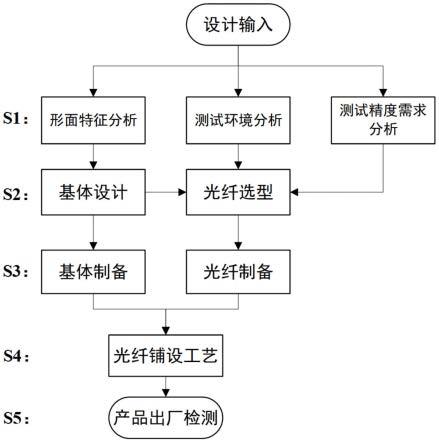
1.本发明属于光纤测量技术领域,具体涉及一种功能光纤网格制备工艺方法。
背景技术:2.在许多需要高瞬态碰撞损伤测量的场合,测量设备感知部件电磁环境复杂,常规电气感知部件或传感器会受到电磁环境影响导致信号失真,而光信号则可以规避该缺陷。
3.利用具有一定物理空间位置关系的光纤组网形成光纤网格,将光纤网格布置在被测形面上,形成光纤感知层,采用配套电子采集设备识别光纤感知层的光信息状态变化,可以有效提升测量系统抵抗电磁干扰能力,从而实现对碰撞损伤的测量。
4.目前,光纤网格在组网设计优化、信息处理方法、壳体制备加工工艺等方面都有了一定的发展,但是,对于光纤网格的选型、制备、工艺实现方法等直接关系到光纤网格应用和功能可靠性的研究还尚有欠缺。
5.为实现光纤网格的物理关系,从而建立光信号的稳定传输通路,当前,亟需发展一种功能光纤网格制备工艺方法,用于指导光纤制备、网格空间位置固定、光纤保护等工艺过程。
技术实现要素:6.本发明所要解决的技术问题是提供一种用于高瞬态碰撞损伤测量的功能光纤网格制备工艺方法。
7.本发明的功能光纤网格制备工艺方法,包括以下步骤:
8.s1.需求分析;
9.根据设计输入参数,对被测形面的应用需求开展分析,分析内容包括被测形面特征分析、被测形面测试环境分析和测试精度需求分析;其中,设计输入参数包括被测物物理尺度、交会速度,被测形面特征包括厚度、材料、工艺和几何对称性,被测形面测试环境包括测试时长、表面温度变化,测试精度需求包括光纤网格密度。
10.s2.方案设计;
11.结合步骤s1的分析结果,根据被测形面特征、被测形面测试环境开展基体设计和光纤选型;
12.s21.基体设计,包括材料选型和线槽设计;
13.s211.材料选型;
14.从有利于制备光纤网格和进行铺设出发,选择具有适应测试环境温度变化性能的基体材料;对于耐温要求100℃及100℃以下,结合材料的轻质要求,并考虑被测形面与基体材料的粘接性能,选择易获取和进行机械加工的低温成型料,低温成型料为包括pc、尼龙在内的质轻易加工材料;对于耐温要求100℃以上,选择耐高温的高温成型料,高温成型料包括耐温pc、合成耐温软木,由于耐温pc在成型后更加轻质、结构稳定,优先选用耐温pc;
15.s212.线槽设计;
16.按照预先设定的精度要求,确定光纤预留线槽的走线方式,采用等距螺旋方式线槽,调整线槽密度,同时进行光纤冗余设计,确保在少数光纤失效的情况下,剩余的光纤完成精度要求的测量;
17.s22.光纤选型;
18.选定基体材料后,根据测试环境温度变化范围选择光纤类型和光电转换接头;
19.s221.选择光纤类型;
20.为实现在轻薄基体内铺设埋入光纤的目的,考虑光纤保护需要,采用小芯径的裸纤,裸纤是祛除光纤的保护外壳后,带有涂覆层的裸光纤;对于耐温要求100℃及100℃以下,采用通信光纤;对于耐温要求100℃以上,选择石英光纤;
21.s222.设计加工光纤转换接头;
22.首先考虑光纤与光纤接头的工艺适配,其次设计光电转换模块,再次将光纤、光电转换模块和光纤接头组合成光纤转换接头,随后检测确认光纤转换接头实现了光信号的可靠传输和识别,最后完成光纤转换接头设计加工。
23.s3.部件制备工艺;
24.s31.部件制备工艺包括基体制备工艺和光纤制备工艺;
25.s311.基体制备工艺;
