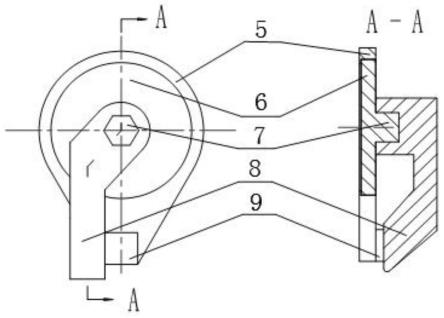
1.本发明涉及轮箍弛缓测试技术领域,尤其涉及一种检验机车轮箍弛缓原因的扭矩试验方法。
背景技术:2.当机车车轮是由轮芯与轮箍组成的结构时,轮芯与轮箍之间的过盈配合是采用热装的方法组装在一起的,目前组装后轮芯与轮箍防弛缓(径向错位)的质量是否合格,在车轮实际运用之前是没有任何检测手段进行认证的。如若在机车运行中车轮的轮芯与轮箍出现了弛缓现象,将会直接影响到机车的运行安全问题。因此,如何在机车车轮发生轮箍弛缓问题之前,从制造源头上查找事故原因,及时更改生产工艺,确保车轮运用的产品质量,填补检验轮箍弛缓原因测试的技术空白,是亟待解决的关键问题。
3.目前在车轮轮芯与轮箍的热装生产过程中,由于在轮箍防弛缓方面的质量保障没有任何的检测手段进行合格认证,属于严重的技术空缺。若在制造中出现失误,会直接影响到机车的运行安全,甚至造成严重的损失事故。目前所能采取的技术方案,只能是在车轮轮芯与轮箍的配合面处画有明显的弛缓线(如图1所示),便于观察判断轮芯与轮箍之间的画线在运用中是否出现有径向错位的弛缓现象。车轮运行后若发现画线产生有径向错位,那就意味着机车车轮发生轮箍弛缓现象,属于严重的车轮装配质量问题,必须应急处理;车轮运行后若画线位置始终保持不变,说明车轮轮芯与轮箍的装配质量合格可靠,属于车轮产品的正常状况。随着机车产品产量的不断发展,不断加强机车事故原因分析,提高机车产品质量,确保机车运行安全,是我们必须面对和完成的重要课题和任务。
4.综上所述,由于在现有的生产制造过程中,没有直接对车轮轮箍防弛缓方面的检测手段,也不做到这方面的质量认证,尤其是目前在轮箍组装中存在一个不能忽略的工艺环节,就是在完成轮箍、轮芯的加工后,通常都要在轮箍内环和轮芯外环的加工表面涂抹一层金属保护剂,以防止轮芯与轮箍在装配前发生锈蚀,造成无法组装的状况。如若在进行轮箍加热组装的过程中,轮箍内环和轮芯外环的防锈油没能及时处理干净,或轮芯轮箍的内外环上带有锈蚀杂质等情况:是否会影响到两者过盈量的变化,从而减弱车轮的装配强度?是否会影响轮芯与轮箍两者之间的扭矩传递,从而发生轮箍径向错位的弛缓现象?这些不确定的质量因素都是由于没有事前的试验认证手段,不做任何产前的测试验证,而无法保证车轮产品质量是否合格的最大缺陷,因此,研制出一种检验机车轮箍弛缓原因的扭矩试验方法具有重要意义。
技术实现要素:5.针对上述问题,本发明的目的在于提供一种检验机车轮箍弛缓原因的扭矩试验方法,确立了从车轮制造源头上查找轮箍弛缓原因根源的先例,填补了检验车轮轮箍弛缓原因扭矩测试的技术空白。
6.本发明采用的技术方案如下:
7.本发明所提出的一种检验机车轮箍弛缓原因的扭矩试验方法,包括以下步骤:
8.s1、研发配制四组相同的模拟车轮轮芯与轮箍的扭矩测试装置;所述扭矩测试装置由外环、内环、内芯六角头、液压扭矩扳手和反力臂挡块等五个部件组成;其中,外环用于模拟轮箍,内环用于模拟轮芯;所述外环的边缘配有一处反力臂挡块;所述内环的中心安置有内芯六角头;
9.s2、扭矩测试装置的组装条件为:外环和内环模拟轮箍和轮芯并加工有0.140mm-0.145mm的过盈量;其中两组扭矩测试装置在内外环的表面涂抹有任意介质,另外两组扭矩测试装置的内外环表面无任何介质;四组扭矩测试装置模拟车轮产品的装配工艺,分别采用加热外环的方式组装在一起;
10.s3、用液压扭矩扳手扭转内环中心的内芯六角头,反力矩点施加在外环边缘处的反力臂挡块上,使试件产生相互转动的趋势,分别测试两种工况下扭矩测试装置的承载扭矩能力,记录两工件发生相对转动临界点时液压扭矩扳手的扭矩值;
11.s4、通过对比四组测试数据,判断轮箍表面涂抹介质对扭矩数值的影响,从而测试出轮箍表面介质是否为造成轮箍弛缓的原因。
12.本发明与现有技术相比具有以下有益效果:
13.1、本发明确立了从车轮制造源头上查找轮箍弛缓事故根源的先例,填补了检验车轮轮箍弛缓原因扭矩测试的技术空白;
14.2、本发明技术方案的研发,解决了机车车轮生产制造过程中,没有直接对车轮轮箍防弛缓方面的检测手段,不做这方面的质量认证,无法保证车轮产品质量的弊端问题;
15.3、本发明技术方案的运用,彻底改变了在车轮装配过程中,没有及时处理干净车轮轮箍内环和轮芯外环防锈油的生产陋习,明确了车轮轮芯与轮箍两者之间扭矩传递的降低和发生轮箍弛缓的原因,提高了机车车轮的产品质量和运用周期。
16.4、实践证明:本发明技术方案的研制,设计思路新颖,操作有效实用,有效提升了车轮产品的生产质量和使用效果,是一项非常实用的创新技术,在机车车轮的制造方面了发挥应有的作用,能够得到很好的实际应用。
