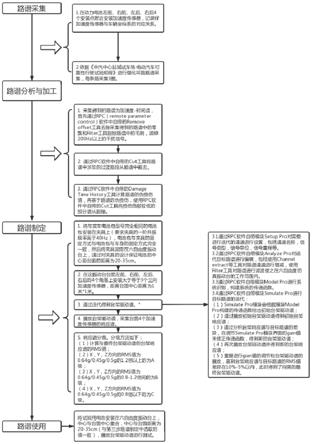
1.本发明涉及动力电池性能测试技术领域,特别是涉及一种动力电池多轴振动通用测试谱生成方法。
背景技术:2.为了验证汽车及其零部件的耐久性能,往往采取路试的方法对其进行测试。但是路试资源较少、成本较高、受天气因素影响较大,对汽车的开发造成了一定的阻碍。所以,作为电动汽车的关键零部件,目前很多汽车制造企业利用可以模拟实车路面激励的多轴仿真振动台对其进行耐久测试。动力电池多轴仿真振动测试一般需要针对某一款车型的动力电池安装点位进行实车路谱采集,基于实车路谱对测试系统进行迭代,使其能够复现动力电池在电动汽车在实车行驶过程中受到的激励。采用多轴仿真振动台对动力电池进行测试的优点很多,如:不需要考虑气候问题、不需要考虑昼夜问题、可以剪切掉过渡路段的无效路谱等,以上优点可以节约开发时间和成本。
3.然而,目前的多轴振动试验方法仍存在如下缺点:
4.(1)为了模拟实车振动激励,需要对测试系统进行迭代操作,使测试样件受测试台架激励产生的响应与实车行驶过程中受到路面激励而产生的响应趋向于一致,该操作复杂性较大,需要专业的人员队伍进行操作。
5.(2)目前的测试流程是针对单一车型的动力电池,即每一次测试都需要单独完成动力电池的实车路谱采集、标准化处理、迭代等流程,这样开发周期将非常的长。
技术实现要素:6.本发明所要解决的技术问题是:针对目前动力电池多轴振动试验存在:迭代操作复杂、效率低,以及测试谱通用性差的两点问题,本发明提供一种动力电池多轴振动通用测试谱生成方法。
7.本发明的设计思路为:动力电车安装位置和安装方式比较单一,都集中在车身下方,通过螺栓与车身连接,具备制定统一的动力电池多轴测试规范的条件。其原理是:动力电池通过多点与车身连接,路面激励通过动力电池与车身的连接点传递到动力电池,路面激励的频率一般在20hz以下,而对车身动态性能影响较大的一阶弯曲振动的频率接近40hz,所以可以默认车身是接近刚性的,由于动力电池不同位置的传感器采集得到的响应加速度有一定的耦合性,样件安装点越接近于刚体,迭代时各个点位的响应才会快速一致地收敛。由于动力电池与车身底部直接连接,几乎不受局部振动影响,合理地设计夹具即可实现不同车型间路谱的通用。
8.本发明解决其技术问题所要采用的技术方案是:一种动力电池多轴振动通用测试谱生成方法,包括以下步骤:
9.步骤1:路谱采集
10.选定某一车型的电动汽车,在电动汽车电池包的不同位置上安装至少三个三向加
速度传感器,并记录好每个三向加速度传感器与车辆坐标系的对应关系,然后对电动汽车进行实车强化坏路路谱采集,获得不同路况下的初始路谱,所述初始路谱为加速度-时间谱;三个三向加速度传感器能够确定一个面,作为主测量传感器,第四个及以上的三向加速度传感器作为过约束,提高其测量的准确性。
11.步骤2:路谱分析与加工
12.首先,去除初始路谱中的零飘和毛刺,滤除掉200hz以上的干扰信号;然后,将初始路谱中涉及的过渡路段从路谱中截去;接着,计算初始路谱的伪损伤值,再基于初始路谱的伪损伤值,将损伤贡献值较低的部分从初始路谱中剔除,即将初始路谱中加速度幅值小于等于峰值2%的部分剔除,从而获得目标路谱;
13.步骤3:台架路谱制定
14.将与步骤1中实车电池包型号完全相同的电池包安装在夹具上,且电池包与夹具的固定方式与电池包与车身的固定方式完全一致,然后将夹具固定在六自由度振动台上,使电池包的中心距六自由度振动台的台面的距离为20-35cm;在六自由度振动台台面的至少三个位置上安装三向加速度传感器,且三个位置不在同一条直线上;三个三向加速度传感器能够确定一个面,第四个及以上的三向加速度传感器作为过约束,提高其测量的准确性。
