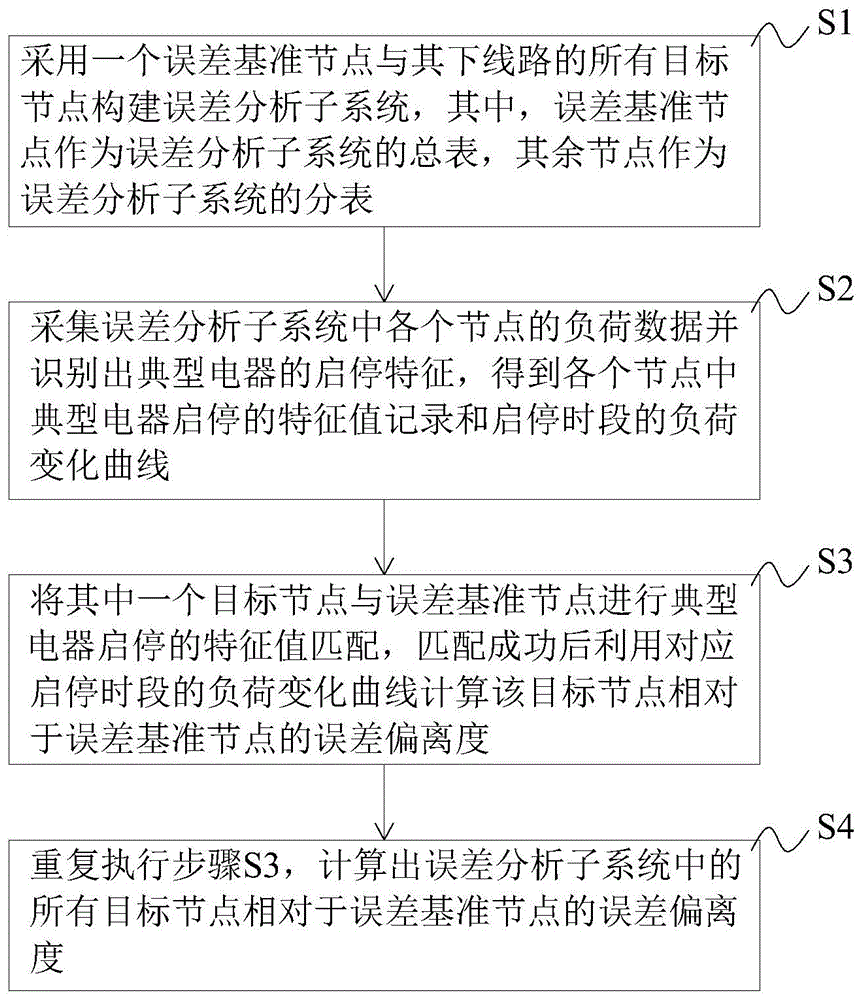
本发明涉及台区计量系统误差分析
技术领域:
,特别地,涉及一种对台区计量设备进行误差分析的方法及系统、设备、计算机可读取的存储介质。
背景技术:
:电力负荷的测量域由总表和众多分表构成,其中总表负责测量总节点,也就是整个测量域的负荷,分表负责测量各个分节点的负荷,如果没有误差的存在,总表的测量值应该是各分表测量值之和。但是在实际应用中,无论总表还是分表,都存在测量误差,如果这些表的误差都在合理范围内,则系统处于误差正常状态,如果有一部分表的误差在合理范围之外,则系统处于误差异常状态,怎样确定每只表的误差状态,以及异常表的相对误差,一直是电力系统需要解决的问题。现有技术中虽然可以对单个电表的误差进行分析,但是暂未对整个测量域的误差进行分析。例如专利cn106772203b公开了一种谐波条件下电表综合误差分析方法,其通过分别计算谐波条件下电表计量方式误差和计算精度误差,从而获得电表的综合误差,误差分析更合理,分析结果更准确,有利于提出更合理的电能计量方案,但是其无法对异常表的相对误差进行分析。技术实现要素:本发明提供了一种对台区计量设备进行误差分析的方法及系统、设备、计算机可读取的存储介质,以解决现有的误差分析方法无法对异常表的相对误差进行分析的技术问题。根据本发明的一个方面,提供一种对台区计量设备进行误差分析的方法,包括以下步骤:步骤s1:采用一个误差基准节点与其下线路的所有目标节点构建误差分析子系统,其中,误差基准节点作为误差分析子系统的总表,其余节点作为误差分析子系统的分表;步骤s2:采集误差分析子系统中各个节点的负荷数据并识别出典型电器的启停特征,得到各个节点中典型电器启停的特征值记录和启停时段的负荷变化曲线;步骤s3:将其中一个目标节点与误差基准节点进行典型电器启停的特征值匹配,匹配成功后利用对应启停时段的负荷变化曲线计算该目标节点相对于误差基准节点的误差偏离度;步骤s4:重复执行步骤s3,计算出误差分析子系统中的所有目标节点相对于误差基准节点的误差偏离度。进一步地,所述步骤s3中进行典型电器启停的特征值匹配的过程包括以下内容:当总表和分表均采用高频计量时,对典型电器启停的特征值进行时间同步,同步后若总表和分表的特征值分量在预设容错范围内相等,则两个特征值匹配;或者,当总表采用高频计量而分表采用低频计量时,在总表的启停时段的负荷变化曲线上遍历每一个启停时刻,并以每个启停时刻为中心、前后各设定一个时间同步最大误差来构建一个排他判别窗口,若排他判别窗口内只有一个启停或者有两个反向的启停,则标记为可用启停,对于总表上所有可用启停对应的特征值与分表的启停特征值进行匹配,若分表的启停时刻落入以总表启停时刻对应的排他判别窗口内,且负荷变化方向相同、负荷变化值在预设容错范围内相等时,则两个特征值匹配。进一步地,所述步骤s3还包括以下内容:当总表与分表都采用高频计量时,对于匹配成功的启停特征值,使用两个节点各自的启停时段负荷变化曲线计算目标节点相对于误差基准节点的时间补偿值,并按照该时间补偿值对目标节点的负荷变化曲线进行补偿。