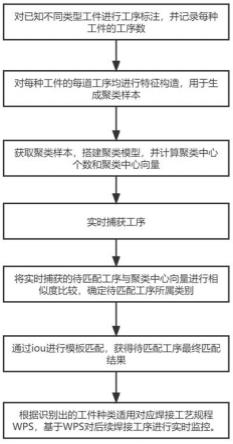
1.本发明涉及智慧焊接技术领域,主要涉及一种基于模式识别的自动焊接工序智能识别方法。
背景技术:2.目前智慧焊接的概念已经越来越深入人心,针对焊接过程的数据采集、数据分析以及信息反馈也逐渐覆盖了包括手工焊、机器人焊接等多种细分焊接市场,基于各种传感器进行焊接过程数据采集、采用多维度分析方法对采集数据进行分析,进而输出反馈信息,已经逐渐成为智慧焊接领域的主要技术手段。
3.针对焊接过程的数据采集多依靠各类传感器,采集的数据也包括声信号、图像信号、电流信号、电压信号等。在机器人焊接时,各道工序基本遵循了焊接工艺规程wps规定的相关焊接工艺参数,因此机器人焊接同一种工件时工序是相同的。当多维传感器对时序数据进行采集时,我们无法得知机器人当前焊接的是何种工件,对工件工序的智能识别也无法实现。因此需要研究一种方法,基于传感器采集到的数据,实时捕捉机器人焊接工序,并识别属于何种工件,进而基于该种工件中各道工序的wps进行工艺监控,监控其是否存在电流、电压超限等问题。
技术实现要素:4.发明目的:基于上述背景技术中提出的问题,本发明提供了一种基于模式识别的自动焊接工序智能识别方法,首先根据已知工件的各道工序建立工序库,通过聚类方法将各道工序组合进行分类。接着实时捕获工序,并预测捕获的工序组合具体属于哪一类别,然后通过iou值计算进行模板匹配,将实时捕获的工序组合与所属类中的各项工序组合进行匹配,进而识别当前捕获的工序组合具体属于哪一种工件的哪几道工序。最后根据识别的工件wps进行电压、电流的超限监控。
5.技术方案:一种基于模式识别的自动焊接工序智能识别方法,包括以下步骤:步骤s1、对已知不同类型工件进行工序标注,并记录各种工件的工序数;步骤s2、对不同种类工件的每道工序均进行特征构造,生成聚类样本;步骤s3、获取聚类样本,搭建聚类模型并计算聚类中心个数及聚类中心向量;步骤s4、实时捕获工序;步骤s5、将步骤s4中实时捕获的连续工序按照步骤s2所述特征构造方法进行特征构造,与聚类中心向量进行相似度比较,确定实时捕获的待匹配工序所属类别;步骤s6、通过模板匹配方法将待匹配工序与所属类别中所有工序分别匹配,识别出待匹配工序属于何种工件的第几道工序。
6.进一步地,所述步骤s2中特征构造包括:(1)每道工序的电流均值、电压均值和送丝速度均值;每道工序内的电流方差、电压方差;
(2)工序的焊接方式及对应的脉冲周期;所述焊接方式包括恒压焊接和脉冲焊接,其中恒压焊接方式标记为0,脉冲周期为0,脉冲焊接方式标记为1,脉冲周期为实际测量值;(3)工序时长。
7.进一步地,当采样频率高于1hz时,计算每秒内的电流均值点、电压均值点和送丝速度均值点依次作为该秒的电流、电压、送丝速度,进而计算每道工序内的电流均值、电压均值和送丝速度均值、电流方差和电压方差。
8.进一步地,所述步骤s3中搭建聚类模型的具体方法如下:步骤s3.1、针对不同类型工件,遍历各工件的所有工序,按顺序提取连续3道工序,分别按步骤s2所述方法构造特征,将3道工序的特征拼接在一起,作为聚类样本;遍历所有工件,获得若干聚类样本;步骤s3.2、通过kmeans算法对聚类样本进行聚类;根据预先设定的聚类中心个数范围[a,b],遍历每个值,将其作为聚类中心个数进行聚类,每次聚类完毕后计算该聚类方案的轮廓系数作为评估指标;最终选取轮廓系数最大的聚类方案作为目标聚类方案,并获取对应的聚类中心个数,进而计算并输出每个类别的聚类中心向量。进一步地,所述步骤s4中实时捕获工序的具体方法包括:步骤s4.1、设置用于存放电流均值点的集合current_list_one,设置三组依次用于存放已识别工序数据的集合current_list_three、voltage_list_three和feedspeed_list_three,分别代表电流、电压和送丝速度;步骤s4.2、捕获每道工序的起始位置和结束位置;将每秒电流均值点放置于current_list_one中。