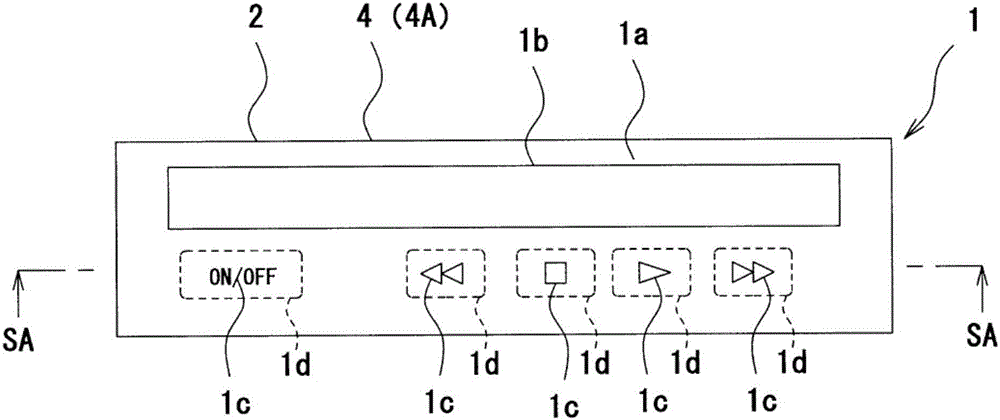
本发明涉及通过触摸操作进行输入的静电电容式的传感片、和在面板基材中具有该传感片的传感面板。
背景技术:
:通过触摸操作进行输入的静电电容式的传感片被用在很多电子设备中,目前对于廉价、可靠性高、高品质的传感片提出了要求。作为传感片的重要构成要素,透明电极一直以来使用的是ITO或导电性高分子,但由于材料本身昂贵、蚀刻加工等工序上的理由,存在着成本非常高的问题。另一方面,已知还有不采用上述昂贵的导电性材料,而是采用便宜的导电性细丝形成传感电极的传感片(日本特开2014-81766号公报)。该导电性细丝的材料本身虽然便宜,但利用感光性材料的方法或蚀刻形成导电性细丝的工序繁杂,成本依然偏高。现有技术文献专利文献专利文献1:日本特开2014-81766号公报技术实现要素:发明要解决的问题除此以外,作为廉价且简便易行的方法,有通过银油墨的印刷来形成导电性细丝的方法。然而,就这种导电性细丝而言,例如,存在着用安装在基板的LED等内部光源对显示部进行照明时,导电性细丝透过并映出在形成显示部的薄的印刷层一侧,或导电性细丝的投影映衬在印刷层的背面,透射到传感面板的外侧的问题。为了解决这些问题,例如,可以采取加大形成显示部的白色等的印刷层的层厚,或尽量加深其颜色,遮蔽后使之无法从表面侧看到的手段。然而,这些会导致显示部的照明亮度降低,可视性下降的问题。针对这些问题,虽可以增加内部光源的输出,但也会引发耗电大幅增加的新问题。本发明是鉴于上述现有技术的问题完成的。本发明的目的是提供一种在照明时的显示部难以看到导电性细丝或其投影,照明时的显示部的可视性良好的传感面板及传感片。解决问题的方法为了实现上述目的,本发明提供以下传感片和传感面板。即,本发明提供一种在具有由内部光源照明的显示部的面板基材的背面侧安装,在面板基材的表面侧进行输入操作的传感片,其特征在于,具有传感电极层和光扩散层,所述传感电极层设置在面板基材的背面侧并具有导电性细丝,所述光扩散层设置在传感电极层与内部光源之间,使内部光源的光扩散后传递到传感电极层。现有技术中,内部光源发出的光被形成有导电性细丝的传感电极层遮蔽一部分后到达显示部的印刷层。即,光自光源起直线前进,导致导电性细丝的投影易于映衬在形成显示部的印刷层的背面。另一方面,本发明中,内部光源发出的光入射到在传感电极层与内部光源之间设置、使内部光源的光扩散后传递到传感电极层的光扩散层,随机改变其前进方向。光的一部分虽然被导电性细丝形成的传感电极层遮蔽,但光的前进方向因光扩散层变得随机,难以生成清晰的投影。由于在照明时的显示部难以看到导电性细丝或其投影,本发明的传感片照明变均匀、外观变漂亮,且由于无需加厚显示部的印刷层来遮蔽导电性细丝或其投影,显示部的照明亮度变高,可视性也得以提高。所述导电性细丝可以用线宽5μm~300μm的导电性涂膜形成。导电性涂膜虽然便宜,但难以形成线宽小的导电性细丝。然而,根据本发明,即使是一定粗度的导电性细丝,导电性细丝的投影也难以映衬在显示部,用导电性涂膜可以廉价地形成导电性细丝。所述光扩散层可以用在内部光源侧具有凹凸面的凹凸层形成。具体地说,可以用在内部光源侧具有由填料和涂膜形成的凹凸面的印刷层形成。并且,可以用在内部光源侧具有由纹理面形成的凹凸面的纹理膜形成。作为光扩散层,可以考虑采用添加了光扩散性的填料的扩散片,但这类扩散片会使透光率下降,照明亮度变弱,可视性反而会降低。但减少填料的添加量时,光变得难以扩散后会反衬至背面。鉴于这一问题,本发明中,用在内部光源侧具有凹凸面的凹凸层形成光扩散层,因而可以切实地使内部光源发出且直线前进的光的前进方向发生散射。