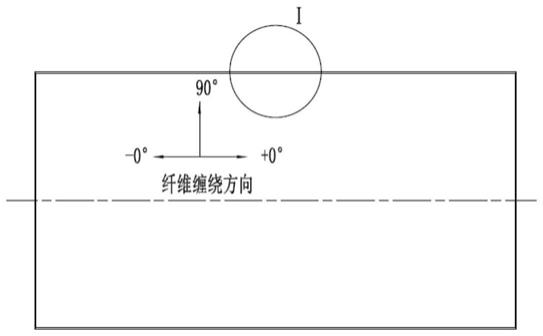
1.本发明涉及复合材料技术领域,具体为一种高速电机用复合材料套筒及其制备方法,特别是涉及一种适用于大功率、高转速的电机转子套筒及其制备方法。
背景技术:2.随着电机额定功率和转速的提高,高速电机线绕式转子外表面需采取光滑转子技术。目前高速电机线绕式转子外表面光滑转子技术主要采用合金套筒,合金套筒虽能增加电机转子的整体强度及降低摩擦产生的热量,但合金套筒也会增加电机的重量及涡流损耗。
3.相对传统的合金套筒,复合材料套筒由于其优良的物理化学性能,可以满足高速转子整体化和强度的要求,减轻电机的整机重量,并减少电机运行过程中的涡流损耗和摩擦损耗。
4.中国专利cn102280230a公开了一种风力发电机用的玻璃钢绝缘套筒及其成型方法,其由多瓣同圆心且等弧度的弧形状筒壁拼装成筒状并粘接于风力发电机定子上,套筒的外径为(3000~6500)mm,长度为(1500~2500)mm,厚度为(2.0~6.0)mm。该玻璃钢绝缘套筒以无碱无捻e玻璃纤维缝编毡作为结构层、聚酯有机毡为防渗层,以环氧树脂或乙烯基树脂为树脂基体,采用rtm复合材料树脂传递模塑工艺成型。
5.中国专利cn203779958u公布了一种复合材料套筒用于柔性版印刷领域,包括内套筒、套筒基体ⅰ和套筒基体ⅱ,内套筒外表面缠绕有弹性体衬垫,弹性体衬垫外表面包覆有套筒基体ⅰ,套筒基体ⅰ通过支撑填充体层与套筒基体ⅱ连接。套筒基体ⅱ外表面附着有表层。内套筒与套筒基体ⅰ由玻璃钢材料制成,支撑填充体层由支撑环或聚合物材料制成,套筒基体ⅱ由玻璃钢或聚合物材料制成,表层由金属或陶瓷材料制成。其表面材料的硬度、粗糙度和耐溶剂型较好。
6.中国专利cn105690793b公布了一种三维编织复合材料汽车传动轴及其制备方法,该复合材料汽车传动轴通过混杂纤维多向编织的方式进行三维多轴向织物结合组合,对传动轴特定部位进行结构性能强化,最终实现三维预制体结构的一体化编织。在相关的三维织物预制体制件制备完成后,选用特定纤维进行厚度向铺缝二次强化处理以提高厚度方向的强度和刚度。最后以热固性树脂胶液为基体材料,采用真空导入与快速热固化相结合的连续成型用以对预制体织物进行树脂浸渍复合以及树脂固化。最终形成的复合材料汽车传动轴具有重量轻、强度高、耐摩擦等优势。
7.中国专利cn106335189a公布了一种碳纤维承压套筒的制作工艺,先将承压套筒分为外壳、定位块和内胆三个部分分别进行成型,然后进行装配,其中外壳采用吹气成型工艺;定位块采用模压工艺进行成型;内胆采用二维缠绕成型工艺,然后进行装配。
8.高速电机用复合材料套筒属于薄壁高强度耐高温复合材料,上述现有技术中制备的套筒无法满足高速电机环境下的使用要求。
技术实现要素:9.本发明的目的是制备一种薄壁、高强度、耐高温复合材料套筒,其可增强高速转子整体化和强度,同时满足耐航空滑油和耐高温要求,并减轻转子的重量和减少电机运行过程中的摩擦损耗,以满足大功率、高转速航空电机转子的设计要求。
10.本发明的技术方案为:
11.所述一种高速电机用复合材料套筒,沿套筒径向分为三层,内层为浸渍耐高温树脂的无碱玻璃纤维布,中间层为浸渍耐高温树脂的高强度碳纤维,外层为浸渍耐高温树脂的无碱玻璃纤维布;
12.其中内层的无碱玻璃纤维预浸料沿模具0
°
轴缠绕,缠绕纤维至90
°
,公差
±
10
°
13.中间层中的碳纤维又分为两层,其中处于内侧的内层碳纤维束沿
±
88
°
环向缠绕,公差为
±2°
,处于外侧的外层碳纤维束纤维沿
±
65
°
环向缠绕,公差为
±2°
;
14.外层的玻璃纤维预浸料沿模具0
°
轴缠绕,缠绕纤维至90
°
,公差
±
10
°
。
15.进一步的,内层和外层的玻璃纤维预浸料分别缠绕两层,纤维结合处的重叠部分最小为2.5mm,最大为15.2mm。
16.进一步的,玻璃纤维预浸料含胶量控制在(40
±
