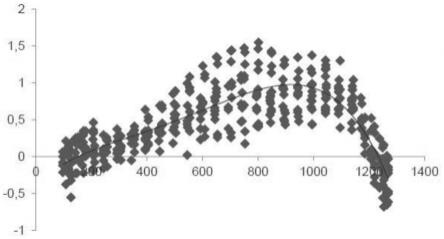
1.本发明涉及车身焊接变形评估技术领域,具体地,涉及一种车身焊接变形量的估算方法及系统。
背景技术:2.目前车身的热成型件焊接预变形量数据评估方法不适用现有的车辆生产工艺,同时无有效的测量方法来测量车身由于焊接产生的变形量,而热成型件焊接预变形量数据预测的不准确后期会产生非常大的模具更改费用,同时影响项目的进度。另一方面,在确定焊接预变形量的过程中,通常采用对建模单元的数据进行点选的方式确定焊点数据信息,因此使焊接仿真模型建模和求解过程效率低。
3.发明专利内容
4.为解决上述问题的至少一个方面,本发明提供一种车辆焊接变形量的估算方法,包括:利用建模单元获取焊接件的焊点信息,所述焊点信息包括焊点名称、焊点坐标、焊点对应的板材编号;利用耦合单元对获取的所述焊点信息进行格式转换;利用仿真单元接收格式转换后的所述焊点信息,并结合所述焊接件的材料信息、夹具信息和焊接信息确定焊接变形仿真数据,所述材料信息包括杨氏模量、泊松比、屈服强度、密度、热膨胀系数和熔点,所述夹具信息包括定位销、支撑块、夹紧块和夹紧力,所述焊接信息包括焊点顺序、焊点坐标和焊核面积;根据焊接变形仿真数据制作所述焊接件的模型,并测量所述模型焊接过程中的实际变形数据;利用计算单元根据所述模型的实际变形数据拟合所述模型的焊接变形曲线;根据所述模型的焊接变形曲线确定所述焊接件的焊接变形量。
5.优选地,根据焊接变形仿真数据制作所述焊接件的模型,并测量所述模型焊接过程中的实际变形数据的步骤包括:利用反变形法根据所述焊接件的焊接变形仿真数据对所述焊接件的结构参数进行修正,并基于修正后的结构参数制作所述焊接件的模型;在所述模型上按预设间距选择多个测量点;对所述模型的测量点在焊接后的焊接变形量进行测量,获取与所述模型的测量点坐标一一对应的焊接变形量,即所述模型的实际变形数据。
6.优选地,利用计算单元根据所述模型的实际变形数据拟合所述模型的焊接变形曲线的步骤还包括:步骤s1,根据所述模型的实际变形数据采用多项式拟合所述模型的初始焊接变形曲线;步骤s2,根据所述模型的初始焊接变形曲线确定所述模型测量点的焊接变形估值;步骤s3,设定所述模型测量点的焊接变形量与焊接变形估值之差的阈值,删除大于设定阈值的测量点;步骤s4,对删除测量点后的所述模型的实际变形数据采用多项式拟合所述模型的校正焊接变形曲线;步骤s5,根据所述模型的校正焊接变形曲线确定上基准点和下基准点的焊接变形估值,所述上基准点焊接变形估值和所述下基准点的焊接变形估值的平均值即校正值;步骤s6,利用校正值对所述模型的实际变形数据进行校正;步骤s7,对所述模型进行多次焊接和测量以获取多组实际变形数据,对所述模型的多组实际变形数据重复步骤s1-步骤s6,得到所述模型的多组校正后的实际变形数据;步骤s8,基于所述模型的多组校正后的实际变形数据进行多项式拟合,确定所述模型的焊接变形曲线。
7.优选地,对所述模型测量点在焊接后的焊接变形量进行测量,获取与所述模型的测量点坐标一一对应的焊接变形量的步骤还包括:根据所述模型的测量点坐标按照预设距离选择第一参考点和第二参考点;分别测量所述第一参考点和所述第二参考点的焊接变形量,所述第一参考点的焊接变形量和所述第二参考点的焊接变形量的平均值即所述模型的测量点坐标对应的焊接变形量。
8.优选地,所述建模单元采用catia建模软件。
9.优选地,所述仿真单元采用装配仿真软件。
10.优选地,所述耦合单元将所述catia建模软件的导出数据通过xls编辑的接口转换成所述装配仿真软件识别的格式。
11.另一方面提供了一种系统,所述系统用于实施权利如前任一所述方法,包括:建模单元,所述建模单元用于生成焊接件的焊接件的焊点信息;耦合单元,所述耦合单元用于转换所述焊点信息的数据格式;仿真单元,所述仿真单元通过所述耦合单元接收格式转换后的所述焊点信息,并结合所述焊接件的材料信息、夹具信息和焊接信息确定焊接变形仿真数据;焊接件模型,所述焊接件模型用于根据所述仿真单元的所述焊点信息、所述焊接件的材料信息、所述夹具信息和所述焊接信息实施焊接,并确定实际变形数据;计算单元,所述计算单元用于接收所述模型的实际变形数据并拟合所述模型的焊接变形曲线,并根据所述模型的焊接变形曲线确定所述焊接件的焊接变形量。
