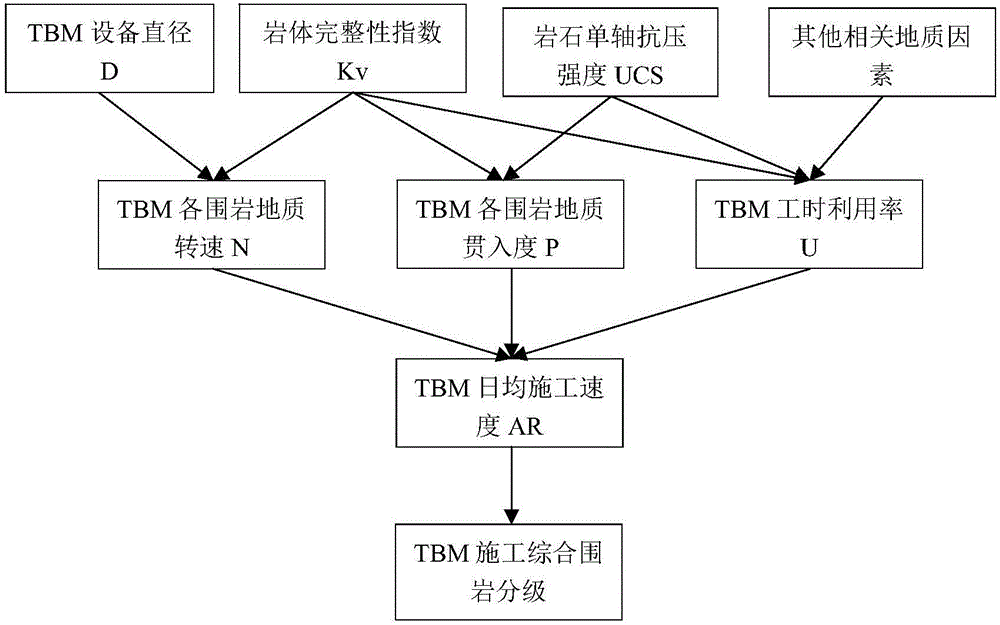
本发明涉及对tbm施工的围岩可掘性分级方法,尤其涉及一种考虑到围岩可掘性与设备适应性的tbm围岩可掘性分级方法。
背景技术:
:与传统的隧道施工方法相比,tbm法施工速度快,通常掘进速率是传统钻爆法的3~10倍,然而tbm对地质条件的适应性很差,如果在掘进时没有采取很好的掘进参数与之匹配,那么可能会导致tbm无法发挥其掘进速度快的优势,进而造成工期延误。传统隧道施工方法一般是通过围岩分类方法来设计隧道支护和指导施工,并据此进行成本和工期预算。但是当前的隧道围岩分级法大多针对隧道围岩稳定性评价和支护结构的设计提出,越来越难以满足tbm隧道的施工需要。tbm施工条件下的隧道围岩分级应该以工程岩体的可掘性为基础,充分考虑影响tbm掘进效率的主要工程地质因素。目前,尚没有公认的tbm施工隧道的围岩分类统一标准。现阶段比较常用的围岩分类方法有挪威学者学者n.barton的q系统分类法、南非学者bieniawski的地质力学分类法(rmr)以及迪尔的rqd分类法等。n.barton于1999年在q系统分类法的基础上提出了qtbm系统,该系统虽然考虑了岩体与tbm之间的相互作用,但是如果隧道围岩岩性差别较大,利用该模型预测得到的误差将会很大,且该系统涉及的参数指标太多,实用困难,无法满足tbm施工隧道的围岩分级要求。因此目前所存在的围岩分级分类系统的普适性较差,往往不能针对特定的项目工程进行合理的分级预测。技术实现要素:针对上述现有技术中描述的不足,本发明提供一种基于数据挖掘的tbm施工围岩可掘性分级方法,以期能够对tbm掘进速率进行准确预测,并对tbm施工提供科学指导。为解决上述技术问题,本发明所采用的技术方案如下:一种基于数据挖掘的tbm施工围岩可掘性分级方法,步骤如下:s1,建立贯入度预测模型。具体步骤为:s1.1,建立不同岩体条件下tbm掘进参数上升段的设备运行参数单刀推力与控制参数贯入度之间的关系模型。首先进行贯入度梯度变化和贯入度连续变化的tbm掘进实验,获得单刀法向力随贯入度的变化规律;然后建立不同岩体条件下tbm掘进参数上升段的设备运行参数单刀推力与控制参数贯入度之间的关系模型:f=a×p+b;其中,a表示贯入度对单刀推力影响系数,b为滚刀破岩门槛值,p表示贯入度。s1.2,建立岩体状态参数与贯入度的关系模型。具体步骤为:s1.2.1,建立贯入度对单刀推力影响系数a与单位体积节理数jv之间的函数逐步回归拟合公式:a=f(jv)=p0×jv2+p1×jv+p2,0<jv<35;式中,p0、p1、p2为拟合常数,f为函数。而a+b与ucs和jv都具有线性相关,因此建立假设函数关系如下:a+b=g(ucs,jv),0<jv<35;0<ucs<100。s1.2.2,建立贯入度为1时,抗压强度指标ucs与单位体积节理数jv之间的函数逐步回归拟合公式:a+b=g(ucs,jv)=p3×ucs+p4×jv+p5;其中,p3、p4、p5为拟合常数,g为回归函数。s1.3,计算岩体基本质量指标bq:bq=100+3ucs+250kv;其中,ucs为抗压强度指标;kv为岩体的完整性系数;且当ucs≥90kv+30时,ucs=90kv+30;当kv≥0.04ucs+0.4时,kv=0.04ucs+0.4。s1.4,确定岩体的传统围岩等级。