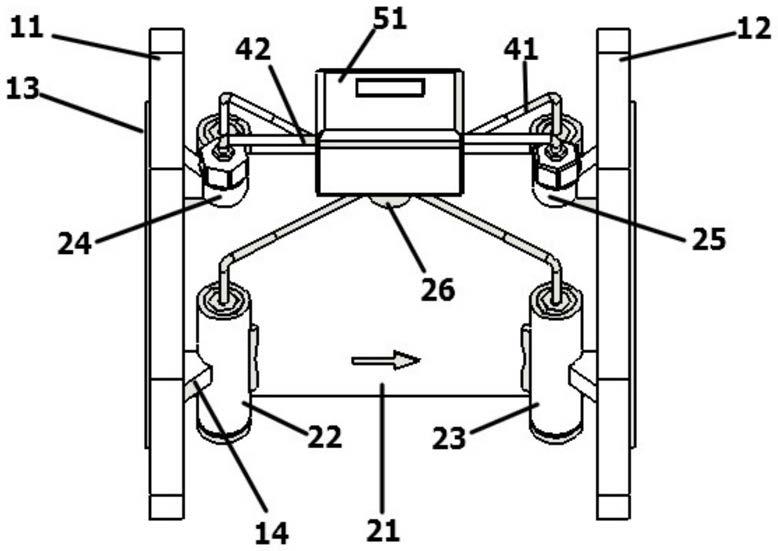
1.本发明隶属流量计量设备的技术领域,具体涉及一种立柱式换能器分层布局的多声道大口径超声波水表。
背景技术:在步入物联网大数据及人工智能与工业自控时代,对于工业及民生水、热、燃气供给计量领域,由全电子模式流量计逐步取代机械式或机电组合模式流量计,已成不可逆转的大趋势。
2.按照实际应用所需,流体计量行业或场合期待兼容各口径规格范围、低压损、高精度、高可靠性、无磨损器件、耐久性及经济性的标准流量计量器具。目前,在世界范围内全电子流量计量应用最广的为电磁流量计以及后起之秀的超声波流量计。
3.超声波流量计是伴随其时差计时芯片(2012~2017年,国际上ams、d-flow、ti等公司先后推出了较先进的时差计时芯片,目前,其分辨率都已达到5~10ps,完全满足了水计量应用需求)的技术突破而崛起的。对比电磁流量计,超声波流量计是通过时差数字信号进行采样的(而电磁流量计则是通过模拟信号采样的)。以水表为例,它具有突出的技术优势:更小的始动流量(如可测量流速0.8~1mm/s的液体)、更宽的量程比、能以声波主动测量过程时差、换算成流体流速及温度并同步对计量的体积变化进行补偿(对此,电磁流量计则需要安装温度计)、大口径多声道的测量具有更高精度及安全性(而电磁流量计只有一对线圈和相应电极,有线圈故障即得报废)、可测量各种低粘度液体(电磁流量计不能测量低电导率液体,如纯净水),另外,对于燃气等气体亦可测量/计量(电磁流量计则不能测量气体流量)。
4.超声波水表升级改进的技术发展方向与原则需要明确界定。通常,流量计的性能指标为计量精度和量程比,计量精度为流量计流量计量值与流量实际值之比,提高流体流动稳定性和批量生产一致性是决定计量精度的重要条件;量程比为在流量计计量精度保证下,常用流量与最小流量之比,体现了可精确计量的范围,增大超声波换能器间的有效距离是提高量程比的必要条件。显然,计量精度越高、量程比越大,则流量计的计量性能就越好。
5.近几年,计量行业对于超声波流量计的实践应用有较大的提升。超声波流量计的构成,除了时差积算电路,还有换能器、换能器布局方式及流道结构等,前者性能决定着可测流量的最小量值,后者整体架构决定着超声波流量计的综合性能和品质。以水表为例,特别是按照水表新标准的约束,业内明确了超声波水表的技术发展方向,其技术导则归纳为如下十条:(1)声程最大化原则:为使超声波水表具有大的量程比,对于大口径流量计,特别是水表,应采用超声波换能器之间声程最大化模式。因为对水表而言,大量程比是贸易结算极其重要的指标,也是水表最主要的技术指标,这点与工业流量计截然不同。例如,某生产厂,白天生产时间的用水量是夜晚用水量的500倍,如果流量计量程比低(比如量程比=200),那么,要兼顾白天大流量段的计量,就必然舍去对夜间小流量用水量段的计量。换句
话说,流量计可能在小流量情况下无法计量或计量误差很大(精度值偏负,如目前旋翼式机械水表),这就必然造成供水方计量损失。要使得超声波水表具有大量程比,做到公平贸易结算,就应将超声波水表的两个换能器间距连线在主管内水流方向的投影距离最大化,以获得较大的量程比及较小的始动流量,(对于水表,中国国标于2018年将量程比或流量比的最大值提升至=1000)。
6.(2)换能器间对射式安装原则:对射式安装的声波信号由一对换能器间相互直接发、收,这样有效信号幅值就最强。大口径流量计尺寸较大,为了保障信号接收强度,换能器应选择对射式安装模式。在换能器声波反射式安装模式情况下,因有一个或数个反射面,声波反射传递有能量损耗(反射面足够大时,理想状态的反射面声能损耗10~20%,一般不至于影响计量),特别是当反射面有角度偏差或使用后结垢,其能量损失就可达40~60%,这将严重影响正常计量。所以,近几年,大口径流量计基本淘汰了换能器间声波反射收、发模式。
7.(3)多声道原则:为使大口径超声波水表具有高的计量精度和可靠性,大口径超声波流量计应采取多声道模式(即多组换能器)。这是因为,对射多声道换能器模式,除了能对流体在管道内不同层面进行分别计算,提高计量精度和准确性外,多声道还是计量可靠性的重要保障(电磁流量计的励磁线圈如果断路,流量计就会报废;而多声道超声波流量计,即便有一对或多对换能器损坏,只要保留一对工作,也能进行流量计量)。
8.(4)内管壁完整性原则:在尽量做到有效声程最大化的前提下,要取得量程比同步提升的必要条件是流量计流量管内壁的平顺与完整。即为提高超声波流量计的计量精度和减小流体阻力,应使流量计内管直通和保证内管壁完整性。当一对换能器的安装设置与水流方向成一角度时,因为要构建对射通道,所以流量计流道表面必须切割出声道,所以必然出现凹凸结构。如果斜度或面积较大,会产生流体流动紊乱,从而导致小流量的计量精度偏差较大(大、小流量都有影响,小流量受影响更为明显),按照量程比的定义(下文有详细描述),由于不稳定即误差较大时,只能通过将其值提高来换得它的稳定,这将导致上述比值减小,量程比会大幅降低,因此,在扩大一对换能器间声程的同时,必须解决不能严重损坏流道,才能保障有效量程比。另外,内壁损伤严重还会导致流量计的一致性差。
9.(5)先进制造工艺原则:为降低制造成本和方便制造,应采取优良制造工艺,使大口径超声波水表具有高的计量精度和一致性与可靠性。尽量不使用成本高、制造流程复杂、精度低的铸造工艺来加工生产流量计管段,而应采用拉伸或锻造成型的成品管段焊接、加工制造。因为用铸造工艺制造的管段,除了管壁较厚(薄管壁不易浇铸,容易有沙眼)成本高以外,其管内径一致性相差较大(有缩径时,内孔加工困难),这使得大口径的流量标定费工费时,每个流量计基表都要单独修正补偿。
