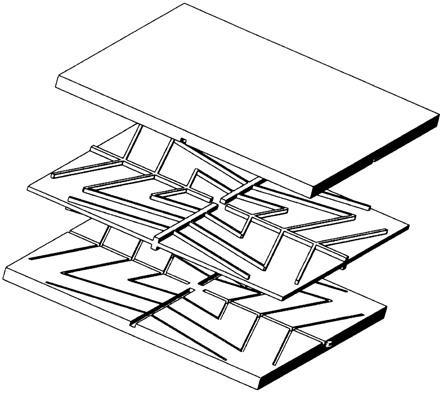
1.本发明公开了一种叶脉仿生负泊松比结构的纤维金属层板制备方法,属于复合材料领域。
背景技术:2.随着我国近些年在汽车、军事装备及航空航天等领域的高速发展,以及对具有高强度、轻量化、耐腐蚀、抗冲击性能的复合材料的战略发展需求,纤维金属层板受到了各界的广泛关注。纤维金属层板是由金属薄板和纤维/树脂预浸料交替铺贴、层压固化而成的一种超混杂复合材料,由于结合了金属材料和纤维材料的双重优势,纤维金属层板具有显著的高强度、抗疲劳性能和高损伤容限等优点。纤维金属层板目前在a380客机、波音757、波音777等飞机上已有大量应用,并且势必将成为我国结构零件制造过程中的关键材料之一。
3.我国对于纤维金属层板的研究尚处在起步阶段,目前主要是关于其成形极限、层间性能等的研究较多,对于如何提高其抗冲击性能,特别是抵抗平行于板面的侧向冲击载荷性能的有关研究较少。航空航天飞行器的工作服役环境较为复杂,飞行器零部什既受到垂直于板面的正向冲击载荷,又会受到平行于板面的侧向冲击载荷,因此开发出一种能承受双向冲击载荷的新型结构的纤维金属层板对于我国航空航天领域零件制造的发展具有很大意义。
技术实现要素:4.本发明提供了一种叶脉仿生负泊松比结构的纤维金属层板制备方法,以达到上述目的。
5.为实现上述目的,本发明采用以下技术方案:
6.首先在金属板表面加工叶脉仿生负泊松比结构凹槽。再将纤维和热塑性树脂制备成纤维增强树脂复合材料,并经过加热加压、冷却定型的过程固化;通过精密铣削等加工方法,在固化后的纤维增强树脂复合材料两面都加工出凸起的叶脉仿生负泊松比结构;并利用热塑性树脂可反复加热软化、冷却硬化的特点,加热软化纤维增强树脂复合材料。最后按金属薄板、纤维增强树脂复合材料的顺序交替铺贴,同时将纤维增强树脂复合材料凸起的结构嵌入金属板的结构凹槽里,再经过加热加压、冷却定型的过程固化,制备完成一种叶脉仿生负泊松比结构的纤维金属层板。
7.叶脉仿生负泊松比结构由叶脉仿生结构和负泊松比结构复合构成。自然界中植物树叶的叶脉由主脉、侧脉以及细脉组成,其中对整个树叶起机械支撑作用的主要是主脉和侧脉,叶脉结构给树叶提供很强的抗拉压、抗弯曲性能,并增加树叶整体强度,因此叶脉仿生结构将由主脉和侧脉构成。负泊松比结构具有良好的能量吸收能力和抗冲击性能,负泊松比结构由不同方向叶脉上的侧脉延伸交汇构成。最后叶脉仿生结构和负泊松比结构复合构成叶脉仿生负泊松比结构。
8.水发明提供了一种叶脉仿生负泊松比结构的纤维金属层板制备方法,制备2/1结
构的纤维金属层板具体包括以下步骤:
9.(1)按照热塑性树脂薄膜、纤维布的顺序交替铺贴,再经过加热加压、冷却定型的工艺过程固化,获得固化后的纤维增强树脂复合材料。
10.(2)确定叶脉仿生负泊松比结构比例,具体步骤如下:
11.i)分析自然界中不同植物叶片上的叶脉,经过数学统计后,确定主脉和侧脉之间的夹角α;
12.ii)根据金属薄板的形状和大小,确定叶脉仿生结构中主脉的长度l、主脉的数量u及侧脉的数量m;
13.iii)将不同方向主脉上的侧脉延伸交汇,得到叶脉仿生负泊松比结构,并根据金属板的大小,确定负泊松比结构的数量w;
