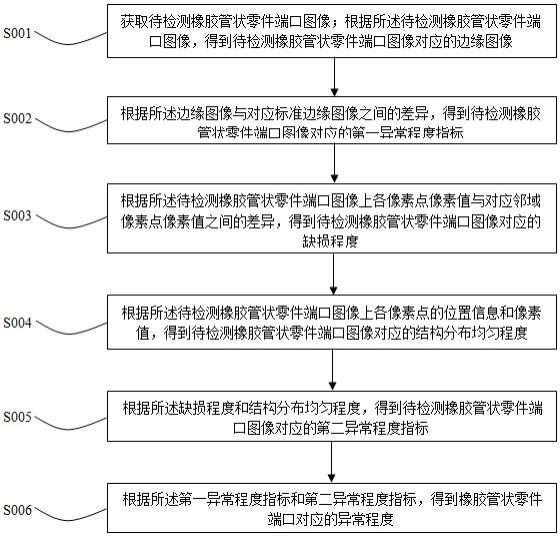
1.本发明涉及管状零件端口异常检测技术领域,具体涉及一种基于图像处理的管状零件端口异常检测方法及系统。
背景技术:2.随着我国机械化水平的提高以及新材料的应用,橡胶管状零件广泛应用于机械以及制造领域;橡胶管构成的橡胶管状零件具有耐冲压、耐磨等性能;由于橡胶管状零件一般用于零件之间的连接,而当橡胶管状零件端口出现严重变形或者其它缺陷时,会导致零件之间连接的密封性出现异常,且密封性出现异常可能会引起不可预测的事故或者后果。
3.现有的橡胶管状零件端口异常检测方法一般是基于人工检测,而通过人工检测橡胶管状零件端口异常的方式主观性较强,一般只能在端口出现较明显的变形或者缺陷时才能发现异常,很容易将一些已经出现轻微变形或者缺陷且影响零件之间连接的密封性的橡胶管状零件端口判定为正常的橡胶管状零件,对橡胶管状零件端口异常检测结果不够准确。
技术实现要素:4.本发明提供一种基于图像处理的管状零件端口异常检测方法及系统,用于解决现有不能准确检测管状零件端口异常的问题,所采用的技术方案具体如下:第一方面,本发明一个实施例提供了一种基于图像处理的管状零件端口异常检测方法及系统包括以下步骤:获取待检测橡胶管状零件端口图像;根据所述待检测橡胶管状零件端口图像,得到待检测橡胶管状零件端口图像对应的边缘图像;根据所述边缘图像与对应标准边缘图像之间的差异,得到待检测橡胶管状零件端口图像对应的第一异常程度指标;根据所述待检测橡胶管状零件端口图像上各像素点像素值与对应邻域像素点像素值之间的差异,得到待检测橡胶管状零件端口图像对应的缺损程度;根据所述待检测橡胶管状零件端口图像上各像素点的位置信息和像素值,得到待检测橡胶管状零件端口图像对应的结构分布均匀程度;根据所述缺损程度和结构分布均匀程度,得到待检测橡胶管状零件端口图像对应的第二异常程度指标;根据所述第一异常程度指标和第二异常程度指标,得到橡胶管状零件端口对应的异常程度。
5.本发明还提供了一种基于图像处理的管状零件端口异常检测系统,包括存储器和处理器,所述处理器执行所述存储器存储的计算机程序,以实现上述一种基于图像处理的管状零件端口异常检测方法。
6.有益效果:本发明将边缘图像与对应标准边缘图像之间的差异作为得到待检测橡
胶管状零件端口图像对应的第一异常程度指标的依据,将待检测橡胶管状零件端口图像上各像素点的像素值与对应邻域像素点的像素值之间的差异作为得到待检测橡胶管状零件端口图像对应的缺损程度的依据,将待检测橡胶管状零件端口图像上像素点的位置信息和像素值作为得到待检测橡胶管状零件端口图像对应的结构分布均匀程度的依据,将缺损程度和结构分布均匀程度作为得到待检测橡胶管状零件端口图像对应的第二异常程度指标的依据,将第一异常程度指标和第二异常程度指标作为得到橡胶管状零件端口对应的异常程度的依据,能提高对橡胶管状零件端口异常检测结果的准确性。
7.优选的,根据所述边缘图像与对应标准边缘图像之间的差异,得到待检测橡胶管状零件端口图像对应的第一异常程度指标的方法,包括:根据所述边缘图像,得到边缘图像对应的外圆边缘;根据所述标准边缘图像,得到标准边缘图像对应的标准外圆边缘;利用霍夫变换得到所述外圆边缘的圆心和所述标准外圆边缘的圆心;将所述外圆边缘的圆心与所述标准外圆边缘的圆心对齐,得到所述外圆边缘的圆心与所述标准外圆边缘的圆心对齐后的图像,将所述外圆边缘的圆心与所述标准外圆边缘的圆心对齐后的图像记为对齐图像,将外圆边缘的圆心与标准外圆边缘的圆心对齐的位置记为对齐图像的圆心;根据所述对齐图像,得到所述对齐图像上所述外圆边缘与所述标准外圆边缘重叠区域的面积和不重叠区域的面积;将所述重叠区域的面积记为橡胶管状零件端口图像对应的第一面积,将所述不重叠区域的面积记为橡胶管状零件端口图像对应的第二面积;过所述对齐图像上的外圆边缘、标准外圆边缘以及对齐图像的圆心做一条直线;将所述直线在所述对齐图像上沿顺时针方向旋转,计算在所述直线与所述对齐图像上的外圆边缘和标准外圆边缘相交的交点距离,得到对齐图像对应的交点距离序列;将所述交点距离序列中的最大交点距离记为待检测橡胶管状零件端口图像对应的第一差异距离;根据所述第一差异距离、第一面积和第二面积,得到橡胶管状零件端口图像对应的第一异常程度指标。