10.(6)低压损原则:流量计通道尽量不要有较大的缩径,以减小流体流动的压力损失。为了克服声程短,即量程比低的劣势,目前许多斜插式流量计都要缩径,有些甚至将流量计流道做成扁腔,如专利授权公告号 cn 202083425 u,以提高相对流速(因为时差芯片所能计算的最小有效时差是定值,为了得到有效计算,当这一最小值达不到时,提高流速就能提高时差值),这样做的后果除了增大了流量计的压损以外,还会带来在常用流量或过载流量时,由于过度缩径造成流体局部流速过快,从而产生水白化现象(即少部分水
被流道汽化),其结果会导致流量计停止计量(含气水的声速会大幅降低,时差值产生紊乱),这就是为什么许多大口径超声波水在大流量情况下不能计量的原因。
11.(7)一致性原则;大口径流量计管体及换能器安装,即流道加工与换能器组件安装工艺须有高的精度和一致性(铸造管体无法做到高度一致性),它决定了流量计批量生产的品质,此项水平,决定流量计等级水平及在其标定时是否省时省力。
12.(8)管体密封安全原则:较大口径流量计,在解决管体密封时,若采用与管径相同较大尺寸的密封圈,安装难度大,密封效果存在隐患。所以,尽量采用较小尺寸的多级密封方式,以保障其密封的可靠性、耐久性。
13.(9)适配性原则:方便安装压力传感器及温度传感器(适应不同应用,如供热计量、气体计量)。
14.(10)结构简单、方便装配原则:结构简约化、安装有唯一的确定性,从而整体易装配,且能保障流量计又稳定可靠,且有高的一致性。
15.对照上述超声波水表的十条技术导则,现有技术仍然存在缺陷或不足。
16.超声波水表的斜插式换能器安置方式,声程短、声道少、斜孔加工精度要求高:如专利授权公告号cn 201993129 u为斜插式,两换能器连线在管段内水流方向的投影距离很短,与技术导则(1)不符;另外在口径较小时管外端无空间安置较多声道,与技术导则(3)不符;流道内有换能器凸出部分,与技术导则(4)不符,对安装换能器的斜孔角度要求很高,偏移微小角度,声波接收强度大幅减少,因此加工有难度。
17.超声波水表的立柱式换能器的安置方式,它相对于斜插式,声程有所加长,得到较大改善,声道数也比斜插式要多并且方便安装,如专利授权公告号cn 208921195 u。但这种柱状换能器安装结构将柱体排列在管道两侧,由于换能器间连线的对射模式也与水流方向有夹角,为了保障一对对射换能器声道畅通,所以不得不切去较大宽度的管体通道内壁,造成了内部流道的破坏(如该专利附图3);又如专利公告号cn 202770480u,图2,其将换能器安装柱凸出于流道表面(换能器柱凸出,但换能器位置流道仍然有较大凹陷),这种流道的凹凸在流速较低时产生紊流,其结果是小流量流动不稳定,流量计的测量精度低,对满足一定计量精度要求的流量计最小流量影响较大,从而降低了流量计的量程比,这与技术导则(4)不符。对应流道内壁的损坏程度而言,立柱式安装方式比斜插式安装方式要严重的多;另外,这种模式目前只能铸造成型,效率低,一致性差,成本较高,与技术导则(5)不符。
18.超声波水表的内衬斜插式换能器的安置方式,是一种较新模式,申请公布号cn 111121895 a比起前两种模式无论是声道数量、声程、流道完整性及壳体制造方便程度(可不用铸造,直接用成品管焊接成型即可)都有所提升。但这种模式亦有弊端:由于换能器安装在内衬上,两侧环形排布,如果在内衬上直接封装换能器,换能器的孔位由于是大斜角及环形分布,所以封装难度很大,如果有个别封装失败就整管报废;如果用独立换能器分立安装,由于内衬厚度有限,孔眼斜度大,空间狭小,密封及固定较困难。又由于,换能器安装内衬厚度有限,随着换能器间距的拉长,对射换能器安装孔倾斜度就越大、孔边沿就越薄,安装空间就更受限制,所以一对换能器的间距不可能在有限的管长情况下,拉开至最大,相对的声程无法做到最大化。专利所示,这种模式采用与管内径相同的大密封圈将内衬与金属管内侧密封,耐久性及安全性无法保障,与技术导则(9)不符。此解决方案是将整体内衬与管体套管内侧整体密封,所以,若要在管体上安装温度或压力传感器,有一定难度,有悖于
技术导则(10)。
19.综上所述,对于大口径超声波水表,现有技术还不能符合上述超声波水表的十条技术导则,尤其在大量程比(大声程)方面还存在许多不足之处,亟待克服和改进。
20.对流量计以及超声波水表而言,计量的高精度和大量程比是最为重要的两大技术指标,如何按照超声波水表的十条技术导则,提出一个大口径超声波水表,正是本文要实现的技术目标。
技术实现要素:21.从上述对现有技术的超声波水表已有专利分析可知,(1)斜插式换能器安置,声程短、声道少、斜孔加工精度要求高,其中,声程短是其无法改变的较大缺陷;(2)内衬斜插式的换能器安装在内衬中,由于内衬厚度有限,所以兼顾密封考虑,一对换能器间的有效声程虽大于斜插式,但其扩展量有限,原因是随声程拉长,换能器安装孔斜度增加,换能器密封更加困难,甚至无法密封,所以,这种模式的长声程与换能器固定及密封的矛盾难以解决;(3)立柱式换能器安装,其优点是在保障较大声程(安装换能器的立柱可靠近法兰,只要能满足固定即可)的同时,立柱式也能极大方便多声道换能器的安装。但目前立柱式出现的弊端是:a. 当一对换能器的安装设置与水流方向成一角度时,因为要构建对射通道,所以流量计流道表面必须以安装柱为参考,切割出对射声道,两个换能器间的距离越大,斜度就越大,对管壁切割的越严重(对于这点,比换能器斜插式安装要严重的多),所以必然出现凹凸结构。如果斜度或面积较大,会产生流体流动紊乱,从而导致小流量的计量精度偏差较大(大、小流量都有影响,小流量受影响更为明显),按照量程比的定义,由于不稳定即误差较大时,只能通过将其值提高来换得它的稳定,这将导致上述比值减小,量程比会大幅降低,这就是换能器立柱式安装的致命缺陷。
