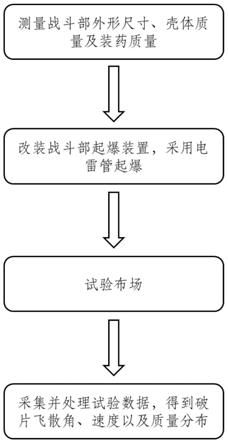
1.本发明属于弹丸(战斗部)破碎性试验技术领域,具体涉及一种战斗部破片质量分布的试验方法及系统。
背景技术:2.破碎性试验通常是把弹丸放在一定中空容器的中央,容器周围放置使破片减速的介质,爆炸后回收破片并按质量分组,从而得到在不同质量范围内的破片数,再采用工程上常用的莫特分布(mott分布)或韦伯分布(weibull分布)对试验得到的破片质量分布数据进行拟合,最终获得弹丸的破片质量分布模型。
3.常采用的自然破片弹丸或战斗部的破碎性试验方法为砂坑试验和水中爆炸试验。根据国军标要求,砂坑试验的装置由空气室、砂箱和土坑组成,其中,空气室即为中空容器。土坑四周铺设装甲钢板,土坑内置直径和高度不等的两个圆筒,由厚纸板、三合板或马粪纸制成。其中,内筒为空气室、外筒为砂箱,内、外筒之间装填细砂或锯木屑作为减速介质。水中爆炸试验的装置由水井、空气室和回收网组成。水井壁面和井底均铺设钢板,回收网置于水井底部。井内灌水作为减速介质,空气室悬浮在水井中央。空气室由聚氯乙烯塑料制成,须保证空气室耐水压且密闭防水。由于传统的破碎性试验需要在一定的试验装置(土坑或者爆炸水井)内进行,为了保证装置不被破坏、装置外人员及设备的安全,往往需要严格限制用于破碎性试验的弹丸或战斗部的尺寸以及内部装填炸药的tnt当量。国内现有的土坑以及爆炸水井的许用tnt当量通常不大于5kg,因此大口径身管武器弹丸、导弹战斗部、火箭弹战斗部等大尺寸、大tnt当量的战斗部较难采用土坑及爆炸水井进行破碎性试验。对于此类大当量战斗部,现有技术中,通常是采用缩尺战斗部进行破碎性试验来获取其破片质量分布。
4.综上所述,在缩尺战斗部破碎性试验中,虽然缩尺战斗部与原尺寸战斗部之间通常为几何相似,但是破片的质量分布却不满足几何相似律,而现有技术中又没有将缩尺战斗部破碎性试验得到的破片质量分布模型转换为原尺寸战斗部的破片质量分布模型的成熟可靠的方法;此外,传统的破碎性试验仅能获得破片的质量分布这唯一的参量,为了评估战斗部爆炸产生的高速破片群对目标的毁伤能力,通常还需要设计综合威力试验以获取破片的飞散角以及速度分布。
技术实现要素:5.有鉴于此,本发明提供了一种战斗部破片质量分布的试验方法及系统,能够根据试验测得的破片对靶板的侵彻情况与破片飞散角及速度计算得到大尺寸、内部装填较大tnt当量炸药的战斗部的破片质量分布。
6.本发明提供的一种战斗部破片质量分布的试验方法,包括以下步骤:
7.步骤1、测量待测战斗部的外形尺寸,称量所述待测战斗部的壳体质量及装药质量;改装所述待测战斗部的起爆装置;
8.步骤2、将所述待测战斗部放置于支架上,使所述待测战斗部的轴线与地面垂直,所述待测战斗部的弹体头部指向地面;在所述支架周围距所述支架不同距离的位置布设通靶与立靶,所述通靶和立靶分别位于通靶布设范围和立靶布设范围之内,所述通靶布设范围与立靶布设范围无交集;在所述通靶布设范围内布设通靶测速系统;所述立靶均面向所述待测战斗部,且互不遮挡,在距所述待测战斗部的距离为15*d≤x≤2.5的范围内至少布设两块所述立靶,x为所述立靶与待测战斗部的距离,d为所述待测战斗部的半径,单位均为m;
9.步骤3、若需要测试所述待测战斗部的弹体头部爆炸产生破片的速度、飞散角以及质量分布,则在所述待测战斗部的正下方布设卧靶,所述卧靶上放置与其具有重合的几何中心的相互绝缘的卧置通靶;所述卧靶的几何中心与所述待测战斗部的质心在地面的投影点重合,执行步骤5;若不需要测试所述待测战斗部的弹体头部爆炸产生破片,执行步骤4;
10.步骤4、引爆所述待测战斗部,根据位于与所述待测战斗部的距离在15*d≤x≤2.5的范围内的所述立靶采集到的数据,计算所述待测战斗部破片的飞散角;根据所述通靶测速系统记录的数据,计算所示待测战斗部破片的速度;执行步骤6;
