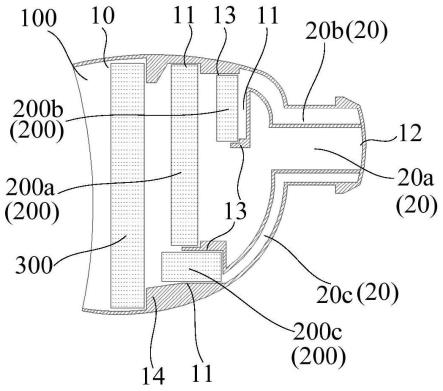
1.本技术实施例涉及蓝牙耳机结构技术领域,尤其涉及一种耳机前壳及蓝牙耳机。
背景技术:2.相比于有线耳机,蓝牙耳机具有蓝牙模块、电池等模块。由于耳机壳内部空间很有限,难以在有限的空间内布置更多的器件。在传统的真无线立体声(true wireless stereo,tws)蓝牙耳机中,如图1所示,每个蓝牙耳机包括前壳1、后壳2、一个发声单元3、一个导音通道4等模块,发声单元3安装在由前壳1和后壳2围成的容纳空间内,导音通道4形成于前壳1内,发声单元3产生的声波通过导音通道4传送至外部,只有一个发声单元3的蓝牙耳机音质欠佳。在传统的颈挂式蓝牙耳机中,由于耳机壳的容纳空间有限,耳机壳内有多个发声单元而没有导音通道,不同发声单元产生声波的频段是不同的,不同频段声波之间存在干涉,使得音质欠佳,还增加了颈挂式线缆,将电池等模块转移至线缆中。业界难以提供一种兼具体积较小、具备多个发声单元、音质较好的蓝牙耳机。
技术实现要素:3.本技术实施例提供一种耳机前壳及蓝牙耳机,解决了现有技术难以提供一种兼具体积较小、具备多个发声单元、音质较好的蓝牙耳机的问题。
4.为达到上述目的,本技术实施例采用如下技术方案:
5.第一方面,本技术实施例提供一种耳机前壳,其包括前壳体和多个导音管,多个导音管位于前壳体内,多个导音管的内腔之间相互独立,前壳体和多个导音管为一体成型结构。相邻的导音管和前壳体之间具有共同管壁,相邻两个导音管之间具有共同管壁。前壳体内设有多个安装位,安装位用于安装发声单元,前壳体具有出音嘴,每个导音管和一个或多个安装位对应设置,每个导音管由出音嘴延伸至与导音管对应的安装位。
6.本技术实施例提供的耳机前壳中,前壳体和多个导音管为一体成型结构,导音管和前壳体之间、相邻两个导音管之间有共同管壁,多个导音管的内腔相互独立,相比于将多个导音管独立组装在耳机壳内的方式,或者相比于在出音嘴内设置隔板以形成不同音腔的方式,本技术实施例对前壳体内部空间利用率较高,减小导音管的空间占比,该耳机前壳的体积较小,后续组装难度较低,并增强结构强度和稳定性。前壳体内有多个与导音管对应的安装位,以在前壳体的有限空间中安装不同频段的发声单元,不同发声单元产生的声波通过各自导音管传送至出音嘴,多个导音管由出音嘴延伸至安装位,较好地隔断不同频段的声波,降低不同频段声波之间的干涉,以获得较好音质,用户体验增强。
7.结合第一方面,在第一方面的第一种可能的实现方式中,安装位处设有用于安装发声单元的第一支架,前壳体和第一支架为一体成型结构。无需进行支架结构的装配,直接将发声单元安装在第一支架上即可,提升装配的便利性以提升结构稳定性。
8.结合第一方面或第一方面的第一种可能的实现方式,在第一方面的第二种可能的实现方式中,前壳体内设有用于安装电池的第二支架,第二支架设于安装位背对出音嘴的
一侧,前壳体和第二支架为一体成型结构。无需进行支架结构的装配,直接将电池安装在第二支架上即可,提升装配的便利性以提升结构稳定性。
9.结合第一方面至第一方面的第二种可能的实现方式中任一项,在第一方面的第三种可能的实现方式中,耳机前壳为金属件。金属制作的耳机前壳可减薄壁厚,降低导音管空间占比。金属耳机前壳的刚度较高,不容易变形,利于减少谐振的产生,实现音质高保真,提升耳机音质,并且提升结构强度。或者,耳机前壳为高分子材料件。也能获得兼具体积较小、具备多个发声单元安装位和多个导音管的耳机前壳。