并且,采用印刷层的方式时,用具有填料的涂料进行印刷或涂装即可以较为轻松地形成这类凹凸层。进而,用作为凹凸面具有纹理面的纹理膜也可以轻松地形成凹凸层。本发明提供一种传感面板,该传感面板具备面板基材、设置在面板基材并具有由内部光源照明的显示部的装饰层、及在面板基材的背面侧设置的上述任意一种本发明的传感片。根据本发明的传感面板,除了具有由前述的传感片所带来的作用和效果以外,尤其是作为车载用电子部件或家电产品等的在暗处可照明显示的传感面板,可以实现照明时的可视性良好、明亮度和外观优美的照明显示。并且,利用面板基材中的装饰层,还可以使位于背面侧的传感片的导电性细丝本身难以从外面看到。上述本发明中,装饰层和传感片的传感电极层相隔的层间距离T、与导电性细丝的线宽W的关系可以为T≥20W。通过规定上述层间距离T,照明时导电性细丝的投影在不会映衬在显示部,可以均匀地照明显示部。发明的效果根据本发明的传感片及传感面板,显示部的均匀照明使得外观优美,显示部的照明亮度高、可视性也良好,因而可以实现在暗处也易于使用的、各种电子设备的输入操作用的高品质的触摸面板。此外,导电性细丝的传感电极层可以通过印刷来形成,可以使制造成本降低。附图说明图1是一种实施方式的传感面板的外观立体图。图2是图1的传感面板的俯视图。图3是图2的SA-SA线剖面图。图4是图3的SB部放大图。图5是图1的传感片的俯视图。图6是将图5的SC部放大的、第一实施方式的传感电极的线路图案的俯视图。图7是将图5的SC部放大的、第二实施方式的传感电极的线路图案的俯视图。图8是第二实施方式的传感面板的与图4相当的局部放大图。图9是第三实施方式的传感面板的与图4相当的局部放大图。图10是第四实施方式的传感面板的与图4相当的局部放大图。具体实施方式以下,参照附图说明本发明的实施方式。此外,各实施方式中通用的部件赋予相同符号,省略重复说明。并且,通用的材质、作用、效果等也省略重复说明。第一实施方式(图1~图7)作为本实施方式的传感面板1,例如,被用作为车辆音响设备的操作面板。作为车辆音响设备的外装部件的一部分,传感面板1被装入壳体A来使用。因此,照明时显示部的可视性的优良是重要的品质要求。传感面板1的说明:传感面板1呈一面具有开口的盒状,具有面板单元2、和在面板单元2的内部安装的传感片3。传感面板1的显示操作面1a中形成有显示窗1b、表示文字或符号的显示部1c,包围显示部1c的周围部分形成了对触摸操作进行反应的操作区域(感应区域)1d。此外,就图示的传感面板1而言,示出的是操作面1a呈平面状的形式,但也可以形成整体或局部弯曲的曲面状的显示操作面。面板单元2的说明:面板单元2为薄形,层合了外装部4、装饰层5及基材6。并且,传感片3层合了基片7、传感电极8及扩散层9,通过粘合层10被固定在面板单元2的内侧面。该粘合层10为薄膜片状,具有不损害显示部1c的照明显示的可视性的透光性。作为面板单元2的外装部4,其表面为进行触摸操作的操作面。考虑到作为操作面的平滑性,本实施方式的外装部4用热塑性的树脂膜4A形成。这是由于易于通过加热来成形,也易于形成平面状或曲面状的显示操作面1a,形状自由度高的缘故。因此,该树脂膜4采用耐磨损性、耐擦伤性、耐光性、耐候性等优异的材质,进而在与基材6一体成形时,优选采用成形性好的材质。作为这种材质,可以使用丙烯酸树脂膜、PET膜、硬涂型的聚碳酸酯树脂膜等。此外,外装部4无需采用树脂膜4A。例如,可以在基材6的表面形成装饰层5,在该装饰层5上用激光等形成显示部1c,在其上涂装形成硬涂层来作为外装部4。树脂膜4A的背面的装饰层5由透光层5a和遮光层5b形成。