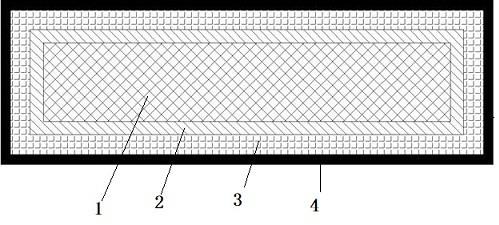
1.本发明属于复合材料制备技术领域,特别涉及一种复合材料及其ooa制备方法。
背景技术:2.在目前市面上,用于防弹领域的纤维材料主要是芳纶纤维和超高分子量聚乙烯纤维,其中超高分子量聚乙烯纤维其断裂伸长低、断裂功大,具有很强的吸收能量的能力,故具备优异的抗冲击性,其冲击吸收能比对位芳纶纤维高近一倍。但是,超高分子量聚乙烯纤维在高温(超过150℃)条件下,防弹性能显著下降;在有明火的情况下,pe纤维会燃烧,并且产生明显的熔滴,在作为防弹材料使用时,在爆炸产生的高温破片或其他可燃物,散落到pe板表面,会使得pe板防弹性能显著降低,若可燃物散落到pe板表面,pe板会燃烧,产生熔滴,扩大火势的蔓延。
技术实现要素:3.针对上述的技术问题,本发明提出一种制备防火绝热阻燃超高分子量聚乙烯防弹板。
4.本发明的另一个发明目的是提供一种防火绝热阻燃超高分子量聚乙烯防弹板及其制作方法。
5.本发明的技术方案是:一种制备防火绝热阻燃超高分子量聚乙烯防弹板,包括pe板、无机纤维布、阻燃涂层和封装层;所述pe板置于防弹板的核心层,所述无机纤维布、阻燃涂层和封装层依次包裹pe板1上;所述pe板为多层pe单向布,按照0
°
,45
°
,90
°
,135
°
,进行循环铺覆,且在每层pe单向布之间均匀刮涂一层微米级氧化锆颗粒。
6.进一步地,上述阻燃涂料为双组份无溶剂改性环氧膨胀型阻燃涂料,质量比a:b=100:7.5~15,用量为800~1500g/
㎡
。
7.进一步地,上述单面封装层的总重量不超过1.3kg/
㎡
,厚度不超过0.4mm。
8.一种制备防火绝热阻燃超高分子量聚乙烯防弹板的方法;s1、制备pe板:将多层pe单向布,按照0
°
,45
°
,90
°
,135
°
,进行循环铺覆,且在每层pe单向布之间均匀刮涂一层微米级氧化锆颗粒,待铺覆好的带有氧化锆的多层pe单向布在模压机上进行升温模压成型,具体升温和加压过程如下:a.入模:将以上铺覆好的pe单向布,送入模压机的模具中,压力为5~8mpa,温度由0℃~100℃;在此过程中需要经过2~3次减压至0 mpa(俗称排气处理,防止制成的pe板中因含有空气,形成空泡影响后续的成型pe板的质量);b.预热:待pe单向布温度升至110℃,压力增加至15mpa,压力不变,保温10~15min;
在此过程中,随着温度的升高,压力表的示数会降低,需严格监控pe单向布的温度以及压力表示数保证预热过程;c.热压:待pe单向布温度升至120~130℃,压力增加至22mpa,压力不变,保温0.5~1h;d.冷却:压力不变,自然降温或冷水循环降温,待pe单向布降温至50℃以下,压力降为0mpa,取出即为pe板;其中a.pe单向布的克重为130
±
10g/
㎡
,需进行以上19个循环铺覆,可制成面密度约10kg/
㎡
的pe板;b.氧化锆粒径在50~300微米为最佳,刮涂量占成型后pe板的重量比≤1.5%;s2、pe板表面覆盖无机纤维布(1)采用60~120目砂纸,单向往复打磨pe板的6个外表面5~10次,直到表面有pe纤维起丝;(2)在打磨后的pe板表面包覆2层以上无机纤维布,通过真空成型工艺,使环氧树脂完全浸透无机纤维布,真空成型条件:常温下,-0.1mpa,固化时间24h以上;(3)固化后,取出pe板,打磨掉四周多余的环氧树脂和纤维材料,用80~100砂纸拉毛上下表面,用气枪清理掉打磨的尘屑;s3、刮阻燃层阻燃涂料为双组份无溶剂改性环氧膨胀型阻燃涂料,在25
