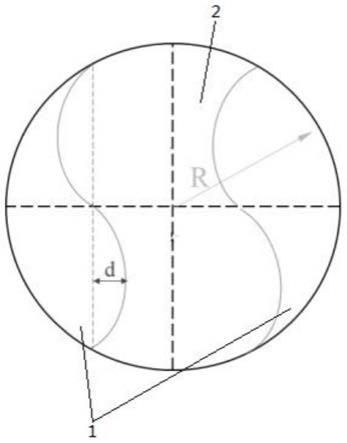
1.本发明涉及复合材料技术领域,具体涉及一种多层复合板材的制备方法。
背景技术:2.镁及其合金具有比强度比刚度高、导热性好、电磁屏蔽及阻尼减震性能优、易于机加工等优势,是实际应用中最轻的金属结构材料,其密度仅为铝合金的2/3、钢铁的1/4,是一种理想的轻量化结构材料,这种显著的低密度特征,使其在航空航天、汽车、轨道运输及3c等领域具有非常广大的市场。
3.尽管镁合金有着显著的轻质优势,但纯镁电极电位低,表面的氧化膜疏松多孔,导致耐腐蚀性差,且相对其他金属,镁的绝对强度偏低,难以作为主要承力部件,这些缺点都限制镁的广泛使用。虽然可以采用合金化的方法,向纯镁中添加al、zn、ca、mn或稀土元素等合金化元素来增加纯镁的强度,改善力学性能和提高耐腐蚀性能,但也只能在一定范围内改善上述不足,难以有质的变化。而在镁合金板材的表面的单侧或者双侧覆盖一层抗腐蚀性好,并兼具优良塑性和低密度的金属薄板无疑能很好的解决上述问题。铝是地壳中分布最广泛的元素,其平均含量为8.8%,仅次于氧和硅而居于第三位。其密度为2.72g/cm3,约为钢的1/3。铝及其合金具有比重小、耐腐蚀性强、比强度高、散热性好、导电性强、塑性加工性优异、表面装饰性好等诸多优点。且铝在元素周期表中铝和镁为相邻元素,镁合铝之间更容易形成金属性结合。因此,通过某种连接技术,将镁和铝进行层状复合,制备兼具镁和铝优势的镁铝复合板材,综合性能优于单一镁或铝板材。
4.在现有技术中,金属复合板主要的连接工艺主要有扩散焊法、爆炸复合法、摩擦焊法等,这些方法都或多或少存在成本高、效率低、工艺复杂、板材性能不稳定等缺陷,难以进行大规模的工业化生产。挤压工艺可充分发挥材料塑性、改善合金组织性能,同时易于实现工业化连续生产,是制备镁合金板材理想的塑性加工方法。通过对现有文献资料的检索,目前采用挤压工艺制备金属复合板的研究还很有限,如何设计挤压工艺方案是制备金属复合板材的难点。
技术实现要素:5.为解决上述技术问题,本发明公开一种镁和铝两种异质金属复合的方法,成功制备具有优异结合性能和力学性能的铝/镁/铝多层复合板材,解决镁合金板单一组元板材力学性能低、耐蚀性差及表面着色能力的不足;同时与双层复合板材相比,多层复合板可将综合性能更优的铝合金层完全分布于外部,使用场景比双层镁/铝板材应用范围更广。
6.本发明具体技术方案为:
7.一种多层复合板材的制备方法,其特征在于,包括以下制备步骤:
8.s1、材料准备:将铝合金及镁合金材料加工至所需要的外形及尺寸,得到的三层板状合金可组合为圆柱体,圆柱体中镁合金位于两层铝合金中间,所述两层铝合金和镁合金三者相贴合的面均为s型弧面;
9.s2、表面清洁:对步骤s1中准备好的铝合金及镁合金材料先进行抛光,再清洗,使合金材料表面洁净;
10.s3、装配组合:将步骤s2中清洁后的合金材料进行装配、组合,通过机械咬合的方式使其固定成为一个圆柱体;
11.s4、挤压成形:将装配完成后的镁铝复合坯料进行预热,随后挤压成形,制备得到镁铝复合板材。
12.进一步地,所述步骤s1中的铝合金包含所有以铝为主要成分的金属材料或金属基复合材料,其中铝的含量为50%
‑
100%,镁合金包含所有以镁为主要成分的金属材料或金属基复合材料,其中mg的含量为50%
‑
100%。
13.进一步地,所述步骤s1中加工方法包括变形方法和机械加工方法,其中变形方法包括挤压、锻造和轧制中的一种,机械加工方法包括线切割或车削中的一种。
