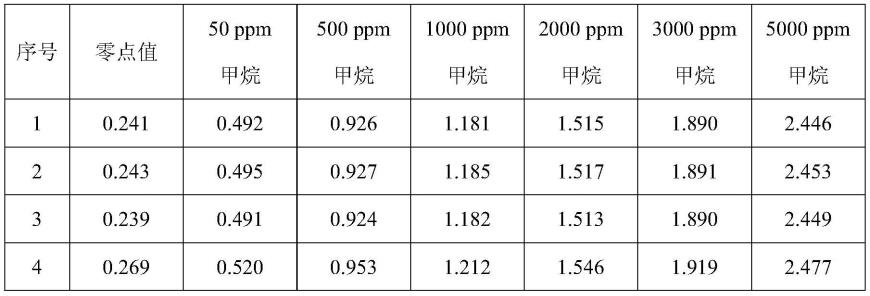
一种基于mems技术的半导体可燃气体传感器及其制备方法
技术领域
1.本发明属于半导体气体传感器技术领域,具体涉及一种基于mems技术的半导体可燃气体传感器及其制备方法。
背景技术:2.半导体气体传感器以金属氧化物为气敏材料,其工作原理是根据在一定工作温度下待测气体在半导体金属氧化物表面发生氧化/还原反应时引起氧化物的电阻值发生变化。目前,应用最多的半导体气体传感器主要是基于陶瓷管和陶瓷基板,此类气体传感器通常需要较长的时间预热,且大体积功耗较高,不利于集成和阵列化。
3.随着mems技术的发展,半导体气体传感器可以制作在一个微小的芯片上,低功耗的半导体气体传感器就是基于mems技术的微热板式气体传感器,此类气体传感器具有体积小、功耗低、重量轻、灵敏度高、寿命长、成本低、易于集成和实现智能化的特点,被广泛应用于碳氧化物、氮氧化物和挥发性有机复合物等部分有毒、易燃、易爆和污染气体等的监测。微热板式气体传感器采用多层悬空薄膜结构,结构由上至下分别是气敏膜薄层、测试电极层、上绝缘膜层、加热电极层、下绝缘膜层、衬底,各层薄膜包括气敏薄膜的热膨胀系数存在较大的差异,当其工作在高温状态下,发生热膨胀形变,内部存在较大的热应力,在反复热冲击中会造成气敏薄膜和电极层的结构翘曲甚至脱落,进而影响气体传感器的性能。
4.为了解决半导体气体传感器材料之间的热膨胀系数失配而造成的器件损坏,申请号为cn201911371286.3的专利公开了一种基于mems集成式的气体传感器,包括相对设置的加热单元和气体敏感单元,其中,所述气体敏感单元包括测试电极和气体敏感结构,所述气体敏感结构与所述测试电极电连接;所述加热单元包括与所述测试电极相匹配的加热层,所述加热层朝向所述气体敏感结构,且所述加热层与所述气体敏感结构无直接接触。该方法加热层与气体敏感结构之间不设置介质膜(绝缘膜层),在使用过程的反复热冲击中,避免了加热层与介质膜之间、气体敏感结构与介质膜之间因热膨胀系数匹配方面产生的问题。该专利所述加热单元与气体敏感结构之间无直接热传导,加热层与衬底完全接触也增加了热损耗,导致了气体传感器能耗增加;同时,气体敏感结构所具有的多根交织多孔导电纤维,是由有磺化石墨烯及噻吩低聚物经特定环境处理下形成的,其影响参数较多,产品一致性不易保证。
5.因此,在满足器件功耗要求及性能一致性的基础上,如何解决气体传感器因长期加热状态所发生的结构性损伤问题,是目前研究亟待解决的问题。
技术实现要素:6.基于现有技术的不足,本发明提供了一种基于mems技术的半导体可燃气体传感器,通过将加热电极呈环绕状包围在测试电极四周,避免了加热电极与测试电极直接接触,进一步通过在气敏涂层中添加酸洗石棉来增加气敏涂层粘附的结合力,从而减免气体传感器因长期加热状态所发生的结构性损伤;本发明还提供了该半导体可燃气体传感器的制备
方法。
7.为了实现上述目的,本发明采用的技术方案为:
8.一种基于mems技术的半导体可燃气体传感器,包括相对设置的气敏模块及加热模块,所述气敏模块与加热模块键合连接,所述气敏模块包括硅衬底,硅衬底下侧面设置有凹槽,且硅衬底的上、下两面均形成有第一绝缘层,位于下侧的第一绝缘层上溅射有测试电极及测试导电带,测试电极上涂覆有气敏涂层,所述气敏涂层中含有半导体金属氧化物、贵金属催化剂、催化剂载体及酸洗石棉,硅衬底厚度方向刻蚀有与测试导电带一一对应的第一引线孔,凹槽的底部刻蚀有若干贯穿硅衬底的通气孔,所述通气孔环绕测试电极,且通气孔呈阵列排布;
9.所述加热模块包括硅基底,硅基底的上、下两面均氧化形成有第二绝缘层,位于上侧的第二绝缘层上沉积有氮化硅层,氮化硅层上溅射有加热电极及加热导电带,硅基底上部刻蚀形成有隔热腔,隔热腔上方形成设有悬空梁支撑结构的加热平台;所述加热电极位于加热平台上,且加热电极呈环绕状包围在测试电极四周,所述加热导电带连接于加热电极的端部,且加热导电带沿悬空梁向外延伸,硅基底厚度方向刻蚀有与加热导电带一一对应的第二引线孔;所述加热模块上表面的外缘设置有衬垫,所述衬垫连接于加热模块与气敏模块之间。
10.所述加热电极包括前后对称设置的蛇形电极,所述蛇形电极布置呈“凹”形,且前后两个蛇形电极之间有间距,使两个蛇形电极之间形成空白的矩形区域及条形区域;所述加热导电带包括连接端部及连接梁部,所述连接端部为4个、并分别位于氮化硅层的四角处,所述连接梁部的一端与连接端部相连,连接梁部的另一端沿悬空梁延伸至加热平台、并与蛇形电极相连;所述测试电极采用插齿电极,且测试电极位于矩形区域的上方,所述测试导电带位于条形区域的上方,且测试导电带沿横向延伸。
11.本发明采用具有悬空梁支撑结构的加热平台,悬空梁与位于中央的加热平台的连接点较少,有助于减小热传导,从而降低了能耗;而为了提高结构强度,通过4个加热导电带增加加热电极与基底的连接点;通过将加热模块与气敏模块相对设置,加热电极包围在测试电极四周,使测试电极与加热电极完全隔开,既避免了加热电极、气敏涂层和测试电极之间的短路,又充分利用加热电极为中心的测试电极提供足够的热量。
12.在保证传感器机械性能稳定和加热性能良好的前提下,本发明将含有半导体金属氧化物、贵金属催化剂、催化剂载体及酸洗石棉的混合浆料涂覆到气敏模块的测试电极区域,经烧结后形成气敏涂层,由于混合浆料交联形态配合酸洗石棉纤维,增加浆料与衬底结合力,避免了气敏涂层的翘起、开裂;制备过程简单易行,气敏元件的性能一致性好,检测灵敏度高,器件使用寿命长,同时机械强度高,自动化制造降低了生产成本。本发明通过设计加热电极和测试电极的几何形态和结构布置,实现传感器的结构紧凑化;进一步将测试电极及加热电极分别引出至硅衬底及硅基底表面,方便连接印刷电路板,有助于减小封装外壳的体积。本发明通过结构设计与材料配合,减免了各层薄膜因热膨胀系数差异而带来的损伤,具有良好的应用效果和产业化前景。
附图说明
13.图1为实施例1所述半导体可燃气体传感器的结构示意图;
14.图2是图1中气敏模块的仰视图;
15.图3是图1中加热模块的俯视图;
16.图4是实施例1所述半导体可燃气体传感器的制备工艺路线图;
17.图5是实施例2所述半导体可燃气体传感器的结构示意图;
18.图6是实施例3所述气敏涂层的扫描电镜表征图。
具体实施方式
19.为了使本发明的技术目的、技术方案和有益效果更加清楚,下面结合具体实施例对本发明的技术方案作出进一步的说明,但所述实施例旨在解释本发明,而不能理解为对本发明的限制,实施例中未注明具体技术或条件者,按照本领域内的文献所描述的技术或条件或者按照产品说明书进行。
