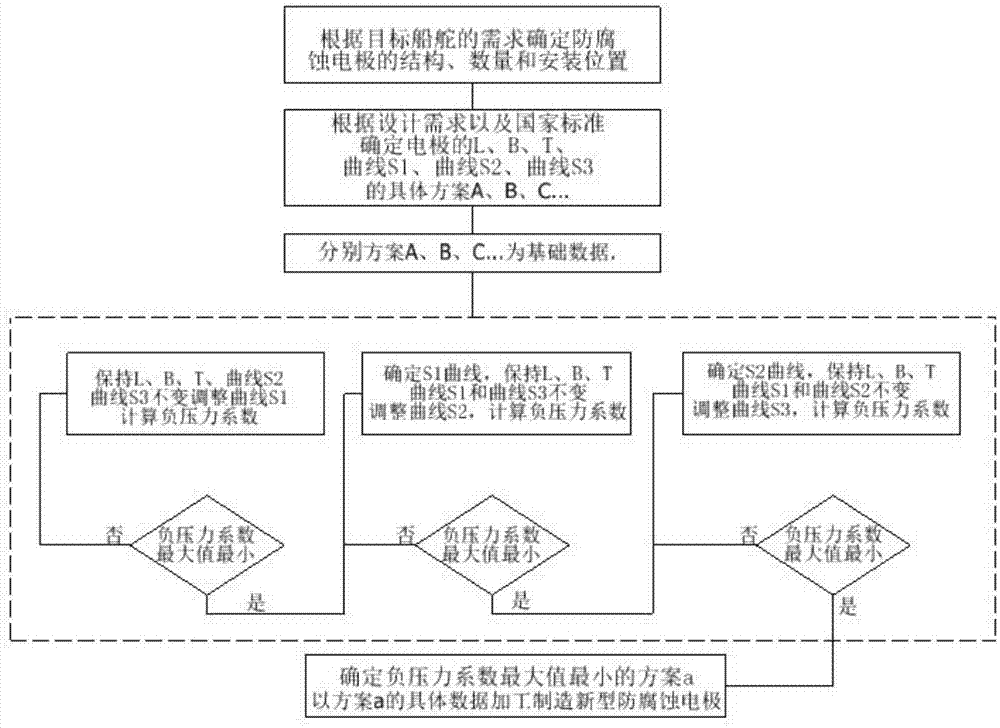
本发明涉及船舶领域,尤其涉及一种新型船舵防腐蚀电极及其设计方法。
背景技术:
应用电化学的方法来防止和减轻金属腐蚀的方法称为电化学保护。电化学保护主要有牺牲电极的阴极保护法和外加电流阴极保护法。但是外加电流阴极保护法对电流密度要求较高,难以达到预期的防腐蚀要求,因此现如今舰船防腐蚀处理的常见方法是牺牲电极的阴极保护法。舵作为舰船上的一个重要部位,长期浸泡在水中,又受到螺旋桨高速尾流的影响,且经常处于活动状态,因此容易发生水解腐蚀和冲击腐蚀等现象。为了有效抑制舵面的腐蚀现象,现有标准规定在分别舵面和舵背两侧安装舵防腐蚀电极,利用更活跃的金属来替代腐蚀,即牺牲电极保护法。然而,当前标准中规定的防腐蚀电极往往是平板状或长条状,其与舵叶表面约成90°角度,存在形状畸变,易发生流体分离现象,且处在螺旋桨尾流的主要作用区域,因此在较低的航速下就会发生空化现象。实船试验结果显示,原有舵防腐蚀电极在较低航速下即会先于面发生空化现象。即防腐蚀电极此时不仅可能未起到防腐蚀的作用,其引起的空化现象还会造成空化剥蚀,增加维护成本,加剧舵叶和船体尾部的局部振动以及结构振动引起的辐射噪声。因此,现有舵防腐蚀电极已不能满足要求,迫切需要对其进行改进设计。技术实现要素:本发明的目的是在于提供一种新型船舵防腐蚀电极及其设计方法,可有效抑制船舵防腐蚀电极处的流体分离,提高抗空化性能,改善空化剥蚀现象,并减小舵的阻力。为实现上述目的,本发明创造采用如下技术方案。新型船舵防腐蚀电极,防腐蚀电极结构为光顺的类椭球形,防腐蚀电极沿弦长方向的厚度分布形式曲线s1、沿展长方向的厚度分布形式曲线s2、以及厚度沿弦向的分布和拱度沿弦向的分布曲线s3的几何形状使得0°舵角对舵防腐蚀电极的负压力系数最小,负压力系数其中p为舵防腐蚀电极表面的压力,p0为参考压力,ρ为海水密度,vs为船舶航速。对上述方案的进一步改进还包括,新型船舵防腐蚀电极的内部贯穿一根铁芯,铁芯两端焊接在一个垫板上以通过垫板与舵叶贴合,垫板焊接在舵叶上,所述新型舵防腐蚀电极的工作面面积与平板状电极面积一致,新型防腐蚀电极结构的数量与平板状防腐蚀电极数量相同;新型舵防腐蚀电极的在舵叶表面均匀分布以使舵叶表面的电流密度均匀分布。新型船舵防腐蚀电极的设计方法,包括以下步骤:步骤一、根据目标船舵的需求,确定新型舵防腐蚀电极的结构、数量和安装位置;步骤二、确定新型防腐蚀电极与进流方向平行的长度l、与舵展长方向平行的宽度b、最大厚度t、沿弦长方向的厚度分布形式曲线s1、沿展长方向的厚度分布形式曲线s2和厚度沿弦向的分布和拱度沿弦向的分布曲线s3为基本参数;步骤三、在设计工况下0°舵角对新型舵防腐蚀电极的压力分布进行计算,并换算成负压力系数,负压力系数的定义为:其中p为新型舵防腐蚀电极表面的压力,p0为参考压力,ρ为海水密度,vs为船舶航速,以新型防腐蚀电极表面最大负压力系数最小值为目标函数,通过迭代计算确定具体参数。对上述方案的进一步改进还包括,步骤一中设计新型舵防腐蚀电极时,使其工作面面积与平板状电极面积一致,新型防腐蚀电极结构的数量与平板状防腐蚀电极数量相同;新型舵防腐蚀电极的在舵叶表面均匀分布以使舵叶表面的电流密度均匀分布。