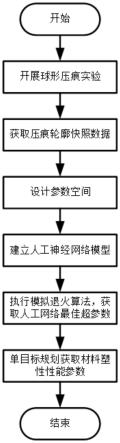
1.本发明属于材料塑性力学性能测试方法技术领域,涉及一种基于人工神经网络及压入测试的材料力学参数识别方法。
背景技术:2.多年来,材料塑性力学性能参数的测量一直是一个长期存在的课题。在传统测量材料塑性力学参数的方法之中,通常采用多次单轴拉伸/压缩实验。但是,传统的试验方法属于一种破坏性的实验,在测量之前需要制备指定形状的测试样品,较为耗时,并不适用于有限体积的样品或者在役件的材料塑性力学参数的测量。因此,对于有限体积的样品或者在役件,寻找一种节约样品、省时省力的实验方法来测量材料塑性力学参数就尤为重要。
3.近年来,仪器化压痕测试技术给金属材料塑性力学性能的实验检测提供了极大便利。相比于常规的拉伸实验而言,压痕测试方法更加的简便、灵活。并且,该种测试方法能够适用于很多单轴拉伸测试方法所不能应用的场合,极大地弥补了常规测试方法的不足。由于压痕测试方法的上述优点,逐渐得到了材料性能检测研究领域的着重关注,并且成为当前国际上学术研究的热点问题。
4.随着有限元仿真技术在压痕弹塑性接触变形研究中的深入应用,采用压痕实验并结合一定的数学方法反推被测试材料的塑性力学性能已经成为可能。2014年,moussa等(evaluation of the tensile properties of a material throughspherical indentation:definition of an average representativestrain and a confidence domain,journal of materials science,49(2014)592
–
603)通过合理定义压痕实验加载曲线与一系列有限元仿真曲线的残差,并深入分析残差的分布特征,建立了一种依据压痕曲线获取材料拉伸性能参数的方法。通过该种方法,能够准确获取被测试材料的单轴力学性能,并且与单轴拉伸实验结果吻合较好。
5.基于压痕测试的有限元仿真和迭代最优化计算,一些学者建立了采用压入测试识别金属材料拉伸性能的方法。2019年,o.iracheta等(a holistic inverse approach based on a multi-objective function optimisation model to recover elastic-plastic properties of materials from the depth-sensing indentation test)journal of the mechanics and physics of solids,128(2019)1-20.)基于多目标优化算法,结合berkovich压痕轮廓形貌和载荷位移关系曲线,建立了识别材料拉伸性能参数的方法。
6.在之前的工作中,测量材料性能的数值算法本质上是基于最小化实验和模拟之间的差异,使用有限元模拟和参数更新。一方面,在识别过程中,需要进行有限元仿真模拟计算过程,需要极高的参数识别计算代价,拉低数值计算的效率。另一方面,在进行压痕仿真和模拟之间的误差与材料参数拟合时,存在精度较低,识别误差较大。
技术实现要素:7.本发明的目的是提供一种基于人工神经网络及压入测试的材料力学参数识别方法,解决了现有技术中利用线性拟合等其他方法对压痕实验和仿真之间的误差与材料参数建立联系时拟合精度不足,以及在原有材料性能识别中需要大规模的迭代有限元仿真计算过程等问题。
8.本发明所采用的技术方案是:
9.基于人工神经网络及压入测试的材料力学参数识别方法,包括以下步骤:
10.步骤1,对待测试金属材料开展球形压痕实验,通过激光共聚焦显微测试获取残留在试件表面的压痕轮廓形貌;
11.步骤2,依据ludwigson硬化法则,开展球形压痕有限元仿真,获取一系列与ludwigson硬化法则参数所对应的压痕形貌快照,获得压痕轮廓快照矩阵;
