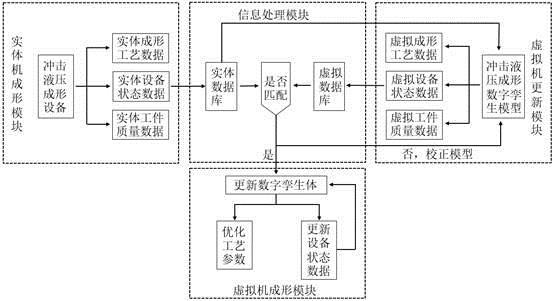
1.本发明涉及数字孪生技术领域,尤其涉及一种冲击液压成形用的数字孪生系统及构建方法。
背景技术:2.冲击液压成形是一种利用冲击体快速冲击液体介质,从而使冲击体的动能瞬时转换成为液体的压力能,最终使得工件快速成型的高能率成形技术。冲击液压成形具有能量利用率高、成形时间短、材料变形速率高等优异性能,同时能够显著提高材料的成形极限,对于复杂小特征具有很好的成形效果。
3.中国专利公开号:201610814955.x公开了一种高能率脉动冲击液压成形方法,该方法单次冲击过程为:冲击动力源驱动冲击体高速运动,高速运动的冲击体冲击液体介质,冲击体的动能瞬时转化为液体介质的压力能,使工件完成快速变形。该方法能够精确控制总的输出能量,经过多次脉动冲击成形出所需的零件形状,贴膜效果好,可用于镁、铝、钛等难变形合金的精密成形。
4.冲击液压成形时间非常短,通常在10μm以内,这导致工件的变形过程难以用试验的方式观测,且试验的成本较为昂贵。而传统的有限元仿真虽能以其实时记录应变、应力、位移等关键参数的功能获取工件成形规律及性能,但通常并未考虑设备状态对成形过程的影响。冲击液压成形设备的工作服役环境通常比较恶劣,在高速冲击过程中,设备内的冲击体、模具等都会产生不同程度的损伤。上述问题都会对工件成形预测结果产生较大影响,因此合理考虑关键设备参数对每一次成形过程的影响,是准确获取工件最佳成形工艺参数的关键。
技术实现要素:5.本发明的目的是提供一种冲击液压成形用的数字孪生系统及构建方法,用于解决现有冲击液压成形工艺参数预测精度不足的问题。
6.为实现上述目的,本发明采用的技术方案如下:本发明的第一目的是提供一种冲击液压成形用的数字孪生系统,包括:用以构建实体数据库的实体机成形模块,所述实体机成形模块包括冲击液压成形设备,以及冲击液压成形设备的实体成形工艺数据、实体设备状态数据和实体工件质量数据;虚拟机更新模块,利用所述实体数据库建立冲击液压成形数字孪生模型,并通过工程仿真模拟软件获取虚拟成形工艺数据、虚拟设备状态数据和虚拟工件质量数据,并匹配实体数据库与虚拟数据库,从而不断更新冲击液压成形数字孪生模型;信息处理模块,与所述实体机成形模块和虚拟机更新模块进行数据交互,用于储存实体数据库和虚拟数据库,并对实体数据库和虚拟数据库进行匹配,最终传达指令给虚拟机更新模块和虚拟机成形模块;
虚拟机成形模块,与所述信息处理模块进行数据交互,通过建立数字孪生体获取最佳冲击液压成形工艺参数和设备状态数据,依据所述设备状态数据更新数字孪生体获取下一次的冲击液压成形最优工艺参数和设备状态数据。
7.优选地,所述实体机成形模块通过获取多组的成形工艺数据,并记录每一次成形完成后的实体工件质量数据,同时检测每一次成形完成后的实体设备状态数据;筛选出其中真实有效的数据并保存至实体数据库。
8.优选地,所述虚拟机更新模块在工程仿真模拟软件上获取与实体机相同工艺条件下的多组虚拟成形工艺数据,并记录每一次成形完成后的虚拟工件质量数据及虚拟设备状态数据,筛选出准确的虚拟数据并保存至虚拟数据库。
9.优选地,当所述信息处理模块将实体数据库与虚拟数据库进行匹配时;若匹配度达标,则将冲击液压成形数字孪生模型更新为数字孪生体;若匹配度不达标,则需基于实体数据库的标准对冲击液压成形数字孪生模型进行校正,直至两者数据库匹配成功。