进一步地,所述使用两个节点各自的启停时段负荷变化曲线计算目标节点相对于误差基准节点的时间补偿值的过程具体包括以下内容:步骤s31:使用第一滑动时间窗口在误差基准节点的启停时段的负荷变化曲线上滑动,找到一个第一时点,此时第一滑动时间窗口内包含完整的启停过程,固定第一滑动时间窗口;步骤s32:使用与第一滑动时间窗口相同宽度的第二滑动时间窗口在待补偿节点的启停时段的负荷变化曲线上滑动,每滑动一个时点,计算一次第一滑动时间窗口内各时点的负荷值与第二滑动时间窗口内各时点的负荷值之间的皮尔逊相关系数,完成第二滑动时间窗口的全部滑动后,找出所有时点中皮尔逊相关系数最大的点作为第二时点,并将第二滑动时间窗口固定在第二时点对应的位置;步骤s33:计算第一时点和第二时点的差值,该时间差值即为待补偿节点相对于误差基准节点的时间补偿值。进一步地,所述步骤s3中采用以下公式来计算误差偏离度:其中,为误差偏离度的加权平均值,wi为单次误差偏离度的权重系数,δi为单次计算的误差偏离度。进一步地,所述步骤s2中采用启停判断窗口来识别典型电器的启停特征,该启停判断窗口包括左侧噪声判别区、启停判别区和右侧噪声判别区,当启停判别区内出现典型电器的启停时,找到启停的起点和终点,则启停判断窗口的左边至启停起点间为左侧噪声区,启停终点至启停判断窗口的右边为右侧噪声区。进一步地,当总表与待分析分表之间的线路较长时,采用以下公式对总表的负荷启停幅值进行修正:ls’=ls-ll其中,ls’为修正后的总表的负荷变化幅值,ls为修正前的总表的负荷变化幅值,ll为发生启停的线路在启停前后的线损差值。另外,本发明还提供一种对台区计量设备进行误差分析的系统,包括构建模块,用于采用一个误差基准节点与其下线路的所有目标节点构建误差分析子系统,其中,误差基准节点作为误差分析子系统的总表,其余节点作为误差分析子系统的分表;数据采集模块,用于采集误差分析子系统中各个节点的负荷数据并识别出典型电器的启停特征,得到各个节点中典型电器启停的特征值记录和启停时段的负荷变化曲线;分析模块,用于将其中一个目标节点与误差基准节点进行典型电器启停的特征值匹配,匹配成功后利用对应启停时段的负荷变化曲线计算该目标节点相对于误差基准节点的误差偏离度。另外,本发明还提供一种设备,包括处理器和存储器,所述存储器中存储有计算机程序,所述处理器通过调用所述存储器中存储的所述计算机程序,用于执行如上所述的方法的步骤。另外,本发明还提供一种计算机可读取的存储介质,用于存储对台区计量设备进行误差分析的计算机程序,该计算机程序在计算机上运行时执行如上所述的方法的步骤。本发明具有以下效果:本发明的对台区计量设备进行误差分析的方法,通过采用一个误差基准节点与其下线路的所有目标节点构成误差分析子系统,然后基于节点负荷数据中的典型电器启停的特征值记录来实现目标节点与误差基准节点之间的特征值匹配,对于每个成功的特征值匹配,基于相应启停时段的负荷变化曲线来计算该目标节点相对于误差基准节点的误差偏离度,从而可以准确评估误差分析子系统中各个目标节点相对于误差基准节点的误差状态,具有广泛的推广价值。另外,本发明的对台区计量设备进行误差分析的系统、设备、计算机可读取的存储介质同样具有上述优点。除了上面所描述的目的、特征和优点之外,本发明还有其它的目的、特征和优点。下面将参照图,对本发明作进一步详细的说明。附图说明构成本申请的一部分的附图用来提供对本发明的进一步理解,本发明的示意性实施例及其说明用于解释本发明,并不构成对本发明的不当限定。在附图中:图1是本发明优选实施例的对台区计量设备进行误差分析的方法的流程示意图。图2是低压台区线路拓扑的示意图。图3是某品牌电热水器上电的电流变化示意图。