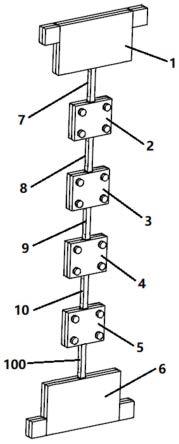
sicf/sic复合材料拉伸比例极限的高通量测试夹具及方法
技术领域
1.本发明属于材料力学性能测试技术领域,特别涉及一种sicf/sic复合材料拉伸比例极限的高通量测试夹具及方法。
背景技术:2.sicf/sic复合材料通过在sic基体中引入增强相sic纤维,可以极大的提升sic陶瓷材料本身的韧性,解决sic自有的高脆性问题,同时保留sic陶瓷材料原本具有的高温耐磨等优良特性,被广泛应用于航空航天、军工、机械、化工、电子技术等领域。
3.sicf/sic复合材料的拉伸应力-应变曲线往往呈现非线性特征,曲线偏离线性的转折点对应基体中贯穿裂纹的萌生,此后由于基体裂纹的扩展、纤维的拔出、界面滑移、纤维断裂等,导致材料刚度下降,该转折点所对应的应力通常称为基体开裂强度,或者比例极限应力。对于sicf/sic复合材料,拉伸比例极限是最重要的设计用力学性能数据,结构设计时均以拉伸比例极限作为最大可用强度,这是因为一旦基体开裂,服役环境中的介质将通过基体中的裂纹进入材料内部,使材料性能被环境腐蚀而发生严重退化。另外,有研究表明sicf/sic的拉伸比例极限与材料的疲劳性能直接相关,拉伸比例极限高的sicf/sic具有更长的寿命和更高的疲劳极限,因此对于sicf/sic复合材料而言,拉伸比例极限比拉伸强度数据更具有使用价值,不仅是结构设计许用值确定的依据,同时也是衡量sicf/sic复合材料力学性能最重要的指标,因此拉伸比例极限的测试对sicf/sic复合材料具有重要意义。
4.由于拉伸比例极限是衡量sicf/sic复合材料力学性能优劣最重要的指标,因此在sicf/sic研发过程中,拉伸比例极限的测试需求越来越多,目前sicf/sic复合材料拉伸比例极限一般通过对一个标准直条试样的拉伸获得,这种方式所采用的试样尺寸较大,对原材料价格昂贵、工艺成本高的sicf/sic复合材料不具备经济性,因此目前材料研发人员对一种小尺寸的y型端部试样非常青睐,通过采用这种小尺寸试样可以大大缩短制样时间,节省材料成本,可对材料工艺改善效果做出快速评估,有助于缩短材料研发周期。
5.现有技术中,专利cn103018101a“一种用于陶瓷基复合材料高温拉伸测试的夹具”也采用一种y型端部试样,利用试样端部的楔面和一体式夹具中y型榫槽的楔面接触产生的支持力来传递载荷。专利cn 109813610 a“一种陶瓷基复合材料超高温拉伸组合夹具”中也采用一种y型端部试样,夹具采用带y型榫槽的一个半圆台卡件用于连接y型端部试样与试验机,也是利用y型端部试样两端的楔面与夹具中卡槽的楔面接触压紧,实现试样与夹具的自锁。但是上述两个专利均采用的是夹具中加工一个深度大于试样厚度的一体式y型榫槽的设计思想,试验时将试样吊挂与夹具中的y型榫槽中,这种很难保证试样相对于试验机加载线的对中。另外上述两种夹具由于完全靠试样的两个楔形面与夹具楔形面的压紧力传递载荷,经常发生楔面处试样的压溃,导致载荷传递不稳定,甚至试验失败。
6.由于这种小尺寸的y型端部试样加载时所承受的载荷较小,使得试样装载、试验员操作差异等外在因素的影响相比于其对常规试样测试的影响更为显著,如果能在一次加载中同时进行多根试样的加载,则能有效地消除上述误差。此外,小尺寸y型试样尺寸较小,而
拉伸极限的测试不需要将试验件拉断,因此我们考虑将这些小尺寸y型试样首尾相连。为此,需要设计一种专用的工装夹具,并开发一种考虑夹具自重的用于计算不同位置处试样中拉伸应力的方法,提供一种sicf/sic复合材料拉伸比例极限高通量的测试方法,实现在一次试验中同时完成多根试样的拉伸加载。
技术实现要素:7.本发明的目的是:提供sicf/sic复合材料拉伸比例极限的高通量测试夹具及方法,设计一种可实现多个试样首尾相连及其试样与试验机连接的夹具,通过一次加载同时完成若干个试样拉伸的测试,同时开发一种分别获得y型端部试样标距段真实拉伸应力-应变曲线的方法,以解决sicf/sic复合材料拉伸比例极限的高通量测试,并消除试样装载有关的人为系统误差,实现sicf/sic拉伸比例极限测试效率和精度的双提升。