对上述方案的进一步改进还包括,步骤二中,使各剖面曲线s1在弦向的厚度分布形式保持一致,使各剖面曲线s2在展向的厚度分布形式保持一致;使各剖面曲线s3为相同形状;长度l、宽度b、最大厚度t和平板状防腐蚀电极一致为初始数据,曲线s1、曲线s2为对称曲线作为初始数据,曲线s3为长轴为l、短轴为b的椭圆作为初始数据。对上述方案的进一步改进还包括,步骤三中新型舵防腐蚀电极的具体优化设计过程包括:过程a,保持长度l、宽度b、最大厚度t、曲线s2和曲线s3参数不变,以曲线s1在弦向的厚度分布形式为调整参数,以舵防腐蚀电极工作面的负压力系数最大值最小化为目标函数,用数值计算方法对桨舵系统下的舵水动力进行计算,以曲线s1在弦向的厚度分布形式作为过程a的设计结果;过程b,在上述基础上,保持长度l、宽度b、最大厚度t、曲线s1和曲线s3参数不变,以曲线s2在展向的厚度分布形式为调整参数,以舵防腐蚀电极工作面的负压力系数最大值最小化为目标函数,用数值计算方法对桨舵系统下的舵水动力进行计算,以曲线s1在展向的厚度分布形式作为过程b的设计结果;过程c,在上述基础上,保持长度l、宽度b、最大厚度t、曲线s1和曲线s2参数不变,以曲线s3的几何形状为调整参数,舵防腐蚀电极工作面的负压力系数最大值最小化为目标函数,用数值计算方法对桨舵系统下的舵水动力进行计算,以曲线s3的几何形状作为过程c的设计结果;过程d,以上述过程a、过程b、过程c的设计结果作为新型船舵防腐蚀电极的最终参数。对上述方案的进一步改进还包括,所述过程c之后还包括:过程c1,保持舵防腐蚀电极工作面面积与原平板状防腐蚀电极一致,对长度l、宽度b、最大厚度t取不同值;过程c2,针对过程c1所得的多种几何方案,重复过程a、过程b、过程c对参数s1、s2和s3进行优化设计,并将舵防腐蚀电极工作面的负压力系数最大值最小化和舵阻力最小化组成一个多目标函数,通过最小二乘法求解获得最优的防腐蚀电极几何形状。其有益效果在于:(1)本发明提出的新型船舵防腐蚀电极,能明显改善舵防腐蚀电极处的流场均匀性,增大该位置处的最小压力值,提高其抗空化性能,大幅提升其空化起始航速。(2)本发明提出的新型船舵防腐蚀电极,能明显改善舵防腐蚀电极的空化剥蚀现象,可延长使用年限,减小维修成本。(3)本发明提出的新型船舵防腐蚀电极,能明显抑制舵防腐蚀电极处的分离涡,减小舵的阻力,提高船舶的快速性能。(4)本发明提出的新型船舵防腐蚀电极,可以降低舵防腐蚀电极空化引起的舵叶振动以及振动引起的结构辐射噪声。(5)本发明提出的新型船舵防腐蚀电极,可不改变舵防腐蚀电极的安装位置,有利于保持舵叶表面的电流均匀度,从而达到其应有的防腐蚀效果。附图说明图1为新型舵防腐蚀电极设计方法的流程示意图;图2是安装原舵防腐蚀电极的舵叶正视图(从船右舷观看);图3是安装原舵防腐蚀电极的舵叶的左剖面视图(从船尾往船首看);图4是安装新型舵防腐蚀电极的舵叶正视图(从船右舷观看);图5是安装新型舵防腐蚀电极的舵叶的左剖面视图(从船尾往船首看);图6是新型舵防腐蚀电极安装图;图7是曲线s1在弦向的厚度分布形式曲线;图8是曲线s2在展向的厚度分布形式曲线;图9是曲线s3在展向的厚度分布形式曲线;图10是对应实船24节航速下0deg时(正视图)的原舵防腐蚀电极压力分布云图;图11是对应实船24节航速下0deg时(正视图)的新型舵防腐蚀电极压力分布云图。其附图标记包括:舵叶1,新型防腐蚀电极2,原舵防腐蚀电极3,铁芯4,垫板5,防腐蚀电极工作面6,舵叶前缘7,舵叶后缘8,舵叶上端9,舵叶下端10。具体实施方式以下结合具体实施例对本发明创造作详细说明。下面结合附图和具体实施例对本发明作进一步的详细说明,以便于更加清楚地了解本发明,但它们并不对
