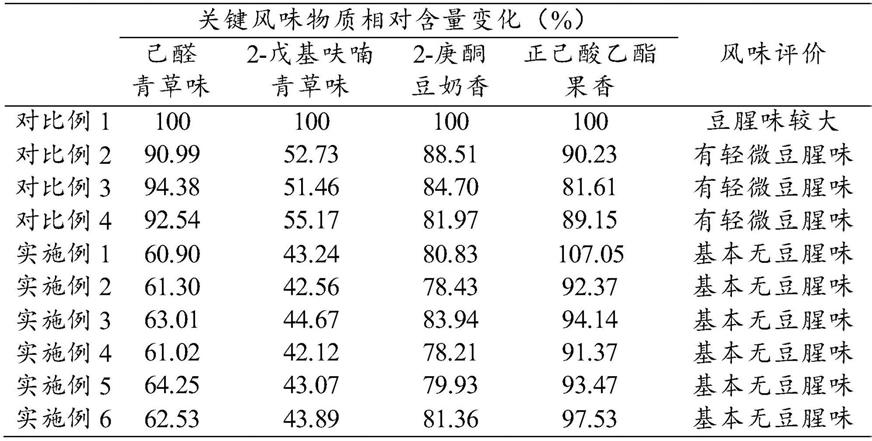
1.本发明涉及食品技术领域,尤其是涉及一种低豆腥味速溶大豆分离蛋白及其制备方法。
背景技术:2.大豆分离蛋白是以低温脱脂豆粕为原料,经过“碱提酸沉”工艺生产的一种蛋白质产品,其含有所有人体必需的氨基酸,具有较高的营养价值,被广泛的应用于食品、保健品等许多领域中。
3.在大豆分离蛋白生产过程中,大豆经过破碎之后,不饱和脂肪酸被氧化会产生一些醛、酮类的挥发性物质,形成令人不愉悦的豆腥味。当大豆分离蛋白作为配料加入到产品中后,会给产品带来不良风味,因此大大限制了其应用范围和使用添加量。所以,在大豆分离蛋白生产的过程中,蛋白生产企业一般会引入加热闪蒸工艺进行脱腥。加热闪蒸脱腥首先将物料加热到一定温度,然后输送到闪蒸罐中进行负压脱气。虽然在这个过程中,物料中易挥发的腥味物质以及小分子腥味物质会被抽出,但是仍有一定量的腥味物质残留,使得大豆分离蛋白具有较明显的豆腥味。
4.现有技术公开了采用物理方法或化学方法消除豆腥味。例如专利cn108935915a公开了一种无豆腥大豆分离蛋白粉的制备方法,将通过“碱提酸沉”工艺提取的大豆蛋白料液进行醛脱氢酶酶解和微波处理脱腥,之后将脱腥后的料液进行喷雾干燥即可得到所需产品。但该方法首先要采购适用于连续化生产的微波设备,投资较大;其次是方案中选用的醛脱氢酶价格较高且添加量较大,极大的增加了生产成本。专利cn108041254a公开了一种无腥味高乳化性的大豆分离蛋白的制备方法。该方案在豆粕碱提的过程加入琥珀酸酐对大豆蛋白进行琥珀酰化,随后对豆乳进行乳酸菌发酵处理。该方案虽然可以获得一种无豆腥味的大豆分离蛋白,但是其在生产过程中加入的辅料琥珀酸酐为非食品添加剂,因此限制了该大豆分离蛋白在一些食品中的应用。
5.此外,普通大豆分离蛋白在冲调食用和生产使用时往往存在溶解过慢和粉体结团的问题,这降低了大豆分离蛋白的品质和对下游产品生产使用造成了不利的影响。为了解决大豆分离蛋白溶解分散性问题,专利cn111587947a公开了一种高分散稳定性大豆分离蛋白的制备方法。该方案使用脱脂大豆粉通过“碱提酸沉”法制得大豆分离蛋白溶液,添加阴离子多糖辅料后,经喷雾干燥、分离过筛后,得到大豆分离蛋白原料。最后用去离子水调配成蛋白溶液,加入风味蛋白酶酶解和微波辐射处理,经冷冻干燥后得到高分散稳定性的大豆分离蛋白。但是此方案中蛋白二次溶解、冷冻干燥等间歇式工序,不仅会导致生产成本高,更不适用于工厂连续化生产,并且经过蛋白酶深度酶解后会产生苦涩的口感,影响产品品质。
6.因此,开发一种能够制备出豆腥味低、溶解分散性好的大豆分离蛋白的方法是非常必要的。
技术实现要素:7.有鉴于此,本发明要解决的技术问题在于提供一种低豆腥味速溶大豆分离蛋白的制备方法,本发明制备的速溶大豆分离蛋白豆腥味低同时分散性好。
8.本发明提供了一种低豆腥味速溶大豆分离蛋白的制备方法,包括如下步骤:
9.a)大豆蛋白碱浸提液、植酸酶和微生物活化液混合处理,得到微生物处理蛋白液;
10.b)将微生物处理蛋白液加入酸调节ph值,搅拌,固液分离,得到蛋白凝乳;
11.c)将蛋白凝乳和水混合,破碎洗涤、离心分离,得到水洗蛋白凝乳;
12.d)将水洗蛋白凝乳和水混合,分散,加碱调节ph值,得到大豆蛋白溶液;
13.e)将大豆蛋白溶液杀菌闪蒸、高压均质、干燥、得到大豆分离蛋白基础粉;向大豆分离蛋白基础粉喷涂造粒液,即得。
