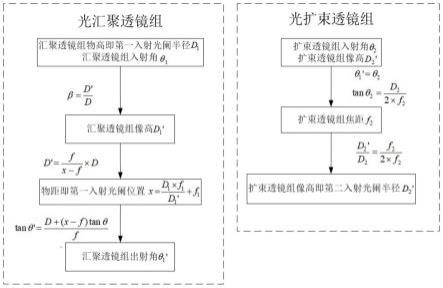
1.本发明涉及气溶胶检测与监测技术领域,尤其涉及一种颗粒检测传感器及恶劣工况下的颗粒检测方法。
背景技术:2.目前在一些以煤为主要能源的化工工业生产过程中,工艺管线内气体常处于高温高压工况,温度和压力范围分别为100~1500℃和1~10mpa。例如煤气化联合循环(igcc)和增压流化床燃烧联合循环(pfbc)这两种先进燃烧循环的过程中会产生温度400~950℃和压力2~3mpa的高温高压气体。这些工况中,由于存在高温裂解过程,所以高温高压气体中都会含有大量颗粒物杂质。一方面,它们跟随气体流动会冲刷管壁对其造成磨损,降低运输管道的使用年限,并且随着工艺管线中颗粒杂质的增多,颗粒会在管道内壁逐步沉积使管道的横截面积缩小,增大输送气体的阻力导致其运输效率下降。另一方面,颗粒的存在也会附着在燃气轮机的透平叶片表面,使得透平叶片磨损腐蚀,降低了电厂的经济效益。
3.为了控制高压高温气体中颗粒的含量,需在工艺管线中设置除尘净化系统。针对这些除尘设备的净化能力考量,则需要颗粒检测技术通过测量颗粒的粒径分布以及浓度等参数来计算它们的分离效率与分级效率。目前颗粒的检测方法种类很多,主要有天平震荡法、重量法、电容电感法、图像法以及光散射法。其中,基于光散射法的颗粒检测方案已被广泛应用,但目依然存在一些技术缺陷:
4.目前现役的光学粒子计数器采用普通光学透镜组和非耐温耐压的结构设计,所以其应用工况与领域会受到极大限制,广泛应用于常温常压工况的粉体制造和除尘设备设计领域。针对非常温常压工况下的颗粒检测需求,研究者们主要集中在高温常压和常温高压工况。需要改良其中的光学传感器使之具有良好的耐温耐压性能,以适应温度100~1500℃且压强1~10mpa的应用工况;并且,除过突破检测装置的耐温和耐压能力外,仍需解决工况参数的变化引起的光学粒子计数器检测性能波动问题;
5.现役光学粒子计数器的光学系统中的光束为高斯光束,表现出光能分布不均匀的特征,这就会导致颗粒的散射光信号所对应的电压信号无法满足有效信息筛选规定的标准特征,在测量中会产生颗粒的计数和粒径等参数测量误差,直接影响了光学传感器的检测精度。同时也就导致了,现役的光学粒子计数器也难以提升对微纳颗粒的最小粒径的检测能力。
技术实现要素:6.本发明的实施例提供一种颗粒检测传感器及恶劣工况下的颗粒检测方法,能够提升对微纳颗粒的最小粒径的检测能力。
7.为达到上述目的,本发明的实施例采用如下技术方案:
8.颗粒检测传感器包括:基体、入射光路系统和散射光路系统;
9.所述入射光路系统,用于接收光源(1)发出的光线,并射入所述散射光路系统;光
线经过所述散射光路系统最终射入接收器(13);所述基体内部开有通光通孔,所述通光通孔与入射的光路对齐,颗粒导管(8)固定于所述基体上;在所述基体上还设置有为信号输入口a和信号输出口b,信号输入口a处安装有第一光纤耦合器(16),第一光纤耦合器(16)连接光源(1),信号输出口b处安装有第二光纤耦合器(17),第二光纤耦合器(17)连接接收器(13)。信号输入口a、信号输出口b利用第一光纤耦合器(16)和第二光纤耦合器(17),将光源(1)和接收器(13)分别进行耦合。
10.通过所述颗粒检测传感器执行一种恶劣工况下的颗粒检测方法,包括:
11.将所述气体传输管道中的含有颗粒的气体输入颗粒导管(8);启动光源(1),之后通过接收器(13)接收颗粒导管(8)上开设有玻璃视窗透出的散射光,得到散射光信号,之后再将散射光信号转换为电压脉冲信号;根据所述电压脉冲信号的幅值和计数,测量颗粒粒径和颗粒个数。