22.b.换能器安装柱与在管体侧面的安置位置不正确,如专利公告号cn 202770480u,图2,其将换能器安装柱凸出于流道表面会导致湍流产生。以上不当因素会导致以换能器柱作为一对对射换能器通道,将水表管体内腔切割,使得管体内壁损伤严重,严重影响小流量的稳定性,从而造成量程比下降较大,另外,考虑到铸造需要方便脱模原因,所以对流量计流道内腔凹陷损伤较严重,这就导致立柱式换能器安装模式的流量特性较差(受紊流影响,主要表现为小流量稳定性差)。但实测量程比低(但仍比斜插式高一倍左右)。
23.c. 金属壳体都是采用铸造完成,成本高,内腔尺寸误差大,一致性差,目前为止,没有采用焊接成型;d.沿用现在常用的1mhz凸形换能器,尺寸大,其在换能器安装柱上安装的方式为用金属板压住、螺丝固定的形式,所以只能用较粗的换能器安装柱安装,用这种方式通常安装柱的直径为30mm。如专利授权公告号cn 208921195 u中的图5所示;综上所述,要获得较高的量程比,换能器立柱式安装要解决的难题是在将一对换能器安装柱(换能器)距离拉开的同时,解决对射声道对流量计管体内壁的严重凸凹切割损伤。因此,如果能成功地克服立柱式换能器安置方式这一结构性弊端,能对其进行显著的技术提升,将会在计量应用领域有很大的实用价值和应用前景。
24.鉴于现有技术所存在的弊端及不足,本发明针对上述立柱式换能器布局模式与结
构进行显著的技术升级改进,提出一种立柱式换能器分层布局的多声道大口径超声波水表。
25.流量计的性能指标为计量精度和量程比,计量精度为流量计的流量计量值与流量实际值之比,量程比为满足一定计量精度要求的常用流量与最小流量之比,体现了可精确计量的范围。显然,能抑制水流过程湍流影响、计量精度越高、量程比越大,则流量计的计量性能就越好。
26.本案对超声波流量计两个换能器之间的声程与量程比的关系推导如下:在水计量领域,量程比定义为,其中,为对应某管径下的常用流量,它是一个给定值;为满足一定计量精度要求的最小流量(比如二级流量计的计量精度为
±
5%)。
27.本文经深入分析与推导,得出了一个重要的结论:对通过流量计管路内的流体而言,所计量的始动流量(即流量计可感知计量的最小流量)越低(对应其流速就越低,而与超声波流量计的时差芯片分辨率及流量计的管路结构有关),与此对应,也成比例地对应变低(即对应的最小流速就变低)。通常,在实际应用中,其经验值是(随超声波流量计电路及换能器产生总体零漂及流量计管路水阻设计不同而不同)。由此,可以导出在某个口径下(流过流量计管路的与所用的时间间隔相等),量程比与两换能器间距之间的关系为:上式中,为某口径流量计的常用流量,为与相对应的流量计管路内流体的流速,为满足一定计量精度要求的最小流量,为与相对应的流量计管路内流体的流速,对某口径流量计而言,和为常量(选定值),为圆周率,为流量计管路的内半径,为计量用时,为超声波流量计管路内两换能器对射面之间的间距,为两换能器之间连线在流量计管路水流方向的夹角(为锐角,当时,两换能器连线与水流方向一致,, 为与流量计的计量时差、声速有关的已知量,为与流量计的计量时差、声速有关的已知量,令= ,为常数,而通过超声波流量计时差公式计算得出,即,因而,在具体计算时,按照代入。由上面的关系式可得出如下结论:增大两换能器间在流量计管路水流方向的投影距离,就可有效提高流量计的量程比,对此结论的应用需要特别注意的是:流量计管路即流量计内管要尽量做到没有较大的凹凸不平,这样才能使流量计内管的小流量稳定性程度高,从而才能保证
稳定。
28.本发明遵从本案提出的十条技术导则,从结构和安装模式上完全克服目前立柱式换能器布局模式和结构上的缺陷,即目前立柱式换能器布局模式的流量计管内壁被凹凸损伤严重的主要原因是换能器的直径大,换能器安装柱的直径亦大、换能器柱安装位置也需要正确调整、换能器对射面的有效直径与产生平面超声波的关系需要认清;另外,铸造模式造成管内一致性差(特别是流道严重切割)。因此,这种模式情况下,如果为了获得较大的量程比,即两换能器柱间距离越大,为了保证两换能器面能对射,那么,流量计管内壁损害就越严重。为了克服这种缺陷,本案提出本发明的技术方案如下:(1)为了减小换能器安装柱的直径,故采用频率2mhz或4mhz、陶瓷谐振片直径为8mm,封装后直径10mm的等径换能器(常规1mhz凸形换能器外径φ17mm
×
φ21mm),这样就显著减小了换能器柱的结构尺寸;(2)换能器不采用常规“凸”结构形,即前端小后端大的形状(这是为了便于在换能器前端加密封圈密封),而是采用上下一致的等径筒形结构及以下的密封方式,做到换能器前后端直径相等,从而显著减小换能器尺寸以及换能器安装柱的尺寸;(3)换能器与换能器安装柱孔间采用胶粘+激光焊接的安全密封方式,而不是按照传统用金属板及胶圈压紧螺丝固定的模式(如专利授权公告号cn 208921195 u中图5);(4)换能器安装柱与流道内腔的最近距离保留1mm结构间距(安装柱不破坏流道,不会如专利公告号cn 202770480u,图2,凸出到腔体流道内);(5)根据换能器产生超声波的原理,一对对射换能器的对射通道尺寸做到8mm最为恰当,而不是现在大多数采用的30mm(按照目前1mhz凸形换能器外径φ17mm
