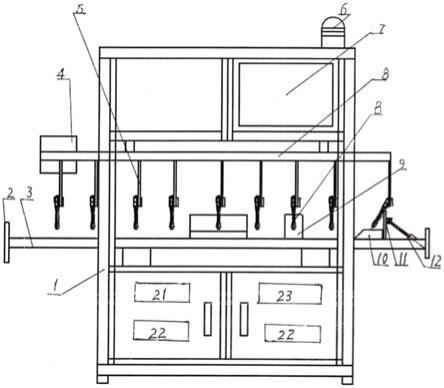
1.本实用新型属于一种发动机连杆制造检验装置,主要用于对衬套装配在连杆小孔内,与连杆小孔内壁贴合程度的检验,也可用于其它类似工件装配的检验。
背景技术:2.发动机连杆(见图1)由连杆体ⅰ、连杆盖ⅱ及螺栓ⅲ组成,在连杆制造工艺中,有一道必不可少的检验工序,即:在连杆体的小头孔2,过盈配合一个零件衬套1,将衬套压入小头孔内后,需要对连杆小孔内壁和衬套外径柱面的贴合度进行检验,该工序十分重要,由于衬套的外径不需要加工,由带材直接冲压卷制成型,当衬套与孔的配合之间存在过大间隙时,会严重影响连杆的使用性能,会发生轴向跳动或转动,出现干摩擦现象,导致磨损加剧,连杆孔将局部或全部直接承受活塞销非周期性复杂交变载荷的冲击,从而产生应力集中,导致连杆断裂或造成抱缸、捣缸和活塞烧穿等重大事故,因此对衬套外壁与连杆小孔内壁贴合度检验是十分有必要的。
3.现行的连杆衬套贴合度检验,主要采用1/600或1/1200件抽检方式,将衬套外径柱面上涂色,用压力机将衬套压入连杆小孔内,再用压力机压出衬套,观察衬套涂色表面与连杆小孔内壁的贴合面积来判定是否合格,一般要求与衬套涂色接触面积越大越好(没接触地方颜色依存在或淡化),一般要求接触面积大于衬套外径柱面总表面积的80%为合格,这种检验方法的不足之处在于:1、破坏性检测,被压力机压进压出,即是合格的产品也不能再用了;2、因人工操作,检验效率低,不适应专业化生产;3、检验可靠性差,不能100%检验,存在不合格产品流出的风险。鉴以这种状况,对于改进该工艺势在必行。
技术实现要素:4.本实用新型要解决的主要技术问题和目的是:针对目前连杆衬套装配贴合度检验存在的缺陷,利用钢件连杆和钢背铜合金层的衬套,具有磁性的特点,设计一种装置,对连杆衬套装配贴合度进行检验,从根本上提高检验效率,提高检验的可靠性,切实保障产品质量,适应专业化大批量生产的需求。
5.本实用新型的主要技术方案:装置包含立式框架、档板、平台、电机固定架、挂架、报警器、计算机及显示器、导轨、退磁器、滑落台、铰链挡板、气缸推杆、固定板、标准件电磁感应器、支架、工程塑料杆、步进电机、齿轮、柔性传送链、检测件电磁感应器、桥式整流平衡电路、信号发生器、设备主电源、螺栓,其具体结构:在立式框架的中间层上,安装平台,在平台上通过固定板安装标准件电磁感应器,标准件电磁感应器配合连接一个支架,支架上放一个工程塑料杆备用,再安装一个检测件电磁感应器、退磁器,在右边,安装滑落台、铰链挡板、气缸推杆;在立式框架的上层,摆放计算机及显示器,顶部安装报警示器,在上层的底板下面固定安装圆形导轨,导轨上均布安装四个齿轮,用于支撑柔性传送链,通过螺栓连接电机固定架,固定步进电机,步进电机通过齿轮,带动柔性传送链沿圆形导轨循环运动,柔性传送链通过螺栓连接挂架;在立式框架的底层,主要安装桥式整流平衡电路、两个信号发生
器及设备主电源;在电器线路中,信号发生器连接标准件电磁感应器,标准件电磁感应器再连接桥式整流平衡电路,桥式整流平衡电路接入计算机及显示器,计算机及显示器再接入报警器,另外一个信号发生器连接检测件电磁感应器,检测件电磁感应器再连接桥式整流平衡电路的另一端。
6.本实用新型通过实际应用证明:完全达到研制目的,生产中使用该装置,实现连杆产品100%得到检验,决不会出现漏检错检的现象,杜绝了不合格品的流出;大副度提高了检验效率(提高50倍以上);改善劳动条件,减小劳动强度,有效地保障了产品质量,填补了国内对连杆自动检验的一项空白,该装置结构简单,可操作性强,易推广应用,它的应用,无疑对促进我国连杆制造业的科技进步具有重要意义。
附图说明
7.下面结合附图,对本实用新型的具体实施方式做进一步详细地描述。
8.图1,是连杆总成图,也是连杆和衬套的装配图。
9.图2,是图1的a
‑
a向剖视图。
10.图3,是衬套1的主视剖视图。衬套由外钢背层i和内铜合金层j组成。
11.图4,是图3的左视图,衬套由外钢背层i和内铜合金层j组成。
12.图5,是本实用新型的装配结构示意图。
13.图6,是图5的左视图。
具体实施方式