10.优选地,所述虚拟机成形模块通过数字孪生体输出第一次成形最优工艺参数及第一次成形后的设备状态数据;利用数字孪生体第一次成形后的设备状态数据更新数字孪生体;通过更新数字孪生体输出第二次成形最优工艺参数及第二次成形后的设备状态数据;以此类推,获取第三次、第四次、直至第n次后的最优工艺参数及设备状态数据。
11.本发明的第二目的是提供一种冲击液压成形用的数字孪生系统的构建方法,用于构建上述冲击液压成形用的数字孪生系统,包括:s1,通过实体数据库建立冲击液压成形数字孪生模型;s2,利用冲击液压成形数字孪生模型获取与实体数据库数据类型相同的虚拟数据库,并将两者数据库相匹配,若匹配度达标,则将冲击液压成形数字孪生模型更新为数字孪生体,若匹配度不达标则以实体数据库为标准更新冲击液压成形数字孪生模型后重新匹配,直至匹配度达标;s3,利用数字孪生体进行成形工艺预测;s4,利用数字孪生体获取冲击液压成形设备工作一次后的最佳成形工艺参数;s5,利用数字孪生体获取冲击液压成形设备工作一次后的设备状态数据;s6,利用冲击液压成形设备工作一次后的设备状态数据,更新冲击液压成形数字孪生体;s7,利用第一次更新后的数字孪生体,获取冲击液压成形设备工作第二次后的最佳成形工艺参数及设备状态参数;s8,重复s3至s7,获取不同设备状态下的最佳成形工艺条件。
12.优选地,s1包括:s11,利用测量工具获取金属坯料的三维尺寸,并通过国标试验获取适用于冲击液压成形仿真模拟所需的johnson-cook准则参数及物理参数,并记录成形前设置的冲击体冲击波参数、成形温度,最终得到实体成形工艺数据;s12,利用测量工具获取冲击液压成形设备的三维尺寸,获取冲击液压成形设备的物理模型参数;同时测量并记录成形前冲击体、型腔内壁的三维尺寸及位置参数,成形前液压油的温度、粘度及体积参数,得到成形前实体设备状态数据;
s13,利用冲击液压成形实体设备进行试验,记录成形后的工件工艺尺寸、减薄率,最终得到实体工件质量数据;同时测量并记录成形后冲击体、型腔内壁的三维尺寸及位置参数,成形后液压油的温度、粘度及被压缩后的体积参数,最终获取成形后实体设备状态数据;s14,采用不同的工艺条件并进行多组上述s11、s12、s13的操作,筛选最优且准确的实体数据,并将实体数据储存至实体数据库;s15,利用实体数据库建立冲击液压成形数字孪生模型。
13.优选地,s2包括:s21,采用冲击液压成形数字孪生模型对冲击液压成形过程进行工程仿真模拟,获取同s11、s12、s13、s14中工艺条件相同情况下的虚拟设备状态数据及虚拟工件质量数据;s22,通过冲击液压成形数字孪生模型进行多组工艺仿真模拟,筛选出准确的虚拟设备状态数据及虚拟工件质量数据;s23,确保冲击液压成形实体设备与数字孪生模型真实工作次数相同的情况下,将冲击液压成形实体设备与数字孪生模型每次工作前后设备状态、工件质量数据相匹配,根据行业标准设置匹配裕度;若匹配度在匹配裕度之内,则将冲击液压成形数字孪生模型更新为数字孪生体;若匹配度在匹配裕度之外,则返回s21,直至最终匹配度在匹配裕度之内。
14.优选地,s3包括:s31,将s23中获取的在匹配裕度之内的冲击液压成形数字孪生模型更新为数字孪生体;s32,利用所述数字孪生体进行工艺预测,以工件成品的三维工艺尺寸及减薄率达标程度进行工艺参数筛选。
