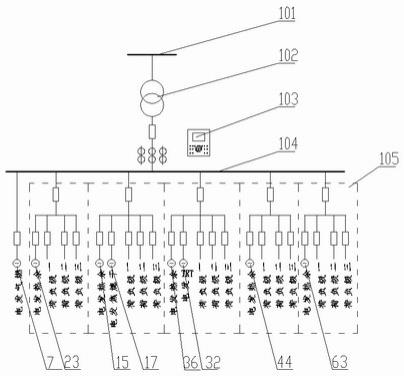
1.本发明申请属于综合能源利用领域,涉及钢铁企业综合能源利用,特别涉及一种基于微电网模式下的钢铁企业综合能源利用系统。
背景技术:2.钢铁企业存在能耗高、污染重、盈利能力弱等弊端,钢铁企业二次能源占总能耗的70%左右,钢铁企业在生产过程中伴随着大量的余热、余压、余气等可利用的可再生资源,但可再生能源具有间歇性和随机性的特点,对电网的调度工作提出了挑战;可再生能源的并网对大电网电压和频率的影响非常大,严重影响大电网电能质量;由于电力市场的不完善,可再生能源的利用率得不到提升,弃用率较高。
3.目前提升新能源消纳的最直接可靠的方式是利用储能电池将过剩的可再生能源存储起来在后续时段放电用于电力消耗。但是装备储能电池的投资成本较大,为了减小储能成本,结合多能源微电网特征以及钢铁企业用能特点建立一套基于微电网模式下的钢铁企业综合能源利用系统,能够避免因为储能电池容量的限制而造成可再生能源发电无法消纳的情况,以及储能电池生命后期污染处理困难的问题。
技术实现要素:4.本发明一种基于微电网模式下的钢铁企业综合能源利用系统,由大电网101,企业总降压站102,微电网测控单元103,微电网母线104以及多个微电网子系统105组成,所述大电网101通过企业总降压站102连接微电网母线104,微电网母线104连接各微电网子系统105和燃气发电机组7,各微电网子系统105通过局域网连接微电网测控单元103,微电网测控单元103还实时监测微电网母线104及大电网101负荷运行情况;所述每一个微电网子系统105均设有负荷配电单元和发电单元,并根据负荷重要程度划分为一级负荷、二级负荷及三级负荷;所述微电网子系统105根据钢铁工艺流程分为:焦化系统、烧结系统、高炉系统、转炉系统、热轧系统;焦化系统的发电单元由干熄焦发电17和焦炉余热发电15组成,焦炉余热发电15的热源包含上升管余热13和焦炉烟道余热14;烧结系统的发电单元为烧结余热发电23,热源包含冷却机余热21和烧结烟道余热22;高炉系统的发电单元由炉顶余压发电32及高炉余热发电36组成,高炉余热发电36热源为高炉熔渣显热35及热风炉烟道余热34;转炉系统的发电单元为炼钢余热发电44,其热源为炼钢烟气余热43;热轧系统的发电单元为热轧余热发电63,其热源为加热炉余热61及冷床余热62;所述干熄焦发电17、焦炉余热发电15、烧结余热发电23、高炉余热发电36、炼钢余热发电44、热轧余热发电63均配有余热锅炉91、电热锅炉92、蒸汽蓄热器93和汽轮发电机94,所述余热锅炉91的热源收集自相应生产系统的余热资源,产出的蒸汽送至蒸汽蓄热器93的蒸汽入口,蒸汽蓄热器93的蒸汽入口还连接有电热锅炉92,蒸汽蓄热器93的蒸汽出口连接汽轮发电机94,发电机出口并入各自微电网子系统105;
所述燃气发电机组7作为微电网调峰机组,所需燃料为钢铁企业副产品焦炉煤气、高炉煤气和转炉煤气,分别来自焦炉煤气柜12、高炉煤气柜33和转炉煤气柜42,焦炉煤气由焦炉1生产,经焦炉煤气管道11送入焦炉煤气柜12;高炉煤气由高炉3生产,经高炉煤气管道31送入高炉煤气柜33;转炉煤气由转炉4生产,经转炉煤气管道41送入转炉煤气柜42。
附图说明
5.图1为本发明申请系统工艺流程分布图;图2为本发明申请余热发工艺示意图;图3为本发明申请电网单线图。
6.图中:1. 焦炉,2.烧结机,3.高炉,4.转炉,5.连铸机,6.热轧机,7. 燃气发电机组,11. 焦炉煤气管道,12. 焦炉煤气柜,13. 上升管余热,14. 焦炉烟道余热,15. 焦炉余热发电,17,干熄焦发电,21. 冷却机余热,22. 烧结烟道余热,23. 烧结余热发电,31. 高炉煤气管道,32. 炉顶余压发电,33. 高炉煤气柜,34. 热风炉烟道余热,35.高炉熔渣显热,36. 高炉余热发电,41. 转炉煤气管道,42. 转炉煤气柜,43. 炼钢烟气余热,44. 炼钢余热发电,61. 加热炉余热,62. 冷床余热,63. 热轧余热发电,91. 余热锅炉,92电热锅炉,93. 蒸汽蓄热器,94. 汽轮发电机,101. 大电网,102. 总降压站,103. 微电网测控单元,104. 微电网母线,105. 微电网子系统。