20.下述实施例中所述氧化锡购自麦克林,型号为t817641,粒径为50~70nm;铂黑购自阿拉丁,型号为p113302,粒径为10nm;氯化钯购自阿拉丁,型号为p282904,粒径为70nm;氧化铝购自麦克林,型号为a800207,粒径为150nm;硫酸亚锡购自阿拉丁,型号为s112918,粒径为0.1mm;氧化镁购自麦克林,型号为m813080,粒径为100nm;三氧化钨购自麦克林,型号为t818835,粒径为150nm;五氧化二钒购自阿拉丁,型号为v112535,粒径为80nm;五氧化二锑购自阿拉丁,型号为a100109,粒径为20nm;酸洗石棉购自阿拉丁,型号为a104830;硅酸四乙酯购自麦克林,型号为t819505。
21.实施例1
22.如图1~3所示,一种基于mems技术的半导体可燃气体传感器,包括相对设置的气敏模块及加热模块,所述气敏模块与加热模块键合连接。所述加热模块上表面的外缘设置有衬垫16,所述衬垫16连接于加热模块与气敏模块之间。
23.所述气敏模块包括硅衬底1,硅衬底1下侧面设置有凹槽2,且硅衬底1的上、下两面均形成有第一绝缘层3,位于下侧的第一绝缘层3上溅射有测试电极4及测试导电带5,测试电极4上涂覆有气敏涂层15,所述气敏涂层15中含有半导体金属氧化物、贵金属催化剂、催化剂载体及酸洗石棉,硅衬底1厚度方向刻蚀有与测试导电带5一一对应的第一引线孔6,凹槽2的底部刻蚀有若干贯穿硅衬底1的通气孔,所述通气孔环绕测试电极4,且通气孔呈阵列排布。
24.所述加热模块包括硅基底8,硅基底8的上、下两面均氧化形成有第二绝缘层9,位于上侧的第二绝缘层9上沉积有氮化硅层10,氮化硅层10上溅射有加热电极11及加热导电带12,硅基底8上部刻蚀形成有隔热腔14,隔热腔14上方形成具有悬空梁17支撑结构的加热平台18(面积约0.2
×
0.2mm);所述加热电极11位于加热平台18上,且加热电极11呈环绕状包围在测试电极4四周,所述加热导电带12连接于加热电极11的端部,且加热导电带12沿悬空梁17向外延伸,硅基底8厚度方向刻蚀有与加热导电带12一一对应的第二引线孔13。
25.其中,所述加热电极11包括前后对称设置的蛇形电极,所述蛇形电极布置呈“凹”形,且前后两个蛇形电极之间有间距,使两个蛇形电极之间形成空白的矩形区域及条形区域;所述加热导电带12包括连接端部1201及连接梁部1202,所述连接端部1201为4个、并分别位于氮化硅层10的四角处,所述连接梁部1202的一端与连接端部1201相连,连接梁部1202的另一端沿悬空梁17延伸至加热平台18、并与蛇形电极相连;所述测试电极4采用插齿
电极,所述测试电极4位于矩形区域的上方,且测试电极4的底面高于加热电极11的顶面。所述测试导电带5位于条形区域的上方,且测试导电带5沿横向延伸。
26.上述半导体可燃气体传感器的制备方法,如图4所示,包括以下步骤:
27.(一)制造气敏模块:
28.(1-1)提供厚度为300μm的硅衬底1,并在硅衬底1下表面的指定区域加工形成圆形的凹槽2,凹槽2深度为20μm,经清洗、干燥后,在硅衬底1的上、下表面热氧化形成厚度为2μm的第一绝缘层3(氧化硅膜);