26.对于耐温要求100℃及100℃以下,采用成型板料,按照基体分片设计和线槽设计开展机械加工,再放置在配套的拼接治具上进行拼接固化,完成基体成型;对于耐温要求100℃以上,选取耐温pc,由于耐温pc的材料流动性差,首先根据耐温pc注塑温度和耐温pc注塑件形状设计若干高压注塑模具,并通过调温、调压和多点注塑工艺,获取若干耐温pc形面,再配合机加在若干耐温pc形面的表面刻线槽,最后将具有线槽的若干耐温pc形面放置在配套拼接治具上进行拼接固化,完成基体成型;
27.s312.光纤制备工艺;
28.光纤制备工艺首先根据线槽设计和应用需求确定光纤长度,并建立光纤编号规则,光纤制备时,按照既定长度和光纤编号进行加工;其次,根据光纤芯径与光纤转接头的标准适配制备工艺,连接裸纤和光纤转换接头;最后,根据应用需求对光纤转换接头根部与裸纤连接处进行硅胶点胶保护,硅胶点胶用于吸收局部应力,保证接头处的结构强度;
29.s32.部件制备工艺还包括设计部件制备工艺包括成型拼接工艺、固定工艺、工艺验证试验以及配套的工装治具;
30.成型拼接工艺根据被测形面的对称性、开孔特征、特殊区域特点设计被测形面专用的成型拼接方法;固定工艺设计包括套装粘接工艺在内的、专用的、基体与被测形面固定方法;工艺验证试验,根据需要开展包括材料成型、材料粘接、材料耐温试验的工艺验证方法;在成型拼接工艺、固定工艺、工艺验证试验过程中,设计制备相应的工装治具。
31.s4.光纤布设工艺;
32.s41.基体和光纤部件复检;
33.对基体尺寸、线槽设计进行复核;检查清理光纤线槽组成的基体网格,清理后用无水酒精清洗光纤线槽,做到线槽内无毛刺,残留物及油渍;暗室检查光纤通光性;
34.s42.光纤铺设粘接;
35.按照设计余量留出光纤长度,然后用软胶将光纤按照编码粘接到对应的线槽槽
底,光纤不高出线槽表面,光纤的交叉点不高出基体表面;
36.s43.光纤通光检测;
37.每根光纤布设完成后,再次检测光纤通光性,及时更换通光性差或有损伤的光纤;
38.s44.线槽填胶;
39.全部光纤铺设完毕后,清除残余软胶,并在线槽内填充软硅胶,初步固化后清除多余软硅胶,使线槽表面平整;
40.s45.光纤保护;
41.对光纤集束和光纤头进行收纳保护;首先,利用热缩管分束保护裸纤,避免在运输过程中因裸纤互相缠绕,产生应力损坏裸纤;其次,用软泡沫薄膜包裹光纤头集束并固定光纤头集束,避免污染光纤端面,保证光纤通光性能。
42.s5.检测;
43.产品检测主要包括过程检测、产品出厂检测和应用功能检测;
44.过程检测是对前一步骤产出的过程产品与设计指标符合情况进行检查,保证后续工序开展和质量;
45.产品出厂检测包括结构参数检测、光纤通光功能检测和产品表面质量检查;结构参数包括外形结构参数、质量和厚度;
46.应用功能检测是产品后续应用过程中,配合应用工艺和场合对产品结构和光纤网格通光性进行检查。
47.进一步地,所述的软胶为808软胶,软硅胶为414软硅胶或者导热硅脂胶。
48.本发明的功能光纤网格制备工艺方法,首先进行被测形面的光纤网格环境分析,选择适用于被测形面的光纤;其次建立适应被测形面的光纤网格的固定工艺,实现光纤网格的物理空间关系;再次制备光纤网格,并不断提高光纤网格的强度和可靠性,建立更加轻薄的光纤网格;最后,进行制备工艺解耦,将本发明的功能光纤网格制备工艺方法高效应用于不同目标结构的被测形面上。
49.本发明的功能光纤网格制备工艺方法能够制备一种应用于不同被测形面的、具有微秒级响应的高瞬态碰撞损伤测量信息感知的光纤网格,光纤网格能够消除碰撞损伤过程中的电磁干扰,实现对碰撞损伤情况的信息高速响应,从而为配套信号采集电子设备提供可靠光信号传播路径,进而实现对包括位置、角度、损伤扩展过程等高瞬态碰撞损伤信息的测量反演。
附图说明
