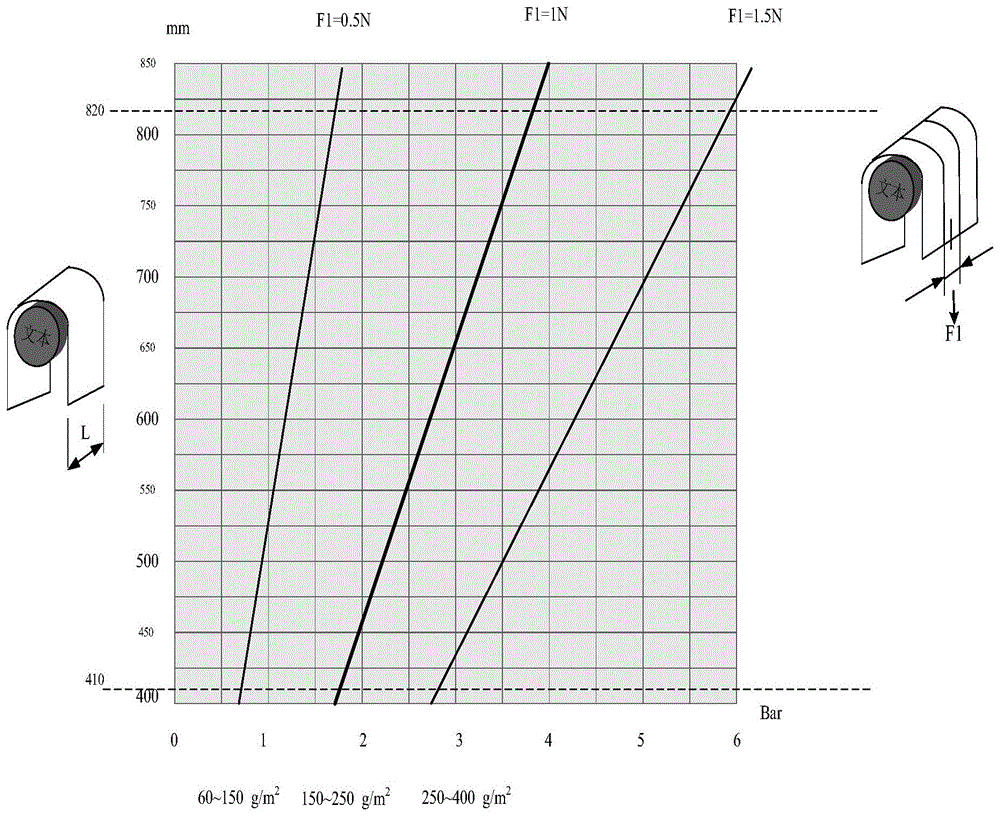
本发明涉及纸制品印刷
技术领域:
,特别涉及一种纸制品圆压圆印刷装置的设计方法,该设计方法可以减少因套印不准的废品产生,提高纸制品的合格率。
背景技术:
:为了解决平张纸在多工序加工过程中易受环境温湿度影响导致纸张伸缩变形产生较多套准偏差废品,平压平全息烫印易产生气泡等问题,经过科学分析与论证,提出对一种卷筒纸制品圆压圆加工方式,即:无版缝卷筒纸印刷→离线卷筒纸圆压圆全息烫印→模切(卷筒纸圆压圆压凸、压痕、模切三工位一体连动),采用此工艺可以节约平张纸加工所必需的咬口、拖梢等辅助用纸、节约资源,并可增加每吨纸的产出率,提高生产效率。同时在模切时压凸,有效规避了卷到卷凹印,即联机压凸中压凸效果衰减的问题,圆压圆全息烫印杜绝了原印刷过程中全息图起雾、起泡的现象,且圆压圆模切精度高,提升了纸制品品质。但是上述工艺中往往会出现离线设备间及同台设备内的不同工序因纸张在不同设备、张力下的伸缩变形导致的各工序套印偏差,使生产出的产品外观难以满足质量要求的问题。技术实现要素:有鉴于此,本发明的目的是克服现有技术的上述不足而提供一种纸制品圆压圆印刷装置的设计方法,该设计方法通过摸索与选取全线工艺参数,主要是设备张力设置值即要保证单工序运行正常(如印刷套准)、又要综合考虑贯穿全线的加工情况(如在张力情况下纸张的伸缩变形量),各色印刷版周长的基数递增量、压凸版、压痕版、模切版的理论基数与实际增减量,通过该方法彻底克服了以上工艺实施方案中的设备精度与纸张伸缩变形导致的各工序套印偏差,使生产出的产品外观满足质量要求。基于上述目的,本发明提供了一种纸制品圆压圆印刷装置的设计方法,所述纸制品圆压圆印刷装置包括卷筒纸凹印机、卷筒纸定位全息烫印机和卷筒纸压凸、压痕、模切三工位连动自定位接纸换卷模切机,具体包括以下步骤:(1)根据承印纸张的单片长度确定卷筒纸凹印机的周向排版个数,由承印纸张的单片长度与卷筒纸凹印机的周向排版个数的乘积得到第一理论周长,然后根据第一理论周长确定卷筒纸凹印机的印版周长范围;(2)由承印纸张的单片长度与卷筒纸定位全息烫印机的周向排版个数的乘积得到第二理论周长,然后根据第二理论周长,建立卷筒纸定位全息烫印机蜂窝辊高点周长的第一函数,根据第一函数确定装上烫金版后的蜂窝辊高点周长,其中,第一函数为:装上烫金版后的蜂窝辊高点周长=第二理论周长×(1+修正系数a);(3)由承印纸张的单片长度与卷筒纸压凸、压痕、模切三工位连动自定位接纸换卷模切机的周向排版个数的乘积得到第三理论周长,卷筒纸压凸、压痕、模切三工位连动自定位接纸换卷模切机的周向排版个数为卷筒纸凹印机的周向排版个数的1.3-1.7倍;根据第三理论周长,分别建立卷筒纸压凸、压痕、模切三工位连动自定位接纸换卷模切机的压凸版辊高点周长的第二函数,压痕版辊高点周长的第三函数和模切版辊高点周长的第四函数,根据第二函数、第三函数和第四函数分别确定压凸版辊高点周长、压痕版辊高点周长和模切版辊高点周长;其中,第二函数为:压凸版辊高点周长=第三理论周长×(1+修正系数b),第三函数为:压痕版辊高点周长=第三理论周长×(1+修正系数c),第四函数为:模切版辊高点周长=第三理论周长×(1+修正系数d)。