的,所述缝隙尺寸检测头包括底部固定板,所述底部固定板的前表面中间位置通过螺栓连接有连接板,所述连接板的前端通过螺栓连接有测头安装机构,所述测头安装机构的内部设有间隙面差测头,所述测头安装机构的左端设有初定位相机,所述测头安装机构的右端设有辅助光源。
10.与现有技术相比,本发明的有益效果是:一种车身表面间隙断差自动测量设备,采用在机器人底座上设置机器人控制柜存放箱并在机器人存放箱的上表面设置滑动机构的设计,替代传统总装车间完成整车装配后采用人工使用塞尺、游标卡尺及断差尺对车身各零部件总成间的间隙面差进行测量和检验的方式,不容易因为人工测量的主观性和人工测量较大的测量误差对车身表面间隙断差检测的结果产生影响,保证检测结果真实有效的反映车身真实的情况,有利于整车质量保障和监督,避免了培养一名经验丰富、技术过硬的车身表面间隙断差检测师,带来的需要多年的实践和积累,需要投入大量的资源和费用等问题,有利于降低人工成本,提高检测效率,取代目前常见的表面间隙断差自动检测设备采用工业机器人带检测测头进行测量的方式,不需要设置安全围栏,可以实现人机协同作业及本工位本地人工复检等任务,有利于节省操作工位,节省工时。
附图说明
11.图1为本发明的主体结构俯视示意图;
12.图2为本发明的机器人结构俯视示意图;
13.图3为本发明的机器人底座结构剖视图;
14.图4为本发明的机器人连接机构结构左视剖视图;
15.图5为本发明的机器人结构示意图;
16.图6为本发明的缝隙尺寸检测头结构俯视剖视图。
17.图中:1
‑
机器人底座、101
‑
地面固定板、102
‑
竖直支撑板、103
‑
倾斜加固板、104
‑
一号窗口、105
‑
二号窗口、106
‑
支撑板、2
‑
机器人控制柜存放箱、3
‑
滑动机构、301
‑
固定板、302
‑
滑道、303
‑
控制箱、304
‑
线缆收集盒、305
‑
限位板、306
‑
齿条、4
‑
机器人固定机构、401
‑
滑块、402
‑
一号伺服电机、403
‑
齿轮、5
‑
机器人、501
‑
连接座、502
‑
一号动力关节、503
‑
二号关节、504
‑
一号臂、505
‑
三号动力关节、506
‑
四号关节、507
‑
二号臂、508
‑
五号动力关节、509
‑
六号动力关节、5010
‑
七号动力关节、6
‑
测头固定机构、7
‑
缝隙尺寸检测头、701
‑
底部固定板、702
‑
连接板、703
‑
测头安装机构、704
‑
间隙面差测头、705
‑
初定位相机、706
‑
辅助光源、8
‑
输送机构、9
‑
车身本体。
具体实施方式
18.下面将结合本发明实施例中的附图,对本发明实施例中的技术方案进行清楚、完整地描述,显然,所描述的实施例仅仅是本发明一部分实施例,而不是全部的实施例。基于本发明中的实施例,本领域普通技术人员在没有做出创造性劳动前提下所获得的所有其他实施例,都属于本发明保护的范围。
19.请参阅图1
‑
6,本发明提供一种技术方案:一种车身表面间隙断差自动测量设备,包括机器人底座1,所述机器人底座1的上端设有机器人控制柜存放箱2,所述机器人控制柜存放箱的上表面中间位置左右方向设有滑动机构3,通过机器人底座1对机器人控制柜存放箱2及机器人控制柜存放箱2上端的滑动结构3提供支撑,所述滑动机构3的上端设有机器人固定机构4,所述机器人固定机构4的上表面通过螺栓连接有机器人5,通过滑动结构3上端的机器人固定结构4固定连接机器人5,所述机器人5的工作端通过螺栓设有测头固定机构6,所述测头固定机构6的内部通过螺栓连接有缝隙尺寸检测头7,四组所述缝隙尺寸检测头7之间设有输送机构8,所述输送结构8的内部设有车身本体9。
20.具体而言,所述机器人底座1包括地面固定板101,所述地面固定板101的四角处通过化学锚栓固定在地面上,所述地面固定板101的上表面中间位置前后方向设有竖直支撑板102,所述竖直支撑板102的前后表面下端与所述地面固定板101之间焊接有倾斜加固板103,所述竖直支撑板102为一整块上端拐角处设有直角倒角的长方形不锈钢板,所述竖直支撑板102的左右侧表面上下端贯穿开设有一号窗口104及二号窗口105,所述一号窗口104的内部卡接有机器人控制柜存放箱2,两块所述竖直支撑板102之间且在所述一号窗口104及所述二号窗口105之间焊接有支撑板106,通过机器人底座1使得机器人控制柜存放箱2与机器人底座1整体连接,为滑动结构3提供稳定的支撑。
