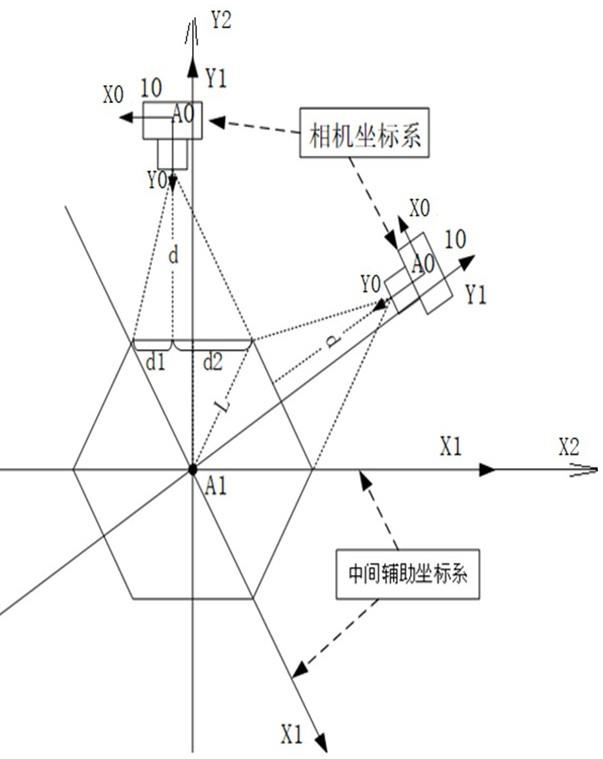
1.本发明属于钢管生产控制技术领域,具体地说,涉及一种钢管测量装置。
背景技术:2.无缝钢管加工工艺复杂,至少涉及长尺坯锯切、环形炉、穿孔机、轧机、定径机、冷床、管排锯切、矫直机、吹吸灰、探伤机、测长称重机、打包机等相关设备,通常各设备由不同厂家提供,各设备有其独立的plc控制工作,并各设备的plc与mes(生产执行系统)连接,由mes进行各设备之间的流程化控制,并实施获取相关生产信息等。一根长尺坯在经过各设备加工期间,物料运动路径多变,且又涉及一根长尺坯变为多根定尺坯,定尺坯经轧制为钢管后,钢管又锯切为多根钢管的工艺过程。
3.在管材质量检测方面,尤其是对于管材的外径,通常是在一批次管材生产完成后,质检人员从其中抽取一部分管材进行检测,这种离线检测的方式具有时间滞后性,离线钢管尺寸精度分析的数据也不能很好的逐支反应钢管实际情况。而且抽检仅是抽查几根,进行离线测量,记录,由专门的质检人员综合考虑各个因素后进行判定。质检人员只能通过少量抽检的数据(离线抽检方式)给出终判,经常有错判的情况发生,质检人员判定合格外发的产品,也会存在质量异议。
4.在工业自动化程度不断提高的背景下,需要实现钢管生产过程中的管材直径的自动检测,而截至目前,暂未有较好的在线解决方法。
技术实现要素:5.为解决现有技术中的以上问题,本发明提供一种钢管测量装置,包括:标定模块,用于对分布于横截面为正六边形棒材各侧面的3d相机进行标定,获得3d相机坐标系位置点到物体空间坐标系的转换矩阵;采集转换模块,用于将标定的3d相机采集的钢管表面在相机坐标系下的位置点坐标通过转换矩阵映射到物体空间坐标系下,获得钢管表面在物体空间坐标系下的位置点坐标,其中,钢管是标定3d相机后同轴替换所述棒材的;直径计算模块,用于根据钢管表面在物体空间坐标系下的位置点坐标,通过最小二乘法以圆形方程为最终拟合目标,得到钢管的直径。
6.可选地,建立有二维的相机坐标系x0a0y0、中间辅助坐标系x1a1y1、物体空间坐标系x2a1y2,其中相机坐标系是在横截面内以3d相机中心为坐标原点a0,相机靶面平行方向为x0轴,相机靶面垂直方向为y0轴;中间辅助坐标系是在横截面内以正六边形的中心为原点a1,以3d相机正对的侧面平行方向为x1轴,垂直该侧面的方向为y1轴;物体空间坐标系是以正六边形的中心为原点a1,以棒材水平宽度方向为x2轴,以棒材竖直宽度方向为y2轴。
7.可选地,标定模块中,对分布于横截面为正六边形棒材各侧面的3d相机进行标定,获得3d相机坐标系位置点到物体空间坐标系的转换矩阵,包括:根据3d相机输出数据得到正对侧面距离相机最小距离d位置对应的在相机靶面图