12.本发明实施例的一种车辆焊接变形量的估算方法及系统有如下有益效果:
13.(1)通过在仿真单元中结合焊接件的材料信息、夹具信息和焊接信息充分考虑了焊接件自重引起的变形量;同时通过基于仿真单元的反变形法制作焊接件的模型,以降低仿真模型与现场实际的差异问题引起的误差,并提高焊接变形量的估算准确性。
14.(2)通过测量焊接件模型的实际变形数据并结合计算单元,以排除车身整体偏差、焊点影响、测量位置等导致的测量误差,提高对车身焊接引起的变形量的预测准确度。
附图说明
15.为了更好地理解本发明的上述及其他目的、特征、优点和功能,可以参考附图中所示的实施方式。附图中相同的附图标记指代相同的部件。本领域技术人员应该理解,附图旨在示意性地阐明本发明的优选实施方式,对本发明的范围没有任何限制作用,图中各个部件并非按比例绘制。
16.图1示出了根据本发明实施例的车辆焊接变形量的估算方法的示例焊接件结构示意图;
17.图2示出了根据本发明实施例的车辆焊接变形量的估算方法的示例焊接件的测量点取点示意图;
18.图3示出了根据本发明实施例的车辆焊接变形量的估算方法的示例焊接件的测量点第一参考点和第二参考点示意图;
19.图4示出了根据本发明实施例的车辆焊接变形量的估算方法的示例初始焊接变形曲线;
20.图5示出了根据本发明实施例的车辆焊接变形量的估算方法的示例校正焊接变形曲线;
21.图6示出了根据本发明实施例的车辆焊接变形量的估算方法的示例焊接变形曲线。
22.附图标记说明:
23.1、内板;2、外板;10、b柱;101、测量点。
具体实施方式
24.以下结合附图对本公开的示范性实施例做出说明,其中包括本公开实施例的各种细节以助于理解,应当将它们认为仅仅是示范性的。因此,本领域普通技术人员应当认识到,可以对这里描述的实施例做出各种改变和修改,而不会背离本公开的范围和精神。同样,为了清楚和简明,以下的描述中省略了对公知功能和结构的描述。
25.在本文中使用的术语“包括”及其变形表示开放性包括,即“包括但不限于”。除非特别申明,术语“或”表示“和/或”。术语“基于”表示“至少部分地基于”。术语“一个示例实施例”和“一个实施例”表示“至少一个示例实施例”。术语“另一实施例”表示“至少一个另外的实施例”。术语“第一”、“第二”等等可以指代不同的或相同的对象。下文还可能包括其他明确的和隐含的定义。
26.为了至少部分地解决上述问题以及其他潜在问题中的一个或者多个,本公开的一个实施例提出了一种车辆焊接变形量的估算方法,包括:利用建模单元获取焊接件的焊点信息,焊点信息包括焊点名称、焊点坐标、焊点对应的板材编号;利用耦合单元对获取的焊点信息进行格式转换;利用仿真单元接收格式转换后的焊点信息,并结合焊接件的材料信息、夹具信息和焊接信息确定焊接变形仿真数据,材料信息包括杨氏模量、泊松比、屈服强度、密度、热膨胀系数和熔点,夹具信息包括定位销、支撑块、夹紧块和夹紧力,焊接信息包括焊点顺序、焊点坐标和焊核面积;根据焊接变形仿真数据制作焊接件的模型,并测量模型焊接过程中的实际变形数据;利用计算单元根据模型的实际变形数据拟合模型的焊接变形曲线;根据模型的焊接变形曲线确定焊接件的焊接变形量。
27.具体地,以车辆b柱10为例对本发明的车辆焊接变形量的估算方法进行说明,如图1和图2所示,b柱10包括内板1和外板2。首先采用建模单元根据b柱10的结构参数进行建模,同时由建模单元生成b柱10的焊点信息文件,焊点信息文件包括b柱10上焊点名称进行编号,按照b柱10所在的坐标系确定焊点坐标,同时确定焊点作用的板材编号,例如,包括内板1和外板2,即该焊点用于固定连接内板1和外板2,本领域技术人员可以理解地,焊点对应的板材编号还可以包括内板1、外板2和填充层。
28.本实施例中,建模单元采用catia建模软件,生成包括焊点名称、焊点坐标、焊点对应板材名称、焊点对应板材数量说明的文件。耦合单元用于连接建模单元和仿真单元,仿真单元采用visual assembly仿真软件,耦合单元将catia建模软件的导出数据通过xls编辑的接口转换成装配仿真软件识别的格式。使仿真单元可以通过耦合单元直接采用catia建模软件生成的包含b柱10的焊点信息文件,以通过仿真单元对焊点信息的全部接收代替现有技术中通过点选的方式获取焊点信息的方式,以提高仿真单元对仿真结果的精度。仿真单元通过结合b柱10实际焊接过程中的焊接顺序、内板1和外板2的材料特征和辅助焊接的夹具信息对b柱10的焊接过程进行仿真,并输出b柱10的焊接变形仿真数据。
