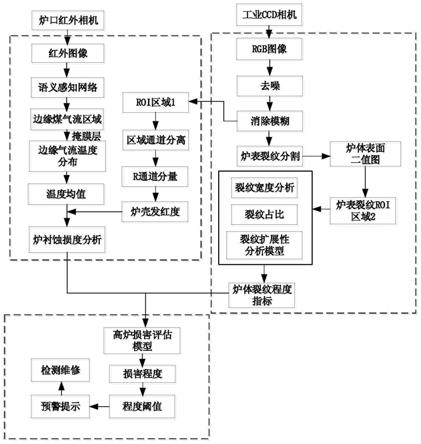
1.本发明涉及人工智能计算机视觉处理领域,特别是涉及一种基于人工智能及图像处理的高炉损坏分析方法。
背景技术:2.高炉的破损程度主要体现在炉衬、炉体、炉壳、炉缸等损坏情况,对于破损程度较大的高炉,如果不及时进行维修或改建,将会造成重大安全事故问题,降低高炉冶炼产品质量。目前对于高炉破损程度分析以及寿命的评价,主要通过操作工观察炉况以及监视高炉炉缸内部布料矿物反应状况,来分析高炉使用情况,进一步对高炉破损度进行评估。该方法准确性低,且不具有实时性,浪费人力,工作效率较低。高炉炼铁是钢铁企业炼钢、铸铁等工艺的基础保障,高炉运行质量的好坏直接关系着企业的效益,高炉能否高效长寿运行越来越受到各国钢铁企业的重视。
技术实现要素:3.本发明克服了现有技术中高炉损坏程度仍需智能化识别的问题,提供一种维护成本低,智能识别程度高的基于人工智能及图像处理的高炉损坏分析方法。
4.本发明的技术解决方案是,提供一种具有以下步骤的基于人工智能及图像处理的高炉损坏分析方法:含有以下步骤:
5.步骤一,在炉口安装防高温红外相机采集炉内图像,在高炉旁边安装多个耐高温ccd相机采集炉表图像;
6.步骤二,将红外相机采集的红外图像送入训练好的语义感知网络,获取炉内边缘煤气流区域;
7.步骤三,提取边缘煤气流的温度分布特征数据来分析炉衬蚀损情况;
8.步骤四,提取炉壳表面特征对边缘煤气流特征数据进行补偿,融合多种特征分析炉衬蚀损程度;
9.步骤五,通过图像处理技术提取炉体表面裂纹特征向量;
10.步骤六,结合高炉炉衬蚀损程度及高炉炉表裂纹程度特征,构建高炉损坏程度分析模型。
11.优选地,所述步骤一中炉口耐高温红外相机位于炉口边,采集炉内红外图像数据;同时在高炉四周布置多个工业ccd相机,相机高度位于炉体中间,对相机位置进行调整并固定,相邻相机之间拍摄范围有部分重合区域。
12.优选地,所述步骤二中采用语义感知网络对炉内红外图像进行分割检测,首先人工制作标签数据,将边缘煤气流区域像素标注为1,其他区域像素标注为0,像素的标注需要根据人为经验进行标注;然后将图像数据以及标签数据均输入网络模型中,采用交叉熵损失函数对网络进行迭代训练。
13.优选地,所述步骤三中获取炉内语义感知效果图后,将其作为掩膜,获取边缘煤气
流的ir图像,得到边缘煤气流的温度分布情况,计算边缘煤气流区域的温度分布均值作为分析高炉炉衬蚀损度的特征数据。
14.优选地,所述步骤四中对相机采集的图像进行去噪以及消除模糊处理后,对各帧图像设置roi区域1为图像中的炉体炉腹部分,将炉体的炉腹发红度作为炉衬蚀损度分析的特征数据;炉腹发红度评估具体过程为:首先对所提取的roi区域1进行通道分离,获取roi区域1的r通道,计算该通道分量,记为r
n
,代表第n帧图像中的roi区域1的r通道分量值,构建高炉炉壳发红度的评估模型,分析高炉炉壳的发红程度:
[0015][0016]
其中,n为所选帧数,r
n
代表第n帧图像中roi区域1的r通道分量值,代表炉壳发红程度,炉壳图像中roi区域1的r通道分量均值越大,则认为炉壳的发红度越高;将基于此特征数据对高炉炉衬蚀损度进行分析估计,构建炉衬蚀损度分析模型,得到高炉炉衬的腐蚀情况,高炉蚀损度分析模型函数表达式为:
[0017][0018]
式中k为模型可调参数,设置k为10,c为炉内炉衬的蚀损度。
[0019]
