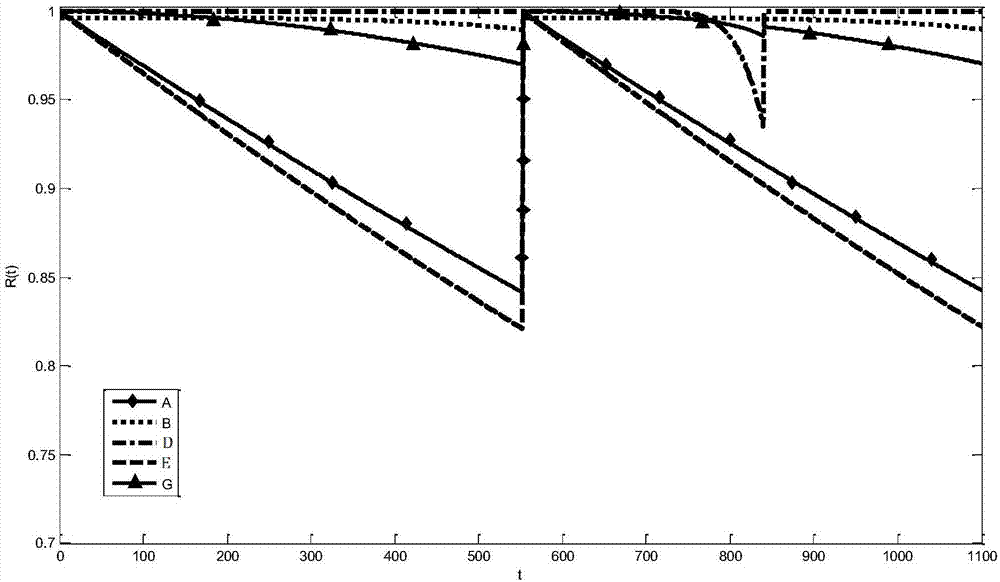
本发明是一种针对结构复杂的多层级系统的退化数据,基于寿命预测模型、维修分组和多目标规划的成组维修决策方法,属于维修决策
技术领域:
。
背景技术:
为了保证系统在规定时间内完成一系列任务,需要一定的维护维修工作来保证系统安全和任务成功,降低发生故障而造成的损失。因此,进行适当的维修策略方案来保证系统在寿命期内具备高效能与低成本是近些年的研究热点内容。对于系统级维修策略,大部分研究往往倾向于机会维修和成组维修。许多技术,如随机过程、优化算法、模型理论等,在复杂系统的成组维修研究中广泛应用和讨论。然而,先前大部分的系统维修工作往往只考虑部件的性能水平,实际上,对于一些高可靠性要求的产品,如航天器、军用飞机等,考虑系统健康状态是至关重要的,这往往决定任务是否成功。由于系统级的数据很难监测且无从参考,因此有必要进行系统级寿命预测,从而获得系统可靠度等信息。此外,对于长寿命高可靠性的产品,其故障是由于老化、磨损等退化型失效,而传统的维修模型往往基于失效率函数,针对偶然失效。针对上述问题,提出如下解决方法。对于退化型失效问题,可基于各个设备的退化数据,建立设备寿命预测模型。现有的预测方法包括马尔可夫过程、数据挖掘、失效物理、信息融合等。针对结构复杂的多层级系统,系统级寿命信息与设备性能息息相关,由于设备间逻辑关系复杂,因此利用贝叶斯网络、机器学习、结构学习等方法可以对系统寿命信息进行预测。对于决策时考虑系统级寿命信息,本发明利用多目标规划模型,以费用和系统可靠度作为双重目标,对成组维修策略进行优化。从上所述,本发明以bn方法为例进行系统级寿命预测说明,以费用和系统可靠度权衡目标,从退化的角度实施成组维修决策的方法,该方法具有一定独创性。技术实现要素:本发明的目的是为了解决上述问题,提出一种能够有效的将系统级寿命预测信息融入成组维修决策的方法,并获得有效且合理的最优维修方案。本发明的具体步骤为:步骤一、获取部件级和系统级寿命预测信息;步骤二、计算各部件预防性维修时间;步骤三、维修成组;步骤四、计算总平均费用;步骤五、获得最佳成组维修策略。本发明的优点在于:(1)本发明建立了考虑系统级寿命预测信息的成组维修决策模型,可在降低费用的同时满足系统的高可靠性要求;(2)本发明利用部件的退化数据寿命预测,不仅适用于偶然失效的部件,也可用于退化型失效的部件。附图说明图1是本发明的流程图;图2是部件成组策略图;图3是系统g可靠性框图;图4是系统g的bn模型;图5是部件预防性维修费用与时间关系;图6是系统g维修前的可靠度预测函数;图7是系统g维修策略下的可靠度预测函数。具体实施方式下面将结合附图和实施案例对本发明作进一步的详细说明。方法的流程图如图1所示,包括以下几个步骤:步骤一、获取部件级和系统级寿命预测信息复杂系统常同时涉及偶然故障与性能退化失效,对于偶然故障选择正态、指数、威布尔分布等经验分布对产品的故障数据进行拟合与参数估计,对于存在性能退化的长寿命、无法直接获取数据的产品,通过建立随机过程模型,进而做出预测。