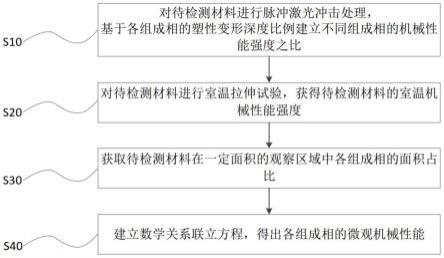
1.本发明涉及材料强度检测领域,尤其涉及一种基于脉冲激光冲击波的结构材料组成相组织强度检测方法。
背景技术:2.金属结构材料通常具有复杂的相组成,不同相组成的金属材料具备不同的宏观机械性能。若获取不同微观组成相的机械性能,后采用数学重组的方式进行不同组合,则有望得到具备不同宏观机械性能表现的应用材料。然而,金属结构材料中不同组成相的机械性能,目前并未见应用价值很高的测试手段。现有的纳米压痕测试方式,直接对金属结构材料的微小组成部分进行机械性能测试,但材料微小局部区域的纳米硬度与材料整体的宏观力学表现缺乏直接的对应关联。如何检测金属结构材料中微观相组成的微观机械性能,并使得所获得的微观机械性能对材料宏观性能设计具有决定性作用,成为技术人员需要解决的问题。
技术实现要素:3.本发明的目的在于提出一种基于脉冲激光冲击波的结构材料组成相组织强度检测方法。
4.为达此目的,本发明采用以下技术方案:
5.基于脉冲激光冲击波的结构材料组成相组织强度检测方法,该方法包括以下步骤:
6.步骤s10:确定待检测材料的组成相,对待检测材料进行脉冲激光冲击处理,测算出激光冲击区域内各组成相的塑性变形深度,基于各组成相的塑性变形深度比例建立不同组成相的机械性能强度之比;
7.步骤s20:对待检测材料进行室温拉伸试验,获得待检测材料的室温机械性能强度;
8.步骤s30:获取待检测材料在一定面积的观察区域中各组成相的面积占比;
9.步骤s40:根据材料不同组成相的机械性能强度之比、待检测材料的室温机械性能强度以及待检测材料各组成相的面积之比,建立数学关系联立方程,得出各组成相的微观机械性能。
10.优选的,步骤s10具体包括:
11.步骤s11:通过测量仪器确定待检测材料的内部组成相及各组成相的面积大小;
12.步骤s12:根据不同组成相的面积大小,调整激光光束的辐照面积,对待检测材料进行激光冲击,使得待检测材料的表面发生塑性变形;
13.步骤s13:观察待检测材料的表面,选定不同组成相中面积比例一致的激光冲击区域作为观测对象;
14.步骤s14:通过三维状态检测设备表征所述观测对象,测算出观测对象中各组成相
的塑性变形深度;
15.步骤s15:基于塑性变形深度比例建立不同组成相的机械性能的强度比。
16.优选的,步骤s12中,当所有组成相均为连续分布状态时,激光光束的辐照面积的大小调整为能够同时覆盖所有组成相;当组成相中含有弥散分布的颗粒析出相时,激光光束辐照面积的大小调整为颗粒析出相面积的1.6~1.9倍。
17.优选的,步骤s11中,待检测材料内部的不同组成相面积均大于50μm2。
18.优选的,步骤s12中,对待检测材料激光冲击的区域中具有3个以上不同组成相的面积比例一致。
19.优选的,步骤s15中,确定不同组成相的塑性变形深度比例的倒数为不同组成相的机械性能强度比。
20.优选的,步骤s20中,室温机械性能强度为屈服强度或抗拉强度。
21.优选的,步骤s30中,观察区域中不同组成相的数量不小于10。
22.优选的,步骤s40中,若待检测材料的组成相包括α相与β相,已得到α相与β相的机械性能强度之比为a:b、待检测材料的室温机械性能强度为m、α相与β相的面积占总面积的比率分别为c%和d%,设α相与β相的微观机械性能分别为ax与bx,建立的数学关系联立方程为c%(ax)+d%(bx)=m,即可得出以室温机械性能强度为测试依据的α相与β相的微观机械性能。