在树脂膜4A的背面,在显示部1b以外的部位形成有遮光层5b,而透光层5a在填充构成显示部1b的镂空形状部的同时,层合形成在遮光层5b的背面。具体地说,如图2所示,在显示窗1a和显示部1b以外的树脂膜4A的背面形成遮光层5b,而透光层5a作为传感面板1的外观形成在显示部1b。照明时该透光层5a明亮地照明显示,在其中反衬的传感电极8的线路图案被隐藏得几乎无法可见的技术是本发明的特征。装饰层5为树脂层,在与基材6一体成形时,优选成形性好的材质。在与基材6一体成形时,例如,将形成有装饰层5的树脂膜4A插入到模具后与基材6一体成形。装饰层5可以通过印刷形成在树脂膜4上,对于形成方法没有特别的限定。作为装饰层4的材质,适宜的是丙烯酸类树脂、乙烯类树脂、聚酯类树脂、聚氨酯类树脂、聚碳酸酯类树脂。装饰层5的透光层5a是作为传感面板1的显示部1c受到关注的部分,因此,透光层5a不能具有可以清晰地看到基底程度的透明性。这是由于在传感面板1的显示部1c易于看到传感电极8的导电性细丝8a,外观变差的缘故。传感电极8的线路图案不需要装饰。作为装饰层5不透明的例子,可以是透光性白色层、提高了雾度的铺垫层、提高了光扩散性的凹凸层、各种着色了的着色透光层。通过至少在透光层5a设置作为非透明层的装饰层5,可以使显示部1c显露的位于透光层5a深处的线路图案难以被看到。基材6是构成面板单元2的成形体主体,采用透明的热塑性树脂。作为热塑性树脂,例如,可以列举聚碳酸酯(PC)树脂、聚甲基丙烯酸甲酯(PMMA)树脂、丙烯腈-苯乙烯(AS)树脂、丙烯腈-丁二烯-苯乙烯(ABS)树脂、它们的树脂合金等。此外,构成基材6的热塑性树脂无需透明。例如,不需要显示窗1b时,可以用不是无色透明的透光性树脂来替代透光层4a,并兼顾作为显示部1c的照明功能和传感电极8的线路图案的遮蔽功能。传感片3的说明:传感片3层合了基片7、传感电极8及扩散层9,基片7用粘合层10固定在面板单元2的内侧面。基片7呈平坦的片状。作为其材质,例如,可以采用聚对苯二甲酸乙二醇酯(PET)树脂、聚萘二甲酸乙二醇酯(PEN)树脂、聚碳酸酯(PC)树脂、聚甲基丙烯酸甲酯(PMMA)树脂、聚丙烯(PP)树脂、聚氨酯(PU)树脂、聚酰胺(PA)树脂、聚醚砜(PES)树脂、聚醚醚酮(PEEK)树脂、三乙酰纤维素(TAC)树脂、环烯烃聚合物(COP)等。在将这些用作为材质的基片7上,可以设置用来提高与导电性高分子的密合性的底漆层、或以抗静电等为目的的覆盖层等来进行表面处理。基片7可以采用将这些用作为素材的无色透明的树脂膜。“透明”是出于以下理由,如将传感面板1也用作为显示器时,可以经由“透明”的基片7从传感面板1的外侧看到在传感片3的背面设置的显示器的显示。因此,这里提到的“透明”是指,从传感片3的表面侧可以看到传感片3背面的显示内容程度的透明性。另一方面,无需从外部看到基片7背面的显示内容时,作为基片7,可以采用将透光性的上述材质用作为素材的树脂膜。传感电极8由导电性细丝8a形成,具有图5所示的操作区域(感应区域)1d的外形。就由导电性细丝8a形成的传感电极8的线路图案而言,主要根据“自电容方式”的情形、和“互电容方式”的情形采用不同的设计。自电容方式的情形(图6):采用自电容方式时,如图6所示,导电性细丝8a可以形成网状的线路模式,从而使操作区域1d整体成为单一的导电性区域。网状的导电性细丝8a的线宽优选为5μm~300μm。形成低于5μm的导电性细丝8a时,需要蚀刻加工或激光加工,会产生高成本的问题。线宽低于5μm的导电性细丝8a其本身难以被识别,因而无需后述的光扩散层9。