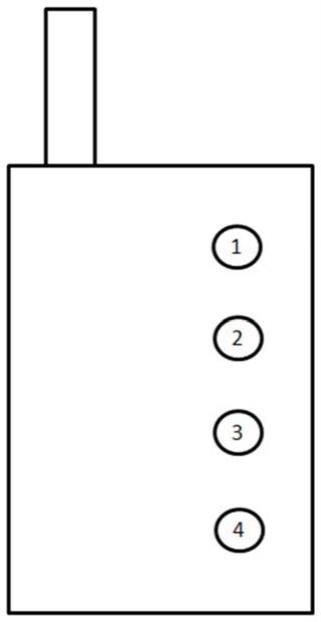
1.本发明涉及一种锂离子电池批产质量问题规避方法。
背景技术:2.随着锂离子电池在3c领域、动力电池领域和储能电池领域的应用越来越广泛,国内外锂离子电池生产厂家在生产过程中通常实行批量滚动生产的模式,如何规避锂离子电池批产质量问题成为重点关注的对象。
3.发生锂离子电池批产质量问题的原因除了原材料因素外,主要有两大类原因,一类是极片质量问题,有可能是在制浆、涂布、辊压、分切、模切等极片制造过程中导致的极片本身的缺陷;另一类是单体装配、测试过程中引入的问题,包括松紧比不恰当、极片组对齐情况不满足要求、化成制度不适用而导致的异常现象。
4.如果在批产时才发现极片质量、单体装配工艺、测试条件存在问题,导致整个批次不满足指标要求,造成锂离子电池的批次性报废,将会给生产厂家带来巨大的损失。所以为了规避锂离子电池批产质量问题,在批产前有必要抽取一定量的正极片和负极片,按照工艺文件和工艺流程进行单体装配、注液化成后形成锂离子电池(以下简称“先行件”),对其开展性能验证,并给出能否按照先行件工艺状态开展批产的结论,将损失控制在极片层面,提高了锂离子电池的可靠性,且避免了不必要的损失。因此,开发出一种锂离子电池批产质量问题规避方法具有较大的实践意义。
技术实现要素:5.本发明的目的在于:提供一种锂离子电池批产质量问题规避方法,该方法通过每批次锂离子电池的先行件制作、电性能测试及拆解后极片表面状态观察、检测,验证了极片组与电池壳之间的松紧比是否恰当、当前的化成制度是否适用、极片组对齐情况是否满足要求,并给出能否按照先行件工艺状态开展批产的结论,有效避免锂离子电池层面的批次报废,将损失控制在极片层面,避免了不必要的损失,进而提高了锂离子电池的可靠性。
6.本发明的技术方案是:一种锂离子电池批产质量问题规避方法,包括以下步骤:
7.1)正、负极片批产结束后,对该批正、负极片的重量、含水量进行检验,具体参数及指标要求可根据不同锂离子电极材料、蓄电池容量进行选择,如果参数符合要求,则进入下一步工序,如果不符合要求,将该批次极片产品进行报废处理或作为试验产品;
8.2)从正极片中抽取两组极片,分别为j
正1
和j
正2
,从负极片中抽取两组极片,分别为j
负1
和j
负2
,抽取的极片从所有极片卷模切所得到的极片中随机抽取,且从每个极片卷模切所得到的极片中抽取的极片数量相当;
9.3)对抽取的j
正1
、j
负1
中的每片极片进行厚度测量,根据每片极片的厚度测量结果计算正、负极片厚度的平均值;
10.4)叠片前计算极片组的松紧度,松紧度=(正极片厚度
×
正极片数+负极片厚度
×
负极片数+隔膜厚度
×
隔膜层数+衬套厚度)/电池壳内腔厚度,根据松紧度的要求确定每只
先行件所需的正、负极片数量j
正3
、j
负3
;所述先行件是指批生产前抽取一定量的正极片和负极片,按照工艺文件和工艺流程进行单体装配、注液、化成、容量测试后形成的锂离子蓄电池;
11.5)在抽取的j
正2
、j
负2
极片中,挑选出几组j
正3
数量的正极片及j
负3
数量的负极片组进行称重,其重量应满足生产厂家要求;
12.6)按照锂离子电池工艺过程进行先行件装配、注液、化成、容量测试;
13.7)对锂离子电池以恒定电流i1充电至生产厂家规定的充电截止电压v0,搁置时间t0;
14.8)对锂离子电池以恒定电压v0充电至电流下降到i2,搁置时间t1;
15.9)判读首次化成效率及容量测试结果,并对锂离子电池进行拆解,观察、检测极片的表面状态,以判断松紧比是否恰当、极片组对齐情况是否满足要求、化成制度是否适用、是否存在其他异常情况等,给出能否按照先行件工艺状态开展批产的结论;
16.10)如果步骤9)的测试结果、极片表面状态无异常,则可以按照先行件工艺状态开展批产,如果步骤9)的测试结果、极片表面状态异常,开展复查和试验工作,同时不允许开展批产,待查明原因后需重新制作先行件,直至先行件拆解后极片的表面状态无异常后方可进行批产,若因极片本身批次性问题导致先行件测试结果、拆解后极片的表面状态始终存在异常,则对该批次极片进行报废处理。
