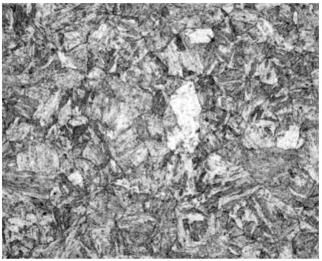
1.本发明涉及金相分析领域一种对特定材料的表征方法,特别提供了一种马氏体不锈钢显微晶粒度的表征方法。
背景技术:2.根据国内行业和国外标准的调查咨询,原有马氏体不锈钢显微晶粒度的表征方法主要使用苦味酸作为主要腐蚀剂成分。但由于苦味酸的毒性和易爆性,2018年开始国内已禁止生产和销售,而替代腐蚀方法尚未成熟,无专用方法。目前公司内对马氏体不锈钢的腐蚀主要借鉴其它材料的腐蚀方法进行,存在腐蚀前热处理方式不统一、腐蚀过程缺乏再现性、晶粒度晶界腐蚀不清晰等问题,需要多次试验才能保证检测质量,严重影响马氏体不锈钢显微晶粒度的评定效果和效率。
3.人们迫切希望获得一种技术效果优良的马氏体不锈钢显微晶粒度的表征方法。
技术实现要素:4.本发明的目的是提供一种技术效果优良的马氏体不锈钢显微晶粒度的表征方法,实现对马氏体不锈钢显微晶粒度的清晰观察和高效评定。
5.所述马氏体不锈钢显微晶粒度的表征方法具体步骤如下:
6.步骤一:取马氏体不锈钢试样淬火热处理,制度为1050
±
10℃保温1小时,然后进行冷却;
7.步骤二:对经过淬火的马氏体不锈钢试样金相制样后进行化学腐蚀,采用的腐蚀液成分及配比具体为:cuso4:乙醇:盐酸:烷基苯磺酸钠=3~4g:80~100ml:15~25ml:0.5~1.5g,腐蚀液现场配置后立即使用,腐蚀方式为在常温状态下擦拭腐蚀180-300s。
8.优选的,步骤一中的冷却方式为油冷或空冷。
9.确定马氏体不锈钢显微晶粒度的表征方法过程如下:
10.首先,通过热处理试验验证不同热处理方式对腐蚀效果影响。
11.切取金相试样,按相应技术标准规定的温度分别对1c12ni3mo2vn(m152)、1cr11ni2w2mov、0cr17ni4cu4nb三种材料进行淬火、淬火+回火热处理。
12.将淬火、淬火+回火热处理与不进行热处理锻态材料试样按同样腐蚀参数分别进行化学腐蚀和电解腐蚀试验,比较同一腐蚀方法下的腐蚀效果,确定不同材料腐蚀前的最佳热处理准备方式。
13.其次,开展腐蚀剂的配方改进和腐蚀参数调整试验,确定最佳腐蚀剂配比和腐蚀参数;
14.主要以硫酸+水、cro3+水等为主要成分,通过其它成分的添加来优化腐蚀效果,开展电解腐蚀试验,并摸索电解电压、时间对晶粒腐蚀效果的影响。
15.通过改变配比,筛选出5种可对马氏体进行腐蚀的化学腐蚀剂,并根据晶粒腐蚀的效果调整腐蚀参数。
16.最后,开展腐蚀验证试验,固化不同马氏体材料的腐蚀方法,并建立操作说明书。
17.所述马氏体不锈钢显微晶粒度的表征方法通过试验与验证,确定了马氏体不锈钢显微晶粒度的腐蚀剂配方和最佳腐蚀方法。相对原有腐蚀效果有了明显改进,晶粒度表征清晰,评级准确性和重复性有了明显提高。该表征方法的发明实现了通过一次热处理+一次磨制抛光腐蚀即可完成评定工作。评定总工时由原来的多次热处理试验和腐蚀试验的31工时缩短为6个工时,淬火3工时+制备腐蚀观测3工时。腐蚀后晶粒度显示效果具备比较法评级条件,经验证,晶粒度评级值的再现性控制在
±
0.5级。
附图说明
18.下面结合附图及实施方式对本发明作进一步详细的说明:
19.图1为1cr11ni2w2mov淬火后组织图;
20.图2为1cr11ni2w2mov淬火并回火后组织图;
21.图3为1cr11ni2w2mov未经加热的锻态组织图;
22.图4为0cr17ni4cu4nb淬火后组织图;
23.图5为0cr17ni4cu4nb淬火并回火后组织图;
24.图6为0cr17ni4cu4nb未经加热的锻态组织图;