15.与现有技术相比,本发明的有益效果为:本发明将冲击液压成形实体设备与数字孪生体互联,基于冲击液压成形设备工作环境恶劣从而导致设备工作可能会出现损伤的特点,通过将实体成形工艺数据、实体设备状态数据、实体工件质量数据相结合,建立适用于冲击液压成形的数字孪生体,有效保证了本发明中冲击液压成形结果预测的准确性。
16.本发明中的数字孪生系统考虑到设备每次工作对其本身造成的损伤且其损伤对每次成形结果的影响程度都会不同,基于每次工作后的设备状态数据更新数字孪生体,最终获取不同设备状态下的冲击液压成形最优工艺参数,进一步有效提高了冲击液压成形工艺参数的预测精度。
附图说明
17.图1为本发明优选实施例的系统结构框图;图2为本发明优选实施例的构建流程图;图3为本发明优选实施例的系统的体逻辑图。
具体实施方式
18.为了使本发明的上述目的、设计的控制系及优点更加清楚明白,以下结合实施例,对本发明进行进一步详细说明。应当理解,此处所描述的具体实施例仅用以解释本发明,并
不用于限定本发明。
19.请参阅图1和图3,一种冲击液压成形用的数字孪生系统,包括:实体机成形模块,其包括以实体存在的冲击液压成形设备,以及基于冲击液压成形的实体成形工艺数据、实体设备状态数据、实体工件质量数据,用以构建实体数据库;虚拟机更新模块,利用实体数据库建立冲击液压成形数字孪生模型,并通过工程仿真模拟软件获取虚拟数据库,并将实体数据库与虚拟数据库匹配从而不断更新冲击液压成形数字孪生模型;信息处理模块,与所述实体机成形模块和虚拟机更新模块相连,用于储存实体数据库和虚拟数据库,并将两者数据库进行匹配,最终传达指令给虚拟机更新模块和虚拟机成形模块;虚拟机成形模块,与所述信息处理模块相连,通过建立数字孪生体获取最佳冲击液压成形工艺参数和设备状态数据,依据所述获取的设备状态数据更新数字孪生体获取下一次的冲击液压成形最优工艺参数和设备状态数据。
20.在上述优选实施例中:所述实体机成形模块包括:获取实体机通过成形工艺的实体成形工艺数据;获取实体机通过所述成形工艺的实体设备状态数据;获取实体机通过所述成形工艺的实体工件质量数据;通过获取多组的成形工艺数据,并记录每一次成形完成后的实体工件质量数据,同时检测每一次成形完成后的设备状态并保存数据;最终根据经验筛选出其中真实有效的数据并保存至实体数据库。
21.获取上述实体成形工艺数据具体为:生产时首先获取坯料的材料属性、三维尺寸;生产时获取上述成形工艺的工艺参数,包括冲击体的冲击速度、冲击能量,压边力,成形温度。
22.获取上述实体设备状态数据具体为:生产时获取上述成形设备三维物理模型数据;生产时获取上述成形设备的状态数据,包括每次成形前后冲击体、成形型腔内壁、凹模的变形量及位置参数,成形型腔内液压油每次被压缩前后的温度、粘度及体积参数。
23.获取上述实体工件质量数据具体为:生产时获取成品工件的三维工艺尺寸、减薄率。
24.所述虚拟机更新模块获取实体机的实体数据库,依据实体数据库建立冲击液压成形数字孪生模型;获取虚拟机通过成形工艺的虚拟工艺数据;获取虚拟机通过成形工艺的虚拟设备状态数据;获取虚拟机通过成形工艺的虚拟工件质量数据;优选的,在工程仿真模拟软件上获取与实体机相同工艺条件下的多组虚拟成形工艺数据,并记录每一次成形完成后的虚拟工件质量数据及设备状态数据,利用优化算法筛选出准确的虚拟数据并保存至虚拟数据库。所述获取的虚拟机成形工艺数据类型与上述实体机数据类型相同。