按照计算的岩体基本质量指标bq与传统围岩等级的关系确定岩体的传统围岩等级。s1.5,计算岩体的传统围岩等级下滚刀的单刀推力值:fn=fmax×fs;其中,fs为传统围岩等级下滚刀单刀推力系数;fmax为最大单刀推力。s1.6,根据步骤s1.1和步骤s1.2以及滚刀的单刀推力值,计算得到滚刀的贯入度p值,从而建立起贯入度预测模型。s2,建立转速预测模型。具体步骤为:s2.1,建立刀盘最大转速与刀盘直径的函数特征关系:nmax=12.44d-0.313;式中,nmax为刀盘转速,d为掘进机直径。s2.2,建立刀盘转速n与岩体完整性指数kv之间的函数关系;s3,建立tbm施工掘进工时利用率预测模型。tbm施工的工时利用率是tbm净掘进时间与总施工时间的比值,它是衡量tbm的使用及管理水平的重要指标。s3.1,进行tbm停机时间工序分类。所述停机时间工序为三类:固定停机时间工序、随掘进距离变化的停机工序、随岩体条件和掘进距离共同变化的停机工序。所述固定停机时间工序,与岩体状况和进尺距离无关,包括班组交接t1、设备维保t2、刀盘检修t3、后配套处理t4、其他延误时间t5。所述随掘进距离变化的停机工序,包括换步时间t6。所述随岩体条件和掘进距离共同变化的停机工序,包括故障处理t7、刀具更换t8、支护时间t9、不良地质处治t10。s3.2,建立tbm停机工序时间统计表。s3.3,建立tbm掘进工时利用率预测函数关系式:其中,u为tbm掘进工时利用率,ar为掘进速度。s4,根据步骤s1-s3计算掘进速度ar,并以tbm掘进速度ar为评价指标,进行tbm施工围岩可掘性分级。具体步骤为:s4.1,根据步骤s1-s3计算掘进速度ar:其中,p为贯入度,n为刀盘转速,u为tbm掘进工时利用率。s4.2,根据掘进速度ar将tbm施工围岩划分为5个等级。当ar≥2.0m/h,时,tbm施工围岩条件极好,定义为ⅰ级围岩;当1.2m/h<ar≤2.0m/h时,表明tbm施工围岩条件好,定义为ⅱ级围岩;当0.6m/h<ar≤1.2m/h,时,tbm施工围岩条件较好,定义为ⅲ级围岩;当0.2m/h<ar≤0.6m/h,时,tbm施工围岩条件一般,定义为ⅵ级围岩;当0.2m/h≤ar时,tbm施工围岩条件差,定义为ⅴ级围岩。本发明采用基于工程案例的数学统计和数学挖掘的研究方法,将影响tbm掘进速率的参数进行明确的定义和划分,合理预测刀盘贯入度、转速、工时利用率,直观明了,以tbm日均掘进速度为评价指标,最终建立基于tbm施工的围岩可掘性分级模型,考虑到tbm的施工围岩可掘性和地质适应性,将围岩分为四个等级:ⅰ级围岩是tbm围岩施工条件极好;ⅱ级围岩是tbm围岩施工条件好;ⅲ级围岩是tbm施工围岩条件较好;ⅵ级围岩是tbm施工围岩条件一般;ⅴ级围岩是tbm施工围岩条件差。附图说明为了更清楚地说明本发明实施例或现有技术中的技术方案,下面将对实施例或现有技术描述中所需要使用的附图作简单地介绍,显而易见地,下面描述中的附图仅仅是本发明的一些实施例,对于本领域普通技术人员来讲,在不付出创造性劳动的前提下,还可以根据这些附图获得其他的附图。图1为本发明的系统流程图。图2为本发明刀盘直径与刀盘转速的关系图。图3为本发明tbm停机时间工序分类图。具体实施方式下面将结合本发明实施例中的附图,对本发明实施例中的技术方案进行清楚、完整地描述,显然,所描述的实施例仅仅是本发明一部分实施例,而不是全部的实施例。