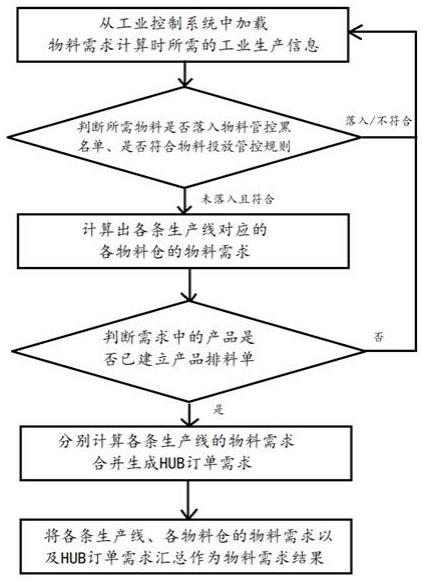
1.本发明涉及一种智能化的物料需求计算系统及其相对应的方法,具体涉及一种基于生产计划的物料需求计算系统与方法,属于工业自动化领域。
背景技术:2.在工业生产、特别是电子制造行业中,对于物料需求的计算和管理是企业内管理人员每日的必要工作。在现阶段的实际应用中,对于物料需求的计算主要还是以人工操作为主,大体包含以下几个步骤:s1、由人工建立报表,设置维护基础信息,如维护产品bom(bill of material,物料清单)、排料单、最小包装、期初在制等,并嵌入相应的公式。
3.s2、根据日计划生产产品,人工计算出物料需求数量,计算步骤至少包含:a、输入每条生产线的计划产能及对应产品的bom;b、将每条生产线的计划产能与产品的bom相乘;c、调整各条生产线的剩余安排接料数;d、调整黑名单管控物料。
4.s3、对物料需求数量进行汇总,并拆分各库位(各条生产线及中转仓)的物料需求;s4、人工核对中转仓内的订单物料是否有相应配额,随后人工上传订单至sap(systems applications and products in data processing,企业管理解决方案)系统。
5.由上述操作流程可以直观地看出,现有技术中存在着多需要改进之处,具体可以归纳为以下几个问题点:1、人工计算物料需求耗时耗力且计算结果受操作者主观因素影响大、数据准确性难以保证;2、涉及到一些较为复杂的工况、例如双站点线体时,极易出现物料少进或多进的情况;3、对于操作流程中黑名单物料的使用完全依赖人工干预,增加了生产企业内管理人员的工作量;4、由于无法对生产线内抛料及挪料的情况进行实时监控,因此各条生产线物料在制的准确性难以保证;5、无法实时监控退仓物料,从而进一步影响了计算结果的准确性。
6.综上所述,如何在提出一种在电子制造行业中适用的、基于生产计划的物料需求计算系统与方法,以克服现有技术中所存在的上述缺陷,也就成为了本领域内技术人员所亟待解决的问题。
技术实现要素:7.鉴于现有技术存在上述缺陷,本发明的目的是提出一种基于生产计划的物料需求计算系统与方法,具体方案如下。
8.一种基于生产计划的物料需求计算系统,包括:生产信息加载模块,与工业控制系统信号连接,用于从所述工业控制系统中加载
物料需求计算时所需的工业生产信息,并将所加载的工业生产信息进行下发;物料需求计算模块,分别与所述生产信息加载模块及工业仓储系统信号连接,用于接收其所加载的工业生产信息,经过分析计算后得到物料需求结果,并将所得到的物料需求结果发送至所述工业仓储系统中;所述工业生产信息至少包含各条生产线的计划工单数、各条生产线的日计划产品排料单、所述工业控制系统中的在制数据、各物料仓的库存在制数据、物料主档中的最大包装、物料最小抛料率、物料管控黑名单以及物料投放管控规则;所述物料需求计算模块具体包括,信息接收与判定单元,与所述生产信息加载模块信号连接,用于接收其所加载的工业生产信息,并依据所述工业生产信息判断所需物料是否合规,若合规则转发所述工业生产信息,若不合规则上传指令至所述生产信息加载模块、重新加载工业生产信息,物料需求计算单元,与所述信息接收与判定单元及工业仓储系统信号连接,用于依据所述工业生产信息计算得出物料需求结果,并将所得到的物料需求结果发送至所述工业仓储系统中;所述物料需求结果包括各条生产线、各物料仓的物料需求以及hub订单需求。
9.优选地,所述工业控制系统为mes系统,所述工业仓储系统包括sap系统及infor系统。
10.一种基于生产计划的物料需求计算系统,使用如上所述的基于生产计划的物料需求计算系统,包括如下步骤:s1、生产信息加载,从工业控制系统中加载物料需求计算时所需的工业生产信息,并将所加载的工业生产信息进行下发;s2、物料需求计算,接收所加载的工业生产信息,经过分析计算后得到物料需求结果,并将所得到的物料需求结果发送至工业仓储系统中。
11.优选地,s1具体包括如下步骤:从工业控制系统中加载物料需求计算时所需的工业生产信息,所述工业控制系统为mes系统,所述工业生产信息至少包含各条生产线的计划工单数、各条生产线的日计划产品排料单、所述工业控制系统中的在制数据、各物料仓的库存在制数据、物料主档中的最大包装、物料最小抛料率、物料管控黑名单以及物料投放管控规则,随后将所加载的工业生产信息进行下发。