14.进一步地,所述步骤s2中所述抛光方法包括机械抛光法和化学抛光法,机械抛光法为砂纸抛光、打磨机打磨和钢丝球打磨中的一种或多种;抛光前两种合金都可以先用除油剂进行表面除油,避免油污影响表面状态;化学抛光是用化学溶液进行抛光,铝合金层用ph为9
‑
11的碱性溶液进行碱洗,时间为20
‑
120s,所述碱性溶液包括naoh溶液、koh和nahco3中的一种;镁合金层用ph为5.5
‑
6.5的酸性溶液进行酸洗,酸洗时间为20
‑
120s,所述酸性溶液包括hcl、h2so4、草酸和磷酸溶液中的一种;所述步骤s2中所述清洗过程为用去离子水或酒精溶液将抛光后的镁合金层及铝合金层清洗干净,随后自然风干或烘干。
15.进一步地,所述步骤s3中所述圆柱体尺寸无具体要求,主要根据所制备板材的尺寸而定,本发明优选圆柱体半径为50
‑
160mm,材料长度为200
‑
800mm;
16.进一步地,所述步骤s3中装配组合方式为将镁合金层及铝合金层按照圆柱体形状进行组合,随后加压固定住三层合金层,使镁合金层与铝合金层之间机械咬合,得到镁铝复合坯料,避免镁铝合金在后续工序中脱落,影响挤压成形。所述固定方法为采用液压机加压将外侧两铝合金层进行上下保压,液压机加压是使三层材料都发生整体变形,达到在某些局部产生锁紧的效果,使两者紧密结合;或用外力敲击圆柱表面的结合界线处,使结合界线产生形变,三层合金之间互相有效结合。这一步的作用主要是为了三层材料有一定的结合力,不会散落,能保证后面挤压的顺利进行。
17.进一步地,所述步骤s4中所述镁铝复合坯料的预热温度为150
‑
450℃,预热时间为6
‑
12h。
18.进一步地,所述步骤s4中挤压所用模具为板材模具,挤压前放入挤压坯料时,镁铝合金层与挤压模具的长度方向平行放置,挤压比为8
‑
30,挤压速度为0.3
‑
5mm/s。
19.所述步骤s4中挤压速度优选为0.6
‑
1.6mm/s。
20.镁合金在挤压变形过程中处于三向压应力状态,可以充分发挥镁合金的塑性,提高变形能力,以获得大变形量。本发明制备的复合板材镁合金层与铝合金层之间结合紧密,界面间形成了冶金结合,界面结合强度高,具有优异的综合力学性能。
21.本发明还提供一种多层复合板材,是通过上述多层复合板材的制备方法所制得。
22.与现有技术相比,本发明具有的有益效果为:
23.本发明合金层截面为s型弧面设计,使三层合金在组合过程中,在外力作用下可以更为有效地机械咬合,防止在后续工艺中发生脱落,影响生产同时还尽可能有效增大了三
层合金的有效接触面积,在挤压过程中镁/铝界面之间能产生更大的热量,为界面处晶粒得动态再结晶提供驱动力,细化晶粒尺寸,也能促进中间层与两侧基体发生明显扩散,使中间层与两侧基体实现冶金结合。
24.现有技术中产生冶金结合的镁/铝界面处会生成硬脆的金属间化合物,严重影响镁合金与铝合金之间的界面结合力,使得复合板材提前破坏。本发明的合金截面的s型弧面设计还能在挤压时,使界面处沿着挤压方向会发生非均匀塑性变形,产生不均匀荷载,随着挤压的进行,这种不均匀荷载能使得镁/铝界面处生成的硬脆金属间化合物发生破碎,有效减少界面处硬脆金属间化合物对复合板结合力得影响,提高综合力学性能。
25.本发明采用外部施力的方法,在挤压变形前,将镁合金及铝合金各层之间施加一定的预结合力,保证后续挤压加工时两者组合成的复合挤压坯料始终为一个整体,不会在挤压时脱落影响生产过程,同时保证镁合金层及铝合金层结合面尽可能与外部空气隔离,减少镁合金和铝合金接触面的表面氧化。
