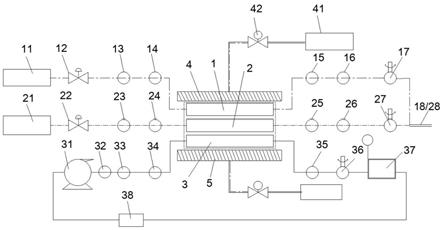
1.本发明涉及燃料电池电堆检测技术领域,特别涉及一种燃料电池电堆的耐压强度检测装置和方法。
背景技术:2.质子交换膜燃料电池电堆是由质子交换膜、催化剂层、碳纤维层、隔离极板等部件组成,质子交换膜是一种高分子薄膜,起到隔绝反应物气体等作用。随着燃料电池的技术快速发展,适应电堆的性能提升,质子交换膜的厚度正在大幅度减薄,而导致结构强度下降,并且电堆的运行条件已经发展到高温高压的工况,质子交换膜承受的压力和应力条件快速提升,需要进一步明确电堆的运行条件的限制,防止电堆的质子交换膜损伤而导致电堆失效。
3.目前质子交换膜燃料电池电堆的运行条件限制没有明确的测试方法,整堆电堆的检测成本过高,而零部件的静态检测结果与整堆运行状态下有较大的差异,导致制定的限制条件过于保守或者限制条件过于宽松而导致实际应用中的批量问题。
4.整堆目前存在的电堆结构强度上限制条件优化制定需要一种在pv和dv阶段的低成本优化检测方案。
5.目前为止,燃料电池行业还没有成熟公开的燃料电池电堆耐压强度等结构特性的检测方案。目前,燃料电池行业可以采用可行性的燃料电池电堆耐压强度检测方案可以采用零部件的独立检测和整堆的静态条件下的检测。零部件的独立检测方案主要集中于质子交换膜的爆破强度检测、质子交换膜应力交变检测等检测。整堆的静态条件下的检测主要为整堆的静态爆破压力检测和进气压力交变检测等。
6.燃料电池行业缺少成熟的电堆耐压强度检测方案,可能导致电堆的运行限制条件缺失或者电堆运行条件过于保守而导致电堆性能和系统性能无法充分发挥。燃料电池行业采用零部件的独立检测方案,可能导致独立零部件的检测状态与电堆集成结构和运行条件状态下有较大的差异,电堆的运行条件限制不适应于运行状态电堆的实际情况。燃料电池行业采用整堆的静态强度检测方案,电堆测试情况过多,整堆的成本过高而导致pv和dv的测试成本过多,整堆的价格通常为十万级的情况,需要一种优化的低成本检测方案。
技术实现要素:7.本发明的目的在于提供一种燃料电池电堆的耐压强度检测装置和方法,采用一种在组合状态下的零部件强度检测,取代零部件的独立状态下检测,零部件的检测状态更加接近实际运行状态为实现上述目的,采用气体流动状态下的部件强度检测,取代整堆或部件的静态状态下的检测,检测状态更加接近实际运行状态;采用融合运行状态下的温度、湿度、压堆压力等影响因素下的电堆强度检测,取代室温等恒定条件下的电堆强度检测。
8.本发明提供如下技术方案:本技术公开了一种燃料电池电堆的耐压强度检测装置,包括压紧装置、燃料管路、
空气管路、冷却管路和控制器,所述压紧装置由上压板和下压板组成,所述上压板与下压板之间设有待检测的燃料电池电堆,所述燃料电池电堆的燃料腔体、空气腔体和冷却腔体均与压紧装置固定连接,所述燃料腔体与所述燃料管路相连接,所述燃料管路随燃料气体流通方向依次设有燃料气源、第一电磁阀、第一进口流量传感器、第一进口压力传感器、燃料腔体、第一出口压力传感器、第一出口流量传感器、第一出口节气门和第一尾排管路,所述空气管路与空气腔体相连接,所述空气管路随空气流通方向依次设有空气气源、第二电磁阀、第二进口流量传感器、第二进口压力传感器、空气腔体、第二出口压力传感器、第二出口流量传感器、第二出口节气门和第二尾排管路,所述第一尾排管路与第二尾排管路相交汇,所述冷却腔体与冷却管路相连接,所述冷却管路随冷却液流动方向依次设有水泵、进口温度传感器、第三进口流量传感器、第三进口压力传感器、冷却腔体、第三出口压力传感器、第三出口节气门、储水箱和加热器,所述控制器与压紧装置、燃料管路、空气管路之间电性连接。