像上x0轴方向位置x0,根据3d相机输出数据得到正对侧面一个角点在相机靶面图像上x0轴方向位置x1,根据3d相机输出数据得到正对侧面另一角点在相机靶面图像上x0轴方向位置x2,由此得到相机坐标系位置点在中间辅助坐标系下位置信息为:由此得到相机坐标系位置点在中间辅助坐标系下位置信息为:由此得到相机坐标系位置点在中间辅助坐标系下位置信息为:由此得到相机坐标系位置点在中间辅助坐标系下位置信息为:a是正对侧面相邻一侧面的角点在相机靶面图像上x0轴方向位置;b是正对侧面相邻另一侧面的角点在相机靶面图像上x0轴方向位置;表示相机坐标系位置点在中间辅助坐标系下x1轴坐标;表示相机坐标系位置点在中间辅助坐标系下y1轴坐标;根据相机坐标系位置点在中间辅助坐标系下位置信息,得到相机坐标系位置点到中间辅助坐标系下的转换矩阵为:构建中间辅助坐标系位置点到物体空间坐标系下的转换矩阵为:中间辅助坐标系与物体空间坐标系的夹角为。
8.可选地,根据钢管表面在物体空间坐标系下的位置点坐标,通过最小二乘法以圆形方程为最终拟合目标,得到钢管的直径,包括:随机取初始角度,以间隔角度从钢管表面在物体空间坐标系下的位置点坐标中抽取得到数据子集,对数据子集利用最小二乘法进行方程拟合得到拟合圆的直径作为钢管直径。
9.可选地,随机取初始角度,以间隔角度从钢管表面在物体空间坐标系下的位置点坐标中抽取得到数据子集,对数据子集利用最小二乘法进行方程拟合得到拟合圆的直径作为钢管直径,包括:采用不同间隔角度反复抽取m次获得m个数据子集,并分别利用最小二乘法获得直径,将直径均值作为钢管的直径。
10.可选地,对于所述m个数据子集,分别利用最小二乘法获得的直径,其中最大直径
与最小直径之差作为钢管的椭圆度。
11.根据本发明的钢管测量装置,能够实现管材直径在线检测,并且由于管材全部进行直径检测,避免了以往抽检的误判情况,保证钢管质量判定的准确性和及时性。
附图说明
12.通过结合下面附图对其实施例进行描述,本发明的上述特征和技术优点将会变得更加清楚和容易理解。
13.图1是表示本发明涉及的相机布置的示意图。
14.图2是表示本发明涉及的二维坐标系的示意图。
15.图3是表示本发明涉及的物体空间坐标系与中间辅助坐标系的夹角关系。
16.图4是表示本发明涉及的3d 相机采集棒材侧面图像的示意图。
具体实施方式
17.下面将参考附图来描述本发明所述的实施例。本领域的普通技术人员可以认识到,在不偏离本发明的精神和范围的情况下,可以用各种不同的方式或其组合对所描述的实施例进行修正。因此,附图和描述在本质上是说明性的,而不是用于限制权利要求的保护范围。此外,在本说明书中,附图未按比例画出,并且相同的附图标记表示相同的部分。
18.图1是表示本发明涉及的相机布置的示意图;图2是表示本发明涉及二维坐标系的示意图。图3是表示本发明涉及的物体空间坐标系与中间辅助坐标系的夹角关系。图4是表示本发明涉及的3d 相机采集棒材侧面图像的示意图。下面,参照图1至图4来说明钢管测量装置,其通过3d相机实现管材直径的测量,包括以下步骤:步骤s1,如图1所示,在横截面为正六边形的棒材100各侧面都布置一个3d相机10,使得各3d相机在同一横截面上,且3d相机10的靶面与其对应的侧面平行。如图2、图3所示,建立二维的相机坐标系x0a0y0、中间辅助坐标系x1a1y1、物体空间坐标系x2a1y2。其中相机坐标系是在横截面内以3d相机中心为坐标原点a0,相机靶面平行方向为x0轴,相机靶面垂直方向为y0轴;中间辅助坐标系是在横截面内以正六边形的中心为原点a1,以3d相机正对的侧面平行方向为x1轴,垂直该侧面的方向为y1轴;物体空间坐标系是以正六面形的中心为原点a1,以棒材水平宽度方向为x2轴,以棒材竖直宽度方向为y2轴。相机坐标系是与相机数量相同的,例如沿正六边形六个侧面分别设置一个3d相机,则建立有6个相机坐标系。对应的,由于要把相机坐标系位置点转换到物体空间坐标系,则对应每个相机坐标系,都有一个中间辅助坐标系。