14.优选的,步骤a)所述大豆蛋白碱浸提液制备步骤具体为:将低温脱脂豆粕和水混合,加碱调节ph值,搅拌、固液分离,得到大豆蛋白浸提液;
15.所述低温脱脂豆粕和水混合的质量比为1:2~10;所述调节ph值为调节ph值至7~10;所述碱为食品级氢氧化钠;所述混合温度为30~55℃。
16.优选的,步骤a)所述微生物活化液为微生物和蔗糖混合保温活化,得到;所述蔗糖溶液的浓度为2wt%~3wt%;所述微生物和蔗糖的质量比为1:(10~15);所述保温活化具体为30~40℃保温活化30min;
17.所述微生物包括根霉菌、米曲霉、酿酒酵母、植物乳杆菌、干酪乳杆菌或保加利亚乳杆菌中的两种或两种以上。
18.优选的,步骤a)所述植酸酶的添加量为5u/(大豆蛋白浸提液干物质,g);所述微生物活化液的添加量为大豆蛋白浸提液中干物质质量的0.1%~1%;
19.所述处理的温度为20~45℃;处理的时间为10~60min。
20.优选的,步骤b)所述酸为盐酸;所述调节ph值为调节ph至为4.0~5.0。
21.优选的,步骤c)所述蛋白凝乳和水混合的质量比为1:(3~4)。
22.优选的,步骤d)所述加碱调节ph值为加碱调节ph值至6.8~7.8。
23.优选的,步骤e)所述杀菌温度为130~148℃,时间为8s;所述闪蒸的负压为0.05~0.08mpa;所述高压均质压力为15~20mpa;所述干燥的热风温度为165~180℃。
24.优选的,步骤e)所述造粒液为水、大豆油、聚氧乙烯(20)山梨醇酐单油酸酯、山梨糖醇酐脂肪酸酯、大豆磷脂、柠檬酸脂肪酸甘油酯、蔗糖脂肪酸酯、山梨醇酐单月桂酸酯和硬脂酰乳酸钠中的两种或两种以上;所述造粒液的喷涂量为大豆分离蛋白基础粉质量的0.05%~1%。
25.本发明提供了一种低豆腥味速溶大豆分离蛋白,由上述技术方案任一项所述的制备方法制得。
26.与现有技术相比,本发明提供了一种低豆腥味速溶大豆分离蛋白的制备方法,包括如下步骤:a)大豆蛋白碱浸提液、植酸酶和微生物活化液混合处理,得到微生物处理蛋白液;b)将微生物处理蛋白液加入酸调节ph值,搅拌,固液分离,得到蛋白凝乳;c)将蛋白凝乳和水混合,破碎洗涤、离心分离,得到水洗蛋白凝乳;d)将水洗蛋白凝乳和水混合,分散,加碱调节ph值,得到大豆蛋白溶液;e)将大豆蛋白溶液杀菌闪蒸、高压均质、干燥、得到大豆分离蛋白基础粉;向大豆分离蛋白基础粉喷涂造粒液,即得。本发明采用微生物对大豆蛋白浸
提液进行脱腥处理;同时,在大豆分离蛋白生产过程中,对蛋白凝乳使用工艺水进行二次洗涤,从而减少料液中豆腥味相关物质含量以及微生物在料液中生长、繁殖所产生的风味,提高最终产品的风味品质。此外,采用使用造粒液对大豆分离蛋白粉体进行喷涂处理,可以改善产品的溶解分散性能。
具体实施方式
27.本发明提供了一种低豆腥味速溶大豆分离蛋白及其制备方法,本领域技术人员可以借鉴本文内容,适当改进工艺参数实现。特别需要指出的是,所有类似的替换和改动对本领域技术人员来说是显而易见的,它们都属于本发明保护的范围。本发明的方法及应用已经通过较佳实施例进行了描述,相关人员明显能在不脱离本发明内容、精神和范围内对本文的方法和应用进行改动或适当变更与组合,来实现和应用本发明技术。
28.本发明提供了一种低豆腥味速溶大豆分离蛋白的制备方法,包括如下步骤:
29.a)大豆蛋白碱浸提液、植酸酶和微生物活化液混合处理,得到微生物处理蛋白液;
30.b)将微生物处理蛋白液加入酸调节ph值,搅拌,固液分离,得到蛋白凝乳;
31.c)将蛋白凝乳和水混合,破碎洗涤、离心分离,得到水洗蛋白凝乳;
32.d)将水洗蛋白凝乳和水混合,分散,加碱调节ph值,得到大豆蛋白溶液;
33.e)将大豆蛋白溶液杀菌闪蒸、高压均质、干燥、得到大豆分离蛋白基础粉;向大豆分离蛋白基础粉喷涂造粒液,即得。
34.本发明提供的低豆腥味速溶大豆分离蛋白的制备方法首先将大豆蛋白碱浸提液、植酸酶和微生物活化液混合处理,得到微生物处理蛋白液。
35.按照本发明,所述大豆蛋白碱浸提液制备步骤优选具体为:将低温脱脂豆粕和水混合,加碱调节ph值,搅拌、固液分离,得到大豆蛋白浸提液。
36.其中,所述低温脱脂豆粕和水混合的质量比优选为1:2~10;更优选为1:3~9;所述调节ph值为调节ph值至7~10;所述碱为食品级氢氧化钠;所述混合温度优选为30℃~55℃;更优选为35℃~50℃。
37.本发明对于所述固液分离的具体操作不进行限定,本领域技术人员熟知的经离心机固液分离即可。经离心机固液分离,除去固相豆渣,得到大豆蛋白浸提液。
38.本发明对于所述低温脱脂豆粕不进行限定,本领域技术人员熟知的即可。
39.本发明所述微生物活化液为微生物和蔗糖混合保温活化,得到。
40.本发明所述微生物包括根霉菌、米曲霉、酿酒酵母、植物乳杆菌、干酪乳杆菌或保加利亚乳杆菌中的两种或两种以上。
41.在本发明其中一部分优选实施方式中,微生物可以为植物乳杆菌和根霉菌按照3:1的比例混合;
42.在本发明其中一部分优选实施方式中,微生物可以为米曲霉和酿酒酵母按照3:1的比例混合;
43.在本发明其中一部分优选实施方式中,微生物可以为干酪乳杆菌和保加利亚乳杆菌按照3:1的比例混合;
44.在本发明其中一部分优选实施方式中,微生物可以为植物乳杆菌、根霉菌和酿酒酵母按照2:1:1的比例混合;
45.在本发明其中一部分优选实施方式中,微生物可以为干酪乳杆菌、保加利亚乳杆菌和米曲霉按照2:1:1的比例混合;
46.在本发明其中一部分优选实施方式中,微生物可以为植物乳杆菌、干酪乳杆菌、根霉菌和保加利亚乳杆菌按照2:2:1:1的比例混合。
47.本发明使用微生物对大豆蛋白浸提液进行脱腥处理,微生物种类包括但不局限于根霉菌、米曲霉、酿酒酵母、植物乳杆菌、干酪乳杆菌、保加利亚乳杆菌等。主要利用微生物在进行生长、繁殖生理活动时对料液中醛类、酮类物质的摄入,或者微生物产生的醛脱氢酶等酶对豆腥味相关物质进行分解,从而降低产品的豆腥味。
48.其中,所述蔗糖溶液的浓度为2wt%~3wt%;优选为2wt%;所述微生物和蔗糖的质量比为1:(10~15);所述保温活化具体为30~40℃保温活化30min。
49.本发明所述植酸酶的添加量为5u/(大豆蛋白浸提液干物质,g);所述微生物活化液的添加量为大豆蛋白浸提液中干物质质量的0.1%~1%。所述处理的温度为20~45℃;更优选为25~45℃;所述处理的时间优选为10~60min;更优选为10~50min。
50.将微生物处理蛋白液加入酸调节ph值;所述酸为盐酸;所述调节ph值为调节ph至为4.0~5.0。
51.调节ph值后搅拌,固液分离,得到蛋白凝乳。即为:搅拌均匀,经离心机固液分离,除去液相乳清水,得到蛋白凝乳。本发明对于上述操作不进行限定,本领域技术人员熟知的即可。