12.步骤3,基于人工神经网络,建立材料拉伸性能参数屈服应力σy、强度因子k和硬化指数n与压痕形貌轮廓之间的直接关联;
13.步骤4,依据机器学习模拟退火算法,建立模拟退火接受函数,并依据此对人工神经网络训练超参数进行优化,以获得人工网络训练最优的人工神经网络训练超参数;
14.步骤5,基于人工神经网络最优超参数构建的人工神经网络及单目标规划,建立单目标规划目标函数约束条件,给定材料拉伸性能参数屈服应力σy、强度因子k和硬化指数n的识别范围,可以得到被测试材料拉伸性能参数的识别结果。
15.本发明的特点还在于:
16.所述步骤1中,压痕轮廓形貌按照轮廓快照的形式表示;其中,n表示压痕轮廓快照y
exp
的维数,向量包含的值是压痕轮廓垂直位移的序列量。
17.所述ludwigson硬化法则表示为:
[0018][0019]
其中,σ为应力;e为弹性模量;ε为应变;σy为屈服应力;k为强度因子;n为硬化指数;ε
p
为塑性应变。
[0020]
所述仿真压痕轮廓快照矩阵y
sim
,且其中,n表示在材料参数设计空间中,用于压痕仿真的材料参数组合的个数。
[0021]
所述人工神经网络包括依次连接的输入层、两层隐藏层和输出层,所述输出层为人工神经网络预测的压痕轮廓数据。
[0022]
材料拉伸性能参数σy、k和n与压痕形貌轮廓之间的表示关系为:
[0023][0024]
其中,矩阵y
pre
为人工神经网络预测的压痕轮廓快照;矩阵w1、w2和w3分别为第1、2、3层神经网络的权重系数矩阵;矩阵b1和b2分别为第1、2层神经网络的偏置矩阵,为列向量;矩阵x为代表拉伸性能参数σy、k和n的行向量;σ(x)为第3层神经网络的激活函数,为线性函
数;为第1、2层人工神经网络的激活函数,取sigmoid函数,将其定义为:
[0025][0026]
所述步骤4中,基于模拟退火算法,引入随时间变化的温度变量t(t)和温度变化系数α;在退火迭代进行过程中,温度变量定义为:
[0027]
t(t+1)=αt(t)
ꢀꢀꢀꢀꢀꢀꢀꢀꢀꢀꢀꢀꢀꢀꢀꢀꢀꢀ
(5)
[0028]
当前优化的神经网络隐含层数为两层,初始的神经网络节点组合使用该组超参数进行网络训练,返回评判神经网络训练好坏及泛化能力的预测集平方和误差e
(n0)
,在二维空间中n(i)的周围高维半径内随机生成新的网络节点组合n
(i+1)
,重复训练获得新的网络训练预测集平方和误差e
(ni+1)
;若e
(ni+1)
>e
(ni)
,则接受该节点组合;反之,系统以一定的概率接受该网络节点组合;模拟退火算法接受概率正比于神经网络压痕轮廓预测值与压痕轮廓真实值之间的均方根误差,表示为
[0029][0030]
其中,p表示模拟退火算法接受概率;y
pre
表示神经网络压痕轮廓预测值矩阵;y
ture
表示压痕轮廓的真实值矩阵;n表示压痕轮廓快照y
exp
的维数;
[0031]
构建模拟退火算法概率函数表示为:
[0032][0033]
其中,t
t
表示为时刻t时的温度,记为t
t
=α
t
t0,α常取0.95,t0为初始温度。
[0034]
所述步骤5中单目标规划目标函数及约束条件,其表示为:
[0035][0036]
其中,n表示压痕轮廓快照y
exp
的维数;y
exp
表示实验压痕轮廓快照,向量包含的值是压痕轮廓垂直位移的序列量;y
pre
表示神经网络压痕轮廓预测值快照;σ
ymin
和σ
ymax
表示所建数据库材料屈服应力σy的最小值和最大值;k
min
和k
max
表示所建数据库材料强度因子k的最小值和最大值;n
min
和n
max
表示所建数据库材料硬化指数n的最小值和最大值;
[0037]
采用单目标规划求解方法对上述单目标规划目标函数及约束条件进行求解,可以得到被测试材料拉伸性能参数屈服应力σy、强度因子k和硬化指数n的识别结果。
[0038]
本发明的有益效果是:
[0039]
(1)本发明采用压痕实验得到的压痕轮廓来获取金属材料的拉伸性能参数,能够有效的避免传统拉伸实验测试过程中的试件制备的繁琐过程,避免了材料被破坏而浪费的