26.本发明采用大挤压比慢速挤压,慢速挤压能促进金属均匀流动,增加镁合金层与铝合金层的变形协调性,能使镁合金层与铝合金层同步挤出,均匀复合,同时避免形成强烈的丝织构,降低板材残余应力及开裂风险,使其获得较好的平直度。此外,大挤压可充分细化合金晶粒,显著提高板材力学性能。慢速挤压使合金动态再结晶更充分,再结晶程度越高,变形丝织构强度越低,板材各向异性降低。
27.本发明采用挤压的工艺方案制备合金复合板材,镁和铝都属于轻金属材料,物理特性相近,变形一致性较好,能够采用挤压的方法同时成形,且能够应用于大批量工业生产,工艺简单,操作易行,可作为通用方法同步推广至其他金属材料的制备,应用场景广阔。
附图说明
28.图1为本发明合金板材组合后圆柱体截面示意图。
29.符号说明:1
‑
铝合金,2
‑
镁合金。
具体实施方式
30.实施例1
31.s1、材料准备:准备两支直径为300mm,长度为405mm的5052铝合金和az31b镁合金铸棒,车加工至直径296mm,长度为400mm;随后线切割为如图1所示的s形截面,其中凸起和凹陷的相切圆弧顶点距离两端连线的距离d为40mm;
32.s2、表面清洁:用砂纸将准备好的镁合金及铝合金表面打磨光亮,去除表面氧化黑皮及线切割痕迹,全部打磨光亮后,用自来水进行清洗,冲洗掉表面打磨粉末,随后风干;
33.s3、装配组合:将清洗干净的镁合金和铝合金按照圆柱体外形进行组合,使各层之间紧密贴合后,随后用锤子用力敲击结合部位,在结合部位产生变形,有一定的结合力,使各层不易脱落;
34.s4、将组合好的复合材料放置于电阻炉中预热,预热温度为300℃,预热时间为8h,到达预热时间后,放入挤压机中进行加压,挤压模具为板材挤压模具,注意复合挤压坯料与挤压模具平行,挤压比为10,挤压速度为0.3mm/s。
35.本实施例挤压板材结合强度测试结果如表1中所示。
36.实施例2
37.s1、材料准备:准备两支直径为300mm,长度为405mm的6061铝合金和az40m镁合金铸棒,车加工至直径296mm,长度为400mm;随后线切割为如图1所示的s形截面,其中凸起和凹陷的相切圆弧顶点距离两端连线的距离d为40mm;
38.s2、表面清洁:用砂纸将准备好的镁合金及铝合金表面打磨光亮,去除表面氧化黑皮及线切割痕迹,全部打磨光亮后,用酒精进行清洗,冲洗掉表面打磨粉末,随后风干;
39.s3、装配组合:将清洗干净的镁合金和铝合金按照圆柱体外形进行组合,使各层之间紧密贴合后,随后用锤子用力敲击结合部位,在结合部位产生变形,有一定的结合力,使各层不易脱落;
40.s4、将组合好的复合材料放置于电阻炉中预热,预热温度为150℃,预热时间为12h,到达预热时间后,放入挤压机中进行加压,挤压模具为板材挤压模具,注意复合挤压坯料与挤压模具平行,挤压比为10,挤压速度为0.3mm/s。
41.本实施例挤压板材结合强度测试结果如表1中所示。
42.实施例3
43.s1、材料准备:准备两支直径为300mm,长度为405mm的5052铝合金和az40m镁合金铸棒,车加工至直径296mm,长度为400mm;随后线切割为如图1所示的s形截面,其中凸起和凹陷的相切圆弧顶点距离两端连线的距离d为40mm;
44.s2、表面清洁:铝合金层用ph为10的nahco3溶液进行碱洗,镁合金层用ph为6的磷酸溶液进行酸洗,然后用酒精溶液冲洗掉表面,随后风干;