发明内容进行限定。一种新型船舵防腐蚀电极,包括舵叶1,舵叶1剖面可为对称型或非对称型,舵叶1类型也可为普通舵或襟翼舵。新型防腐蚀电极2一般在舵叶1内外两侧的中上部位和中下部位各安装一块,也可根据实际需要在舵叶不同位置安装不同数量的新型防腐蚀电极2。新型防腐蚀电极2形状为光顺地椭球体或者其他可抑制流体分离的流线型形状。新型船舵防腐蚀电极内部贯穿一根铁芯4,铁芯4两端通过焊接与垫板5相连,垫板5通过焊接与舵叶1相贴合,防腐蚀电极工作面6裸露在海水中起防腐蚀作用。上述新型船舵防腐蚀电极的设计方法包括以下步骤:步骤一、根据目标船舵的需求,确定舵防腐蚀电极的数量和安装位置,以此作为防腐蚀电极设计的固定参数;在设计新型舵防腐蚀电极时,其工作面面积与平板状电极面积一致,故在确定防腐蚀电极的数量时,可采用确定平板状防腐蚀电极数量的方法,具体见gjb157a-2008;根据行业准则以及国家标准,可知上述工作面面积与平板状电极面积为有限的几种方案;进一步地,在确定舵防腐蚀电极的安装位置时以其在舵叶表面均匀分布为主要参考标准为使舵叶表面的电流密度均匀分布步骤二、新型舵防腐蚀电极为类椭球体结构,设计时以其与进流方向平行的长度l(见图6)、与舵展长方向平行的宽度b(见图4)、最大厚度t(见图6)、沿弦长方向的厚度分布形式曲线s1(见图7)、沿展长方向的厚度分布形式曲线s2(见图8)和厚度沿弦向的分布和拱度沿弦向的分布曲线s3(见图9)为基本数。为简化设计过程设计,提高计算效率,本实施例中各剖面曲线s1在弦向的厚度分布形式保持一致,使各剖面曲线s2在展向的厚度分布形式保持一致,各剖面曲线s3为相同形状。以l、b和t和平板状防腐蚀电极一致作为初始数据,s1、s2以对称曲线作为初始数据,与舵叶表面接触的曲线s3以长轴为l、短轴为b的椭圆为初始数据。步骤三、依据步骤二所述基本参数对舵防腐蚀电极进行优化设计,在设计工况下0°舵角对舵防腐蚀电极的压力分布进行计算,并换算成负压力系数,负压力系数的定义为:其中p为舵防腐蚀电极表面的压力,p0为参考压力,ρ为海水密度,vs为船舶航速。以防腐蚀电极表面最大负压力系数最小化为目标,通过迭代计算确定最优方案。其中,关于舵防腐蚀电极几何优化设计的具体过程为:过程a,长度l、宽度b、最大厚度t、曲线s2和曲线s3等参数保持不变,曲线s1在弦向的厚度分布形式为调整参数,舵防腐蚀电极工作面的负压力系数最大值最小化为目标函数,用三维面元法或计算流体力学方法对桨舵系统下的舵水动力进行计算,曲线s1在弦向最优的厚度分布形式作为此过程的设计结果;过程b,在过程a的基础上,长度l、宽度b、最大厚度t、曲线s1和曲线s3等参数保持不变,曲线s2在展向的厚度分布形式为调整参数,舵防腐蚀电极工作面的负压力系数最大值最小化为目标函数,用数值计算方法(三维面元法或计算流体力学方法)对桨舵系统下的舵水动力进行计算,曲线s1在展向的最优的厚度分布形式作为此过程的设计结果;过程c,在过程b的基础上,长度l、宽度b、最大厚度t、曲线s1和曲线s2等参数保持不变,曲线s3的几何形状为调整参数,舵防腐蚀电极工作面的负压力系数最大值最小化为目标函数,用数值计算方法(三维面元法或计算流体力学方法)对桨舵系统下的舵水动力进行计算,该过程的设计结果即舵防腐蚀电极的一种设计方案;过程d,以上述过程a、过程b、过程c的设计结果作为新型船舵防腐蚀电极的最终参数。