25.所述信息处理模块的功能包括:通过实体机成形模块获取的实体数据库;
通过虚拟机成形模块获取的虚拟数据库;将实体数据库与虚拟数据库进行匹配;若匹配度达标,则将冲击液压成形数字孪生模型更新为数字孪生体;若匹配度不达标,则需基于实体数据库的标准对冲击液压成形数字孪生模型进行校正,直至两者数据库匹配成功。
26.所述虚拟机成形模块通过实体机成形模块、虚拟机模块、信息处理模块获取数字孪生体;通过数字孪生体输出第一次成形最优工艺参数及第一次成形后的设备状态数据;利用数字孪生体第一次成形后的设备状态数据更新数字孪生体;通过更新后的数字孪生体输出第二次成形最优工艺参数及第二次成形后的设备状态数据;以上述方案类推,获取第三次、第四次、第n次后的最优工艺参数及设备状态数据。上述“第一次、第二次、第n次”指的是所述成形工艺实体设备工作次数,实体设备成形出工件一次则记为工作一次。
27.请参阅图2,一种冲击液压成形用的数字孪生系统的构建方法,用于构建上述的冲击液压成形用的数字孪生系统,包括:s1,通过实体机成形模块获取的实体数据库建立冲击液压成形数字孪生模型;s2,利用冲击液压成形数字孪生模型获取与实体数据库数据类型相同的虚拟数据库,并将两者数据库相匹配,若匹配度达标则将冲击液压成形数字孪生模型更新为数字孪生体,若匹配度不达标则以实体数据库为标准更新冲击液压成形数字孪生模型后重新匹配;s3,利用匹配度达标的冲击液压成形数字孪生模型更新为数字孪生体;并利用数字孪生体进行成形工艺预测;s4,利用数字孪生体获取所述设备工作一次后的最佳成形工艺参数;s5,利用数字孪生体获取所述设备工作一次后的设备状态数据;s6,利用所述设备工作一次后的设备状态数据,更新冲击液压成形数字孪生体;s7,利用第一次更新后的数字孪生体,获取设备工作第二次后的最佳成形工艺参数及设备状态参数。
28.重复上述的s3、s4、s5、s6、s7,即可合理考虑冲击液压成形设备每次工作后对其本身造成的损伤,从而预测其损伤对下一次成形结果的影响,获取不同设备状态下的最佳成形工艺条件,最终提高冲击液压成形预测精度、提高工件质量。
29.请参阅图3,其为本发明所述一种基于冲击液压成形的数字孪生系统的整体逻辑图,所述s1包括:s11,利用测量工具获取金属坯料的三维尺寸,并通过国标试验获取适用于冲击液压成形仿真模拟所需的johnson-cook准则参数及其他物理参数,并记录成形前设置的冲击体冲击波参数、成形温度,最终得到实体成形工艺数据;s12,利用测量工具获取冲击液压成形设备的三维尺寸,用于获取设备物理模型参数;同时测量并记录成形前冲击体、型腔内壁的三维尺寸及位置参数,成形前液压油的温度、粘度及体积参数,得到成形前实体设备状态数据;s13,利用冲击液压成形实体设备进行试验,记录成形后的工件工艺尺寸、减薄率,最终得到实体工件质量数据;同时测量并记录成形后冲击体、型腔内壁的三维尺寸及位置参数,成形后液压油的温度、粘度及被压缩后的体积参数,最终获取成形后实体设备状态数据;
具体而言,将s12和s13中所述得到的成形前和成形后设备状态数据综合后,最终得到实体设备状态数据。
30.s14,采用不同的工艺条件并进行多组上述s11、s12、s13的操作,通过经验筛选最优且准确的实体数据,并将实体数据储存至实体数据库;s15,利用s14获取的实体数据库建立冲击液压成形数字孪生模型。