本发明纸制品圆压圆印刷装置的设计方法中的参数包括:⑴凹印制版时各色印版理论需求直径、张力设置与修正系数,⑵烫金工序印刷工序版辊数值的修正系数,⑶圆压圆模切后加工工序各工位之间修正系数,⑷各工序离线状态下的周向拼版个数选择标准。在本发明中,模切周向排版个数选择范围在凹印排版个数的1.3-1.7倍数之间,以保证印刷后的半成品纸张处于可控的定长拉伸范围。在本发明的一个实施例中,所述修正系数a为+3‰,修正系数b为+0.3‰,修正系数c为+0.5‰,修正系数d为+4‰。在制作版辊时需考虑前工序纸张加工对纸张伸缩变形量的影响,确定各工序中辊周长,防止套印不准。在本发明中,各色组凹印版辊的圆周长应以第一色组等于第一理论值为基准,逐次递增。其中蜂窝辊、压凸版辊、压痕版辊和模切版辊在作业前应进行预热处理,预热温度宜控制在40±2℃。卷筒纸印刷的优势可以采用无缝拼版的方式来节约纸张,但必须配合卷筒纸烫印与圆压圆模切才能更好地发挥出该优势。然而,由于卷筒纸生产设计的设备较多,在工艺流程设计时必须考虑全面,对每台设备的特殊要求都要全面关注。特别是凹印张力气压控制尤其重要,需要确定每台设备的张力气压控制数值,否则带来的套印、模切不准问题会相当严重。在本发明的一个实施例中,卷筒纸凹印机的张力气压设置方法如下:根据承印纸张的幅宽l,建立卷筒纸凹印机的张力气压p的第五函数,根据第五函数设置卷筒纸凹印机的张力气压p。在本发明的一个实施例中,所述第五函数根据承印纸张克重和1mm幅宽范围承印纸张所受到的拉力f1的不同而不同,具体为:当f1=0.5n,承印纸张克重为60~150g/m2时,第五函数为:l=376.5×p+161.15;当f1=1n,承印纸张克重为150~250g/m2时,第五函数为:l=195×p+70;当f1=1.5n,承印纸张克重为250~400g/m2时,第五函数为:l=130×p+45。卷筒纸凹印机是以卷料形式供应承印材料的印刷机。为了实现卷筒纸印刷工作,纸带在进入印刷装置之前必须保持平整、绷紧程度适中,就是保持一定的走纸张力气压。纸卷在输送纸带的过程中,使纸带处于拉紧状态的力称为张力气压。在印刷过程中假如纸带处于无约束状态自由展开,则纸带就不能完成印刷工作。纸带张力气压的大小直接关系到卷筒纸印刷机图像转移的状态。在印刷过程中纸带的张力气压需要恒定不变和大小适当。当纸带张力气压过大时,印刷网点会产生一定的变形,纸带在纵向会打皱、甚至发生横向断裂;当纸带张力气压过小时,会造成印迹模糊、套印不准、横向皱褶。因此卷筒纸印刷机在印刷过程中,纸带必须具有一定的张力气压,以便控制纸带的运动。不同材质、规格的承印纸张需要设定不同的张力气压,更换品种时要及时调整各部分的张力气压,以防止张力气压太小时易导致横向套印不准和张力气压过大时则易引起成品尺寸缩短等问题。在实际操作过程中,操作人员往往根据自己的经验进行多次操作才能确定一个大概的范围。