以性能退化服从维纳过程的设备为例给出预测模型。假设性能参数w是反映产品性能状态的关键指标,且对应力s敏感,相应的可靠度函数即设备预测模型,如下式:其中,t为工作时间,μ(s)为反映性能退化率的漂移系数,是应力与时间的函数,常数σ是与环境、时间无关的扩散系数,w0是参数初始值,l为性能w的失效阈值。对于系统级寿命预测,本发明以bn方法为例进行说明。对于一个复杂多层级系统,其部件、子系统和系统都可以用bn的节点表示,其中各个部件是bn的根节点,系统为叶节点,其余的子系统为中间节点。以部件预测的寿命信息作为根节点的先验信息,通过bn,中间节点和叶节点的寿命分布即可推导而得。分别以表征根节点xi(i=1,2,…,p)、中间节点yj(j=1,2,…,q)及叶节点l在时刻t的第ai、bj、k种状态,则有ai=bj=k=0,1分别表征节点xi、yj和l处于正常和故障的状态。因此为部件的可靠度预测函数。pa()为父节点,则系统级节点的寿命预测信息,即系统可靠度可由下式推导而得:且为系统可靠度函数。对于每个维修时刻进行维修的部件,其可靠度发生变化,相应的系统可靠度也需要重新进行预测。步骤二、计算各部件预防性维修时间;本方法考虑部件级维修策略为完全换件,当产品的运行时间达到tp时执行预防性换件。若产品在运行时间达到tp前发生了失效,则执行修复性换件,并重置产品的运行时间。产品在预定的预防性换件时间tp前不发生失效的概率为r(tp),在tp前发生失效的概率为f(tp)。则产品在时间间隔(0,tp)的总期望费用tec(tp)为:其中cp、cc、cdp、cdc分别为预防性维修、修复性维修的费用和两者的停机费用,m(tp)是失效周期期望时间长度。通过上式的趋势可得到最优预防性维修的时间t。步骤三、维修成组系统在其寿命期要完成规定的任务,这些任务通过系统的任务剖面来表达。假设系统每完成一次任务可获得一次维修机会,{t1,t2,...,tn}为系统n个部件的最佳预防性维修时间。由于部件维修只考虑完全换件,则部件每次进行换件的时间间隔一致。如果多个部件的最佳维修时间落在同一区间,则它们存在成组维修的可能性(如图2)。在第k个时间区间内,区间两端为两个维修时刻,表示为tk0、tk1。设有m个部件落入该区间,表示为集合g,在tk0时维修的r个部件记为g0,tk1时维修的s个部件记为g1,可知t(k-1)1=tk0。步骤四、计算总平均费用;令总平均时间费用分为平均维修费用umc和平均停机费用udc,则twc=udc+umc(4)由于成组维修可减少重复的停机费用,因此tk0时的平均停机费用为:其中rj(t)和fj(t)为部件j维修前的可靠度函数,tj(n-1)为上次维修的时间,部件维修后可靠度重回1并重新进行预测。同理可得tk1时的平均停机费用。维修费用为每个部件预防性维修和修复性维修的总和,因此tk0时的平均维修费用为:同理可得tk1时的平均维修费用,并得到区间k的总平均费用。由于区间内每个部件有2个维修选择,则该区间共有2m个成组维修策略需要决策。