优选地,所述步骤五中首先对预处理后的炉体表面rgb图像进行分割,用像素阈值分割法将缺陷区域分割出来,再对高炉炉体裂纹缺陷程度中的裂纹占比特征、裂纹扩展性特征以及裂纹宽度特征进行评估:
[0020]
其中裂纹占比特征获取过程为:根据裂纹分割二值图获取图像中裂纹的宽度、面积,记为w
m
、s
m
,通过图像处理的方式获取裂纹区域的最小外接矩形,将最小外接矩的长宽记为l
m
、w
m
,构建裂纹占比计算模型,用于计算图像中的裂纹占比:
[0021][0022]
裂纹扩展性特征分析模型表达式为:
[0023]
式中τ
m
为第m个裂纹的扩展性;根据高炉炉表裂纹的宽度特征、裂纹占比特征及其扩展性特征,构建
[0024]
裂纹严重程度估计模型,具体函数表达式为:
[0025][0026]
式中,d
m
为第m个裂纹的严重程度,为整体分析高炉炉表的裂纹严重程度指标,将对所有的裂纹进行求和处理,得到判定整个高炉炉表裂纹严重程度指标的最终模型:
[0027][0028]
其中,m代表裂纹个数,d为整个高炉炉壳表面的裂纹严重程度指标,判定函数值越大,认为高炉炉表裂纹越严重。
[0029]
优选地,所述步骤六中结合高炉炉衬蚀损程度及高炉炉表裂纹严重程度,构建高炉损坏程度分析模型为:
[0030][0031]
式中,α、β权重值且α+β=1,权重值的分配实施者可自行选取,本发明设置为α=0.5、β=0.5,δ代表高炉炉体损坏程度指标,所述模型函数值越大,则认为高炉炉体损坏程度越高,设高炉炉体损坏程度预设程度阈值δ
t
,当高炉炉体损坏程度指标高于所设程度阈值时,即δ>δ
t
,将认为高炉炉体损坏程度较大,系统将作出相应预警维修提示。
[0032]
与现有技术相比,本发明基于人工智能及图像处理的高炉损坏分析方法具有以下优点:采用人工智能的方法,通过高炉炉体以及炉内状况,分析高炉破损程度评价指标,便于冶炼厂操作人员实时掌控高炉状态,避免因高炉出现状况而引起的安全事故发生。主要通过高炉炉体自身情况来分析其破损程度,针对炉料等对炉内的机械冲刷作用不做考虑。
[0033]
针对高炉破损程度,结合炉衬、炉壳以及炉体表面缺陷特征,构建数学模型,并基于此模型对高炉破损程度进行分析。不仅能够实时可靠监测高炉破损程度,大幅度降低大修投资,提高经济效益,辅助高炉运维,便于工作人员实时了解高炉损坏程度,并及时采取有效措施,有效提高高炉生产效率,延长高炉寿命。
附图说明
[0034]
图1是本发明的系统流程图。
具体实施方式
[0035]
下面结合附图和具体实施方式对基于人工智能及图像处理的高炉损坏分析方法作进一步说明:为了让本领域技术人员更好的理解下面结合实施例和附图对展开描述,参见图1。
[0036]
步骤一,首先在炉口安装防高温红外相机,对炉内进行图像采集,在高炉旁边布置多个耐高温ccd相机,用于采集高炉炉表图像。
[0037]
通过炉口耐高温红外相机采集炉内图像,所述相机位于炉口边,图像采集前对相机位置进行调整,以便拍摄完整炉内图像,相机位置调好后将其固定,用于采集炉内红外图像数据。同时在高炉四周布置多个工业ccd相机,相机高度位于炉体中间,对相机位置进行调整并固定,保证相机在采集过程中不会出现抖动现象,且相邻相机之间拍摄范围有少量的重合区域,以便采集完整的炉体表面图像。
[0038]
步骤二,将红外相机采集的红外图像送入训练好的语义感知网络,以获取炉内边缘煤气流区域。为识别炉内边缘煤气流区域及检测其分布情况,采用语义感知网络对炉内红外图像进行分割检测。
[0039]