11.步骤5、引爆所述待测战斗部,根据位于与所述待测战斗部的距离在15*d≤x≤2.5的范围内的所述立靶采集到的数据,及根据所述卧靶所采集到的数据,计算待测战斗部破片的飞散角;根据通靶测速系统记录的数据,计算待测战斗部破片的速度;
12.步骤6、根据步骤4或步骤5中计算得到的所述待测战斗部的飞散角和速度,以及破片对靶板的侵彻情况,计算得到所述待测战斗部的破片的累积质量分布数据,通过对所述累积质量分布数据进行拟合得到所述待测战斗部破片的质量分布。
13.进一步地,所述步骤6中的计算得到所述待测战斗部的破片的累积质量分布数据的方式为:采用球形破片穿甲公式计算得到能够穿透靶板的破片的最小质量,及每块靶板上的穿孔数量,从而得到所述待测战斗部的破片的累积质量分布数据。
14.进一步地,所述步骤6中的通过对所述累积质量分布数据进行拟合得到所述待测战斗部破片的质量分布,所述拟合的过程为采用weibull分布进行拟合。
15.本发明提供的一种战斗部破片质量分布的试验系统,包括:支架、立靶、通靶及通靶测速系统;
16.其中,所述支架用于放置待测战斗部,使得所述待测战斗部的弹体轴线与地面垂直;在所述支架周围距所述支架不同距离的位置布设通靶与立靶,所述通靶和立靶分别位于通靶布设范围和立靶布设范围之内,所述通靶布设范围与立靶布设范围无交集;在所述通靶布设范围内布设所述通靶测速系统;
17.所述立靶均面向所述待测战斗部放置,互不遮挡,在与所述待测战斗部的距离范围15*d≤x≤2.5内至少布设两块所述立靶,x为所述立靶与所述待测战斗部间的距离,d为所述待测战斗部的半径,单位均为m。
18.进一步地,所述试验系统还包括卧靶和卧置通靶,所述卧靶位于所述待测战斗的正下方,所述卧靶的几何中心与所述待测战斗的质心在地面的投影点重合;所述卧置通靶放置于所述卧靶的上表面,所述卧置通靶与所述卧靶的几何中心重合,所述卧置通靶与所述卧靶之间相互绝缘。
19.进一步地,所述卧靶为长2m、宽2m、厚0.004m的q235钢板。
20.进一步地,所述立靶由靶板与靶架焊接而成。
21.进一步地,所述靶板为长2m、宽1.5m、厚0.004m的q235钢板。
22.有益效果:
23.本发明通过将测试得到待测战斗部爆炸产生的高速破片群对靶板的侵彻情况与破片飞散角及速度相结合,通过拟合得到破片的质量分布,不仅解决了通过试验难以直接获取大尺寸、内部装填较大tnt当量炸药的战斗部的破片质量分布的问题;同时实现了单次实验即可获得破片的飞散角和速度分布,有效提高了试验效率,节省了大量的人力、物力和财力。
附图说明
24.图1为本发明提供的一种战斗部破片质量分布的试验方法的流程图。
25.图2为本发明提供的一种战斗部破片质量分布的试验系统的结构示意图。
26.图3为本发明提供的一种战斗部破片质量分布的试验系统所采用的立靶的示意图。
27.图4为待测战斗部的侧向破片飞散角及头部破片飞散角的示意图。
28.图5为采用本发明提供的一种战斗部破片质量分布的试验方法得到的待测战斗部破片的累积质量分布数据与破片质量分布拟合结果示意图。
29.其中,1
‑
待测战斗部,2
‑
立靶,3
‑
卧靶,4
‑
卧置通靶,5
‑
通靶测速系统,6
‑
靶板,7
‑
靶架,8
‑
炸点,9
‑
靶板上90%破片的分布区域,10
‑
通靶。
具体实施方式
30.下面结合附图,对本发明进行详细描述。
31.本发明提供的一种战斗部破片质量分布的试验方法及系统,其基本思想是:在待测战斗部周围部署与该待测战斗部相隔不同距离的一系列靶板,通过测试待测战斗部爆炸产生的高速破片群对靶板的侵彻情况,再结合试验测得的破片飞散角及速度,根据破片穿甲公式计算得到破片的累积质量分布数据,在此基础上采用分布模型对试验数据进行拟合,即可得到待测战斗部的破片质量分布模型。