19.步骤s2,各相机拍摄对应侧面图像,利用侧面图像建立相机坐标系位置点到物体空间坐标系的转换矩阵,包括:步骤s21,如图4所示,根据3d相机输出数据得到该侧面距离相机最小距离d位置对应的在拍摄的相机靶面图像上x0轴方向位置为x0,根据3d相机输出数据得到正对侧面一个角点在相机靶面图像上x0轴方向位置x1,根据3d相机输出数据得到正对侧面另一角点在相机靶面图像上x0轴方向位置x2,由此得到相机坐标系位置点在中间辅助坐标系下位置信息为:
表示相机坐标系位置点在中间辅助坐标系下x1轴坐标;表示相机坐标系位置点在中间辅助坐标系下y1轴坐标。
20.a是正对侧面相邻一侧面的边在相机靶面图像上x0轴方向位置;b是正对侧面相邻另一侧面的边在相机靶面图像上x0轴方向位置。
21.步骤s22,根据相机坐标系位置点在中间辅助坐标系下位置信息,得到相机坐标系位置点到中间辅助坐标系下的转换矩阵为:步骤s23,构建中间辅助坐标系位置点到物体空间坐标系下的转换矩阵为:中间辅助坐标系与物体空间坐标系的夹角为。
22.步骤s3,采用标定的3d相机围绕钢管周围,即采用钢管同轴替换掉标定用棒材,并对钢管外周进行拍摄,3d相机输出数据包括钢管表面在相机坐标系下的横向位置和距离钢管表面位置;步骤s4,将各相机在相机坐标系下输出的数据,依据步骤s2中获得的两个转换矩阵和,同步映射到物体空间坐标系下,数据映射关系为:其中,为相机输出数据中钢管表面在相机坐标系下的平行于相机靶面方向的位置和距离钢管表面位置;,为物体空间坐标系下钢管表面的位置信息。
23.步骤s5,依据步骤s4得到的物体空间坐标系下的位置点坐标,根据位置点坐标通
过最小二乘法以圆形方程为最终拟合目标,得到钢管的直径和椭圆度信息。
24.具体的,可以统计各3d相机的输出数据点,依据步骤s4获得出的转换矩阵和,得到物体空间坐标系下的数据,在这些数据中,随机取初始角度,然后以一定的间隔角度在数据中抽取,抽取得到的数据子集利用最小二乘法进行方程拟合得到拟合圆的直径即为钢管直径,如此反复执行m次该过程,得到m组直径值,取其均值作为钢管的平均直径,其中的最大直径与最小直径之差即为钢管的椭圆度。
25.例如,以初始角度为60度,间隔角度为60度来抽取得到数据子集利用最小二乘法进行方程拟合得到拟合圆的直径即为钢管直径。然后再以可以以初始角度为30度,间隔角度为50度来抽取得到数据子集利用最小二乘法进行方程拟合得到拟合圆的直径即为钢管直径,然后可以得到m组直径值,取平均值可以作为钢管的直径。其中的最大直径与最小直径之差即为钢管的椭圆度。
26.以上所述仅为本发明的优选实施例,并不用于限制本发明,对于本领域的技术人员来说,本发明可以有各种更改和变化。凡在本发明的精神和原则之内,所作的任何修改、等同替换、改进等,均应包含在本发明的保护范围之内。