8.为解决此技术问题,本发明的技术方案是:
9.一方面,提供一种sicf/sic复合材料拉伸比例极限的高通量测试夹具,
10.所述高通量拉伸测试夹具通过保持每个试样加载状态的对中性,实现多个试样的首尾相连,并在加载时利用夹具和试样自锁,将试验机的载荷有效传递到每个试样的标距段,实现在一次力学试验中同时完成多个试样的拉伸;
11.所述高通量拉伸测试夹具分为两部分:与试验机连接部分和多个试样之间连接的部分;
12.所述与试验机连接部分由4个中间加工梯形槽的t形夹板构成,两两组成一对使用,其中梯形槽的形状与试样y型端部的形状相似,斜面一致,两者的斜面能相互契合,将第1根y型端部小试样的上端夹在一对t形夹板中间,而y型端部小试样的上端部分恰好可被卡到2个t形夹板的梯形槽中,试验时将这一对t形夹板夹持到试验机的上夹头中;另外2个t形夹板也组成一对,将最后1根y型端部小试样的下端夹在中间,而y型端部小试样的下端部分也正好卡到2个t形夹板的梯形槽中,试验时将这一对t形夹板夹持到试验机的下夹头中;
13.所述工装夹具中多个试样之间相连部分由n对两两组合的矩形小夹板组成,其中每个矩形小夹板的上、下两端镜像对称地加工两个与y型试样端部构型相似的梯形槽,y型端部小试样的端部可恰好卡在其中,每个试样的下端与其下面相邻的试样的上端被卡到同一对矩形小夹板镜像对称的梯形槽中,并用螺栓将2个矩形小夹板和试样固定夹紧。
14.拉伸试验中,处于拉伸状态时,每个试样被吊挂于夹具中,由于y型端部试样的端部与一对夹板中梯形槽的形状契合,拉伸载荷作用下,夹具与试样之间的配合越来越紧密,可有效传递载荷,因此试验机的载荷可通过这一套可实现拉伸自锁的夹具/试验组合件,将试验机的拉伸载荷传递到每个试样的标距段。
15.所述n取决于待测试的试样数量,n为试样数量减1。
16.与试验机连接的所述2对t形夹板,以及中间的n对用于多个试样首尾相连的矩形小夹板完全贴合时,中间所构成的梯形槽的深度比试样的厚度略小(贴合后梯形槽的深度小于试样的厚度),这样的设计可以适应变化的试样厚度,可使每个试样的中心线与试验机的加载线始终精确重合,确保每个试样加载状态的对中性,并确保载荷有效、平稳地在这套加载系统中传递。
17.与试验机连接的2对t形夹板“i形”部分的宽度恰好等于试验机夹块的宽度,夹持
时将其与夹块对齐,即可实现整个加载系统的对中,而t形夹板端部具有手持部,所述手持部是t形夹板端部左、右伸出来的两个形似“翅膀”的小矩形位于夹块外部,是考虑将一对合起来的t形夹板向夹块中夹持时,试验员方便操作而设计的手持部分。
18.每对矩形小夹板通过螺栓固定贴合;每对矩形小夹板中的一个矩形夹板在其4个角加工4个完全相同的通孔,孔直径略大于螺栓直径,以便螺栓顺利穿过,另外一个与之组合的矩形夹板在其4个角加工4个完全相同的螺纹孔,以便螺栓可以拧入。
19.所述夹具适用于端部为y型的sicf/sic试样拉伸性能的测试,具体的试样构型和尺寸可根据实际情况确定。
20.所述试样数量至少3个。使用时可增减试样和用于连接中间部分试样的矩形小夹板的对数,一次可测试的最大试样数量取决于试验机横梁的行程。
21.另一方面,提供一种利用上述sicf/sic复合材料拉伸比例极限的高通量测试夹具进行高通量测试的方法,所述方法利用截面法对每个试样标距段截面进行受力分析,计算每个试样标距段真实拉伸载荷,进一步绘制每个试样的拉伸应力-应变曲线,并根据曲线确定每根试样的拉伸比例极限和拉伸模量;具体步骤如下,其中步骤1)2)没有必然先后顺序可以互换:
22.1)、测试准备:根据对中性的要求完成试样与夹具的装配,得到试样/夹具组合件;