32.根据现有理论可知,若将战斗部爆炸产生的形状、质量各异的自然破片按照质量相等原则转化为相同材质的球形破片,那么球形破片能否穿透一定厚度的靶板仅与破片的质量、作用到靶板时的存速以及破片的着角有关,破片的着角由破片的飞散角决定。若通过试验获取到破片对靶板的穿透情况、破片的存速以及飞散角,则可以通过采用可靠的球形破片穿甲公式计算得到能够穿透靶板的破片的最小质量。由于试验布设的立靶与战斗部之间的距离各不相同,导致破片飞行至每一块立靶时的存速不同,因此能穿透每块立靶的破片的最小质量各不相同。获取不同立靶处的穿孔数量、计算得到能够穿透每块立靶的破片的最小质量,即得到了破片的累积质量分布数据,再采用分布模型对数据进行拟合,即可得到破片的质量分布模型。
33.本发明提供的一种战斗部破片质量分布的试验方法,流程如图1所示,具体包括以下步骤:
34.步骤1、测量待测战斗部的外形尺寸,称量待测战斗部的壳体质量以及装药质量;
改装待测战斗部的起爆装置,采用电雷管起爆待测战斗部。
35.步骤2、将待测战斗部放置于支架上,使待测战斗部的轴线与地面垂直,弹体头部向下指向地面。在支架周围距支架不同距离的位置布设通靶与立靶,通靶和立靶分别位于通靶布设范围和立靶布设范围之内,通靶布设范围与立靶布设范围无交集;在通靶布设范围内布设通靶测速系统,通靶测速系统用于测试破片的平均初速。其中,所有立靶均面向待测战斗部放置,互不遮挡;且在距待测战斗部的距离为15*d≤x≤2.5的范围内至少布设两块立靶,x为立靶与待测战斗部间的距离,d为待测战斗部的半径,单位均为m。
36.为减小对破片飞散的影响程度,通常情况下支架选用木质材料。测试设备、布场方式参见《gjb 3197
‑
98炮弹试验方法》中“方法402破片速度”部分。根据国军标的要求,待测战斗部质心距地面1.5m。
37.步骤3、根据待测战斗部外形或根据具体需求,确定是否需要测试待测战斗部的弹体头部爆炸产生破片的速度、飞散角以及质量分布。如果需要测量弹体头部爆炸产生破片的速度、飞散角以及质量分布,则在待测战斗部的正下方布放卧靶,卧靶上放置通靶;卧靶几何中心与待测战斗部的质心在地面的投影点重合,通靶的几何中心与卧靶的几何中心重合,卧靶与通靶之间相互绝缘。
38.一般情况下,对于头部为卵形的榴弹、迫弹等身管武器弹丸,无需测试头部破片;而对于头部为平面的某些导弹战斗部,则可根据需要测试头部破片。对于需要测量弹体头部爆炸产生破片的速度、飞散角以及质量分布的情况,可采用如下布场方式:
39.首先,在待测战斗部的正下方布放1块卧靶,用于测试头部破片的飞散角及质量分布。放置卧靶前,需在卧靶的正下方挖掘一个1.2m见方的坑,以消除地面对测试结果的影响。卧靶的几何中心与待测战斗部的质心在地面的投影点重合。卧靶可选择长2m、宽2m、厚0.004m,材质为q235的钢。
40.然后,在卧靶上放置一块卧置通靶,用于测试头部破片的速度,卧置通靶的几何中心与卧靶的几何中心重合。卧靶与卧置通靶之间做绝缘处理。
41.步骤4、引爆待测战斗部,根据在距待测战斗部间的距离为15*d≤x≤2.5的范围内布设的立靶所采集到的数据,及根据需要布设的卧靶所采集到的数据,计算待测战斗部破片的飞散角;根据通靶测速系统记录的数据,计算待测战斗部破片的速度。
42.步骤4.1、计算待测战斗部破片的飞散角。
43.确定在距待测战斗部间的距离为15*d≤x≤2.5的范围内布设的立靶2
‑
1、立靶2
‑