14.iiii)根据金属薄板的厚度、固化后的纤维增强树脂复合材料的厚度,确定出叶脉仿生负泊松比结构的高度h。
15.(3)在金属薄板一面加工出叶脉仿生负泊松比结构凹槽,可采用切削、铣削或激光雕刻等加工方法。
16.(4)在固化后的纤维增强树脂复合材料两面都加工出凸起的叶脉仿生负泊松比结构,固化目的是为了易于在纤维表面加工出该结构,可采用精密铣削等加工方法。
17.(5)利用热塑性树脂可反复加热软化、冷却硬化的特点,加热已加工好的纤维增强树脂复合材料至玻璃化转变温度,使其树脂软化处于玻璃态。
18.(6)按照金属薄板、软化后的纤维增强树脂复合材料的顺序交替铺贴,同时将纤维增强树脂复合材料的凸起结构嵌入金属薄板的结构凹槽里;再加热复合材料至粘流态转变温度,使其树脂处于粘流态,便于树脂在金属薄板结构凹槽内重新均匀分布,增强纤维金属层板固化性能;最后通过加热加压、冷却定型的工艺过程固化,制备完成一种叶脉仿生负泊松比结构的纤维金属层板。
19.若要加工n+1/n(n≥2)结构的叶脉仿生负泊松比结构纤维金属层板,只需将处在中间层的金属薄板两面都加工出叶脉仿生负泊松比结构凹槽,然后按上述步骤完成即可。
20.本发明利用大自然中叶脉结构、负泊松比结构具有较强能量吸收、抗冲击性能的优势,并利用纤维是作为纤维金属层板主要承力部件这一特点,将加工后具有叶脉仿生结构和负泊松比结构的纤维增强树脂复合材料嵌入金属层,最终叶脉仿生结构能够提升纤维金属层板抵抗垂直于板面的正向冲击载荷性能,并增加纤维金属层板整体的强度,负泊松比结构能够提升纤维金属层板抵抗平行于板面的侧向冲击载荷性能。
21.本发明所提到的纤维增强树脂复合材料中所使用的树脂是热塑性树脂,先将复合材料固化,通过精密铣削等加工方法,实现对纤维表面加工所需结构的工艺,工艺过程简单且容易实现,并且用上述工艺方法加工纤维时可以做到几乎不破坏原本复合材料里纤维的结构,同时利用热塑性树脂制备的纤维金属层板具有可回收重复使用、资源利用率高、避免环境污染等优点。
22.本发明利用热塑性树脂可反复加热软化、冷却硬化的特点,在纤维金属层板的铺贴过程中,加热复合材料至玻璃化转变温度,使其中的树脂处于玻璃态,此时树脂为固体并具有一定的弹性,能够很便捷地将复合材料表面凸起结构嵌入金属薄板的结构凹槽里,为自动化生产提供可行方案;再加热复合材料至粘流态转变温度,使其中的树脂处于粘流态,
此时树脂为具有粘性的液体并能够在结构凹槽内发生粘性流动并重新均匀分布,提高纤维金属层板的固化性能。
23.本发明所提到的叶脉仿生结构和负泊松比结构的数量可根据金属薄板形状和大小调整,通过控制主脉的数量控制叶脉仿生结构的数量,通过控制侧脉的数量可以控制负泊松比结构的数量和形状,最终可通过配比不同数量的叶脉仿生结构和负泊松比结构,以获得对纤维金属层板不同的强度、抗冲击性能的增强作用。
24.本发明提出了一种叶脉仿生负泊松比结构的纤维金属层板制备方法,有益效果在于:自然界中叶脉在树叶中起主要机械承力作用,使树叶具有足够的强度和刚度,本发明通过将具有叶脉仿生负泊松比结构的纤维增强树脂复合材料嵌入金属薄板里,既减轻了纤维金属层板整体的重量,实现比以往纤维金属层板程度更高的轻量化,又实现了对纤维金属层板整体强度的增强作用。