8.优选的,根据如下公式计算橡胶管状零件端口图像对应的第一异常程度指标:其中,为橡胶管状零件端口图像对应的第一异常程度指标,为橡胶管状零件端口图像对应的第二面积,为橡胶管状零件端口图像对应的第一面积,为橡胶管状零件端口图像对应的第一差异距离。
9.优选的,得到标准边缘图像的方法,包括:获取大量橡胶管状零件端口样本图像;利用边缘检测算法识别各橡胶管状零件端口样本图像对应的样本边缘图像;根据所述样本边缘图像,得到各橡胶管状零件端口样本图像对应的样本外圆边缘;根据所述样本外圆边缘,得到各样本外圆边缘对应的最小外接矩形;根据所述最
小外接矩形对应的长和宽,构建各最小外接矩形对应的样本向量;对所述样本向量进行聚类,选取最多样本向量数量对应的类别,将所述最多样本向量数量对应的类别记为第一类别;根据所述第一类别中各样本向量对应的最小外接矩形的长,得到第一类别中样本向量对应的最小外接矩形长的均值;根据所述第一类别中各样本向量对应的最小外接矩形的宽,得到第一类别中样本向量对应的最小外接矩形宽的均值;根据所述第一类别中各样本向量对应的最小外接矩形的长和宽、所述第一类别中样本向量对应的最小外接矩形长的均值和所述第一类别中样本向量对应的最小外接矩形宽的均值,得到第一类别中各样本向量对应的最小外接矩形对应的样本外圆边缘的标准程度;根据所述第一类别中各样本向量对应的最小外接矩形对应的样本外圆边缘的标准程度,构建所述第一类别中样本向量对应的标准程度序列;选取所述标准程度序列中最大标准程度对应的样本外圆边缘对应的样本边缘图像,将所述最大标准程度对应的样本外圆边缘记为所述边缘图像对应的标准边缘图像。
10.优选的,根据如下公式计算第一类别中各样本向量对应的最小外接矩形对应的样本外圆边缘的标准程度:其中,为第一类别中第个样本向量对应的最小外接矩形对应的样本外圆边缘的标准程度,为第一类别中样本向量对应的最小外接矩形长的均值,为第一类别中样本向量对应的最小外接矩形宽的均值,为第一类别中第个样本向量对应的最小外接矩形的长,为第一类别中第个样本向量对应的最小外接矩形的宽。
11.优选的,根据所述待检测橡胶管状零件端口图像上各像素点像素值与对应邻域像素点像素值之间的差异,得到待检测橡胶管状零件端口图像对应的缺损程度的方法,包括:计算待检测橡胶管状零件端口图像上各像素点像素值与对应八邻域的各像素点像素值之间的差值;根据所述待检测橡胶管状零件端口图像上各像素点的像素值与对应八邻域各像素点的像素值之间的差值,得到待检测橡胶管状零件端口图像上的异常像素点;根据所述异常像素点,得到待检测橡胶管状零件端口图像对应的缺损程度。
12.优选的,根据所述待检测橡胶管状零件端口图像上各像素点的位置信息和像素值,得到待检测橡胶管状零件端口图像对应的结构分布均匀程度的方法,包括:利用分割线将所述待检测橡胶管状零件端口图像均匀的划分成多个区域;根据所述分割线上的各像素点对应的左右两侧的各像素点的位置信息和像素值,拟合得到各分割线上的各像素点对应的三维高斯混合模型;根据所述三维高斯混合模型,得到各分割线上的各像素点对应的结构分布特征向量;根据所述各分割线上的各像素点对应的结构分布特征向量,得到各分割线对应的结构分布特征向量序列;计算所述结构分布特征向量序列中两两结构分布特征向量之间的余弦相似度,根据所述余弦相似度,得到各分割线对应的余弦相似度均值;