图4是某品牌电磁炉上电的电流变化示意图。图5是图1中的步骤s3中计算时间同步补偿值的子流程示意图。图6是本发明优选实施例中的启停判断窗口的示意图。图7是本发明优选实施例的一具体实施方式中某典型电器启停过程的负荷变化曲线。图8是本发明另一实施例的对台区计量设备进行误差分析的系统的模块结构示意图。具体实施方式以下结合附图对本发明的实施例进行详细说明,但是本发明可以由下述所限定和覆盖的多种不同方式实施。如图1所示,本发明的优选实施例提供一种对台区计量设备进行误差分析的方法,包括以下步骤:步骤s1:采用一个误差基准节点与其下线路的所有目标节点构建误差分析子系统,其中,误差基准节点作为误差分析子系统的总表,其余节点作为误差分析子系统的分表;步骤s2:采集误差分析子系统中各个节点的负荷数据并识别出典型电器的启停特征,得到各个节点中典型电器启停的特征值记录和启停时段的负荷变化曲线;步骤s3:将其中一个目标节点与误差基准节点进行典型电器启停的特征值匹配,匹配成功后利用对应启停时段的负荷变化曲线计算该目标节点相对于误差基准节点的误差偏离度;步骤s4:重复执行步骤s3,计算出误差分析子系统中的所有目标节点相对于误差基准节点的误差偏离度。可以理解,本实施例的对台区计量设备进行误差分析的方法,通过采用一个误差基准节点与其下线路的所有目标节点构成误差分析子系统,然后基于节点负荷数据中的典型电器启停的特征值记录来实现目标节点与误差基准节点之间的特征值匹配,对于每个成功的特征值匹配,基于相应启停时段的负荷变化曲线来计算该目标节点相对于误差基准节点的误差偏离度,从而可以准确评估误差分析子系统中各个目标节点相对于误差基准节点的误差状态,具有广泛的推广价值。可以理解,如图2所示,低压台区线路拓扑包括的相关节点有总节点、分支节点和端节点,总节点可以是能源控制器、融合终端、台区总表等设备,总节点可以对整个台区的负荷进行计量,分支节点可以是分支单元、分支上的智能断路器或表箱终端等设备,分支节点可以对始于该节点的整个分支的负荷进行计量,端节点是户表,端节点可以对该端点的负荷进行计量。为了对台区各节点的误差状态进行分析,本发明引入一个逻辑上的误差基准节点,该误差基准节点可以是物理上位于总结点或者分支节点,也可以位于一个新引入的高精度的计量设备,此时该误差基准节点与其下线路的所有目标节点构成一个误差分析子系统,误差基准节点是这个子系统的总表,其余节点是这个子系统的分表。例如,当误差基准节点为总节点时,则可以对台区内所有节点相对于总表进行误差分析;当误差基准节点为分支节点时,则可以对该分支节点以下的所有节点相对于该分支单元进行误差分析;而当误差基准节点为新引入的高精度计量设备时,则可以对该子系统中的各个节点做出精准的误差分析。可以理解,由于需要进行误差分析的子系统可能非常复杂,因此需要选择特定电器的启停特征来进行误差分析。常见的家用电器包括阻性电器和综合性电器(包括阻性、感性、容性的综合性电器),阻性电器通常包括电热水器、电烤箱、电暖器、电饭煲、电烧水壶等,综合性电器包括空调、洗衣机、冰箱、吸尘器等。其中,阻性电器在上电后可以在几十毫秒内达到稳态,稳态时负荷保持平稳。图3为某品牌电热水器上电的电流变化图,横轴为时间,纵轴为电流的测量值,测量的频率为20毫秒1次。从图3可以看到,电热水器启动后,电流经过3个测量周期达到工作稳态,即瞬态上升时间为20ms*3=60ms。