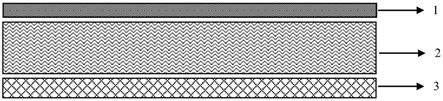
1.本实用新型涉及汽车内饰材料,尤其是一种汽车门板内饰用低气味复合表皮。
背景技术:2.目前汽车门板内饰用复合材料,一般由表皮层、海绵层、面料层组成,表皮层与海绵层之间、海绵层与面料层之间通常采用火焰复合工艺进行贴合。所用海绵层为火焰复合绵,包括聚醚型海绵和聚酯型海绵,聚酯型海绵复合后的产品具有较高的拉伸强度、撕裂强度、复合牢度等,性能优越,但其需要高压设备发泡、得材率低、成本高;聚醚型海绵发泡设备简单、成本低,复合后产品的拉伸强度、撕裂强度、复合牢度也可以达到使用要求,所以聚醚型海绵在行业内的应用比较广泛,但与聚酯型海绵不同,为了得到一定复合牢度的复合产品,聚醚型海绵火焰复合时需添加大量的火焰复合剂,而火焰复合剂中含有大量易挥发的小分子物质,使得最终得到的复合产品voc高、气味大,越来越无法满足人们对汽车内饰材料的环保性要求。
3.中国专利cn111154066a提供了一种低voc海绵及制备方法及应用,通过在海绵配方中添加光电子催化剂rgo/tio2制备了一种低voc海绵,继而控制聚氨酯海绵复合后的voc释放问题,但其对海绵在火焰复合过程中火焰复合剂的添加情况未进行具体描述,如果还是常规的火焰复合剂用量,那么由火焰复合剂产生的voc及气味问题就没有得到解决。
4.pv3900
‑
2000为常用气味测试标准,气味评价采用6级评价标准:1级表示无气味,2级表示有气味,但不扰人,3级表示有明显气味,但仍不扰人,4级表示有扰人气味,5级表示有强烈的扰人气味,6级表示无法忍受;参与气味测评人员为3~5人,测评结果可采用半级描述,取平均值作为最终气味等级结果,等级越低,气味越小。
技术实现要素:5.本实用新型所要解决的技术问题是,现有技术中存在的由火焰复合工艺制备的汽车门板用复合表皮气味大、voc高的问题,提供一种低气味复合表皮,该复合表皮具有在复合牢度一定时气味更小、voc更低的优点。
6.为解决上述技术问题,本实用新型采用的技术方案如下:一种低气味复合表皮,其特征在于,自上而下依次为pvc层1、新型海绵层2、针织布层3;其中,所述的pvc层1、新型海绵层2、针织布层3之间通过火焰复合工艺贴合;所述新型海绵层2为低气味、低voc火焰复合用聚氨酯海绵。
7.上述技术方案中,优选地,所述新型海绵层2的气味等级为3.5~4.0、tvoc为3800~5500μg/m3。
8.上述技术方案中,优选地,所述新型海绵层2的厚度为2.0~6.0mm。
9.上述技术方案中,优选地,所述pvc层1的厚度为0.8~1.3mm。
10.上述技术方案中,优选地,所述针织布层3选自纬编布或经编布中的一种。
11.上述技术方案中,优选地,所述针织布层3的厚度为0.3~0.5mm。
12.上述技术方案中,优选地,所述新型海绵层2为聚氨酯火焰复合海绵,由组分i和组分ii组成,组分i与组分ii的重量份数比为100:20~60,其中组分i中以重量份数计包括聚醚多元醇a:30~60份,聚醚多元醇b:30~60份,聚合物多元醇c:10~40份,水:1~5份,胺类催化剂:0.1~1份,锡类催化剂:0.1~1份,泡沫稳定剂:0.5~2份,阻燃剂:2~12份,火焰复合剂:0.5~5份;组分ii以重量份数计包括异氰酸酯20~60份;其中,聚醚多元醇a分子量为1000~3000,不饱和度为0.01~0.2mmol/g,官能度为2~4;聚醚多元醇b的分子量为1300~2800,不饱和度为0.01~0.2mmol/g,官能度2~4,且聚醚多元醇b是一种含有酯键结构的聚醚多元醇,酯键含量以重量百分数计为3~15%,聚醚多元醇b以小分子醇为起始剂,由环氧烷烃和小分子有机酸共聚而成;聚合物多元醇c的分子量为4000~7000,官能度为2~4,固含量为28%~50%;异氰酸酯选自2,6