对于语义感知网络的训练,首先人工制作标签数据,将边缘煤气流区域像素标注为1,其他区域像素标注为0,像素的标注需要根据人为经验进行标注。然后将图像数据以及标签数据均输入网络模型中,采用交叉熵损失函数对网络进行迭代训练。
[0040]
至此,经训练完成的语义感知网络,可从炉内红外图像中获取边缘煤气流区域感知图。
[0041]
步骤三,首先提取炉内边缘煤气流区域,并获取边缘煤气流的温度分布特征,用于后续系统分析炉衬蚀损情况。
[0042]
边缘煤气流分布状态直接影响高炉内侧炉衬的使用情况,炉内边缘煤气流过于发展时,会使得炉衬表面温度增加,造成炉衬局部过热受损,加重炉衬侵蚀和金属渗透。因此,将通过炉内边缘煤气流发展分布情况分析高炉炉衬蚀损度。
[0043]
获取炉内语义感知效果图后,将其作为掩膜,基于此获取边缘煤气流的ir图像,进一步得到边缘煤气流的温度分布情况。计算边缘煤气流区域的温度分布均值并将其作为分析高炉炉衬蚀损度的特征。
[0044]
步骤四:为提高系统准确度,将提取高炉炉壳表面特征,根据炉表发红度进一步分析高炉内部的炉衬蚀损度。
[0045]
由于炉内反应过程复杂,且炉内边缘煤气流及中心煤气流的区域分界不够明显,易造成边缘煤气流区域提取出现误差,因此仅通过边缘煤气流发展状态,不足以准确判断炉衬蚀损度,为提高系统检测炉衬腐蚀度的精度,将结合炉壳情况对炉内炉衬进一步分析。
[0046]
首先采用多个耐高温工业相机进行炉体表面图像采集,相机高度位于炉体中间,对相机位置进行调整,以便炉体炉腹与相机高度大概一致,考虑到高炉冶炼环境较为恶劣,存在大量烟尘,导致图像出现很多噪声,对相机采集的图像进行去噪以及消除模糊处理。具体的去噪以及消除图像模糊的方法有很多,实施者可自行选取,不做一一阐述。
[0047]
对图像进行预处理之后,将对各帧图像设置roi区域1,考虑到高炉在使用过程中,由于高炉内部炉衬的情况不同,炉体表面炉腹会出现不同程度的发红,因此,所述roi区域1为图像中的炉体炉腹部分,将炉体的炉腹发红度作为炉衬蚀损度分析的特征数据。
[0048]
所述炉腹发红度评估具体过程为:首先对所提取的roi区域1进行通道分离,获取roi区域1的r通道,计算该通道分量,记为r
n
,代表第n帧图像中的roi区域1的r通道分量值,构建高炉炉壳发红度的评估模型,分析高炉炉壳的发红程度:
[0049][0050]
其中,n为所选帧数,r
n
代表第n帧图像中roi区域1的r通道分量值,代表炉壳发红程度,炉壳图像中roi区域1的r通道分量均值越大,则认为炉壳的发红度越高。
[0051]
至此,即可得到炉壳发红度以及炉内边缘煤气流的温度均值,将基于此特征数据对高炉炉衬蚀损度进行分析估计,构建炉衬蚀损度分析模型,得到高炉炉衬的腐蚀情况。所述高炉蚀损度分析模型函数表达式为:
[0052][0053]
式中,k为模型可调参数,设置k为10,c为炉内炉衬的蚀损度。
[0054]
步骤五:炉体表面状况也是体现高炉破损程度的重要特征,采用工业相机拍摄高炉炉表图像,并通过图像处理技术提取炉体表面裂纹特征,分析高炉炉表的裂纹严重程度指标,用于后续分析最终的高炉损坏情况。
[0055]
主要目的是分析高炉的损坏程度,高炉损坏主要体现在高炉炉内以及高炉炉表的损坏,因此,为全面分析高炉损坏情况,将对高炉炉表情况进行判断分析。
[0056]
所述高炉炉表分析主要分析高炉炉表的裂纹现象。高炉在使用过程中由于高温冶炼等操作会导致高炉炉表出现开裂、裂纹等缺陷,为分析高炉炉表状况,首先对预处理后的炉体表面rgb图像进行分割,将缺陷区域分割出来,用于后续分析裂纹程度。所述裂纹区域