23.2)、在测试时对每个试样的前、后表面中心处粘贴应变计,试验过程中监控所有试样前、后表面粘贴的应变计的示值,以每个试样前、后表面应变计示值的平均值作为试样的拉伸应变;
24.3)、以恒定的加载速率对组合件进行加载,直到其中任意一个试样发生断裂,加载过程中记录试验机的载荷和每个试样表面粘贴的应变计的应变数据;
25.4)、根据为每个试样计算得到的拉伸应力和为每个试样测得的拉伸应变,绘制每个试样的拉伸应力-应变曲线,根据拉伸应力-应变曲线偏离初始线性段时对应的应力水平确定拉伸比例极限,根据应力-应变曲线初始线性段的斜率计算每个试样的拉伸模量。
26.所述方法适用于室温环境下sicf/sic复合材料拉伸比例极限的测试。
27.本发明的有益效果是:
28.1、本发明的sicf/sic复合材料拉伸比例极限的高通量测试夹具,可在一次试验中同时获得多个试样的拉伸比例极限,大大提高试验效率。
29.2、本发明的sicf/sic复合材料拉伸比例极限的高通量测试夹具,能够消除一组待测试样分开测试可能引入试验操作误差,减少可能的数据分散源。
30.3、本发明的sicf/sic复合材料拉伸比例极限的高通量测试夹具,与试验机连接的2对t形夹板,以及中间的若干对用于试样之间首尾相连的矩形小夹板完全贴合时形成的梯形槽的深度比试样厚度略小,这种设计确保当试样厚度变化时,每个试样的中心线始终保持相对试验机加载线的精确对中。
31.4、本发明的sicf/sic复合材料拉伸比例极限的高通量测试方法,采用若干对分体式的,中间开梯形槽的夹板将y型试样夹在中间,并通过试验机夹头或者螺栓拧紧,此时夹具向y型试样的载荷传递方式包括试样左、右两个楔形面的接触压力和试样前、后表面处的摩擦力,有效避免一体式楔形槽夹具使用时,容易在试样端部两侧楔形面处被压溃的问题。
附图说明
32.为了更清楚地说明本发明实施的技术方案,下面将对本发明的实例中需要使用的附图作简单的解释。显而易见,下面所描述的附图仅仅是本发明的一些实施例,对于本领域的技术人员来讲,在不付出创造性劳动的前提下,还可以根据这些附图获得其他的附图。
33.图1高通量拉伸测试夹具的结构示意图;
34.图2两对t形夹板的结构及其与试样的装配细节图;
35.图3一对t形夹板夹紧y形端部试样后的仰视图;
36.图4t形夹板正视图;
37.图5中间4对矩形夹板将多个试样首尾相连的示意图;
38.图6一对矩形夹具的结构细节图;
39.图7一对矩形夹板夹紧y形端部试样后的俯视图;
40.图8从上到下5根试样的受力分析图;
41.图9sicf/sic复合材料y形端部试样的拉伸应力-应变曲线。
42.其中:1-夹持于试验机上夹块中的一对t型夹板,2、3、4、5-分别为从上到下第1对、第2对、对3对、第4对用于连接中间部分试样的矩形夹板,6-夹持于试验机下夹块中的一对t型夹板,7、8、9、10、100-分别为从上到下第1根、第2根、第3根、第4根、第5根y型端部小试样,11、12-夹持于试验机上夹块中的一对t型夹板中两个分开的夹板,61、62-夹持于试验机下夹块中的一对t型夹板中两个分开的夹板,21、22-从上到下第1对用于连接中间部分试样的矩形小夹板两个分开的夹板,31、32-从上到下第2对用于连接中间部分试样的矩形小夹板两个分开的夹板;41、42-从上到下第3对用于连接中间部分试样的矩形小夹板两个分开的夹板,51、52-从上到下第4对用于连接中间部分试样的矩形小夹板两个分开的夹板,110-t型夹板11中的梯形槽,120-t型夹板12中的梯形槽,610-t型夹板61中的梯形槽,620-t型夹板62中的梯形槽,111-一对t型夹板与试样完成装配后形成的缝隙,210-t型夹板21中镜像对称分布的梯形槽,220-t型夹板22中的镜像对称分布的梯形槽,23、24-从上到下第1对矩形小夹板中穿过的拧紧螺栓,215-从上到下第1对矩形小夹板与试样完成装配后形成的缝隙,211、212、213、214-第一对矩形小夹板其中之一上分布于四个角的通孔,221、222、223、224-第一对矩形小夹板中的另一个上分布于4个角的螺纹孔。