9.作为优选,所述上压板和下压板上均连有压力气源和减压阀。
10.作为优选,所述上压板上连有压力气源和减压阀,所述下压板采用固定结构。
11.作为优选,所述储水箱的一端与外界大气连接。
12.作为优选,所述燃料气源与空气气源处设有气体加湿器。
13.本技术还公开了一种燃料电池电堆的耐压强度检测方法,包括基础测试操作、燃料腔体压力检测、空气腔体压力检测和冷却腔体压力检测,所述基础测试操作包括如下步骤:s1、安装待检测的燃料电池电堆,通过压紧装置调节待检测的燃料电池电堆的压堆压力;s2、调节启动控制器,检查各部件是否工作正常;s3、运行冷却管路:运行水泵,设置冷却液流量,启动加热器,监控冷却腔体进口的冷却液温度,控制待检测的燃料电池电堆的温度在设定运行范围内;s4、待检测的燃料电池电堆的温度稳定后,运行燃料管路和空气管路,保证燃料腔体、空气腔体和冷却腔体的压力平衡:开启第一电磁阀和第二电磁阀,设置燃料管路的燃料气体流量和燃料气体压力,同时设置空气管路的空气流量和空气压力;s5、当运行参数到达要求的测试范围后,监测第一进口流量传感器、第一出口流量传感器、第二进口流量传感器、第二出口流量传感器,计算燃料腔体的泄露量、空气腔体的泄露量以及燃料腔体与空气腔体的总泄露量;所述燃料腔体压力检测包括如下操作:a1、完成基础测试操作;a2、调节第一出口节气门的开度,监测第一进口流量传感器、第一出口流量传感器,计算燃料腔体的泄露量是否有突变以及燃料腔体泄露量是否超出要求;a3、多次运行a2,记录下运行数据;所述空气腔体压力检测包括如下操作:b1、完成基础测试操作;b2、调节第二出口节气门的开度,监测第二进口流量传感器、第二出口流量传感器,计算空气腔体的泄露量是否有突变以及空气腔体泄露量是否超出要求;
b3、多次运行b2,记录下运行数据;所述冷却腔体压力检测包括如下操作:c1、完成基础测试操作;c2、调节第三出口节气门的开度和水泵的转速,监测第一进口流量传感器、第一出口流量传感器、第二进口流量传感器、第二出口流量传感器,计算空气腔体的泄露量是否有突变以及空气腔体泄露量是否超出要求;计算燃料腔体的泄露量是否有突变以及燃料腔体泄露量是否超出要求;计算燃料腔体与空气腔体的总泄露量是否有突变以及燃料腔体与空气腔体的总泄露量是否超出要求;c3、多次运行c2,记录下运行数据。
14.作为优选,还包括气体压力交变耐久测试,包括如下操作:d1、完成基础测试操作;d2、设置第一出口节气门的开度上限和开度下限;d3、令第一出口节气门的开度在开度上限和开度下限之间周期性交变,监测第一进口流量传感器、第一出口流量传感器、第二进口流量传感器、第二出口流量传感器,计算空气腔体的泄露量是否有突变以及空气腔体泄露量是否超出要求;计算燃料腔体的泄露量是否有突变以及燃料腔体泄露量是否超出要求;计算燃料腔体与空气腔体的总泄露量是否有突变以及燃料腔体与空气腔体的总泄露量是否超出要求;d4、多次运行d2,记录下运行数据。