‑
二甲基苯基二异氰酸酯或2,4
‑
二甲基苯基二异氰酸酯中的至少一种。
13.上述技术方案中,优选地,所述新型海绵层2的制备方法,包括如下步骤:
14.a)制备聚醚多元醇b:
15.(1)100重量份数的小分子醇与500~900重量份数的环氧烷烃反应形成低分子聚醚多元醇,反应时间6~10h,反应温度100~120℃;
16.(2)由步骤(1)制备得到的低分子聚醚多元醇100份与50~150重量份数的小分子有机酸聚合反应形成多元醇i,反应时间4~8h,反应温度110~130℃;
17.(3)由步骤(2)制备得到的多元醇i 100份与50~200重量份数的环氧烷烃反应形成聚醚多元醇b,反应时间6~10h,反应温度110~135℃;
18.b)制备组分i:
19.在容器a中按照重量份数计算,加入聚醚多元醇a:30~60份,聚醚多元醇b:30~60份,聚合物多元醇c:10~40份,水:1~5份,胺类催化剂:0.1~1份,锡类催化剂:0.1~1份,泡沫稳定剂:0.5~2份,阻燃剂:2~12份,火焰复合剂:0.5~5份,均匀搅拌,搅拌速度为2000~3000rpm/min,混合物料温度为20~30℃;
20.c)制备组分ii:
21.在容器a中加入异氰酸酯重量份数为20~60份,搅拌4~6秒得到物料ⅰ,搅拌速度为2000~4000rpm/min;
22.d)将物料ⅰ快速倒入发泡箱中熟化,熟化时间为10~72小时,熟化后制备得到聚氨酯火焰复合海绵。
23.本实用新型提供的低气味复合表皮,使用低气味、低voc的新型海绵替代传统海绵,在相同密度的配方体系中,在保证复合牢度一定(即剥离力相近)的情况下,新型海绵的使用可以减少火焰复合剂的用量,从而降低火焰复合过程中源自火焰复合剂的易挥发难闻小分子物质的散发,使得复合产品的气味得以降低;如在50密度的配方体系中,保证剥离力达到汽车门板内饰使用要求(≥10n/5cm)的情况下,新型海绵的使用可以使火焰复合剂用量从5.0份减少到1.5份,复合表皮气味等级从4.5降低到3.5,tvoc从6812.33μg/m3降低到4588.23μg/m3;在35密度的配方体系中,保证剥离力达到汽车门板内饰使用要求(≥8n/5cm)的情况下,新型海绵的使用可以使火焰复合剂用量从7.0份减少到3.0份,复合表皮气味等级从4.5降低到3.7,tvoc从7308.45μg/m3降低到3908.46μg/m3;此外,由于新型海绵发泡配方中使用了含有酯键结构的聚醚多元醇,使得新型海绵在柔性链条的基础上增加了部
分刚性结构,兼具了部分聚酯型海绵的机械强度优势,使得在pvc、针织布层相同的情况下,复合表皮的延伸率也得到了提高,如50密度体系中静态延伸率达到19.5%,永久延伸率达到2.3%;35密度体系中静态延伸率达到27.5%,永久延伸率达到3.8%,优于常规复合表皮,取得了较好的技术效果。
附图说明
24.附图1是低气味复合表皮。
25.附图1中,1为pvc层,2为新型海绵层,3为针织布层。
具体实施方式