根据所述各分割线对应的余弦相似度均值,得到待检测橡胶管状零件端口图像对应的结构分布均匀程度。
13.优选的,根据如下公式计算待检测橡胶管状零件端口图像对应的第二异常程度指标:其中,为待检测橡胶管状零件端口图像对应的第二异常程度指标,为待检测橡胶管状零件端口图像对应的缺损程度,为待检测橡胶管状零件端口图像对应的结构分布均匀程度。
附图说明
14.为了更清楚地说明本发明实施例或现有技术中的技术方案和优点,下面将对实施例或现有技术描述中所需要使用的附图作简单的介绍,显而易见地,下面描述中的附图仅仅是本发明的一些实施例,对于本领域普通技术人员来讲,在不付出创造性劳动的前提下,还可以根据这些附图获得其它附图。
15.图1为本发明一种基于图像处理的管状零件端口异常检测方法的流程图;图2为本发明的边缘图像示意图;图3为本发明的对齐图像示意图;图4为本发明的待检测橡胶管状零件端口图像区域分割示意图。
具体实施方式
16.下面将结合本发明实施例中的附图,对本发明实施例中的技术方案进行清楚、完整的描述,显然,所描述的实施例仅仅是本发明一部分实施例,而不是全部的实施例,基于本发明实施例,本领域普通技术人员所获得的所有其它实施例,都属于本发明实施例保护的范围。
17.除非另有定义,本文所使用的所有的技术和科学技术语与属于本发明的技术人员通常理解的含义相同。
18.本实施例提供了一种基于图像处理的管状零件端口异常检测方法,详细说明如下:如图1所示,该基于图像处理的管状零件端口异常检测方法,包括以下步骤:步骤s001,获取待检测橡胶管状零件端口图像,识别所述待检测橡胶管状零件端口对应的边缘图像。
19.本实施例中,将待检测橡胶管状零件与其它零件进行连接的端口竖直向上放置在检测平台上,工业相机布置在检测平台的正上方,工业相机俯视向下,工业相机采集的待检测橡胶管状零件图像为rgb图像。
20.本实施例中,将工业相机采集的待检测橡胶管状零件端口图像输入到语义感知网络进行橡胶管状零件端口提取,得到仅有待检测橡胶管状零件端口图像的语义感知效果图,将得到的仅有待检测橡胶管状零件端口图像的语义感知效果图记为待检测橡胶管状零件端口效果图;本实施例语义感知网络为encoder
‑
decoder结构,语义感知网络通过编码器
进行卷积操作提取特征,编码器输出结果为特征图,特征图通过解码器操作,得到语义感知效果图;语义感知网络的具体训练过程为:获取训练样本集,所述训练样本集包括多个同一规格的橡胶管状零件端口样本rgb图像;对各橡胶管状零件端口样本rgb图像的端口区域标注为1,其它区域标注为0,将各橡胶管状零件端口样本rgb图像和标注数据输入至没有训练的语义感知网络网络中,并采用交叉熵损失函数进行进行迭代训练,不断更新网络参数;本实施例中,语义感知网络的具体网络结构和训练过程为现有技术,因此本实施例不做具体描述。
21.本实施例中,利用canny边缘检测算法对得到的待检测橡胶管状零件端口效果图进行边缘提取得到待检测橡胶管状零件端口效果图对应的边缘图像,所述边缘图像上包含内圆边缘和外圆边缘,如图2所示,1为内圆边缘,2为外圆边缘;本实施例中,canny边缘检测算法为公知技术,因此本实施例不做具体描述;作为其它的实施方式,根据需求的不同也可以使用其它的算法对待检测橡胶管状零件端口效果图进行边缘提取,例如可以是sobel边缘检测算法或者roberts边缘检测算法。
22.步骤s002,根据所述边缘图像与对应标准边缘图像之间的差异,得到待检测橡胶管状零件端口图像对应的第一异常程度指标。