分割为像素阈值分割法,对高炉炉表图像设置像素阈值,基于像素阈值对裂纹区域进行分割,图像分割算法较为成熟且为常规技术,具体分割方法实施者自行选取,不在保护范围内,不做详细描述。
[0057]
至此,即可获取各炉表裂纹区域。
[0058]
为对高炉炉体裂纹缺陷程度进行评估,将提取高炉炉体缺陷特征,用于后续对高炉裂纹严重程度进行分析判断。所述高炉炉表缺陷特征主要包括:裂纹占比特征、裂纹扩展性特征以及裂纹宽度特征。
[0059]
所述裂纹占比特征会获取过程具体为:根据裂纹分割二值图获取图像中裂纹的宽度、面积,记为w
m
、s
m
。裂纹宽度用于作为裂纹的宽度特征。通过图像处理的方式获取裂纹区域的最小外接矩形,将最小外接矩的长宽记为l
m
、w
m
,构建裂纹占比计算模型,用于计算图像中的裂纹占比:
[0060][0061]
所述裂纹扩展性特征具体分析过程为:为体现高炉炉体的裂纹等级,准确分析高炉裂纹的严重程度,将构建裂纹扩展性特征分析模型,对高炉裂纹向四周扩展的可能性进行分析,所述炉表裂纹扩展性特征分析模型表达式为:
[0062][0063]
式中τ
m
为第m个裂纹的扩展性。
[0064]
最终根据高炉炉表裂纹的宽度特征(即裂纹宽度)、裂纹占比特征及其扩展性特征,对裂纹严重程度进行评估分析。构建裂纹严重程度估计模型,具体函数表达式为:
[0065][0066]
式中,d
m
为第m个裂纹的严重程度,为整体分析高炉炉表的裂纹严重程度指标,将对所有的裂纹进行求和处理,得到判定整个高炉炉表裂纹严重程度指标的最终模型:
[0067][0068]
其中,m代表裂纹个数,d为整个高炉炉壳表面的裂纹严重程度指标。判定函数值越大,认为高炉炉表裂纹越严重。
[0069]
至此,根据所述方法可获取高炉炉内炉衬蚀损度以及高炉炉体表面裂纹的严重程度。
[0070]
步骤六:结合高炉炉衬蚀损程度以及高炉炉表裂纹严重程度,构建高炉损坏程度分析模型,基于此模型对高炉整体损坏程度进行评估。
[0071]
最后,将基于高炉炉衬以及炉表情况对整个高炉炉体的损坏程度进行分析判断,以便工作人员实时掌握高炉使用情况。所述高炉炉体损坏程度分析模型为:
[0072][0073]
式中,α、β权重值且α+β=1,权重值的分配实施者可自行选取,设置为α=0.5、β=0.5,δ代表高炉炉体损坏程度指标,所述模型函数值越大,则认为高炉炉体损坏程度越高。
[0074]
至此,实施者可基于本系统对高炉炉体情况进行实时掌握,为避免高炉炉体损坏程度过大,而导致的冶炼过程中安全问题以及产品质量下降等问题,将对高炉炉体损坏程度预设程度阈值δ
t
。当高炉炉体损坏程度指标高于所设程度阈值时,也即δ>δ
t
,将认为高炉炉体损坏程度较大,系统将作出相应预警提示,及时提示维修人员尽快对高炉炉况进行检测维修,必要时进行高炉零件更换,以防高炉损坏程度过高引起安全事故等问题。
[0075]
综上所述,本发明提出一种基于人工智能及图像处理的高炉破损分析系统。首先通过炉口处的防高温工业相机采集炉内图像,对图像进行滤波处理,炉内边缘煤气流发展过盛时会加重炉衬渣侵蚀和金属渗透,并容易造成炉衬局部过热烧穿,因此本发明结合炉内边缘煤气流特征向量以及炉壳发红程度特征,分析炉衬蚀损度。同时在高炉外部采用多相机采集高炉炉表图像,对炉表rgb图像进行处理,提取炉体表面缺陷特征,分析炉体裂纹程度。基于炉表裂纹程度特征以及炉衬蚀损度构建数学模型,实时检测高炉损坏程度,为高炉运维提供数据分析,以便及时提示工作人员对高炉检测相应检测维修,延长高炉寿命。