电热水器的这种瞬态时间短、负荷变化大、瞬态前后保持稳态的启停特征,很容易识别。图4为某品牌电磁炉上电的电流变化图,横轴为时间,纵轴为电流的测量值,测量的频率为20ms/次。从图4可以看出,电磁炉启动后,电流经过2s多达到稳态,电磁炉的这种启停特征,由于瞬态周期长,很容易被其它电器的负荷变化所干扰,不易于识别。由于需要进行误差分析的子系统可能非常复杂,此时意味着误差基准节点的负荷变化也可能非常复杂,所以需要选择合适电器的启停特征进行识别。通常,启动后瞬态时间短、负荷变化明显的电器,其启停的负荷特征不易被干扰,在高频计量的情况下,其启停特征容易从误差基准节点的负荷数据中被分解出来,同时,由于后续计算需要使用启停前后负荷变化的幅值,故还需要电器在启停前后保持负荷稳态,以便得到准确的启停幅值,以用于后续计算。而大功率阻性电器(如电热水器等)由于其启停的瞬态时间非常短,负荷变化明显,启停前后保持负荷稳态,利于识别与计算,因而常被选择用于本方案的误差分析。另外,短瞬态的大功率综合性电器,如果其具备启停的瞬态时间短、负荷变化明显、启停前后保持负荷稳态的条件,也可以用于本方案的误差分析。可以理解,对于周波(20毫秒)量级的高频计量节点,典型电器启停的负荷特征值包括启停时刻、瞬态上升时长、负荷变化方向(即启或停)、负荷变化值,而对于秒级的相对低频计量节点,典型电器启停的负荷特征值包括启停时刻、负荷变化方向(启或停)、负荷变化值。误差基准节点是误差分析子系统中的总表,其负荷变化可能非常复杂,因而一般采用高频计量,而子系统的其他节点依其计量范围,可采用高频计量,也可采用相对低频的计量。可以理解,所述步骤s3中进行典型电器启停的特征值匹配的过程包括以下内容:当总表和分表均采用高频计量时,对典型电器启停的特征值进行时间同步,同步后若总表和分表的特征值分量在预设容错范围内相等,则两个特征值匹配。其中,这个容错范围可以根据实际情况而定,例如启停时刻的容错为两个周波时长,瞬态上升时长的容错为1个周波时长,负荷变化方向不进行容错,负荷变化幅值的容错为分表相对总表在20%以内。另外,特征值分量指的是启停时刻、瞬态上升时长、负荷变化方向(即启或停)、负荷变化值。而当总表采用高频计量而分表采用低频计量时,由于典型电器启停的特征值无法进行精确的时间同步,则需要对时间进行容错以筛选出可用的启停特征值。假定误差分析子系统中各节点间的时间同步的最大误差为δt,则在总表的启停时段的负荷变化曲线上遍历每一个启停时刻,并以每个启停时刻为中心、前后各设定一个时间同步最大误差δt来构建一个排他判别窗口,若排他判别窗口内只有一个启停或者有两个反向的启停,则标记为可用启停,否则为不可用启停。对于总表上所有可用启停对应的特征值与分表的启停特征值进行匹配,若分表的启停时刻落入以总表启停时刻对应的排他判别窗口内,且负荷变化方向相同、负荷变化值在预设容错范围内相等时,则两个特征值匹配。针对总表与分表之间无法进行时间同步的情况,本发明设置了排他判别窗口来进行时间容错,以放弃相当数量的启停特征值为代价实现了两个不同时间精度的节点之间启停匹配的准确性。可以理解,当误差分析子系统中的总表与分表都采用高频计量时,子系统各节点间负荷数据需保持严格的时间同步,如此则可以大幅提升处理速度与准确性。但在实际的电力系统中,带有计量功能的节点设备,其计量功能和管理功能分别在计量芯和管理芯上实现,计量芯用于电压、电流等数据的计量,管理芯用于这些数据的采集和其他管理功能。