10.结合第一方面至第一方面的第三种可能的实现方式中任一项,在第一方面的第四种可能的实现方式中,多个安装位沿预定方向依次排布。这种方式便于不同发声单元的安装。或,至少一个安装位与另外一个安装位沿发声单元的轴向排布。在发声单元的轴向投影上,其中两个安装位的发声单元具有重叠区域。
11.结合第一方面至第一方面的第四种可能的实现方式中任一项,在第一方面的第五种可能的实现方式中,至少一个导音管跟随前壳体的侧壁设置为弯曲流道,导音管的形状依据前壳体内部剩余空间自由设置。依据前壳体侧壁的延伸方向去设置导音管,充分利用前壳体内部空间。
12.结合第一方面至第一方面的第五种可能的实现方式中任一项,在第一方面的第六种可能的实现方式中,多个导音管沿预定方向依次排布。多个导音管沿直线排布。或者,多个导音管沿周向排布。
13.结合第一方面至第一方面的第六种可能的实现方式中任一项,在第一方面的第七种可能的实现方式中,至少一个导音管被套设于另外一个导音管以内。这种方式适用于其中两个发声单元具有重叠区域的情况,不同发声单元发出的声波通过各自的导音管传送至出音嘴,降低不同频段声波干涉情况。
14.结合第一方面至第一方面的第七种可能的实现方式中任一项,在第一方面的第八种可能的实现方式中,导音管的管壁的横截面沿直线、弧线、波浪线或圆形延伸,具体形状结合前壳体的横截面形状、导音管的数量、多个发声单元的布局按需设置。
15.结合第一方面至第一方面的第八种可能的实现方式中任一项,在第一方面的第九种可能的实现方式中,当耳机前壳为金属件时,前壳体的外表面设有注塑层。有效遮蔽了粗糙的凹凸面,得到光滑表面。
16.结合第一方面至第一方面的第九种可能的实现方式中任一项,在第一方面的第十种可能的实现方式中,当耳机前壳为金属件时,导音管具有通过磨粒流抛光的内表面。磨粒流可完成抛光和去毛刺加工。或者,当耳机前壳为金属件时,导音管的内表面设有电镀层,电镀层有一定的填平效果。这两种方式可降低导音管内表面的粗糙度,以降低表面凹凸不平对声音传导的阻抗效应,提升输出音质。
17.结合第一方面至第一方面的第十种可能的实现方式中任一项,在第一方面的第十一种可能的实现方式中,耳机前壳通过三维立体打印成型。采用三维立体打印直接成型出耳机前壳,自由设计前壳体内部结构,提高空间利用率。
18.结合第一方面至第一方面的第十种可能的实现方式中任一项,在第一方面的第十二种可能的实现方式中,耳机前壳由三维立体打印成型得到的前壳坯体,通过失蜡铸造成型。该方式可一体成型出具有前壳体和多个导音管的耳机前壳。
19.结合第一方面至第一方面的第十种可能的实现方式中任一项,在第一方面的第十三种可能的实现方式中,耳机前壳由三维立体打印成型得到的前壳模具,通过铸造或注塑成型。该方式可一体成型出具有前壳体和多个导音管的耳机前壳。
20.第二方面,本技术实施例提供一种蓝牙耳机,包括上述的耳机前壳、多个发声单元和耳机后壳,多个发声单元一一对应地安装于多个安装位,耳机前壳相对出音嘴的一端连接于耳机后壳。由于本蓝牙耳机采用了上述所有实施例的全部技术方案,因此同样具有上述实施例的技术方案所带来的所有有益效果,在此不再一一赘述。
21.结合第二方面,在第二方面的第一种可能的实现方式中,耳机前壳内设有电池,电池设于发声单元背对出音嘴的一侧,电池和多个发声单元电连接。电池用于给发声单元等模块供电。电池位于所有发声单元背对出音嘴的一侧,不影响发声单元工作,充分利用前壳体内部空间。
附图说明
22.图1为传统tws蓝牙耳机的立体分解图;
23.图2为本技术实施例提供的耳机前壳的结构示意图;
24.图3为图2的沿a-a线剖视图;
25.图4为图2的耳机前壳在组装发声单元和电池后的结构示意图;
26.图5中的(a)至(h)分别为本技术不同实施例提供的耳机前壳中的前壳体和导音管的剖视图;
