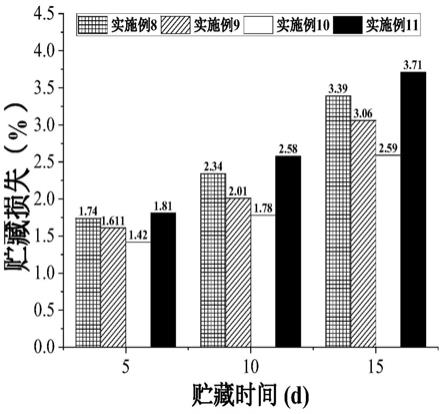
1.本发明涉及畜产食品加工技术领域,更具体地涉及一种预调理肉制品腌制液及其制备方法和使用方法。
背景技术:2.预调理肉制品因食用方便、附加值高、营养均衡、包装精美和小容量化而深受消费者喜爱,还可满足现代消费者对多元肉食消费的需求,生产量和消费量与日俱增,现已成为肉制品消费的主要趋势。2019年发达国家预调理肉制品消费量占肉制品总量的80%以上,我国预调理肉制品消费量仅为肉制品总量的33%,较发达国家有较大差距。品种单一、品质层次不齐、产品货架期短是制约我国预调理肉制品发展的主要瓶颈,亟需通过加工关键技术研究和产品开发,形成我国自主知识产权,支撑预调理肉制品产业提质增效,提升我国肉类企业的国际市场竞争力。
3.家畜红脏(主要为心脏、肝脏、肺脏、肾脏)是家畜屠宰后主要的副产物,以牛、羊的肝脏为例,肝脏具有高蛋白(18%~23%)、低脂肪(<6%)、富含维生素(v
a
、v
b
)、矿物质等营养成分的特性,具备开发优质蛋白质及相关产品的潜质。根据国家统计局数据,2019年我国牛、羊肉产量为1155万吨,牛、羊肝等脏器副产物约占胴体重的8.5%,估算脏器副产物产量约为98万吨,但是,由于缺乏高效和多元化利用技术的支撑,目前牛、羊肝等脏器副产物的可食化加工利用率低,80%以上的肝脏仅以原料形式上市,或被用于加工肥料和饲料,造成了可食性副产物资源的浪费。因此,通过关键技术研发以充分利用其丰富蛋白质等功能性物质,是家畜屠宰加工企业实现提质增效的必要途径。
4.预调理肉制品现有加工过程中,腌制是大多数产品的必需工艺。现有技术中,通常采用磷酸盐、食盐、硝酸盐和亚硝酸盐等腌制剂,借助干腌、注射腌制、滚揉腌制等工艺技术,达到改善预调理肉制品色泽、嫩度、风味和保水性,提升产品出品率和延长货架期的目的。但是,磷酸盐、硝酸盐以及食盐在改善肉制品品质的同时,也带来诸多健康隐患。硝酸盐虽对肉制品具有护色、抗氧化、抑菌等多重功效,但是过量使用后产品在加热时易生成亚硝基二甲胺和亚硝基吡咯烷等有害物质,会对人体产生致癌、致突变、致畸作用。磷酸盐能够有效提升肉制品的保水性,但是过量或者长期食用后可导致钙化性肾机能不全、低钙血症等疾病。因此,天然腌制剂替代物、低钠腌制技术已经成为预调理肉制品加工技术研究的热点。
技术实现要素:5.为了解决所述现有技术的不足,本发明提供了一种预调理肉制品腌制液及其制备方法和使用方法,以家畜红脏中提取的蛋白质组合物作为天然保水剂,配合海藻糖、天然抗氧化剂和防腐剂使用后,能够有效提升预调理肉制品的保水性、降低脂质氧化速率、提高肉色稳定性和贮藏性能。
6.本发明所要达到的技术效果通过以下方案实现:一种预调理肉制品腌制液的制备
方法,按照重量百分比将5~15%的家畜红脏蛋白粉、3~7%的海藻糖、1~6%的食盐、0.1~0.4%的天然抗氧化剂和防腐剂的混合物、71.6~90.9%的水混合而成。
7.其中儿茶素与迷迭香提取物作为天然抗氧化剂,乳酸链球菌素作为防腐剂的添加量应当均符合gb 2760
‑
2014《食品安全国家标准食品添加剂使用标准》。本发明实施例的预调理肉制品腌制液的制备方法,以新鲜的家畜红脏(主要为心脏、肝脏、肺脏、肾脏)中提取的蛋白质组合物作为天然保水剂,配合海藻糖、天然抗氧化剂和防腐剂使用后,能够有效提升预调理肉制品的保水性、降低脂质氧化速率、提高肉色稳定性和贮藏性能。同时,该工艺能够提升家畜屠宰副产物的综合利用水平。
8.优选地,家畜红脏蛋白粉的制备方法包括以下步骤:
9.原料处理步骤:检疫合格的家畜屠宰后,将红脏从胴体中分离,剥除表面的脂肪和筋膜,清水洗净后沥干水分;
10.破碎匀浆步骤:将红脏切成小块,再与冷却水混合后转移至匀浆机中匀浆;
11.微发酵与多酚去腥步骤:在匀浆液中添加儿茶素,搅拌均匀后在30~50℃条件下反应0.5~1.5h,然后加入酵母粉和蔗糖,在相同温度条件下发酵0.5~5h;