23.本发明的有益效果为:本发明的方法是以材料宏观机械性能为数据依据,以非接触自由塑性变形程度表征微结构机械强度,通过结构材料宏观表现与微观性能的直接对应,实现了对金属结构材料中微观相组成的微观机械性能的检测。
附图说明
24.附图对本发明做进一步说明,但附图中的内容不构成对本发明的任何限制。
25.图1是本发明其中一个实施例的方法流程图。
具体实施方式
26.下面结合附图并通过具体实施方式来进一步说明本发明的技术方案。
27.实施例1
28.本实施例的一种基于脉冲激光冲击波的结构材料组成相组织强度检测方法,参考附图1,该方法包括以下步骤:
29.步骤s10:确定待检测材料的组成相,对待检测材料进行脉冲激光冲击处理,测算出激光冲击区域内各组成相的塑性变形深度,基于各组成相的塑性变形深度比例建立不同组成相的机械性能强度之比;
30.步骤s20:对待检测材料进行室温拉伸试验,试验过程按照金属材料室温拉伸试验方法国家标准开展,获得待检测材料的室温机械性能强度;
31.步骤s30:获取待检测材料在一定面积的观察区域中各组成相的面积占比;
32.步骤s40:根据材料不同组成相的机械性能强度之比、待检测材料的室温机械性能强度以及待检测材料各组成相的面积之比,建立数学关系联立方程,得出各组成相的微观机械性能。
33.通过对待检测材料进行激光冲击,使得在激光冲击波作用下材料表面形成不同深度宏观凹坑,而宏观凹坑底部不同组成相的强度差别导致不同相组织区域发生微观起伏的高度差,实现基于不同激光冲击作用力下的不同相组织的高度比值来判断和计算不同组成相的微观机械强度。
34.由此,本实施例的方法以材料宏观机械性能为数据依据,以非接触自由塑性变形程度表征微结构机械强度,通过结构材料宏观表现与微观性能的直接对应,实现了对金属结构材料中微观相组成的微观机械性能的检测。
35.优选的,步骤s10具体包括:
36.步骤s11:通过扫描电子显微镜或金相显微镜等测量仪器确定待检测材料的内部组成相及各组成相的面积大小;
37.步骤s12:根据不同组成相的面积大小,调整激光光束的辐照面积,对待检测材料进行激光冲击,使得待检测材料的表面发生塑性变形;
38.步骤s13:观察待检测材料的表面,选定不同组成相中面积比例一致的激光冲击区域作为观测对象;
39.步骤s14:通过采用白光干涉仪等三维状态检测设备表征所述观测对象,测算出观测对象中各组成相的塑性变形深度;
40.步骤s15:基于塑性变形深度比例建立不同组成相的机械性能的强度比。
41.若金属材料不同组成相的数量大于两种,则不同组成相的强度比可通过两两比对的方式获得。例如:某金属材料组成相包括α相、β相与γ相,可首先通过塑性变形程度的定量对比分别得出α相与β相、β相与γ相的强度比例,最终建立α相、β相与γ相的强度的整体比例。
42.由此,通过对待检测材料的激光冲击,使得待检测材料材料表面形成不同深度宏观凹坑,而宏观凹坑底部不同组成相的强度差别导致不同相组织区域发生微观起伏的高度差,从而通过不同相组织的高度比值来判断和计算不同组成相的微观机械强度。
43.进一步的,步骤s12中,当所有组成相均为连续分布状态时,激光光束的辐照面积的大小调整为能够同时覆盖所有组成相;当组成相中含有弥散分布的颗粒析出相时,激光光束辐照面积的大小调整为颗粒析出相面积的1.6~1.9倍。以此确保待检测材料两类不同组成相的面积占比约为1:1。
44.优选的,步骤s11中,受到脉冲激光光束聚焦面积的制约,待检测材料内部的不同组成相面积均大于50μm2。
45.优选的,步骤s12中,对待检测材料激光冲击的区域中具有3个以上不同组成相的面积比例一致。保证检测的准确性。