15.对六自由度振动台加载驱动普,采用三向加速度传感器对六自由度振动台的响应谱进行采集,并将采集到的响应谱与目标路谱进行比较,然后对驱动普进行调整,使六自由度振动台的响应谱趋于目标路谱,直到六自由度振动台的响应谱与目标路谱的rms(root mean square,有效值)值的差异在5%-10%以内,记录此时六自由度振动台的驱动普,并将该驱动普作为该六自由度振动台的最终驱动谱,存储在六自由度振动台上;
16.步骤4:路谱使用
17.当需要对步骤1中所述车型的电池包进行测试时,按照该车型的测试要求,将电池包安装在六自由度振动台上,然后直接选择最终驱动谱中对应的驱动谱加载到六自由度振动台上,由六自由度振动台播放驱动普以模拟不同路况的路谱对电池包进行测试。
18.为了提高最终驱动普的准确性,还包括以下步骤:
19.采用步骤1-步骤3的方法采用其他车型进行初始路谱的采集,然后计算出每个车型对应的目标路谱,并将每个车型的电池包安装在六自由度振动台上,获得采用该六自由度振动台进行测试时的最终驱动普,将不同车型获得最终驱动普均存储在六自由度振动台上,从而形成驱动普库。当需要对某一车型的电池包进行测试时,只需要调用驱动普数据库中的驱动普即可。
20.进一步,还包括对驱动普库进行分级的过程,分级方法如下:
21.计算与最终驱动谱对应的响应谱的rms值,然后根据rms值进行分级,其中,
22.x,y,z方向的rms值分别为0.64g、0.45g、0.5g的1.2倍以上的为a级;
23.x,y,z方向的rms值分别为0.64g、0.45g、0.5g的0.8-1.2倍间的为b级;
24.x,y,z方向的rms值分别为0.64g、0.45g、0.5g的0.8倍以下的为c级;
25.进行电池包测试时,先选择对应的级别,然后再选择该级别下对应的驱动普,从而提高测试的效率。
26.具体的,步骤1中电动汽车的电池包上安装四个三向加速度传感器,分别位于电池
包的左前、右前、左后和右后4个安装点。
27.具体的,步骤3中六自由度振动台的台面上安装四个三向加速度传感器,分别位于台面的左前、右前、左后和右后的4个角上,且三向加速度传感器距离台面中心的距离相同。
28.进一步,步骤3中在使六自由度振动台的响应谱趋于目标路谱时采用了迭代的方法,具体包括以下步骤:
29.步骤3.1:根据目标路谱初步确定其包含的路谱通道,目标路谱包含若干路谱通道,并通过rpc软件自带模块setup pro对需要进行迭代的路谱通道的参数进行设置,所述参数包括但不限于通道名称、信号类型、信号单位和信号量程;
30.步骤3.2:通过rpc软件自带模块analyze pro对目标路谱进行编辑,包括使用channel extract工具对步骤1中路谱通道的数量进行增减,使用filter工具对路谱进行滤波使之在六自由度振动台的工作范围内;
31.步骤3.3:通过rpc软件自带模块model pro进行系统识别,构建测试系统的传递函数,其中,测试系统包括电池包、夹具和六自由度振动台;
32.步骤3.4:通过rpc软件自带模块simulate pro进行目标路谱的迭代:
33.(1)simulate pro模块会根据模块model pro构建的传递函数给出六自由度振动台的初始驱动谱;
34.(2)通过播放初始驱动谱得到六自由度振动台的初始响应谱;
35.(3)分析初始响应谱与目标路谱的差异,再调节simulate pro模块界面的gain值来修正传递函数,得到新的驱动谱,其中,gain值为传递函数的增益值;
36.(4)再次播放新的驱动谱并得到新的响应谱;
37.(5)重复进行gain值的调节和驱动谱的播放,直到六自由度振动台的响应谱与目标路谱的rms值差异在5%-10%以内,此时得到了所需的最终驱动谱。
38.本发明的有益效果是:本方法将包含制定统一的动力电池多轴测试规范的完整流程,通过该方法开发得到统一的台架驱动谱,来避免复杂的路谱开发及迭代工作,由于本方法可以形成规范的测试流程,所以无需样车成型即可先对电池这一关键零部件进行测试。本发明不仅成功解决了动力电池六轴振动测试流程繁杂的问题,最重要的是解决了动力电池六轴测试谱的通用性问题,实现了动力电提前进入研发验证阶段,降低试验难度,提高试验效率,减少研发周期。