12.超声波与盐溶浸提步骤:向去腥后的匀浆液中添加nacl,混合均匀后转入超声波提取机中浸提,再离心去除上层油脂,抽滤并收集蛋白质提取液;
13.等电点沉淀步骤:采用nahco3溶液调节蛋白质提取液ph值至4.0~6.2,离心后收集蛋白质沉淀;
14.真空冷冻干燥步骤:将蛋白质沉淀按照1:1重量比重新悬浮于蒸馏水中,采用真空冷冻干燥技术制备成冻干蛋白粉。制成的冻干蛋白粉质量指标为提取率≥70.0%,蛋白质含量≥85%,水分含量≤5.0%。
15.优选地,在破碎匀浆步骤中,红脏原料与冷却水的重量比例为1:4~1:10,匀浆的速度为500~1300rpm,匀浆时间为30s~3min。
16.优选地,在微发酵与多酚去腥步骤中,儿茶素占匀浆液重量百分比为0.5~2.5%,酵母粉占红脏原料重量百分比为0.5~4%,蔗糖占红脏原料重量百分比为1~4%。
17.优选地,在超声波与盐溶浸提步骤中,nacl占匀浆液重量百分比为0.1~3%,超声波浸提的条件为60~300w、10~40℃,浸提时间为5~30min,离心条件为1000~5000g、4℃,离心时间为5~15min。
18.优选地,混合后的腌制液再用0.5~10%重量的nahco3溶液调节ph值到6.5,再置于灭菌容器中并迅速加热至55~75℃(巴氏杀菌),保持5~20min后冷却,然后在温度为0~4℃条件下密封贮藏。巴氏杀菌的方式,有效杀灭病原微生物,并减轻了腌制液中蛋白质保水性能的损伤。
19.优选地,所述天然抗氧化剂和防腐剂的混合物为儿茶素+迷迭香提取物+乳酸链球菌素的混合物,其中儿茶素、迷迭香提取物、乳酸链球菌素的重量比为1:1:2。
20.具体地,等电点沉淀步骤为采用浓度为0.5~10%的nahco3溶液调节蛋白质提取液ph值至4.0~6.2,并在1~4℃静置4
‑
8h,然后在3000~4500g、1
‑
4℃条件下离心15
‑
30min再沉淀后收集沉淀蛋白质,其中离心再沉淀的步骤重复1~2次,离心时沉淀蛋白质与2倍体积蒸馏水混合,静置5min后再离心,最终收集沉淀蛋白质。
21.真空冷冻干燥步骤为将沉淀蛋白质按照1:1重量比重新悬浮于蒸馏水中,在
‑
25
~
‑
40℃条件下预冻3~6h,然后在5~20pa、
‑
35~
‑
50℃条件下真空冷冻干燥30
‑
40h,形成冻干蛋白粉,然后采用真空包装,贮藏于阴凉干燥处。
22.本发明提供的预调理肉制品腌制液的制备方法,优选以新鲜的牛或羊肝脏为原料,在生产过程中首先采用微发酵与多酚去腥工艺,有效去除肝脏中的腥味,提升了蛋白质产品的适用性;其次采用超声波与盐溶浸提工艺,提升了蛋白质产率、降低了成本、缩短了提取时间;采用等电点沉淀工艺,进一步提升的蛋白质纯度;采用真空冷冻干燥工艺,避免了蛋白质结构的损伤,提升了腌制液的保水性功能;本发明提供了预调理肉制品基础腌制液的组分,采用本发明制备的冻干蛋白粉,替代了传统的磷酸盐保水剂,同时复配天然抗氧化剂,有效提升了预调理肉制品的抗氧化性能;采用巴氏杀菌工艺,有效杀灭病原微生物,并有效减轻了腌制液中蛋白质保水性能的损伤。本发明提供的预调理肉制品基础腌制液,能够和任意香辛料复配,具有应用范围广、腌制效果好、性能稳定、生产成本低的特点,避免了磷酸盐、硝酸盐等腌制剂带来的健康隐患,提升了牛或羊屠宰副产物的利用率,具备良好的推广应用前景。
23.一种预调理肉制品腌制液,所述预调理肉制品腌制液按照重量百分比包括以下组分:5~15%的家畜红脏蛋白粉、3~7%的海藻糖、1~6%的食盐、0.1~0.4%的儿茶素与迷迭香提取物与乳酸链球菌素的混合物、71.6~90.9%的水。
24.采用上述预调理肉制品腌制液进行腌制后,预调理肉制品增重率>12%,烹调出品率>77%,初始菌落总数<1
×
105cfu/g,致病菌未检出。
25.儿茶素与迷迭香提取物作为天然抗氧化剂,乳酸链球菌素作为防腐剂的添加量应当均符合gb 2760
‑
