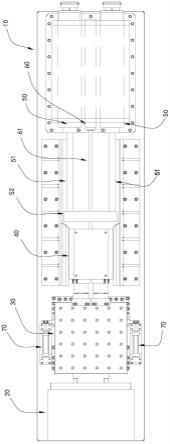
1.本发明属于测试仪器技术领域,具体涉及一种水平冲击响应谱试验台。
背景技术:2.冲击响应谱通常简称“冲击谱”,是描述单自由度振动系统受一定冲击作用时,响应的最大值与振动的固有频率或固有周期的关系的图线,广泛应用于结构动力学和缓冲减振系统设计。
3.水平冲击响应谱试验台是用于测试水平冲击响应谱的实验仪器,通常包括试验台底座、可滑动地设置在试验台底座上的冲击平台、用于承受冲击的响应平台、以及驱使冲击平台产生冲击力的冲击气缸,如中国专利cn106525373a就公开了这类水平冲击响应谱测量装置,由于冲击平台的冲击速度需要根据实验要求确定,使得冲击气缸的进气端较为复杂,在驱使冲击平台回位时,并不方便,若增设回位气缸,由于回位气缸的动作方向与冲击气缸基本一致,只能将其设置在冲击气缸下方的底座内,需要在底座上开设窗口连接冲击平台,对底座强度的影响较大,安装检修也并不方便,同时,采用常规气缸作为回位气缸时,由于进排气速度慢,又容易干涉冲击气缸的冲击动作,导致水平冲击响应谱测试结果的准确性不佳、复现性较差。
技术实现要素:4.本发明的目的是为了克服现有技术的缺点,提供一种测试结果准确性更好、复现性更好的水平冲击响应谱试验台。
5.为达到上述目的,本发明采用的技术方案是,水平冲击响应谱试验台,包括:沿前后方向依次设置在试验台底座上的固定座、响应平台、冲击平台、冲击气缸,所述响应平台、所述冲击平台可相对所述试验台底座前后移动的设置,所述冲击气缸用于驱动所述冲击平台向前移动,以撞击所述响应平台产生水平冲击;以及用于驱动所述冲击平台回位的回位气缸;所述冲击气缸有两个,这两个冲击气缸沿左右方向并排并间隔设置,这两个所述冲击气缸的气缸杆端部连接在同一块冲击板上,并通过该冲击板驱动所述冲击平台向前移动,所述回位气缸设置在这两个冲击气缸之间,所述回位气缸的气缸杆贯穿所述冲击板并与所述冲击平台的后端部相连接;所述回位气缸包括缸筒、连接在所述缸筒的前端部的前端盖、连接在所述缸筒的后端部的后端盖、可滑动地设置在所述缸筒内将所述缸筒的内腔分隔成前腔与后腔的活塞,所述活塞与所述回位气缸气缸杆远离所述冲击平台的端部相连接,所述前端盖内设有用于所述前腔进气的进气气道、用于所述前腔排气的排气气道,所述进气气道、所述排气气道交替通断,所述后端盖内设有用于所述后腔进排气的常通气道,所述常通气道的直径大于等于所述排气气道的直径,所述排气气道的直径大于等于所述进气气道直径的两倍。
6.优选地,所述回位气缸气缸杆的端部设有环形凹槽,所述冲击平台的后端部连接
与所述环形凹槽相匹配的卡块,所述卡块的一部分伸入所述环形凹槽内。
7.优选地,所述前端盖上还设有用于控制所述进气气道和所述排气气道交替通断的控制阀,所述控制阀包括阀体、设于所述阀体内的阀腔、阀芯,所述阀腔沿前后方向延伸,所述阀腔串联在所述进气气道及所述排气气道上,所述阀芯可前后滑动地设置在所述阀腔内,所述阀芯上设有与所述进气气道相匹配的连接气道,在所述阀芯向后移动至极限位置时,所述进气气道通过所述连接气道接通,所述排气气道断开,在所述阀芯向前移动至极限位置时,所述进气气道断开,所述排气气道接通。
8.进一步优选地,所述阀腔包括第一阀腔和第二阀腔,所述第一阀腔、所述第二阀腔的轴心线对称分布在所述缸筒的轴心线的两侧,所述第一阀腔串联在所述进气气道上,所述第二阀腔串联在所述排气气道上,所述阀芯包括设置在所述第一阀腔内的第一阀芯和设置在所述第二阀腔内的第二阀芯,所述连接气道设置在所述第一阀芯上。
9.进一步优选地,所述第一阀腔内还设有用于驱使所述第一阀芯向前移动的弹簧,所述第一阀芯的后端面设有用于容纳所述弹簧的前端部的环形弹簧槽。
10.进一步优选地,所述前端盖上还设有用于驱使所述阀芯向后移动的驱动组件,所述驱动组件包括连接在所述阀体的前端面的阀盖板、设于所述阀盖板内与用于向所述阀腔进排气的驱动气道。
11.进一步优选地,所述阀盖板的后端面设有环形气槽,所述驱动气道通过所述环形气槽与所述阀腔相连通。