2以及卧靶(根据需要布设)上90%破片的分布区域,并测量图4中所标注的数据,其中,立靶与待测战斗部间的距离为h1,卧靶与待测战斗部间的距离为h2,h1与h2的单位均是m。根据测量值,采用如下公式计算侧向破片的飞散角θ
侧
以及头部破片的飞散角θ
前
:
[0044][0045][0046]
其中,a为炸点8在立靶上的投影点与90%破片分布区域9(在立靶上为矩形)上边界之间的距离,单位是m;b为炸点8在立靶上的投影点与90%破片分布区域9下边界之间的距离,单位是m;r为炸点8在卧靶上的投影点与90%破片分布区域9(在卧靶上为圆形)边界
的距离,单位是m。
[0047]
将立靶2
‑
1与立靶2
‑
2与待测战斗部间的距离分别作为h1代入公式(1)进行计算,对立靶2
‑
1与立靶2
‑
2的计算结果取算术平均值,即为待测战斗部侧向破片的飞散角以及头部破片的飞散角。
[0048]
步骤4.2、计算待测战斗部破片的速度。
[0049]
根据通靶测速系统记录的数据,计算得到破片的平均初速v0(单位为:m/s),数据处理方法参见《gjb 3197
‑
98炮弹试验方法》中“方法402破片速度”部分。破片在空气中运动时受到空气阻力的作用会产生速度衰减,工程上已经有较为成熟的方法根据破片初速来计算破片飞行x米后的存速v
i
(单位为:m/s):
[0050]
v
i
=v0exp(
‑
αx
i
)
ꢀꢀꢀ
(3)
[0051]
其中,α为衰减系数,对于大部分自然破片战斗部爆炸产生的钢制破片,0.02≤α≤0.04。
[0052]
步骤5、根据步骤4中计算得到的待测战斗部的飞散角和速度,计算待测战斗部破片的质量分布。
[0053]
根据试验数据及步骤4的计算结果能够获取破片对靶板的穿透情况、破片的存速以及飞散角,由此可通过采用可靠的球形破片穿甲公式计算得到能够穿透靶板的破片的最小质量。由于试验中所布设的立靶与战斗部之间的距离各不相同,导致破片飞行至每一块立靶时的存速不同,因此能穿透每块立靶的破片的最小质量各不相同。那么获取不同立靶的穿孔数量、计算得到能够穿透每块立靶的破片的最小质量,即可得到待测战斗部的破片的累积质量分布数据,再采用分布模型对数据进行拟合,最终即可得到破片的质量分布模型。具体的数据处理过程如下:
[0054]
步骤5.1令公式(3)中的x分别取x1、x2、
…
、x
i
、
…
、x
10
,x1、x2、
…
、x
i
、
…
、x
10
分别对应破片飞行至立靶2
‑
1、立靶2
‑
2、
……
、立靶2
‑
10处的飞行距离,破片飞行至立靶2
‑
1、立靶2
‑
2、
…
、立靶2
‑
i、
…
、立靶2
‑
10处的存速分别为v1、v2、
…
、v
i
、
…
、v
10
,其中,i为立靶的编号。
[0055]
步骤5.2根据步骤4得到的数据采用公式(4)计算破片的平均着角ψ:
[0056][0057]
步骤5.3采用现有技术给出的球形破片穿甲公式(5),计算能够穿透每块立靶的破片的最小质量m
i
(单位为:kg):
[0058][0059]
其中,ρ
i
为靶板的密度,ρ
p
为破片的密度,靶板与破片的材质均为钢,因此ρ
i
=ρ
p
=7850kg/m3;h为靶板厚度,h=0.004m;σ
b
为靶板的抗拉强度,对于q235钢,σ
b
=375
×
106pa。令v
i
分别取v1、v2、
…
、v
10
,计算得到能够穿透立靶1、立靶2、
…
、立靶i、
…
、立靶10的破片的最小质量分别为m1、m2、
…
、m
i
、
…
、m
10
。
[0060]
步骤5.4统计每块立靶上的穿透破片的数量(即靶板上的穿孔数),立靶2
‑
1、立靶2
‑
2、
…
、立靶2
‑
i、
…
、立靶2
‑
10上的穿孔数分别记为n1、n2、
…
、n
i
、
…
、n
10