46.优选的,步骤s15中,确定不同组成相的塑性变形深度比例的倒数为不同组成相的机械性能强度比。
47.优选的,步骤s20中,室温机械性能强度为屈服强度或抗拉强度。由此,屈服强度或抗拉强度作为待检测材料微观机械性能的测试依据。若确定待检测材料室温拉伸试验获得屈服强度为测试依据,则测得的待检测材料不同组成相的微观机械性能的强度为不同组成相的微观屈服强度。
48.优选的,步骤s30中,为了满足统计分析观察区域内部不同组成相面积比例的要
求,即观察区域内需包含较大数量的不同组成相,在本实施例中,对观察区域的面积设置的要求为观察区域中不同组成相的数量不小于10个。根据拟要求的观察区域的面积大小,根据实际需要选择观测设备。当观测区域大于1000μm2时,优选金相显微镜进行较大区域的组成相面积检测。
49.优选的,步骤s40中,若待检测材料的组成相包括α相与β相,已得到α相与β相的机械性能强度之比为a:b、待检测材料的室温机械性能强度为m、α相与β相的面积占总面积的比率分别为c%和d%,设α相与β相的微观机械性能分别为ax与bx,建立的数学关系联立方程为c%(ax)+d%(bx)=m,即可得出以室温机械性能强度为测试依据的α相与β相的微观机械性能。由此,通过上述联立方程,即可得到不同组成相的微观机械性能,实现对金属结构材料中微观相组成的微观机械性能的检测。
50.实施例2
51.本实施例以采用本发明所述方法检测某金属结构材料内部组成相为例,其组成相为基体相与弥散分布的颗粒相。
52.(1)采用金相显微镜确定某待检测材料内部组成相为α相和β相,其中α相为基体相,β相为析出第二相;通过金相显微镜分析软件表征和统计计算,得出待检测材料内部β相为弥散分布状态,且其面积大小大致为50μm2;设定脉冲激光光束直径为11μm(此时光束辐照面积约为95μm2),对待检测材料进行脉冲激光冲击处理,激光冲击处理采用厚度不大于50μm的黑色胶带为吸收层,采用激光能量为500mj(此时,激光冲击处理能在保证材料表面吸收层不被烧穿的条件下诱导材料表面最大程度的塑性变形);对待检测材料表面进行10次激光冲击处理,通过扫描电子显微镜观察挑选其中α相和β相面积占比约为1:1的冲击区域作为观测对象,利用白光干涉仪进行表面塑性变形状态的三维表征;基于白光干涉仪测试数据,测算出激光冲击区域内α相处塑性变形深度为80μm,而β相处塑性变形深度为60μm;由此,确定α相与β相的机械性能的强度比为60μm:80μm=3:4。
53.(2)对待检测材料进行室温拉伸试验,试验过程按照金属材料室温拉伸试验方法国家标准开展,获得待检测材料的室温屈服强度为660mpa。
54.(3)对待检测材料进行研磨抛光金相制样,采用金相显微镜观察材料表面显微组织状态,设定观察区域面积在1000μm2,统计分析观察区域内部α相与β相的面积比例,得出待检测材料α相与β相的面积占比分别为70%和30%。
55.(4)设定α相与β相的微观机械性能为3x与4x,建立数学关系联立方程70%(3x)+30%(4x)=660mpa,得出α相与β相的微观机械性能分别为600mpa与800mpa。
56.实施例3
57.本实施例以采用本发明所述方法检测某金属结构材料内部组成相为例,其组成相为基体相与连续分布的第二相。
58.(1)采用扫描电子显微镜确定某待检测材料内部组成相为α相和β相,其中α相为基体相,β相为析出第二相;通过组织分析软件表征和统计计算,得出待检测材料内部β相为连续分布状态;设定脉冲激光光束直径为20μm(此时光束辐照面积约为314μm2),对待检测材料进行脉冲激光冲击处理,激光冲击处理采用厚度不大于80μm的黑色胶带为吸收层,采用激光能量为800mj(此时,激光冲击处理能在保证材料表面吸收层不被烧穿的条件下诱导材料表面最大程度的塑性变形);对待检测材料表面进行激光冲击处理,直至通过扫描电子显