12.本发明实施例提供的颗粒检测传感器及恶劣工况下的颗粒检测方法,在光学检测系统中提供一个较窄的光学检测区域,使得气体中的颗粒能够以单个颗粒或者较小的粒子微团通过检测区域,能够提高系统的检测精度;且通过光路整形使得入射光以平行的方式射入检测区域,有效的避免了由于高温高压所产生的折射率的影响;另外,由于在检测区域通过添加球面反射镜来扩大散射光的接收角度,增强所接收到的散射光强,提高输出信号的准确性,从而提升对微纳颗粒的最小粒径的检测能力。
附图说明
13.为了更清楚地说明本发明实施例中的技术方案,下面将对实施例中所需要使用的附图作简单地介绍,显而易见地,下面描述中的附图仅仅是本发明的一些实施例,对于本领域普通技术人员来讲,在不付出创造性劳动的前提下,还可以根据这些附图获得其它的附图。
14.图1为本发明实施例提供的设计原理的示意图;
15.图2为本发明实施例提供的光学系统中体现的散射光路的结构图
16.图3为本发明实施例提供的颗粒导管横向截面图;
17.图4为本发明实施例提供的颗粒导管整体结构图,其中,(a)为支架固定式颗粒导管;(b)为法兰固定式颗粒导管;
18.图5为本发明实施例提供的颗粒光学检测传感器整体结构图;
19.图6为本发明实施例提供的传感器封装示意图,其中,(a)为颗粒物检测封装示意图,(b)为支架固定式颗粒导管安装示意图,(c)为颗粒物检监测封装示意图;
20.图7为颗粒导管的安装细节的示意图,其中,a为法兰固定式颗粒导管安装示意图,b为支架固定式颗粒导管安装示意图;
21.图8为本发明实施例提供的方法流程示意图;
22.光源(1)、光束整型器(2)、第一光阑(3)、汇聚透镜组(4)、第二光阑(5)、扩束透镜组(6)、多反射光路系统(7)、平面反射镜(7-1)、球面反射镜(7-2)、离轴抛物面镜(7-3)、颗粒导管(8)、光陷阱(9)、凸凹透镜组(10)、第三光阑(11)、散射光汇聚透镜组(12)、接收器(13)、金属管固定支架(14)、焊接法兰(15)、第一光纤耦合器(16)第二光纤耦合器(17)。
具体实施方式
23.为使本领域技术人员更好地理解本发明的技术方案,下面结合附图和具体实施方式对本发明作进一步详细描述。下文中将详细描述本发明的实施方式,所述实施方式的示例在附图中示出,其中自始至终相同或类似的标号表示相同或类似的元件或具有相同或类似功能的元件。下面通过参考附图描述的实施方式是示例性的,仅用于解释本发明,而不能解释为对本发明的限制。本技术领域技术人员可以理解,除非特意声明,这里使用的单数形式“一”、“一个”、“所述”和“该”也可包括复数形式。应该进一步理解的是,本发明的说明书中使用的措辞“包括”是指存在所述特征、整数、步骤、操作、元件和/或组件,但是并不排除存在或添加一个或多个其他特征、整数、步骤、操作、元件、组件和/或它们的组。应该理解,当我们称元件被“连接”或“耦接”到另一元件时,它可以直接连接或耦接到其他元件,或者也可以存在中间元件。此外,这里使用的“连接”或“耦接”可以包括无线连接或耦接。这里使用的措辞“和/或”包括一个或更多个相关联的列出项的任一单元和全部组合。本技术领域技术人员可以理解,除非另外定义,这里使用的所有术语(包括技术术语和科学术语)具有与本发明所属领域中的普通技术人员的一般理解相同的意义。还应该理解的是,诸如通用字典中定义的那些术语应该被理解为具有与现有技术的上下文中的意义一致的意义,并且除非像这里一样定义,不会用理想化或过于正式的含义来解释。
24.本发明实施例提供一种颗粒检测传感器及恶劣工况下的颗粒检测方法,可以利用光学检测颗粒,主要通过光学系统和颗粒导管两部分。光由光源发出经整型后沿水平方向平行射入光学测量体。在光学测量体内,被测试样由颗粒导管引入,并与入射光束相互作用,发生散射现象,通过收集一定范围内单个颗粒的散射光,用于颗粒粒径、个数和浓度等参数的测量。如图1、5所示,包括:
25.基体、入射光路系统和散射光路系统;
26.所述入射光路系统,用于接收光源(1)发出的光线,其中,在所述入射光路系统中,光源(1)发出的光线依次经过光束整型器(2)、第一光阑(3)、汇聚透镜组(4)、第二光阑(5)和扩束透镜组(6),射入所述散射光路系统;扩束透镜组(6)的主要作用是扩展激光直径,减小发散角。
27.在所述散射光路系统中,包括:多反射光路系统(7)、颗粒导管(8)、凸凹透镜组(10)、第三光阑(11)和散射光汇聚透镜组(12),光线经过所述散射光路系统最终射入接收器(13);其中,由光束整型器(2)、第一光阑(3)、第二光阑(5)、第三光阑(11)、汇聚透镜组(4)、扩束透镜组(6)、多反射光路系统(7)、凸凹透镜组(10)和散射光汇聚透镜组(12)组成光学系统,入射光路系统与散射光路系统在各自方向同轴封装。
28.所述基体内部开有通光通孔,所述通光通孔与入射的光路对齐;例如图6所示的,通光孔即在金属基体内部用于固定光学元件和使光路通过的孔。
29.颗粒导管(8)固定于所述基体上,其中,在所述基体上开设有一个通孔c,颗粒导管(8)穿过通孔c并固定;例如图6b所示的,通孔c处为一个通孔使得颗粒导管穿过的通孔,并且可固定颗粒导管。通常而言,金属基体可以采用一个六面体金属块(也可以采用非金属材料),而通孔c靠近金属基体的一个角。
30.光陷阱(9)镶嵌在颗粒导管(8)右侧d处;其中,光陷阱镶嵌在颗粒导管右侧,是将未发生散射的并从颗粒导管右侧视窗射出的光束反射到光学系统的外部。以此来避免多余
光束对光脉冲的干扰。比如图6c中所示的右侧d处。
31.在所述基体上还设置有为信号输入口a和信号输出口b,信号输入口a处安装有第一光纤耦合器(16),第一光纤耦合器(16)连接光源(1),信号输出口b处安装有第二光纤耦合器(17),第二光纤耦合器(17)连接接收器(13)。图6a所示,信号输入口a、信号输出口b利用第一光纤耦合器(16)和第二光纤耦合器(17),将光源(1)和接收器(13)分别进行耦合。
32.光纤耦合器是光纤与光纤之间进行可拆卸连接的器件,所谓的耦合,指的是利用光纤耦合器把光纤的两个端面精密对接起来,以保证发射光纤输出的光能量能最大限度地耦合到接收光纤中去。
33.信号输入口a、信号输出口b利用第一光纤耦合器(16)和第二光纤耦合器(17),将光源(1)和接收器(13)分别进行耦合。例如:图6a所示的,信号输入口a,信号输出口b可利用适配器将光源和接收器进行耦合,该基体若采用金属材料,则可以通过注塑模的方法进行加工制作。
34.本实施例中,如图7a所示的,通过焊接法兰(15)将颗粒导管(8)固定在所述基体的通孔c处;颗粒导管(8)与气体传输管道直接相连,所述气体传输管道,用于输送含有颗粒的气体。可选的,也可以采用如图7b所示的方式,通过金属管固定支架(14)将颗粒导管(8)固定在所述基体的通孔c处;颗粒导管(8)连接气流导管,所述气流导管接入气体传输管道,所述气流导管用于将所述气体传输管道中的含有颗粒的气体输入颗粒导管(8)。即一方面可以利用金属管固定支架将颗粒导管固定在基体上,通过与气流导管相连接将被测气体引入,实施颗粒检测。另一方面还可以利用双法兰固定结构与气体传输管道直接连接进行颗粒物浓度在线监测。颗粒导管(8)固定时,使通光孔与光路对齐,防止部分光束被遮挡而减小散射光强。
35.本实施例中,光源(1)发出的光线经光束整型器(2)后沿水平方向平行射入光学测量体,所述光学测量体包括:入射光与带有颗粒物的被测气体所重合的部分;被测试样输入颗粒导管(8),并通过颗粒导管(8)引入所述光学测量体内。