27.图6中的(a)、(b)分别为本技术实施例提供的耳机前壳中的前壳体外表面在注塑前后的结构示意图;
28.图7中的(a)至(c)分别为本技术实施例提供的耳机前壳中的导音管内表面在抛光前、抛光后和电镀后的结构示意图;
29.图8中的(a)至(c)分别为本技术实施例提供的耳机前壳中的导音管内表面在抛光前、抛光后和电镀后的光学显微镜图。
具体实施方式
30.本技术实施例提供一种耳机前壳,用于与耳机后壳配合使用,耳机前壳和耳机后壳组装后可围成容纳空间,发声单元、电池和电路板等模块安装于容纳空间内。该耳机前壳可用于蓝牙耳机或有线耳机,其中,蓝牙耳机可以为tws蓝牙耳机或颈挂式蓝牙耳机,tws蓝牙耳机的佩戴舒适性更好。
31.图2为本技术实施例提供的耳机前壳的结构示意图;图3为图2的沿a-a线剖视图;
32.图4为图2的耳机前壳在组装发声单元和电池后的结构示意图。
33.参阅图2,本技术实施例提供的一种耳机前壳100,其包括前壳体10和多个导音管20,多个导音管20位于前壳体10内,多个导音管20的内腔之间相互独立,前壳体10和多个导音管20为一体成型结构。结合图3,相邻的导音管20和前壳体10之间具有共同管壁21,相邻两个导音管20之间具有共同管壁22。参阅图2、图4,前壳体10内设有多个安装位11,安装位11用于安装发声单元200,前壳体10具有出音嘴12,每个导音管20和一个或多个安装位11对应设置,每个导音管20由出音嘴12延伸至与导音管20对应的安装位11。
34.本技术实施例提供的耳机前壳100中,前壳体10和多个导音管20为一体成型结构,导音管20和前壳体10之间、相邻两个导音管20之间有共同管壁21、22,多个导音管20的内腔相互独立,相比于将多个导音管独立组装在耳机壳内的方式,或者相比于在出音嘴内设置隔板以形成不同音腔的方式,本技术实施例对前壳体10内部空间利用率较高,减小导音管20的空间占比,该耳机前壳100的体积较小,后续组装难度较低,并增强结构强度和稳定性。前壳体10内有多个与导音管20对应的安装位11,以在前壳体10的有限空间中安装不同频段的发声单元200,不同发声单元200产生的声波通过各自导音管20传送至出音嘴12,多个导音管20由出音嘴12延伸至安装位11,较好地隔断不同频段的声波,降低不同频段声波之间的干涉,以获得较好音质,用户体验增强。
35.其中,一个导音管20可以和一个安装位11对应设置,一个导音管20还可以和两个以上的安装位11对应设置。发声单元200安装在安装位11。前一种情况是一个发声单元200配置一个导音管20。后一种情况是两个以上的发声单元200配置一个导音管20,这种情况考虑空间限制或者结构设计原因。
36.示例性的,三个发声单元配置三个导音管,三个导音管和三个安装位一一对应设置。或者,三个发声单元配置两个导音管,也就是其中两个发声单元共用一个导音管,其中一个导音管和两个安装位对应,另外一个导音管和一个安装位对应。
37.其中,发声单元200是耳机的发声部分,起到将电信号转换成声音信号的作用,可以是动圈单元、动铁单元、平板单元、静电单元等等。参阅图4,多个发声单元200是指两个以上发声单元200,通常配置为分别输出不同频段声波的发声单元200,比如配置低频发声单元、中频发声单元和高频发声单元,或者配置中低频发声单元和中高频发声单元,以获得低、中、高频段的声波。不同频段发声单元的排布由导音管的长度、截面积大小等因素决定。一般而言,导音管的内部空腔体积与发声单元的频率成负相关,大体积导音管对应低频发声单元。