12.优选地,s2具体包括如下步骤:s21、接收所述工业生产信息,并依据所述工业生产信息判断所需物料是否落入物料管控黑名单、是否符合物料投放管控规则,若未落入物料管控黑名单且符合物料投放管控规则转发所述工业生产信息,否则跳转返回s1、重新加载工业生产信息;s22、依据各条生产线的计划工单数及各条生产线的日计划产品排料单,计算出各条生产线对应的各物料仓的物料需求;s23、依据物料仓的物料需求,判断需求中的产品是否已建立产品排料单,若是则按序进入s24,否则跳转返回s1、重新加载工业生产信息;s24、依据所述工业生产信息,分别计算各条生产线的物料需求;s25、将各条生产线、各物料仓的物料需求以及hub订单需求汇总作为物料需求结
果,并将所得到的物料需求结果发送至所述工业仓储系统中,所述工业仓储系统包括sap系统及infor系统,由sap系统自动匹配物料的配额问题,由infor系统依据物料需求结果生成最终的物料需求订单。
13.优选地,s22中各物料仓的物料需求的计算公式为:物料仓的物料需求=生产线的计划工单数*生产线的日计划产品排料单。
14.优选地,s24中各条生产线的物料需求的计算公式为:生产线的物料需求=生产线的计划工单数*生产线的日计划产品排料单*物料主档中的最大包装*物料最小抛料率
‑
工业控制系统中的在制数据,随后将各条生产线的物料需求合并生成hub订单需求。
15.与现有技术相比,本发明的优点主要体现在以下几个方面:本发明所提供的一种基于生产计划的物料需求计算系统,充分地利用了生产企业中现有的工业控制系统,以自动化的方式完成了对于生产过程中物料需求的计算,不仅减少了人工作业的工时、降低了企业的人力投入成本,而且避免了计算过程中的数据错误、显著地提升了计算结果的准确性。
16.与系统相对应的,本发明所提供的一种基于生产计划的物料需求计算方法,使得生产企业对于工业控制系统的智能化应用水平得到了进一步提升,实现了对于各生产线、个库存内在制分布的精确监控,保证了物料需求计算的期初准确性。
17.以下便结合实施例附图,对本发明的具体实施方式作进一步的详述,以使本发明技术方案更易于理解、掌握。
附图说明
18.图1为本发明系统的方法流程示意图。
具体实施方式
19.本发明提供了一种基于生产计划的物料需求计算系统与方法,具体方案如下。
20.一种基于生产计划的物料需求计算系统,包括如下模块。
21.生产信息加载模块,与工业控制系统信号连接,所述工业控制系统为mes系统,在实际设置时,可以将所述生产信息加载模块集成于mes系统中。所述生产信息加载模块用于从所述工业控制系统中加载物料需求计算时所需的工业生产信息,并将所加载的工业生产信息进行下发。
22.物料需求计算模块,分别与所述生产信息加载模块及工业仓储系统信号连接,所述工业仓储系统包括sap系统及infor系统,同样的,在实际设置时,仍然可以将所述物料需求计算模块集成于mes系统中、只需要保证其与sap系统及infor系统信号连接即可。所述物料需求计算模块用于接收其所加载的工业生产信息,经过分析计算后得到物料需求结果,并将所得到的物料需求结果发送至所述工业仓储系统中;此处所述工业生产信息至少包含各条生产线的计划工单数、各条生产线的日计划产品排料单、所述工业控制系统中的在制数据、各物料仓的库存在制数据、物料主档中的最大包装、物料最小抛料率、物料管控黑名单以及物料投放管控规则。
23.其中,所述物料需求计算模块具体包括:信息接收与判定单元,与所述生产信息加载模块信号连接,用于接收其所加载的
工业生产信息,并依据所述工业生产信息判断所需物料是否合规,若合规则转发所述工业生产信息,若不合规则上传指令至所述生产信息加载模块、重新加载工业生产信息。
24.物料需求计算单元,与所述信息接收与判定单元及工业仓储系统信号连接,用于依据所述工业生产信息计算得出物料需求结果,并将所得到的物料需求结果发送至所述工业仓储系统中;此处所述物料需求结果包括各条生产线、各物料仓的物料需求以及hub订单需求。