。根据下式换算得到破片飞散面上的穿透破片的数量n
i
:
[0061][0062]
其中,令i=1,即可得到立靶1处破片飞散面上的穿透破片的数量n1。以此类推,即可得到立靶2
‑
2、
…
、立靶2
‑
i、
…
、立靶2
‑
10中每块立靶处破片飞散面上的穿透破片的数量n2、n3、
…
、n
10
。
[0063]
步骤5.5采用工程上常用的weibull分布拟合得到破片的质量分布模型。weibull分布的形式为:
[0064][0065]
其中,n(m
f
)表示质量大于等于m
f
的破片的数量;m为待测战斗部的壳体质量,单位是g;μ和β均为weibull分布的控制参数。μ为比例参数,单位是g;β为形状参数。令n(m
f
)分别为n1、n2、
…
、n
10
,m
f
分别为m1、m1、
…
、m
10
,应用最小二乘法即可拟合得到weibull分布的控制参数μ和β。
[0066]
基于本发明提供的一种战斗部破片质量分布的试验方法,本发明提供了一种战斗部破片质量分布的试验系统,包括:支架、立靶2、卧靶3、通靶10及通靶测速系统5。
[0067]
其中,支架用于放置待测战斗部1,使得待测战斗部1的弹体轴线与地面垂直,待测战斗部1的质心距地面1.5m,弹体头部向下、尾部(起爆端)向上。
[0068]
在支架周围距支架不同距离的位置布设通靶10与立靶2,通靶10和立靶2分别位于通靶布设范围和立靶布设范围之内,通靶布设范围与立靶布设范围无交集;在通靶布设范围内布设通靶测速系统5,通靶测速系统5用于测试破片的平均初速。其中,所有立靶2均面向待测战斗部放置,互不遮挡;且在距待测战斗部1的距离为15*d≤x≤2.5的范围内至少布设两块立靶2,x为立靶2与待测战斗部1间的距离,d为待测战斗部1的半径,单位均为m。立靶2用于测试待测战斗部的飞散角以及质量分布;通靶10用于测试待测战斗部破片的速度。
[0069]
立靶2垂直于地面放置,立靶2由靶板6与靶架7组成,如图3所示。靶板6与靶架7之间的连接方式为焊接,靶板6材质为q235钢,靶板6长2m、宽1.5m、厚0.004m。靶架7对靶板6起支撑作用,且保证靶板6几何中心距地面1.5m。
[0070]
例如,为方便叙述,在地面上以待测战斗部投影点为原点建立平面直角坐标系,两条相互垂直的坐标轴将试验场地划分为四个象限。自右上角开始沿顺时针方向直至左上角,将四个象限依次命名为第一象限、第二象限、第三象限以及第四象限。
[0071]
在第一象限内布置两块立靶,分别命名为“立靶2
‑
1”和“立靶2
‑
2”,两块立靶用于测试战斗部的飞散角以及质量分布。两块立靶与战斗部之间的距离分别记为x1和x2,单位均为m。为防止战斗部爆炸产生的冲击波先于破片作用到立靶从而对测试结果产生影响,同时保证破片群的纵向作用范围小于等于立靶高(2m),x1与x2应满足:15d≤x1<x2≤2.5,其中,d为战斗部半径,单位为m。
[0072]
在第二象限与第三象限内各布置4块立靶,用于测试破片的质量分布。8块立靶依次命名为“立靶2
‑
3”、“立靶2
‑
4”、
……
、“立靶2
‑
10”,与战斗部之间的距离分别记为x3、
…
、x
i
、
…
、x
10
。x3、
…
、x
i
、
…
、x
10
的取值分别为4m、6m、
……
、18m。
[0073]
在第四象限内布设通靶测速系统,测试破片的平均初速。测试设备、布场方式参见
《gjb 3197
‑
98炮弹试验方法》中“方法402破片速度”部分。
[0074]