38.其中,耳机前壳100中的前壳体10和导音管20的壁厚大于或等于0.1mm,该前壳体10集成了多个导音管20,容易成型,可满足耳机前壳100的强度需求。示例性的,前壳体10和导音管20的壁厚可以为0.1mm、0.3mm、0.5mm、0.8mm、1mm、1.5mm、2mm或3mm等。
39.在装配发声单元200到前壳体10时,安装位11处设有用于安装发声单元200的第一支架13,前壳体10和第一支架13为一体成型结构。相比于将支架结构独立组装到耳机壳的方式,本技术实施例第一支架13一体成型于前壳体10内,无需进行支架结构的装配,直接将发声单元200安装在第一支架13上即可,提升装配的便利性以提升结构稳定性。
40.示例性的,第一支架13可以为在导音管20的一端延伸形成的围壁,围壁内形成有安装槽,发声单元200和第一支架13的安装槽相适配,以便于发声单元200容纳在安装槽内,通过粘接、紧配合或卡扣方式将发声单元200固定在安装位11。发声单元200大致呈圆柱状,第一支架13具有圆柱状的安装槽,将发声单元200放置在安装槽内,这样容易装配,结构紧凑。或者,发声单元200呈长方体形,第一支架13的安装槽呈相适配的长方体形。此外,发声单元和第一支架的安装槽还可以设置为其它形状。
41.在装配电池300到前壳体10时,前壳体10内设有用于安装电池300的第二支架14,第二支架14设于安装位11背对出音嘴12的一侧,前壳体10和第二支架14为一体成型结构。相比于将支架结构独立组装到耳机壳的方式,本技术实施例第二支架14一体成型于前壳体
10内,无需进行支架结构的装配,直接将电池300安装在第二支架14上即可,提升装配的便利性以提升结构稳定性。
42.示例性的,第二支架14可以为在前壳体10内壁凸出形成的凸台,电池300贴合在凸台的一侧。电池300可通过粘接、紧配合或卡扣方式固定在前壳体10上。电池300位于所有发声单元200背对出音嘴12的一侧,不影响发声单元200工作。为了充分利用前壳体10内部空间,可以使电池300的径向尺寸尽量接近前壳体10的内壁,以提升电池300的容量。
43.在选用耳机前壳100的材料时,耳机前壳100可以为金属件。金属制作的耳机前壳100可减薄壁厚,降低导音管20空间占比。相比于高分子材料制作的耳机前壳100,在同样壁厚条件下,金属耳机前壳100的刚度较高,不容易变形,利于减少谐振的产生,实现音质高保真,提升耳机音质,并且提升结构强度。耳机前壳100采用金属制作时,可为不锈钢、铝合金、钛合金、镁合金、铜合金等金属材料。
44.或者,耳机前壳100可以为高分子材料件。高分子材料可以是塑料、橡胶或合成纤维等等。在选用高分子材料制作时,也能获得兼具体积较小、具备多个发声单元200安装位11和多个导音管20的耳机前壳100。
45.在布置多个安装位时有多种不同的实现方式。第一种多个安装位的排布方式是:多个安装位11沿预定方向依次排布。这种方式便于不同发声单元200的安装。示例性的,多个安装位11沿直线排布,如图4中的发声单元200a和发声单元200c对应的两个安装位11就是沿直线排布。或者,多个安装位11沿周向排布。这里的周向是绕发声单元200的轴线的旋转方向。
46.第二种多个安装位的排布方式是:至少一个安装位11与另外一个安装位11沿发声单元200的轴向排布。在发声单元200的轴向投影上,其中两个安装位11的发声单元200具有重叠区域,这样不会对两个发声单元200的发声造成影响,也充分利用前壳体10的内部空间。