附图说明
39.下面结合附图和实施例对本发明作进一步说明。
40.图1是本发明动力电池多轴振动通用测试谱生成方法的流程示意图。
41.图2是中汽中心盐城汽车试验场道路总平面示意图。
42.图中:t1-联接路,t2-直线性能路,t3-外部噪声路,t4-直线制动路,t5-动态广场,t6-舒适路,t7-高速环路,t8-强化耐久路,t9-坡道,t10-干操控路。
43.图3是强化耐久路t8的平面示意图。
44.图中:1.2-混凝土补丁路,1.3-拱形车道,3.5-均匀波浪路,4.1-振动路ⅰ,4.2-混凝土板冲击路,4.3-鱼鳞坑路,4.4-倾斜车道,6.1-比利时路,6.3-振动路ⅱ,6.4-长波路7.2-井盖路,7.3-锯齿路,7.4-正弦坡路,7.5-鹅卵石路,9.1-不规则混凝土路,9.3-溅水
路,10.1-森林路。
45.图4是坡道t9的平面示意图。
46.图5是前9个循环每个循环中里程与加速减速行驶程序(顺时针行驶)示意图。
具体实施方式
47.现在结合附图对本发明作详细的说明。此图为简化的示意图,仅以示意方式说明本发明的基本结构,因此其仅显示与本发明有关的构成。
48.如图1所示,本发明的一种动力电池多轴振动通用测试谱生成方法,包括以下步骤:
49.步骤1:路谱采集
50.1.选定某一车型的电动汽车,在电动汽车电池包的不同位置上安装至少三个三向加速度传感器,本实施例中电动汽车的电池包上安装四个三向加速度传感器,分别位于电池包的左前、右前、左后和右后4个安装点,并记录好每个三向加速度传感器与车辆坐标系的对应关系。
51.2.传感器安装好后,对电动汽车进行实车强化坏路路谱采集,获得不同路况下的初始路谱,所述初始路谱为加速度-时间谱。
52.不同测试场地的强化坏路的路况不尽相同,本实施例中依据《中汽中心盐城汽车试车场
·
电动汽车可靠性行驶试验规程》(试行)进行强化坏路路谱采集,每条路采集3圈,以提高采集的路谱的准确性。
53.《中汽中心盐城汽车试车场
·
电动汽车可靠性行驶试验规程》(试行)的内容如下:
54.1.范围
55.本规范规定了电动汽车产品在中汽中心盐城汽车试验场进行可靠性行驶试验的规程。
56.本规范适用于总质量不大于5吨的各类电动汽车。
57.2.引用标准
58.gb/t5910-1998汽车质量分布
59.gb/t12678-1990汽车可靠性行驶试验方法
60.gb/t18384-2015电动汽车安全要求
61.gb/t18385-2005电动汽车动力性能试验方法
62.gb/t18386-2005电动汽车能量消耗率和续驶里程试验方法
63.gb/t18388-2005电动汽车定型试验规程
64.gb/t19750-2005混合动力电动汽车定型试验规程
65.gb/t28382-2012纯电动乘用车技术条件
66.3.试验条件
67.3.1试验道路设施
68.试验道路设施详见图2所示的《中汽中心盐城汽车试验场道路总平面示意图》。
69.3.2试验样车
70.试验样车应装备齐全。
71.试验样车应技术状况良好,满足车辆技术条件要求。
72.3.3试验人员
73.试验人员应由试验负责人、技术人员、汽车驾驶员和修理工组成。试验人员应正确理解和掌握本规程,按规定进行试验操作。对于首次来场人员应接受培训。
74.4.实验方法
75.4.1车辆分类:
76.座位数在5座及以下的m1类电动车为a类电动车;
77.座位数大于5座的m1类、m2类、n1类以及总质量不超过5吨的n2类电动车为b类电动车。
78.4.2试验工况
79.a.强化耐久工况:按照高速环道两圈
→
强化坏路一个大圈
→
标准坡道两圈的顺序组成一个强化耐久工况试验循环,每个试验循环约53km。强化耐久工况试验循环各种道路如图3所示,各种道路里程分配见表1。
80.表1强化耐久工况各种道路里程分配表
[0081][0082][0083]
强化坏路大圈行驶顺序:
[0084]
强化坏路1个大圈包括5次ⅰ型循环和1次ⅱ型循环,总共约36km,其中包含坏路19km,一般路面17km。
[0085]ⅰ型循环:
[0086]
由起点(北环岛入口)沿逆时针方向进入10#森林路(2100m)(25-40km/h),逆时针方向行驶一圈通过北环岛进入1#路。依次通过混凝土补丁路(200m)(5-10km/h)和拱形车道路(90m)(30-35km/h),进入南环岛。
[0087]
逆时针方向沿南环岛进入9#路,通过不规则混凝土路(400m)(30-35km/h),进入北环岛。
[0088]
逆时针方向沿北环岛进入3#路,通过均匀波浪路(315m)(20-25km/h),进入南环
岛。
[0089]
逆时针方向沿南环岛进入7#路,通过井盖路(135m)(25-30km/h),锯齿路(140m)(25-30km/h),,鹅卵石路(240m)(15-20km/h)进入北环岛入口处。
[0090]
第5次ⅰ型循环时以30km/h的速度通过9#溅水路(50m)。
[0091]ⅱ型循环:
[0092]
由起点(北环岛入口)沿逆时针方向进入4#路,依次通过振动路ⅰ(240m)(20-25km/h),混凝土板冲击路(180m)(40-45km/h),鱼鳞坑路(100m)(35-40km/h)、倾斜车道(130m)(40-45km/h),进入南环岛。
[0093]
逆时针方向沿南环岛进入6#路,依次通过比利时路(210m)(20-25km/h),振动路ⅱ(150m)(25-30km/h)和长波路(156m)(45-50km/h),进入北环岛入口处。
[0094]
坡道行驶顺序:
[0095]
如图4所示,进入坡道道闸后左转沿道路边缘按顺时针方向行驶,沿10%坡度盘山道向上行驶,从20%坡道下坡,下坡过程进行一次驻车制动。然后从15%坡道上坡,行驶至中央位置制动停车,2s后进行坡道起步行驶至坡顶,然后从18%坡度下坡。完成后右拐,再重复进行一次坡道试验。
[0096]
b.平路工况:在高速环道上进行,以60km/h-80km/h的速度行驶,行驶过程正常的加速减速。
[0097]
c.变速工况:
[0098]
耐久工况试验在高速环道上进行,行驶里程应符合下述行驶规范,如图5所示;
[0099]
试验规范由11个循环组成,每个循环的行驶里程为7.85km;
[0100]
在前9个循环中,车辆在每个循环中途停车4次,每次怠速15s;
[0101]
正常的加速和减速;
[0102]
每个循环中途,有5次减速,车速从循环最大车速减速到30km/h,然后再逐渐加速到循环最大车速;
[0103]
第10个循环,车辆从0km/7.85km点处以最大加速度加速到90km/h,然后保持在90km/h下等速运行(若最高车速小于90km/h,则以最高车速运行),在0km/7.85km前正常使用制动器,直至车辆在0km/7.85km处停止;
[0104]
第11个循环,车辆从0km/7.85km点处以最大加速度加速到循环最大车速(若最高车速大于120km/h,则以120km/h运行),到该循环里程一半时,正常使用制动器,直至车辆停止,随之进行15s怠速,然后第二次最大加速到循环最大车速(若最高车速大于120km/h,则以120km/h运行),在0km/7.85km前正常使用制动器,直至车辆在0km/7.85km处停止;
[0105]
然后重新开始此规范,每个循环的最大车速见表2所示。
[0106]
表2每个循环的最大车速
[0107]
循环循环最大车速km/h循环循环最大车速km/h1657552508703659554651090/最高车速55511最高车速/120
650
ꢀꢀ
[0108]
4.3试验里程
[0109]
4.3.1a类电动车及变型车可靠性试验总里程为15000km,其中强化坏路2000km,平路和高速路8000km,耐久工况5000km。b类电动车可靠性试验总里程为15000km,其中强化坏路5250km,平路和高速路9750km。