3)%,碳纤维预浸料含胶量控制在(40
±
3)%。
17.进一步的,所述无碱玻璃纤维布为电子级玻璃纤维布1080、106或3313。
18.进一步的,所述高强度碳纤维型号采用m46jb(12k或6k)、m55jb(6k)、hms
‑
55x(12k)、t1000(12k)或t800(12k或6k)。
19.进一步的,所述耐高温树脂采用改性马来酰亚胺树脂、聚酰亚胺树脂或改性酚醛氰酸酯。
20.上述高速电机用复合材料套筒的制备方法,包括以下步骤:
21.步骤1:在芯轴上铺覆内层浸渍耐高温树脂的无碱玻璃纤维布:
22.将玻璃纤维预浸料含胶量控制在(40
±
3)%,将裁好的玻璃纤维预浸料沿芯轴模具0
°
轴缠绕,缠绕纤维至90
°
,公差
±
10
°
,共缠绕两层,纤维结合处的重叠部分最小为2.5mm到最大为15.2mm;
23.步骤2:浸渍耐高温树脂的高强度碳纤维在内层浸渍耐高温树脂的无碱玻璃纤维布上缠绕成型:
24.将碳纤维预浸料含胶量控制在(40
±
3)%;
25.内层碳纤维束沿
±
88
°
环向缠绕,公差为
±2°
;
26.外层碳纤维束纤维沿
±
65
°
环向缠绕1~3层,公差为
±2°
;
27.步骤3:在中间层上铺覆浸渍耐高温树脂的无碱玻璃纤维布:
28.将玻璃纤维预浸料含胶量控制在(40
±
3)%,将裁好的玻璃纤维预浸料沿芯轴模具0
°
轴缠绕,缠绕纤维至90
°
,公差
±
10
°
,共缠绕两层;纤维结合处的重叠部分最小为2.5mm到最大为15.2mm;
29.步骤4:固化工艺:
30.固化工艺分为两个阶段,第一阶段套筒在芯轴上采用真空热压罐进行固化,第二阶段将套筒从芯轴取下进行常压固化。
31.进一步的,第一阶段真空热压罐固化中,抽真空至真空度≥0.084mpa,加压至压力
(0.5~1.5)mpa。
32.进一步的,当内层和外层采用浸渍改性马来酰亚胺树脂的玻璃纤维布1080,中间层采用浸渍改性马来酰亚胺树脂的高强度碳纤维m46jb(12k);内层和外层的浸渍改性马来酰亚胺树脂的玻璃纤维1080预浸料分别缠绕两层;内层碳纤维束环向缠绕8层,外层碳纤维束环向缠绕1层时,具体固化工艺为:
33.第一阶段:套筒在芯轴上采用真空热压罐进行固化:
34.抽真空至真空度≥0.084mpa;
35.以5℃/min的升温速率升温到(160
±
5)℃,当温度达到65℃时进行加压,加压至(0.6~0.7)mpa;
36.当温度(160
±
5)℃,压力(0.6~0.7)mpa时,保持时间2小时;
37.第二阶段:将套筒从芯轴取下进行常压后固化;
38.以5℃/min的升温速率升温到(80
±
5)℃,在(80
±
5)℃下保温1h;
39.以3℃/min的升温速率升温到(180
±
5)℃,在(180
±
5)℃下保温2h;
40.以2℃/min的升温速率升温到(200
±
5)℃,在(200
±
5)℃下保温8h;
41.以2℃/min的升温速率升温到(250
±
5)℃,在(250
±
5)℃下保温4h。
42.进一步的,当内层和外层采用浸渍聚酰亚胺树脂的玻璃纤维布106,中间层采用浸渍聚酰亚胺树脂的高强度碳纤维hms
‑
55x(12k),内层和外层的浸渍聚酰亚胺树脂的玻璃纤维106预浸料分别缠绕两层;内层碳纤维束环向缠绕7层,外层碳纤维束环向缠绕2层时,具体固化工艺为:
43.第一阶段:套筒在芯轴上采用真空热压罐进行固化:
44.抽真空至真空度≥0.084mpa;
45.以5℃/min的升温速率升温到(200
±
5)℃,当温度达到165℃时进行加压,加压至(1.2~1.4)mpa;
46.且当温度(200
±
5)℃,压力(1.2~1.4)mpa,保持时间2小时;
47.以5℃/min的升温速率升温到(225
±
5)℃,且当温度(225
±
5)℃,压力(1.2~1.4)mpa,保持时间2小时;
48.以5℃/min的升温速率升温到(250
±