而本发明提供了一种卷筒纸凹印机的张力气压的设置方法,该设置方法根据承印纸张的幅宽,建立了卷筒纸凹印机的张力气压的第五函数(一次函数),并且该一次函数根据承印纸张克重和1mm幅宽范围承印纸张所受到的拉力f1的不同而不同,但操作人员需要设置卷筒纸凹印机的张力气压值时,只需要根据承印纸张克重和1mm幅宽范围承印纸张所受到的拉力f1确定第五函数,然后测定承印纸张的幅宽,根据第五函数得到张力气压值。在本发明的一个实施例中,卷筒纸凹印机的每色组印版直径递增量设置方法如下:测量得到承印纸张所受到的拉力,然后计算得到1mm幅宽范围承印纸张所受到的拉力f1,从而建立1mm幅宽范围承印纸张所受到的拉力f1与卷筒纸凹印机的每色组印版直径递增量的对应函数,根据对应函数设置卷筒纸凹印机的每色组印版直径递增量。在本发明的一个实施例中,所述对应函数根据1mm幅宽范围承印纸张所受到的拉力f1的不同而不同,具体为:当f1=0.5n时,每色组印版直径递增量为0.01mm;当f1=1n时,每色组印版直径递增量为0.02mm;当f1=1.5n时,每色组印版直径递增量为0.03mm。在凹印过程中为了弥补套印误差,制版时各色组的印版滚筒(即版辊)直径必须按色序以一定的系数逐色递增。利用版辊直径的递增来弥补套印误差,卷筒纸凹印机版辊的尺寸以第一色为基础逐渐递增。承印纸张的特性不同,所施加压力的宽度不同,每色组印版直径递增量应该是不同的。本发明提供了1mm幅宽范围承印纸张所受到的拉力f1与每色组印版直径递增量的对应函数,只需要测得1mm幅宽范围承印纸张所受到的拉力f1值,根据对应函数就可设置每色组印版直径递增量。与现有技术相比,本发明具有以下有益效果:1、本发明提供的圆压圆印刷装置的设计方法,实现了全线工艺参数的设计,解决了卷到卷生产工艺流程中各不同工序离线设备之间、及同台设备内不同工序间的产品套准问题,将套准偏差小于0.15mm的产品比例提升到98%以上(正态分布),使生产出的产品外观满足质量要求。2、本发明提供的圆压圆印刷装置的设计方法,省去了摸索和尝试步骤,节省了大量的时间,提高了生产效率。附图说明附图是结合具体的工艺实施方式,详细的说明了工艺走向。图1为本发明卷筒纸凹印机的张力气压与承印纸张的幅宽的函数图,其中,f1为1mm幅宽范围纸张所受到的拉力,单位n;三条线段与三个不同范围克重的纸张对应;纵轴l为幅宽,横轴bar为设备所需设置张力气压值。具体实施方式为使本发明的目的、技术方案和优点更加清楚明白,以下结合具体实施例,并参照附图,对本发明进一步详细说明。实施例1一种纸制品圆压圆印刷装置的设计方法,纸制品圆压圆印刷装置包括卷筒纸凹印机、卷筒纸定位全息烫印机和卷筒纸压凸、压痕、模切三工位连动自定位接纸换卷模切机,具体包括以下步骤:(1)根据承印纸张的单片长度确定卷筒纸凹印机的周向排版个数,其中,第一理论周长=单片长度×卷筒纸凹印机的周向排版个数,然后根据理论周长确定卷筒纸凹印机的印版周长范围;卷筒纸凹印机的张力气压设置方法如下:根据承印纸张的幅宽l,建立卷筒纸凹印机的张力气压p的第五函数,根据第五函数设置卷筒纸凹印机的张力气压p;卷筒纸凹印机的每色组印版直径递增量设置方法如下:测量得到承印纸张所受到的拉力,然后计算得到1mm幅宽范围承印纸张所受到的拉力f1,从而建立1mm幅宽范围承印纸张所受到的拉力f1与卷筒纸凹印机的每色组印版直径递增量的对应函数,根据对应函数设置卷筒纸凹印机的每色组印版直径递增量。