25.图7为1cr12ni3mo2vn(m152)淬火后组织图;
26.图8为1cr12ni3mo2vn(m152)淬火并回火后组织图;
27.图9为1cr12ni3mo2vn(m152)未经加热的锻态组织图;
28.图10为10%草酸溶液对1c12ni3mo2vn(m152)电解腐蚀后组织图;
29.图11为10%草酸溶液对1cr11ni2w2mov电解腐蚀后组织图;
30.图12为4%铬酸溶液对1c12ni3mo2vn(m152)电解腐蚀后组织图;
31.图13为4%铬酸溶液对1cr11ni2w2mov电解腐蚀后组织图;
32.图14为10%硫酸溶液对1cr11ni2w2mov电解腐蚀后组织图;
33.图15为10%硫酸溶液对1c12ni3mo2vn(m152)电解腐蚀后组织图;
34.图16为对马氏体不锈钢采用hno3+乙醇,擦拭300s后组织图;
35.图17为对马氏体不锈钢采用cucl2+乙醇+盐酸,擦拭60s后组织图;
36.图18为马氏体不锈钢采用cuso4+乙醇+盐酸,擦拭90s后组织图;
37.图19为对马氏体不锈钢采用cuso4+乙醇+盐酸”+乙醇,擦拭120s后组织图;
38.图20为对马氏体不锈钢采用cuso4+乙醇+盐酸”+烷基苯磺酸钠,擦拭240s后组织图;
39.图21为对马氏体不锈钢采用cuso4+乙醇+盐酸”+烷基苯磺酸钠+乙醇,擦拭240s后组织图;
40.图22为对马氏体不锈钢采用浓硫酸+高锰酸钾+水,加热600s后组织图;
41.图23为对马氏体不锈钢采用浓硫酸+高锰酸钾+水,加热400s+擦拭200s后组织图。
具体实施方式
42.实施例1
43.①
比较热处理对马氏体不锈钢组织的影响:
44.对1c12ni3mo2vn(m152)、1cr11ni2w2mov、0cr17ni4cu4nb三种材料分别进行淬火、淬火+回火热处理,热处理后三种材料均为较为细小的隐针马氏体组织。直接采用淬火的组织上还能隐约看到晶界轮廓;而淬火+回火后的组织上主要显示晶内的马氏体束形貌,晶界相对显示不清楚;未进行热处理的锻态组织与淬火+回火后的组织类似,晶界更不清楚。具体参见附图1-9。
45.通过对马氏体不锈钢试样分别进行“淬火”和“淬火+回火”热处理后,与原锻态相比,腐蚀效果从高到低为:“淬火”》“淬火+回火”》原锻态。因此试样的最佳处理方式为淬火,避免了回火和重新热处理时间。
46.②
比较电解腐蚀和化学腐蚀对马氏体不锈钢的腐蚀效果:
47.电解腐蚀后马氏体不锈钢的显微组织未完全显示,不适于晶粒度的腐蚀。其中,利用10%草酸溶液,通120s的10v电压,对1c12ni3mo2vn(m152)电解腐蚀后的组织图参见附图10。利用10%草酸溶液,通120s的10v电压,对1cr11ni2w2mov电解腐蚀后的组织图参见附图11。利用4%铬酸溶液,通120s的10v电压,对1c12ni3mo2vn(m152)电解腐蚀后的组织图参见附图12。利用4%铬酸溶液,通120s的10v电压,对1cr11ni2w2mov电解腐蚀后的组织图参见附图13。利用10%硫酸溶液,通120s的10v电压,对1cr11ni2w2mov电解腐蚀后的组织图参见附图14。利用10%硫酸溶液,通120s的10v电压,对1c12ni3mo2vn(m152)电解腐蚀后的组织图参见附图15。