29.(1-2)旋涂光刻胶并烘干,然后紫外光刻、显影,得到测试电极4及测试导电带5图形,用去离子水清洗、烘干,先磁控溅射ti作为粘结层(厚度为100nm),再磁控溅射pt(厚度为900nm),经剥离后(去除光刻胶及胶上的金属),形成测试电极4(线宽5μm)及测试导电带5,用去离子水清洗、烘干;
30.(1-3)在硅衬底1内激光刻蚀形成第一引线孔6及通气孔7(直径为300μm),在第一引线孔6内填充金属浆料,以使测试电极4通过测试导电带5及第一引线孔6被引线至气敏模块的上表面;
31.(1-4)利用点胶的方式,将含有半导体金属氧化物、贵金属催化剂、催化剂载体及酸洗石棉的混合浆料涂覆于测试电极4上,涂覆厚度为200nm,于700℃烧结3.5小时(包含升温时间和保温时间,升温是以10℃/min的速率升至700℃),冷却至室温,形成气敏涂层15;
32.(二)制造加热模块:
33.(2-1)提供厚度为500μm的硅基底8,经清洗、干燥后,在硅衬底1的上、下表面热氧化形成厚度为2μm的第二绝缘层9(氧化硅膜),并在位于上侧的第二绝缘层9上沉积有厚度为300nm的氮化硅层10;
34.(2-2)旋涂光刻胶并烘干,然后紫外光刻、显影,得到加热电极11及加热导电带12图形,用去离子水清洗、烘干,先磁控溅射cr作为粘结层(厚度为100nm),再磁控溅射pt(厚度为900nm),经剥离后,形成加热电极11(线宽5μm)及加热导电带12;
35.(2-3)旋涂光刻胶并烘干,然后光刻、显影,得到刻蚀窗口图形,用去离子水清洗、烘干,溅射cr/cu金属层,经剥离后(去除光刻胶及胶上的金属)、清洗并烘干后,电镀2~3μm的ni作为掩膜版,再利用反应离子刻蚀去除刻蚀窗口下暴露的第二绝缘层9及氮化硅层10,使用koh溶液水浴加热湿法刻硅,最后湿法刻蚀去除掩膜版及cr/cu金属层,释放器件,形成隔热腔14;
36.(2-4)在硅基底8内激光刻蚀形成第二引线孔13,在第二引线孔13内填充金属浆料,以使加热电极11通过加热导电带12及第二引线孔13被引线至加热模块的下表面;
37.(三)键合连接:
38.在加热模块上表面的外缘设置有衬垫16,采用键合方式将气敏模块与加热模块连接为一体。
39.其中,所述光刻、溅射、剥离、刻蚀、键合等工艺参数采用本领域常规技术手段即可,并非本发明创新所在,故不再详细赘述。
40.实施例2
41.如图5所示,由于测试导电带5与加热电极11、加热导电带12不重叠,故所述第一引线孔6可设置于加热模块上,所述测试电极4可通过测试导电带5、第一引线孔6被引线至加
热模块底面,这样有助于进一步方便传感器封装。
42.实施例2与实施例1相比,区别在于:加热模块与气敏模块之间不再设置衬垫16,气敏模块中所述凹槽2的深度增加至40μm,气敏模块中不设置第一引线孔6,加热模块与测试导电带5端部相对应的部位设置第一引线孔6。
43.实施例3
44.按照实施例1所述半导体可燃气体传感器的结构,为了改善气敏涂层15的一致性和稳定性,具体涂覆步骤如下:
45.(a)准备混合浆料的各原料:
46.氧化锡180~220份、硫酸亚锡72~88份、酸洗石棉3.6~4.4份、氧化铝45~55份、贵金属催化剂6.7~8.3份、三氧化钨6.3~7.7份、氧化镁3.0~3.8份、五氧化二钒2.7~3.3份、五氧化二锑1.4~1.8份、硅酸四乙酯250~310份、甲酸330~400份、乙二醇100~125份、n-甲基吡咯烷酮135~170份、无水乙醇140~175份、纯水180~220份;
47.本实施例采用最优配方,具体为:氧化锡2.0g、硫酸亚锡0.8g、酸洗石棉0.04g、氧化铝0.5g、铂黑0.06g、氯化钯0.015g、三氧化钨0.07g、氧化镁0.034g、五氧化二钒0.03g、五氧化二锑0.016g、硅酸四乙酯3.0ml、甲酸3.0ml、乙二醇1.0ml、n-甲基吡咯烷酮1.5ml、无水乙醇2.0ml、纯水2.0ml;
48.(b)制备混合浆料:
49.采用行星式球磨设备(罐体体积为20ml),以密闭湿磨的混合方式,将铂黑、氯化钯、氧化铝及纯水混合40min,再加入硫酸亚锡,混合30min后,以30℃/min的速率升温至180℃并保温混合50min,冷却至室温;然后依次加入氧化锡、无水乙醇、n-甲基吡咯烷酮、氧化镁、三氧化钨、五氧化二钒、五氧化二锑、酸洗石棉、乙二醇、硅酸四乙酯及甲酸,继续混合30min,即得混合浆料;
50.(c)将步骤(b)所得混合浆料采用点胶的方式涂覆在气敏模块上,涂覆厚度为200nm,然后将气敏模块置于晶圆烧结炉内,于700℃烧结3.5小时(包含升温时间和保温时间,升温是以10℃/min的速率升至700℃),冷却至室温后取出。
51.实施例3中所述混合浆料以氧化锡(sno2,能带隙eg为3.5ev)作为基体材料,在弱酸性环境中,通过各纳米材料的不饱和键进行键和反应,提升气敏模块高温工作环境中的稳定性;其中,三氧化钨(wo3)、氧化镁(mgo)、五氧化二钒(v2o5)主要作用是维持浆料制备过程中的酸碱环境,依据元素的活泼性,w、mg、v和配方内其他过渡元素共同保持烧结后的气敏材料内的平衡;五氧化二锑(sb2o5)在混合浆料中维持半导体浆料的半导体特性,对半导体浆料电阻值起调节作用;经高温烧结后,sno2与wo3(eg 2.7ev)、v2o5(eg 2.8ev)、sb2o5(eg 3.0ev)形成半导体复合氧化物,晶格内产生替位杂质缺陷和氧空位缺陷,有助于载流子的释放、传输及注入输运过程,促进了测试气体的吸、脱附过程及响应速度。
52.选用铂黑(pt)及氯化钯(pdcl2)作为贵金属催化剂,充分附着在al2o3载体上,再与金属氧化物混合,可以增加材料表面的活性位点,使材料可以吸附更多的气体,同时还会夺走金属氧化物材料表面的电子,形成耗尽层,当材料暴露于还原气体之下时,贵金属氧化物会迅速还原,导致阻值明显下降,从而提高气敏性质。硫酸亚锡(snso4)同步参与al2o3和贵金属催化剂的置换反应,so
42-增加贵金属元素在高温条件下工作过程中的稳定性,增加气敏模块在整个可燃气体传感器中的使用寿命及产品稳定性。另外,在气敏模块工作过程中,
其反应的灵敏度取决于贵金属催化剂的活性与含量,w、v、sb元素与贵金属催化剂形成点位势能互补,保持贵金属元素在高温环境下的活性,增加气敏模块在工作过程中的稳定性。