47.示例性的,参阅图4,发声单元200a的径向尺寸大于发声单元200b的径向尺寸,将发声单元200a、发声单元200b和出音嘴12依次排布,在发声单元的轴向上发声单元200b的投影在发声单元200a的投影以内,发声单元200a和发声单元200b在轴向间隔设置,这样不会影响两个发声单元的出音。此外,这两个发声单元可以同轴或者两者轴线间隔设置。
48.在布置多个导音管时有多种不同的实现方式。第一种多个导音管的布置方式是:参阅图4,至少一个导音管20跟随前壳体10的侧壁设置为弯曲流道,导音管20的形状依据前壳体10内部剩余空间自由设置。依据前壳体10侧壁的延伸方向去设置导音管20,充分利用前壳体10内部空间。示例性的,前壳体10内沿直线依次配置三个导音管20a、20b、20c,在前壳体10的纵向截面上,位于两个端部的导音管20b、20c依据前壳体10的侧壁设置为弯曲流道。其中,纵向截面就是与发声单元200的轴线平行的截面。
49.第二种多个导音管的布置方式是:多个导音管20沿预定方向依次排布。示例性的,参阅图3、图5中的(a)至(e),两个或三个或四个导音管20沿直线排布。或者,参阅图5中的(f),四个导音管20沿周向排布。
50.第三种多个导音管的布置方式是:参阅图5中的(g)、(h),至少一个导音管20d被套设于另外一个导音管20e以内。这种方式适用于其中两个发声单元具有重叠区域的情况,不同发声单元发出的声波通过各自的导音管20传送至出音嘴,降低不同频段声波干涉情况。
51.可以理解的,在布置多个导音管时,还可以选用其中两种方式组合,或者选用三种方式组合。比如,参阅图5中的(g)、(h),若干个导音管20沿直线排布,并且其中一个导音管20d被若个个导音管中的一个导音管20e包围设置。
52.在设置导音管20的管壁时,导音管20的管壁的横截面沿直线、弧线、波浪线或圆形延伸,具体形状结合前壳体10的横截面形状、导音管20的数量、多个发声单元200的布局按需设置。
53.示例性的,参阅图3、图5中的(c),前壳体10的横截面大致呈椭圆形、圆形或其它形状,前壳体10内沿直线排布有三个导音管20,位于前壳体10内的两个共同管壁22的横截面均沿弧形延伸。或者,参阅图5中的(d),前壳体10内沿直线排布有三个导音管20,位于前壳体10内的其中一个共同管壁22的横截面沿波浪线延伸,另外一个共同管壁22沿直线延伸。
54.在一些实施例中,为了使前壳体10的外表面更光滑,当耳机前壳为金属件时,如图6中的(a)所示,耳机前壳中的前壳体外表面在没有注塑时为凹凸面,如图6中的(b)所示,前壳体10的外表面15设有注塑层151。在制作好前壳体坯体时,在前壳体10的外表面15注塑形成注塑层151,有效遮蔽了粗糙的凹凸面,使得耳机前壳100和耳机后壳的粗糙度更接近,以得到光滑表面。
55.在一些实施例中,为了使导音管的内表面更光滑以提升导音性能,当耳机前壳为金属件时,如图7中的(a)所示,导音管20的初始内表面16’为凹凸面,参阅图7中的(b),导音管20具有通过磨粒流抛光的内表面16。磨粒流抛光是通过一种挤压方法,其磨料具有流动性,其中的颗粒不断地对工件表面进行研磨,完成抛光加工。或者,当耳机前壳100为金属件时,如图7中的(c)所示,导音管20的内表面16设有电镀层17,比如镀铜或铜合金或其它金属,电镀层17有一定的填平效果。这两种方式可降低导音管20内表面的粗糙度,以降低表面凹凸不平对声音传导的阻抗效应,从而提升输出音质。图8中的(a)至(c)分别为导音管内表面在抛光前、抛光后和电镀后的光学显微镜图,可以清楚地看出:在抛光前、抛光后和电镀后,导音管表面由凹凸面逐渐变为平面,粗糙度逐渐降低。