另一方面,线宽超过300μm时,装饰层5与光扩散层9的距离、或装饰层5与传感电极8的距离将超过6mm,传感面板1或传感片3的厚度过度增大,因而不优选。关于网状的线路图案,导电性细丝8a彼此的间距优选为50μm~10mm。间距超过10mm时,导电性细丝8a彼此的间隙变得过大,存在着用指尖触摸操作区域1d时不与导电性细丝8a重合,感应灵敏度降低的问题。另一方面,低于50μm时,间距相对于配线宽变得过小,存在着传感电极8中的导电体(导电性细丝8a)的占有面积增大,基板中安装的LED等内部光源L发出的光的透光率变低,显示部1c的照明亮度大幅降低的问题。基于这些观点,更优选的范围为400μm~1500μm。就这种传感电极8中的导电体(导电性细丝8a)的占有面积而言,按以下定义的“开口率”计优选为80%~98%的范围。开口率=开口部的面积/感应区域的面积该开口率低于80%时,存在着透光率降低,显示部1c的照明亮度降低的问题。另一方面,开口率超过98%时,存在着操作区域1d中导电体(导电性细丝8a)所占的面积小,静电电容的变化小,感应灵敏度降低的问题。这种导电性细丝8a可以用导电性涂膜或金属层形成,其中,优选采用导电性涂膜来形成。具体地说,出于形成线路图案时的容易性及成本的观点,优选采用将银粉末分散在液状树脂中的、所谓的银浆等导电性油墨。互电容方式的情形(图7):作为第二种方式,触摸传感器采用互电容方式时,如图7所示,可以用导电性细丝8a形成一对梳形电极,在操作区域(感应区域)1d组合梳形电极彼此。与自电容方式的不同点在于电极的形状,而导电性细丝8a的线宽、间距、开口率、材质等可以为同等的构成。基片7的下面设置有光扩散层9。光扩散层9也设置在传感面板中与显示部1c对应的位置。通过设置光扩散层9可以实现均匀的照明,同时如后所述,可以使导电性细丝8a难以被看到。并且,作为光扩散层9的外形,本实施方式中示出了覆盖传感电极8的形状的例子,但只要覆盖显示部1c,则可以是任意的大小。光扩散层9透光率高且表面具有凹凸,因而如图4所示,具有折射、反射光的性质。光扩散层9的透光率优选为0.5%以上。透光率低于0.5%时,存在着照明亮度过低的问题。所述透光率更优选为2%以上,由此可以实现充分且明亮的照明。透光率的上限没有特别的限定,但超过10%时存在着光扩散性不充分,无法均匀照明的问题。并且,光扩散层9特别优选为无色,但也可以是无色以外的颜色。此外,本发明中的透光率是用分光光度计测定的、波长550nm的光的平行线透过率。对于总透光率,优选为50%以上。就光扩散层9的表面凹凸而言,JISB0601规定的算术平均粗糙度Ra的值优选为0.3μm以上。这是由于,Ra低于0.3μm时光扩散性低,照明不均匀的缘故。Ra值的上限没有特别的限定,但优选精细到每个凹凸的反射面都无法被识别的程度,出于这个观点,Ra的值优选为50μm以下。光扩散层9的材质没有特别的限定,通过涂布或印刷形成时,优选采用含有透明、粒径为1~100μm大小且具有光扩散性的填料9a的油墨(参照图4)。通过印刷,用填料9a可以形成具有指定凹凸的光扩散层9。光扩散层9除了通过涂布或印刷形成的方法以外,还可以利用实施压花加工等的方法形成,对于此没有特别的限定。出于生产性、材料调整的容易性的观点,优选用丝网印刷形成。对于如上所述的具有面板单元2和传感片3的传感面板1,为了提高传感片3的光扩散效果,进一步确保导电性细丝8a或导电性细丝8a的投影不反衬至装饰层5的透光层5a,可以采取以下措施。即,透光层5a(装饰层5)与传感电极8的层间距离T、和导电性细丝8a的线宽W的关系满足“T≥20W”。例如,导电性细丝8a的线宽为100μm时,层间距离T需在2000μm以上。