步骤五、获得最佳成组维修策略本方法中使用多属性价值理论将权衡维修策略的因素整合到一个指标中,解决需要同时考虑多个权衡目标的维修决策问题。使用twci表示方案i的总平均费用,使用rl(t)i表示方案i的系统可靠度,*为最大值,则方案i的权衡值vi为:其中,w为权重系数,w1+w2=1。当需要决策的方案数量庞大时,可利用粒子群算法、蚁群算法等优化算法进行模型求解,得到最优成组维修策略。实施案例:(1)仿真算例概述假设某产品g具有图3所示的功能结构关联,其中子系统c和f并联,分别由a、b和d、e串联构成。该产品在552h和840h有两个任务停休时间,即两个维修机会,在工作时间达到1100h后退役。部件a,b,e,d的失效模式及相关费用如下表所示。表1各部件失效模式及相关费用(2)模型构建根据系统可靠性框图,可建立个组件间的关系,可知组件a,b,d,e为根节点,子系统cf为中间节点,系统g为叶节点。由组件间串并联关系及专家经验,可建立bn模型如图4所示。根据部件的失效模式和寿命分布模型,可仿真其参数和可靠度函数如下表所示。表2部件级寿命预测模型通过部件级预测模型及预防性费用计算表达式,可获得各部件平均时间费用与预防性维修时间的关系,如图5所示。可以得到各部件最佳维修时间ta,tb,td,te分别为607h,833h,883h,576h。由部件最佳维修时间可知,部件a,b,e的维修时间落在区间(552,840)中,因此有8个成组维修方案需要决策,并可得到各个方案的相关费用,如下表所示。表3区间(552,840)成组维修策略策略在552h维修的部件在840h维修的部件平均时间总费用1a,b,e/19.821542/a,b,e20.216943a,be20.347514ea,b19.690985ab,e19.734086b,ea20.30447a,eb19.208128ba,e20.83036通过上表可知费用最省的方案为策略7。根据bn及部件级寿命预测模型,用matlabbn工具包中的“engine=jtree_inf_engine(bnet)”进行算法实现,得到系统维修前的可靠度函数如图6所示。由于在552h有部件进行维修,其可靠度在维修后重回到1,因此重新进行系统级预测。以840h维修前的可靠度作为系统可靠度权衡目标值,结合平均时间总费用,可得多目标权衡值:令w1=w2=0.5,可得各策略的权衡值如下表所示。表4各成组策略权衡比较(3)最优策略及分析由各方案的权衡值可得,最优方案为策略7。也就是说,费用和系统可靠度比重相同时,策略7不仅费用最低,也是权衡值最高的最优策略。然而,当系统可靠度的比重加大,如w1=0.2,w2=0,8时,最优方案为策略1,此时适用于对可靠性要求极高的产品。同理,在840h到1100h区间内,只有部件d落在该区间内,经权衡选择在840h维修。在此方案下系统的可靠度表达如图7所示。通过上述分析,可知本方法可结合系统级寿命预测信息进行成组维修决策,同时可根据实际情况对费用和系统可靠度的权重进行调整。当前第1页12