对于需要测试待测战斗部的头部破片的情况,还需要布设卧靶3。具体来说,在待测战斗部正下方布放1块卧靶3,用于测试头部破片的飞散角及质量分布。放置卧靶3前,需在卧靶正下方挖掘一个1.2m见方的坑,以消除地面对测试结果的影响。卧靶3的几何中心与待测战斗部的质心在地面的投影点重合,卧靶3长2m、宽2m、厚0.004m,材质为q235钢。然后,在卧靶3上放置一块卧置通靶4,用于测试头部破片的速度,卧置通靶4的几何中心与卧靶3的几何中心重合。卧靶与卧置通靶之间需要做绝缘处理。
[0075]
实例一:测试某型导弹战斗部爆炸产生高速破片群的飞散角、速度以及质量分布。
[0076]
1、待测战斗部的壳体质量为6.5kg,内部装填炸药的tnt当量约为7.3kg。战斗部的尺寸较大且装药的tnt当量超过5kg,采用传统的破碎性试验无法对该战斗部的破片质量分布进行测试,因此应用本发明设计的试验方法。
[0077]
2、对待测战斗部的起爆装置进行改装,在扩爆药柱的端面开孔并插入电雷管。
[0078]
3、按照图2所示方式进行布场。
[0079]
3.1、按式要求确定立靶2
‑
1以及立靶2
‑
2与战斗部之间的距离。战斗部的半径d=0.067m,15d=1.005m。因此,x1=1.2m,x2=2m。
[0080]
3.2、本试验不需要测试战斗部的头部破片,因此未布设卧靶以及测试头部破片速度的通靶。
[0081]
4、试验后测量、统计试验结果,并对试验数据进行处理,得到破片的飞散角、速度以及质量分布。
[0082]
4.1、破片的飞散角
[0083]
按照图4要求测量数据,计算侧向破片的飞散角。立靶2
‑
1以及立靶2
‑
2的测试结果以及飞散角如表1所示。
[0084]
表1测试结果以及侧向破片飞散角
[0085]
靶板名称h1/ma/mb/mθ
侧
/度立靶10.960.150.4516.23立靶21.810.290.8616.31
[0086]
将立靶2
‑
1与立靶2
‑
2测得的飞散角取算术平均值,得到战斗部的侧向破片飞散角为16.27
°
。
[0087]
4.2、破片的速度
[0088]
参考《gjb 3197
‑
98炮弹试验方法》中“方法402破片速度”部分,共布设3块通靶测试侧向破片的平均初速。3块通靶与战斗部之间的距离分别为2.4m、4m和8m,测试得到的破片着靶的平均时间分别为1.09ms、1.66ms以及4.56ms。计算得到侧向破片的平均初速为2304.71m/s,取α=0.039,得到破片的存速为:v
i
=2304.71exp(
‑
0.039x
i
)。
[0089]
4.3、破片的质量分布
[0090]
4.3.1、令x
i
分别为1.2m、2m、4m、6m、8m、10m、12m、14m、16m、18m,计算得到破片飞行至立靶2
‑
1、立靶2
‑
2、
……
、立靶2
‑
10处的存速,计算结果见表2。
[0091]
4.3.2、根据表1所示的试验数据计算得到破片的平均着角ψ=0.30。
[0092]
4.3.3、代入表2中所示的速度值,计算得到能够穿透立靶2
‑
1、立靶2
‑
2、
……
、立靶2
‑
10的破片的最小质量,计算结果见表2。
[0093]
4.3.4、统计立靶2
‑
1、立靶2
‑
2、
……
、立靶2
‑
10上的穿孔数,结果见表2。采用穿孔数计算得到每块立靶处破片飞散面上的穿透破片的数量,结果见表2。
[0094]
4.3.5、在origin软件中选择最小二乘法,对表2中所示的m
i
、n
i
进行拟合,拟合结果如图5所示。由此得到破片的质量分布模型为:
[0095][0096]
表2每块立靶处的破片存速、穿透破片的最小质量、穿孔数以及破片飞散面上的穿透破片数量
[0097][0098]
综上所述,以上仅为本发明的较佳实施例而已,并非用于限定本发明的保护范围。凡在本发明的精神和原则之内,所作的任何修改、等同替换、改进等,均应包含在本发明的保护范围之内。