23.本实施例中,通过分析待检测橡胶管状零件端口效果图对应的边缘图像与对应的标准边缘图像之间的差异,得到待检测橡胶管状零件端口图像对应的第一异常程度指标,第一异常程度指标将作为后续分析橡胶管状零件端口异常程度的基础;本实施例中,根据待检测橡胶管状零件端口效果图对应的第一差异距离、第一面积和第二面积,得到待检测橡胶管状零件端口图像对应的第一异常程度指标。
24.(a)标准边缘图像是得到待检测橡胶管状零件端口效果图对应的第一差异距离、第一面积和第二面积的基础;本实施例中,获得标准边缘图像具体过程为:获取大量橡胶管状零件端口样本图像;利用语义感知效果网络得到仅有橡胶管状零件端口样本图像的语义感知效果图,将得到的仅有橡胶管状零件端口样本图像的语义感知效果图记为橡胶管状零件端口样本效果图;利用canny边缘检测算法对各橡胶管状零件端口样本效果图进行边缘提取得到各橡胶管状零件端口样本效果图对应的样本边缘图像。
25.本实施例中,对橡胶管状零件端口样本效果图对应的样本边缘图像上的样本内圆边缘和样本外圆边缘进行标记,各样本边缘图像上的样本内圆边缘标记为,其中,为第1个样本边缘图像上的样本内圆边缘,为第个样本边缘图像上的样本内圆边缘,为样本边缘图像的数量也是橡胶管状零件端口样本效果图的数量;将各样本边缘图像上的样本外圆边缘标记为,其中,为第1个样本边缘图像上的样本外圆边缘,为第个样本边缘图像上的样本外圆边缘。
26.本实施例中,根据各橡胶管状零件端口样本效果图对应的样本边缘图像上的样本外圆边缘,得到各样本外圆边缘对应的最小外接矩形;根据各样本外圆边缘对应的最小外接矩形的长和宽,构建各最小外接矩形对应的样本向量,其中,为第1个样本边缘图像上的样本外圆边缘对应最小外接矩形的长,为第1个样本边缘图像上的样本外圆边缘对应最小外接矩形的宽,为第1个样本边缘图像上的样本外圆边缘对应
最小外接矩形的样本向量,为第个样本边缘图像上的样本外圆边缘对应最小外接矩形的长,为第个样本边缘图像上的样本外圆边缘对应最小外接矩形的宽,为第个样本边缘图像上的样本外圆边缘对应最小外接矩形的样本向量。
27.本实施例中,利用dbscan聚类算法对各最小外接矩形对应的样本向量进行聚类,得到多个聚类类别;dbscan聚类算法使用前需要确定邻域半径大小和邻域样本个数阈值,本实施例将邻域半径设置为3,邻域样本个数阈值设置为5。
28.作为其它的实施方式,也可以根据需求的不同设置不同的dbscan聚类算法使用前的邻域半径大小和邻域样本个数阈值,例如可以是将邻域半径设置为4,邻域样本个数阈值设置为6。
29.本实施例中,选取上述聚类类别中最多样本向量数量对应的类别,将最多样本向量数量对应的类别记为第一类别,根据第一类别中各样本向量对应的最小外接矩形的长,得到第一类别中样本向量对应最小外接矩形长的均值;根据如下公式计算第一类别中样本向量对应的最小外接矩形长的均值:其中,为第一类别中样本向量对应的最小外接矩形长的均值,为第一类别中样本向量的数量,为第一类别中第个样本向量对应的最小外接矩形的长。
30.本实施例中,根据第一类别中各样本向量对应的最小外接矩形的宽,得到第一类别中样本向量对应的最小外接矩形宽的均值;根据如下公式计算第一类别中样本向量对应的最小外接矩形宽的均值:其中,为第一类别中样本向量对应的最小外接矩形宽的均值,为第一类别中样本向量的数量,为第一类别中第个样本向量对应的最小外接矩形的宽。
31.本实施例中,根据上述得到的第一类别中各样本向量对应的最小外接矩形的长和宽、第一类别中样本向量对应的最小外接矩形长的均值和第一类别中样本向量对应的最小外接矩形宽的均值,得到第一类别中各样本向量对应的最小外接矩形对应的样本外圆边缘的标准程度;根据如下公式计算第一类别中各样本向量对应的最小外接矩形对应的样本外圆边缘的标准程度:其中,为第一类别中第个样本向量对应的最小外接矩形对应的样本外圆边缘的标准程度,为第一类别中样本向量对应的最小外接矩形长的均值,为第一类别中样本向量对应的最小外接矩形宽的均值,为第一类别中第个样本向量对应的最小外接矩形的长,为第一类别中第个样本向量对应的最小外接矩形的宽;的值越小,对应的值越大,的值越大,表明第一类别中各样本向量对应的最小外接矩形对应的样本外圆边缘越接近于标准外圆边缘。