36.其中,第一光阑(3)位于汇聚透镜组(4)的物距x处,其中,汇聚透镜组(4)的焦距为f1,第一光阑(3)的孔径半径为d1且发散角为θ1,,折射后光的发散角为θ1',扩束透镜组(6)焦距为f2,扩束透镜组(6)之前的光线宽度为d2,且d2=2d2′
,d2'表示经扩束之后的光线宽度。
37.例如图1所示的,经过光束整型器(2)的光束具有一定的发散角,并且出射光束的光斑半径也无法满足光学测量体的宽度要求,所以要对出射的光束添加光阑进行限制,具体在第一光阑(3)后放置光汇聚透镜组(4)使光束汇聚,设光汇聚透镜组(4)的物距为x将第一光阑放在x处来确定其像的大小,令第一光阑孔径半径为d1则x处的光斑半径为d1,又发散角为θ1,汇聚透镜组(4)焦距为f1,经透镜折射后光的发散角为θ1',所以可根据近轴光学系统的透镜成像公式来求得物距x。
38.[0039][0040]
其中l为物距l'为像距d为物高d'为像高,又x为物距所以联立方程组得到下面公式:
[0041][0042][0043]
汇聚透镜组(4)将光路汇聚后,入射光却仍然存在较小的发散角,如果想要得到平行光则需放置一个扩束透镜组(6)对汇聚后的光束进行扩束,使出射光线为平行光,但因光学测量体的宽度要求为50~100微米,所以在准直透镜组的焦点处放置第二光阑以调整入射光斑的大小。
[0044]
由于要得到一个宽度确定的检测区域所以,所以应先确设扩束透镜组(6)焦距为f2,和经扩束之后的光线宽度d2',再由d2'推算出经扩束透镜组(6)之前的光线宽度d2,即孔径光阑的大小为d2,并将孔径光阑置于双凹透镜的焦点处,这样就能得到一个光线宽度为d2'的平行光。
[0045]
根据公式:
[0046][0047][0048]
其中,扩束部分的入射角未知,但光汇聚部分的出射角等于扩束部分的入射角即θ1'=θ2,设a'b'为像高ab为汇聚透镜组上的光斑大小o为光路与主光轴交点,所以根据公式和三角形相似法可得出θ2:
[0049][0050][0051]
ab=d+x
×
tanθ
[0052][0053]
联立上式得:
[0054]
d2=2d2′
[0055][0056]
从而可根据上述公式得出d2、f2大小。
[0057]
具体的,光源(1)发出的光线的波长范围为780~1100nm。所述散射光路系统中的多反射光路系统(7)的组成部分,包括:两组平面反射镜(7-1)、球面反射镜(7-2)、两片离轴
抛物面镜(7-3)和光陷阱(9),球面反射镜(7-2)和两片离轴抛物面镜(7-3)组成曲面镜;其中,球面反射镜(7-2)、平面反射镜(7-1)、离轴抛物面镜(7-3)都可以采用棱镜。球面反射镜(7-2)的顶点置于光学测量体正上方,两片离轴抛物面镜(7-3)的中心位置对称放置于30
°
和-30
°
,以便于所述曲面镜的焦点与所述光学测量体重合;两组平面反射镜(7-1)采用对称安装的方式,安装角度分别为45
°
和-45
°
。其中,两片离轴抛物面镜(7-3)的间距大于d,其中,f表示球面反射镜(7-2)顶点到光学测量体得距离,表示球面反射镜(7-2)的圆心角。
[0058]
举例来说,本实施例中所设计的散射光路系统,由多反射光路系统、散射光接收系统组成。入射光束射入光学测量体,经散射光路后传输到接收器上进行接收。散射光的强度较小,可能使得最小颗粒产生的脉冲信号小于检测阈值,导致检测颗粒被忽略,从而影响系统的分辨率。所以需添加一个散射光反射系统来将更多散射光汇聚以增强接收器所采集到的光强。在散射光反射系统中,通过多反射光路采集多角度范围内散射光。如图2所示的,多反射光路系统主要由平面反射镜(7-1)、球面反射镜(7-2)、离轴抛物面镜(7-3),和光陷阱(9)组成。球面反射镜(7-2)和离轴抛物面镜(7-3)组成曲面镜。或者,球面反射镜(7-2)、平面反射镜(7-1)、离轴抛物面镜(7-3)都可以采用棱镜。将球面反射镜(7-2)的顶点置于光学测量体正上方,两片离轴抛物面镜(7-3)的中心位置对称放置于30