具体实施方式
43.为使本发明实施例的目的、技术方案和优点更加清楚,下面将结合本发明实施例中的附图,对本发明实施例中的技术方案进行清楚、完整地描述。下面将详细描述本发明实施例的各个方面的特征。下面结合实施例对本发明作更进一步的说明,本实施例中一次加载中涉及的sicf/sic复合材料y型端部拉伸试样数量为5个。
44.一、概述
45.本实施例的sicf/sic复合材料拉伸比例极限的高通量测试方法,包括一种可实现高通量拉伸测试的夹具和确定加载系统不同方位处试样标距段真实拉伸应力-应变曲线的方法。其中,高通量拉伸测试夹具通过精巧设计实现多个试样的首尾相连,并在加载时利用夹具和试样自锁,将试验机的载荷有效传递到每个试样的标距段,实现在一次力学试验中同时完成至少5个试样的拉伸。拉伸应力的数据处理方法考虑夹具自重的影响,利用截面法
对每个试样标距段截面进行精细受力分析,计算每个试样标距段真实拉伸载荷,进而确定每个试样的拉伸应力-应变曲线,并根据拉伸应力-应变曲线确定每个试样的拉伸比例极限。
46.本方法适用于端部为y型的sicf/sic试样拉伸性能的测试,具体的试样构型和尺寸可根据实际情况确定,另外本方法适用于常温环境下sicf/sic复合材料拉伸比例极限的测试,可在一次加载中实现至少5个sicf/sic拉伸试样的测试,使用时可增减试样以及用于连接中间部分试样的矩形小夹板的对数,一次加载中可测试的最大试样数量取决于试验机横梁的行程。
47.二、本实施例的高通量拉伸测试的夹具结构
48.本实施例可实现高通量拉伸测试的夹具,该夹具通过精巧地设计实现多个试样的首尾相连,并在加载时利用夹具和试样自锁,将试验机的载荷有效传递到每个试样的标距段,在一次力学试验中同时完成待测的5个y型端部试样的拉伸,夹具的结构形式如图1~7所示。
49.如图1所示,该夹具可分为两部分,即与试验机连接部分1、6和用于试样之间相连的部分2、3、4、5。如图2所示,与试验机连接部分由4个中间加工梯形槽的t形夹板11、12、61、62构成,11、12组成一对使用,61、62组成一对使用,t形夹板11的一端中间位置处加工形状与y型试样端部形状相似的梯形槽110,t形夹板12一端中间位置处加工形状与y型试样端部形状相似的梯形槽120,t形夹板61一端中间位置处加工形状与y型试样端部形状相似的梯形槽610,t形夹板62一端中间位置处加工形状与y型试样端部形状相似的梯形槽621。从上到下第1根y型端部试样7的上端部分恰好可被卡夹到2个t形夹板11、12的梯形槽110、120处,试验时可将y型端部小试样7的上端夹在一对t形夹板11、12中间,试验时将这一对t形夹板1夹持到试验机的上夹头中。另外2个t形夹板61、62也组成一对,最后1根y型端部试样100的下端卡到2个t形夹板61、62的梯形槽610、620中,试验时可将最后1根y型端部小试样100的下端恰好可被卡夹到一对t形夹板61、62梯形槽610、620处,试验时将这一对t形夹板夹持2到试验机的下夹头中。
50.此外,与试验机连接的2对t形夹板合起来时,构成的梯形槽的深度比试样的厚度略小,这样的设计可以适应变化的试样厚度,可使每个试样的中心线与试验机的加载线重合,确保每个试样加载状态的精确对,并有利于载荷有效、平稳地在这套加载系统中传递。以夹持于试验机上夹块中的一对t形夹板11、12为例,见图3,当y型端部试样7的上端卡夹在一对t形夹板11、12的梯形槽110、120处时,y型端部试样7的厚度略大于t形夹板11、12上两个梯形槽110、120的深度之和,因此这一对t形夹板11、12不会贴合,而是之间存在一个小缝隙111。