×
φ21mm所形成的安装柱直径尺寸约30mm。故,都是按照安装柱30mm来切除内腔表面的对射通道宽度);(6)换能器分层安装,如4声道就安排4层(目前模式是对称的,即4声道的换能器安排在两层内),这样计算精度更高;(6)水表流量计管体采用激光焊接形成而不是铸造,这样,标准化生产,不但一致性好,而且成本低。
29.实施以上的技术方案所得到的显著益处是:(1)换能器安装柱可以靠近法兰内侧而不会引起对流道造成切割的严重破坏而引起紊流,这样就大幅提高了实际的量程比;(2)一对对射换能器对流道所产生的切割由宽度约30mm变为8mm,因此在流速较低时,流动特性稳定(流速较高时,更稳定),即会更小,结合(1)大声程的结果,据,所以可得到更大的量程比;(3)换能器分层计算更为合理,精度高;(3)采用法兰、管段焊接模式而不是铸造成型,不但降低了成本,而且提高了流量计基表的一致性。
30.本发明为一种立柱式换能器分层布局的多声道大口径超声波水表,其特征在于:包括法兰、管体套管、换能器柱安装座、换能器安装柱、换能器、换能器引出线固定头及线管、温度传感器固定座、压力传感器固定座、仪表电路盒;大口径水表流量计的两个法兰与流量计中间金属套管间由激光焊接连接;换能器柱安装座、压力传感器座和温度传感器座及仪表盒安装座与金属套管间都用激光焊接连接;将换能器安装柱协同换能器插入靠近法兰内侧的换能器柱安装座内,在一个换能器安装柱上,可安装一个或多个换能器,与另一平行且在另外一侧斜对的换能器安装柱上对应的换能器构成一个或多个超声波流速测量声道;其信号引出线通过金属管通至仪表盒连接柱后,导入电路仪表盒内,协同压力传感器及温度传感器,构成了立柱式换能器分层安装的多声道大口径超声波水表,在换能器安装柱尽可能的靠近法兰内侧的同时,改进后的管体流道消除了严重的凹凸损伤,管体套管两侧安装的换能器柱,以及其上的成对换能器,均安置在管内流体的不同水平面上,由此,形成
了立柱换能器分层对射模式,可实现多声道、多流层的流量测量;配合压力及温度传感器的数据采集,实现了一种立柱式换能器分层布局的多声道大口径超声波水表;达到了流量计流道通顺、始动流量值最小化、计量量程比最大化、量程范围内有很高的计量精度,确保贸易结算的准确、公平性的效果;所述换能器安装柱安置于安装座内,所述的安装座位于法兰内侧、管体套管外侧,以对称的形式排布;每一个安装座,安装一个换能器安装柱;换能器安装柱由上安装口插入,安装座上口端对换能器安装柱起到转动定位、压紧固定和密封等作用;下口端对换能器安装柱只起到密封和位置定位作用;进一步,上安装口内由两个半圆形槽对准换能器安装柱端帽上对应的两个半圆形凸台,由此,对换能器安装柱进行方向定位;柱上有轴向密封圈及帽内侧槽里的密封圈对换能器安装柱进行侧密封和压紧密封等两种不同方式的密封,有效保证了换能器安装柱的密封安全性;所述内六角外螺纹堵头,结合其下部的弹性垫圈,起到对换能器安装柱端帽的压紧作用;所述外六角堵头盖安装于内六角外螺纹堵头的内六角腔内,用以防止内六角外螺纹柱被外人旋转及也起到美观效果。
31.所述内六角外螺纹帽及其下部延伸一体的套筒,安装于安装座下端口,其下有铜密封垫用于硬密封。内六角外螺纹帽通过其下部延伸的套筒对换能器安装柱下端起到位置定位的作用;为了安全起见,可将所述内六角帽与安装座之间用激光点焊固定(这个固定端以后不用拆卸)。
32.所述引出线管固定帽分别用于换能器固定柱引出线金属管以及压力、温度引出线金属管的固定、密封作用,即将金属引出线管从引出线根部密封且固定;其密封方式是通过旋紧引出线管固定帽,在线管与侧壁间通过垫片压缩密封圈密封。
33.所述的换能器安装柱由工程塑料pps、ppo、ppa、pa66注塑完成,其可获得的益处是:(1)大大降低了金属部件的加工成本;(2)方便添加如图5所示,换能器安装柱端帽内槽里的密封圈(这个位置如采用金属部件很难加工,如专利授权公告号cn 208921195 u中的图5所示,只有一道侧密封);(3)方便将换能器外壳与换能器安装柱孔的边沿通过激光焊接成为一体,形成永久的密封结构(同为工程塑料,可以用激光焊接连接)。
34.由于技术应用水平参差不齐,目前多数厂家生产的超声波流量计仍采用前端直径φ17、后端直径φ21的1mhz换能器,其体积大,换能器在安装柱上安装的方式为用金属板压住、螺丝固定的形式,如专利授权公告号cn 208921195 u中的图5所示;所以只能采用较粗的换能器安装柱安装,为了在柱体上加侧密封槽,用这种方式对应的安装柱的直径通常为30mm。这种型号换能器及安装方式对应安装柱就粗,当一对与水流方向有较小斜角的换能器柱在管道内的距离拉开较大时,如专利授权公告号cn 208921195 u中的图3所示,流量计管内壁将损伤严重;如图7所示,本发明所述换能器为行业标准规定中的频率2mhz或4mhz,直径8mm陶瓷片封装成的外壳直径10mm的等径小型筒形换能器,换能器内部由换能器组件即陶瓷片、pcb及引出线组成,所述的陶瓷片用环氧胶与外壳内底部粘接;外壳后部有u形槽便于引出线在换能器安装柱内走线。