52.将蛋白凝乳和水混合,破碎洗涤、离心分离,得到水洗蛋白凝乳;优选具体为:向所述蛋白凝乳中加入3~4倍蛋白凝乳质量的工艺水进行破碎洗涤,经离心机分离,除去液相乳清水,得到水洗蛋白凝乳。
53.在大豆分离蛋白生产过程中,本发明人创造性的对蛋白凝乳使用工艺水进行二次洗涤,从而减少料液中豆腥味相关物质含量以及微生物在料液中生长、繁殖所产生的风味,提高最终产品的风味品质。
54.其中,所述蛋白凝乳和水混合的质量比优选为1:(3~4);更优选为1:3。
55.将水洗蛋白凝乳和水混合,分散,加碱调节ph值,得到大豆蛋白溶液;
56.所述分散为破碎分散;所述加碱调节ph值为加碱调节ph值至6.8~7.8;所述碱包括氢氧化钠,优选为食品级氢氧化钠。
57.将大豆蛋白溶液杀菌闪蒸、高压均质、干燥、得到大豆分离蛋白基础粉。
58.本发明所述杀菌温度为130~148℃,时间为8s;所述闪蒸的负压为0.05~0.08mpa;所述高压均质压力为15~20mpa;所述干燥优选为在喷雾干燥塔中进行热风脱水干燥;所述热风温度为165~180℃。
59.向大豆分离蛋白基础粉喷涂造粒液,即得。
60.本发明所述造粒液为水、大豆油、聚氧乙烯(20)山梨醇酐单油酸酯、山梨糖醇酐脂肪酸酯、大豆磷脂、柠檬酸脂肪酸甘油酯、蔗糖脂肪酸酯、山梨醇酐单月桂酸酯和硬脂酰乳酸钠中的两种或两种以上;
61.优选的,所述造粒液中各物质的比例可为水:大豆油:聚氧乙烯(20)山梨醇酐单油酸酯:山梨糖醇酐脂肪酸酯:大豆磷脂:柠檬酸脂肪酸甘油酯:蔗糖脂肪酸酯:山梨醇酐单月桂酸酯:硬脂酰乳酸钠为(500~1000):(0~5):(0~6):(0~5):(0~8):(0~5):(0~5):(0
~8):(0~6);更优选为(500~800):(0~4):(0~5):(0~4):(0~4):(0~4):(0~3):(0~5):(0~5)。
62.在本发明其中一部分优选实施方式中,所述造粒液中各物质的比例可为水:大豆油:硬脂酰乳酸钠:柠檬酸脂肪酸甘油酯=600:2:5:1;
63.在本发明其中一部分优选实施方式中,所述造粒液中各物质的比例可为水:聚氧乙烯(20)山梨醇酐单油酸酯:大豆油:山梨醇酐单月桂酸酯=500:2:1.5:5;
64.在本发明其中一部分优选实施方式中,所述造粒液中各物质的比例可为水:蔗糖脂肪酸酯:大豆磷脂:硬脂酰乳酸钠=500:3:1:4。
65.本发明所述造粒液的喷涂量优选为大豆分离蛋白基础粉质量的0.05%~1%;更优选为0.1%~0.9%。
66.本发明使用造粒液对大豆分离蛋白粉体进行喷涂处理,改善产品的溶解分散性能。经造粒液喷涂的大豆分离蛋白产品,其在水中溶解分散速度快、不易形成干粉团,且溶解后浆体细腻。
67.本发明提供了一种低豆腥味速溶大豆分离蛋白,由上述技术方案任一项所述的制备方法制得。
68.本发明提供了一种低豆腥味速溶大豆分离蛋白的制备方法,包括如下步骤:a)大豆蛋白碱浸提液、植酸酶和微生物活化液混合处理,得到微生物处理蛋白液;b)将微生物处理蛋白液加入酸调节ph值,搅拌,固液分离,得到蛋白凝乳;c)将蛋白凝乳和水混合,破碎洗涤、离心分离,得到水洗蛋白凝乳;d)将水洗蛋白凝乳和水混合,分散,加碱调节ph值,得到大豆蛋白溶液;e)将大豆蛋白溶液杀菌闪蒸、高压均质、干燥、得到大豆分离蛋白基础粉;向大豆分离蛋白基础粉喷涂造粒液,即得。本发明采用微生物对大豆蛋白浸提液进行脱腥处理;同时,在大豆分离蛋白生产过程中,对蛋白凝乳使用工艺水进行二次洗涤,从而减少料液中豆腥味相关物质含量以及微生物在料液中生长、繁殖所产生的风味,提高最终产品的风味品质。此外,采用使用造粒液对大豆分离蛋白粉体进行喷涂处理,可以改善产品的溶解分散性能。