15.本发明的有益效果:1、本技术的技术方案,可以有效模拟电堆在实际运行状态下的温度、气体流量、工作压力和湿度等情况,测试的情况和结构基本接近运行情况,提高了相对于零部件单独检测等条件下的模拟真实性;2、本技术可以适用于单电池或均布流道模拟电池等结构,可以快速、有效、低成本的大量测试电堆设计耐压情况;3、本技术专利测试在电堆的流体运行情况下进行,充分考虑电堆内部的流量、压力等变化情况,相比于静态测试,提高实际的测试精度等;4、本技术采用流量传感器和压力传感器等检测流体特性,可以通过流量传感器的数值的技术,精确测试电堆的外漏、窜漏等数值及其变化情况,通过泄漏量的突变和超出阈值报警可以准确判读按压数据的极限;5、本技术可以用于测试流体运行状态下的电堆气体压力交变的耐久性,电堆的运行寿命和运行限制值制定了依据;6、本技术采用一个压力气缸固定电堆单电池,取消了复杂的固定结构,并且能够在测试中快速变更压堆预紧力,测试不同预紧力下的耐压极限值,提升压堆的参数控制精度;本发明的特征及优点将通过实施例结合附图进行详细说明。
附图说明
16.图1是本发明一种燃料电池电堆的耐压强度检测装置的结构示意图;图2是本发明一种燃料电池电堆的耐压强度检测方法的基础测试操作的流程图;
图3是本发明一种燃料电池电堆的耐压强度检测方法的燃料腔体压力检测的流程图;图4是本发明一种燃料电池电堆的耐压强度检测方法的空气腔体压力检测的流程图;图5是本发明一种燃料电池电堆的耐压强度检测方法的冷却腔体压力检测的流程图;图6是本发明一种燃料电池电堆的耐压强度检测方法的气体压力交变耐久测试的流程图;图中:1
‑
燃料腔体、11
‑
燃料气源、12
‑
第一电磁阀、13
‑
第一进口流量传感器、14
‑
第一进口压力传感器、15
‑
第一出口压力传感器、16
‑
第一出口流量传感器、17
‑
第一出口节气门、18
‑
第一尾排管路、2
‑
空气腔体、21
‑
空气气源、22
‑
第二电磁阀、23
‑
第二进口流量传感器、24
‑
第二进口压力传感器、25
‑
第二出口压力传感器、26
‑
第二出口流量传感器、27
‑
第二出口节气门、28
‑
第二尾排管路、3
‑
冷却腔体、31
‑
水泵、32
‑
进口温度传感器、33
‑
第三进口流量传感器、34
‑
第三进口压力传感器、35
‑
第三出口压力传感器、36
‑
第三出口节气门、37
‑
储水箱、38
‑
加热器、4
‑
上压板、41
‑
压力气源、42
‑
减压阀、5
‑
下压板。
具体实施方式
17.为使本发明的目的、技术方案和优点更加清楚明了,下面通过附图及实施例,对本发明进行进一步详细说明。但是应该理解,此处所描述的具体实施例仅仅用以解释本发明,并不用于限制本发明的范围。此外,在以下说明中,省略了对公知结构和技术的描述,以避免不必要地混淆本发明的概念。
18.参阅图1,一种燃料电池电堆的耐压强度检测装置分为燃料管路、空气管路、冷却管路和压紧装置组成,其原理图如下。
19.该装置的燃料管路由燃料气源11、第一电磁阀12、第一进口流量传感器13、第一进口压力传感器14、燃料腔体1、第一出口压力传感器15、第一出口流量传感器16、第一出口节气门17和第一尾排管路18等组成。燃料气源11用于提供检测用的气体,可以采用干燥的氢气、氦气、氮气等,也可以与电堆测试台或独立加湿器系统相连接,提供加湿后的氢气、氮气等。第一电磁阀12用于控制管路的启闭情况,第一出口节气门17通过开度调节控制进口气体的压力。第一进口流量传感器13用于检测进口流量,控制通过燃料腔的气体通量,第一进口压力传感器14用于控制和检测进气的压力,模拟运行情况。第一出口流量传感器16检测出口的气体流量,并且进口流量比对计算管路的气体流量泄露值,第一出口压力传感器15检测出口的压力,与计算电堆的燃料腔的流体压降,调整气体流量等,更好模拟电堆的运行情况。