2014《食品安全国家标准食品添加剂使用标准》。本发明实施例的预调理肉制品腌制液的制备方法,主要以新鲜的家畜红脏,例如牛、羊肝脏中提取的蛋白质组合物作为天然保水剂,配合海藻糖、天然抗氧化剂和防腐剂使用后,能够有效提升预调理肉制品的保水性、降低脂质氧化速率、提高肉色稳定性和贮藏性能,使用本发明提供的预调理肉制品腌制液腌制得到的肉制品,真空包装后低温(0~4℃)冷藏,保质期可达15d。
26.本发明实施例的腌制液可以作为基础腌制液,能够与任意香辛料复配,制备成不同风味的腌制液,具有应用范围广、腌制效果好、性能稳定、生产成本低的特点。
27.本发明的预调理肉制品腌制液,完全取代了磷酸盐和硝酸盐,避免了磷酸盐和硝酸盐在肉制品加工中带来的食品安全隐患,符合肉制品绿色制造技术的要求。
28.一种预调理肉制品腌制液的使用方法,将上述所述的预调理肉制品腌制液按照原料肉重量的15~25%添加至原料肉中,在真空度为0.04~0.08mpa、转速为6~15r/min、温度为4
±
1℃的条件下滚揉20~60min,然后静置腌制6~24h。
29.本发明具有以下优点:
30.1、本发明所述的预调理肉制品腌制液制备方法,以家畜红脏中提取的蛋白质组合物作为天然保水剂,配合海藻糖、天然抗氧化剂和防腐剂使用后,能够有效提升预调理肉制品的保水性、降低脂质氧化速率、提高肉色稳定性和贮藏性能;同时,该工艺能够提升家丑屠宰副产物的综合利用水平;
31.2、本发明提供的预调理肉制品腌制液,完全取代了磷酸盐和硝酸盐,避免了上述盐类在肉制品加工中带来的食品安全隐患,符合肉制品绿色制造技术的要求;
32.3、本发明家畜肝脏中蛋白质组合物提取工艺中,采用酵母菌微发酵联合植物多酚
去腥技术,有效去除了蛋白质产物的腥味,消除了蛋白质不良风味对腌制液感官品质的影响;
33.4、本发明提供的预调理肉制品腌制液制备方法中,采用巴氏杀菌工艺,有效杀灭病原微生物,并减轻了腌制液中蛋白质保水性能的损伤;
34.5、本发明提供的预调理肉制品腌制液,能够和任意香辛料复配,制备成不同风味的腌制液,具有应用范围广、腌制效果好、性能稳定、生产成本低的特点。
附图说明
35.图1为预调理肉制品贮藏损失测定结果;
36.图2为预调理肉制品蒸煮损失测定结果;
37.图3为预调理肉制品tbars值测定结果;
38.图4为预调理肉制品pov值测定结果;
39.图5为预调理肉制品a*值测定结果;
40.图6为预调理肉制品omb相对含量测定结果;
41.图7为预调理肉制品tvb
‑
n值测定结果。
具体实施方式
42.家畜红脏富含的蛋白质本身具备较好的亲水能力,在一定条件下添加到肉制品中能够显著改善肉制品保水性,减少贮藏和加工过程中的水分流失。同时,其本身作为营养成分,能够提高肉制品的营养价值。现有技术中,还未见利用此类蛋白质制备预调理肉制品腌制剂的技术。此外,一些天然的植物源活性成分(如海藻糖、茶多酚、迷迭香提取物等)具备良好的保水性、抗氧化以及抑菌效能,具备替代磷酸盐和硝酸盐的潜力,但目前上述天然活性成分用于制备预调理肉制品腌制液的技术也未出现。
43.实施例1
44.本发明实施例1提供一种预调理肉制品腌制液的制备方法,按照重量百分比将10%的家畜红脏蛋白粉、5%的海藻糖、3%的食盐、0.3%的天然抗氧化剂和防腐剂的混合物、81.7%的水混合而成。
45.其中家畜红脏蛋白粉包括以下步骤:
46.原料处理步骤:检疫合格的家畜屠宰后,将红脏从胴体中分离,剥除表面的脂肪和筋膜,清水洗净后沥干水分;
47.破碎匀浆步骤:将红脏原料切成小块,再与冷却水混合后转移至匀浆机中匀浆。在该破碎匀浆步骤中,红脏原料与冷却水的重量比为1:4,匀浆的速度为500rpm,匀浆时间为30s。
48.微发酵与多酚去腥步骤:在匀浆液中添加儿茶素,搅拌均匀后在30℃条件下反应0.5h,然后加入酵母粉和蔗糖,在相同温度条件下发酵0.5h。在该微发酵与多酚去腥步骤中,儿茶素添加量为0.5%(占匀浆液重量百分比),酵母粉添加量为0.5%(占脏器原料重量百分比),蔗糖添加量为1%(占脏器原料重量百分比)。