51.此外,被试验机夹头夹持的2对t形夹板“i形”部分115的宽度恰好等于试验机夹块的宽度,夹持时将其与夹块对齐,即可实现整个加载系统的对中,而t形夹板端部左、右伸出来的两个形似“翅膀”的小矩形位于夹块外部,是考虑将一对合起来的t形夹板向夹块中夹持时,试验员方便操作而设计的手持部分。以第一对t形夹板为例,见图4,其中i形”部分115的宽度恰好等于试验机夹块的宽度,而t形夹板端部左、右伸出来的两个形似“翅膀”的小矩形113、114为手持部分。
52.此外,可实现高通量拉伸测试的夹具还包括4对完全相同的用于多个拉伸试样之
间连接的矩形小夹板(从上到下分别为2、3、4、5),每对矩形小夹板都由两个分体的中间开槽的矩形小夹板组成(从上到下,从左到右分别为21、22、31、32、41、42、51、52,见图5)。以第1对矩形小夹板为例,见图6,每个矩形小夹板21、22的上、下两端镜像对称地加工两个与y型试样端部构型相似的梯形槽210、220,y型端部试样的端部可恰好卡夹在其中,y型端部试样7的下端与其下面相邻的y型端部试样8的上端被卡夹到同一对矩形小夹板21、22镜像对称的梯形槽210、220处,并用螺栓将2个矩形小夹板和试样进行固定夹紧。拉伸试验中,每个试样被吊挂于夹具中,由于y型端部试样的端部与夹具中梯形槽的形状恰好契合,拉伸载荷作用下,夹具与试样之间的配合越来越紧密,可有效传递载荷,因此试验机的载荷可通过这一套可实现拉伸自锁夹具/试验组合件,将试验机的拉伸载荷传递到每个试样的标距段。
53.此外,中间的4对用于试样之间连接的矩形小夹板合起来时,构成的梯形槽的深度比试样的厚度略小,这样的设计可以适应每个不同试样厚度的偏差,可保证中间首尾相连的每个试样的中心线均与试验机的加载线重合,确保每个试样加载状态的精确对中,也有利于载荷能有效、平稳地在这套加载系统中传递。以第1对矩形小夹板21、22为例,见图7,当第1根y型端部试样7的下端卡夹到第一对矩形夹板21、22之间,并用螺栓23、24拧紧后,y型端部试样7的厚度略大于矩形夹板21、22两个梯形槽210、220的深度之和,因此一对t形夹板21、22不会贴合,而是之间存在一个小缝隙215。
54.此外,中间的4对用于试样之间连接的矩形小夹板具有如下完全相同的结构特征:其中的一个矩形夹板的4个角加工4个完全相同的通孔211、212、213、214,孔直径略大于螺栓直径,以便螺栓顺利穿过,另外一个与之组合的矩形夹板的4个角分别开4个完全相同的螺纹孔221、222、223、224,以便螺栓可以拧入。
55.三、确定加载系统中不同方位处试样标距段真实拉伸应力-应变曲线
56.由于试验载荷较小,为了获得试样标距段真实的应力,夹具的自重不宜忽略。由于夹具的重量,不同空间位置处的试样标距段所受的拉伸载荷是不同的。可根据材料力学经典的截面法对每个试样标距段截面进行精细受力分析,计算每个试样标距段真实的拉伸载荷,对加载系统中每个不同方位处试样的受力分析见图8。如图8(a)所示,从上到下第1个试样标距段的拉伸载荷p1等于试验机载荷p;如图8(b)所示,第2个试样标距段的拉伸载荷p2为试验机载荷p减去其上方1对用于连接试样的矩形小夹块的重力pg,;如图8(c)所示,第3个试样标距段的拉伸载荷p3等于试验机载荷p减去其上方2对用于连接试样的矩形小夹块的重力2pg;如图8(d)所示,第4个试样标距段的拉伸载荷pn等于试验机载荷p减去其上方3对用于连接试样的矩形小夹块的重力3pg;如图8(e)所示,第5个试样标距段的拉伸载荷pn等于试验机载荷p减去其上方4对用于连接试样的矩形小夹块的重力4pg。以每个试样标距段承受的拉伸载荷pi(i=1,2,3,4,5)除以对应试样标距的横截面积,计算得到每个试样标距段所承受的拉伸应力σi(i=1,2,3,4,5)。
57.为了获得每个试样的应变,在测试时对每个试样的前、后表面中心处粘贴应变计,试验过程中监控每个试样前、后表面粘贴的应变计的示值,以每个试样前、后表面应变计示值的平均值作为试样的拉伸应变εi(i=1,2,3,4,5)。以恒定的加载速率对一套装配组合后的夹具/试验组合件进行加载,直到其中任意一个试样发生断裂,加载过程中记录试验机的载荷和每个试样表面粘贴的应变计的应变数据。根据试验记录的数据,以及试样的尺寸确定每个试样的拉伸应力-应变曲线。绘制每个试样的拉伸应力-应变曲线,根据拉伸应力-应