25.相较于现有技术,本发明的系统具有以下几个方面的优点:1、能够减少人工作业的工时;2、能够更精确地计算生产线上的物料需求;3、能够更精准地监控各条生产线、各库存的在制分布,保证系统计算物料需求的期初准确性;4、能够更好的监控生产线抛料及挪料的情况,并更好地监控黑名单物料的投入及使用情况;综上所述,本发明所提供的一种基于生产计划的物料需求计算系统,充分地利用了生产企业中现有的工业控制系统,以自动化的方式完成了对于生产过程中物料需求的计算,不仅减少了人工作业的工时、降低了企业的人力投入成本,而且避免了计算过程中的数据错误、显著地提升了计算结果的准确性。
26.如图1所示,本发明还提出了一种基于生产计划的物料需求计算系统,使用如上所述的基于生产计划的物料需求计算系统,其特征在于,包括如下步骤:s1、生产信息加载,从工业控制系统中加载物料需求计算时所需的工业生产信息,并将所加载的工业生产信息进行下发。
27.这一步骤具体为,从工业控制系统中加载物料需求计算时所需的工业生产信息,所述工业控制系统为mes系统,所述工业生产信息至少包含各条生产线的计划工单数、各条生产线的日计划产品排料单、所述工业控制系统中的在制数据、各物料仓的库存在制数据(由mes系统自动拆解为虚拟ppid在制数据)、物料主档中的最大包装、物料最小抛料率、物料管控黑名单以及物料投放管控规则,随后将所加载的工业生产信息进行下发。
28.s2、物料需求计算,接收所加载的工业生产信息,经过分析计算后得到物料需求结果,并将所得到的物料需求结果发送至工业仓储系统中。
29.这一步骤具体包括:s21、接收所述工业生产信息,并依据所述工业生产信息判断所需物料是否落入物料管控黑名单、是否符合物料投放管控规则,若未落入物料管控黑名单且符合物料投放管控规则转发所述工业生产信息,否则跳转返回s1、重新加载工业生产信息。
30.s22、依据各条生产线的计划工单数及各条生产线的日计划产品排料单,计算出各条生产线对应的各物料仓的物料需求,计算公式为:物料仓的物料需求=生产线的计划工单数*生产线的日计划产品排料单。
31.s23、依据物料仓的物料需求,判断需求中的产品是否已建立产品排料单,若是则按序进入s24,否则跳转返回s1、重新加载工业生产信息。
32.s24、依据所述工业生产信息,分别计算各条生产线的物料需求,计算公式为:生产线的物料需求=生产线的计划工单数*生产线的日计划产品排料单*物料主档中的最大包
装*物料最小抛料率
‑
工业控制系统中的在制数据,随后将各条生产线的物料需求合并生成hub订单需求。
33.s25、将各条生产线、各物料仓的物料需求以及hub订单需求汇总作为物料需求结果,并将所得到的物料需求结果发送至所述工业仓储系统中。所述工业仓储系统包括sap系统及infor系统,由sap系统自动匹配物料的配额问题,由infor系统依据物料需求结果生成最终的物料需求订单。
34.与系统相对应的,本发明所提供的一种基于生产计划的物料需求计算方法,其核心在于利用ppid管控生产物料在制及各库存在制状态,使得生产企业对于工业控制系统的智能化应用水平得到了进一步提升,实现了对于各生产线、个库存内在制分布的精确监控,保证了物料需求计算的期初准确性。
35.此外,本发明还可以作为解决同领域内相关近似问题的参考依据,可以通过对本方案的优化、明确,拓宽其应用范围拓宽,从而进一步地丰富本方案的应用场景。
36.对于本领域技术人员而言,显然本发明不限于上述示范性实施例的细节,而且在不背离本发明的精神和基本特征的情况下,能够以其他的具体形式实现本发明。因此,无论从哪一点来看,均应将实施例看作是示范性的,而且是非限制性的,本发明的范围由所附权利要求而不是上述说明限定,因此旨在将落在权利要求的等同要件的含义和范围内的所有变化囊括在本发明内,不应将权利要求中的任何附图标记视为限制所涉及的权利要求。
37.最后,应当理解,虽然本说明书按照实施方式加以描述,但并非每个实施方式仅包含一个独立的技术方案,说明书的这种叙述方式仅仅是为清楚起见,本领域技术人员应当将说明书作为一个整体,各实施例中的技术方案也可以经适当组合,形成本领域技术人员可以理解的其他实施方式。