49.超声波与盐溶浸提步骤:向去腥后的匀浆液中添加nacl,混合均匀后转入超声波提取机中浸提,再离心去除上层油脂,抽滤并收集蛋白质提取液。在该超声波与盐溶浸提步
骤中,nacl的含量占匀浆液重量百分比为0.1%,超声波浸提的条件为60w、10℃,浸提时间为5min,离心条件为1000g、4℃,离心时间为5min。
50.等电点沉淀步骤:采用浓度为0.5%(w/v)的nahco3溶液调节蛋白质提取液ph值至4.0,并在1℃静置4h,然后在3000g、4℃条件下离心15min再沉淀后收集沉淀蛋白质,其中离心再沉淀的步骤重复1~2次,离心时沉淀蛋白质与2倍体积蒸馏水混合,静置5min后再离心,最终收集沉淀蛋白质。
51.真空冷冻干燥步骤:将沉淀蛋白质按照1:1重量比重新悬浮于蒸馏水中,在
‑
25℃条件下预冻3h,然后在5pa、
‑
35℃条件下真空冷冻干燥30h,形成冻干蛋白粉,然后采用真空包装,贮藏于阴凉干燥处。
52.实施例2
53.本发明实施例2提供一种预调理肉制品腌制液的制备方法,按照重量百分比将10%的家畜红脏蛋白粉、5%的海藻糖、3%的食盐、0.3%的天然抗氧化剂和防腐剂的混合物、81.7%的水混合而成。
54.其中家畜红脏蛋白粉包括以下步骤:
55.原料处理步骤:检疫合格的家畜屠宰后,将红脏从胴体中分离,剥除表面的脂肪和筋膜,清水洗净后沥干水分;
56.破碎匀浆步骤:将红脏原料切成小块,再与冷却水混合后转移至匀浆机中匀浆。在该破碎匀浆步骤中,红脏原料与冷却水的重量比为1:7,匀浆的速度为900rpm,匀浆时间为2min。
57.微发酵与多酚去腥步骤:在匀浆液中添加儿茶素,搅拌均匀后在40℃条件下反应1h,然后加入酵母粉和蔗糖,在相同温度条件下发酵3h。在该微发酵与多酚去腥步骤中,儿茶素添加量为1.5%(占匀浆液重量百分比),酵母粉添加量为2%(占脏器原料重量百分比),蔗糖添加量为2.5%(占脏器原料重量百分比)。
58.超声波与盐溶浸提步骤:向去腥后的匀浆液中添加nacl,混合均匀后转入超声波提取机中浸提,再离心去除上层油脂,抽滤并收集蛋白质提取液。在该超声波与盐溶浸提步骤中,nacl占匀浆液重量百分比为1.5%,超声波浸提的条件为150w、25℃,浸提时间为15min,离心条件为3000g、4℃,离心时间为10min。
59.等电点沉淀步骤:采用浓度为5%(w/v)的nahco3溶液调节蛋白质提取液ph值至5.5,并在2℃静置6h,然后在4000g、4℃条件下离心20min再沉淀后收集沉淀蛋白质,其中离心再沉淀的步骤重复1~2次,离心时沉淀蛋白质与2倍体积蒸馏水混合,静置7min后再离心,最终收集沉淀蛋白质。
60.真空冷冻干燥步骤:将沉淀蛋白质按照1:1重量比重新悬浮于蒸馏水中,在
‑
30℃条件下预冻4h,然后在10pa、
‑
40℃条件下真空冷冻干35h,形成冻干蛋白粉,然后采用真空包装,贮藏于阴凉干燥处。
61.实施例3
62.本发明实施例3提供一种预调理肉制品腌制液的制备方法,按照重量百分比将10%的家畜红脏蛋白粉、5%的海藻糖、3%的食盐、0.3%的天然抗氧化剂和防腐剂的混合物、81.7%的水混合而成。
63.其中家畜红脏蛋白粉包括以下步骤:
64.原料处理步骤:检疫合格的家畜屠宰后,将红脏从胴体中分离,剥除表面的脂肪和筋膜,清水洗净后沥干水分;
65.破碎匀浆步骤:将红脏原料切成小块,再与冷却水混合后转移至匀浆机中匀浆。在该破碎匀浆步骤中,红脏原料与冷却水的重量比为1:10,匀浆的速度为1300rpm,匀浆时间为3min。
66.微发酵与多酚去腥步骤:在匀浆液中添加儿茶素,搅拌均匀后在50℃条件下反应1.5h,然后加入酵母粉和蔗糖,在相同温度条件下发酵5h。在该微发酵与多酚去腥步骤中,儿茶素添加量为2.5%(占匀浆液重量百分比),酵母粉添加量为4%(占脏器原料重量百分比),蔗糖添加量为4%(占脏器原料重量百分比)。