56.在制作耳机前壳时有多种不同的实现方式。第一种制作耳机前壳的方式是:耳机前壳100通过三维立体打印成型。采用三维立体打印直接成型出耳机前壳100,摆脱了对传统注塑成型脱模需求的约束,自由设计前壳体10内部结构,提高空间利用率。
57.具体步骤包括:建立耳机前壳100的三维模型;依据耳机前壳100的三维模具进行三维立体打印,得到耳机前壳坯体;对耳机前壳坯体进行后处理,以获得具有光滑表面的耳机前壳。其中,后处理方式可以是计算机数字化控制(computer numerical control,cnc)加工、打磨、抛光、电镀、物理气相沉积(physical vapor deposition,pvd)、烤漆、注塑等,这些后处理方式都能将耳机前壳坯体加工成具有光滑表面的耳机前壳。
58.第二种制作耳机前壳的方式是:耳机前壳100由三维立体打印成型得到的前壳坯体,通过失蜡铸造成型。该方式可一体成型出具有前壳体10和多个导音管20的耳机前壳100。具体步骤包括:建立耳机前壳100的三维模型;依据耳机前壳100的三维模具进行三维立体打印,得到预成型坯体,该预成型坯体可以为高分子材料件;将预成型坯体进行失蜡铸造成型出耳机前壳坯体;对耳机前壳坯体进行后处理,以获得具有光滑表面的耳机前壳。后处理方式可以是cnc加工、打磨、抛光、电镀、pvd、烤漆、注塑等。
59.第三种制作耳机前壳的方式是:耳机前壳100由三维立体打印成型得到的前壳模
具,通过铸造或注塑成型。该方式可一体成型出具有前壳体10和多个导音管20的耳机前壳100。具体步骤包括:建立前壳模具的三维模型;依据前壳模具的三维模型进行砂型三维立体打印,得到前壳模具;利用前壳模具进行铸造、注塑等工艺成型前壳坯体;对前壳坯体进行后处理,以获得具有光滑表面的耳机前壳。后处理方式可以是cnc加工、打磨、抛光、电镀、pvd、烤漆、注塑等。
60.相比于传统技术将导音管、用于安装发声单元和电池的支架结构等结构逐个组装在耳机前壳中,本技术以上三个实施例的耳机前壳100可以将导音管20、第一支架13、第二支架14等结构集成地成型在耳机前壳100中,降低了后续组装难度,提升结构可靠性。
61.参阅图2至图4,本技术实施例提供一种蓝牙耳机,包括上述的耳机前壳100、多个发声单元200和耳机后壳(图未示),多个发声单元200一一对应地安装于多个安装位11,耳机前壳100相对出音嘴12的一端连接于耳机后壳。由于本蓝牙耳机采用了上述所有实施例的全部技术方案,因此同样具有上述实施例的技术方案所带来的所有有益效果,在此不再一一赘述。
62.其中,多个发声单元200配置为可分别输出不同频段声波的发声单元200,比如配置低频发声单元、中频发声单元和高频发声单元,或者配置中低频发声单元和中高频发声单元,以获得低、中、高频段的声波。耳机前壳100和耳机后壳之间可通过粘接或卡扣等方式连接。
63.在一些实施例中,参阅图4,耳机前壳100内设有电池300,电池300设于发声单元200背对出音嘴12的一侧,电池300和多个发声单元200电连接。电池300用于给发声单元200等模块供电。电池300位于所有发声单元200背对出音嘴12的一侧,不影响发声单元200工作,充分利用前壳体10内部空间。此外,耳机前壳100内还设有电路板(图未示),电路板和发声单元200、电池300电连接,电路板用于驱动发声单元200。电路板可设于电池300背对发声单元200的一侧。
64.最后应说明的是:以上所述,仅为本技术的具体实施方式,但本技术的保护范围并不局限于此,任何在本技术揭露的技术范围内的变化或替换,都应涵盖在本技术的保护范围之内。因此,本技术的保护范围应以所述权利要求的保护范围为准。