32.本实施例中,根据上述得到的标准程度,构建标准程度序列;选取标准程度序列中
的最大标准程度,将最大标准程度对应的样本外圆边缘对应的样本边缘图像记为待检测橡胶管状零件端口效果图对应的边缘图像的标准边缘图像。
33.作为其它的实施方式,也可以根据需求的不同设置其它的获得标准边缘图像的方法,例如也可以根据各橡胶管状零件端口样本效果图对应的样本边缘图像上的样本内圆边缘,得到待检测橡胶管状零件端口效果图对应边缘图像的标准边缘图像。
34.(b)获得待检测橡胶管状零件端口效果图对应的第一差异距离、第一面积和第二面积的具体过程为:本实施例中,根据得到的待检测橡胶管状零件端口效果图对应的边缘图像,得到待检测橡胶管状零件端口效果图对应的边缘图像的外圆边缘;根据得到的待检测橡胶管状零件端口效果图对应的边缘图像对应的标准边缘图像,得到边缘图像对应的标准边缘图像的标准外圆边缘;利用霍夫变换得到外圆边缘的圆心和标准外圆边缘的圆心,将得到的外圆边缘的圆心与标准外圆边缘的圆心对齐,得到外圆边缘的圆心与标准外圆边缘的圆心对齐后的图像,将外圆边缘的圆心与标准外圆边缘的圆心对齐后的图像记为对齐图像,将外圆边缘的圆心与标准外圆边缘的圆心对齐的位置记为对齐图像的圆心,如图3所示,3为对齐图像上的标准外圆边缘,4为对齐图像上的外圆边缘,阴影部分为外圆边缘与标准外圆边缘重叠区域的面积;根据对齐图像,计算得到对齐图像上外圆边缘与标准外圆边缘重叠区域的面积和不重叠区域的面积,将对齐图像上外圆边缘与标准外圆边缘重叠区域的面积记为橡胶管状零件端口图像对应的第一面积,将对齐图像上外圆边缘与标准外圆边缘不重叠区域的面积记为橡胶管状零件端口图像对应的第二面积。
35.本实施例中,过对齐图像上的外圆边缘、标准外圆边缘以及对齐图像的圆心做一条直线;将直线在对齐图像上沿顺时针方向和固定角度进行多次旋转,计算在直线与对齐图像上的外圆边缘和标准外圆边缘相交的交点距离;根据得到的在直线与对齐图像上的外圆边缘和标准外圆边缘相交的交点距离,构建对应的交点距离序列,即对齐图像对应的交点距离序列;选取交点距离序列中的最大交点距离,将最大交点距离记为待检测橡胶管状零件端口图像对应第一差异距离;本实施例中,将直线在对齐图像上旋转的固定角度设置为1度,对应的旋转的次数为360次。
36.作为其它的实施方式,也可以根据需求的不同设置不同的旋转方式和旋转角度,例如可以是将直线在对齐图像上沿逆时针进行旋转,旋转的固定角度为2度。
37.(c)根据待检测橡胶管状零件端口效果图对应的第一差异距离、第一面积和第二面积,得到待检测橡胶管状零件端口图像对应的第一异常程度指标的具体过程为:本实施例中,根据待检测橡胶管状零件端口图像对应的第一差异距离、第一面积和第二面积,得到橡胶管状零件端口图像对应的第一异常程度指标;待检测橡胶管状零件端口图像对应的第一差异距离和待检测橡胶管状零件端口图像对应的第二面积与橡胶管状零件端口图像对应的第一异常程度指标成正相关关系,待检测橡胶管状零件端口图像对应的第一面积与橡胶管状零件端口图像对应的第一异常程度指标成负相关关系;根据如下公式计算橡胶管状零件端口图像对应的第一异常程度指标:其中,为橡胶管状零件端口图像对应的第一异常程度指标,为橡胶管状零件
端口图像对应的第二面积,为橡胶管状零件端口图像对应的第一面积,为橡胶管状零件端口图像对应的第一差异距离;橡胶管状零件端口图像对应的第一异常程度指标的值越大,表明橡胶管状零件端口对应的异常程度越严重。