67.超声波与盐溶浸提步骤:向去腥后的匀浆液中添加nacl,混合均匀后转入超声波提取机中浸提,再离心去除上层油脂,抽滤并收集蛋白质提取液。在该超声波与盐溶浸提步骤中,nacl占匀浆液重量百分比为的3%,超声波浸提的条件为300w、40℃,浸提时间为30min,离心条件为5000g、4℃,离心时间为15min。
68.等电点沉淀步骤:采用浓度为10%(w/v)的nahco3溶液调节蛋白质提取液ph值至6.2,并在4℃静置8h,然后在4500g、4℃条件下离心30min再沉淀后收集沉淀蛋白质,其中离心再沉淀的步骤重复1
‑
2次,离心时沉淀蛋白质与2倍体积蒸馏水混合,静置10min后再离心,最终收集沉淀蛋白质。
69.真空冷冻干燥步骤:将沉淀蛋白质按照1:1重量比重新悬浮于蒸馏水中,在
‑
40℃条件下预冻6h,然后在20pa、
‑
50℃条件下真空冷冻干燥40h,形成冻干蛋白粉,然后采用真空包装,贮藏于阴凉干燥处。
70.实施例4
71.本发明实施例4提供一种预调理肉制品腌制液的制备方法,与实施例3的区别仅在于家畜红脏蛋白粉中去掉微发酵与多酚去腥步骤。
72.将上述4个实施例制备得到的冻干蛋白粉进行腥味感官得分、提取率、水分含量评定,得出以下实验数据:
73.a、腥味感官评分
74.采用5分制评定蛋白粉的腥味,将各个样品编号后分别取10g蛋白粉置于150ml的烧杯中,加入90ml蒸馏水,搅拌均匀。选取10位评价员(男女各5人)对各个样品的腥味进行综合评分。将所有评价员的评分去掉1个最高分和1个最低分,然后对剩下的8个评分取平均值作为该样品的最后得分。蛋白粉腥味感官得分评定标准见表1。
75.表1蛋白粉腥味感官评分标准
[0076][0077]
腥味感官得分评定结果见表2。
[0078]
b、提取率测定
[0079]
按照gb 5009.5
‑
2016《食品安全国家标准食品中蛋白质的测定》凯氏定氮法测定蛋白粉和原料中的蛋白质含量。
[0080]
蛋白质提取率(%)=[(蛋白粉中蛋白质的含量/原料中蛋白质的含量)
×
100]。蛋白质提取率测定结果见表3。
[0081]
c、水分含量测定
[0082]
蛋白粉水分含量按照gb 5009.3
‑
2016《食品安全国家标准食品中水分的测定》直接干燥法测定蛋白粉中水分含量。蛋白粉水分含量测定结果见表4。
[0083]
表2蛋白粉腥味感官评分结果
[0084][0085]
本发明实施例1~实施例4中家畜肝脏蛋白粉中,采用酵母菌微发酵联合植物多酚去腥技术(实施例1~实施例3),相比于不经去腥处理(实施例4)而制备的蛋白粉,有效去除了蛋白质产物的腥味,消除了蛋白质不良风味对腌制液感官品质的影响。
[0086]
表3蛋白质提取率测定结果(%)
[0087][0088]
本发明实施例1~实施例4中家畜肝脏蛋白粉中,采用超声波
‑
盐溶浸提工艺提取蛋白质,随着超声浸提功率、时间以及nacl使用量等条件逐步提升,蛋白质提取率随之升高。表明本发明中家畜肝脏蛋白粉的制备方法中,超声波
‑
盐溶浸提工艺能够显著提升蛋白质产率,降低生产成本。
[0089]
表4蛋白粉水分含量测定结果(%)
[0090][0091]
本发明实施例1~实施例4中家畜肝脏蛋白粉中,采用真空冷冻干燥技术制备蛋白粉,随着预冻温度和真空冷冻温度的降低、预冻时间、真空冷冻干燥时间、压力的升高,所制备的蛋白质样品中水分含量逐步降低,且总体水平低于5%,有效提升了蛋白粉的质量。且真空冷冻干燥工艺能够在较低温度下去除产品中的水平,与传统加热干燥技术对比,降低了高温对蛋白质结构和功能的损伤。
[0092]
将上述4个实施例制备得到的预调理肉制品腌制液进行致病菌检验,得出以下实验数据:
[0093]
分别以实施例1~实施例4制备的得到的蛋白粉制备预调理肉制品腌制液,在贮藏的30d分别按照gb 4789.4
‑
2016《食品安全国家标准:食品微生物学检验》沙门氏菌检验、gb 4789.3
‑
2016《食品安全国家标准:食品微生物学检验》大肠菌群计数、gb 4789.10
‑
2016《食品安全国家标准:食品微生物学检验》金黄色葡萄球菌检验,测定腌制液贮藏期间致病菌数量。预调理肉制品腌制液致病菌测定结果见表5。
