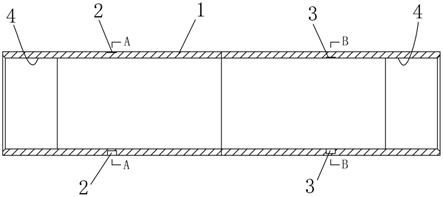
1.本实用新型属于管道未焊透检测技术领域,具体是涉及一种用于管道焊缝缺陷检测的模拟试件。
背景技术:2.压力管道定期检验过程中,由于安装过程中焊接等因素影响,未焊透缺陷较为普遍。目前,常采用数字射线成像技术(digital radiography,dr)进行检测,实时成像,曝光时间短,采用了计算机与图像处理,理论上可以实现缺陷的精确测量,但由于dr系统结构和射线束角度等原因,检测图像存在几何放大和边缘变形等问题,若整幅图像采用单一的修正系数计算,会存在误差。对于缺陷检测而言,目前的误差是可以接受的。但对于测量精度要求较高的,如由于腐蚀等原因引起的壁厚减薄的检测,则需要在被测区域放置已知尺寸的标准试件参与成像,计算出此点或区域的修正系数,最后换算出本区域的实际精确数据。因此,为达到高精度的检测结果,必须采用与之相匹配的标准试件来提高检测精度。
技术实现要素:3.本实用新型主要是解决上述现有技术所存在的技术问题,提供一种用于管道焊缝缺陷检测的模拟试件。
4.本实用新型的上述技术问题主要是通过下述技术方案得以解决的:一种用于管道焊缝缺陷检测的模拟试件,包括中空的直管,所述直管一侧的外壁呈环形阵列设有不同孔深、且间隔一定角度设置的若干第一平底孔,所述直管另一侧的内壁呈环形阵列设有不同孔深、且间隔一定角度设置的若干第二平底孔,所述第一平底孔和第二平底孔的数量相一致,间隔角度相一致。
5.作为优选,所述第一平底孔与第二平底孔对称设置。
6.作为优选,所述第一平底孔的孔径和第二平底孔的孔径相同。
7.作为优选,所述第一平底孔的孔深顺时针先递增后递减变化,且孔深最小的第一平底孔位于0
°
方向,孔深最大的第一平底孔位于180
°
方向;所述第二平底孔的孔深顺时针先递增后递减变化,且孔深最小的第二平底孔位于0
°
方向,孔深最大的第二平底孔位于 180
°
方向。
8.作为优选,所述第一平底孔的孔深变化和第二平底孔的孔深变化相同。
9.作为优选,所述第一平底孔、第二平底孔均呈环形阵列间隔45
°
设置。
10.作为优选,所述第一平底孔的孔深顺时针依次设置为0.5mm、1.0mm、1.5mm、2.0mm、 2.5mm、2.0mm、1.5mm、1.0mm,所述第一平底孔的孔径为5mm;所述第二平底孔的孔深顺时针依次设置为0.5mm、1.0mm、1.5mm、2.0mm、2.5mm、2.0mm、1.5mm、1.0mm,所述第二平底孔的孔径为5mm。
11.作为优选,所述第一平底孔的孔深顺时针依次设置为0.5mm、1.0mm、2.0mm、3.0mm、 4.0mm、3.0mm、2.0mm、1.0mm,所述第一平底孔的孔径为5mm;所述第二平底孔的孔深顺时针
依次设置为0.5mm、1.0mm、2.0mm、3.0mm、4.0mm、3.0mm、2.0mm、1.0mm,所述第二平底孔的孔径为5mm。
12.作为优选,所述第一平底孔、第二平底孔均呈环形阵列间隔90
°
设置,所述第一平底孔的孔深顺时针依次设置为0.5mm、2.0mm、3.0mm、1.0mm,所述第一平底孔的孔径为5mm;所述第二平底孔的孔深顺时针依次设置为0.5mm、2.0mm、3.0mm、1.0mm,所述第二平底孔的孔径为5mm。
13.作为优选,所述直管为20#钢直管。
14.本实用新型具有的有益效果:本实用新型使用简单方便,通过将管道、与管道相同规格的模拟试件在相同透照条件下进行数字射线照射,经比对即可得到管道腐蚀深度。本实用新型通过在直管一侧的外壁上设有第一平底孔,用于模拟外壁腐蚀缺陷,通过在直管另一侧的内壁上设有第二平底孔,用于模拟内壁腐蚀缺陷。
附图说明
15.图1是本实用新型的一种结构示意图;
16.图2是图1中a-a的剖视示意图;
17.图3是图1中b-b的剖视示意图;
18.图4是本实用新型第一平底孔的一种使用状态图;
19.图5是本实用新型第二平底孔的一种使用状态图;
20.图6是本实用新型第一平底孔的另一种使用状态图;
21.图7是本实用新型第二平底孔的另一种使用状态图。
22.图中:1、直管;2、第一平底孔;3、第二平底孔;4、螺纹。
具体实施方式
23.下面通过实施例,并结合附图,对本实用新型的技术方案作进一步具体的说明。