°
和-30
°
,其中,是为了避免遮挡光路,所以离轴反射镜的间距大于d,因此本设计使离轴反射镜对称放置于30
°
和-30
°
。且所述曲面镜(离轴抛物面镜和球面反射镜的总称)的焦点与光学测量体重合,以保证散射光被曲面镜反射后转化为平行光,便于散射光汇聚透镜组(12)将光路汇聚。但由于散射光经离轴抛物面镜后方向与汇聚透镜组相反,所以两组平面反射镜(7-1)则用于改变由离轴抛物面镜(7-3)所反射的光路方向,从而使得所有被反射的散射光经聚焦后由接收器(13)采集产生脉冲信号,其中,可由凸凹透镜组减小散射光直径,再利用第三光阑滤除杂散光,最后利用散射光汇聚透镜组将光汇聚。而光陷阱(9)则是将未发生散射的光束反射到光学系统的外部。以此来避免多余光束对光脉冲的干扰。两组平面反射镜(7-1)采用对称安装,安装角度分别为45
°
和-45
°
[0059]
设球面反射镜(7-2)的圆心角为焦距即球面反射镜(7-2)顶点到光学测量体得距离为f。
[0060]
根据公式:
[0061][0062][0063]
得球面反射镜直径:
[0064]
所以为避免遮挡光路,两片离轴抛物面镜(7-3)的间距大于d。
[0065]
由于用于聚焦功能的透镜(可称为聚焦透镜)的焦距与焦点大小成正比,而焦点的尺寸直接影响接收器是否能更准确的收集散射光强,所以在条件满足的情况下尽可能选用
焦距较小的透镜。其中,d为入射光直径d为光斑直径,当入射光直径一定时,焦距越小则光斑直径越小。
[0066]
在本设计中散射光经双反射光路后的光束直径较大,利用两个焦距不同的凸凹透镜组并使其焦点重合来减小光束直径。此外光束在直径减小后依然存在一定强度的杂散光影响光学传感器的信噪比,因此需放置光阑滤除杂散光。最后再利用散射光汇聚透镜组将光路聚集。所述基体可以采用金属基体,或者非金属基体,制造基体的材料需要同时满足热膨胀系数较低且具有一定强度的特性,比如铜铁等金属材料,陶瓷、玻璃等,基体的制造方法可以采用3d打印技术。本实施例中,如图6a所示的,可以将设计好的光学元件按其结构封装于热膨胀系数较低且具有一定强度的金属或非金属基体内部,在基体侧边开孔,用螺钉紧固和调整光学元件位置,使得各个光学元件同轴封装。并利用环氧树脂等粘接剂对光学元件进行密封,保证整个腔体的气密性,避免传感器内部有灰尘进入导致光路被灰尘遮挡。
[0067]
本实施例中,颗粒导管(8)上开设有4个玻璃视窗,上下两个对称安装的玻璃视窗用于散射光通过,左右两个对称安装的玻璃视窗用于入射光通过,且所述上下两个对称安装的玻璃视窗的尺寸,大于左右两个对称安装的玻璃视窗。其中,所述上下两个对称安装的玻璃视窗,采用耐高温高压的高分子帕姆板特种工业透明材料;所述左右两个对称安装的玻璃视窗,采用高分子透明材料;
[0068]
颗粒导管(8)的管体(也可以称之为导管基体),采用镍含量为32%的铁镍合金,热膨胀系数为0.7
×
10-6
m/℃。
[0069]
本实施例中,如图8所示的,利用所述颗粒检测传感器进行颗粒检测的过程,包括:将所述气体传输管道中的含有颗粒的气体输入颗粒导管(8);启动光源(1),之后通过接收器(13)接收颗粒导管(8)上开设有玻璃视窗透出的散射光,得到散射光信号,之后再将散射光信号转换为电压脉冲信号;根据所述电压脉冲信号的幅值和计数,测量颗粒粒径和颗粒个数。
[0070]