变曲线偏离初始线性段时对应的应力水平确定每个试样的拉伸比例极限,并根据每个试样初始线性段的应力-应变曲线斜率计算拉伸模量。
58.本实施例中,以正交铺层的sicf/sic复合材料为例,测试一组(共计5根)试样在常温下的拉伸比例极限。具体操作如下:
59.1、测量夹具中用于中间部分试样之间连接的一对矩形夹板(带四个螺栓)的质量m,计算的一对矩形夹板的重力,计算公式为:pg=mg。
60.2、分别测量5根试样标距段的宽度和厚度,计算每根试样标距段的截面积si(i=1,2,3,4,5),并在每个试样标距段的前、后表面中心位置处粘贴应变片。
61.3、使用夹具中的4对矩形小夹板将5个试样首尾相连起来,将每个试样的两端卡入每对矩形小夹板其中之一的梯形卡槽处,然后将令一个与之成对使用的小夹板也扣在试样上方,令试样也卡入其中的梯形卡槽处,穿入螺栓后将试样和一对矩形小夹板拧紧。将第1根试样的上端卡入一个t形夹板中,然后将与之成对使用的t形夹板扣在试样上方,令试样也卡入其中的梯形卡槽处,然后将第5根试样的下端卡入一个t形夹板中,然后将与之成对使用的t形夹板扣在试样上方。由此完成试样与夹具的装配,得到试样/夹具组合件。
62.4、由测试人员,手持试样/夹具组合件上、下两端的t形夹板左、右伸出来的两个形似“翅膀”的小矩形部分,将最上方的一对t形夹板夹持于试验机上夹头的一对楔形夹块中,此时对试验机的载荷进行归零,然后将最下方的一对t形夹板夹持于试验机下夹头的一对楔形夹块中。
63.5、为每个试样的应变片连接应变仪,启动试验机,以0.25mm/min的位移速率进行加载,连续采集、记录载过程中记录试验机的载荷和每个试样表面粘贴的应变计的应变数据,直到其中任意一个试样发生断裂。
64.6、利用试验中连续记录的载荷-应变数据,考虑夹具重量,将每列载荷数据作为第1根试样的载荷p1,每列载荷数据减去pg作为第2根试样的载荷p2,每列载荷数据减去一个2pg作为第3根试样的载荷p3,每列载荷数据减去3pg作为第4根试样的载荷p4,每列载荷数据减去4pg作为第5根试样的载荷p5,以每根试样真实的载荷数据除以试样标距段的横截面积si(i=1,2,3,4,5),得到每根试样加载过程中真实的应力数据σi(i=1,2,3,4,5)。每根试样的应变则取为其前、后表面粘贴的应变计数据的平均值εi(i=1,2,3,4,5)。
65.6、绘制每个试样的拉伸应力-应变曲线,如图9所示,根据拉伸应力-应变曲线偏离初始线性段时对应的应力水平确定每个试样的拉伸比例极限,并根据每个试样初始线性段的应力-应变曲线斜率计算拉伸模量。此外,对于5根试样中发生断裂的3#试样,其最大载荷对应的应力值为该3#试样的拉伸强度值,对应的应变值为3#试样的破坏应变。5根试样的试验结果见表1。
66.表1数据结果汇总
67.试样编号拉伸比例极限/mpa拉伸模量/gpa拉伸强度/mpa破坏应变/uε1#115243
ꢀꢀ
2#121238
ꢀꢀ
3#13224225023674#114227
ꢀꢀ
5#105265
ꢀꢀ
68.经试验表明,本发明的拉伸夹具可以很好的应用于sicf/sic复合材料的拉伸比例极限和拉伸模量的测试,同时获得一个拉伸强度和拉伸破坏应变的单个值。夹具没有对y型端部试件的夹持段造成损伤,试样的断裂部位均在标距范围内,表明夹具设计较为合理。5根试样的数据稳定,分散性较小,表明本发明的拉伸比例极限测试方法的可靠性。
69.显然,所描述的实施例是本发明的一部分实施例,而不是全部实施例。基于本发明中的实施例,本领域的普通技术人员在没有做出创造性劳动的前提下,所获得的所有其他实施例,都属于本发明保护的范围。