24.实施例:一种用于管道焊缝缺陷检测的模拟试件,如图1-图3所示,包括中空的直管1,所述直管1的材质为20#钢,所述直管1一侧的外壁呈环形阵列设有不同孔深、且间隔一定角度设置的若干第一平底孔2,所述直管1另一侧的内壁呈环形阵列设有不同孔深、且间隔一定角度设置的若干第二平底孔3,所述第一平底孔2和第二平底孔3的数量相一致,所述第一平底孔2的间隔角度和第二平底孔3的间隔角度相一致,所述直管1两端的内壁均设有螺纹4。
25.所述第一平底孔2与第二平底孔3对称设置;所述第一平底孔2的孔径和第二平底孔3的孔径相同。
26.所述第一平底孔2的孔深顺时针先递增后递减变化,且孔深最小的第一平底孔2位于 0
°
方向,孔深最大的第一平底孔2位于180
°
方向;所述第二平底孔3的孔深顺时针先递增后递减变化,且孔深最小的第二平底孔3位于0
°
方向,孔深最大的第二平底孔3位于 180
°
方向。
27.所述第一平底孔2的孔深变化和第二平底孔3的孔深变化相同。
28.所述第一平底孔2和第二平底孔3的孔深可根据需求进行设置:
29.如图1-图3所示,直管1的外径为57mm,长度为240mm,管壁为3.5mm;第一平底孔 2
设置在直管1左侧的外壁上,第一平底孔2设置有八个,呈环形阵列间隔45
°
设置,第一平底孔2的孔深按顺时针依次设置为0.5mm、1.0mm、1.5mm、2.0mm、2.5mm、2.0mm、1.5mm、 1.0mm,第一平底孔2的孔径为5mm;第二平底孔3设置在直管1右侧的内壁上,第二平底孔3设置有八个,呈环形阵列间隔45
°
设置,第二平底孔3的孔深按顺时针依次设置为 0.5mm、1.0mm、1.5mm、2.0mm、2.5mm、2.0mm、1.5mm、1.0mm,第二平底孔3的孔径为5mm;孔深相同的第一平底孔2、第二平底孔3相对称,直管1的两端内壁上均设有扣型尺寸为 2的锥管螺纹。
30.如图1、图4、图5所示,直管1的外径为108mm,长度为240mm,管壁为4.0mm;第一平底孔2设置在直管1左侧的外壁上,第一平底孔2设置有四个,呈环形阵列间隔90
°
设置,第一平底孔2的孔深按顺时针依次设置为0.5mm、2.0mm、3.0mm、1.0mm,第一平底孔2的孔径为5mm;第二平底孔3设置在直管1右侧的内壁上,第二平底孔3设置有四个,呈环形阵列间隔90
°
设置,第二平底孔3的孔深按顺时针依次设置为0.5mm、2.0mm、3.0mm、 1.0mm,第二平底孔3的孔径为5mm;孔深相同的第一平底孔2、第二平底孔3相对称,直管1的两端内壁上均设有扣型尺寸为4的锥管螺纹。
31.如图1、图6、图7所示,直管1的外径为219mm,长度为240mm,管壁为6.0mm;第一平底孔2设置在直管1左侧的外壁上,第一平底孔2设置有八个,呈环形阵列间隔45
°
设置,第一平底孔2的孔深按顺时针依次设置为0.5mm、1.0mm、2.0mm、3.0mm、4.0mm、 3.0mm、2.0mm、1.0mm,第一平底孔2的孔径为5mm;第二平底孔3设置在直管1右侧的内壁上,第二平底孔3设置有八个,呈环形阵列间隔45
°
设置,第二平底孔3的孔深按顺时针依次设置为0.5mm、1.0mm、2.0mm、3.0mm、4.0mm、3.0mm、2.0mm、1.0mm,第二平底孔 3的孔径为5mm;孔深相同的第一平底孔2、第二平底孔3相对称,直管1的两端内壁上均设有扣型尺寸为8的锥管螺纹。
32.上述模拟试件用于模拟管道内壁和外壁发生局部腐蚀缺陷,其使用为:在检验现场,发现管道有局部腐蚀缺陷存在时,把管道、与管道相同规格的模拟试件在相同透照条件下进行数字射线照射,经比对可得到管道腐蚀深度。
33.综上所述,本实用新型使用简单方便,通过将管道、与管道相同规格的模拟试件在相同透照条件下进行数字射线照射,经比对即可得到管道腐蚀深度。本实用新型通过在直管一侧的外壁上设有第一平底孔,用于模拟外壁腐蚀缺陷,通过在直管另一侧的内壁上设有第二平底孔,用于模拟内壁腐蚀缺陷。
34.最后,应当指出,以上实施例仅是本实用新型较有代表性的例子。显然,本实用新型不限于上述实施例,还可以有许多变形。凡是依据本实用新型的技术实质对以上实施例所作的任何简单修改、等同变化与修饰,均应认为属于本实用新型的保护范围。