48.通过合理的化学腐蚀和腐蚀参数适于晶粒度的腐蚀。其中,对马氏体不锈钢采用hno3+乙醇,擦拭300s后,组织图参见附图16,对马氏体不锈钢采用cucl2+乙醇+盐酸,擦拭60s后,组织图参见附图17,对马氏体不锈钢采用cuso4+乙醇+盐酸,擦拭90s后,组织图参见附图18,对马氏体不锈钢采用cuso4+双份乙醇+盐酸,擦拭120s后,组织图参见附图19,对马氏体不锈钢采用cuso4+乙醇+盐酸”+烷基苯磺酸钠,擦拭240s后,组织图参见附图20,对马氏体不锈钢采用cuso4+双份乙醇+盐酸”+烷基苯磺酸钠,擦拭240s后,组织图参见附图21,对马氏体不锈钢采用浓硫酸+高锰酸钾+水,加热600s后,组织图参见附图22,对马氏体不锈钢采用浓硫酸+高锰酸钾+水,加热400s+擦拭200s后,组织图参见附图23,最佳腐蚀方式为使用cuso4+双份乙醇+盐酸+烷基苯磺酸钠进行化学腐蚀(配比为4g:80ml:20ml:0.5g),腐蚀方式为常温擦拭240s。
49.通过腐蚀试验确定马氏体不锈钢最佳腐蚀方式为使用“cuso4+乙醇+盐酸+烷基苯磺酸钠”进行化学腐蚀,可以通过一次腐蚀就获得良好的显微组织和晶粒度,避免了多次重复镶嵌、研磨、腐蚀和观测。
50.验证试验表明,按上述方式热处理及腐蚀后的晶粒晶界可有效辨识,可以按gb/t6394《金属平均晶粒度测定方法》中的比较法进行评级,同批试样的晶粒度评级值的再现性控制在
±
0.5级。
51.实施例2
52.①
马氏体不锈钢试样热处理试验
53.分别切取马氏体不锈钢试样,参考常用技术标准规定的温度分别对1cr11ni2w2mov、0cr17ni4cu4nb、1cr12ni3mo2vn三种材料进行淬火、淬火+回火、回火热处理,选择热处理制度见表1。淬火保温时间及回火保温时间均为1小时。
[0054][0055]
表1
[0056]
将热处理后试样磨制马氏体不锈钢试样,均采用kalling腐蚀剂对试样进行腐蚀,观察其显微组织,腐蚀时间30s,放大倍数均为100倍。
[0057]
热处理后三种材料均为较为细小的隐针马氏体组织。直接采用淬火的组织上还能隐约看到晶界轮廓;而淬火+回火后的组织上主要显示晶内的马氏体束形貌,晶界相对显示不清楚;未进行热处理的锻态组织与淬火+回火后的组织类似,晶界更不清楚。根据对马氏体束的观察,未发现热处理前后晶粒大小存在明显改变。
[0058]
热处理试验结果
[0059]
第一,晶界显示均不清楚,主要靠马氏体束分析晶粒大小;
[0060]
第二,晶界相对显示效果:淬火》淬火+回火》锻态
[0061]
第三,热处理前后晶粒大小未发生明显改变
[0062]
从热处理试验结果看,只采用淬火的试样相对淬火+回火的试样晶界更为清楚,推荐在标准允许情况下,对马氏体进行晶粒度评级前进行淬火处理,为晶粒度评级创造更好的基础。
[0063]
②
马氏体不锈钢试样电解腐蚀试验
[0064]
参见表2的电解腐蚀试验方案,分别采用草酸溶液、铬酸溶液、硫酸溶液这3种腐蚀剂对三种材料“淬火”后的试样进行腐蚀试验。电解设备均采用标乐公司的electromet 4型电解抛光机。电解电压为3v-10v,电解时间为10s-120s。
[0065][0066]
表2
[0067]
对于10%草酸溶液,分别采用3v,5v,10v对三种马氏体不锈钢进行了电解,电解过程试样表面均无明显变化。在电压和时间最大情况下的典型腐蚀效果其显微组织未完全显现,表明该腐蚀剂不适于马氏体不锈钢晶粒度的腐蚀。
[0068]
对于4%铬酸溶液,铬酸溶液的电解腐蚀效果略强于草酸溶液,但在最大设计参数条件下,显微组织未完全显示,同样不适于马氏体不锈钢晶粒度的腐蚀。
[0069]
对于10%硫酸溶液,3v条件下电解腐蚀无明显变化,电压达到5v和10v时试样表面出现变化,其中10v,180s条件显微组织显现明显,但晶界仅有局部显示,清晰度也不足以进行晶粒度评定。因此,该腐蚀剂不适于马氏体不锈钢晶粒度的腐蚀。