17.所述步骤1)中正极片重量为1.0g~6.0g,负极片重量为1.0g~4.5g,正负极片的含水量小于100~150ppm。
18.所述步骤2)中j
正1
、j
负1
为30~50片,j
正2
、j
负2
不小于制作先行件所需的极片数量。
19.所述步骤3)中,对抽取的j
正1
、j
负1
中的每片极片进行厚度测量时,厚度测量点为3~5个,且包含极片长度方向的上、中、下位置。
20.所述步骤4)中,松紧度在0.93~0.98范围内,其中正极片数量为(40~110)
±
2片,其中负极片数量为(41~111)
±
2片,且负极片应比正极片多一片,其中隔膜层数为正、负极片数及隔膜缠绕层数之和。
21.所述步骤5)中,正负极片组的组数与先行件数量一致,为3~5组,其中正极片组重量为30g~600g,其中负极片组重量为20g~400g。
22.所述步骤6)中,先行件的数量为3~5只,装配方法、注液量、化成方法可以根据不同电池结构、不同锂离子电极材料特性、不同容量进行选择。
23.所述步骤7)中,i1为c/5~c/3,v0为4.1v~4.2v,t0为10~30min。
24.所述步骤8)中,i2为i1的1/5~1/2,t1不大于5天。
25.所述步骤9)中,判读首次化成效率及容量的指标要求应根据不同的锂离子电池电极材料特性及不同容量来确定,其中观察、检测极片的表面状态,包括:1)负极片表面有无目视可见白斑;2)正极片边缘是否完全被负极片包络;3)极片活性物质粘结力是否良好;4)是否存在其他异常情况。
26.本发明的有益效果是:本发明提供的一种锂离子电池批产质量问题规避方法,通过每批次锂离子电池的先行件制作、电性能测试及拆解后极片表面状态观察、检测,验证了极片组与电池壳之间的松紧比是否恰当、极片组对齐情况是否满足要求、当前的化成制度是否适用,并给出能否按照先行件工艺状态开展批产的结论,为批产的极片组结构组成和
工艺状态提供依据或指导,有效规避了锂离子电池生产过程中的批产质量问题,避免了不必要的损失,进而提高了锂离子电池的可靠性。
附图说明
27.图1为极片的厚度测量点示意图。
28.图2为锂离子电池先行件拆解后负极片。
具体实施方式
29.以下结合附图和具体实施例对本发明提出的锂离子电池批产质量问题规避方法作进一步详细说明。
30.本发明方法包括如下步骤:
31.步骤1正、负极片批产结束后,对该批正、负极片的重量、含水量等参数进行检验,具体参数及指标要求可根据不同锂离子电极材料、蓄电池容量进行选择,如果参数符合要求,则进入下一步工序,如果不符合要求,将该批次极片产品进行报废处理或作为试验产品;其中正极片重量为1.0g~6.0g,负极片重量为1.0g~4.5g,正负极片的含水量小于100~150ppm,本实施例中,正极片重量为4.80g~5.01g,负极片重量为3.36g~3.45g,正极片的含水量为14.8ppm,负极片的含水量为13.5ppm;
32.步骤2从正极片中抽取两组极片,分别为j
正1
和j
正2
,从负极片中抽取两组极片,分别为j
负1
和j
负2
,抽取的极片应尽量体现随机性和代表性,应从所有极片卷模切所得到的极片中随机抽取,且从每个极片卷模切所得到的极片中抽取的极片数量相当,其中j
正1
、j
负1
为30~50片,j
正2
、j
负2
应不小于制作先行件所需的极片数量,本实施例中,j
正1
、j
负1
均为30片,j
正2
、j
负2
均为240片;
33.步骤3对抽取的j
正1
、j
负1
中的每片极片进行厚度测量,根据每片极片的厚度测量结果计算正、负极片厚度的平均值,其中每片极片的厚度测量点应为3~5个,且应包含极片长度方向的上、中、下位置;本实施例中,每片极片的厚度测量值为4个,正极片厚度的平均值为135.6μm,负极片厚度的平均值为167.8μm;
34.步骤4叠片前计算极片组的松紧度,松紧度=(正极片厚度
×
正极片数+负极片厚度
×
负极片数+隔膜厚度
×