当current_list_one集合中元素个数大于等于10时进行如下判断:当集合中元素的最大值小于预设阈值时,清空集合;当集合中元素的最大值大于等于时,找到第一个大于等于的电流均值点,此均值点对应的时间位置即为工序的起始位置,剔除该时间位置之前的所有数据;在获取工序的起始位置后,继续获取电流均值点并填充current_list_one,直至找到最后一个大于等于的电流均值点,该均值点对应的位置即为该道工序的结束位置;步骤s4.3、将捕获到的工序对应的电流均值点放置于current_list_three中,作为该道工序对应的电流集合,根据起始位置和结束位置对应的时间区间,截取对应时序位置的电压均值点和送丝速度均值点集合,并分别存入voltage_list_three和feedspeed_list_three中;步骤s4.4、每捕获1道工序后,清空current_list_one并重新开始捕获下一道工序;连续捕获3道工序,分别填充至current_list_three、voltage_list_three和feedspeed_list_three中,获取实际焊接过程中连续3道工序的电流、电压和送丝速度情况,即待匹配工序情况。
[0009]
进一步地,所述步骤s5中确定实时捕获的待匹配工序所属类别具体方法包括:将步骤s4中获取的集合current_list_three、voltage_list_three和feedspeed_list_three按照步骤s2所述的特征构造方法进行特征构造,拼接3道工序的样本特征,获取待匹配工序的样本特征列表;计算待匹配工序与步骤s3中获取的每个聚类中心向量间的余弦相似度:
其中a为待匹配工序的样本特征列表,b为一个聚类中心向量,n为特征个数,最终获得待匹配工序与聚类中心的余弦相似度;遍历所有聚类中心,计算出待匹配工序与所有聚类中心的余弦相似度,选取最大的余弦相似度对应的类,即为待匹配工序所属类别。
[0010]
进一步地,将步骤s4中获取的集合current_list_three、voltage_list_three和feedspeed_list_three与步骤s5中匹配的类别下所有样本进行模板匹配,最终获取匹配结果;具体地,步骤s6.1、分别计算待匹配工序中3道工序的电流、电压、送丝速度的均值和3道工序的起止时长,计算所述聚类类别下所有样本的电流、电压、送丝速度均值点的均值和3道工序的起止时长;步骤s6.2、计算待匹配的3道连续工序与聚类类别下单个样本的3道连续工序间电流的iou值;具体地,取第1道工序的起止时长为矩形长,以工序内所有电流点均值为矩形宽,生成第一矩形,同理生成对应单个样本的第二矩形,计算第一矩形和第二矩形的交集面积与并集面积间的比值,即为iou值;依次计算第2-3道工序,共生成3个iou值;分别对电压和送丝速度进行相同处理,一共计算9个iou值,求取均值,作为iou均值;步骤s6.3、计算聚类类别下所有样本的3道连续工序与待匹配的3道连续工序间的iou均值,选取iou均值最大的样本工序作为待匹配工序的匹配结果。
[0011]
进一步地,模板匹配完成后,继续捕获新的工序,current_list_three、voltage_list_three和feedspeed_list_three中保留最近的3道工序数据,重复步骤s2-s6,直至匹配到工件的最后一道工序,清空current_list_three、voltage_list_three和feedspeed_list_three。
[0012]
本发明采用的技术方案与现有技术方案相比,具有以下有益效果:(1)本发明针对在焊接过程监控中,单独采集高频时序数据无法识别当前焊接的是何种工件的哪道工序的问题,提供了一种基于模式识别的自动焊接工序智能识别方法,通过模板匹配方法,将实时捕获的连续3道工序与已知工件的工序组合进行匹配,进而识别出当前焊接的工件属于何种工件的第几道工序。
[0013]
(2)本发明采用聚类模型将已知工件先进行聚类,首先通过聚类预测确定待匹配工序所在类别,接着在该类别中进一步进行模板匹配,这样可以有效减小计算时间,进而实现实时匹配,实时监控的功能。
附图说明
[0014]
图1为本发明提供的基于模式识别的自动焊接工序智能识别方法流程图;图2为本发明实施例中工件工序示意图;图3为本发明实施例中iou值计算方法示意图。
具体实施方式
[0015]
下面结合附图对本发明做更进一步的解释。
[0016]
一种基于模式识别的自动焊接工序智能识别方法,首先根据已知的不同工件类型进行工序标注,大规模机器人焊接过程中,同一类型的工件工序是固定的,因此可以准确标注每道工序所用时间。针对每个类型工件的每道工序,采集包括电压、电流和送丝速度在内的高频时序数据,并进行特征构造。针对所有已知类型工件,将连续若干道工序构造的特征进行拼接,并进行聚类,获取聚类中心个数及每个类别的聚类中心向量。本实施例中选择3道连续工序进行拼接,即可适用于大多数应用场景。应当认为,采用不低于2道连续工序拼接均可实现本发明的技术效果。对拼接特征的次数进行调整均应当属于本发明的保护范围。