所述将所述气体传输管道中的含有颗粒的气体输入颗粒导管(8),包括:将气流导管接入气体传输管道,通过气流导管将所述气体传输管道中的含有颗粒的气体输入颗粒导管(8),其中,通过金属管固定支架(14)将颗粒导管(8)固定在所述基体的通孔c处,颗粒导管(8)连接气流导管;或者,颗粒导管(8)与气体传输管道直接相连,所述颗粒导管(8)直接从所述气体传输管道获取含有颗粒的气体。
[0071]
举例来说,由于被测对象为高温高压气体,所以该气体不能与球面反射镜(7-2)所形成的腔体直接接触,因此需要颗粒导管(8)将高温高压气体导入。颗粒导管(8)由玻璃视窗和金属基体组成。如图3,颗粒导管(8)带有4个视窗,上下两个视窗可使散射光通过,左右视窗可使入射光通过。视窗与金属基体用石墨密封,使视窗与基体之间产生的径向压紧力使填料紧贴于轴表面而阻止介质外漏。颗粒导管(8)与三片曲面反射镜(包括球面反射镜和两片离轴抛物面镜。因这三篇反射镜的面都是非平面,因此也可称为曲面反射镜)保持一定距离,以保证可收集的散射光角度总和,即图3中的αβγ总和为150
°
。此外,一方面,为能最大限度的扩大曲面反射镜(一片球面反射镜和两片离轴抛物面镜)所接收到的散射光角度,该颗粒导管(8)的上下两个视窗大于左右视窗。
[0072]
其中,对于大玻璃视窗,采用耐高温高压的高分子帕姆板特种工业透明材料,且具
有极低的热膨胀系数,在高压下仍可保持所需要的机械强度,不但拥有良好的尺寸稳定性,还保证了玻璃视窗的透光性。对于小玻璃视窗,其所受到的压力较小若与大视窗厚度相同,不但浪费材料提高成本,还会使得视窗厚度过大导致平行光线产生平移,改变光的传播方向。所以小视窗采用机械强度较低的高分子透明材料以降低玻璃视窗厚度。另一方面,采用有较高的强度﹑硬度﹑韧性的镍含量为32%的铁镍合金,热膨胀系数为0.7
×
10-6
m/℃的材料作为导管基体。并可以进一步利用能阻滞热流传递耐高温隔热涂料对高强度耐压基体内外壁面进行隔热保温处理。例如:采用zs-1耐高温隔热保温涂料,其耐温2000度,由特制合成的无机硅酸盐溶液、硅酸铝纤维、热反射物质和精选空心陶瓷微珠加工而成。涂料属于无机单组份,无毒无害。涂层的导热系数极低,只有0.03w/m.k,隔热保温效果明显,在一定厚度条件下抑制效率可达到90%左右。涂层整体构造相当于打造了暖水瓶保温隔热机理,涂料中加入的空心陶瓷微珠腔体内部的空气在高温受热后,不会产生热对流,空心陶瓷微珠排列紧密彼此之间也存在三维的空气层,也避免了热对流的产生。相对较低导热系数的无机成膜物质作为涂层的支撑,共同构造了以静态空气层和无机成膜物质的绝热屏蔽层。加入的热反射材料作为辅助填料加入,这样使涂层的导热系数接近真空导热系数,起到了有效的隔热保温。
[0073]
进一步的,如图4所示的法兰固定式颗粒导管安装示意图以及支架固定式颗粒导管安装示意图,一方面可以利用金属管固定支架(14)将颗粒导管(8)固定在金属基体上,通过与气流导管相连接将被测气体引入实施颗粒检测,其中,气流导管的作用是将气体从气体传输管道引入颗粒导管。另一方面还可以利用双焊接法兰(15)固定结构与气体传输管道直接连接进行颗粒物浓度在线监测。导管固定时使玻璃视窗与光路对齐,防止部分光束被遮挡而减小散射光强。通过测量单个颗粒的散射光信号,将其转换成电压脉冲信号,利用该脉冲信号的幅值和计数,实现颗粒粒径与个数等参数的在线测量,同时结合颗粒的密度等参数获得颗粒的浓度信息。
[0074]