50.图1为本发明的功能光纤网格制备工艺方法的流程图;
51.图2为本发明的功能光纤网格制备工艺方法中的光纤网格铺设工艺流程图;
52.图3为本发明的功能光纤网格制备工艺方法中的检测工艺流程图。
具体实施方式
53.为使本发明所述设计方法和优点更加清楚,下面将对一种功能光纤网格制备及其工艺方法进行全面阐述,对不同的应用需求场景的光纤选型方案进行分类说明,并结合实施例,对本发明实施例中的技术方案和实施结果进行清楚、完整地描述,显然,所描述的实
施例是本发明的一部分实施例,而不是全部的实施例。基于本发明中的实施例,本领域普通技术人员在没有做出创造性劳动的前提下所获得的所有其他实施例,都属于本发明保护的范围。
54.如图1所示,本发明的功能光纤网格制备工艺方法,包括以下步骤:
55.s1.需求分析;
56.根据设计输入参数,对被测形面的应用需求开展分析,分析内容包括被测形面特征分析、被测形面测试环境分析和测试精度需求分析;其中,设计输入参数包括被测物物理尺度、交会速度,被测形面特征包括厚度、材料、工艺和几何对称性,被测形面测试环境包括测试时长、表面温度变化,测试精度需求包括光纤网格密度。
57.s2.方案设计;
58.结合步骤s1的分析结果,根据被测形面特征、被测形面测试环境开展基体设计和光纤选型;
59.s21.基体设计,包括材料选型和线槽设计;
60.s211.材料选型;
61.从有利于制备光纤网格和进行铺设出发,选择具有适应测试环境温度变化性能的基体材料;对于耐温要求100℃及100℃以下,结合材料的轻质要求,并考虑被测形面与基体材料的粘接性能,选择易获取和进行机械加工的低温成型料,低温成型料为包括pc、尼龙在内的质轻易加工材料;对于耐温要求100℃以上,选择耐高温的高温成型料,高温成型料包括耐温pc、合成耐温软木,由于耐温pc在成型后更加轻质、结构稳定,优先选用耐温pc;
62.s212.线槽设计;
63.按照预先设定的精度要求,确定光纤预留线槽的走线方式,采用等距螺旋方式线槽,调整线槽密度,同时进行光纤冗余设计,确保在少数光纤失效的情况下,剩余的光纤完成精度要求的测量;
64.s22.光纤选型;
65.选定基体材料后,根据测试环境温度变化范围选择光纤类型和光电转换接头;
66.s221.选择光纤类型;
67.为实现在轻薄基体内铺设埋入光纤的目的,考虑光纤保护需要,采用小芯径的裸纤,裸纤是祛除光纤的保护外壳后,带有涂覆层的裸光纤;对于耐温要求100℃及100℃以下,采用通信光纤;对于耐温要求100℃以上,选择石英光纤;
68.s222.设计加工光纤转换接头;
69.首先考虑光纤与光纤接头的工艺适配,其次设计光电转换模块,再次将光纤、光电转换模块和光纤接头组合成光纤转换接头,随后检测确认光纤转换接头实现了光信号的可靠传输和识别,最后完成光纤转换接头设计加工。
70.s3.部件制备工艺;
71.s31.部件制备工艺包括基体制备工艺和光纤制备工艺;
72.s311.基体制备工艺;
73.对于耐温要求100℃及100℃以下,采用成型板料,按照基体分片设计和线槽设计开展机械加工,再放置在配套的拼接治具上进行拼接固化,完成基体成型;对于耐温要求100℃以上,选取耐温pc,由于耐温pc的材料流动性差,首先根据耐温pc注塑温度和耐温pc
注塑件形状设计若干高压注塑模具,并通过调温、调压和多点注塑工艺,获取若干耐温pc形面,再配合机加在若干耐温pc形面的表面刻线槽,最后将具有线槽的若干耐温pc形面放置在配套拼接治具上进行拼接固化,完成基体成型;
74.s312.光纤制备工艺;