[0017]
接着对上述高频时序数据进行实时捕获,对捕获的连续3道工序进行同样的特征构造、获取特征列表,并根据聚类结果进行预测,通过计算特征列表与聚类中心向量的余弦相似度,进而预测所属类别。获取特征列表对应的连续3道工序的数据点均值和工序时长,通过与所属类别下的每一个样本计算iou值,最终确定焊接的工件类型和所处工序段,进而实现最终工序识别的效果,最终根据不同工序的wps对后续焊接过程进行监控。具体步骤如图1所示:步骤s1、对已知类型工件进行工序标注,并记录每种工件的工序个数。
[0018]
由于机器人焊接过程中某一类型的工件焊接工序是固定的,因此本发明将不同类型的工件焊接工序作为待匹配模板,通过模板匹配的方法进行工件类型的识别。针对已知类型工件,需要首先对其工序进行标注,包括每道工序的起始和终止时间,获取工件的工序信息。
[0019]
步骤s2、对每道工序分别构造特征,用于生成聚类模型。构造的特征类型包括:(1)本发明中,当采样频率大于1hz时,分别以每秒的电流均值点、电压均值点和送丝速度均值点代替该秒的电流、电压和送丝速度,如图2所示。当采样频率为1hz时,则无需先计算均值点。以此为基础计算各道工序内的电流均值、电压均值和送丝速度均值;同时计算电流方差和电压方差;(2)工序的焊接方式及对应的脉冲周期;所述焊接方式包括恒压焊接和脉冲焊接,其中恒压焊接方式设置为0,脉冲周期为0,脉冲焊接方式设置为1,脉冲周期为实际测量值;(3)工序时长。
[0020]
步骤s3、获取聚类样本,通过聚类方法计算聚类中心个数和聚类中心向量。
[0021]
首先,针对不同类型的工件,遍历各工件的所有工序,按顺序提取连续3道工序,分别按步骤s2所述方法构造特征,将3道工序的特征拼接在一起,作为聚类的一个样本。例如,对第n类工件,设定i为工序序号;将第i至i+2道连续工序分别提取步骤s2中的特征并拼接,作为一个聚类样本。i取值范围为[1,m-2],其中m为该类型工件的总工序数量。遍历所有工件,即可获得若干聚类样本。
[0022]
接着,通过kmeans算法对上述聚类样本进行聚类。根据预先设定的聚类中心个数范围[a,b],遍历每个值,将其作为聚类中心个数进行聚类,每次聚类完毕后计算该聚类方案的轮廓系数作为评估指标;最终选取轮廓系数最大的聚类方案作为目标聚类方案,并获取对应的聚类中心个数,进而计算并输出每个类别的聚类中心向量。
[0023]
在建立聚类模型后,实时采集时序数据,进行模板匹配步骤。具体包括实时捕获工序、聚类模型预测类别和工序匹配三个阶段。如下所示:步骤s4、实时捕获工序首先设置用于存放电流均值点的集合current_list_one,接着设置三组用于存放已识别工序数据的集合current_list_three、voltage_list_three和feedspeed_list_three,分别代表电流、电压和送丝速度。
[0024]
然后捕获每道工序的起始位置和结束位置。将每秒电流均值点放置于current_list_one中。当current_list_one集合中元素个数大于等于10时进行如下判断:当集合中元素的最大值小于预设阈值时,清空集合;当集合中元素的最大值大于等于时,找到第一个大于等于的电流均值,此均值对应的位置即为工序的开始位置,剔除该位置之前的所有数据。例如:当预设阈值=1a时,检测到第7100个均值点以后所有的电流均值均大于1a,则第7100个均值点即为该道工序的起始位置,剔除第7100个均值点前的所有电流均值。捕获每道工序的结束位置。在获取起始位置后,不断填充current_list_one,找到最后一个大于等于的电流均值点,该均值点对应的位置即为该道工序的结束位置。
[0025]
将该道工序对应的所有电流均值点作为一个集合放置于current_list_three中,作为该道工序对应的电流集合。根据电流均值点的时序位置,对应地截取相应位置的电压和送丝速度均值点,并将其分别存入voltage_list_three和feedspeed_list_three中。
[0026]
每捕获1道工序后,清空current_list_one并开始新一轮捕获,连续捕获3道工序,填充上述集合,这样就获得了实际焊接过程中连续3道工序的电流、电压和送丝速度情况,即为待匹配工序情况。
