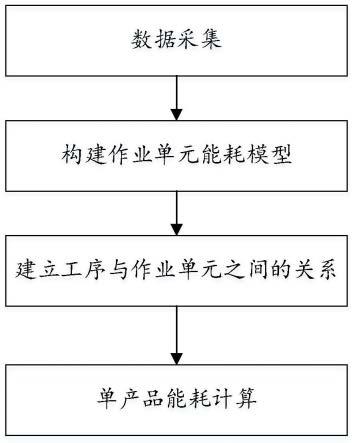
1.本发明涉及离散制造业技术领域,尤其涉及一种离散制造业单产品制造能耗计算方法。
背景技术:2.离散制造业具有工序多,流程复杂等特点,在生产过程中关键零部件采用批量生产的方式,并最终完成组装。在此条件下无法区分出产品生产过程中各环节的能源消耗情况,目前,主要采用单产品能耗=当月总能耗/当月产量的方式进行计算。实际生产过程会出现当月生产的零部件不一定在当月就完成产品组装,这就造成了该方法计算的精度不够,无法达到精益管理的要求。
技术实现要素:3.本发明的目的在于提供一种离散制造业单产品制造能耗计算方法,从而解决现有技术中存在的前述问题。
4.为了实现上述目的,本发明采用的技术方案如下:
5.一种离散制造业单产品制造能耗计算方法,包括如下步骤,
6.s1、数据采集
7.选取某一周期为基准,采集车间内产线和设备的能耗数据,汇总计算获取各作业单元的实际能耗数据;以生产过程中各作业单元的实际能耗数据为基准采集实际开报工相关信息;
8.s2、构建作业单元能耗模型
9.建立作业单元能耗模型,利用优化算法迭代寻优确定最优作业单元能耗模型;并基于最优作业单元能耗模型,利用作业单元的标准能耗数据确定作业单元的能耗预测值;
10.s3、建立工序与作业单元之间的关系
11.基于产品制造过程中生产流转的过程,确定某单产品的生产工序与各个作业单元之间的关系;进而确定该单产品的生产工序所涉及到的所有作业单元;
12.s4、单产品能耗计算
13.基于确定的某单产品的生产工序与各个作业单元之间的关系,对该单产品的生产工序涉及到的所有作业单元的能耗预测值进行累加计算,获取该单产品制造能耗预测值;计算公式为,
14.单产品制造能耗预测值=作业单元1的能耗预测值+作业单元2的能耗预测值+
…
+作业单元m的能耗预测值;
15.其中,m为该单产品制造工序中涉及到的作业单元的总数。
16.优选的,步骤s2具体为,
17.基于作业单元的实际能耗数据以及作业单元的标准能耗数据,建立作业单元能耗模型;利用优化算法对模型迭代寻优,确定模型中参数的最优值,并将参数最优值回代入模
型中,获取最优作业单元能耗模型;则将作业单元的标准能耗数据输入最优作业单元能耗模型中,即可获取作业单元的能耗预测值。
18.优选的,步骤s2中建立的作业单元能耗模型如下,
[0019][0020]
其中,a,b为能耗影响因素;f(xi)为第i个作业单元的能耗预测值;xi为第i个作业单元的能耗实际值;yi为第i个作业单元的标准能耗值;i=1,2,3,
…
,n;n为作业单元的总数。
[0021]
优选的,步骤s2中,由于作业单元能耗模型为二次函数,存在极小值,因此,当j(a,b)取最小值的时候,作业单元的能耗预测值和标准能耗值之间的差值最小;基于多周期作业单元的实际能耗数据,利用梯度下降法对作业单元能耗模型进行迭代寻优,给定学习率α,逐步修改a,直到j(a)取得最小值,最终确定a的最优值;计算公式如下,
[0022][0023]
本发明的有益效果是:1、本发明方法结合了生产工艺信息,并综合考虑的生产过程数据,具有较高的精准度。2、本发明中的能耗模型是一个动态的算法,随着数据量的变化对参数进行动态调整。3、通过本发明可以一键生成某一周期内的单产品能耗,基于产品能耗的趋势分析可以精准监控能耗趋势,为提升管理决策的精准度提供数据支撑。
附图说明
[0024]
图1是本发明实施例中能耗计算方法的流程示意图。
具体实施方式
[0025]
为了使本发明的目的、技术方案及优点更加清楚明白,以下结合附图,对本发明进行进一步详细说明。应当理解,此处所描述的具体实施方式仅仅用以解释本发明,并不用于限定本发明。
[0026]
实施例一
[0027]
本实施例中,提供了一种离散制造业单产品制造能耗计算方法,包括如下步骤,