[0070]
③
马氏体不锈钢试样化学腐蚀试验
[0071]
化学腐蚀试验方案参见表3,分别对三种材料进行化学腐蚀测试。腐蚀剂分别为hno3+乙醇、cucl2+乙醇+盐酸(kalling腐蚀剂)、cuso4+乙醇+盐酸、cuso4+乙醇+盐酸+烷基苯磺酸钠,浓硫酸+高锰酸钾+水。采用这5种腐蚀剂开展腐蚀试验。试样选择为“淬火”态。
[0072][0073]
表3
[0074]
对于hno3+乙醇,腐蚀时间30s-300s。从腐蚀结果看,该腐蚀剂对马氏体不锈钢的显微组织均很难腐蚀,随腐蚀时间的延长,组织也仅有轻微显现。
[0075]
对于cucl2+乙醇+盐酸,腐蚀时间20s-60s。从腐蚀结果看,该腐蚀剂对马氏体不锈钢的马氏体组织优先腐蚀,随腐蚀时间的延长,晶界开始显现,但并不完全。进一步放大后采用暗场方式观察,可看出经长时间腐蚀后,晶界与晶内存在明显高度差,因而晶界开始显现,但晶粒内的条状的马氏体针也开始腐蚀,出现过腐蚀,干扰了晶粒边界的判断。
[0076]
对于cuso4+乙醇+盐酸/cuso4+乙醇+盐酸+烷基苯磺酸钠,cuso4+乙醇+盐酸,相对cucl2+乙醇+盐酸,腐蚀程度较慢,而且腐蚀相对均匀,不像cucl2+乙醇+盐酸对一些特定强化相和组织,比如高温合金δ相更具腐蚀性,因而判断可能更适合对马氏体的腐蚀。
[0077]
分别采用cuso4+乙醇+盐酸,对三种材料进行腐蚀,腐蚀时间20s-90s。从腐蚀结果看,该腐蚀剂对马氏体不锈钢腐蚀效果与cucl2+乙醇+盐酸的腐蚀效果相近,也是马氏体优先腐蚀,晶界随后显现,但晶粒度清晰度相对更高。
[0078]
试验结果证明了cuso4+乙醇+盐酸,对马氏体晶粒度有较好的腐蚀效果,但显示出的晶界仍不足以准确判定晶粒大小。通过减慢马氏体针的腐蚀速度应有利于晶粒度的全部显现。根据这一分析结果,开展了对该配方的改进,主要途径有两个:通过增加乙醇量降低腐蚀剂浓度;通过加入烷基苯磺酸钠,即洗洁精中的表面活性剂,作为缓蚀剂。
[0079]
通过改进试验可见,在cuso4+乙醇+盐酸,腐蚀剂加入乙醇和烷基苯磺酸钠都有助于马氏体组织腐蚀程度减缓和晶界的显现,最优的腐蚀剂配比为两者同时加入并延长擦拭腐蚀时间,具体为cuso4+乙醇+盐酸+烷基苯磺酸钠:4g+80ml+20ml+0.5g,腐蚀方式为常温擦拭180s-300s。其中烷基苯磺酸钠可用市场销售家用洗洁精,含烷基苯磺酸钠12%左右替代,约为4ml。该腐蚀方法对马氏体不锈钢的晶粒腐蚀效果较好,晶界基本都已显示,可用于进行晶粒度大小的检测。
[0080]
对于浓硫酸+高锰酸钾+水,第一次腐蚀选择常温下进行,腐蚀最长时间最长为300s,通过观察可见,所有试样的显微组织未完全显现,无法评定晶粒大小。鉴于第一次腐蚀缓慢,第二次腐蚀在加热状态下进行,将试样浸入腐蚀液,并加热至沸腾状态,腐蚀300s发现表面开始腐蚀,见图20。马氏体组织充分显示,但晶界并不完整。将试样重新浸入腐蚀液继续腐蚀,腐蚀延长至600s。腐蚀过程中可见腐蚀表面产生大量腐蚀产物,将其中一组试样在腐蚀400s时取出对表面的腐蚀层进行擦拭去除后继续腐蚀,另一组试样一直腐蚀,并在腐蚀后进行超声清洗,清洗时间30s。根据腐蚀结果,在400s腐蚀中断重新处理后的试样晶粒度显示效果强于一直腐蚀600s的试样。表明腐蚀过程中间的试样表面腐蚀层去除有利于试样均匀腐蚀和晶界的显现。因此采用“浓硫酸+高锰酸钾+水”腐蚀剂对马氏体不锈钢进行腐蚀时应在加热状态进行,并腐蚀较长时间才能显示晶界,其中中途去除腐蚀产物会获得更好的效果。最优的腐蚀方式为“浓硫酸+高锰酸钾+水:10ml+2.5g+90ml”,煮沸腐蚀400s后将试样取出擦拭去除腐蚀层,并继续腐蚀至600s。