[0110]
4.3.2b类电动车在现有电动车基础上进行变型,车辆主要总成(电池系统、电机及其控制系统、车载充电系统等)更换不超过两项,可靠性试验总里程为5000km,其中强化坏路1750km,平路和高速路3250km;超过两项更换则可靠性试验总里程为15000km,其中强化坏路5250km,平路和高速路9750km。
[0111]
4.4试验程序
[0112]
4.4.1a类电动车可靠性试验由强化耐久工况试验、平路工况试验和变速工况试验三部分组成。首先进行约105个强化耐久工况试验循环(约2000km坏路和3600km平路),全部强化耐久工况试验完成后在高速环道上进行约4300km平路工况试验,最后在高速环道上按附录b进行5000km变速工况试验。
[0113]
4.4.2进行15000km可靠性试验的b类电动车行驶约275个强化耐久工况循环(约5250km坏路和9750km平路);进行5000km可靠性试验的b类电动车可靠性行驶约92个强化耐久工况循环(约1750km坏路和3250km平路)。
[0114]
5.载荷
[0115]
5.1总里程超过5000公里的车型
[0116]
前1/2强化耐久工况按照半载装载;
[0117]
后1/2强化耐久工况按照满载装载;
[0118]
平路工况按照空载装载;
[0119]
变速工况按照空载装载。
[0120]
5.2总里程小于等于5000公里的车型
[0121]
全部按照满载装载。
[0122]
6其他
[0123]
整个可靠性试验过程中,试验人员应严格遵守盐城试验场《驾驶与安全规程》要求进行试验。
[0124]
7可靠性评价
[0125]
7.1故障统计分析;
[0126]
7.2平均首次故障里程(mttff)
[0127]
7.3平均故障间隔里程(mtbf)
[0128]
7.4平均故障维修时间(mttr)
[0129]
7.5有效度(a)。
[0130]
步骤2:路谱分析与加工
[0131]
1.对采集的加速度-时间谱,首先通过rpc(remote parameter control)软件中自带的remove offset工具去除采集得到的初始路谱中的零飘,以及采用filter工具剔除初始路谱中的毛刺,滤掉200hz以上的干扰信号。
[0132]
2.通过rpc软件中自带的cut工具将初始路谱中涉及的过渡路段从路谱中截去。
[0133]
3.通过rpc软件中自带的damage time history工具计算初始路谱的伪损伤值,再基于初始路谱的伪损伤值,使用rpc软件中自带的cut工具将损伤贡献较低的部分谱从初始路谱中剔除,即将初始路谱中加速度幅值小于等于峰值2%的部分剔除,从而获得目标路谱。
[0134]
步骤3:台架路谱制定
[0135]
1.将与步骤1中实车电池包型号完全相同的电池包安装在夹具上(要求夹具的一阶共振频率高于40hz),且电池包与夹具的固定方式与电池包与车身的固定方式完全一致,然后将夹具固定在六自由度振动台上,通过对夹具的设计使电池包的中心距六自由度振动台台面的距离为20-35cm。能够实现该距离的夹具结构不限于某一种结构,只要满足刚性连接以及距离要求的夹具结构都可以,因此,夹具的结构此处不做具体限制。
[0136]
2.在六自由度振动台台面的至少三个位置上安装三向加速度传感器,且三个位置不在同一条直线上;三个三向加速度传感器能够确定一个面,第四个及以上的三向加速度传感器作为过约束,提高其测量的准确性。
[0137]
作为优选,六自由度振动台的台面上安装四个三向加速度传感器,分别位于台面的左前、右前、左后和右后的4个角上,且三向加速度传感器距离台面中心的距离相同,且三向加速度传感器分布的越远越好,本实施例中六自由度振动台的台面大小为2m*2m,则三向加速度传感器距离中心的长宽方向分别位于接近1m的位置。
[0138]
3.通过迭代获得台架驱动普
[0139]