26.下面将结合本实用新型实施例中的附图,对本实用新型实施例中的技术方案进行清楚、完整的描述,显然,所描述的实施例仅仅是本实用新型一部分实施例,而不是全部的实施例。
27.【实施例1】
28.一种低气味复合表皮,自上而下依次为:pvc层1、新型海绵层2、针织布层3,三层材料之间采用火焰复合工艺贴合;其中pvc层1厚度为1.1mm;新型海绵层2厚度为3.0mm;针织布层3选用纬编布,厚度为0.4mm;其中新型海绵2的制备步骤如下:
29.a)制备聚醚多元醇b1:
30.(1)100重量份数的丙二醇与767重量份数的环氧乙烷反应形成低分子聚醚多元醇,反应时间8h,反应温度120℃;
31.(2)由步骤(1)中低分子聚醚多元醇100份与90重量份数的邻苯二甲酸酐聚合反应形成多元醇i,反应时间8h,反应温度120℃;
32.(3)由步骤(2)中多元醇i 100份与93重量份数的环氧丙烷反应形成聚醚多元醇b1,反应时间6h,反应温度125℃;
33.b)制备组分i:
34.在容器a中按照重量份数计算,加入聚醚多元醇a1(分子量为2000,不饱和度为0.01mmol/g,官能度为2):30份,聚醚多元醇b1:50份,聚合物多元醇c1(分子量为6000,官能度为3,固含量为45%):20份,水:1.9份,二甲基苄胺:0.17份,二乙基环己胺:0.18份,二月桂酸二丁基锡:0.12份,si
‑
2302:0.7份,yk
‑
68le:0.5份,fle
‑
200lf:1份,均匀搅拌,搅拌速度为2500rpm/min,混合物料温度为25℃;
35.c)制备组分ii:
36.在容器a中加入重量百分数为80%的2,4
‑
二甲基苯基二异氰酸酯和20%重量百分数为2,6
‑
二甲基苯基二异氰酸酯的混合物重量份数为28份,搅拌6秒钟得到物料ⅰ,搅拌速度为3000rpm/min;
37.d)将物料ⅰ快速倒入发泡箱中熟化,熟化时间为48小时,熟化后制备得到聚氨酯火焰复合海绵。
38.制备得到的新型海绵2的性能数据如表1所示,火焰复合后复合表皮的质量检测数据见表2。
39.【实施例2】
40.一种低气味复合表皮,自上而下依次为,pvc层1、新型海绵层2、针织布层3,三层材料之间采用火焰复合工艺贴合;其中pvc层1厚度为1.0mm;新型海绵层2厚度为2.0mm;针织布层3选用纬编布,厚度为0.3mm;其中新型海绵2的制备步骤如下:
41.a)制备聚醚多元醇b2:
42.(1)100重量份数的丙三醇与622重量份数的环氧丙烷反应形成低分子聚醚多元醇,反应时间8h,反应温度120℃;
43.(2)由步骤(1)中低分子聚醚多元醇100份与90重量份数的邻苯二甲酸酐聚合反应形成多元醇i,反应时间8h,反应温度125℃;
44.(3)由步骤(2)中多元醇i 100份与93重量份数的环氧丙烷反应形成聚醚多元醇b1,反应时间8h,反应温度130℃;
45.b)制备组分i:
46.在容器a中按照重量份数计算,加入聚醚多元醇a2(分子量为3000,不饱和度为0.02mmol/g,官能度为3):40份,聚醚多元醇b2:30份,聚合物多元醇c2(分子量为7000,官能度为3,固含量为35%):30份,水:2.5份,三乙烯二胺:0.16份,辛酸亚锡:0.17份,l
‑
5702:1.2份,yk
‑
80lv:5份,fle
‑
200lf:3.0份,均匀搅拌,搅拌速度为3000rpm/min,混合物料温度为25℃;