基于本发明中的实施例,本领域普通技术人员在没有付出创造性劳动前提下所获得的所有其他实施例,都属于本发明保护的范围。一种基于数据挖掘的tbm施工围岩可掘性分级方法,如图1所示,步骤如下:s1,建立贯入度预测模型。前期准备:收集tbm施工案例中的tbm掘进参数和岩体状态参数数据,tbm掘进参数包括tbm的推力、扭矩等运行参数,贯入度和转速控制参数,岩体状态参数包括岩体抗压强度ucs、单位体积节理数jv和围岩等级。岩体单轴抗压强度指标ucs是通过现场取芯并进行实验室岩石抗压强度试验获取或者通过统计洞壁素描中节理间距、节理条数,并根据岩体体积节理数jv的计算公式:jv=∑(1/dk)+sk/5得到,其中,dk为第k组节理的间距,sk为第k组每立方体岩体非成组节理条数。围岩等级通过详细的地勘报告获取,或者利用岩体抗压强度ucs和单位体积节理数jv计算围岩基本质量指标bq值进行围岩分级,建立运行参数与控制参数函数表达式,并提出单刀推力的经验系数,从而建立贯入度预测模型。具体步骤为:s1.1,建立不同岩体条件下tbm掘进参数上升段的设备运行参数单刀推力与控制参数贯入度之间的关系模型。首先进行贯入度梯度变化和贯入度连续变化的tbm掘进实验,获得单刀法向力随贯入度的变化规律;然后建立不同岩体条件下tbm掘进参数上升段的设备运行参数单刀推力与控制参数贯入度之间的关系模型:f=a×p+b;其中,a表示贯入度对单刀推力影响系数,b为滚刀破岩门槛值,p表示贯入度。s1.2,建立岩体状态参数与贯入度的关系模型。具体步骤为:s1.2.1,建立贯入度对单刀推力影响系数a与单位体积节理数jv之间的函数逐步回归拟合公式:a=f(jv)=p0×jv2+p1×jv+p2,0<jv<35;式中,p0、p1、p2为拟合常数,f为函数。贯入度对单刀推力影响系数a表示的是增加单位贯入度所需要的单刀推力增量,由于当岩体越破碎时,增加单位贯入度所需要的推力增量越小,故贯入度对单刀推力影响系数a是与岩体节理数量相关的函数。而a+b与ucs和jv都具有线性相关,因此建立假设函数关系如下:a+b=g(ucs,jv),0<jv<35;0<ucs<100。s1.2.2,建立贯入度为1时,抗压强度指标ucs与单位体积节理数jv之间的函数逐步回归拟合公式:a+b=g(ucs,jv)=p3×ucs+p4×jv+p5;其中,p3、p4、p5为拟合常数,g为回归函数。刀具破岩门槛值b为滚刀侵入岩体并产生压痕的最小门槛值,当p=1时,单刀推力f=a+b,说明了滚刀产生1mm有效贯入度时,滚刀所需要具备的推力,因此a+b可以用来衡量岩体的可掘进性能特征。s1.3,计算岩体基本质量指标bq:bq=100+3ucs+250kv;其中,ucs为抗压强度指标;kv为岩体的完整性系数;且当ucs≥90kv+30时,ucs=90kv+30;当kv≥0.04ucs+0.4时,kv=0.04ucs+0.4。岩体完整性系数kv是由单位体积节理数jv确定,单位体积节理数jv与岩体完整性系数kv的对照关系如表1所示。表1s1.4,确定岩体的传统围岩等级。按照计算的岩体基本质量指标bq与传统围岩等级的关系确定岩体的传统围岩等级,如表2所示。表2s1.5,计算岩体的传统围岩等级下滚刀的单刀推力值:fn=fmax×fs;其中,fs为传统围岩等级下滚刀单刀推力系数;fmax为最大单刀推力,单刀推力与传统围岩等级的对应关系,如表3所示。