[0094]
表5预调理肉制品腌制液致病菌数量测定结果(%)
[0095][0096]
注:n表示未检出。
[0097]
本发明得到的预调理肉制品腌制液,采用巴氏杀菌技术,腌制液贮藏30d时均未检出食品中常见的致病菌,符合gb29921
‑
2013《食品安全国家标准食品中致病菌限量》的要求。此外,与传统高温高压灭菌方式相比,本发明采用巴氏杀菌工艺,有效杀灭病原微生物的同时,降低了高温对蛋白质结构和功能的破坏,减轻了腌制液中蛋白质保水性能的损伤。
[0098]
实施例5
[0099]
本发明实施例5提供一种预调理肉制品腌制液使用方法,其中预调理肉制品腌制液采用实施例1所述的预调理肉制品腌制液制备方法制成,预调理肉制品腌制液使用方法包括以下步骤:将预调理肉制品腌制液按照原料肉重量的15%添加至原料肉中,在真空度为0.04mpa、转速为6r/min、温度为4
±
1℃的条件下滚揉20min,然后静置腌制6h。
[0100]
实施例6
[0101]
本发明实施例6提供一种预调理肉制品腌制液使用方法,其中预调理肉制品腌制液采用实施例1所述的预调理肉制品腌制液制备方法制成,预调理肉制品腌制液使用方法包括以下步骤:将预调理肉制品腌制液按照原料肉重量的20%添加至原料肉中,在真空度为0.08mpa、转速为15r/min、温度为4
±
1℃的条件下滚揉60min,然后静置腌制24h。
[0102]
实施例7
[0103]
本发明实施例7提供一种预调理肉制品腌制液使用方法,其中预调理肉制品腌制液采用实施例1所述的预调理肉制品腌制液制备方法制成,预调理肉制品腌制液使用方法包括以下步骤:将预调理肉制品腌制液按照原料肉重量的25%添加至原料肉中,在真空度为0.08mpa、转速为15r/min、温度为4
±
1℃的条件下滚揉60min,然后静置腌制24h。
[0104]
将实施例5~实施例7中制备得到的预调理肉制品腌制液使用方法进行使用效果评价,得出以下实验数据:
[0105]
a、增重率测定
[0106]
对实施例5~实施例7中的原料肉,称量腌制处理前重量(w1),腌制完成后,用滤纸吸干肉块表面多余的腌制液后再次称重(w2)。
[0107]
增重率(%)=[(w2‑
w1)
×
100]。增重率测定结果见表6。
[0108]
b、出品率测定
[0109]
将实施例5~实施例7中得到的块装入塑料蒸煮袋,将温度计探头由上而下插入至肉块中心,将蒸煮袋口用夹子夹住,称重(w1),将包装肉块放入72℃水浴锅中,当肉块中心温度达到70℃时,立即取出肉样,同蒸煮袋一同放入流水中冷却,然后擦除蒸煮袋表面水分,称重(w2)。
[0110]
出品率(%)=(w2/w1)
×
100。出品率测定结果见表6。
[0111]
c、初始菌落总数和致病菌测定
[0112]
实施例5~实施例7中腌制结束后,立即收集肉块样品,按照gb 4789.2
‑
2016《食品安全国家标准:食品微生物学检验》菌落总数测定方法测定肉块中的初始菌落总数。按照上述方法测定大肠杆菌、沙门氏菌和金黄色葡萄球菌数量。初始菌落总数和致病菌测定结果见表7。
[0113]
表6预调理肉制品增重率和出品率结果(%)
[0114][0115]
本发明实施例5~实施例7提供一种预调理肉制品腌制液使用方法,使用该方法腌制后,样品增重率>12%,烹调出品率>77%。对比实施例6和7可以看出,当真空滚揉腌制工艺相同的情况下,提高本发明得到的腌制液,能够显著提升产品的增重率和出品率。因此,本发明提供一种预调理肉制品腌制液使用方法使用后效果良好。
[0116]
表7预调理肉制品初始菌落总数和致病菌测定结果(%)
[0117][0118]
注:n表示未检出。
[0119]
本发明实施例5~实施例7提供一种预调理肉制品腌制液使用方法,使用该方法腌制后,样品中未检出致病菌。初始菌落总数小于1
×
106cfu/g,参考ny/t 2073
‑