[0081]
通过化学腐蚀剂的试验和验证,常温状态的cuso4+乙醇+盐酸+烷基苯磺酸钠,及加热状态的浓硫酸+高锰酸钾+水,均可对马氏体不锈钢的晶界有较好的腐蚀效果,可作为晶粒度评定的腐蚀剂。但从检测过程的复杂程度看,后者需去除表面腐蚀产物方可观察,操作过程复杂,污染较高。同时,高锰酸钾也面临化学药品管控问题,建议作为备选方案。
[0082]
④
验证试验
[0083]
根据上述试验结果,马氏体不锈钢的最佳热处理方式为淬火,最佳腐蚀剂为cuso4+乙醇+盐酸+烷基苯磺酸钠,进行化学腐蚀,腐蚀方式为常温擦拭240s。选取
1cr11ni2w2mov、0cr17ni4cu4nb、1c12ni3mo2vn三种材料的各3块试样按同样方式进行淬火热处理,磨制、抛光进行腐蚀。将腐蚀后的试样放大100倍观察,并与标准评级图进行比较。
[0084]
一次腐蚀,三种材料的晶粒基本全部显现,各组试样的评定结果基本一致,同批晶粒度评级值的再现性最大为0.5级,验证试验方案见表4。
[0085][0086]
表4
[0087]
实施例3
[0088]
所述马氏体不锈钢显微晶粒度的表征方法具体步骤如下:
[0089]
步骤一:取马氏体不锈钢试样淬火热处理,制度为1050
±
10℃保温1小时,然后进行冷却;
[0090]
步骤二:对经过淬火的马氏体不锈钢试样金相制样后进行化学腐蚀,采用的腐蚀液成分及配比具体为:cuso4:乙醇:盐酸:烷基苯磺酸钠=3~4g:80~100ml:15~25ml:0.5~1.5g,腐蚀液现场配置后立即使用,腐蚀方式为在常温状态下擦拭腐蚀180-300s。
[0091]
所述步骤一中的冷却方式为油冷或空冷。
[0092]
实施例4
[0093]
所述马氏体不锈钢显微晶粒度的表征方法具体步骤如下:
[0094]
步骤一:取马氏体不锈钢试样淬火热处理,制度为1050
±
10℃保温1小时,然后进行冷却;
[0095]
步骤二:对经过淬火的马氏体不锈钢试样金相制样后进行化学腐蚀,采用的腐蚀液成分及配比具体为:cuso4:乙醇:盐酸:烷基苯磺酸钠=3g:80ml:15ml:0.5g,腐蚀液现场配置后立即使用,腐蚀方式为在常温状态下擦拭腐蚀180-300s。
[0096]
所述步骤一中的冷却方式为油冷或空冷。
[0097]
实施例5
[0098]
所述马氏体不锈钢显微晶粒度的表征方法具体步骤如下:
[0099]
步骤一:取马氏体不锈钢试样淬火热处理,制度为1050
±
10℃保温1小时,然后进行冷却;
[0100]
步骤二:对经过淬火的马氏体不锈钢试样金相制样后进行化学腐蚀,采用的腐蚀液成分及配比具体为:cuso4:乙醇:盐酸:烷基苯磺酸钠=4g:100ml:25ml:1.5g,腐蚀液现场配置后立即使用,腐蚀方式为在常温状态下擦拭腐蚀180-300s。
[0101]
所述步骤一中的冷却方式为油冷或空冷。
[0102]
实施例6
[0103]
所述马氏体不锈钢显微晶粒度的表征方法具体步骤如下:
[0104]
步骤一:取马氏体不锈钢试样淬火热处理,制度为1050
±
10℃保温1小时,然后进行冷却;
[0105]
步骤二:对经过淬火的马氏体不锈钢试样金相制样后进行化学腐蚀,采用的腐蚀液成分及配比具体为:cuso4:乙醇:盐酸:烷基苯磺酸钠=3.5g:90ml:20ml:1g,腐蚀液现场配置后立即使用,腐蚀方式为在常温状态下擦拭腐蚀180-300s。
[0106]
所述步骤一中的冷却方式为油冷或空冷。