更具体地说,本实施方式中,基材6、粘合层10和基片7的总厚度相当于层间距离T。构成该层间的部件在后述的图9及图10中虽为不同的部件,但其构成都要满足层间距离T。本实施方式中,对于构成层间的部件的厚度,各部件的厚度没有特的殊限定,但通常基片7采用厚度为10~200μm、粘合层10采用厚度为10~100μm的部件,因而需调整基材6的厚度,从而使总厚达到层间距离T。并且,相对于层间距离,基片7的厚度或粘合层10的厚度薄,因而基材6的厚度设在T以上时实质上也没有太多影响。通过具有这种层间距离T,可以提高光扩散效果,在显示部1c也难以看到导电性细丝8a或导电性细丝8a的投影。关于难以看到导电性细丝8a的原理,有如下看法。透光层5a采用透光性白色层、提高了雾度的铺垫层、提高了扩散性的凹凸层、或各种着色了的着色透光层等时,可以隐藏导电性细丝8a,使其难以被直接看到。然而,只设置这种装饰层时,存在着用内部光源L的背光进行照明时在显示部1c可以清晰地看到导电性细丝8a的投影的问题。追究其原因时,可以认为是由于自内部光源L起至透光层4a的光线直线传播的缘故,由此产生了配置光扩散层9使光线的导光路径随机扩散的方案。经过各种探讨,发现该投影的易见程度与导电性细丝8a的线宽W、透光层4a与导电性细丝8a的距离T相关。进而还发现所述T为指定的距离时,可以使导电性细丝8a的投影难以被看到,且相对于线宽设置20倍的距离时,装饰层5几乎不会产生导电性细丝8a的投影,可以实现均匀的照明。传感面板1的作用、效果:观察内部光源L不照明的非照明时的传感面板1外观时,形成显示部1c的透光层5a不具有可以清晰地识别底层的程度的透明性。因此,不会看到在透光层5a的深处形成的传感电极8的导电性细丝8a的线路图案。进而,照明时透光层5a虽然被照亮,但从其外观观察时,传感电极8的线路图案对透光层5a及遮光层5b的反衬被遮挡后几乎无法看到。即,自内部光源L直线前进的光首先到达并进入光扩散层9后,如上所述,由于具有光扩散性的填料和因该填料变为凹凸面的表面的光扩散层9,光的前进方向随机扩散。虽然一部分光被导电性细丝8a遮挡后产生投影,但光扩散层9使光的前进方向随机扩散,因而难以生成清晰的投影。在传感电极8的导电性细丝8a之间穿过,前进方向随机扩散的光均透过透光性的基片7、粘合层10及基材6后到达装饰层5。此时,本实施方式中,前述的层间距离T与导电性细丝8a的线宽W的关系满足“T≥20W”,因而在显示部1c更难看到导电性细丝8a或其投影。再者,光经由装饰层5的透光层5a并通过树脂膜4A后,向外部放出。由此,显示部1c被照亮后产生显示。进而,装饰层5不反衬线路图案的投影,因而无需涂厚装饰层5来遮蔽投影,利用薄的装饰层5即可以提高显示部1c的照明亮度,还可以提高可视性。因此,尤其是作为适用在车载用电子部件或家电产品的传感面板1,可以实现兼顾优异的可视性、明亮度和外观优美的照明显示。第二实施方式(图8)本实施方式的传感面板21部分改良了第一实施方式的传感面板1的传感片3。第一实施方式是在传感电极8上直接层合了光扩散层9,但在传感片22中,传感电极8上形成了由抗蚀层构成的保护层23,在该保护层23上形成光扩散层9。构成保护层23的树脂可以是硬质的树脂,例如,可以使用丙烯酸类、聚氨酯类、环氧类、聚烯烃类树脂或其他树脂。根据该传感面板21、传感片22,利用保护层23可以保护传感电极8的导电性细丝8a,可以进一步提高传感面板21、传感片23的运转可靠性。第三实施方式(图9)本实施方式的传感面板31与第一实施方式的传感面板1的不同点在于传感片32的构成。就第一实施方式的传感片3而言,在基片7的一面层合了传感电极8和光扩散层9,基片7的另一面固定在面板单元2上。