12.优选地,所述常通气道与外界大气连通。
13.优选地,所述水平冲击响应谱试验台还包括用于驱使所述响应平台复位的复位气缸。
14.进一步优选地,所述复位气缸设置在所述试验台底座上并位于所述响应平台的左右两侧。
15.由于上述技术方案运用,本发明与现有技术相比具有下列优点:通过设置两个沿左右方向并排并间隔设置的冲击气缸,将这两个冲击气缸的气缸杆端部连接在同一块冲击板上,并通过该冲击板驱动冲击平台向前移动,将回位气缸设置在这两个冲击气缸之间,使回位气缸的气缸杆贯穿冲击板并与冲击平台的后端部相连接;使回位气缸包括缸筒、连接在缸筒的前端部的前端盖、连接在缸筒的后端部的后端盖、可滑动地设置在缸筒内将缸筒的内腔分隔成前腔与后腔的活塞,活塞与回位气缸气缸杆远离冲击平台的端部相连接,前端盖内设有用于前腔进气的进气气道、用于前腔排气的排气气道,进气气道、排气气道交替通断,后端盖内设有用于后腔进排气的常通气道,常通气道的直径大于等于排气气道的直径,排气气道的直径大于等于进气气道直径的两倍,既能从进气气道进气驱使冲击平台回位,又能利用排气气道、常通气道直径大的特点实现较高的进排气速度,避免对冲击动作的干涉,该水平冲击响应谱试验台测试结果的准确性、复现性更好,由于回位气缸设置在两个冲击气缸之间,安装检修方便,也无需在试验台台面上开设窗口,不影响试验台底座的强度。
附图说明
16.图1是本发明优选实施例的俯视示意图。
17.图2是图1中回位气缸的剖视放大示意图,此时,冲击平台处于冲击位置,第一阀芯和第二阀芯均处于第一工作位置。
18.图3是图2中a处的局部放大示意图。
19.图4是图1中回位气缸的剖视放大示意图,此时,冲击平台处于回位位置,第一阀芯和第二阀芯均处于第二工作位置。
20.图5是图4中b处的局部放大示意图。
21.图6是图1中回位气缸的剖视放大示意图,此时,冲击平台处于回位位置,第一阀芯处于第一工作位置,第二阀芯处于第二工作位置。
22.图7是图6中c处的局部放大示意图。
23.其中:10.试验台底座;11.承载台面;20.固定座;30.响应平台;40.冲击平台;41.卡块;50.冲击气缸;51.气缸杆;52.冲击板;60.回位气缸;61.气缸杆;611.环形凹槽;62.缸筒;621.前腔;622.后腔;63.前端盖;6311.第一进气气道;6312.第二进气气道;6321.第一排气气道;6322.第二排气气道;633.控制阀;6331.阀体;6332.第一阀腔;6333.第二阀腔;6334.第一阀芯;6335.第二阀芯;6336.第一连接气道;6337.第二连接气道;6338.弹簧;6339.环形弹簧槽;634.驱动组件;6341.阀盖板;6342.驱动气道;6343.环形气槽;635.进气口;636.排气口;64.后端盖;641.常通气道;65.活塞;70.复位气缸。
具体实施方式
24.下面结合附图对本发明的较佳实施例进行详细阐述,以使本发明的优点和特征更易于被本领域技术人员理解,从而对本发明的保护范围做出更为清楚明确的界定。
25.本发明中描述的前后、左右方向为图1中的下上、左右方向,本发明中描述的上下、前后方向是图2、图4、图6中的上下、左右方向。
26.如图1至图7所示,本发明提供的水平冲击响应谱试验台,包括:试验台底座10、固定座20、响应平台30、冲击平台40、冲击气缸50、回位气缸60、复位气缸70,其中,试验台底座10为框架式底座并具有沿前后方向水平延伸的承载台面11,固定座20、响应平台30、冲击平台40、冲击气缸50沿前后方向依次设置在承载台面11上,具体地,响应平台30、冲击平台40可相对于承载台面11前后移动地设置,冲击气缸50用于驱动冲击平台40向前移动,使冲击平台40撞击响应平台30,产生水平冲击,回位气缸60用于驱动冲击平台40回位,冲击气缸50有两个,这两个冲击气缸50沿左右方向并排并间隔设置,这两个冲击气缸50的气缸杆51的端部连接在同一块冲击板52上,冲击板52