69.本发明没有引入新的生产设备,不主要依赖于生物酶对产品的处理作用,所以不会大幅度提高生产成本。本发明没有使用化学试剂等辅料,所以产品更安全、在食品中的应用限制更小。
70.为了进一步说明本发明,以下结合实施例对本发明提供的一种低豆腥味速溶大豆分离蛋白及其制备方法进行详细描述。
71.实施例1
72.一种低豆腥味速溶大豆分离蛋白的制备方法,具体如下:
73.(1)将低温脱脂豆粕和40℃的工艺水按照1:8的质量比进行混合,使用食品级碱调节ph至7.5,搅拌均匀,经离心机分离,得到大豆蛋白浸提液。
74.(2)向大豆蛋白浸提液中加入5u/(大豆蛋白浸提液干物质,g)的植酸酶和0.8%的微生物活化液,于40℃下处理30min,得到微生物处理蛋白液。其中微生物活化液的配置方法为:将植物乳杆菌和根霉菌按照3:1的比例混合,加入15倍菌体质量的2%浓度的蔗糖溶液,于35℃下活化30min。
75.(3)向微生物处理蛋白液中加入食品级酸,调节ph至4.8,搅拌均匀,经离心机分
离,得到蛋白凝乳。然后向蛋白凝乳加入3倍的工艺水进行破碎洗涤,再次进行离心后,得到水洗蛋白凝乳。
76.(4)将水洗蛋白凝乳破碎加水分散,使用食品级碱调节ph至7.0,并将溶液固形物含量调节至12%,搅拌均匀,得到大豆蛋白溶液。
77.(5)将大豆蛋白溶液进行杀菌和闪蒸。杀菌温度为138℃,时间为8s。闪蒸压力为-0.06mpa。
78.(6)将步骤(5)处理后的物料进行高压均质处理,压力为18mpa。然后送入喷雾干燥塔,在170℃条件下进行脱水干燥,得到大豆分离蛋白基础粉。
79.(7)向所述大豆分离蛋白基础粉喷涂造粒液进行粉体表面喷涂处理,即得到大豆分离蛋白产品。其中造粒液的配置方法为水:大豆油:硬脂酰乳酸钠:柠檬酸脂肪酸甘油酯=600:2:5:1,喷涂量为大豆分离蛋白基础粉质量的0.2%。
80.实施例2
81.一种低豆腥味速溶大豆分离蛋白的制备方法,具体如下:
82.(1)将低温脱脂豆粕和45℃的工艺水按照1:10的质量比进行混合,使用食品级碱调节ph至7.2,搅拌均匀,经离心机分离,得到大豆蛋白浸提液。
83.(2)向大豆蛋白浸提液中加入5u/(大豆蛋白浸提液干物质,g)的植酸酶和0.5%的微生物活化液,于45℃下处理10min,得到微生物处理蛋白液。其中微生物活化液的配置方法为:将米曲霉和酿酒酵母按照3:1的比例混合,加入15倍菌体质量的2%浓度的蔗糖溶液,于30℃下活化30min。
84.(3)向微生物处理蛋白液中加入食品级酸,调节ph至4.5,搅拌均匀,经离心机分离,得到蛋白凝乳。然后向蛋白凝乳加入3倍的工艺水进行破碎洗涤,再次进行离心后,得到水洗蛋白凝乳。
85.(4)将水洗蛋白凝乳破碎加水分散,使用食品级碱调节ph至6.8,并将溶液固形物含量调节至11%,搅拌均匀,得到大豆蛋白溶液。
86.(5)将大豆蛋白溶液进行杀菌和闪蒸。杀菌温度为145℃,时间为8s。闪蒸压力为-0.07mpa。
87.(6)将步骤(5)处理后的物料进行高压均质处理,压力为20mpa。然后送入喷雾干燥塔,在175℃条件下进行脱水干燥,得到大豆分离蛋白基础粉。