2011《调理肉制品加工技术规范》,该方法得到的预调理肉制品卫生标准符合上述标准的质量安全要求。此外,随着腌制液添加量的升高,样品中初始菌落总数呈下降趋势。因此,本发明提供的预调理肉制品腌制液在使用后,能够有效抑制预调理肉制品中的初始菌落总数,有利于提高产品卫生质量,具有良好的应用前景。
[0120]
实施例8
[0121]
本发明实施例8提供一种预调理肉制品腌制液,所述预调理肉制品腌制液按照重量百分比包括以下组分:5%的家畜红脏蛋白粉、3%的海藻糖、1%的食盐、0.1%的天然抗氧化剂和防腐剂的混合物,以及90.9%的水。
[0122]
实施例9
[0123]
本发明实施例9提供一种预调理肉制品腌制液,所述预调理肉制品腌制液按照重量百分比包括以下组分:10%的家畜红脏蛋白粉、7%的海藻糖、6%的食盐、0.4%的天然抗氧化剂和防腐剂的混合物和76.6%的水。
[0124]
实施例10
[0125]
本发明实施例10提供一种预调理肉制品腌制液,所述预调理肉制品腌制液按照重量百分比包括以下组分:15%的家畜红脏蛋白粉、7%的海藻糖、6%的食盐、0.4%的天然抗氧化剂和防腐剂的混合物和71.6%的水。
[0126]
实施例11
[0127]
本发明实施例11提供一种预调理肉制品腌制液,与实施例10的区别在于采用传统的复合磷酸盐(保水剂)、亚硝酸钠(护色剂、防腐剂)作为腌制剂,按照gb
‑
2760《食品安全国家标准:食品添加剂使用标准》允许的复合磷酸盐、亚硝酸钠的最大添加量与水复配成腌制液。其中所述的复合磷酸盐由三聚磷酸钠、焦磷酸钠和六偏磷酸钠按照重量比2:2:1组合而成。
[0128]
使用本发明实施例8~实施例10中的预调理肉制品腌制液,按照实施例6中提供的使用方法得到的牛肉制品,真空包装后低温(0~4℃)冷藏,分别在5、10、15d测定肉的保水性、脂质氧化水平、肉色稳定性和贮藏性能,得出以下实验数据:
[0129]
a、保水性测定
[0130]
保水性采用贮藏损失和蒸煮损失两个指标表征。加压损失和蒸煮损失分别按照ny/t 2793
‑
2015《肉的食用品质客观评价方法》中相应的方法测定。保水性测定结果见图1和图2。
[0131]
b、脂质氧化水平测定
[0132]
脂质氧化水平采用硫代巴比妥酸值(tbars)和过氧化值(pov)表征。tbars值按照gb/t 35252
‑
2017《动植物油脂2
‑
硫代巴比妥酸值的测定》直接法,pov值按照gb 5009.227
‑
2016《食品安全国家标准:食品中过氧化值的测定》滴定法进行测定。脂质氧化水平测定结果见图3和图4。
[0133]
c、肉色稳定性测定
[0134]
肉色稳定性采用红度值(a*)和氧合肌红蛋白相对含量(omb%)表征。a*值按照ny/t 2793
‑
2015《肉的食用品质客观评价方法》中相应的方法测定。
[0135]
omb%值测定方法:样品从真空包装中取出,至于空气中静置30min后称取5.0g肉样,加入25ml磷酸缓冲液(40mmol/l、ph6.8、4℃),1000r/min匀浆25s后冰浴静置1h,然后离心(3000g、25min、4℃),上清液经滤纸过滤分别在525、545、565、572nm波长下的吸光值。
[0136]
omb%=(0.882r1‑
1.267r2+0.809r3‑
0.361)
×
100,式中r1、r2、r3分别为572、565、545nm与525nm吸光值的比值。肉色稳定性测定结果见图5和图6。
[0137]
d、贮藏性能测定
[0138]
贮藏性能采用挥发性盐基氮(tvb
‑
n)两个指标评价。tvb
‑
n按照gb5009.228
‑
2016《食品安全国家标准:食品中挥发性盐基氮的测定》半微量定氮法测定。贮藏性能测定见图7。
[0139]
保水性是衡量预调理肉制品食品和加工品质的重要指标,也是评价预调理肉制品腌制效果的关键指标。图1和图2中可以看出,本发明实施例8~实施例10中提供一种预调理