29.通过焊接变形仿真数据对建模单元采用的b柱10的结构参数进行修正,根据修正
后的结构参数制作b柱10的模型件,然后按照实际生产工艺流程对b柱模型,对制作的b柱模型进行焊接操作并测量焊接过程中的实际焊接变形数据,即实际焊接变形量与焊点坐标一一对应的数据集合。根据实际焊接变形数据,以焊点坐标为横坐标以实际焊接变形量为纵坐标拟合b柱模型的焊接变形曲线。根据b柱10模型的焊接变形曲线确定的焊接变形量,即b柱10的焊接变形量估算结果,以估算结果为参考对批量生产的b柱结构参数进行修正,以降低或避免焊接变形对实际生产质量的影响。
30.在一些实施例中,根据焊接变形仿真数据制作焊接件的模型,并测量模型焊接过程中的实际变形数据的步骤包括:利用反变形法根据焊接件的焊接变形仿真数据对焊接件的结构参数进行修正,并基于修正后的结构参数制作焊接件的模型;在模型上按预设间距选择多个测量点;对模型的测量点在焊接后的焊接变形量进行测量,获取与模型的测量点坐标一一对应的焊接变形量,即模型的实际变形数据。
31.具体地,利用反变形法对b柱10的结构参数进行修正,例如,当焊接变形仿真数据显示b柱在焊接过程中向内弯曲时,增加b柱模型向内的曲率半径。如图2所示,对b柱模型按照预设间距5cm在前后法兰边选择多组测量点101,在b柱模型的每一阶段的焊接过程中针对测量点的焊接变形量进行测量,以模型测量点在空间坐标系的z轴坐标和其对应的焊接变形量确定模型的实际变形数据。本领域技术人员可以理解地,在其他的实施例中,实际变形数据中测量点的坐标还可以是焊接件所在空间坐标系的x轴坐标或者y轴坐标,或者在另外的实施例中,测量点的坐标还可以是焊接件所在空间坐标系的x轴坐标、y轴坐标和z轴坐标中的任意一个或者多个的组合,坐标的选择以按照焊接变形的趋势为参考。
32.在一些实施例中,对模型测量点在焊接后的焊接变形量进行测量,获取与模型的测量点坐标一一对应的焊接变形量的步骤还包括:根据模型的测量点坐标按照预设距离选择第一参考点和第二参考点;分别测量第一参考点和第二参考点的焊接变形量,第一参考点的焊接变形量和第二参考点的焊接变形量的平均值即模型的测量点坐标对应的焊接变形量。
33.具体地,如图2和图3所示,以b柱模型的aa向视图为例对测量点101的焊接变形量测量数据的确定为例进行说明。在每个测量点选择两个参考点,设定两个参考点与法兰边两侧的距离d相等,其中第一参考点b距离法兰边边缘3mm,第二参考点c距离法兰边拐角3mm。其中第一参考点b的焊接变形量为该参考点在b柱模型所在空间坐标系的y轴坐标的焊接前后的差值,该测量的点的焊接变形量为第一参考点b和第二参考点c的焊接变形量的平均值。b柱的模型的实际变形数据即为包括b柱模型的测量点z轴坐标及其对应焊接变形量的集合。
34.在一些实施例中,利用计算单元根据模型的实际变形数据拟合模型的焊接变形曲线的步骤还包括:
35.步骤s1,根据模型的实际变形数据采用多项式拟合模型的初始焊接变形曲线。
36.具体地,如图4和表1所示,以b柱模型的测量点z轴坐标为自变量,以该测量点的焊接变形量为因变量进行多项式拟合,以得到b柱模型的初始焊接变形曲线。
37.y=-1.5645315076
×
10-11
x4+3.6760895466
×
10-8
x
3-2.9028901012
×
10-5
x2+0.0101608046x-1.0696164718
38.步骤s2,根据模型的初始焊接变形曲线确定模型测量点的焊接变形估值。
39.具体地,基于b柱模型的测量点坐标,根据初始焊接变形曲线确定b柱模型测量点的焊接变形估值。
40.步骤s3,设定模型测量点的焊接变形量y
测
与焊接变形估值y
拟
之差δy的阈值,删除大于设定阈值的测量点。
41.如表1所示,通过设定阈值对b柱模型的实际变形数据进行筛选,判断当测量点的焊接变形量y
测
与焊接变形估值y
拟
