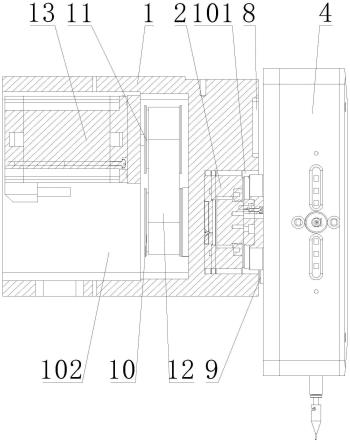
1.本发明涉及推拉力装置技术领域,尤其是一种推拉力机旋转定位机构。
背景技术:2.推拉力机是一种用于推力及拉力测试的力学测量仪器,适用于电子电器、轻工纺织、建筑五金、打火机及点火装置、消防器材、制笔、制锁、渔具、动力机械、科研机构等行业的推拉负荷测试。现有技术中的推拉力设备一般都是将传感器作为一个独立的单件,从而能够方便工作人员手动更换传感器,达到传感器自动更换的目的。
3.手动更换容易造成模块损坏或者摔坏,且更换增加工时,一定程度上降低了设备的生产效率。
技术实现要素:4.本发明的目的是针对背景技术中存在的问题,提出一种能够避免更换传感器模块造成其损坏的推拉力机旋转定位机构。
5.本发明的技术方案:一方面,本发明提出的一种推拉力机旋转定位机构,包括机壳、旋转盘、第一推力传感器、第二推力传感器、拉力传感器、定位传感器、感应基准点和用于控制旋转盘转动的动力机构;
6.机壳横向两侧分别设置有安装槽和放置槽,安装槽和放置槽错开;动力机构设置在安装槽和放置槽内;旋转盘设置在设置在动力机构上,旋转盘中心设置有安装孔,动力机构贯穿安装孔;第一推力传感器、第二推力传感器和拉力传感器均内嵌设置在旋转盘远离动力机构的横向一侧,第一推力传感器和第二推力传感器分别位于安装孔前后两侧,拉力传感器位于安装孔下方;定位传感器内嵌设置在机壳靠近旋转盘的横向一侧,定位传感器位于安装槽上方,感应基准点设置在机壳靠近旋转盘的横向一侧且位于安装槽下方;定位传感器与感应基准点通讯连接,定位传感器与动力机构控制连接。
7.优选的,动力机构包括减速器和电动机;减速器设置在安装槽内,旋转盘设置在减速器上,减速器贯穿安装孔,电动机设置在放置槽内,电动机通过皮带传动机构或链传动机构与减速器传动连接,定位传感器与电动机控制连接。
8.优选的,皮带传动机构包括从动带轮、主动带轮和皮带;从动带轮设置在放置槽内,从动带轮与减速器传动连接,主动带轮设置在电动机输出端,主动带轮通过皮带与从动带轮传动连接。
9.优选的,皮带的截面为圆形或三角形。
10.另一方面,本发明提供一种推拉力机旋转定位机构的使用方法,包括以下步骤:
11.s1、将计算机与动力机构进行控制连接,并将计算机与定位传感器通讯连接;
12.s2、通过计算机控制动力机构启动,动力机柜带动旋转盘转动,旋转盘带动其上的推力传感器或拉力传感器转动;
13.s3、定位传感器通过检测感应基准点的位置,将相关电信号传递给计算机,计算机
控制动力机构转动一定角度。
14.优选的,与现有技术相比,本发明具有如下有益的技术效果:
15.本发明使用时,通过传感器固定座以电动机旋转角度完成各工位自动定位,可以完全避免人员在更换传感器模时因人为因素造成模块损坏及摔落的风险,同时无需更换传感器模块,大大提高设备生产效率。
附图说明
16.图1为本发明提出的一种实施例的局部剖视图。
17.图2为本发明提出的一种实施例的主视图。
18.附图标记:1、机壳;101、安装槽;102、放置槽;2、减速器;4、旋转盘;401、安装孔;5、第一推力传感器;6、第二推力传感器;7、拉力传感器;8、定位传感器;9、感应基准点;10、从动带轮;11、主动带轮;12、皮带;13、电动机。
具体实施方式
19.如图1-2所示,一方面,本发明提出的一种推拉力机旋转定位机构,包括机壳1、旋转盘4、第一推力传感器5、第二推力传感器6、拉力传感器7、定位传感器8、感应基准点9和用于控制旋转盘4转动的动力机构;
20.机壳1横向两侧分别设置有安装槽101和放置槽102,安装槽101和放置槽102错开;动力机构设置在安装槽101和放置槽102内;旋转盘4设置在设置在动力机构上,旋转盘4中心设置有安装孔401,动力机构贯穿安装孔401;第一推力传感器5、第二推力传感器6和拉力传感器7均内嵌设置在旋转盘4远离动力机构的横向一侧,第一推力传感器5和第二推力传感器6分别位于安装孔401前后两侧,拉力传感器7位于安装孔401下方;定位传感器8内嵌设置在机壳1靠近旋转盘4的横向一侧,定位传感器8位于安装槽101上方,感应基准点9设置在机壳1靠近旋转盘4的横向一侧且位于安装槽101下方;定位传感器8与感应基准点9通讯连接,定位传感器8与动力机构控制连接。本发明中,第一推力传感器5、第二推力传感器6和拉力传感器7的数量并不限定,可以选择多个传感器配合使用。
21.动力机构包括减速器2和电动机13;减速器2设置在安装槽101内,旋转盘4设置在减速器2上,减速器2贯穿安装孔401,电动机13设置在放置槽102内,电动机13通过皮带传动机构或链传动机构与减速器2传动连接,定位传感器8与电动机13控制连接。