问题,同时也可以将其推广到在役件材料性能检测。采用卸载残留的压痕轮廓形貌作为参数识别中有效的材料相应信息,能够有效避免对压痕加载和卸载过程中载荷-位移关系曲线的准确测量,不需要额外了解压痕加载中材料的变形历史,同时,卸载残留压痕轮廓获取方便、灵活。
[0040]
(2)本发明基于机器学习中的人工神经网络建立了压痕轮廓快照与材料性能的直接有效关联,通过输入材料性能参数,即可得到材料压痕轮廓仿真数据,避免了原有材料性能识别中大规模的迭代有限元仿真计算过程,降低了参数识别计算代价,提高了数值计算的效率。
[0041]
(3)本发明在构建人工神经网络时,使用了机器学习算法中的模拟退火算法对所建立的人工神经网络进行优化,从而能够得到预测更加准确的人工神经网络超参数,避免了由于预测压痕轮廓而导致在识别过程中而引入的误差,导致识别结果不准确,其所得到的人工神经网络超参数能够更好的预测给定参数下的材料压痕轮廓数据,降低了由于预测而导致的误差,提高了识别精度。
附图说明
[0042]
图1为本发明的步骤示意图;
[0043]
图2为在球形压痕加载下的压入测试模型,1为球形压头,2为试件;
[0044]
图3为实施例1中2099-t83铝锂合金材料在612.75n力载荷作用下的残留压痕轮廓快照,表示为y
exp
;
[0045]
图4为实施例1中用于压痕仿真的轴对称有限元模型;
[0046]
图5为实施例1中使用已建立的人工神经网络预测不同材料塑性参数下的压痕形貌轮廓与仿真值的对比;
[0047]
图6为实施例1中使用已建立的机器学习模拟退火算法获取的人工神经网络超参数。
[0048]
图7为实施例1中使用已建立的机器学习模拟退火算法获取的模拟退火当前和最小误差曲线。
[0049]
图8为实施例1中建立的神经网络训练过程训练性能曲线;
[0050]
图9为实施例1中基于人工神经网络的单目标规划识别材料屈服应力σy的识别结果及迭代过程;
[0051]
图10为实施例1中基于人工神经网络的单目标规划识别材料强度因子k的识别结果及迭代过程;
[0052]
图11为实施例1中基于人工神经网络的单目标规划识别材料硬化指数n的识别结果及迭代过程;
[0053]
图12为实施例1中2099-t83铝锂合金单轴拉伸曲线与采用ludwigson硬化法则拟合曲线的对比。
[0054]
图中:1.压头,2.试件。
具体实施方式
[0055]
下面结合附图和具体实施方式对本发明进行详细说明。
[0056]
本发明于人工神经网络的金属材料力学参数识别方法,如图1,包括以下步骤:
[0057]
步骤1:将待测试金属试件的表面进行抛光处理,如图2,压头1和试件2开展球形压痕实验。球形压痕实验在布氏硬度计下进行,加载方式为载荷控制模式。压头卸载后,在试件表面残留下球形压痕的轮廓形貌;采用激光共聚焦显微镜测试来获取残留在试件表面压痕轮廓快照的实验数据。压痕轮廓快照表示为向量y
e x
,且y
exp
∈rn。其中,n表示压痕轮廓快照y
exp
的维数,向量包含的值是压痕轮廓垂直位移的序列量。
[0058]
步骤2:依据ludwigson硬化法则,建立材料塑性参数的设计空间,开展一系列球形压痕有限元仿真,建立仿真压痕轮廓快照矩阵y
sim
。
[0059]
ludwigson硬化法则表示为:
[0060][0061]
其中,σ为应力;e为弹性模量;ε为应变;σy为屈服应力;k为强度因子;n为硬化指数;ε
p
为塑性应变。
[0062]
仿真压痕轮廓快照矩阵y
sim
表示为:
[0063][0064]
其中,y
sim
∈r
n*n
,n表示在材料参数设计空间中,用于压痕仿真的材料参数组合的个数。因此,仿真轮廓快照向量是对应于第i个材料参数组合的有限元仿真得到的。表示ludwigson硬化法则参数,且
[0065]
步骤3:建立人工神经网络包括依次连接的输入层、两层隐藏层和输出层,所述输出层为人工神经网络预测的压痕轮廓数据。基于人工神经网络,建立材料性能参数与压痕轮廓之间的函数关系。