20.该装置的空气管路由空气气源21、第二电磁阀22、第二进口流量传感器23、第二进口压力传感器24、空气腔体2、第二出口压力传感器25、第二出口流量传感器26、第二出口节气门27和第二尾排管路28等组成。空气气源21用于提供检测用的气体,可以采用干燥的氮气、空气等,也可以与电堆测试台或独立加湿器系统相连接,提供加湿后的氮气、空气等。第二电磁阀22用于控制管路的启闭情况,第二出口节气门27通过开度调节控制进口气体的压力。第二进口流量传感器23用于检测进口流量,控制通过空气腔的气体通量,第二进口压力
传感器24用于控制和检测进气的压力,模拟运行情况。第二出口流量传感器26检测出口的气体流量,并且进口流量比对计算管路的气体流量泄露值,第二出口压力传感器25检测出口的压力,与计算电堆的空气腔的流体压降,调整气体流量等,更好模拟电堆的运行情况。空气管路设计有汇流的第二尾排管路28,用于汇流燃料腔的检测气体,当检测气体为氢气时,可以稀释氢气排放的浓度,降低安全风险。
21.该装置的冷却管路由水泵31、进口温度传感器32、第三进口流量传感器33、第三进口压力传感器34、冷却腔体3、第三出口压力传感器35、第三出口节气门36、储水箱37和加热器38等组成。水泵31用于冷却水循环的动力和进口压力,第三出口节气门36通过开度调节控制冷却腔进口冷却水的压力,储水箱37用于储水而提高蓄水量,提高运行稳定性,并且储水箱37一端与大气连接,作为冷却管路的压力平衡点,压力数值为0(大气压)。第三进口流量传感器33用于检测进口流量,控制通过冷却腔的流量,第三进口压力传感器34用于控制和检测冷却液的入口压力,模拟运行情况,第三出口压力传感器35检测出口压力,并且计算电堆的冷却腔的流体压降,更好模拟电堆的运行情况。管路中的加热器38用于冷却管路的冷却液加热,进口温度传感器32用于检测入口温度,整体上控制冷却却液和电堆的温度,模拟运行工况。
22.本装置的压紧装置由上下两套相互连接的气缸套件组成,分别为上压紧气缸和下压紧气缸,也可以采用下压紧气缸改为固定结构,仅采用单个压紧气缸压紧,气缸连接减压阀42和压力气源41,由压力气源提供压紧力,通过控制通入气缸的气体压力,有效控制电堆的压紧力,模拟运行工况,并且可以在测试中调整减压阀的出口压力调整预紧力。压紧装置采用上下平面结构,将准备检测的单个单电池(双极板2个+mea n 个)或多个(n)单电池(双极板n+1个+mea n个)叠放入压紧装置内,形成等检测的小型电堆及其各腔体。压紧装置采用卡扣接头、快插接头等结构与燃料、空气和冷却腔体相连接。气缸采用绝热的高强度塑料或者金属与塑料材料的复合体制造,提供较好的保温性能,有利于实现小型电堆运行温度的控制。
23.该检测装置还包含用于控制、监测和计算用途的控制软件程序等。
24.参阅图2
‑
5,本发明一种燃料电池电堆的耐压强度检测方法,具体操作如下:启动设备控制系统,检查控制部件和传感器等监测部件是否工作正常。