沿左右方向竖直延伸并位于冲击平台40的后方,冲击气缸50通过带动该冲击板52向前移动以驱动冲击平台40向前移动,冲击气缸50与冲击平台40不直接接触,在冲量传递完成后,冲击气缸50的气缸杆51、冲击板52不会对冲击平台40的移动产生影响,冲量的传递更加纯粹,测试指标基本不会出现偏差,回位气缸60设置在这两个冲击气缸50之间,回位气缸60的气缸杆61贯穿冲击板52并与冲击平台40的后端部相连接,该贯穿是指冲击板52上开设有与气缸杆61同轴的通孔,且该通孔的孔径大于气缸杆61的外径,气缸杆61在该通孔内前后移动时,不会与该通孔的孔壁产生接触;回位气缸60包括沿前后方向水平延伸的缸筒62、连接在缸筒62前端部的前端盖63、连接在缸筒62后端部的后端盖64、可滑动地设置在缸筒62内将缸筒62内腔分隔成前腔621与后腔622的活塞65,活塞65的前端部与回位气缸60气缸杆61远离冲击平台40的端部(后端部)相连接,前端盖63
内设有用于前腔621进气的进气气道、用于前腔621排气的排气气道,进气气道、排气气道交替通断,后端盖64内设有用于后腔622进排气的常通气道641,常通气道641与外界大气连通,常通气道641的直径大于等于排气气道的直径,排气气道的直径大于等于进气气道直径的两倍,具体地,常通气道641的直径为8mm,排气气道的直径也为8mm,进气气道的直径为4mm,上述直径是指气道最窄处的直径。
27.这样设置的好处在于,既能从进气气道进气驱使冲击平台回位,又能利用排气气道、常通气道直径大的特点实现较高的进排气速度,避免对冲击动作的干涉,该水平冲击响应谱试验台测试结果的准确性、复现性更好,同时,由于进气气道与排气气道交替通断,可以很好地匹配冲击气缸的冲击动作,由于回位气缸设置在两个冲击气缸之间,安装检修方便,也无需在试验台台面上开设窗口,不影响试验台底座的强度。
28.在本实施例中,为便于连接,回位气缸60气缸杆61的端部设有环形凹槽611,冲击平台40的后端部连接与环形凹槽611相匹配的卡块41,卡块41的一部分伸入环形凹槽611内,使回位气缸60的气缸杆61与冲击平台40相连接。
29.为实现进气气道与排气气道的交替通断,在本实施例中,前端盖63上还设有用于控制进气气道和排气气道交替通断的控制阀633,控制阀633包括阀体6331、设于阀体内的阀腔、阀芯,阀腔沿前后方向延伸,阀腔串联在进气气道及排气气道上,具体地,阀腔包括第一阀腔6332和第二阀腔6333,第一阀腔6332、第二阀腔6333的轴心线对称分布在缸筒62的轴心线的两侧,第一阀腔6332串联在进气气道上,将进气气道分隔成相互垂直的第一进气气道6311和第二进气气道6312,第二阀腔6333串联在排气气道上,将排气气道分隔成相互垂直的第一排气气道6321和第二排气气道6322;阀芯可前后滑动地设置在阀腔内,具体地,阀芯包括设置在第一阀腔6332内的第一阀芯6334以及设置在第二阀腔6333内的第二阀芯6335,第一阀芯6334上设有与进气气道相匹配的连接气道,连接气道包括垂直连通的第一连接气道6336和第二连接气道6337;进一步地,第一进气气道6311沿前后方向水平延伸,第一进气气道6331的后端部向后贯穿前端盖63的后侧壁与前腔621连通,第一进气气道6311的前端部向前贯穿第一阀腔6332的底壁,第二进气气道6312沿上下方向竖直延伸,第二进气气道6312的上端部向上贯穿前端盖63的侧壁形成进气口635,第二进气气道6312的下端部向下贯穿第一阀腔6332的侧壁;第一排气气道6321沿前后方向竖直延伸,第一排气气道6321的后端部向后贯穿前端盖63的后侧壁与前腔621连通,第一排气气道6321的前端部向前贯穿第二阀腔6333的底壁,第二排气气道6322沿上下方向竖直延伸,第二排气气道6322的上端部向上贯穿第二阀腔6333的侧壁,第二排气气道6322的下端部向下贯穿前端盖63的侧壁形成排气口636;第一连接气道6336沿前后方向水平延伸,第一连接气道6336的前端部