45.s3、装配组合:将清洗干净的镁合金和铝合金按照圆柱体外形进行组合,使各层之间紧密贴合后,随后用液压机进行加压,压下量为1mm,在结合部位产生变形,有一定的结合力,使各层不易脱落;
46.s4、将组合好的复合材料放置于电阻炉中预热,预热温度为300℃,预热时间为8h,到达预热时间后,放入挤压机中进行加压,挤压模具为板材挤压模具,注意复合挤压坯料与挤压模具平行,挤压比为8,挤压速度为0.3mm/s。
47.本实施例挤压板材结合强度测试结果如表1中所示。
48.实施例4
49.s1、材料准备:准备两支直径为300mm,长度为405mm的5052铝合金和az31b镁合金铸棒,车加工至直径296mm,长度为400mm;随后线切割为如图1所示的s形截面,其中凸起和凹陷的相切圆弧顶点距离两端连线的距离d为40mm;
50.s2、表面清洁:铝合金层用ph为11的koh溶液进行碱洗,镁合金层用ph为6.5的草酸溶液进行酸洗,然后用酒精溶液冲洗掉表面,随后风干;
51.s3、装配组合:将清洗干净的镁合金和铝合金按照圆柱体外形进行组合,使各层之间紧密贴合后,随后用锤子用力敲击结合部位,在结合部位产生变形,有一定的结合力,使各层不易脱落;
52.s4、将组合好的复合材料放置于电阻炉中预热,预热温度为350℃,预热时间为12h,到达预热时间后,放入挤压机中进行加压,挤压模具为板材挤压模具,注意复合挤压坯料与挤压模具平行,挤压比为15速度为0.5m/s。
53.本实施例挤压板材结合强度测试结果如表1中所示。
54.实施例5
55.s1、材料准备:准备两支直径为300mm,长度为405mm的5052铝合金和az31b镁合金铸棒,车加工至直径296mm,长度为400mm;随后线切割为如图1所示的s形截面,其中凸起和凹陷的相切圆弧顶点距离两端连线的距离d为40mm;
56.s2、表面清洁:铝合金层用ph为9的naoh溶液进行碱洗,镁合金层用ph为5.5的hcl溶液进行酸洗,然后用酒精溶液冲洗掉表面,随后风干;
57.s3、装配组合:将清洗干净的镁合金和铝合金按照圆柱体外形进行组合,使各层之间紧密贴合后,随后用锤子用力敲击结合部位,在结合部位产生变形,有一定的结合力,使各层不易脱落;
58.s4、将组合好的复合材料放置于电阻炉中预热,预热温度为450℃,预热时间为6h,到达预热时间后,放入挤压机中进行加压,挤压模具为板材挤压模具,注意复合挤压坯料与挤压模具平行,挤压比为30速度为5m/s。
59.本实施例挤压板材结合强度测试结果如表1中所示。
60.上述实施例1
‑
5中,圆柱体中铝合金s形弧面两段圆弧的相切点到圆心的距离为该柱体半径的一半,在实验中使用此设计能获得较好的生产效果。实际生产中可能对板材产品的各层合金厚度要求不同,各层尺寸可根据具体要求做不同的设计,两侧的铝合金厚度尺寸不一定相同。
61.对比例1
62.a:材料准备:准备两支直径为300mm,长度为405mm的5052铝合金和az31b镁合金铸棒,车加工至直径296mm,长度为400mm;随后线切割为如图1所示的s形截面,其中凸起和凹陷的相切圆弧顶点距离两端连线的距离d为40mm;
63.b:表面清洁:用砂纸将准备好的镁合金及铝合金表面打磨光亮,去除表面氧化黑皮及线切割痕迹,全部打磨光亮后,用自来水进行清洗,冲洗掉表面打磨粉末,随后风干;
64.c:将组合好的三层板材放置于电阻炉中预热,预热温度为300℃,预热时间为8h,到达预热时间后,放入挤压机中进行加压,挤压模具为板材挤压模具,注意复合挤压坯料与挤压模具平行,挤压比为10,挤压速度为0.3mm/s。