微镜观察可挑选出其中α相和β相面积占比约为1:1(激光辐照材料表面不同组成相的相边界,保持不同组成相的面积大致相同)的冲击区域,利用白光干涉仪对挑选出的冲击区域进行表面塑性变形状态的三维表征;基于白光干涉仪测试数据,测算出激光冲击区域内α相处塑性变形深度为150μm,而β相处塑性变形深度为100μm;由此,确定α相与β相的机械性能之强度比为100μm:150μm=2:3。
59.(2)对待检测材料进行室温拉伸试验,试验过程按照金属材料室温拉伸试验方法国家标准开展,获得待检测材料的室温屈服强度为480mpa。
60.(3)对待检测材料进行研磨抛光金相制样,采用金相显微镜观察材料表面显微组织状态,要求观察区域面积在2000μm2,统计分析观察区域内部α相与β相的面积比例,得出待检测材料α相与β相的面积占比分别为60%和40%。
61.(4)设定α相与β相的微观机械性能为3x与5x,建立数学关系联立方程60%(2x)+40%(3x)=480mpa,得出α相与β相的微观机械性能分别为400mpa与600mpa。
62.实施例4
63.本实施例以采用本发明所述方法检测某金属结构材料内部组成相为例,其组成相为基体相与连续分布的析出相与弥散分布的析出相。
64.(1)采用扫描电子显微镜确定某待检测材料内部组成相为α相、β相和γ相,其中α相为基体相,β相为连续析出第二相,γ相为弥散析出第二相;设定脉冲激光光束直径为30μm(此时光束辐照面积约为707μm2),对待检测材料进行脉冲激光冲击处理,激光冲击处理采用厚度不大于100μm的黑色胶带为吸收层,采用激光能量为1000mj(此时,激光冲击处理能在保证材料表面吸收层不被烧穿的条件下诱导材料表面最大程度的塑性变形);对待检测材料表面进行激光冲击处理,直至通过扫描电子显微镜观察可挑选出其中α相、β相和γ相面积占比约为1:1:1(激光辐照材料表面不同组成相的相边界,保持不同组成相的面积大致相同)的冲击区域,利用白光干涉仪对挑选出的冲击区域进行表面塑性变形状态的三维表征;基于白光干涉仪测试数据,测算出激光冲击区域内α相处塑性变形深度为120μm,β相处塑性变形深度为100μm,而γ相处塑性变形深度为50μm;由此,确定α相、β相与γ相的机械性能之强度比为5:6:12。
65.(2)对待检测材料进行室温拉伸试验,试验过程按照金属材料室温拉伸试验方法国家标准开展,获得待检测材料的室温屈服强度为690mpa。
66.(3)对待检测材料进行研磨抛光金相制样,采用金相显微镜观察材料表面显微组织状态,要求观察区域面积在3000μm2,统计分析观察区域内部α相、β相与γ相的面积比例,得出待检测材料α相、β相与γ相的面积占比分别50%、30%和20%。
67.(4)设定α相、β相与γ相的微观机械性能为5x、6x与12x,建立数学关系联立方程50%(5x)+30%(6x)+20%(12x)=690mpa,得出α相、β相与γ相的微观机械性能分别为500mpa、600mpa与1200mpa。
68.以上结合具体实施例描述了本发明的技术原理。这些描述只是为了解释本发明的原理,而不能以任何方式解释为对本发明保护范围的限制。基于此处的解释,本领域的技术人员不需要付出创造性的劳动即可联想到本发明的其它具体实施方式,这些方式都将落入本发明的保护范围之内。