[0066]
材料拉伸性能参数σy、k和n与压痕形貌轮廓之间的表示关系为:
[0067][0068]
其中,矩阵y
pre
为人工神经网络预测的压痕轮廓快照;矩阵w1、w2和w3分别为第1、2、3层神经网络的权重系数矩阵;矩阵b1和b2分别为第1、2层神经网络的偏置矩阵,为列向量;矩阵x为代表拉伸性能参数σy、k和n的行向量;σ(x)为第3层神经网络的激活函数,为线性函数;为第1、2层人工神经网络的激活函数,取sigmoid函数,将其定义为:
[0069][0070]
步骤4:采用机器学习中的模拟退火算法对所建立的人工神经网络超参数进行优化。基于模拟退火算法,引入随时间变化的温度变量t(t)和温度变化系数α。在退火迭代进行过程中,温度变量定义为:
[0071]
t(t+1)=αt(t)
ꢀꢀꢀꢀꢀꢀꢀꢀꢀꢀꢀꢀꢀꢀꢀꢀꢀꢀ
(5)
[0072]
当前优化的神经网络隐含层数为两层,初始的神经网络节点组合使用该组超参数进行网络训练,返回评判神经网络训练好坏及泛化能力的预测集平方和误差e
(n0)
。在二维空间中n(i)的周围高维半径内随机生成新的网络节点组合n
(i+1)
,重复训练获得新的网络训练预测集平方和误差e
(ni+1)
。若e
(ni+1)
>e
(ni)
,则接受该节点组合;反之,系统以一定的概率接受该网络节点组合。模拟退火算法接受概率正比于神经网络压痕轮廓预测值与压痕轮廓真实值之间的均方根误差,表示为
[0073][0074]
其中,p表示模拟退火算法接受概率;y
pre
表示神经网络压痕轮廓预测值矩阵;y
ture
表示压痕轮廓的真实值矩阵;n表示压痕轮廓快照y
exp
的维数。
[0075]
构建模拟退火算法概率函数表示为:
[0076][0077]
其中,t
t
表示为时刻t时的温度,记为t
t
=α
t
t0,α常取0.95,t0为初始温度。
[0078]
步骤5:基于人工神经网络最优超参数构建的人工神经网络及单目标规划,建立单目标规划目标函数及约束条件,并进一步采用单目标规划求解方法对上述单目标规划目标函数及约束条件进行求解,可以得到被测试材料拉伸性能参数屈服应力σy、强度因子k和硬化指数n的识别结果。
[0079]
单目标规划目标函数及约束条件其表示为:
[0080][0081]
其中,n表示压痕轮廓快照y
exp
的维数;y
exp
表示实验压痕轮廓快照,向量包含的值是压痕轮廓垂直位移的序列量;y
pre
表示神经网络压痕轮廓预测值快照;σ
ymin
和σ
ymax
表示所建数据库材料屈服应力σy的最小值和最大值;k
min
和k
max
表示所建数据库材料强度因子k的最小值和最大值;n
min
和n
max
表示所建数据库材料硬化指数n的最小值和最大值。
[0082]
下面通过具体实施例来进一步说明本发明方法的效果。
[0083]
实施例1
[0084]
步骤1,如图2,为球形压痕加载下的压入测试。将2099-t83铝锂合金材料的表面进行抛光处理,开展球形压痕实验。球形压痕实验在布氏硬度计下进行,加载方式为载荷控制模式。如图3,通过激光共聚焦显微测试来获取残留在试件表面的压痕轮廓形貌实验数据,通过b样条曲线拟合压痕轮廓快照,以平滑压痕轮廓实验数据,降低实验误差扰动。步骤2,如图4,在给定材料塑性参数区间内开展大量的球形压痕有限元仿真,获取压痕轮廓快照矩阵y
sim
。所选取的材料塑性参数计算区间为260mpa≤σy≤380mpa,180mpa≤k≤300mpa,0.05
≤n≤0.35。铝锂合金的弹性模量假定为已知量,取定值为77.68gpa。通过在给定材料塑性参数区间内开展大量的球形压痕有限元仿真,建立压痕轮廓快照矩阵y
sim
。
[0085]
步骤3,如图5,建立的人工神经网络包括依次连接的输入层、两层隐藏层和输出层,所述输出层为人工神经网络预测的压痕轮廓数据。基于人工神经网络,建立ludwigson本构模型材料性能参数与压痕轮廓之间的函数关系,表示为:
[0086][0087]
其中,矩阵y
pre
为人工神经网络预测的压痕轮廓快照;矩阵w1、w2和w3分别为第1、2、3层神经网络的权重系数矩阵;矩阵b1和b2分别为第1、2层神经网络的偏置矩阵,为列向量;矩阵x为代表拉伸性能参数σy、k和n的行向量;σ(x)为第3层神经网络的激活函数,为线性函数;为第1、2层人工神经网络的激活函数,取sigmoid函数,将其定义为:
[0088][0089]
步骤4,如图6、图7和图8,基于模拟退火算法,引入随时间变化的温度变量t(t)和温度变化系数α;在退火迭代进行过程中,温度变量定义为:
[0090]
t(t+1)=αt(t)
ꢀꢀꢀꢀꢀꢀꢀꢀꢀꢀꢀꢀꢀꢀꢀꢀꢀꢀ
(5)
[0091]
当前优化的神经网络隐含层数为两层,初始的神经网络节点组合使用该组超参数进行网络训练,返回评判神经网络训练好坏及泛化能力的预测集平方和误差e
(n0)
,在二维空间中n(i)的周围高维半径内随机生成新的网络节点组合n
(i+1)
,重复训练获得新的网络训练预测集平方和误差e
(ni+1)
。若e
(ni+1)
>e
(ni)
,则接受该节点组合;反之,系统以一定的概率接受该网络节点组合;模拟退火算法接受概率正比于神经网络压痕轮廓预测值与压痕轮廓真实值之间的均方根误差,表示为
[0092][0093]
其中,p表示模拟退火算法接受概率;y
pre
表示神经网络压痕轮廓预测值矩阵;y
ture
表示压痕轮廓的真实值矩阵;n表示压痕轮廓快照y
exp
的维数;
[0094]
构建模拟退火算法概率函数表示为:
[0095][0096]
其中,t
t
表示为时刻t时的温度,记为t
t
=α
t
t0,α常取0.95,t0为初始温度。
[0097]
步骤5,基于人工神经网络最优超参数构建的人工神经网络及单目标规划,建立单目标规划目标函数及约束条件,表示为:
[0098]
[0099]
其中,n表示压痕轮廓快照y
exp
的维数;y
exp
表示实验压痕轮廓快照,向量包含的值是压痕轮廓垂直位移的序列量;y
pre
表示神经网络压痕轮廓预测值快照;σ
ymin
和σ
ymax
表示所建数据库材料屈服应力σy的最小值和最大值;k
min
和k
max
表示所建数据库材料强度因子k的最小值和最大值;n
min
和n
max
表示所建数据库材料硬化指数n的最小值和最大值。
[0100]
进一步采用单目标规划求解方法对上述单目标规划目标函数及约束条件进行求解,可以得到被测试材料拉伸性能参数屈服应力σy、强度因子k和硬化指数n的识别结果。识别迭代过程如图9-11。
[0101]
如图12,对2099-t83铝合金材料进行拉伸实验,通过ludwigson法则进行拟合,得出材料拉伸性能参数。通过拉伸实验所得材料拉伸性能参数与本方法所得材料拉伸性能参数进行对比。表1中所示为采用ludwigson硬化法则拟合所得2099-t83铝锂合金材料的单轴拉伸塑性性能参数。表2中所示为2099-t83铝锂合金拉伸性能参数的单轴结果与压痕测试结果对比。
[0102]
表1采用ludwigson硬化法则拟合所得2099-t83铝锂合金的单轴性能参数
[0103][0104][0105]
表2 2099-t83铝锂合金拉伸性能参数的单轴结果与压痕测试结果对比
[0106][0107]
通过分析表2中2099-t83铝锂合金单轴拉伸性能参数与依据本发明所提出方法识别所得拉伸性能参数对比可以得到如下结论:
[0108]
1)采用本发明识别所得2099-t83铝锂合金拉伸性能参数准确度高,与单轴实验误差非常小,与预期结果吻合非常好。
[0109]
2)本发明实施过程简单,将压痕轮廓作为有效实验数据,避免了对压痕载荷-位移关系曲线的测量,降低了实验的难度,更容易执行。
[0110]
3)本发明专利在进行材料塑性性能参数识别时,不需要大规模的迭代有限元仿真计算过程,降低了参数识别计算代价,提高了数值计算的效率。