5)℃,且当温度(250
±
5)℃,压力(1.2~1.4)mpa,保持时间2小时;
49.以3℃/min的升温速率升温到(300
±
5)℃,且当温度(300
±
5)℃,压力(1.2~1.4)mpa,保持时间2小时;
50.以3℃/min的升温速率升温到(325
±
5)℃,且当温度(300
±
5)℃,压力(1.2~1.4)mpa,保持时间2小时;
51.以3℃/min的升温速率升温到(350
±
5)℃,且当温度(350
±
5)℃,压力(1.2~1.4)mpa,保持时间2小时;
52.第二阶段:将套筒从芯轴取下进行常压后固化;
53.以2℃/min的升温速率升温到(375
±
5)℃,在(375
±
5)℃下保温2h。
54.有益效果
55.本发明提供的复合材料套筒中树脂重量百分比为(35~42)%,套筒壁厚(1.5~2)mm。其表面光滑,无纤维翘曲及微裂纹出现,可耐温180℃以上。
56.本发明提供的复合材料套筒按astm d2290在室温下进行拉力测试,截取6.35mm
±
0.02mm宽套筒,其最小破坏应力≥944mpa。
57.本发明提供的复合材料套筒在180℃/15000h耐4050航空润滑油,其表面光滑,无纤维翘曲及微裂纹出现。
58.本发明的附加方面和优点将在下面的描述中部分给出,部分将从下面的描述中变得明显,或通过本发明的实践了解到。
附图说明
59.本发明的上述和/或附加的方面和优点从结合下面附图对实施例的描述中将变得明显和容易理解,其中:
60.图1:套筒主视图;
61.图2:套筒左视图;
62.图3:图1中的局部放大图。
具体实施方式
63.下面结合具体的实施例对本发明进行详细的说明,但不限于这些实施例。
64.实施例1
65.复合材料套筒内层(图1放大图ⅰ的a区域)为浸渍改性马来酰亚胺树脂的玻璃纤维布1080,中间层(图1放大图ⅰ的b+c区域)为浸渍改性马来酰亚胺树脂的高强度碳纤维m46jb(12k),外层(图1放大图ⅰ的d区域)为浸渍改性马来酰亚胺树脂的玻璃纤维布1080。
66.复合材料转子套筒的制备工艺如下:
67.(1)铺覆浸渍改性马来酰亚胺树脂的玻璃纤维布1080(图1放大图ⅰ的a区域)
68.将玻璃纤维预浸料含胶量控制在(40
±
3)%,将裁好的玻璃纤维1080预浸料沿芯轴模具0
°
轴缠绕,缠绕纤维至90
°
,公差
±
10
°
,共缠绕两层。纤维结合处的重叠部分最小为2.5mm到最大为15.2mm。
69.(2)浸渍改性马来酰亚胺树脂的高强度碳纤维在内层上缠绕成型(图1放大图ⅰ的b+c区域)
70.①
在缠绕工艺前,将m46jb纤维置于(70
±
5)℃烘干24h;
71.②
将碳纤维纱锭安装在可调节张力的纱箱内,将配制好的改性马来酰亚胺树脂倒入浸胶槽,直至改性马来酰亚胺树脂温度达到(105
±
5)℃;
72.③
将碳纤维依次通过浸胶槽,刮刀,导柱,缠绕头直到内层表面固定,设置计算机缠绕参数。碳纤维预浸料含胶量控制在(40
±
3)%。
73.图1放大图ⅰ的b区域:双束纤维沿
±
88
°
环向缠绕8层,公差为
±2°
。
74.图1放大图ⅰ的c区域:双束纤维沿
±
65
°
环向缠绕一层,公差为
±2°
。
75.(3)铺覆浸渍改性马来酰亚胺树脂的玻璃纤维布(图1放大图ⅰ的d区域)
76.将玻璃纤维预浸料含胶量控制在(40
±
3)%,将裁好的玻璃纤维1080预浸料在中间层上沿模具0
°
轴缠绕,缠绕纤维至90
°
,公差
±
10
°
,共缠绕两层。纤维结合处的重叠部分最小为2.5mm到最大为15.2mm。
77.(4)固化工艺
78.第一阶段:套筒在芯轴上采用真空热压罐进行固化。
79.抽真空至真空度≥0.084mpa。
80.以5℃/min的升温速率升温到(160
±
5)℃,当温度达到65℃时进行加压,加压至(0.6~0.7)mpa。
81.当温度(160
±
5)℃,压力(0.6~0.7)mpa时,保持时间2小时。