65.本对比例挤压板材结合强度测试结果如表1中所示,挤压完后,镁合金层与铝合金层直接脱落,未产生有效结合,结合力为0。
66.对比例2
67.a:材料准备:准备两支直径为300mm,长度为405mm的5052铝合金和az31b镁合金铸棒,车加工至直径296mm,长度为400mm;随后线切割为如图1所示的s形截面,其中凸起和凹陷的相切圆弧顶点距离两端连线的距离d为40mm;
68.b:装配组合:将清洗干净的镁合金和铝合金按照圆柱体外形进行组合,使三层板材紧密贴合后,随后用锤子用力敲击结合部位,在结合部位产生变形,有一定的结合力,使二者不易脱落;
69.c:将组合好的复合材料放置于电阻炉中预热,预热温度为300℃,预热时间为8h,到达预热时间后,放入挤压机中进行加压,挤压模具为板材挤压模具,注意复合挤压坯料与挤压模具平行,挤压比为10,挤压速度为0.3mm/s。
70.本对比例挤压板材结合强度测试结果如表1中所示,挤压完后,镁合金层与铝合金
层直接脱落,未产生有效结合,结合力为0。
71.对比例3
72.a.材料准备:准备两支直径为300mm,长度为405mm的5052铝合金和az31b镁合金铸棒,车加工至直径296mm,长度为400mm;随后线切割为能组合为圆柱体的层状块体,其外侧铝合金层厚度为74mm,中间镁合金层为148mm,界面处为平面;
73.b.表面清洁:用砂纸将准备好的镁合金及铝合金表面打磨光亮,去除表面氧化黑皮及线切割痕迹,全部打磨光亮后,用自来水进行清洗,冲洗掉表面打磨粉末,随后风干;
74.c.装配组合:将清洗干净的镁合金和铝合金按照圆柱体外形进行组合,使各层之间紧密贴合后,随后用锤子用力敲击结合部位,在结合部位产生变形,有一定的结合力,使各层不易脱落;
75.d.将组合好的复合材料放置于电阻炉中预热,预热温度为300℃,预热时间为8h,到达预热时间后,放入挤压机中进行加压,挤压模具为板材挤压模具,注意复合挤压坯料与挤压模具平行,挤压比为10,挤压速度为0.3mm/s。
76.本对比例挤压板材结合强度测试结果如表1中所示,可以看出,各层界面为平面时,最终制得的复合板材界面结合力很低。
77.对比例4
78.a.材料准备:准备两支直径为300mm,长度为405mm的5052铝合金和az31b镁合金铸棒,车加工至直径296mm,长度为400mm;随后线切割为如图1所示的s形截面,其中凸起和凹陷的相切圆弧顶点距离两端连线的距离d为40mm;
79.b.表面清洁:用砂纸将准备好的镁合金及铝合金表面打磨光亮,去除表面氧化黑皮及线切割痕迹,全部打磨光亮后,用自来水进行清洗,冲洗掉表面打磨粉末,随后风干;
80.c.装配组合:将清洗干净的镁合金和铝合金按照圆柱体外形进行组合,使各层之间紧密贴合后,随后用锤子用力敲击结合部位,在结合部位产生变形,有一定的结合力,使各层不易脱落;
81.d.将组合好的复合材料放置于电阻炉中预热,预热温度为300℃,预热时间为8h,到达预热时间后,放入挤压机中进行加压,挤压模具为板材挤压模具,注意复合挤压坯料与挤压模具平行,挤压比为6,挤压速度为10mm/s。
82.本对比例挤压板材结合强度测试结果如表1中所示,可以看出,采用小挤压比快速挤压成形,复合板各层之间不能充分焊合,形成的结合力较低。
83.表1
84.实施例结合力/mpa实施例121.4实施例222.3实施例323.3实施例422.7实施例520.1对比例10对比例20对比例312.2
对比例414.2