14.参照图5、6,对本实用新型的主要技术方案进行说明:该装置主要是,利用钢件连杆小头孔内壁和钢背铜合金层的衬套,具有磁导性的特点,设计一种连杆衬套装配贴合度检验装置 ,装置包含立式框架1、档板2、平台3、电机固定架4、挂架5、报警器6、计算机及显示器7、导轨8、退磁器9、滑落台10、铰链挡板11、气缸推杆12、固定板13、标准件电磁感应器14、支架15、工程塑料杆16、步进电机17、齿轮18、柔性传送链19、检测件电磁感应器20、桥式整流平衡电路21、信号发生器22、设备主电源23、螺栓24,其具体结构:在立式框架1的中间层上,安装平台3,在平台上通过固定板13安装标准件电磁感应器14,标准件电磁感应器配合连接一个支架15,支架上放一个工程塑料杆16备用,再安装一个检测件电磁感应器20、退磁器9,在右边,安装滑落台10、铰链挡板11、气缸推杆12;在立式框架1的上层,摆放计算机及显示器7,顶部安装报警示器6,在上层的底板下面固定安装圆形导轨8,导轨上均布安装四个齿轮18,用于支撑柔性传送链19,通过螺栓24连接电机固定架4,固定步进电机17,步进电机通过齿轮18,带动柔性传送链19沿圆形导轨8循环运动,柔性传送链通过螺栓连接挂架5;在立式框架1的底层,主要安装桥式整流平衡电路21、两个信号发生器22及设备主电源23;在电器线路中,信号发生器22连接标准件电磁感应器14,标准件电磁感应器再连接桥式整流平衡电路21,桥式整流平衡电路接入计算机及显示器7,计算机及显示器再接入报警器6,另外一个信号发生器22连接检测件电磁感应器20,检测件电磁感应器再连接桥式整流平衡电路21的另一端。以上结构构成了一个完整的连杆衬套装配贴合度检验装置。
15.参照图5、6,对检验装置的各电子器件进行说明:信号发生器22,是自制的连续输出0
‑
24v交流精密可调的电源;标准件电磁感应器14和检测件电磁感应器20,是自制的与连
杆小头宽度相应的铜线绕制的电磁感应线圈,约150匝,将其加工变为u形线圈;退磁器9,是自制的约500匝的u形线圈,接入一个简单的普通退磁电路,安装在一起,构成一个器件;桥式整流平衡电路21,是自制的由四只二极管及可调电阻组成;计算机及显示器7,是一般的ohr计算机示波器;报警器6,是市场购置的,型号为jdsg
‑
25,防爆火灾报警器;挂架5,是自制的一般带钩的架;柔性传送链19,是购置的工业上常用的链带;气缸推杆12,是标准件受计算机控制;设备主电源23,是控制各器件线路的总电源。
16.参照图5、6,本实用新型对连杆衬套装配贴合度检验步骤:、选样件,首先按现行的连杆衬套贴合度检验的涂色方法,检测选取连杆衬套贴合度合格与不合格的两个标准样品(贴合面积≥80%为合格,贴合面积<80%的为不合格),作为标定调试检验装置的样件; 、标定装置,将装置电源打开,将连杆衬套贴合度合格的样品的大头孔穿入工程塑料杆16,塑料杆的两头安放在支架15的壁上(起绝缘作用),连杆衬套小头孔部位放入标准件电磁感应器14中间(起铁芯作用),再把不合格的样品放在检测件电磁感应器20中间,计算机及显示器显示不同的电信号电压值,该值已超出确定的数据范围,说明标准不合格样件还是不合格,同理找多个不合格连杆件来测,仍然不合格,此时标定完毕;、开始检验,人工把被测件b逐个挂在挂架5上,步进电机17带动挂架运行,当被测件小头部进入检测件电磁感应器20时,进行对比检测,接着步进电机17继续带动挂架被测件进入退磁器9,消除被测件的微弱充磁,当步进电机带动挂架被测件进入到出口时,人工取下合格件,如检测出不合格件时,气缸推杆12推动铰链挡板11自动翻起,阻止不合格件向前运行,不合格件自动进入滑落台10被剔除。柔性传送链19不断循环运行,检验也不断地继续工作。
17.这里对检验步骤开始检验,作具体说明:当检验被测件的贴合度合格时,显示器显示电信号(电压读数)与合格标准样品的电信号不完全相同,因为所有合格的连杆贴合面积不一样,所以显示电信号(电压读数)也不一样,故根据合格标准件(贴合面积≥80%),所对应的输出电压值,确定一定的范围 (如8.4—10v),所以显示电信号在范围内的为合格,说明电磁感应器产生的电路阻、感抗电阻及电压是相同或相近似的。
18.本实用新型只需根据连杆小头部位的几何尺寸,调整标准电磁感应器14和检测件电磁感应器20的尺寸和相对位置,可满足不同规格、不同宽度的连杆检验需要,目前已应用于jl465q、da462q、vm、b15d、d01、368q等多种规格的连杆衬套贴合度检验,效果较好。