附图说明
25.图1为叶脉仿生负泊松比结构示意图。
26.图2为叶脉仿生结构示意图。
27.图3为负泊松比结构示意图。
28.图4为金属薄板叶脉仿生负泊松比结构示意图。
29.图5为金属薄板叶脉仿生负泊松比结构加工区域示意图。
30.图6为纤维增强树脂复合材料叶脉仿生负泊松比结构示意图。
31.图7为纤维增强树脂复合材料叶脉仿生负泊松比结构加工区域示意图。
32.图8为2/1结构的叶脉仿生负泊松比结构的纤维金属层板夹层示意图。
33.图9为主脉数量为6的叶脉仿生负泊松比结构纤维增强树脂复合材料示意图。
34.图中:1
‑
主脉;2
‑
侧脉。
具体实施方式
35.以下结合附图对本发明作进一步的详细说明。
36.一种叶脉仿生负泊松比结构的纤维金属层板制备方法,制备2/1结构的纤维金属层板具体包括以下步骤:
37.(1)按照热塑性树脂薄膜、纤维布的顺序交替铺贴,再经过加热加压、冷却定型的工艺过程固化,获得固化后的纤维增强树脂复合材料。
38.(2)确定叶脉仿生负泊松比结构比例,具体步骤如下:
39.i)参照图2,分析自然界中不同植物叶片上的叶脉,经过数学统计后,确定主脉1和侧脉2之间的夹角α;
40.ii)参照图4,根据金属薄板的形状和大小,确定主脉1的长度l、主脉1的数量u及侧脉2的数量m;
41.iii)参照图1、2、3,将不同方向的主脉1上的侧脉2延伸交汇,得到叶脉仿生负泊松比结构,并根据金属板的大小,确定负泊松比结构的数量w;
42.iiii)参照图4、6,根据金属薄板的厚度、固化后的纤维增强树脂复合材料的厚度,确定出叶脉仿生负泊松比结构的高度h。
43.(3)参照图4、5,在金属薄板一面加工出叶脉仿生负泊松比结构凹槽,可采用切削、铣削或激光雕刻等加工方法。
44.(4)参照图6、7,在固化后的纤维增强树脂复合材料两面都加工出凸起的叶脉仿生负泊松比结构,可采用精密铣削等加工方法。
45.(5)利用热塑性树脂可反复加热软化、冷却硬化的特点,加热已加工好的纤维增强树脂复合材料至玻璃化转变温度,使其树脂软化处于玻璃态,此时树脂为固体并具有一定的弹性。
46.(6)参照图8,按照金属薄板、软化后的纤维增强树脂复合材料的顺序交替铺贴,同时将纤维增强树脂复合材料的凸起结构嵌入金属薄板的结构凹槽里;再加热复合材料至粘流态转变温度,此时树脂为具有粘性的液体,便于树脂在金属薄板结构凹槽内重新均匀分布,增强纤维金属层板固化性能;最后通过加热加压、冷却定型的工艺过程固化,制备完成一种叶脉仿生负泊松比结构的纤维金属层板。
47.若要加工n+1/n(n≥2)结构的叶脉仿生负泊松比结构纤维金属层板,只需将处在中间层的金属薄板两面都加工出叶脉仿生负泊松比结构凹槽,然后按上述步骤完成即可。
48.需要注意的是,本发明中所使用的树脂为热塑性树脂。
49.本发明中涉及到的叶脉仿生负泊松比结构,可根据不同金属薄板的形状、尺寸设计不同的结构形式,参考图9,凸起部位为主脉数量为6的叶脉仿生负泊松比结构,不同的叶脉仿生负泊松比结构可增强纤维金属层板抵抗来自不同方向的冲击载荷性能。