35.所述换能器与换能器安装柱上安装孔之间的连接:在换能器安装柱孔底部涂胶,再将换能器插入固定,待胶干后,用激光对换能器外边沿与换能器安装柱换能器安装内孔沿之间焊接密封。由于换能器在管道内所受是外侧向里的压力,所以,对换能器只受由外部
向内推动的力,故,用胶粘及激光焊接密封不但强度足够而且省去了密封圈,提高了密封安全性。
36.由于换能器在换能器柱上采用了新的安装方案,即本发明所采用的换能器是一直筒形,直径为10mm,这与常规在换能器下面要安装密封圈形式的凸形换能器有较大区别(如专利授权公告号cn 208921195 u中的图5所示),由于筒形换能器上下尺寸一致,加上不采用金属板及螺丝固定,所以,由此所带来的有益效果是,除了采用频率2mhz或4mhz直径较小的换能器陶瓷片外,上、下直径一致的等径筒状结构可以有效地减小换能器安装柱的直径。进一步,本发明采用2mhz换能器及其筒形结构,改进后,可以将1mhz换能器安装柱直径30mm左右,减小至2mhz换能器安装柱16mm。
37.本发明所述的超声波换能器陶瓷片的直径为8mm,据精确实验测试得知,换能器所发出的是指向性很高的平面超声波(声柱),其发出声波的直径就是谐振陶瓷片的发声有效直径(注:即以陶瓷片两个电极镀银面积中较小的面积为基准)。根据这一实验结果,本发明,如图6所示,安装柱整体不外露于流量计管体内侧,所述的换能器安装柱的安装位置与流量计套管内壁间,最小距离保持1mm左右的厚度(管内弧与换能器柱的相切处),其目的是,除了保留换能器能发出超声波8mm部分的通道将管体内壁切开之外,由于换能器柱在管道内不外露,所以其余内壁均保持完整;这样的结构可大幅减少了流量计管体内壁的损伤;例如,选用1mhz的换能器,其安装柱的直径为30mm左右,通常的做法是按照换能器安装柱来切开套管内壁,即切开30mm的通道;如果选择2mhz的换能器,而且按照本案的换能器安装方法,那么换能器安装柱的直径为16mm,换能器有效发出超声波的面积直径为8mm,那么将换能器对射通道在流量计内管壁上切开8mm的缺口即可,这显然比切开30mm的缺口对内壁的损伤小得多。从专利授权公告号cn 208921195 u中的图3可以看出,其切开的宽度就是换能器固定柱的宽度;再如本案附图6所示,切口宽度仅为8mm,所以切口宽度只占前者的27%,即减小了73%,流道损伤大幅减小,解决了小流量的稳定性难题。
38.如附图2所示,本发明对换能器安装柱中的换能器,也进行了合理的成对分层排布安装,对于四通道或更多通道的水表基表而言,管内流体的分层测量越细,测量结果就越精确,这对于时时监测流体在不同层流的流速变化,至关重要。图2中,换能器a、c在一个换能器安装柱上;换能器b、d在一个换能器安装柱上;而成对的a、b、c、d换能器把被测流体截面分为四层,比起目前立柱式常规分为2层的结构,对流体流速的测量,可获得更为精确的结果。
39.与目前立柱式流量计管体的铸造工艺不同,由于本发明对换能器安装柱的安置位置、换能器选型及换能器在换能器安装柱中的安装方式均有较大的调整,根据现在的结构,采用金属套管及换能器安装座用cnc进行标准加工、以激光焊接来完成更为恰当,这样,不但能标准化生产,而且能大幅提高水表基表的一致性,减少后续标定工作以及减少成本(通常,铸造成本比焊接高出一倍或更多)。
40.本发明流量计管体部件的焊接顺序为:先将换能器安装座及压力、温度传感器安装座用夹具固定,激光焊接;最后再将两侧法兰与流量计管体用夹具固定,激光焊接完成。
41.所述温度传感器固定座位于管体套管外侧中部,靠近出水口端法兰内侧。所述温度传感器固定头位于温度传感器固定座上,所述温度传感器固定头通过其下方的铜密封垫圈密封,温度传感器安置在出水端的理由是测温杆不会影响对流体流动的测量。
42.所述压力传感器固定座位于管体套管外侧中部,靠近入水口端法兰内侧,所述压力传感器固定头位于压力传感器固定座上,所述压力传感器固定头通过其下方的铜密封垫圈密封,压力传感器安置在进水端不外露,所以不影响对流体流动的测量。
43.所述仪表盒由螺丝固定于管体外侧中部的固定柱上,其内部有积算电路板、显示屏、电池等,流量及压力、温度信号线管直接联通到仪表电路盒固定柱或仪表电路盒内部,通至积算电路板上。如果需要做ip68防护,可在仪表电路盒内部灌封防水密封胶。
44.综上所述,本发明成功克服了现在立柱式超声波水表的技术缺陷,使超声波立柱换能器布局模式的性能大幅提升,形成了全新结构的和性能卓越的超声波水表,与现有技术相比,本发明具有突出的实质性特点和显著进步,表现为:第一,进行系统性的结构改进,大幅提升立柱式流量计性能。本发明采取换能器安装柱非流道的定位布局、换能器与换能器安装柱间的优化安全密封方式、同径结构的换能器与换能器安装柱的优化适配、立柱式换能器分层布局的多声道结构、以及部件的定位结构和整表的优化布局,使本发明的计量精度和量程比显著提升。通过计算和实验表明,在相同管径、相同流量计管路长度下,本发明比现有技术的立柱式超声波水表,量程比至少提高一倍以上。
45.第二,管体及附件以焊接连接方式,可以容易地扩大声程。即通过在工字形即由两个法兰与管体套管构成的金属管体上,位于法兰内测、管体套管外侧两端,尽量靠近法兰,设置两对相互平行的换能器柱安装座,换能器柱安装在换能器安装座内,在一个换能器安装柱上,可安装一个或多个换能器,与另一平行且斜对的换能器安装柱上对应的换能器构成一个或多个超声波测量声道;由于管体与换能器柱安装座之间是焊接模式,所以只要不影响法兰焊接(换能器柱安装座可先焊接到金属管体对应位置),换能器柱安装座可以尽可能地靠近法兰内侧,由此获得了流量计更大的量程比。