不同节点的管理芯、计量芯之间存在着时间同步的误差,包括:1)台区各节点管理芯之间的同步误差2)各节点内部的管理芯和计量芯之间同步误差,该误差各节点随机,最大可以在几百毫秒量级。对于1)的误差部分,使用传统的精准校时方案,对台区各节点进行校时,可以将系统各节点管理芯的时间同步误差控制秒量级(1~2秒以内),未来的通过hplc校时、gps校时,可以将管理芯的同步误差控制在毫秒量级。而对于2)的误差部分,目前仍无好的解决方案。因此,作为优选的,所述步骤s3还包括以下内容:当总表与分表都采用高频计量时,对于匹配成功的启停特征值,使用两个节点各自的启停时段负荷变化曲线计算目标节点相对于误差基准节点的时间补偿值,并按照该时间补偿值对目标节点的负荷变化曲线进行补偿。本发明通过基于两个匹配成功的节点在启停时段的负荷变化曲线来计算时间补偿值,实现了目标节点与误差基准节点之间的时间同步补偿,进一步提升了误差分析的精准度。具体地,如图5所示,所述使用两个节点各自的启停时段负荷变化曲线计算目标节点相对于误差基准节点的时间补偿值的过程具体包括以下内容:步骤s31:使用第一滑动时间窗口在误差基准节点的启停时段的负荷变化曲线上滑动,找到一个第一时点,此时第一滑动时间窗口内包含完整的启停过程,固定第一滑动时间窗口;步骤s32:使用与第一滑动时间窗口相同宽度的第二滑动时间窗口在待补偿节点(即误差分析子系统中的目标节点)的启停时段的负荷变化曲线上滑动,每滑动一个时点,计算一次第一滑动时间窗口内各时点的负荷值与第二滑动时间窗口内各时点的负荷值之间的皮尔逊相关系数,完成第二滑动时间窗口的全部滑动后,找出所有时点中皮尔逊相关系数最大的点作为第二时点,并将第二滑动时间窗口固定在第二时点对应的位置;此时,第一滑动时间窗口内的负荷变化曲线与第二时间窗口内的负荷变化曲线具有最大的相关性;步骤s33:计算第一时点和第二时点的差值,该时间差值即为待补偿节点相对于误差基准节点的时间补偿值。通过使用两个等宽的滑动时间窗口在总表和分表的负荷变化曲线上滑动,并计算总表窗口内的负荷变化曲线与分表窗口内的负荷变化曲线之间的皮尔逊相关系数,并找出相关度最大的两个时点,基于两个时点的差值来实现高频计量分表的负荷数据相对于总表负荷数据的时间同步补偿值,精准地实现了分表相对于总表的时间同步补偿,从而完成误差分析子系统中所有节点相对于误差基准节点的时间补偿,进一步提高了误差分析的精准度。另外,还可以分别对总表和分表的负荷变化曲线上的点进行三次样条差值处理或等距节点差值处理,可以进一步提高时间同步补偿值的精度。可以理解,误差基准节点作为误差分析子系统的总表,其负荷变化会非常复杂,分解出来的典型电器启停的负荷变化差值会受到误差基准节点负荷噪声的影响,如果想得到更加准确的节点误差分析,则需要降低噪声的影响。作为优选的,所述步骤s2中采用启停判断窗口来识别典型电器的启停特征,如图6所示,该启停判断窗口包括左侧噪声判别区、启停判别区和右侧噪声判别区,所述左侧噪声判别区用于进行启停左侧的噪声数据判别,所述启停判别区用于进行启停数据判别,所述右侧噪声判别区用于进行启停右侧的噪声数据判别,当启停判别区内出现典型电器的启停时,找到启停的起点和终点,则启停判断窗口的左边至启停起点间为左侧噪声区,启停终点至启停判断窗口的右边为右侧噪声区。定义为左侧噪声区负荷数据的算术平均值,为右侧噪声区负荷数据的算术平均值,ls为典型电器启停的负荷变化幅值,abs()为绝对值函数。