21.具体而言,所述滑动机构3包括固定板301,所述固定板301通过螺栓与所述机器人控制柜存放箱2的上表面固定连接,所述固定板301的上端通过螺栓固定连接有滑道302,所述滑道302的右端且在所述机器人控制柜存放箱2的右端外部设有控制箱303,所述控制箱303的左端且在所述滑道302的上端设有线缆收集盒304,所述滑道302的左端设有限位板305,所述滑道302的内部后端设有齿条306,所述滑道302与所述机器人固定机构4滑动连接。
22.具体而言,所述机器人固定机构4包括滑块401,所述滑块401与所述滑道302滑动
连接,所述滑块401的内部通过螺栓连接有一号伺服电机402,所述一号伺服电机402的输出端贯穿所述滑块401的下壁伸入到所述滑道302的内部,所述一号伺服电机402的输出端通过连接键连接有齿轮403,所述齿轮403与所述齿条306啮合,所述滑块401的上表面开设有供所述机器人5连接的螺纹孔,在滑块401的上表面通过螺栓固定连接机器人5,为机器人5提供稳定的支撑。
23.具体而言,所述机器人5包括机器人连接座501,所述连接座501通过螺栓与所述滑块401的上表面连接,所述机器人连接座501的上端通过转轴转动连接有一号动力关节502,所述一号动力关节502的左端通过转轴转动连接有二号关节503,所述二号关节503的上端设有一号臂504的下端,所述一号臂504的上端设有三号动力关节505,所述三号动力关节505的右端通过转轴转动连接有四号关节506,所述四号关节506的上端设有二号臂507的下端,所述二号臂507的上端设有五号动力关节508,所述五号动力关节508的左端通过转轴转动连接有六号动力关节509,所述六号动力关节509的上端通过转轴转动连接有七号动力关节5010,所述七号动力关节5010的左端通过螺栓与所述测头固定机构6固定连接。
24.具体而言,所述缝隙尺寸检测头7包括底部固定板701,所述底部固定板701的前表面中间位置通过螺栓连接有连接板702,所述连接板702的前端通过螺栓连接有测头安装机构703,所述测头安装机构703的内部设有间隙面差测头704,所述测头安装机构703的左端设有初定位相机705,所述测头安装机构703的右端设有辅助光源706。
25.工作原理:本发明在使用时,首先通过输送机构8将需要组装的车身主体9输送到设备中部,输送机构8将车身主体9运送到设定的位置后,给设备发送到位信号,设备启动开始工作,此时机器人5带动尺寸检测头7运动到预先设定好的车身特征位置,初定位相机705对车身上特征点进行拍照并生成该点的空间坐标信息,并与初始特征点的位置坐标信息进行比对,得出补偿坐标数值并补偿给机器人5,在完成初定位后,机器人5带动尺寸检测头7上的间隙断差测头704按照车身上选取的检测点依照程序中设定的运行轨迹进行逐一的测量并生成实时数据,检测结果实时显示在工位显示屏上并记录在现场工控机中,同时也将本车次的检测结果上传车间信息管理系统进行备份和存储,完成该工作流程后,设备控制系统给输送机构8发送检测完成信号,输送机构8将车身主体9运送至下一工位,完成本工作循环。
26.在本发明的描述中,除非另有明确的规定和限定,术语“安装”、“相连”、“连接”、“固定”应做广义理解,例如,可以是固定连接,也可以是可拆卸连接,或成一体;可以是机械连接,也可以是电连接;可以是直接相连,也可以通过中间媒介间接相连,可以是两个元件内部的连通或两个元件的相互作用关系。对于本领域的普通技术人员而言,可以具体情况理解上述术语在本发明中的具体含义。
27.本发明使用到的标准零件均可以从市场上购买,异形件根据说明书和附图的记载均可以进行订制,各个零件的具体连接方式均采用现有技术中成熟的螺栓、铆钉、焊接等常规手段,机械、零件和设备均采用现有技术中,常规的型号,加上电路连接采用现有技术中常规的连接方式,在此不再详述。
28.尽管已经示出和描述了本发明的实施例,对于本领域的普通技术人员而言,可以理解在不脱离本发明的原理和精神的情况下可以对这些实施例进行多种变化、修改、替换和变型,本发明的范围由所附权利要求及其等同物限定。