目前现役的各种商用的光学粒子计数器采用普通光学透镜组和非耐温耐压的结构设计,所以其应用工况与领域会受到极大限制,广泛应用于常温常压工况的粉体制造和除尘设备设计领域。针对非常温常压工况下的颗粒检测需求,研究者们主要集中在高温常压和常温高压工况。例如,针对高温常压工况,国内外学者基于光学粒子计数器的耐温要求,采用降温-在线的方式,将检测气体温度降温至检测仪器所能允许的最大操作温度,实现颗粒粒径及浓度等参数的测量。然而这种方法存在一些问题,一方面,由于降温过程中原本高温下呈气态的物质会逐渐凝结从而产生有害物质;另一方面,高温高压状态下颗粒表现出液体属性,其形状与液滴一样呈球形,当温度降低后颗粒冷凝形成不规则固体,引起检测误差。针对常温高压工况,多集中在高压天然气输气领域,研究者们通过采用耐高压玻璃,提高了光学粒子计数器的耐压能力。然而在满足耐压性能的同时,由于气体介质在常温高压工况下的特性与常温常压时存在差异,因此,随着检测压力工况的升高,存在光学粒子计数器的光学测量体增大等现象,引起仪器检测性能退化的问题。因此,需要改良其中的光学传感器使之具有良好的耐温耐压性能,以适应温度100~1500℃且压强1~10mpa的应用工况。
[0075]
(1)欲实现高温高压工况下颗粒的光学准确测量,除过突破检测装置的耐温和耐压能力外,仍需解决工况参数的变化引起的光学粒子计数器检测性能波动问题。由于气体
的体积在高温下具有膨胀性,而在高压下具有压缩性,两者产生相反的作用效果,导致此时气体光学特性相较于高温常压和常温高压时更加多变,所以在此基础上,现役光学粒子计数器的光学系统采用聚焦光模式,其光束传输性能将受到气体温度和压力的双重严重影响。
[0076]
(2)现役光学粒子计数器的光学系统中的光束为高斯光束,光束横截面中心位置能量最大,边缘位置能量最小,表现出光能分布不均匀的特征。正是由于该问题,导致颗粒的散射光信号所对应的电压信号无法满足有效信息筛选规定的标准特征,在测量中会产生颗粒的计数和粒径等参数测量误差。同时,亦会导致检测系统的分辨率降低。
[0077]
基于上述现役光学粒子计数器存在的问题,也为解决工业领域对高温高压工况下颗粒光学检测技术的需求,本发明提出一种应用于高温高压工况的颗粒光学检测传感器的设计思路,主要是基于光散射理论,通过测量单个颗粒的散射光信号,将其转换成电压脉冲信号,利用该脉冲信号的幅值和计数,实现颗粒粒径与个数等参数的在线测量,同时结合颗粒的密度等参数获得颗粒的浓度信息,具体的设计方案具体有如下特点:光学传感器具有良好的耐温耐压性能,应用工况为:温度100~1500℃,压强1~10mpa;颗粒光学检测传感器在不同温度压力工况下具有普遍适用性,解决工况参数的变化引起的光学粒子计数器检测性能波动问题,尤其是解决了高压高温工况下气体折射率变化引起的光学测量体增大等问题,保持传感器的设计测量精度指标;采用双反射光路系统,采集多角度范围内散射光,提高了光学检测传感器对微纳颗粒的最小检测粒径;光学系统中增设光学元件,消除光束能量高斯分布,使得光学测量体区域的横截面光能分布均匀,拓展单颗粒散射光信号探测和筛选能力,提高光学传感器的检测精度。
[0078]
总的来说,本实施例所提供的方案,在光学检测系统中提供一个较窄的光学检测区域,使得气体中的颗粒能够以单个颗粒或者较小的粒子微团通过检测区域(图5所示的),能够提高系统的检测精度;且通过光路整形使得入射光以平行的方式射入检测区域,有效的避免了由于高温高压所产生的折射率的影响;另外,由于在检测区域通过添加曲面反射镜(7-2)来扩大散射光的接收角度,增强所接收到的散射光强,提高输出信号的可靠性、稳定性和准确性。
[0079]
本说明书中的各个实施例均采用递进的方式描述,各个实施例之间相同相似的部分互相参见即可,每个实施例重点说明的都是与其他实施例的不同之处。尤其,对于设备实施例而言,由于其基本相似于方法实施例,所以描述得比较简单,相关之处参见方法实施例的部分说明即可。以上所述,仅为本发明的具体实施方式,但本发明的保护范围并不局限于此,任何熟悉本技术领域的技术人员在本发明揭露的技术范围内,可轻易想到的变化或替换,都应涵盖在本发明的保护范围之内。因此,本发明的保护范围应该以权利要求的保护范围为准。