22.皮带传动机构包括从动带轮10、主动带轮11和皮带12;从动带轮10设置在放置槽102内,从动带轮10与减速器2传动连接,主动带轮11设置在电动机13输出端,主动带轮11通过皮带12与从动带轮10传动连接,皮带12的截面为圆形或三角形,皮带12的形状不仅限于此,还可以是其他形状的皮带12。
23.本发明使用时,工作人员应当先将计算机与电动机13进行控制连接,然后将计算机与定位传感器8通讯连接;工作人员需要根据需要选择不同规格的推力传感器或者拉力传感器时,只需要通过计算机软件控制电动机13启动,电动机13驱动主动带轮11转动,主动带轮11通过皮带12带动从动带轮10转动,从而带动减速器2转动,进而带动旋转盘4转动,进而带动其上的推力传感器和拉力传感器转动。安装在旋转盘4上的第一推力传感器5、第二推力传感器6和拉力传感器7可以依据产品需要任意选择使用。在选择使用某一款传感器
后,电动机13会利用定位传感器8通过感应基准点9后进行精确计算,旋转到指定角度进行准确定位。
24.本发明使用时,通过传感器固定座以电动机13旋转角度完成各工位自动定位,可以完全避免人员在更换传感器模时因人为因素造成模块损坏及摔落的风险,同时无需更换传感器模块,大大提高设备生产效率。
25.上面结合附图对本发明的实施方式作了详细说明,但是本发明并不限于此,在所属技术领域的技术人员所具备的知识范围内,在不脱离本发明宗旨的前提下还可以作出各种变化。
技术特征:1.一种推拉力机旋转定位机构,其特征在于,包括机壳(1)、旋转盘(4)、第一推力传感器(5)、第二推力传感器(6)、拉力传感器(7)、定位传感器(8)、感应基准点(9)和用于控制旋转盘(4)转动的动力机构;机壳(1)横向两侧分别设置有安装槽(101)和放置槽(102),安装槽(101)和放置槽(102)错开;动力机构设置在安装槽(101)和放置槽(102)内;旋转盘(4)设置在设置在动力机构上,旋转盘(4)中心设置有安装孔(401),动力机构贯穿安装孔(401);第一推力传感器(5)、第二推力传感器(6)和拉力传感器(7)均内嵌设置在旋转盘(4)远离动力机构的横向一侧,第一推力传感器(5)和第二推力传感器(6)分别位于安装孔(401)前后两侧,拉力传感器(7)位于安装孔(401)下方;定位传感器(8)内嵌设置在机壳(1)靠近旋转盘(4)的横向一侧,定位传感器(8)位于安装槽(101)上方,感应基准点(9)设置在机壳(1)靠近旋转盘(4)的横向一侧且位于安装槽(101)下方;定位传感器(8)与感应基准点(9)通讯连接,定位传感器(8)与动力机构控制连接。2.根据权利要求1所述的一种推拉力机旋转定位机构,其特征在于,动力机构包括减速器(2)和电动机(13);减速器(2)设置在安装槽(101)内,旋转盘(4)设置在减速器(2)上,减速器(2)贯穿安装孔(401),电动机(13)设置在放置槽(102)内,电动机(13)通过皮带传动机构或链传动机构与减速器(2)传动连接,定位传感器(8)与电动机(13)控制连接。3.根据权利要求2所述的一种推拉力机旋转定位机构,其特征在于,皮带传动机构包括从动带轮(10)、主动带轮(11)和皮带(12);从动带轮(10)设置在放置槽(102)内,从动带轮(10)与减速器(2)传动连接,主动带轮(11)设置在电动机(13)输出端,主动带轮(11)通过皮带(12)与从动带轮(10)传动连接。4.根据权利要求3所述的一种推拉力机旋转定位机构,其特征在于,皮带(12)的截面为圆形或三角形。5.一种根据权利要求1-4任意一项所述的推拉力机旋转定位机构的使用方法,其特征在于,包括以下步骤:s1、将计算机与动力机构进行控制连接,并将计算机与定位传感器(8)通讯连接;s2、通过计算机控制动力机构启动,动力机柜带动旋转盘(4)转动,旋转盘(4)带动其上的推力传感器或拉力传感器转动;s3、定位传感器(8)通过检测感应基准点(9)的位置,将相关电信号传递给计算机,计算机控制动力机构转动一定角度。
技术总结本发明涉及一种推拉力机旋转定位机构,属于推拉力装置技术领域。其主要针对现有装置手动更换传感器模块容易造成损坏的问题,提出如下技术方案:包括机壳、旋转盘、第一推力传感器、第二推力传感器、拉力传感器、定位传感器、感应基准点和用于控制旋转盘转动的动力机构;机壳横向两侧分别设置有安装槽和放置槽,安装槽和放置槽错开;动力机构设置在安装槽和放置槽内;旋转盘设置在设置在动力机构上,旋转盘中心设置有安装孔,动力机构贯穿安装孔;第一推力传感器、第二推力传感器和拉力传感器均内嵌设置在旋转盘远离动力机构的横向一侧。本发明无需更换传感器模块,从而避免其造成损坏。从而避免其造成损坏。从而避免其造成损坏。
技术研发人员:靳海昆
受保护的技术使用者:力标精密设备(深圳)有限公司
技术研发日:2022.10.17
技术公布日:2023/1/2