附图说明
17.图1为现有机车车轮的结构示意图;
18.图2为本发明方法使用的扭矩试验装置的结构示意图。
19.其中,附图标记:1-轮箍;2-轮芯;3-弛缓线;4-车轴;5-外环;6-内环;7-内芯六角头;8-液压扭矩扳手;9-反力臂挡块。
具体实施方式
20.为了更清楚地说明本发明实施例或现有技术中的技术方案,下面将对实施例或现有技术描述中所需要使用的附图做以简单地介绍,显而易见地,下面描述中的附图是本发明的一些实施例,对于本领域普通技术人员来讲,在不付出创造性劳动的前提下,还可以根据这些附图获得其他的附图。
21.需要说明的是,在本发明的描述中,术语“上”、“下”、“顶部”、“底部”、“一侧”、“另一侧”、“左”、“右”等指示的方位或位置关系为基于附图所示的方位或位置关系,仅是为了
便于描述本发明和简化描述,而不是指装置或元件必须具有特定的方位、以特定的方位构造和操作。
22.本发明所提出的一种检验机车轮箍弛缓原因的扭矩试验方法,包括以下步骤:
23.s1、为了对比车轮轮芯与轮箍环状配合面有无金属保护剂工况下的扭矩承载能力,研发配制四组相同的模拟车轮轮芯与轮箍的扭矩测试装置,如图2所示,该扭矩测试装置由外环5、内环6、内芯六角头7、液压扭矩扳手8和反力臂挡块9等五个部件组成,现有的机车车轮如图1所示,其中外环5模拟轮箍1,内环6模拟轮芯2,外环5的边缘配有一处反力臂挡块9,内环6的中心安置有内芯六角头7;
24.s2、扭矩测试装置的组装条件为:外环5和内环6模拟轮箍1和轮芯2并加工有0.140mm-0.145mm的过盈量;其中两组扭矩测试装置在内外环的表面涂抹有任意保护介质,另外两组扭矩测试装置的内外环表面无任何介质;四组扭矩测试装置模拟车轮产品的装配工艺,分别采用加热外环5的方式组装在一起;
25.s3、试验原理:用液压扭矩扳手8扭转内环6中心的内芯六角头7,反力矩点施加在外环5边缘处的反力臂挡块9上,使试件产生相互转动的趋势,分别测试两种工况下扭矩测试装置的承载扭矩能力,记录两种工况下工件发生相对转动临界点时液压扭矩扳手8的扭矩值;
26.s4、通过对比四组测试数据,判断表面保护介质对扭矩数值的影响,从而测试出表面的保护介质是否为造成轮箍弛缓的原因。
27.下面通过一个具体实例对本发明方法作进一步说明:
28.s1、研发配制四组相同的模拟车轮轮芯与轮箍的扭矩测试装置,如图2所示,该扭矩测试装置由外环5、内环6、内芯六角头7、液压扭矩扳手8和反力臂挡块9等五个部件组成,现有的机车车轮如图1所示,其中外环5模拟轮箍1,内环6模拟轮芯2,外环5的边缘配有一处反力臂挡块9,内环6的中心安置有内芯六角头7;
29.s2、首先将具有0.140mm-0.145mm过盈量的扭矩测试装置,其中两组在内外环的表面涂抹防锈剂,另外两组的内外环表面无任何介质,按照车轮轮芯与轮箍的组装工艺,采用加热外环5的热装方法将扭矩测试装置组装到一起;
30.s3、对每组扭矩测试装置分别利用液压扭矩扳手8扭转内环6中心的内芯六角头6,反力臂点施加在外环5边缘处的反力臂挡块9上,使扭矩测试装置产生相互转动的趋势,记录每组扭矩测试装置发生相对转动临界点时液压扭矩扳手8的扭矩值;
31.具体试验操控为:试验开始前设定液压扭矩扳手8的力矩值,开动液压力矩扳手8,并保持5秒以上,观察弛缓线是否错位,若发生错位,该组试验停止并记录力矩值;若不发生错位,继续增大力矩值,直至发生错位或达到液压扭矩扳手8的限值4200n.m。
32.试验结果记录如下:
[0033][0034]
s4、试验结论:通过以上试验结果进行分析,配合表面未涂抹任何介质的两组扭矩测试装置扭转力矩达到液压扳手限值4200n.m时未发生转动,配合表面涂有金属保护剂的两组扭矩测试装置在扭转力矩为3500n.m至3800n.m时发生转动。
[0035]
试验结果表明:涂有金属保护剂介质的两组扭矩数值明显小于无任何介质的两组扭矩数值;可得出有无金属保护剂介质直接影响到扭矩数值变化的结论;从而得出在热装轮箍之前,必须要把轮箍内环表面的防锈介质清理干净,否则,就会在车轮的运用中影响到轮箍弛缓的问题。
[0036]
当结合面存在金属保护剂的情况下,摩擦系数降低,导致扭矩承载能力降低,存在车轮轮箍弛缓的很大风险。
[0037]
本发明未详尽事宜为公知技术。
[0038]
以上所述的实施例仅仅是对本发明的优选实施方式进行描述,并非对本发明的范围进行限定,在不脱离本发明设计精神的前提下,本领域普通技术人员对本发明的技术方案做出的各种变形和改进,均应落入本发明权利要求书确定的保护范围内。