再定义lnm为噪声区波动极值,为左侧噪声区负荷均方差与右侧噪声区负荷均方差的较大者,lnm=max(snl,snr),snl为左侧噪声区的负荷均方差,snr为右侧噪声区的负荷均方差。其中,均方差的计算公式如下:xi为左/右侧噪声区的负荷值,为左/右侧噪声区负荷数据的算术平均值,即或s为左/右侧噪声区负荷数据的均方差,即snl或snr。定义典型电器启停的信噪比为r,r=ls/lnm,显然,信噪比越高,噪声的影响越小,计算的结果越可靠。定义单次误差偏离度δ,对于典型电器的启停匹配成功的两个节点(例如节点1为误差基准节,节点2为目标节点),目标节点相对于误差基准节点的单次误差偏离度定位为目标节点与误差基准节点的启停负荷变化幅值之差与误差基准节点的负荷变化幅值的比值,即:δ=(ls2-ls1)/ls1。对于误差基准节点,由于典型电器启停前后的噪声负荷会影响到ls1的计算,从而影响单次误差偏离度的计算,因此,需要消除噪声的干扰来提高误差偏离度的计算精准度。在通常情况下,典型电器启停的信噪比决定了噪声对偏离度计算的影响,信噪比越高,噪声影响越小,因此,本发明涉及了一个正比于信噪比r的权重系数,以此来计算所有单次误差偏离度的加权平均值,并作为最终的误差偏离度其中,权重系数基于以下公式计算:其中,r0为启停信噪比的门限值,r为单次计算误差偏离度时的启停信噪比,k和b为常数。当单次计算的信噪比小于等于r0时,噪声对计算出的误差偏离度的影响过大,则将本次计算的权重系数设置为0,意味着计算得出的单次误差偏离度无效。r0、k、b可根据实际应用情况确定,显然,当k为0时,所有有效单次误差偏离度具有相同权重。则最终的误差偏离度为:其中,wi为单次误差偏离度的权重系数,δi为单次计算的误差偏离度。通过采用权重计算的方式,消除了噪声干扰过大的负荷数据,大大提升了误差偏离度计算的精准度。例如,下表1为某典型电器启停中各时点的负荷值,采用了较大的噪声波动。表1、某典型电器启停中各时点的负荷值相对时点1234567891011负荷值5871000602920590195033333758355837633458图7为该启停过程中的负荷变化曲线,在本例中,图6的滑动窗口可以设计为左侧噪声判别区宽度为3,启停判别区宽度为4,右侧噪声判别区宽度为3,时点5是本次启动的起点,时点7是本次启动的终点,则时点1至时点5是左侧噪声区,时点7至时点11是右侧噪声区,时点5至时点7的数据是启动数据。则左侧噪声区负荷数据的算术平均值右侧噪声区负荷数据的算术平均值左侧噪声区负荷均方差snl=203.1,右侧噪声区负荷均方差snr=171.2,噪声区波动极值,lnm=max(snl,snr)=max(203.1,171.2)=203.1,负荷启停幅值,ls=abs(3585.0-739.8)=2845.2,启停信噪比,r=ls/lnm=14.01,假定启停信噪比的门限值在r0=5,即当启停信噪比小于等于5时,权重系数为0,假定r=100时,权重系数为1,则可以解得因此,当启停信噪比为14.01时,对应权重系数为:w=kr+b=0.095。可以理解,在误差分析子系统中,总表的负荷包括两部分,即所有分表的负荷和线损。当误差分析子系统的总表和分表之间线路较短时,线路阻抗较小,则线损对于计算的误差偏离度的影响可以忽略。