之差δy大于设定阈值(例如,设定阈值为0.3),该测量点为无效测量点,则从实际变形数据中删除该无效测量点,例如,z轴坐标为744的测量点d,以降低由于测量误差对估算精度的影响。
42.表1.b柱模型的实际测量数据
[0043][0044][0045]
步骤s4,对删除测量点后的模型的实际变形数据采用多项式拟合模型的校正焊接变形曲线。
[0046]
具体地,如图5所示,根据删除无效测量点d后b柱模型的实际变形数据重新进行多项式拟合校正焊接变形曲线。
[0047]
y=-1.4073424173
×
10-11
x4+3.2276844722
×
10-8
x
3-2.4884578054
×
10-5
x2+0.0088206941017x-0.94804751604
[0048]
步骤s5,根据模型的校正焊接变形曲线确定上基准点和下基准点的焊接变形估值,上基准点焊接变形估值和下基准点的焊接变形估值的平均值即校正值。
[0049]
具体地,总成焊接可能导致车身尺寸整体变化从而整体影响计算出的热变形量,设定b柱模型的上下两基准点热变形理论值为零。在本实施例中,通过校正焊接变形曲线计算上基准点和下基准点的焊接变形估值分别为0.0520和-0.0735,进一步确定校正值为-0.01085。
[0050]
步骤s6,利用校正值对模型的实际变形数据进行校正。具体地,如表2所示,对删除无效测量点的b柱模型的实际变形数据根据校正值进一步校正,即用y
测
减校正值得到y
校
。
[0051]
表2.实际变形数据校正表
[0052]
zy
测y校
1254.05-0.105-0.0941249.42-0.04-0.02911750.510.52110970.90.91110441.2951.3069951.3651.3768941.231.2418440.750.7617950.80.8116460.610.6215470.680.6914990.510.5214440.360.3713950.3350.3463440.240.2512940.1950.2062120.0250.0361800.060.071127-0.255-0.244
[0053]
步骤s7,对模型进行多次焊接和测量以获取多组实际变形数据,对模型的多组实际变形数据重复步骤s1-步骤s6,得到模型的多组校正后的实际变形数据。
[0054]
具体地,针对b柱模型在多个车辆模型的焊接过程进行测量以获取多组实际变形数据,或者在另外的实施例中,制作多个相同的b柱模型进行相同的前述焊接过程以获取多组实际变形数据,对获取的b柱模型的多组实际变形数据重复进行步骤s1-步骤s6的数据处理步骤,保留每一组的校正实际变形数据。
[0055]
步骤s8,基于模型的多组校正后的实际变形数据进行多项式拟合,确定模型的焊接变形曲线。
[0056]
如图6所示,根据b柱模型的多组校正后的实际变形数据进行多项式拟合得到b柱模型的焊接变形曲线。将b柱模型的焊点坐标带入最终确定的焊接变形曲线得到焊接变形量即为根据本估算方法确定的b柱的焊接变形量。
[0057]
另一方面提供了一种系统,系统用于实施权利如前任一方法,包括:建模单元,建模单元用于生成焊接件的焊接件的焊点信息;耦合单元,耦合单元用于转换焊点信息的数据格式;仿真单元,仿真单元通过耦合单元接收格式转换后的焊点信息,并结合焊接件的材料信息、夹具信息和焊接信息确定焊接变形仿真数据;焊接件模型,焊接件模型用于根据仿真单元的焊点信息、焊接件的材料信息、夹具信息和焊接信息实施焊接,并确定实际变形数据;计算单元,计算单元用于接收模型的实际变形数据并拟合模型的焊接变形曲线,并根据模型的焊接变形曲线确定焊接件的焊接变形量。
[0058]
具体地,建模单元、耦合单元、仿真单元和计算单元为具有执行上述方法的程序指令的计算机可识别介质,焊接件模型为基于车身结构数据、建模单元和仿真单元的确定的仿真数据制造的车身部件模型。
[0059]
以上已经描述了本公开的各实施例,上述说明是示例性的,并非穷尽性的,并且也不限于所披露的各实施例。在不偏离所说明的各实施例的范围和精神的情况下,对于本技术领域的普通技术人员来说许多修改和变更都是显而易见的。本文中所用术语的选择,旨在最好地解释各实施例的原理、实际应用或对市场中的技术改进,或者使本技术领域的其它普通技术人员能理解本文。