印刷工序的张力设置与制版修正递增参数设置如下:步骤一:设计出一套图表,如图1所示,根据承印纸张克重类型---确定选择三条线中的某一条,在纵坐标中找到宽幅l的对应值,结合对应线条,在图表中可找到设备所需设置张力气压p(单位为bar);f1为1mm幅宽范围纸张所受到的拉力,单位n(用拉力测量传感器测量某一种克重的纸张,要保持单位宽度内受到的拉力(n)恒定---伸缩一致)。具体为:当f1=0.5n,承印纸张克重为60~150g/m2时,第五函数为:l=376.5×p+161.15;当f1=1n,承印纸张克重为150~250g/m2时,第五函数为:l=195×p+70;当f1=1.5n,承印纸张克重为250~400g/m2时,第五函数为:l=130×p+45。以f1对应纸张类型0.5n,承印纸张克重为60~150g/m2为例说明,当纸张宽度(幅宽,l)为500mm时张力气压p需要为0.9bar,当纸张宽度为820mm时张力气压p需要为1.75bar,否则f值发生变化导致纸张伸缩率变化,印刷每色组印版直径递增量无效。以f1对应纸张类型1n,承印纸张克重为150~250g/m2为例说明,当纸张宽度为460mm时张力气压p需要为2.0bar,当纸张宽度为850mm时张力气压p需要为4.0bar,否则f值发生变化导致纸张伸缩率变化,印刷每色组印版直径递增量无效。以f1对应纸张类型1.5n,承印纸张克重为250~400g/m2为例说明,当纸张宽度为825mm时张力气压p需要为6.0bar,当纸张宽度为500mm时张力气压p需要为3.5bar,否则f值发生变化导致纸张伸缩率变化,印刷每色组印版直径递增量无效。步骤二:根据上图中的确定的每mm所受的拉力,从下表1中可找到凹印版制作时每个单元的直径递增值(以第一单元为基准递增)。表1每mm宽度承受的拉力f1=0.5f1=1f1=1.5每色组印版直径递增量0.01mm0.02mm0.03mm(2)根据第二理论周长,建立卷筒纸定位全息烫印机蜂窝辊高点周长的第一函数,第二理论周长=单片长度×卷筒纸烫金机的周向排版个数;根据第一函数确定装上烫金版后的蜂窝辊高点周长,其中,第一函数为:装上烫金版后的蜂窝辊高点周长=第二理论周长×(1+3‰),即以此为标准制作装上烫金版后的蜂窝辊,蜂窝辊表面均匀分布着蜂巢洞,烫金版安装于蜂窝辊的表面,烫金版的内表面与蜂窝辊的表面相吻合,并具有一定的弧度,烫金版的外表面刻有所要烫印的图案。