但在传感片32的构成中,将一面经凹凸加工的纹理膜用作为基片33,另一面层合了传感电极8和保护该传感电极8的抗蚀层即保护层34,并利用粘合层10将该保护层34固定在面板单元2上。即,基片33既是传感片32的基片,也是光扩散层,兼具两个功能。根据该传感面板31,基片33兼具有光扩散层的功能,因而无需另行形成光扩散层。因此,通过减少制造工序可以降低成本。第四实施方式第一实施方式中,作为光扩散层9,通过涂装或印刷透明性高且光扩散性的填料形成了凹凸层,但也可以形成含有氧化钛等光扩散剂的白色层。光扩散层9为白色层时,透光率低于0.5%、亮度降低,但可以提高光扩散性。此时,可以将第一实施方式中规定的透光层4b(装饰层4)与传感电极8的层间距离T、和导电性细丝8a的线宽W的关系“T≥20W”调整为更短的间隔。更具体地说,调整为“T≥10W”。因此,根据本实施方式的传感面板1及传感片3,减小了层间距离T,可以实现更为薄型的传感面板1和传感片3。第五实施方式(图10)本实施方式的传感面板51与第一实施方式的传感面板1在以下几点有所不同。即,作为构成传感面板51的部件,第一实施方式的传感面板1是将传感片3固定在面板单元2的构成,但在传感面板51中,面板单元和传感面板为一体,在传感面板51上设置有传感电极8等。即,基材6的表面层合了由透光层5a及遮光层5b构成的装饰层5、和树脂膜4A,基材6的背面层合了传感电极8和光扩散层9。本实施方式中,该传感电极8和光扩散层9构成了传感片52。因此,传感面板51中并不存在第一实施方式的基片7及粘合层10。并且,就传感面板51而言,基材6的厚度为第一实施方式的层间距离T,与导电性细丝8a的线宽W的关系满足“T≥20W”。因此,根据本实施方式的传感面板51,无需设置基片7及粘合层10,可以减少照明时的光透过的部件数,使显示部1c变得更为明亮。并且,通过部件数的减少可以削减制造成本。在不出现不良问题的前提下,可以组合本发明的各实施方式及变形例中提到的特征构成。并且,上述实施方式是本发明的示例,本发明并不受这些方式的限定,在不脱离本发明构思的前提下,各部件的形状、材质、制造方法等的改良也包括在本发明的范围内。例如,在上述实施方式中示出了将装饰层5设置在基材6的表面侧的例子,但也可以设置在基材6的背面。此时的层间距离T为位于基材6的背面侧的装饰层5、与直接或间接层合在其下方的传感电极8的距离。实施例实施例1本实施例中,制作了在第一实施方式所示的传感面板1构成中导电性细丝8a的线宽W、与装饰层5和传感电极8的层间距离T取各种数值的试样后,评价了导电性细丝8a和其投影的可视难易度。试样1:在由350μm的聚碳酸酯树脂板构成的基材(6)的一面,用白色的聚酯类油墨形成装饰层(5)(透光层(5a))后制作了与面板单元(2)相当的装饰片。其次,用与所述基材(6)不同的厚度为100μm的聚对苯二甲酸乙二醇酯膜作为基片(7),在其一面用银油墨形成了网状的传感电极层(8)。构成该网状图案的导电性细丝(8a)的线宽为80μm。随后,将含有粒径为2μm且透明的有机硅的聚酯类油墨用作为形成凹凸的填料(9a),通过印刷形成光扩散层(9)并覆盖导电性细丝(8a)后制作了传感片(3)。最后,用厚度50μm的双面胶(10)固定装饰片(2)的另一面与传感片(3)的另一面,从而制作了试样1。该试样1中,装饰层(5)与传感电极层(8)的层间距离T为500μm。对于上述光扩散层(9),只将光扩散层(9)印刷在无色透明的膜上所测得的透光率为3.4%。并且,该光扩散层(9)的表面凹凸的算术平均粗糙度Ra为0.63μm。此外,用紫外可见分光光度计(岛津制作所制“UV-1600”)测定了透光率。