88.(7)向所述大豆分离蛋白基础粉喷涂造粒液进行粉体表面喷涂处理,即得到大豆分离蛋白产品。其中造粒液的配置方法为水:聚氧乙烯(20)山梨醇酐单油酸酯:大豆油:山梨醇酐单月桂酸酯=500:2:1.5:5,喷涂量为大豆分离蛋白基础粉质量的0.25%。
89.实施例3
90.一种低豆腥味速溶大豆分离蛋白的制备方法,具体如下:
91.(1)将低温脱脂豆粕和45℃的工艺水按照1:10的质量比进行混合,使用食品级碱调节ph至7.0,搅拌均匀,经离心机分离,得到大豆蛋白浸提液。
92.(2)向大豆蛋白浸提液中加入5u/(大豆蛋白浸提液干物质,g)的植酸酶和0.5%的微生物活化液,于40℃下处理15min,得到微生物处理蛋白液。其中微生物活化液的配置方法为:将干酪乳杆菌和保加利亚乳杆菌按照3:1的比例混合,加入15倍菌体质量的2%浓度的蔗糖溶液,于37℃下活化30min。
93.(3)向微生物处理蛋白液中加入食品级酸,调节ph至4.5,搅拌均匀,经离心机分离,得到蛋白凝乳。然后向蛋白凝乳加入3倍的工艺水进行破碎洗涤,再次进行离心后,得到水洗蛋白凝乳。
94.(4)将水洗蛋白凝乳破碎加水分散,使用食品级碱调节ph至6.8,并将溶液固形物含量调节至11%,搅拌均匀,得到大豆蛋白溶液。
95.(5)将大豆蛋白溶液进行杀菌和闪蒸。杀菌温度为140℃,时间为8s。闪蒸压力为-0.07mpa。
96.(6)将步骤(5)处理后的物料进行高压均质处理,压力为20mpa。然后送入喷雾干燥塔,在175℃条件下进行脱水干燥,得到大豆分离蛋白基础粉。
97.(7)向所述大豆分离蛋白基础粉喷涂造粒液进行粉体表面喷涂处理,即得到大豆分离蛋白产品。其中造粒液的配置方法为水:蔗糖脂肪酸酯:大豆磷脂:硬脂酰乳酸钠=500:3:1:4,喷涂量为大豆分离蛋白基础粉质量的0.4%。
98.实施例4
99.一种低豆腥味速溶大豆分离蛋白的制备方法,具体如下:
100.(1)将低温脱脂豆粕和40℃的工艺水按照1:8的质量比进行混合,使用食品级碱调节ph至7.5,搅拌均匀,经离心机分离,得到大豆蛋白浸提液。
101.(2)向大豆蛋白浸提液中加入5u/(大豆蛋白浸提液干物质,g)的植酸酶和0.8%的微生物活化液,于40℃下处理30min,得到微生物处理蛋白液。其中微生物活化液的配置方法为:将植物乳杆菌、根霉菌和酿酒酵母按照2:1:1的比例混合,加入15倍菌体质量的2%浓度的蔗糖溶液,于35℃下活化30min。
102.(3)向微生物处理蛋白液中加入食品级酸,调节ph至4.8,搅拌均匀,经离心机分离,得到蛋白凝乳。然后向蛋白凝乳加入3倍的工艺水进行破碎洗涤,再次进行离心后,得到水洗蛋白凝乳。
103.(4)将水洗蛋白凝乳破碎加水分散,使用食品级碱调节ph至7.0,并将溶液固形物含量调节至12%,搅拌均匀,得到大豆蛋白溶液。
104.(5)将大豆蛋白溶液进行杀菌和闪蒸。杀菌温度为138℃,时间为8s。闪蒸压力为-0.06mpa。
105.(6)将步骤(5)处理后的物料进行高压均质处理,压力为18mpa。然后送入喷雾干燥塔,在170℃条件下进行脱水干燥,得到大豆分离蛋白基础粉。
106.(7)向所述大豆分离蛋白基础粉喷涂造粒液进行粉体表面喷涂处理,即得到大豆分离蛋白产品。其中造粒液的配置方法为水:大豆油:硬脂酰乳酸钠:柠檬酸脂肪酸甘油酯=600:2:5:1,喷涂量为大豆分离蛋白基础粉质量的0.2%。