[0028]
s1、数据采集;
[0029]
选取某一周期(月)为基准,利用物联网、大数据技术采集车间内产线和设备的能耗数据,汇总计算获取各作业单元的实际能耗数据;以生产过程中各作业单元的实际能耗数据为基准采集实际开报工相关信息;
[0030]
s2、构建作业单元能耗模型
[0031]
建立作业单元能耗模型,利用优化算法迭代寻优确定最优作业单元能耗模型;并基于最优作业单元能耗模型,利用作业单元的标准能耗数据确定作业单元的能耗预测值;
[0032]
具体过程如下:
[0033]
基于作业单元的实际能耗数据以及作业单元的标准能耗数据,建立作业单元能耗模型;利用优化算法对模型迭代寻优,确定模型中参数的最优值,并将参数最优值回代入模
型中,获取最优作业单元能耗模型;则将作业单元的标准能耗数据输入最优作业单元能耗模型中,即可获取作业单元的能耗预测值;
[0034]
作业单元能耗模型如下,
[0035][0036]
其中,a,b为能耗影响因素;f(xi)为第i个作业单元的能耗预测值;xi为第i个作业单元的能耗实际值;yi为第i个作业单元的标准能耗值;i=1,2,3,
…
,n;n为作业单元的总数。
[0037]
可以假设每条产线的能耗(因变量)与其他特征(自变量)之间满足线性相关,因此可以将能耗预测问题转化为多元线性回归问题,自变量为每日报工数据,因变量为对应工序的产线能耗,模型参数则为单项工艺能耗。求解多元线性回归问题,目标是使通过所构建模型预测的因变量与实际因变量的之间的差异最小。
[0038]
由于作业单元能耗模型为二次函数,存在极小值,因此,当j(a,b)取最小值的时候,作业单元的能耗预测值和标准能耗值之间的差值最小;基于多周期作业单元的实际能耗数据,利用梯度下降法对作业单元能耗模型进行迭代寻优,给定学习率α,逐步修改a,直到j(a)取得最小值,最终确定a的最优值;计算公式如下,
[0039][0040]
其中,α为学习率,预先设定。
[0041]
s3、建立工序与作业单元之间的关系;
[0042]
基于产品制造过程中生产流转的过程,确定某单产品的生产工序与各个作业单元之间的关系;进而确定该单产品的生产工序所涉及到的所有作业单元;
[0043]
s4、单产品能耗计算;
[0044]
基于确定的某单产品的生产工序与各个作业单元之间的关系,对该单产品的生产工序涉及到的所有作业单元的能耗预测值进行累加计算,获取该单产品制造能耗预测值;计算公式为,
[0045]
单产品制造能耗预测值=作业单元1的能耗预测值+作业单元2的能耗预测值+
…
+作业单元m的能耗预测值;
[0046]
其中,m为该单产品制造工序中涉及到的作业单元的总数。
[0047]
实施例二
[0048]
本实施例中,选取某一车间56个作业单元进行验证,选取一个月为周期,实时采集车间15块智能电表的数据,通过本模型自动计算出56个作业单元的能耗,并基于82道工序与作业单元进行有效关联,最终形成了大部件级的能耗情况,经过连续三个月的数据进行训练及验证,并最终得出单产品能耗(大部件级),计算结果与历史能耗数据进行对比,其精准度得到了显著提升。
[0049]
通过采用本发明公开的上述技术方案,得到了如下有益的效果:
[0050]
本发明提供了一种离散制造业单产品制造能耗计算方法,本发明方法结合了生产
工艺信息,并综合考虑的生产过程数据,具有较高的精准度。本发明中的能耗模型是一个动态的算法,随着数据量的变化对参数进行动态调整。通过本发明可以一键生成某一周期内的单产品能耗,基于产品能耗的趋势分析可以精准监控能耗趋势,为提升管理决策的精准度提供数据支撑。
[0051]
以上所述仅是本发明的优选实施方式,应当指出,对于本技术领域的普通技术人员来说,在不脱离本发明原理的前提下,还可以做出若干改进和润饰,这些改进和润饰也应视本发明的保护范围。