46.第三,对换能器安装柱进行有效的定位、固定及密封。所述的换能器安装柱安置于安装座内,所述的安装座位于法兰内侧、管体套管外侧,以对称的形式排布;换能器安装柱由上安装口插入,上口端安装座对换能器安装柱起到转动定位、压紧固定和密封等作用;下口端对换能器安装柱只起到密封和位置定位作用;进一步,上安装口内由两个半圆形槽对准换能器安装柱端帽上对应的两个半圆形凸台,由此,对换能器安装柱进行方向定位;柱上有轴向密封圈及帽内侧密封圈对换能器安装柱进行侧密封和压紧密封等两种不同方式的密封,有效保证了换能器安装柱的密封安全性;所述内六角外螺纹堵头,结合其下部的弹性垫圈,起到对换能器安装柱端帽的压紧作用;所述外六角堵头盖安装于内六角外螺纹堵头的内六角腔内,用以防止内六角外螺纹柱被外人旋转及也起到美观效果;所述内六角外螺纹帽及其下部延伸一体的套筒,安装于安装座下端口,其下有铜密封垫用于硬密封。内六角外螺纹帽通过其下部延伸的套筒对换能器安装柱下端起到位置定位的作用;为了安全起见,可将所述内六角帽与安装座之间用激光点焊固定(这个固定端以后不用拆卸)。
47.第四,对信号引出线的保护与密封。所述引出线管固定帽分别用于换能器固定柱引出线金属管以及压力、温度引出线金属管的固定、密封作用,即将金属引出线管从引出线根部密封且固定;其密封方式是通过旋紧引出线管固定帽,在线管与侧壁间通过垫片压缩密封圈密封。
48.第五,以新材料制造换能器安装柱。所述的换能器安装柱由工程塑料pps、ppo、
ppa、pa66注塑完成,其可获得的益处是:(1)大大降低了金属部件的加工成本;(2)方便添加如图5所示,换能器安装柱端帽内槽里的密封圈(这个位置如采用金属部件很难加工,如专利授权公告号cn 208921195 u中的图5所示,只有一道侧密封);(3)方便将换能器外壳与换能器安装柱孔的边沿通过激光焊接成为一体,形成永久的密封结构(同为工程塑料,可以用激光焊接连接)。
49.第六,改进换能器结构,使其更适于换能器立柱安装模式。由于换能器在换能器柱上采用了新的安装方案,本发明所采用的换能器是一等径直筒形,直径为10mm,这与常规在换能器下面要安装密封圈形式的凸形换能器有较大区别,由于筒形换能器上下尺寸一致,加上不采用金属板及螺丝固定,所以,由此所带来的有益效果是,除了采用频率2mhz或4mhz直径较小的换能器陶瓷片外,上、下直径一致的筒状结构可以有效地减小换能器安装柱的直径。进一步,本发明采用2mhz换能器及其筒形结构,改进后,可以将1mhz换能器直径30mm左右的安装柱减小至2mhz换能器安装柱16mm。
50.第七,以超声波发声原理,调整声道尺寸结构。本发明所述的超声波换能器陶瓷片的直径为8mm,据实验测试得知,换能器所发出的是指向性很高的平面超声波,其发出声波的直径就是谐振陶瓷片的发声有效直径(注:即以陶瓷片两电极镀银面积中较小的面积为基准)。根据这一实验结果,本发明,如图6所示,安装柱整体不外露于流量计管体内侧,所述的换能器安装柱的安装位置与流量计套管内壁间,最小距离保持1mm左右的厚度,其目的是,除了保留换能器能发出超声波8mm部分的通道将管体内壁切开之外,由于换能器柱在管道内不外露,所以其余内壁均保持完整;这样的结构可大幅减少了流量计管体内壁的损伤;例如,选用1mhz的换能器,其安装柱的直径为30mm左右,通常的做法是按照换能器安装柱来切开套管内壁,即切开30mm的通道;如果选择2mhz的换能器,而且按照本案的安装方法,那么换能器安装柱的直径为16mm,换能器有效发出超声波的面积直径为8mm,那么将换能器对射通道在流量计内管壁上切开8mm的缺口即可,这显然比切开30mm的缺口对内壁的损伤小得多。从专利授权公告号cn 208921195 u中的图3可以看出,其切开的宽度就是换能器固定柱的宽度;再如附图6所示,本案的切口宽度是8mm,所以切口宽度只占前者的27%,即减小了73%,流道损伤大幅减小,提高了小流量的稳定性。
51.第八,提高测量面,对换能器进行分层排布。如附图2所示,本发明对换能器安装柱中的换能器,也进行了合理的成对分层排布安装,对于四通道或更多通道的水表基表而言,管内流体的分层测量越细,测量结果就越精确,这对于时时监测流体在不同层流的流速变化,至关重要。图2中,换能器a、c在一个换能器安装柱上;换能器b、d在一个换能器安装柱上;而成对的a、b、c、d换能器把被测流体截面分为四层,比起目前立柱式常规分为2层的结构,对流体流速的测量,可获得更为精确的结果。
52.第九,克服铸造缺陷,调整结构,采用标准化生产。与目前立柱式流量计管体的铸造工艺不同,由于本发明对换能器安装柱的安置位置、换能器选型及换能器在换能器安装柱中的安装方式均有较大的调整,根据现在的结构,采用金属套管及换能器安装座用cnc进行标准加工、以激光焊接来完成更为恰当,这样,不但能标准化生产,提高生产效率,而且能大幅提高水表基表的一致性,减少后续流量计的标定工作以及减少成本(通常,铸造成本比焊接高出一倍或更多)。
53.第十,方便压力、温度传感器安装。本发明在管体套管外侧中部靠近法兰内侧,进
水口端安装有压力传感器,出水口端安装有温度传感器;所述压力及温度传感器都不影响对流体流动的测量。
附图说明