38.作为其它的实施方式,也可以通过分析待检测橡胶管状零件端口效果图对应的边缘图像的内圆边缘与对应的标准内圆边缘的差异,得到橡胶管状零件端口图像对应的第一异常程度指标。
39.步骤s003,根据所述待检测橡胶管状零件端口图像上各像素点像素值与对应邻域像素点像素值之间的差异,得到待检测橡胶管状零件端口图像对应的缺损程度。
40.本实施例中,通过分析待检测橡胶管状零件端口图像上各像素点像素值与对应邻域像素点像素值之间的差异,得到待检测橡胶管状零件端口图像对应的缺损程度,得到的缺损程度将作为后续分析待检测橡胶管状零件端口图像对应的第二异常程度指标的基础。
41.本实施例中,得到待检测橡胶管状零件端口rgb图像上异常像素点的过程为:将上述通过语义感知网络得到的待检测橡胶管状零件端口效果图作为掩膜与待检测橡胶管状零件端口图像进行相乘操作,得到待检测橡胶管状零件端口rgb图像;根据待检测橡胶管状零件端口rgb图像,得到待检测橡胶管状零件端口rgb图像上各像素点的坐标和像素值;根据待检测橡胶管状零件端口rgb图像上各像素点的坐标,得到待检测橡胶管状零件端口rgb图像上各像素点对应的八邻域的各像素点;根据待检测橡胶管状零件端口rgb图像上各像素点对应的八邻域的各像素点,构建待检测橡胶管状零件端口rgb图像上各像素点对应的邻域像素点序列;计算待检测橡胶管状零件端口rgb图像上各像素点像素值与对应的邻域像素点序列中各像素点像素值之间的差值,根据待检测橡胶管状零件端口rgb图像上各像素点像素值与对应的邻域像素点序列中各像素点像素值之间的差值,构建待检测橡胶管状零件端口rgb图像上各像素点对应的差值序列,并得到待检测橡胶管状零件端口rgb图像上各像素点对应的差值序列中各差值的绝对值大于预设差值阈值的数量;判断待检测橡胶管状零件端口rgb图像上各像素点对应的差值序列中各差值的绝对值大于预设差值阈值的数量是否大于预设数量阈值,若是,则判定差值序列对应的待检测橡胶管状零件端口rgb图像上的像素点为异常像素点,否则,判定差值序列对应的待检测橡胶管状零件端口rgb图像上的像素点为正常像素点。
42.本实施例中,将预设差值阈值设置为5,将预设数量阈值设置为2;作为其它的实施方式,也可以根据需求的不同设置其它的预设差值阈值和预设数量阈值,例如可以是预设差值阈值为6,预设数量阈值为3。
43.本实施例中,通过上述过程可以得到待检测橡胶管状零件端口rgb图像上的异常像素点的数量,将待检测橡胶管状零件端口rgb图像上的异常像素点的数量记为待检测橡胶管状零件端口图像对应的缺损程度;待检测橡胶管状零件端口rgb图像上的异常像素点的数量越多对应的待检测橡胶管状零件端口图像对应的缺损程度越严重。
44.步骤s004,根据所述待检测橡胶管状零件端口图像上各像素点的位置信息和像素值,得到待检测橡胶管状零件端口图像对应的结构分布均匀程度。
45.本实施例中,通过分析待检测橡胶管状零件端口rgb图像上像素点的位置信息和像素值,得到待检测橡胶管状零件端口图像对应的结构分布均匀程度,得到的结构分布均匀程度将作为后续分析第二异常程度指标的基础。
46.本实施例中,利用与待检测橡胶管状零件端口rgb图像对应边缘图像上的内圆边缘和外圆边缘相交的分割线,将待检测橡胶管状零件端口rgb图像均匀的划分成多个区域,本实施例利用八条分割线将待检测橡胶管状零件端口rgb图像均匀的划分成8个区域,如图4所示,5为分割线;所述每条分割线上有多个像素点,每条分割线上的像素点构成各分割线对应的像素点序列,即每条分割线对应一个像素点序列;过各分割线上的各像素点作垂直于对应分割线的垂线,根据垂线上的像素点,得到各分割线上的各像素点对应的像素点分布序列;得到各分割线上的各像素点对应的像素点分布序列的具体过程为:根据上述过程得到第1条分割线上的第1个像素点处垂直于该分割线的垂线,将该像素点记为该分割线垂线的中心点,在垂线上选取中心点左侧的m个像素点和中心点右侧的m个像素点;根据第1条分割线上的第1个像素点、对应的中心点左侧的f个像素点和中心点右侧的m个像素点,构建第1条分割线上的第1个像素点对应的像素点分布序列,该像素点分布序列中像素点的数量为2m+1;同理,可以得到各分割线上的各像素点对应的像素点分布序列。