(3)卷筒纸压凸、压痕、模切三工位连动自定位接纸换卷模切机的周向排版个数为卷筒纸凹印机的周向排版个数的1.3-1.7倍,第三理论周长=单片长度×卷筒纸压凸、压痕、模切三工位连动自定位接纸换卷模切机的周向排版个数;根据第三理论周长,分别建立卷筒纸压凸、压痕、模切三工位连动自定位接纸换卷模切机的压凸版辊高点周长的第二函数,压痕版辊高点周长的第三函数和模切版辊高点周长的第四函数,根据第二函数、第三函数和第四函数分别确定压凸版辊高点周长、压痕版辊高点周长和模切版辊高点周长,即以此为标准制作压凸版辊、压痕版辊和模切版辊,压凸版辊高点周长为装上压凸版后的辊周长、压痕版辊高点周长为装上压痕版后的辊周长,模切版辊高点周长为装上刀锋后的辊周长;其中,第二函数为:压凸版辊高点周长=第三理论周长×(1+0.3‰),第三函数为:压痕版辊高点周长=第三理论周长×(1+0.5‰),第四函数为:模切版辊高点周长=第三理论周长×(1+4‰);具体如表2所示。表2后加工工序制版修正系数工序模切工序压痕工序压凸工序烫金工序修正系数+4‰+0.5‰+0.3‰+3‰注:以上工序版材使用前,需提前预热升温至40±2℃。实施例2购制一台卷筒纸凹印机、一台卷筒纸定位全息烫印机、一台卷筒纸压凸、压痕、模切三工位连动自定位接纸换卷模切机;通过工序的集约,形成全新的圆压圆生产技术。设计全线工艺参数的设置及对设备制作的要求。根据某产品工艺标准与尺寸要求(以周向方向为98mm为例),确定如下工艺标准,从而确定设备规格配置:①凹印工序:考虑凹印的操作适宜性,选择6联×98=588mm(对应第一理论周长),根据此要求,确定设备规格(印版周长范围400--700mm);②烫印工序:根据凹版印刷工艺参数设定,同步选择6联×98=588mm(对应第二理论周长);确定烫金设备将烫金版的蜂窝辊周长约500mm,根据以上公式计算出装上烫金版后的蜂窝辊高点周长为589.76mm,计算过程为:588mm×(1+3‰)=589.76mm;③模切工序:考虑线接触弧形模切圆刀的使用性能,大弧度能提高圆刀的使用寿命,但太大对版材制作的要求相对较高,压凸、压痕、模切版确定为10×98=980mm(对应第三理论周长)联拼的方式,以此为基础订制相应规格模切设备与机架;根据以上公式计算出压凸版辊高点(凸出点)周长为980.29mm、压痕版辊高点(凸出点)周长为980.49mm,模切版辊高点(刀锋)周长为983.92mm,计算过程为:980mm×(1+0.3‰)=980.29mm,980mm×(1+0.5‰)=980.49mm,980mm×(1+4‰)=983.92mm。综上所述,本发明提供的圆压圆印刷装置的设计方法,实现了全线工艺参数的设计,解决了卷到卷生产工艺流程中各不同工序离线设备之间、及同台设备内不同工序间的产品套准问题,将套准偏差小于0.15mm的产品比例提升到98%以上(正态分布),使生产出的产品外观满足质量要求。本发明提供的圆压圆印刷装置的设计方法,省去了摸索和尝试步骤,节省了大量的时间与实验材料,提高了生产效率。所属领域的普通技术人员应当理解:以上任何实施例的讨论仅为示例性的,并非旨在暗示本公开的范围(包括权利要求)被限于这些例子;在本发明的思路下,以上实施例或者不同实施例中的技术特征之间也可以进行组合,并存在如上所述的本发明的不同方面的许多其它变化,为了简明它们没有在细节中提供。因此,凡在本发明的精神和原则之内,所做的任何省略、修改、等同替换、改进等,均应包含在本发明的保护范围之内。当前第1页1 2 3