47.c)制备组分ii:
48.在容器a中加入重量百分数为80%的2,4
‑
二甲基苯基二异氰酸酯和20%重量百分数为2,6
‑
二甲基苯基二异氰酸酯的混合物重量份数为36份,搅拌6秒钟得到物料ⅰ,搅拌速度为3000rpm/min;
49.d)将物料ⅰ快速倒入发泡箱中熟化,熟化时间为48小时,熟化后制备得到聚氨酯火焰复合海绵。
50.制备得到的新型海绵2的性能数据如表1所示,火焰复合后复合表皮的质量检测数据见表2。
51.【比较例1】
52.一种复合表皮,自上而下依次为,pvc层、普通pu海绵层、针织布层,三层材料之间采用火焰复合工艺贴合;其中,pvc层厚度为1.1mm;普通pu海绵层厚度为3.0mm;针织布选用纬编布,厚度为0.4mm;普通pu海绵的质量检测数据见表1,火焰复合后复合表皮的质量检测数据见表2。
53.【比较例2】
54.一种复合表皮,自上而下依次为,pvc层、普通pu海绵层、针织布层,三层材料之间采用火焰复合工艺贴合;其中,pvc层厚度为1.0mm;普通pu海绵层厚度为2.0mm;针织布选用纬编布,厚度为0.3mm;普通pu海绵的质量检测数据见表1,火焰复合后复合表皮的质量检测数据见表2。
55.表1实施例1~2及比较例1~2中海绵的质量检测数据
[0056][0057]
表2实施例1~2及比较例1~2的复合表皮的质量检测数据
[0058][0059]
结合表1及表2的数据分析,由pvc、海绵、针织布三层材料复合而成的复合表皮用于汽车门板内饰时,海绵与pvc、海绵与针织布之间均需要具有一定的复合牢度,即达到一定的剥离力要求,剥离力越大复合牢度越大。在50密度体系中,汽车门板内饰的剥离力使用要求为≥10n/5cm,为达到此要求,由比较例1使用普通pu海绵进行火焰复合,配方中需添加的火焰复合剂重量份数为5.0份,此时复合表皮的气味等级为4.5,tvoc为6812.33μg/m3;而实施例1中使用密度为50.3kg/m3的新型海绵代替普通pu海绵,配方中只需添加火焰复合剂用量1.5份,且制备的复合表皮不同层之间的经向、纬向剥离力均高于普通pu海绵,气味等级为3.5,tvoc为4588.23μg/m3,气味更小、voc散发更少。
[0060]
同样的,在35密度体系中,汽车门板内饰的剥离力使用要求为≥8n/5cm,为达到此要求,比较例2中使用普通pu海绵进行火焰复合,配方中需添加重量份数为7.0份的火焰复合剂,此时复合表皮的气味等级为4.5,tvoc为7308.45μg/m3;而在实施例2中使用新型海绵,配方中只需添加重量份数3.0份的火焰复合剂,且制备的复合表皮不同层之间的经向、纬向剥离力均高于普通pu海绵,气味等级为3.7,tvoc为3908.46μg/m3,气味更小、voc散发
更少。
[0061]
从表2中实施例1~2及比较例1~2复合表皮的延伸率性能测试结果看,同密度体系中,在pvc、针织布层相同的情况下,使用新型海绵的复合表皮的静态延伸率、永久延伸率均高于普通复合表皮。
[0062]
综上所述,与普通pu海绵制备的复合表皮相比,低气味新型海绵的使用,降低了火焰复合所需火焰复合剂的用量,减少了易挥发小分子物质的散发,使得复合表皮具备了低气味、低voc的优点;同时由于新型海绵配方中添加了含有酯键结构的聚醚多元醇参与反应,新型海绵具有了部分聚酯型海绵的刚性结构,增强了新型海绵的机械强度,提高了复合表皮的延伸率,取得了较好的技术效果,可用于汽车门板内饰中。