47.本实施例中,将m的值设置为20,作为其它的实施方式,也可以根据需求的不同设置不同的m值,例如可以将m的值设置为10;作为其它的实施方式,也可以根据需求的不同设置不同分割线数量,例如可以将分割线的数量设置为10。
48.本实施例中,将待检测橡胶管状零件端口rgb图像进行灰度化处理,得到待检测橡胶管状零件端口rgb图像对应的待检测橡胶管状零件端口灰度图像;在待检测橡胶管状零件端口灰度图像上获得各分割线上的各像素点对应的像素点分布序列中各像素点的灰度值和坐标信息;根据各分割线上的各像素点对应的像素点分布序列中各像素点的灰度值和坐标信息,拟合得到各分割线上的各像素点对应的三维高斯混合模型;即:其中,为第个分割线上的第个像素点对应的三维高斯混合模型,为为第个分割线上的第个像素点对应的三维高斯混合模型中高斯子模型的数量,为第个分割线上的第个像素点对应的三维高斯混合模型中第个高斯子模型的权值,为第个分割线上的第个像素点对应的三维高斯混合模型中第个高斯子模型的协方差,为第个分割线上的第个像素点对应的三维高斯混合模型中第个高斯子模型的特征向量,为第个分割线上的第个像素点对应的三维高斯混合模型中第个高斯子模型的特征向量的均值;第个分割线上的第个像素点对应的三维高斯混合模型中第个高斯子模型的特征向量,其中,为第个分割线上的第个像素点对应的像素分布序列中第个像素点的横坐标,为第个分割线上的第个像素点对应的像素分布序列中第个像素点的纵坐标,为第个分割线上的第个像素点对应的像素分布序列中第个像素点的灰度值。
49.本实施例中,拟合得到三维高斯混合模型过的程为现有技术,因此不做具体描述;
本实施例中,各分割线上的各像素点对应的三维高斯混合模型中高斯子模型的权值是通过em算法计算得到的;em算法为现有技术,因此本实施例不做具体描述。
50.本实施例中,上述得到的各分割线上的各像素点对应的三维高斯混合模型中的各高斯子模型对应三个参数,分别是各分割线上的各像素点对应三维高斯混合模型中各高斯子模型的权值、各高斯子模型的协方差以及各高斯子模型的特征向量的均值;因此各分割线上的各像素点对应的三维高斯混合模型中共含有3*个参数,根据各分割线上的各像素点对应的三维高斯混合模型对应的3*个参数,构建各分割线上的各像素点对应的3*维的向量;将各分割线上的各像素点对应的3*维的向量记为各分割线上的各像素点对应的结构分布特征向量。
51.本实施例中,根据各分割线上的各像素点对应的结构分布特征向量,构建各分割线对应的结构分布特征向量序列,计算各分割线对应的结构分布向量序列中两两结构分布向量之间的余弦相似度,得到各分割线对应的余弦相似度集合;将各分割线对应的余弦相似度集合中的余弦相似度求和之后求均值,得到各分割线对应的余弦相似度均值;将待检测橡胶管状零件端口rgb图像对应各分割线对应的余弦相似度均值求和,将求和之后的结果记为待检测橡胶管状零件端口图像对应的结构分布均匀程度;本实施例中,余弦相似度的计算过程为现有技术,因此不做具体描述。
52.步骤s005,根据所述缺损程度和结构分布均匀程度,得到待检测橡胶管状零件端口图像对应的第二异常程度指标。