步骤3.1:根据目标路谱初步确定其包含的路谱通道,目标路谱包含若干路谱通道,并通过rpc软件自带模块setup pro对需要进行迭代的路谱通道的参数进行设置,所述参数包括但不限于通道名称、信号类型、信号单位和信号量程;
[0140]
步骤3.2:通过rpc软件自带模块analyze pro对目标路谱进行编辑,包括使用channel extract工具对步骤1中路谱通道的数量进行增减,使用filter工具对路谱进行滤波使之在六自由度振动台的工作范围内;
[0141]
步骤3.3:通过rpc软件自带模块model pro进行系统识别,构建测试系统的传递函数,其中,测试系统包括电池包、夹具和六自由度振动台;
[0142]
步骤3.4:通过rpc软件自带模块simulate pro进行目标路谱的迭代:
[0143]
(1)simulate pro模块会根据模块model pro构建的传递函数给出六自由度振动台的初始驱动谱;
[0144]
(2)通过播放初始驱动谱得到六自由度振动台的初始响应谱;
[0145]
(3)分析初始响应谱与目标路谱的差异,再调节simulate pro模块界面的gain值来修正传递函数,得到新的驱动谱,其中,gain值为传递函数的增益值;
[0146]
(4)再次播放新的驱动谱并得到新的响应谱;
[0147]
(5)重复进行gain值的调节和驱动谱的播放,直到六自由度振动台的响应谱与目标路谱的rms值差异在5%-10%以内,此时得到了所需的最终驱动谱。其中,由于不同车型其电池包的振动要求不尽相同,因此,此处响应谱与目标路谱的rms值差异允许的最大值也不同,根据测试经验允许的最大差异一般在5%-10%范围内,因此,只要该车型的响应谱与目标路谱的rms值差异在允许的最大差异值之内即满足测试要求,例如:某车型允许的响应谱与目标路谱的rms最大差异值为7%,则只要六自由度振动台的响应谱与目标路谱的rms
值差异≤7%即可。
[0148]
4.获得驱动普库
[0149]
采用步骤1-步骤3的方法采用其他车型进行初始路谱的采集,然后计算出每个车型对应的目标路谱,并将每个车型的电池包安装在六自由度振动台上,获得采用该六自由度振动台进行测试时的最终驱动普,将不同车型获得最终驱动普均存储在六自由度振动台上,从而形成驱动普库。
[0150]
5.驱动普库分级
[0151]
依次播放驱动普库中的驱动普,通过六自由度振动台上的四个三向加速度传感器测量每个驱动普对应的响应谱,然后对响应谱进行分级,分级方法如下:
[0152]
计算与最终驱动谱对应的响应谱的rms值,然后根据rms值进行分级,其中,
[0153]
x,y,z方向的rms值分别为0.64g、0.45g、0.5g的1.2倍以上的为a级;
[0154]
x,y,z方向的rms值分别为0.64g、0.45g、0.5g的0.8-1.2倍间的为b级;
[0155]
x,y,z方向的rms值分别为0.64g、0.45g、0.5g的0.8倍以下的为c级;
[0156]
进行电池包测试时,先选择对应的级别,然后再选择该级别下对应的驱动普,从而提高测试的效率。
[0157]
步骤4:路谱使用
[0158]
当需要对某一车型的电池包进行测试时,按照该车型的测试要求,将电池包安装在六自由度振动台上,然后先确定该车型的电池包对应的分级,再从对应的级别中选择驱动谱加载到六自由度振动台上,由六自由度振动台播放驱动普以模拟不同路况的路谱对电池包进行测试。
[0159]
本发明可用于开发阶段动力电池的六轴振动研发验证测试,由于本方法可以形成规范的测试流程,所以无需样车成型即可先对电池这一关键零部件进行测试,大大压缩了的开发周期,降低了电池六轴验证的准入门槛。
[0160]
以上述依据本发明的理想实施例为启示,通过上述的说明内容,相关的工作人员完全可以在不偏离本发明的范围内,进行多样的变更以及修改。本项发明的技术范围并不局限于说明书上的内容,必须要根据权利要求范围来确定其技术性范围。