肉制品腌制液能够显著提升牛肉腌制后贮藏期间的保水性,其贮藏损失和蒸煮损失在贮藏15d时最高分别为3.39%和24.93%,同时实施例10中其他组分比例不变的情况下,提高蛋白粉的添加量后,贮藏损失和蒸煮损失均比实施例8和9显著降低。尤其是,对比于实施例11,当腌制液中采用本发明制备的蛋白粉替代传统保水剂复合磷酸盐时,能够显著降低预调理肉制品贮藏期间的贮藏损失和蒸煮损失,贮藏15d时,实施例8~实施例10中贮藏损失分别比实施例11低8.63%、17.52%、30.19%,蒸煮损失分别比实施例11低13.38%、25.51%和33.74%。说明家畜红脏蛋白粉在提高预调理肉制品保水性的方面效果优异,能够完全替代磷酸盐,降低磷酸盐潜在的健康风险。
[0140]
一般认为,肉制品在贮藏期间如果tbars值超过1.0mg mda/kg,则该产品中脂质氧化程度过高,消费者难以接受,该产品失去商品价值。实施例8~实施例10中,预调理牛肉tbars值在贮藏期间略有升高,但是在冷藏15d时tbars值最高为0.41mg mda/kg,pov值最高为1.51meq/kg,表明样品中脂质氧化产物和过氧化物浓度处于较低水平。实施例8~实施例9中,随着儿茶素、迷迭香提取物添加量的升高,样品中tbars值和pov值均显著降低。实施例11中,常规腌制剂腌制配合真空包装虽能够保证产品贮藏15d时tbars值在可接受范围内。但产品的tbars值和pov值均明显高于实施例8~实施例10,在15d和10d分别达到最高值(0.67mda/kg和1.77meq/kg)。因此,本发明提供一种预调理肉制品腌制液,其中的天然抗氧化剂明显延缓预调理肉制品贮藏期间的脂质氧化水平,能够替代常规的磷酸盐和亚硝酸盐使用,对产品品质表现出更好的维持能力。
[0141]
肉色是预调理肉制品重要的感官品质,也是消费者衡量肉新鲜程度的重要指标。肌红蛋白氧化状态决定肉色,新鲜肉中omb相对含量一般在70%以上,但是脂质氧化容易引起omb氧化,当omb含量低于30%时,肉表现出红褐色而失去商品价值。实施例8~实施例10中,冷藏15d期间肉的a*值基本保持在13~19之间的水平,同时冷藏15d时omb相对含量均高于55%。同时,随着儿茶素、迷迭香提取物添加量的升高,a*值和omb相对含量降低趋势明显减缓。对比于实施例11,常规护色剂亚硝酸盐抑制和a*值和omb相对含量降低效果明显不如本发明制备的腌制液,贮藏15d时,a*值低于11、omb相对含量低于50%。因此,本发明提供一种预调理肉制品腌制液,其中使用的天然抗氧化剂能够显著提升预调理肉制品的抗氧化能力,降低omb氧化速率,同时乳酸链球菌素还具备一定的发色功能,能够显著提升产品在贮藏期间的肉色稳定性。
[0142]
tvb
‑
n值是标志新鲜肉中微生物引起的腐败变质的重要指标,用于评价肉的新鲜度。gb 2707
‑
2016《食品安全国家标准:鲜(冻)畜、禽产品》中规定,鲜肉中tvb
‑
n不得高于15mg/100g。实施例8~实施例10中,样品中tvb
‑
n值在冷藏15d时达到的最高值为13.71mg/100g,符合国家标准的要求。同时,随着乳酸链球菌素添加量的升高,样品贮藏期间tvb
‑
n值的升高趋势显著降低。对比于实施例11,本发明提供的预调理肉制品腌制液中天然生物防腐剂乳酸链球菌素抑菌能力显著。实施例11中尽管采用真空包装一定程度上抑制了好氧型微生物的生长繁殖,但是冷藏15d时,tvb
‑
n值仍达到了17.32mg/100g,超出国家标准最高限量(15mg/100g)。因此,本发明提供一种预调理肉制品腌制液,能够显著抑制微生物生长繁殖,提升预调理肉制品的贮藏性能,使其货架期达到15d。
[0143]
最后需要说明的是,以上实施例仅用以说明本发明实施例的技术方案而非对其进行限制,尽管参照较佳实施例对本发明实施例进行了详细的说明,本领域的普通技术人员
应当理解依然可以对本发明实施例的技术方案进行修改或者等同替换,而这些修改或者等同替换亦不能使修改后的技术方案脱离本发明实施例技术方案的范围。