±
5℃条件下,质量比a:b=100:7.5~15,搅拌均匀,使用锯齿形塑料刮板,在经过s2步骤的pe板的上表面均匀刮涂,用量为800~1500g/
㎡
;在室温下(20
±
5℃),放置在水平平台上,待24h以上,彻底固化,再翻面刮涂pe板剩余的5个外表面,用量和固化条件与刮涂上表面相同;s4、封装层封装层主要用油漆,为了保护阻燃涂层的功效,使用底漆+面漆封装,其中底漆的使用量约为400g/
㎡
,面漆的使用量为200g/
㎡
,即单面封装层的总重量不超过1.3kg/
㎡
,厚度不超过0.4mm,使经过步骤s3的pe板保持良好的适用性和阻燃涂层耐久性。
9.本发明的有益效果是:a.在pe板的制备过程中,增加氧化锆,可提高pe板的刚度和耐冲击性能,使得防弹吸能提升5~10%;b.模压通过表面粘接无机纤维布,改善pe板表面的惰性,使得阻燃涂料与pe板结合的更牢固;c.最终成型的pe板,可在800~1000℃的火焰下,烧10min,不产生熔滴,pe板上的烧蚀扩散面积≤50mm。
附图说明
10.图1是本发明的防弹板结构示意图;1
‑ꢀ
pe板;2-无机纤维布;3-阻燃涂层;4-封装层。
具体实施方式
11.下面结命会图对本发明作进一步的说明:
参见图1,防火绝热阻燃超高分子量聚乙烯防弹板组成示意图;pe板1置于防弹板的核心层,无机纤维布2、阻燃涂层3和封装层4依次包裹pe板1上。
12.其中:pe板厚度5~30mm,阻燃涂层单面厚度1~3mm,无机纤维布单面厚度0.2~0.5mm,封装层(底漆+面漆)单面厚度0.2~0.5mm实施例1,一种制备防火绝热阻燃超高分子量聚乙烯防弹板其制备方法;s1、制备pe板:将多层pe单向布,按照0
°
,45
°
,90
°
,135
°
,进行循环铺覆,且在每层pe单向布之间均匀刮涂一层微米级氧化锆颗粒,待铺覆好的带有氧化锆的多层pe单向布在模压机上进行升温模压成型,具体升温和加压过程如下:a.入模:将以上铺覆好的pe单向布,送入模压机的模具中,压力为5mpa,温度由0℃~100℃;在此过程中需要经过2次减压至0 mpa(俗称排气处理,防止制成的pe板中因含有空气,形成空泡影响后续的成型pe板的质量);b.预热:待pe单向布温度升至110℃,压力增加至15mpa,压力不变,保温10min;在此过程中,随着温度的升高,压力表的示数会降低,需严格监控pe单向布的温度以及压力表示数保证预热过程;c.热压:待pe单向布温度升至120℃,压力增加至22mpa,压力不变,保温0.5h;d.冷却:压力不变,自然降温或冷水循环降温,待pe单向布降温至50℃以下,压力降为0mpa,取出即为pe板。
13.其中a.pe单向布的克重为130
±
10g/
㎡
,需进行以上19个循环铺覆,可制成面密度约10kg/
㎡
的pe板;b.氧化锆粒径在50~300微米为最佳,刮涂量占成型后pe板的重量比≤1.5%;s2、pe板表面覆盖无机纤维布(1)采用60~120目砂纸,单向往复打磨pe板的6个外表面5次,直到表面有pe纤维起丝;(2)在打磨后的pe板表面包覆2层以上无机纤维布,通过真空成型工艺,使环氧树脂完全浸透无机纤维布,真空成型条件:常温下,-0.1mpa,固化时间24h以上;(3)固化后,取出pe板,打磨掉四周多余的环氧树脂和纤维材料,用80~100砂纸拉毛上下表面,用气枪清理掉打磨的尘屑;s3、刮阻燃层阻燃涂料为双组份无溶剂改性环氧膨胀型阻燃涂料,在25