53.本实施例中,通过分析待检测橡胶管状零件端口图像对应的缺损程度和结构分布均匀程度,得到待检测橡胶管状零件端口图像对应的第二异常程度指标,后续将第二异常程度指标作为分析橡胶管状零件端口对应的异常程度的基础。
54.本实施例中,根据待检测橡胶管状零件端口图像对应的缺损程度和结构分布均匀程度,得到待检测橡胶管状零件端口图像对应的第二异常程度指标,并对待检测橡胶管状零件端口图像对应的第二异常程度指标;待检测橡胶管状零件端口图像对应的缺损程度和结构分布均匀程度与待检测橡胶管状零件端口图像对应的第二异常程度指标成正相关关系;根据如下公式计算待检测橡胶管状零件端口图像对应的第二异常程度指标:其中,为待检测橡胶管状零件端口图像对应的第二异常程度指标,为待检测橡胶管状零件端口图像对应的缺损程度,为待检测橡胶管状零件端口图像对应的结构分布均匀程度;待检测橡胶管状零件端口图像对应的结构分布均匀程度,其中,为待检测橡胶管状零件端口rgb图像第1条分割线对应的余弦相似度均值,为待检测橡胶管状零件端口rgb图像第8条分割线对应的余弦相似度均值;待检测橡胶管状零件端口图像对应的第二异常程度指标的值越大,表明橡胶管状零件端口对应的异常程度越严重。
55.步骤s006,根据所述第一异常程度指标和第二异常程度指标,得到橡胶管状零件端口对应的异常程度。
56.本实施例中,将上述得到的待检测橡胶管状零件端口图像对应的第一异常程度指标和第二异常程度指标进行归一化处理,归一化处理为现有技术,因此本实施例不做具体
描述;根据归一化处理之后的待检测橡胶管状零件端口图像对应的第一异常程度指标和第二异常程度指标,得到橡胶管状零件端口对应的异常程度;归一化处理之后的待检测橡胶管状零件端口图像对应的第一异常程度指标和第二异常程度指标与橡胶管状零件端口对应的异常程度成正相关关系;根据如下公式计算橡胶管状零件端口对应的异常程度:其中,为橡胶管状零件端口对应的异常程度,为归一化处理之后的待检测橡胶管状零件端口图像对应的第一异常程度指标,为对应的权重,为归一化处理之后的检测橡胶管状零件端口图像对应的第二异常程度指标,为对应的权重,;橡胶管状零件端口对应的异常程度的值越大,表明橡胶管状零件端口与其它零件进行连接时的密封性越差;本实施例中,将设置为0.4,将设置为0.6;作为其它的实施方式,也可以根据需求的不同设置不同的权重值,例如可以将设置为0.3,将设置为0.7。
57.本实施例中,当橡胶管状零件端口对应的异常程度的值大于预设异常程度阈值时,判定该橡胶管状零件为异常零件,不能投入使用;当橡胶管状零件端口对应的异常程度的值小于预设异常程度阈值时,判定该橡胶管状零件为正常零件,能投入使用;本实施例中,预设异常程度阈值为经验值,需要根据实际情况进行设置。
58.有益效果:本实施例将边缘图像与对应标准边缘图像之间的差异作为得到待检测橡胶管状零件端口图像对应的第一异常程度指标的依据,将待检测橡胶管状零件端口图像上各像素点的像素值与对应邻域像素点的像素值之间的差异作为得到待检测橡胶管状零件端口图像对应的缺损程度的依据,将待检测橡胶管状零件端口图像上像素点的位置信息和像素值作为得到待检测橡胶管状零件端口图像对应的结构分布均匀程度的依据,将缺损程度和结构分布均匀程度作为得到待检测橡胶管状零件端口图像对应的第二异常程度指标的依据,将第一异常程度指标和第二异常程度指标作为得到橡胶管状零件端口对应的异常程度的依据,能提高对橡胶管状零件端口异常检测结果的准确性。
59.本实施例的基于图像处理的管状零件端口异常检测系统包括存储器和处理器,所述处理器执行所述存储器存储的计算机程序,以实现上述基于图像处理的管状零件端口异常检测方法。
60.需要说明的是,上述本发明实施例先后顺序仅仅为了描述,不代表实施例的优劣,在一些情况下,在权利要求书中记载的动作或步骤可以按照不同于实施例中的顺序来执行并且仍然可以实现期望的结果。