并且,用激光显微镜(Keyence公司制“UK-8510”)测定了算术平均粗糙度Ra。试样2~试样16:采用与试样1相同的方法,改变了基材(6)的厚度,如表1所示,将装饰层(5)与传感电极层(8)的层间距离T调整为0.5mm、1mm、2mm、3mm的同时,将导电性细丝(8a)的线宽W调整为80μm、50μm、25μm、10μm,组合以上各条件来制作了试样。扩散性的评价:在作为光源的俯视型白色LED上配置各试样1~16,通过肉眼观察分别评价了导电性细丝8a或导电性细丝8a的投影的可视难易度。就实验结果而言,在所有试样中均没有看到导电性细丝8a。另一方面,其投影的可视程度上存在着差异,依据1)看到了投影的为“×”、2)隐约有投影、可视度低的试样为“Δ”、3)几乎看不到投影的为“○”的标准做了3个级别的评价。表1光扩散性的评价结果揭示了层间距离T与线宽W的关系。即,就某一线宽的试样而言,层间距离T在一定程度以上时难以看到导电性细丝(8a)的投影。表1中,计算评价结果为“Δ”的试样的“T/W值”时,试样3为25,试样6为20,试样9为25。另一方面,评价为“×”的试样中,试样1为6.25,试样2为12.5,试样5为10。由此可见,12.5以下时易于看到导电性细丝(8a)的投影,20以上时难以看到导电性细丝(8a)的投影。并且,37.5以上时看不到导电性细丝(8a)的投影,可以实现特别均匀的照明。实施例2针对实施例1的光扩散层(9),用含有氧化钛的白色聚酯类油墨作为光扩散剂后,与实施例1相同地进行了评价。对于该光扩散层(以下,亦称之为“白色层”),只将该光扩散层印刷在无色透明膜上时测得的透光率为0.23%,低于实施例1的光扩散层(9)的透光率3.4%。并且,该光扩散层(9)的表面平坦且有光泽,但算术平均粗糙度Ra为0.21μm。表2实施例2的光扩散性的评价结果揭示了将光扩散层(9)改为白色层时的、层间距离T与线宽W的关系。表2中,计算评价结果为“Δ”的试样的“T/W值”时,试样21为10。另一方面,评价为“×”的试样中,试样1为6.25。由此可见,6.25以下时易于看到导电性细丝(8a)的投影,10以上时难以看到导电性细丝(8a)的投影。并且,12.5以上时看不到导电性细丝(8a)的投影,照明特别均匀。并且,实施例2的光扩散层(9)与实施例1的光扩散层相比,透光率低、照明亮度低。但在实施例1中评价为“×”的试样2在实施例2的试样18中评价变为“○”,同样在实施例1中为“×”的试样5在实施例2的试样21中变为“Δ”,实施例1中为“Δ”的试样3、6、9在实施例2的试样19、22、25中分别变为“○”,得到了改善。即,在透光率低的实施例2中,减小层间距离T时也得到了难以看到投影,可以得到层间距离T减小的传感面板(1)。实施例3测定了实施例1的光扩散层(9)单层和试样8、实施例2的光扩散层(9)单层和试样24的照明亮度。作为测定方法,将各试样配置在1236cd/m2的透光桌上,用亮度计(柯尼卡美能达公司制“LS-100”)测定了照明亮度。表3试样亮度(cd/m2)实施例1的光扩散层单层1300试样8502实施例2的光扩散层单层540试样24377表3示出了实施例1的光扩散层(9)的透光率高,单层时比透光桌的亮度还明亮的结果。可以认为,这是由于与透光桌的扩散板结合后进一步提高了扩散效果,表观亮度提高了的缘故(透光桌也由荧光灯和扩散板构成)。相对于此,就实施例2的光扩散层(9)即白色层而言,亮度减半至540cd/m2。对比试样8和试样24时,也显示了采用实施例1的光扩散层(9)时可以得到更高亮度照明的结果。当前第1页1 2 3