75.光纤制备工艺首先根据线槽设计和应用需求确定光纤长度,并建立光纤编号规则,光纤制备时,按照既定长度和光纤编号进行加工;其次,根据光纤芯径与光纤转接头的标准适配制备工艺,连接裸纤和光纤转换接头;最后,根据应用需求对光纤转换接头根部与裸纤连接处进行硅胶点胶保护,硅胶点胶用于吸收局部应力,保证接头处的结构强度;
76.s32.部件制备工艺还包括设计部件制备工艺包括成型拼接工艺、固定工艺、工艺验证试验以及配套的工装治具;
77.成型拼接工艺根据被测形面的对称性、开孔特征、特殊区域特点设计被测形面专用的成型拼接方法;固定工艺设计包括套装粘接工艺在内的、专用的、基体与被测形面固定方法;工艺验证试验,根据需要开展包括材料成型、材料粘接、材料耐温试验的工艺验证方法;在成型拼接工艺、固定工艺、工艺验证试验过程中,设计制备相应的工装治具。
78.s4.光纤布设工艺,见图2;
79.s41.基体和光纤部件复检;
80.对基体尺寸、线槽设计进行复核;检查清理光纤线槽组成的基体网格,清理后用无水酒精清洗光纤线槽,做到线槽内无毛刺,残留物及油渍;暗室检查光纤通光性;
81.s42.光纤铺设粘接;
82.按照设计余量留出光纤长度,然后用软胶将光纤按照编码粘接到对应的线槽槽底,光纤不高出线槽表面,光纤的交叉点不高出基体表面;
83.s43.光纤通光检测;
84.每根光纤布设完成后,再次检测光纤通光性,及时更换通光性差或有损伤的光纤;
85.s44.线槽填胶;
86.全部光纤铺设完毕后,清除残余软胶,并在线槽内填充软硅胶,初步固化后清除多余软硅胶,使线槽表面平整;
87.s45.光纤保护;
88.对光纤集束和光纤头进行收纳保护;首先,利用热缩管分束保护裸纤,避免在运输过程中因裸纤互相缠绕,产生应力损坏裸纤;其次,用软泡沫薄膜包裹光纤头集束并固定光纤头集束,避免污染光纤端面,保证光纤通光性能。
89.s5.检测,具体的检验点设置见图3;
90.产品检测主要包括过程检测、产品出厂检测和应用功能检测;
91.过程检测是对前一步骤产出的过程产品与设计指标符合情况进行检查,保证后续工序开展和质量;
92.产品出厂检测包括结构参数检测、光纤通光功能检测和产品表面质量检查;结构参数包括外形结构参数、质量和厚度;
93.应用功能检测是产品后续应用过程中,配合应用工艺和场合对产品结构和光纤网格通光性进行检查。
94.进一步地,所述的软胶为808软胶,软硅胶为414软硅胶或者导热硅脂胶。
95.实施例1
96.本实施例的测量对象是薄壳金属锥段,被测形面为锥段,锥段高度1.2m,工作环境最高耐受温度为170℃,测试精度小于等于3cm。考虑到被测形面为尺度较大的锥段,决定设计可调温的钢模具,在高压下,通过钢模具的多点注塑口将牌号拜耳1803的耐高温pc颗粒料注塑制成基体片材,同时,按照精度和开孔需求设计等距螺旋结构网格,利用加工中心在基体片材上加工线槽,得到局部带网格的基体片材,再通过拼接治具对基体片材进行拼合粘接,得到整体锥段光纤网格。
97.选择芯径为200μm的石英光纤,按照线槽长度,将石英光纤预留合适的余量后分段,并剖离石英光纤的外壳,得到裸纤,在裸纤的两端适配光电转换接头,并进行填胶保护。而后利用808胶将裸纤固定在基体的网格线槽内,利用630mm~670mm光纤笔测量通光性,通光性合格后利用导热硅脂胶填充线槽,完成具有固定物理空间位置的薄锥段光纤网格制备。
98.将薄锥段光纤网格粘接到被测锥段薄壳上开展碰撞实验,结果表明,薄锥段光纤网格可以在高温条件下实现高瞬态碰撞损伤测量。
99.本实施例仅代表了该实施例的应用条件下的实施情况,不同情况的设计和工艺方法指导已在前述给出。