表3s1.6,根据步骤s1.1和步骤s1.2以及滚刀的单刀推力值,计算得到滚刀的贯入度p值,从而建立起贯入度预测模型。s2,建立转速预测模型。具体步骤为:s2.1,建立刀盘最大转速与刀盘直径的函数特征关系,如图2所示,nmax=12.44d-0.313;式中,nmax为刀盘转速,d为掘进机直径。s2.2,建立刀盘转速n与岩体完整性指数kv之间的函数关系;具体如表4所示。表4kv取值岩体完整程度刀盘转速的取值0-0.25破碎(kv+0.25)×nmax0.25-0.45完整性差(kv+0.25)×nmax0.45-0.75较完整(kv+0.25)×nmax0.75-1.0完整nmaxs3,建立tbm施工掘进工时利用率预测模型。tbm施工的工时利用率是tbm净掘进时间与总施工时间的比值,它是衡量tbm的使用及管理水平的重要指标。s3.1,进行tbm停机时间工序分类,如图3所示。所述停机时间工序为三类:固定停机时间工序、随掘进距离变化的停机工序、随岩体条件和掘进距离共同变化的停机工序。所述固定停机时间工序,与岩体状况和进尺距离无关,包括班组交接t1、设备维保t2、刀盘检修t3、后配套处理t4、其他延误时间t5,其他延误时间t5包括硫化皮带,测量换站,后配套处理等,根据大量案例统计将其固定化分摊到各个工序中。所述随掘进距离变化的停机工序,包括换步时间t6。所述随岩体条件和掘进距离共同变化的停机工序,包括故障处理t7、刀具更换t8、支护时间t9、不良地质处治t10。其中tbm耗费在支护和不良地质处治工序上的时间可以根据当前围岩完整程度和实际进尺估算得到。而另外一些工序,比如故障处理和刀具更换等所耗费的时间较为随机,但总体上与地质状况强相关,统计发现当岩体强度越大,两工序在单位掘进距离下平均耗时越多,总体上可以根据统计结果进行平均化处理。s3.2,建立tbm停机工序时间统计表,如表5所示。表5s3.3,建立tbm掘进工时利用率预测函数关系式:其中,u为tbm掘进工时利用率,ar为掘进速度。s4,根据步骤s1-s3计算掘进速度ar,并以tbm掘进速度ar为评价指标,进行tbm施工岩石可掘性分级。具体步骤为:s4.1,根据步骤s1-s3计算掘进速度ar:其中,p为贯入度,n为刀盘转速,u为tbm掘进工时利用率。s4.2,根据掘进速度ar将tbm施工围岩划分为5个等级。当ar≥2.0m/h,时,tbm施工围岩条件极好,定义为ⅰ级围岩;当1.2m/h<ar≤2.0m/h时,表明tbm施工围岩条件好,定义为ⅱ级围岩;当0.6m/h<ar≤1.2m/h,时,tbm施工围岩条件较好,定义为ⅲ级围岩;当0.2m/h<ar≤0.6m/h,时,tbm施工围岩条件一般,定义为ⅵ级围岩;当0.2m/h≤ar时,tbm施工围岩条件差,定义为ⅴ级围岩。具体如表6所示。表6本发明针对现有tbm施工领域缺乏统一有效的围岩地质预测及掘进速率预测的实施方法的这一行业应用现状,提出依据工程案例的数据统计和数据挖掘,建立tbm施工条件下的隧道围岩可掘性分级方法,使其能够准确预测各类围岩地质条件下的tbm掘进速率,指导tbm各项施工参数,并预期进行施工成本和工期预测。以上实施方式仅用于对本发明的描述,而非对本发明的限制。对本领域的技术人员来说在不脱离本发明的范围下进行适当的变化或修改是显而易见的,因此所有等同的技术方案也属于本发明的范畴,本发明的专利保护范围由所附的权利要求定义。当前第1页12