82.第二阶段:将套筒从芯轴取下进行常压后固化。
83.以5℃/min的升温速率升温到(80
±
5)℃,在(80
±
5)℃下保温1h;
84.以3℃/min的升温速率升温到(180
±
5)℃,在(180
±
5)℃下保温2h;
85.以2℃/min的升温速率升温到(200
±
5)℃,在(200
±
5)℃下保温8h;
86.以2℃/min的升温速率升温到(250
±
5)℃,在(250
±
5)℃下保温4h。
87.实施例2
88.复合材料套筒内表面(图1放大图ⅰ的a区域)为浸渍聚酰亚胺树脂的玻璃纤维布106,中间层(图1放大图ⅰ的b+c区域)为浸渍聚酰亚胺树脂的高强度碳纤维hms
‑
55x(12k),外表面(图1放大图ⅰ的d区域)为浸渍聚酰亚胺树脂的玻璃纤维布106。
89.复合材料转子套筒的制备工艺如下:
90.(1)铺覆浸渍聚酰亚胺树脂的玻璃纤维布106(图1放大图ⅰ的a区域)
91.将玻璃纤维预浸料含胶量控制在(40
±
3)%,将裁好的玻璃纤维预浸料沿芯轴模具0
°
轴缠绕,缠绕纤维至90
°
,公差
±
10
°
,共缠绕2层。纤维结合处的重叠部分最小为2.5mm到最大为15.2mm。
92.(2)浸渍改性马来酰亚胺树脂的高强度碳纤维在内层上缠绕成型(图1放大图ⅰ的b+c区域)
93.①
在缠绕工艺前,将碳纤维置于(70
±
5)℃下烘干24h;
94.②
将碳纤维纱锭安装在可调节张力的纱箱内,将配制好的耐高温树脂倒入浸胶槽,直至树脂的温度达到(95
±
5)℃。
95.③
将纤维依次通过浸胶槽,刮刀,导柱,缠绕头直到内层表面固定,设置计算机缠绕参数。碳纤维预浸料含胶量控制在(40
±
3)%。
96.图1放大图ⅰ的b区域:双束纤维沿
±
88
°
环向缠绕7层,公差为
±2°
。
97.图1放大图ⅰ的c区域:双束纤维沿
±
65
°
环向缠绕2层,公差为
±2°
。
98.(3)铺覆浸渍聚酰亚胺树脂的玻璃纤维布106(图1放大图ⅰ的d区域)
99.将玻璃纤维预浸料含胶量控制在(40
±
3)%,将裁好的玻璃纤维预浸料在中间层上沿模具0
°
轴缠绕,缠绕纤维至90
°
,公差
±
10
°
,共缠绕两层。纤维结合处的重叠部分最小为2.5mm到最大为15.2mm。
100.(4)固化工艺
101.第一阶段:套筒在芯轴上采用真空热压罐进行固化。
102.抽真空至真空度≥0.084mpa。
103.以5℃/min的升温速率升温到(200
±
5)℃,当温度达到165℃时进行加压,加压至(1.2~1.4)mpa。
104.且当温度(200
±
5)℃,压力(1.2~1.4)mpa,保持时间2小时。
105.以5℃/min的升温速率升温到(225
±
5)℃,且当温度(225
±
5)℃,压力(1.2~1.4)
mpa,保持时间2小时。
106.以5℃/min的升温速率升温到(250
±
5)℃,且当温度(250
±
5)℃,压力(1.2~1.4)mpa,保持时间2小时。
107.以3℃/min的升温速率升温到(300
±
5)℃,且当温度(300
±
5)℃,压力(1.2~1.4)mpa,保持时间2小时。
108.以3℃/min的升温速率升温到(325
±
5)℃,且当温度(300
±
5)℃,压力(1.2~1.4)mpa,保持时间2小时。
109.以3℃/min的升温速率升温到(350
±
5)℃,且当温度(350
±
5)℃,压力(1.2~1.4)mpa,保持时间2小时。
110.第二阶段:将套筒从芯轴取下进行常压后固化。
111.以2℃/min的升温速率升温到(375
±
5)℃,在(375
±
5)℃下保温2h。
112.尽管上面已经示出和描述了本发明的实施例,可以理解的是,上述实施例是示例性的,不能理解为对本发明的限制,本领域的普通技术人员在不脱离本发明的原理和宗旨的情况下在本发明的范围内可以对上述实施例进行变化、修改、替换和变型。