54.图1 是一种立柱式换能器分层布局的多声道大口径超声波水表外观示意图;图2 是立柱式换能器分层布局结构剖视图;图3 是换能器安装柱及其配件的安装结构爆炸图;图4 是换能器安装柱帽在安装座内的定位结构示意图;图5 是对射安装的换能器在流道内壁的位置通道以及压力和温度传感器结构示意图;图6 是对射安装的换能器柱在流道内与内壁的位置通道示意图;图7是筒形换能器及其结构和组件示意图;图8是换能器安装柱及其配件的安装位置示意图;图中:11.进水口管体法兰;12.出水口管体法兰;21.管体套管;13.法兰密封面;14.加强筋;22、23.换能器安装柱固定座;24.压力传感器固定座;25.温度传感器固定座;244.压力传感器;243、253.铜垫圈;242、252.密封圈;241、251、313.引出线管固定帽;221.外六角堵头盖;222.内六角外螺纹帽;31.换能器安装柱;36.换能器安装柱帽;316.定位凸头;315.换能器安装柱帽密封圈;314.换能器安装柱侧密封圈;312.垫片;311.密封圈;317.换能器安装孔;32.换能器;321.陶瓷片;322.pcb;323.出线u形槽;324.信号线;228.下安装座半圆形凹槽;41.换能器信号线护管;42.压力及温度传感器护管;a,b,c,d:换能器在换能器安装柱上的排布高度位置;211.对射换能器在流量计套管内壁的位置及切口通道;212.换能器安装柱与流量计套管内壁的位置(距离);51.仪表盒;511.显示屏;512.积算电路pcb板;513.电池;514.仪表盒固定螺丝;
具体实施方式
55.下面结合附图和实例对本发明的实施做进一步详细说明。
56.实施例:本实施例是一种立柱式换能器分层安装的多声道大口径dn150超声波水表。
57.如图1所示,本实施例包括法兰11及12、管体套管21、换能器柱安装座22及23、换能器安装柱31、换能器32、换能器引出线固定头241,251和313及线管41和42、温度传感器固定座25、压力传感器固定座24、仪表电路盒51;大口径水表流量计的两个法兰11,12与流量计中间金属套管21间由激光焊接连接;换能器柱安装座22,23、压力传感器座24和温度传感器座25及仪表盒安装座26与金属套管21间都用激光焊接连接;将换能器安装柱31协同换能器32插入靠近法兰内侧的换能器柱安装座22及23内,在一个换能器安装柱31上,可安装一个或多个换能器32,与另一平行且在另外一侧斜对的换能器安装柱上对应的换能器构成一个或多个超声波流速测量声道;其信号引出线通过金属管41通至仪表盒连接柱26后,导入电路仪表盒51内,协同压力传感器244及温度传感器254,构成了立柱式换能器分层安装的多声道大口径超声波水表,在换能器安装柱尽可能的靠近法兰内侧的同时,改进后的管体流
道消除了严重的凹凸损伤,管体套管21两侧安装的换能器柱,以及其上的成对换能器,均安置在管内流体的不同水平面上,由此,形成了立柱换能器分层对射模式,可实现多声道、多流层的流量测量;配合压力及温度传感器的数据采集,实现了一种立柱式换能器分层布局的多声道大口径超声波水表;达到了流量计流道通顺、始动流量值最小化、计量量程比最大化、量程范围内有很高的计量精度,确保贸易结算的准确、公平性的效果;如图2所示,所述换能器安装柱31安置于安装座22及23内,所述的安装座位于法兰内侧、管体套管外侧,以对称的形式排布;每一个安装座,安装一个换能器安装柱;换能器安装柱由上安装口插入,安装座上口端对换能器安装柱起到转动定位、压紧固定和密封等作用;下口端对换能器安装柱只起到密封和位置定位作用;进一步,图4所示,上安装口内由两个半圆形槽228对准换能器安装柱端帽上对应的两个半圆形凸台316,由此,对换能器安装柱31进行方向定位;柱上有轴向密封圈314及帽内侧槽里的密封圈315对换能器安装柱进行侧密封和压紧密封等两种不同方式的密封,有效保证了换能器安装柱的密封安全性;所述内六角外螺纹堵头222,结合其下部的弹性垫圈223,起到对换能器安装柱端帽36的压紧作用;所述外六角堵头盖221安装于内六角外螺纹堵头222的内六角腔内,用以防止内六角外螺纹柱被外人旋转及也起到美观效果。
58.所述内六角外螺纹帽225及其下部延伸一体的套筒,安装于安装座下端口,其下有铜密封垫224用于硬密封。内六角外螺纹帽通过其下部延伸的套筒对换能器安装柱下端起到位置定位的作用;为了安全起见,可将所述内六角帽225与安装座22或23之间用激光点焊固定(这个固定端以后不用拆卸)。
59.如附图2所示,本发明对换能器安装柱中的换能器,也进行了合理的成对分层排布安装,对于四通道或更多通道的水表基表而言,管内流体的分层测量越细,测量结果就越精确,这对于时时监测流体在不同层流的流速变化,至关重要。图2中,换能器a、c在一个换能器安装柱上;换能器b、d在一个换能器安装柱上;而成对的a、b、c、d换能器把被测流体截面分为四层,比起目前立柱式常规分为2层的结构,对流体流速的测量,可获得更为精确的结果。
60.所述引出线管固定帽313、241及251分别用于换能器固定柱引出线金属管41以及压力、温度引出线金属管42的固定、密封作用,即将金属引出线管从引出线根部密封且固定;其密封方式是通过旋紧引出线管固定帽,在线管与侧壁间通过垫片312压缩密封圈311密封。
61.如图3所示,所述的换能器安装柱31由工程塑料pps、ppo、ppa、pa66注塑完成,其可获得的益处是:(1)大大降低了金属部件的加工成本;(2)方便添加如图5所示,换能器安装柱端帽36内槽里的密封圈315(这个位置如采用金属部件很难加工,如专利授权公告号cn 208921195 u中的图5所示,只有一道侧密封);(3)方便将换能器32外壳与换能器安装柱孔317的边沿通过激光焊接成为一体,形成永久的密封结构(同为工程塑料,可以用激光焊接连接)。