具体实施方式
7.本发明一种基于微电网模式下的钢铁企业综合能源利用系统,由大电网101,企业总降压站102,微电网测控单元103,微电网母线104以及多个微电网子系统105组成,所述大电网101通过企业总降压站102连接微电网母线104,微电网母线104连接各微电网子系统105和燃气发电机组7,各微电网子系统105通过局域网连接微电网测控单元103,微电网测控单元103还实时监测微电网母线104及大电网101运行负荷情况;所述每一个微电网子系统105均设有负荷配电单元和发电单元,并根据负荷重要程度划分为一级负荷、二级负荷及三级负荷;所述微电网子系统105根据钢铁工艺流程分为:焦化系统、烧结系统、高炉系统、转炉系统、热轧系统;焦化系统的发电单元由干熄焦发电17和焦炉余热发电15组成,焦炉余热发电15的热源包含上升管余热13和焦炉烟道余热14;烧结系统的发电单元为烧结余热发电23,热源包含冷却机余热21和烧结烟道余热22;高炉系统的发电单元由炉顶余压发电32及高炉余热发电36组成,高炉余热发电36热源为高炉熔渣显热35及热风炉烟道余热34;转炉系统的发电单元为炼钢余热发电44,其热源为炼钢烟气余热43;热轧系统的发电单元为热轧余热发电63,其热源为加热炉余热61及冷床余热62;所述干熄焦发电17、焦炉余热发电15、烧结余热发电23、高炉余热发电36、炼钢余热发电44、热轧余热发电63均配有余热锅炉91、电热锅炉92、蒸汽蓄热器93和汽轮发电机94,所述余热锅炉91的热源收集自相应生产系统的余热资源,产出的蒸汽送至蒸汽蓄热器93的蒸汽入口,蒸汽蓄热器93的蒸汽入口还连接有电热锅炉92,蒸汽蓄热器93的蒸汽出口连接汽轮发电机94,发电机出口并入各自微电网子系统105;所述燃气发电机组7作为微电网调峰机组,所需燃料为钢铁企业副产品焦炉煤气、
高炉煤气和转炉煤气,分别来自焦炉煤气柜12、高炉煤气柜33和转炉煤气柜42,焦炉煤气由焦炉1生产,经焦炉煤气管道11送入焦炉煤气柜12;高炉煤气由高炉3生产,经高炉煤气管道31送入高炉煤气柜33;转炉煤气由转炉4生产,经转炉煤气管道41送入转炉煤气柜42。
8.各微电网子系统105的发电单元发电电量采用自发自用,自用有余时送入微电网母线104,发电量不足时由微电网母线104提供电能,各微电网子系统105供电及用电负荷通过微电网母线104进行平衡;微电网母线104出现电能过剩时开启余热发电系统的电热锅炉92,产生的蒸汽存入蒸汽蓄热器93,当出现全部电热锅炉92满负荷以及蒸汽蓄热器93满容量仍不能消纳过剩电量时,微电网母线104将通过企业总降压站102返送到大电网101;当微电网母线104在正常发电量不能满足供电负荷需求时,一是通过微电网测控单元103向各微电网子系统105发出指令,释放蒸汽蓄热器93存储的蒸汽,加大汽轮发电机94做功出力;二是由燃气发电机组7增加发电量;三是通过增加大电网101供电量来满足企业供电负荷需求,最后在极端情况下仍然无法满足供电负荷需求时,将通过微电网测控单元103精准依次切除相应容量的三级负荷,确保一级负荷的安全稳定用电需求。
9.本发明一种基于微电网模式下的钢铁企业综合能源利用系统,根据钢铁企业余能分布结构,就地组建微电网子系统,形成内部自发自用余电上网结构,采用蒸汽蓄热加电热模式解决可再生能源具有间歇性和随机性的问题,同时利用燃气发电机煤气柜存储煤气作为调峰机组,以及接入大电网来平衡企业内部微电网用电保障。本发明申请充分结合钢铁企业用能及余能结构,可最大限度地发掘余能潜力。