53.同时,硅酸四乙酯(teos)与纯水发生水解反应生成sio2,通过sio2表面不饱和键与带有羟基(-oh)的有机挥发性气体(如甲醇、乙醇等)发生键合反应,在工作过程中避免-oh基团直接与贵金属催化剂接触,从而降低此类气体的干扰。并且,sio2与配方中的sb元素产生偶联,进而改善整体器件涂层的稳定性,在浆料配制过程中实现对可燃气体的检测,又能满足抗干扰的效果。
54.现有技术中为了解决气体传感器不能有效区分目标气体和干扰气体而误报的问题,申请号为cn201711242427.2的专利公开了一种抗干扰气体传感器,在封装底座中设置有至少一组阵列传感器芯片,每组阵列传感器芯片均包括至少一个对目标气体和干扰气体均具有第一响应的目标气体气敏元件和至少一个对干扰气体具有第二响应的干扰气体气敏元件;申请号为cn201910630446.5的专利公开了一种mems气体传感器,包括:基于n型掺杂半导体材料的敏感单元和基于p型掺杂半导体材料的敏感单元中的至少一种,以及,基于p型本征半导体材料的敏感单元;所述基于n型掺杂半导体材料的敏感单元用于检测氧化性气体;所述基于p型掺杂半导体材料的敏感单元用于检测还原性气体。为了消除环境中其他气体因素对气体传感器自身性能的影响,上述方法均是通过增加气敏元件的方式来实现抗干扰,这就意味着传感器体积的增大,同时带来功耗的增加和传感器封装工序的增多。传统的半导体可燃气体传感器在实现抗干扰时,可以采用双层厚膜涂覆,但是基于mems技术的半导体可燃气体传感器结构微型化,对于气敏元件厚度的要求更为苛刻,无法采用双层厚膜涂覆。而实施例3所述气敏涂层15,仅单层涂覆气敏涂层15、不额外增加气敏模块,就可实现在检测目标气体时抗羟基(-oh)类有机挥发性气体的干扰。
55.为了观察气敏涂层15的微观组织形貌,将实施例3所述混合浆料直接涂覆上陶瓷基板上(涂覆厚度为0.2mm),经烧结后(以50℃/min的升温速率升温至730℃,恒温烧结3.5小时)形成样品涂层,对该样品涂层进行扫描电镜表征,结果如图6所示。从图6可以看到,样品涂层的微观形貌呈蜂窝状离散分布,同时存在大量介孔,可燃气体小分子气流通过介孔被贵金属催化剂捕捉,进而发生氧化还原反应,引起电位变化实现对可燃气体气体(如甲烷、丙烷、异丁烷等)检测,表面纳米二氧化硅包覆,隔绝醇类中羟基,实现抗酒精干扰。
56.为了测试实施例3所述半导体可燃气体传感器的气敏性能,将上述半导体可燃气体传感器连接印刷电路板,并置于检测环境中。印刷电路板上通过加热引脚为加热电极11提供所需电源,使其发出固定条件的温度给气敏涂层15,被测气体到达固定温度的气敏涂层15表面,并与气敏涂层15内部的自由电荷进行氧化还原反应,在反应过程中伴随电荷转移,进而引起气敏涂层15材料电阻的变化,材料测量端电阻的变化直接引起电压变化,通过测试电极4读取电压值,通过对电压差的变化就可以实现对气体浓度的检测。
57.由于半导体可燃气体传感器的气敏特性受工作温度影响,下面检测实施例3所制备的半导体可燃气体传感器在不同工作温度下(250~600℃)对甲烷(5000ppm)的响应情况。按照gb 15322.2-2003规范条件进行重复测试,使用现有数据采集系统,在传感器正常工作条件下,对传感器相匹配的固定阻值的分压测量电阻的电压进行采集,通过采集分压测量电阻在注气前后的电压变化,得出传感器半导体气敏材料的响应变化量,以此来判定传感器的气敏性能。