而当总表与待分析分表之间的线路较长时,线路阻抗较大,则采用以下公式对总表的负荷启停幅值进行修正:ls’=ls-ll其中,ls’为修正后的总表的负荷变化幅值,ll为发生启停的线路在启停前后的线损差值。由于误差偏离度采用典型电器启停的负荷变化幅值进行计算,负荷变化幅值表现在总表上就是负荷变化前后稳态间的差值,而其中线损的贡献就是前后稳态间线损的差值。在未发生大负荷启停的线路中,其线损差值可以忽略,而在发生启停的线路中,可以通过使用线路阻抗与启停前后的电流值来计算出线损的差值,从而对总表的负荷变化幅值进行修正,以得到更精确的误差分析结果。另外,如图8所示,本发明的另一实施例还提供一种对台区计量设备进行误差分析的系统,优选采用如上所述的对台区计量设备进行误差分析的方法,该系统包括构建模块,用于采用一个误差基准节点与其下线路的所有目标节点构建误差分析子系统,其中,误差基准节点作为误差分析子系统的总表,其余节点作为误差分析子系统的分表;数据采集模块,用于采集误差分析子系统中各个节点的负荷数据并识别出典型电器的启停特征,得到各个节点中典型电器启停的特征值记录和启停时段的负荷变化曲线;分析模块,用于将其中一个目标节点与误差基准节点进行典型电器启停的特征值匹配,匹配成功后利用对应启停时段的负荷变化曲线计算该目标节点相对于误差基准节点的误差偏离度。可以理解,本实施例的系统中的各个模块与上述方法实施例中的各个步骤相对应,故具体的工作原理在此不再赘述。可以理解,本实施例的对台区计量设备进行误差分析的系统,通过采用一个误差基准节点与其下线路的所有目标节点构成误差分析子系统,然后基于节点负荷数据中的典型电器启停的特征值记录来实现目标节点与误差基准节点之间的特征值匹配,对于每个成功的特征值匹配,基于相应启停时段的负荷变化曲线来计算该目标节点相对于误差基准节点的误差偏离度,从而可以准确评估误差分析子系统中各个目标节点相对于误差基准节点的误差状态,具有广泛的推广价值。另外,本发明还提供一种设备,包括处理器和存储器,所述存储器中存储有计算机程序,所述处理器通过调用所述存储器中存储的所述计算机程序,用于执行如上所述的方法的步骤。另外,本发明还提供一种计算机可读取的存储介质,用于存储对台区计量设备进行误差分析的计算机程序,该计算机程序在计算机上运行时执行如上所述的方法的步骤。一般计算机可读取介质的形式包括:软盘(floppydisk)、可挠性盘片(flexibledisk)、硬盘、磁带、任何其与的磁性介质、cd-rom、任何其余的光学介质、打孔卡片(punchcards)、纸带(papertape)、任何其余的带有洞的图案的物理介质、随机存取存储器(ram)、可编程只读存储器(prom)、可抹除可编程只读存储器(eprom)、快闪可抹除可编程只读存储器(flash-eprom)、其余任何存储器芯片或卡匣、或任何其余可让计算机读取的介质。指令可进一步被一传输介质所传送或接收。传输介质这一术语可包含任何有形或无形的介质,其可用来存储、编码或承载用来给机器执行的指令,并且包含数字或模拟通信信号或其与促进上述指令的通信的无形介质。传输介质包含同轴电缆、铜线以及光纤,其包含了用来传输一计算机数据信号的总线的导线。以上所述仅为本发明的优选实施例而已,并不用于限制本发明,对于本领域的技术人员来说,本发明可以有各种更改和变化。凡在本发明的精神和原则之内,所作的任何修改、等同替换、改进等,均应包含在本发明的保护范围之内。当前第1页12