±
5℃条件下,质量比a:b=100:7.5,搅拌均匀,使用锯齿形塑料刮板,在经过s2步骤的pe板的上表面均匀刮涂,用量为800g/
㎡
;在室温下(20
±
5℃),放置在水平平台上,待24h以上,彻底固化,再翻面刮涂pe板剩余的5个外表面,用量和固化条件与刮涂上表面相同。
14.s4、封装层封装层主要用油漆,为了保护阻燃涂层的功效,使用底漆+面漆封装,其中底漆的使用量约为400g/
㎡
,面漆的使用量为200g/
㎡
,即单面封装层的总重量不超过1.3kg/
㎡
,厚
度不超过0.4mm,使经过步骤s3的pe板保持良好的适用性和阻燃涂层耐久性。
15.实施例2,一种制备防火绝热阻燃超高分子量聚乙烯防弹板其制备方法;s1、制备pe板:将多层pe单向布,按照0
°
,45
°
,90
°
,135
°
,进行循环铺覆,且在每层pe单向布之间均匀刮涂一层微米级氧化锆颗粒,待铺覆好的带有氧化锆的多层pe单向布在模压机上进行升温模压成型,具体升温和加压过程如下:a.入模:将以上铺覆好的pe单向布,送入模压机的模具中,压力为7mpa,温度由0℃~100℃;在此过程中需要经过3次减压至0 mpa(俗称排气处理,防止制成的pe板中因含有空气,形成空泡影响后续的成型pe板的质量);b.预热:待pe单向布温度升至110℃,压力增加至15mpa,压力不变,保温13min;在此过程中,随着温度的升高,压力表的示数会降低,需严格监控pe单向布的温度以及压力表示数保证预热过程;c.热压:待pe单向布温度升至125℃,压力增加至22mpa,压力不变,保温0.75 h;d.冷却:压力不变,自然降温或冷水循环降温,待pe单向布降温至50℃以下,压力降为0mpa,取出即为pe板。
16.其中a.pe单向布的克重为130
±
10g/
㎡
,需进行以上38个循环铺覆,可制成面密度约20kg/
㎡
的pe板;b.氧化锆粒径在50~300微米为最佳,刮涂量占成型后pe板的重量比≤1.5%;s2、pe板表面覆盖无机纤维布(1)采用60~120目砂纸,单向往复打磨pe板的6个外表面7次,直到表面有pe纤维起丝;(2)在打磨后的pe板表面包覆2层以上无机纤维布,通过真空成型工艺,使环氧树脂完全浸透无机纤维布,真空成型条件:常温下,-0.1mpa,固化时间24h以上;(3)固化后,取出pe板,打磨掉四周多余的环氧树脂和纤维材料,用80~100砂纸拉毛上下表面,用气枪清理掉打磨的尘屑;s3、刮阻燃层阻燃涂料为双组份无溶剂改性环氧膨胀型阻燃涂料,在25
±
5℃条件下,质量比a:b=100:11,搅拌均匀,使用锯齿形塑料刮板,在经过s2步骤的pe板的上表面均匀刮涂,用量为1200g/
㎡
;在室温下(20
±
5℃),放置在水平平台上,待24h以上,彻底固化,再翻面刮涂pe板剩余的5个外表面,用量和固化条件与刮涂上表面相同。
17.s4、封装层封装层主要用油漆,为了保护阻燃涂层的功效,使用底漆+面漆封装,其中底漆的使用量约为400g/
㎡
,面漆的使用量为200g/
㎡
,即单面封装层的总重量不超过1.3kg/
㎡
,厚度不超过0.4mm,使经过步骤s3的pe板保持良好的适用性和阻燃涂层耐久性。
18.实施例 3,一种制备防火绝热阻燃超高分子量聚乙烯防弹板其制备方法;s1、制备pe板:将多层pe单向布,按照0