与第二连接气道6337垂直连通,第一连接气道6336的后端部贯穿第一阀芯6334的后端面,第二连接气道6337沿上下方向竖直延伸,第二连接气道6337的中部与第一连接气道6336垂直连通,第二连接气道6337的端部贯穿第一阀芯6334的侧壁并与第一阀芯6334侧壁上开设的环形气道相连通;进气口635位于排气口636的前方,排气口636与外界大气连通;在第一阀芯6334向前移动至极限位置(第一工作位置)时,环形气道与第二进气气道6312在第一阀腔6332侧壁的开口错开,第一阀芯6334的外壁封堵住第二进气气道6312在第一阀腔6332侧壁的开口,使进气气道断开,在第一阀芯6334向后移动至极限位置(第二工作位置)时,环形气道与第二进气气道6312在第一阀腔6332侧壁的开口对齐,第一进气气道6311通过第一连
接气道6336、第二连接气道6337、环形气道与第二进气气道6312连通,使得进气气道通过连接气道接通;在第二阀芯6335向前移动至极限位置(第一工作位置)时,第一排气气道6321在第二阀腔6333底壁的开口和第二排气气道6322在第二阀腔6333侧壁的开口均露出,且第二阀芯6335位于这两个开口的前方,第一排气气道6321通过第二阀腔6333与第二排气气道6322连通,使排气气道接通,在第二阀芯6335向后移动至极限位置(第二工作位置)时,第二阀芯6335封堵住第一排气气道6321在第二阀腔6333底壁的开口和第二排气气道6322在第二阀腔6333侧壁的开口,使排气气道断开。
30.在本实施例中,第一阀芯6334与第二阀芯6335向后移动至极限位置的动作保持同步,以实现进气气道、排气气道的交替通断,为实现这一效果,优选地,前端盖63上还设有用于驱使第一阀芯6334和第二阀芯6335同步向后移动的驱动组件634,驱动组件634包括连接在阀体6331的前端面的阀盖板6341、设于阀盖板6341内与用于向第一阀腔6332和第二阀腔6333进排气的驱动气道6342、以及设置在阀盖板6341后端面的环形气槽6343,驱动气道6342通过环形气槽6343与第一阀腔6332和第二阀腔6333同步接通。
31.在驱动气道6342通入压缩空气、第一进气气道6311通入压缩空气,且冲击气缸50的冲击动作结束时,第一阀芯6334、第二阀芯6335向后移动至极限位置,进气气道接通,排气气道断开,缸体61的前腔621进气,推动活塞65向后移动,带动回位气缸60的气缸杆61、冲击平台40向后移动,实现回位,在回位过程中,冲击平台40触碰冲击板52并带动冲击板52向后移动,使冲击气缸50回位。
32.为实现第一阀芯6334的自动复位,在本实施例中,第一阀腔6332内还设有用于驱使第一阀芯6334向前移动至极限位置的弹簧6338,第一阀芯6334的后端面设有用于容纳弹簧6338前端部的环形弹簧槽6339。
33.在回位气缸60带动冲击平台40、冲击气缸50回位后,释放驱动气道6342内的压缩空气,第一阀芯6334在弹簧6338及前腔621内气压的作用下向前移动至极限位置,断开进气气道,在其移动至极限位置后,第二阀芯6335才在前腔621内气压的作用下向前移动至极限位置,使排气气道接通,使前腔621内的压缩空气通过排气气道释放至外界大气。
34.由于弹簧6338的存在,第一阀芯6334和第二阀芯6335在向前移动至极限位置时有时间差,使得第一进气气道6311可以保持在通入压缩空气的状态,而不会造成压缩空气的浪费,为方便冲击作业,在本发明中,进气口635与恒压气源连通。
35.为实现响应平台30的复位,在本实施例中,该水平冲击响应谱试验台还包括用于驱使响应平台30复位的复位气缸70,复位气缸70设置在试验台底座10上并位于响应平台30的左右两侧。
36.上述实施例只为说明本发明的技术构思及特点,其目的在于让熟悉此项技术的人士能够了解本发明的内容并据以实施,并不能以此限制本发明的保护范围,凡根据本发明精神实质所作的等效变化或修饰,都应涵盖在本发明的保护范围之内。