62.由于技术应用水平参差不齐,目前多数厂家生产的超声波流量计仍采用前端直径φ17、后端直径φ21的1mhz换能器,其体积大,换能器在安装柱上安装的方式为用金属板压住、螺丝固定的形式,如专利授权公告号cn 208921195 u中的图5所示;所以只能采用较粗的换能器安装柱安装,为了在柱体上加侧密封槽,用这种方式对应的安装柱的直径通常为
30mm。这种型号换能器及安装方式对应安装柱就粗,当一对与水流方向有较小斜角的换能器柱在管道内的距离拉开较大时,如专利授权公告号cn 208921195 u中的图3所示流量计管内壁将损伤严重;如图7所示,本发明所述换能器为行业标准规定中的频率2mhz或4mhz,直径8mm陶瓷片封装成的外壳直径10mm的等径小型筒形换能器32,换能器内部由换能器组件即陶瓷片312、pcb322及引出线324组成,所述的陶瓷片312用环氧胶与外壳内底部粘接;外壳后部有u形槽323便于引出线在换能器安装柱内走线。
63.如图3所示,所述换能器32与换能器安装柱上安装孔317之间的连接:在换能器安装柱孔底部涂胶,再将换能器插入固定,待胶干后,用激光对换能器32外边沿与换能器安装柱换能器安装内孔317沿之间焊接密封。由于换能器在管道内所受是外侧向里的压力,所以,对换能器只受由外部向内推动的力,故,用胶粘及激光焊接密封不但强度足够而且省去了密封圈,提高了密封安全性。
64.由于换能器在换能器柱上采用了新的安装方案,即本发明所采用的换能器32是一等径直筒形,直径为10mm,这与常规在换能器下面要安装密封圈形式的凸形换能器有较大区别(如专利授权公告号cn 208921195 u中的图5所示),由于筒形换能器上下尺寸一致,加上不采用金属板及螺丝固定,所以,由此所带来的有益效果是,除了采用频率2mhz或4mhz直径较小的换能器陶瓷片312外,上、下直径一致的筒状结构可以有效地减小换能器安装柱31的直径。进一步,本发明采用2mhz换能器及其筒形结构,改进后,可以将1mhz换能器安装柱直径30mm左右,减小至2mhz换能器安装柱16mm。
65.本发明所述的超声波换能器陶瓷片312的直径为8mm,据精确实验测试得知,换能器所发出的是指向性很高的平面超声波(声柱),其发出声波的直径就是谐振陶瓷片的发声有效直径(注:即以陶瓷片两个电极镀银面积中较小的面积为基准)。根据这一实验结果,本发明,如图6所示,安装柱31整体不外露于流量计管体内侧,所述的换能器安装柱的安装位置与流量计套管内壁间,最小距离212保持1mm左右的厚度(管内弧与换能器柱的相切处),其目的是,除了保留换能器能发出超声波8mm部分的通道将管体内壁切开之外,由于换能器柱在管道内不外露,所以其余内壁均保持完整;这样的结构可大幅减少了流量计管体内壁的损伤;例如,选用1mhz的换能器,其安装柱的直径为30mm左右,通常的做法是按照换能器安装柱来切开套管内壁,即切开30mm的通道;如果选择2mhz的换能器,而且按照本案的换能器安装方法,那么换能器安装柱的直径为16mm,换能器有效发出超声波的面积直径为8mm,那么将换能器对射通道在流量计内管壁上切开8mm的缺口即可,这显然比切开30mm的缺口对内壁的损伤小得多。从专利授权公告号cn 208921195 u中的图3可以看出,其切开的宽度就是换能器固定柱的宽度;再如本案附图6所示,切口211宽度仅为8mm,所以切口宽度只占前者的27%,即减小了73%,流道损伤大幅减小,解决了小流量的稳定性难题。
66.与目前立柱式流量计管体的铸造工艺不同,由于本发明对换能器安装柱的安置位置、换能器选型及换能器在换能器安装柱中的安装方式均有较大的调整,根据现在的结构,采用金属套管21及换能器安装座22及23用cnc进行标准加工、以激光焊接来完成更为恰当,这样,不但能标准化生产,而且能大幅提高水表基表的一致性,减少后续标定工作以及减少成本(通常,铸造成本比焊接高出一倍或更多)。
67.本发明流量计管体部件的焊接顺序为:先将换能器安装座22、23及压力、温度传感
器安装座24、25用夹具固定,激光焊接;最后再将两侧法兰11、12与流量计管体21用夹具固定,激光焊接完成。
68.所述温度传感器固定座25位于管体套管21外侧中部,靠近出水口端法兰12内侧。所述温度传感器固定头254位于温度传感器固定座25上,所述温度传感器固定头通过其下方的铜密封垫253圈密封,温度传感器安置在出水端的理由是测温杆不会影响对流体流动的测量。
69.如图5所示,所述压力传感器固定座24位于管体套管外侧中部,靠近入水口端法兰11内侧,所述压力传感器固定头244位于压力传感器固定座24上,所述压力传感器固定头通过其下方的铜密封垫圈243密封,压力传感器安置在进水端不外露,所以不影响对流体流动的测量。
70.所述仪表盒51由螺丝514固定于管体外侧中部的固定柱26上,其内部有积算电路板512、显示屏511、电池513等,流量及压力、温度信号线管41及42直接联通到仪表电路盒固定柱26或仪表电路盒51内部,通至积算电路板512上。如果需要做ip68防护,可在仪表电路盒内部灌封防水密封胶。
71.通过以上例证对本发明一种立柱式换能器分层布局的多声道大口径超声波水表的dn150口径,进行了实施应用说明,但本发明不限于上述具体实施例,凡基于本发明内容所做的任何改动或变形均属于本发明要求保护的范围 。