25.第一步运行冷却腔管路,启动冷却液管路的水泵,开始阶段设置较小的转速,保证冷却水循环并且进口压力控制在50kpa以下,保证节气门全开状态,再按设置要求启动加热器,监控冷却腔进口的温度,通过控制系统控制电堆温度在设定运行范围内。
26.电堆运行温度稳定后,启动燃料腔的电磁阀开始供气,检测进口流量传感器,控制小流量,等待流量稳定后再调节节气门角度提升进口压力,待压力稳定后,然后逐步提升流量和增加节气门开度而提升入口气体压力,流量和压力交替提升至需要的运行参数值。
27.在燃料腔供气和提升气流流量和压力的同时,按相同的操作流程逐步提升空气腔的流量和压力,并且与燃料腔保持压力跟随提升,自至燃料腔和空气腔的压力平衡并且流量和压力符合运行要求。
28.在燃料腔供气和提升气流流量和压力的同时,需要逐步提升水泵的转速和减小节气门的开度,保持冷却液流量适当,保持冷却液进口压力跟随空气腔的进口压力(可以偏低20~50kpa)。
29.等待所有运行参数到达要求测试的范围值后,监测燃料腔前后的流量传感器和空气腔前后的流量传感器,根据前后流量传感器的流量差,计算燃料腔的总泄漏量(燃料腔前端流量—燃料腔后端流量)、空气腔的总泄漏量(空气腔前端流量—空气腔后端流量)、气腔(空气腔+燃料腔)的总泄漏量(燃料腔前端流量+空气腔前端流量—燃料腔后端流量—空气腔的后端流量)。
30.根据测试腔的选择情况,逐步减小节气门的开度,保持流量不变,提升进口压力,实时监测燃料腔的总泄漏量、空气的总泄漏量、气腔的总泄漏量。当燃料腔的总泄漏量、空气的总泄漏量和气腔的总泄漏量等发生突变或者超出设定的泄露范围时,可以判断电堆内部发生泄露,记录下此时的各腔出入口压力、流量和泄漏量,可以精确的判定电堆的耐压压力数值和泄露情况。在每一个压力档位停留适当的时长(如10min等),确认电堆能否长时间耐受压力和耐受压力时间值。
31.本装置可以模拟测试不同电堆运行温度、燃料气体流量、工作压力和湿度下的耐压强度,通过调整装置上的温度、流量、压力等参数值实现精细化测试和分析,可以精确地判读电堆的整堆、各腔的总外漏、空气和燃料腔的窜漏、气体腔与冷却腔的窜漏等。
32.本装置可以调整装置中固定气缸进气减压阀的压力调整,实现精确控制电堆的压堆压力和检测,能够模拟不同压力下的电堆耐压强度和寿命。
33.参阅图6,在测试燃料电池电堆各腔腔体的耐压强度的基础上,该装置还可以用于测试电堆气体(空气和燃料腔)的气体压力交变耐久性测试,流程如下:按在耐压强度基础检测流程启动设备,保证各腔的流量、压力好温度等满足测试要求职,保持压力平衡。根据选择的测试腔(燃料腔和空气腔等),调整节气门开度,根据进气压力的反馈情况,制定合适的压力上限的节气门对应值和压力下限的节气门对应值。按测试的节气门开度上下限值,设置节气门的开度周期性变化,使电堆运行的进口压力周期性交变,持续测试,检测电堆的气腔总泄露、单腔泄露等值,在检测值突变或者超出设计范围时,记录运行的周期数和时间、各腔的压力、流量和温度等。
34.本方案的燃料腔可以采用氮气、氦气等模拟气体或者实际采用氢气等测试,也可以与加湿器、电堆测试台等气源相连接,测试加湿情况下的电堆耐压情况,空气路可以采用空气、氮气,也可以与加湿器、电堆测试台等气源连接,测试加湿情况下的电堆耐压情况。
35.以上所述仅为本发明的较佳实施例而已,并不用以限制本发明,凡在本发明的精神和原则之内所作的任何修改、等同替换或改进等,均应包含在本发明的保护范围之内。