为进一步提高防腐蚀电机的设计出效果,对其进一步地改进还包括,在上述过程c之后还设置了进一步优化设计的过程,包括过程c1,以保持舵防腐蚀电极工作面面积与平板状防腐蚀电极一致为原则,对长度l、宽度b、最大厚度t进行改变形成多种几何方案,在对实际船舶以及船舵形状以及结构进行设计过程中,本领域技术人员根据设计需求以及国家标准可以确定有限的集中方案;过程c2,针对过程c1所得的多种几何方案,重复过程a、b、c对其参数s1、s2和s3进行优化设计,并将舵防腐蚀电极工作面的负压力系数最大值最小化和舵阻力最小化组成一个多目标函数,通过最小二乘法求解获得最优的防腐蚀电极几何形状。为了清楚地了解新型船舵防腐蚀电极的抗空化性能和减阻效果,以某水面舰船的桨和舵模型为设计载体,在原舵防腐蚀电极3的基础上设计了一型新型舵防腐蚀电极2,并针对安装两种舵防腐蚀电极的桨和舵模型开展了cfd计算和模型试验。其中,图7为新型防腐蚀电极s1曲线沿弦向的厚度分布形式,图中x/c=0指向舵叶后缘8,x/c=1指向舵叶前缘7。tmax为弦向最大厚度;图8为新型防腐蚀电极s2曲线沿展向的厚度分布形式,图中x/c=0指向舵叶上端9,x/c=1指向舵叶下端10,hmax为展向最大厚度;图9为新型舵防腐蚀电极的s3曲线形状;新型防腐蚀电极长度l=25mm,宽度b=10mm。在该实施例中,舵展长为198.7mm,螺旋桨直径为240mm。根据国家标准设计的现有防腐蚀电极(见图2和图3)为平板状,长度方向顺流线方向安装。设计新防腐蚀电极时可保持长、宽和厚度等参数与传统平板状电极相同,将平板进行优化设计为类椭球形(见图4和图5)。采用star-ccm+软件对安装两种舵防腐蚀电极的舵水动力性能和抗空化性能进行计算,表1为两种舵防腐蚀电极在转速1200rpm,进速4.8m/s工况下的舵阻力计算结果。表1防腐蚀电极阻力/n平板状9.98流线型8.58由表1可以看出,安装新型舵防腐蚀电极2后,舵阻力由9.98n降低8.58n,阻力减小值为1.4n,减阻程度为14.02%,故安装新型新型舵防腐蚀电极2可有利于提升船舶的快速性能。图10为对应实船24节航速下0deg时(正视图)的原舵防腐蚀电极压力分布云图,由图中可以看出,在该工况下,原舵防腐蚀电极3的最小绝对压力值为-3926.1pa,早已低于此时的饱和蒸汽压力2300pa,表明此时已经发生了空化现象。图11是对应实船24节航速下0deg时(正视图)的新型舵防腐蚀电极压力分布云图,由图11可以看出,新型舵防腐蚀电极2在此工况下的最小压力值为9157.2pa,远大于饱和蒸汽压力2300pa,即此时未发生空化现象。结合所开展的cfd计算和模型试验结果可知,原舵防腐蚀电极2在对应实船航速16节工况下即开展发生空化,而新型舵防腐蚀电极2在26节航速工况下仍未发生空化,因此设计的新型舵防腐蚀电极2的空化起始航速可提升10节以上。因此,通过该实施例说明本发明所设计的新型船舵防腐蚀电极具有良好的抗空化性能和减阻效果。最后应当说明的是,以上实施例仅用以说明本发明创造的技术方案,而非对本发明创造保护范围的限制,尽管参照较佳实施例对本发明创造作了详细地说明,本领域的普通技术人员应当理解,可以对本发明创造的技术方案进行修改或者等同替换,而不脱离本发明创造技术方案的实质和范围。当前第1页12