58.经检测得出,随着工作温度的升高,半导体可燃气体传感器对甲烷的响应值逐渐增大,当工作温度升至450℃时,响应值达到最大,随着温度的进一步升高,半导体可燃气体传感器对甲烷的响应值反而下降。这是因为,在温度较低时,没有足够的能量支持气敏反应,因此随着温度的升高,灵敏度增加;当温度过高时,气体在材料表面的吸附变得更困难,即吸附在材料表面的气体还未反应就已经脱附,导致参与气敏过程的分子数降低,从而使灵敏度有所下降。实施例1所述半导体可燃气体传感器在450℃对5000ppm甲烷表现出了最大的响应值(传感器对5000ppm甲烷的读数值减去零点值),约为2.21v。并且,加热模块加热到450℃时所需功率仅为16mw。
59.通过检测实施例3所述半导体可燃气体传感器在450℃对5000ppm甲烷的响应恢复情况,计算得出实施例1所述半导体可燃气体传感器在450℃对5000ppm甲烷的响应、恢复时间,分别为3s和6s,可见该半导体可燃气体传感器具有较快的响应恢复速度。所述半导体可燃气体传感器在接触甲烷气体后,迅速响应,接触空气时快速恢复,其响应及恢复特征在整个测试期间几乎一致。
60.为了验证实施例3所述半导体可燃气体传感器对甲烷检测的重复性,于不同时间、在450℃的工作温度下对该传感器实施了连续15次的检测,响应数据(传感器读数值)如表1所示。
61.表1实施例3所述半导体可燃气体传感器对不同浓度甲烷检测结果(单位/v)
62.[0063][0064]
从表1中可以看出,随着测试甲烷浓度的增大,当甲烷浓度大于500ppm,半导体可燃气体传感器的响应值表现出明显的阶梯状分布,响应值变化与甲烷浓度近似呈线性关系。此外,该传感器对低至50ppm的甲烷的响应值约为0.25v,表现出了良好的低浓度甲烷检测能力。并且,该传感器的最大响应值仅有较小幅度的变化。这说明半导体可燃气体传感器在450℃的工作温度下对甲烷气体具有良好的重复性。
[0065]
下面对实施例3所述半导体可燃气体传感器的抗干扰气敏性能进行检测,制备5个平行试样,每个试样测试5次,最后取平均值。在2000ppm酒精蒸汽环境中的读数减去零点值,即为传感器对2000ppm酒精的响应值,在5000ppm甲烷气体浓度中的数值减去零点值,即为传感器对5000ppm甲烷的响应值。5000ppm甲烷响应值减去2000ppm酒精响应值,即为抗酒精干扰差值。
[0066]
经检测,实施例3所述半导体可燃气体传感器在2000ppm酒精环境下响应值为0.46v,在5000ppm甲烷环境下响应值为2.21v,甲烷与干扰气体差值均能达到700mv以上的落差,持续12个月重复使用后,响应值无明显衰减。
[0067]
综上所述,本发明制备的半导体可燃气体传感器,产品不仅一致性好,而且检测数据具有良好的稳定性,检测灵敏度高,响应/恢复时间短,通过涂覆单层气敏涂层15,可以用于检测甲烷、丙烷、异丁烷等气体,还可稳定实现抗酒精挥发干扰。
[0068]
最后应说明的是:以上各实施例仅用以说明本发明的技术方案,而非对其限制;尽管参照前述各实施例对本发明进行了详细的说明,本领域的普通技术人员应当理解:其依然可以对前述各实施例所记载的技术方案进行修改,或者对其中部分或者全部技术特征进行等同替换;而这些修改或者替换,并不使相应技术方案的本质脱离本发明各实施例技术方案的范围。