31.具体而言,上述s14中进行的多组试验是具有设备工作次数之分的,成形一次工件都视为实体设备工作一次。
32.所述s2包括:s21,采用s15所建立的冲击液压成形数字孪生模型对冲击液压成形过程进行工程仿真模拟,获取同s11、s12、s13、s14所述工艺条件相同情况下的虚拟设备状态数据及虚拟工件质量数据;s22,通过上述冲击液压成形数字孪生模型进行多组工艺仿真模拟,利用优化算法、人工经验等方式筛选出准确的虚拟设备状态数据及虚拟工件质量数据;s23,确保冲击液压成形实体设备与数字孪生模型真实工作次数相同的情况下,将冲击液压成形实体设备与数字孪生模型每次工作前后设备状态、工件质量数据相匹配,根据行业标准设置匹配裕度;若匹配度在匹配裕度之内,则将冲击液压成形数字孪生模型更新为数字孪生体;若匹配度在匹配裕度之外,则返回s21,直至最终匹配度在匹配裕度之内。
33.具体而言,在所述s21中,所获取的虚拟设备及工件质量数据类型应当是与所述s12、s13、s14中实体数据类型相同的,目的是为了对比判断所建立的冲击液压成形数字孪生模型的运行数据是否符合现有冲击液压成形设备的运行数据,最终创建准确性高的冲击液压成形数字孪生模型。
34.在所述s22中,所进行的多组工艺仿真模拟,指的是在同一种工艺条件下进行多组重复的仿真模拟,目的是筛选出准确的虚拟数据。
35.在所述s23中,所述确保冲击液压成形实体设备与数字孪生模型真实工作次数相同,指的是以实体设备为标准,实体设备成形工件一次,对应的冲击液压成形数字孪生模型为了得到一次最优数据的整个仿真过程都将视为虚拟设备工作一次;本领域技术人员可以理解的是,在上述虚拟设备工作一次的整个成形仿真过程中,冲击液压成形数字孪生模型所采用的设备状态数据都应当相同,是为此次虚拟设备工作前的设备状态数据。
36.所述s3包括:s31,将s23中获取的在匹配裕度之内的冲击液压成形数字孪生模型更新为数字孪生体;s32,利用s31创建的数字孪生体进行工艺预测,以工件成品的三维工艺尺寸及减薄率达标程度进行工艺参数筛选。
37.具体而言,上述s32中一组工艺参数筛选过程应当作为虚拟设备工作一次;本领域技术人员可以理解的是,所述一组工艺参数是成形一次工件所需的所有工艺参数。
38.所述s4包括:s41,通过s32获取虚拟设备工作一次后的最佳成形工艺参数,其参数即可作为实体设备工作一次所采用的最佳工艺参数。
39.所述s5包括:
s51,通过s32获取虚拟设备工作一次后的设备状态数据,其数据即可视为实体设备工作一次后的设备状态数据。
40.所述s6包括:s61,利用s51获取的设备状态数据更新数字孪生体。
41.所述s7包括:s71,重复s3、s4、s5,以获取虚拟设备工作第二次后的最佳工艺参数和设备状态数据。
42.重复s3、s4、s5、s6、s7、即可获取虚拟设备工作第三次、第四次、第n次后的最佳成形工艺条件和设备状态数据,在本发明所提供的一种基于冲击液压成形的数字孪生系统下,实体设备与虚拟设备工作次数相同条件下的最佳成形工艺条件和设备状态数据都相同,因此针对冲击液压成形设备易损伤的特点,合理考虑关键零部件及关键参数对每次成形结果的影响,最终进一步提高了冲击液压成形工艺参数预测的精度。
43.以上所述仅是对本发明的较佳实施例而已,并非对本发明作任何形式上的限制,凡是依据本发明的技术实质对以上实施例所做的任何简单修改,等同变化与修饰,均属于本发明技术方案的范围内。