隔膜层数+衬套厚度)/电池壳内腔厚度,根据松紧度的要求确定每只先行件所需的正、负极片数量j
正3
、j
负3
,其中松紧度应该在0.93~0.98范围内,其中正极片数量为(40~110)
±
2片,其中负极片数量为(41~111)
±
2片,具体数量根据不同锂离子电极材料特性、不同容量进行选择,且负极片应比正极片多一片,其中隔膜层数为正、负极片数及隔膜缠绕层数之和;本实施例中,松紧度为0.959,正极片数量为76片,负极片数量为77片;
35.步骤5在抽取的j
正2
、j
负2
极片中,挑选出几组j
正3
数量的正极片及j
负3
数量的负极片组进行称重,其重量应满足生产厂家要求,其中正、负极片组的组数与先行件数量一致,为3~5组,其中正极片组重量为30g~600g,其中负极片组重量为20g~400g,具体重量根据不同锂离子电极材料特性、不同容量进行选择;本实施例中,分别挑选出3组正、负极片组,正极片组重量分别为372.72g、372.69g、372.88g,负极片组重量分别为261.75g、261.71g、261.68g;
36.步骤6按照锂离子电池工艺过程进行先行件装配、注液、化成、容量测试,其中先行件的数量一般为3~5只,其中装配方法、注液量、化成方法可以根据不同电池结构、不同锂离子电极材料特性、不同容量进行选择;本实施例中,先行件数量为3只;
37.步骤7对锂离子电池以恒定电流i1充电至生产厂家规定的充电截止电压v0,搁置时间t0;
38.步骤7所述恒定电流i1的大小可以根据锂离子电池容量进行选择。设锂离子电池容量为c(单位:ah),则所述恒定电流i1的大小可为c/5~c/3(单位:a),本实施例中,所述锂离子电池容量为30ah,所述恒定电流i1的大小为6a。所述充电截止电压v0可为4.0v~4.2v,可以根据不同的锂离子电池电极材料特性进行选择,以使所述锂离子电池接近满电态,本实施例中,所述充电截止电压为4.1v。所述搁置时间t0可为10~30min,本实施例中,所述搁置时间为t0为10min。
39.步骤8对锂离子电池以恒定电压v0充电至电流下降到i2,搁置时间t1,其中i2约为i1的1/5~1/2,其中t1应不大于5天;
40.步骤8所述充电截止电流i2约为i1的1/5~1/2,以进一步使锂离子电池充至满电态,本实施例中,所述充电截止电流i2为0.05c。所述t1应不大于5天,本实施例中,t1为1天;
41.步骤9判读首次化成效率及容量测试结果,并对锂离子电池进行拆解,观察、检测极片的表面状态,以判断松紧比是否恰当、极片组对齐情况是否满足要求、化成制度是否适用、是否存在其他异常情况等,给出能否按照先行件工艺状态开展批产的结论;其中判读首次化成效率及容量的指标要求应根据不同的锂离子电池电极材料特性及不同容量来确定,本实施例中,首次化成效率应不低于85%,容量应不低于33ah;其中观察、检测极片的表面状态,包括:1)负极片表面有无目视可见白斑;2)正极片边缘是否完全被负极片包络;3)极片活性物质粘结力是否良好;4)是否存在其他异常情况。
42.步骤10如果步骤9的测试结果、极片表面状态无异常,则可以按照先行件工艺状态开展批产,如果步骤9的测试结果、极片表面状态异常,应开展复查和试验工作,同时不允许开展批产,待查明原因后需重新制作先行件,直至先行件拆解后极片的表面状态无异常后方可进行批产,若因极片本身批次性问题导致先行件测试结果、拆解后极片的表面状态始终存在异常,则对该批次极片进行报废处理。
43.图1为极片的厚度测量点示意图,每片极片的厚度测量值为4个,包含极片长度方向的上、中、下位置。
44.图2为锂离子电池先行件拆解后负极片,先行件完成化成及容量测试后充电至4.1v,进行满电态拆解,观察负极片表面状态,发现负极表面呈现比较均匀的深褐色、无白斑,正极片边缘完全被负极片包络。
45.显然,本领域的技术人员可以对本发明进行各种改动和变形而不脱离本发明的精神和范围。这样,倘若本发明的这些修改和变型属于本发明权利要求及其等同技术的范围之内,则本发明也意图包含这些改动和变型在内。