°
,45
°
,90
°
,135
°
,进行循环铺覆,且在每层pe单向布之间均匀刮涂一层微米级氧化锆颗粒,待铺覆好的带有氧化锆的多层pe单向布在模压机上进行升温模压成型,具体升温和加压过程如下:
a.入模:将以上铺覆好的pe单向布,送入模压机的模具中,压力为8mpa,温度由0℃~100℃;在此过程中需要经过3次减压至0 mpa(俗称排气处理,防止制成的pe板中因含有空气,形成空泡影响后续的成型pe板的质量);b.预热:待pe单向布温度升至110℃,压力增加至15mpa,压力不变,保温10~15min;在此过程中,随着温度的升高,压力表的示数会降低,需严格监控pe单向布的温度以及压力表示数保证预热过程;c.热压:待pe单向布温度升至130℃,压力增加至22mpa,压力不变,保温1h;d.冷却:压力不变,自然降温或冷水循环降温,待pe单向布降温至50℃以下,压力降为0mpa,取出即为pe板。
19.其中a.pe单向布的克重为130
±
10g/
㎡
,需进行以上57个循环铺覆,可制成面密度约30kg/
㎡
的pe板;b.氧化锆粒径在50~300微米为最佳,刮涂量占成型后pe板的重量比≤1.5%;s2、pe板表面覆盖无机纤维布(1)采用60~120目砂纸,单向往复打磨pe板的6个外表面10次,直到表面有pe纤维起丝;(2)在打磨后的pe板表面包覆2层以上无机纤维布,通过真空成型工艺,使环氧树脂完全浸透无机纤维布,真空成型条件:常温下,-0.1mpa,固化时间24h以上;(3)固化后,取出pe板,打磨掉四周多余的环氧树脂和纤维材料,用80~100砂纸拉毛上下表面,用气枪清理掉打磨的尘屑;s3、刮阻燃层阻燃涂料为双组份无溶剂改性环氧膨胀型阻燃涂料,在25
±
5℃条件下,质量比a:b=100: 15,搅拌均匀,使用锯齿形塑料刮板,在经过s2步骤的pe板的上表面均匀刮涂,用量为1500g/
㎡
;在室温下(20
±
5℃),放置在水平平台上,待24h以上,彻底固化,再翻面刮涂pe板剩余的5个外表面,用量和固化条件与刮涂上表面相同。
20.s4、封装层封装层主要用油漆,为了保护阻燃涂层的功效,使用底漆+面漆封装,其中底漆的使用量约为400g/
㎡
,面漆的使用量为200g/
㎡
,即单面封装层的总重量不超过1.3kg/
㎡
,厚度不超过0.4mm,使经过步骤s3的pe板保持良好的适用性和阻燃涂层耐久性。
21.本发明的技术方案带来的技术效果:本发明的防火绝热阻燃超高分子量聚乙烯防弹板,a.在pe板的制备过程中,增加氧化锆,可提高pe板的刚度和耐冲击性能,使得防弹吸能提升5~10%;b.模压通过表面粘接无机纤维布,改善pe板表面的惰性,使得阻燃涂料与pe板结合的更牢固;c.最终成型的pe板,可在800~1000℃的火焰下,烧10min,不产生熔滴,pe板上的烧蚀扩散面积≤50mm。
22.上述实施例的检测报告1,报告号:ajf2008007489rscn
上述实施例的检测报告2,报告号:ajf2006005052rscn在本技术领域的公知,pe单向布为无纬单向布,铺层方式1:一般为0
°
,90
°
正交铺覆,铺层方式2:0
°
,90
°
,+45
°‑
45
°‑
45
°
+45
°
90
°0°
铺覆,按照铺层方式1和铺层方式2,通过升温加压成型的pe板1、pe板2,在打靶试验时,pe板2变形吸能较pe板1变形吸能,效果要好5%~10%。