[0027]
当捕获新工序时,剔除原有第一道工序的相关数据,剩余工序数据依次向前平移,实时捕捉并更新工序。
[0028]
步骤s5、聚类模型预测。
[0029]
将步骤s4中获取的集合current_list_three、voltage_list_three和feedspeed_list_three按照步骤s2所述的特征构造方法进行特征构造,获取待匹配工序的样本特征列表。与步骤s3中获取的每一个聚类中心向量按照如下公式计算余弦相似度:其中a为待匹配工序的样本特征列表,b为一个聚类中心向量,n为特征个数,最终获得待匹配工序与聚类中心的余弦相似度。遍历所有聚类中心,计算出待匹配工序与所有聚类中心的余弦相似度,选取最大的余弦相似度对应的类,即为待匹配工序所属类别。
[0030]
步骤s6,工序匹配。
[0031]
将步骤s4中获取的集合current_list_three、voltage_list_three和feedspeed_list_three与步骤s5中匹配的类别下所有样本进行模板匹配,最终获取匹配结果。
[0032]
模板匹配的具体方法如下:首先,分别计算待匹配工序中3道工序的电流、电压、送丝速度的均值和3道工序的起止时长,接着计算所述聚类类别下所有样本的电流、电压、送丝速度均值点的均值和3道
工序的起止时长。分别计算待匹配工序与聚类类别下各样本的电流、电压、送丝速度的iou值。以电流为例,先求出待匹配工序中3个电流均值,记为a1、a2、a3,再求出各样本的电流均值点的均值,记为a
j1
,a
j2
、a
j3
,j代表不同样本序号。
[0033]
以工序时间为横坐标,电流均值为纵坐标,分别绘制待匹配工序与第1个样本工序的iou矩形,分别计算获得3道工序的iou值,对于电压和送丝速度同样采用上述处理,最终获得9个iou值,求取平均值,即为待匹配工序和第1个样本工序间的iou均值。遍历j个样本工序,最终获得j个对应iou均值,选取iou均值最大的样本工序,即为待匹配工序最终的匹配结果。
[0034]
iou值的计算方法为两个矩形框的交集除以两个矩形框的并集,计算示例如图3所示:横轴为工序时长,纵轴为工序电流均值,虚线代表的模板工序电流为284.7a,工序时长为191s,实线代表的待匹配工序,电流为222.8a,工序时长为285s。两个由电流和工序时长所构成的矩形的交集为191*222.8=42554.8,并集为284.7*191+222.8*285-42554.8=75320.9,则iou=42554.8/75320.9=0.565。
[0035]
模板匹配完成后,即可获知该三道工序属于哪一种工件。在此基础上,需要继续实时捕获工序,并持续进行匹配,直至集合current_list_three、voltage_list_three和feedspeed_list_three中最后一道工序为该工件的最后一道工序,此时应当清空current_list_three、voltage_list_three和feedspeed_list_three,表示此时该工件焊接完毕。
[0036]
实际机器人焊接中,假设捕获了3道工序,匹配至某一类工件,该工件工序总数为28,捕获的第3道工序位于28道工序总数的第7道。继续捕获新的工序,每捕获一道新工序,实时匹配,直至current_list_three中捕获到该工件的最后一道工序,此时该工件焊接完成,清空current_list_three、voltage_list_three和feedspeed_list_three三个列表。直至焊接下一个工件,重新开始捕获、匹配。
[0037]
需要注意的是,当超过特定时间未能捕获到新工序时,应当默认此时停止焊接,同样需要清空上述列表。待重新捕获新工序时,重新匹配。
[0038]
根据上述匹配结果,即可获知当前焊接的工件对应类型,在本发明提出的自动焊接工序智能识别方法基础上,基于该工件的焊接工艺规程wps记载的相关工艺参数,可以向用户推荐合理的焊接工艺参数范围,进而指导用户在合理合规的焊接环境下焊出符合质量要求的工件。此外,还可以根据不同工序的wps范围对电压超限、电流超限等问题进行实时监控和报警。
[0039]
以上所述仅是本发明的优选实施方式,应当指出,对于本技术领域的普通技术人员来说,在不脱离本发明原理的前提下,还可以做出若干改进和润饰,这些改进和润饰也应视为本发明的保护范围。