107.实施例5
108.一种低豆腥味速溶大豆分离蛋白的制备方法,具体如下:
109.(1)将低温脱脂豆粕和45℃的工艺水按照1:10的质量比进行混合,使用食品级碱调节ph至7.0,搅拌均匀,经离心机分离,得到大豆蛋白浸提液。
110.(2)向大豆蛋白浸提液中加入5u/(大豆蛋白浸提液干物质,g)的植酸酶和0.5%的微生物活化液,于40℃下处理15min,得到微生物处理蛋白液。其中微生物活化液的配置方法为:将干酪乳杆菌、保加利亚乳杆菌和米曲霉按照2:1:1的比例混合,加入15倍菌体质量
的2%浓度的蔗糖溶液,于37℃下活化30min。
111.(3)向微生物处理蛋白液中加入食品级酸,调节ph至4.5,搅拌均匀,经离心机分离,得到蛋白凝乳。然后向蛋白凝乳加入3倍的工艺水进行破碎洗涤,再次进行离心后,得到水洗蛋白凝乳。
112.(4)将水洗蛋白凝乳破碎加水分散,使用食品级碱调节ph至6.8,并将溶液固形物含量调节至11%,搅拌均匀,得到大豆蛋白溶液。
113.(5)将大豆蛋白溶液进行杀菌和闪蒸。杀菌温度为140℃,时间为8s。闪蒸压力为-0.07mpa。
114.(6)将步骤(5)处理后的物料进行高压均质处理,压力为20mpa。然后送入喷雾干燥塔,在175℃条件下进行脱水干燥,得到大豆分离蛋白基础粉。
115.(7)向所述大豆分离蛋白基础粉喷涂造粒液进行粉体表面喷涂处理,即得到大豆分离蛋白产品。其中造粒液的配置方法为水:蔗糖脂肪酸酯:大豆磷脂:硬脂酰乳酸钠=500:3:1:4,喷涂量为大豆分离蛋白基础粉质量的0.4%。
116.实施例6
117.一种低豆腥味速溶大豆分离蛋白的制备方法,具体如下:
118.(1)将低温脱脂豆粕和40℃的工艺水按照1:8的质量比进行混合,使用食品级碱调节ph至7.5,搅拌均匀,经离心机分离,得到大豆蛋白浸提液。
119.(2)向大豆蛋白浸提液中加入5u/(大豆蛋白浸提液干物质,g)的植酸酶和0.8%的微生物活化液,于40℃下处理30min,得到微生物处理蛋白液。其中微生物活化液的配置方法为:将植物乳杆菌、干酪乳杆菌、根霉菌和保加利亚乳杆菌按照2:2:1:1的比例混合,加入15倍菌体质量的2%浓度的蔗糖溶液,于35℃下活化30min。
120.(3)向微生物处理蛋白液中加入食品级酸,调节ph至4.8,搅拌均匀,经离心机分离,得到蛋白凝乳。然后向蛋白凝乳加入3倍的工艺水进行破碎洗涤,再次进行离心后,得到水洗蛋白凝乳。
121.(4)将水洗蛋白凝乳破碎加水分散,使用食品级碱调节ph至7.0,并将溶液固形物含量调节至12%,搅拌均匀,得到大豆蛋白溶液。
122.(5)将大豆蛋白溶液进行杀菌和闪蒸。杀菌温度为138℃,时间为8s。闪蒸压力为-0.06mpa。
123.(6)将步骤(5)处理后的物料进行高压均质处理,压力为18mpa。然后送入喷雾干燥塔,在170℃条件下进行脱水干燥,得到大豆分离蛋白基础粉。
124.(7)向所述大豆分离蛋白基础粉喷涂造粒液进行粉体表面喷涂处理,即得到大豆分离蛋白产品。其中造粒液的配置方法为水:大豆油:硬脂酰乳酸钠:柠檬酸脂肪酸甘油酯=600:2:5:1,喷涂量为大豆分离蛋白基础粉质量的0.2%。
125.对比例1
126.一种大豆分离蛋白的制备方法,具体如下:
127.(1)将低温脱脂豆粕和45℃的工艺水按照1:10的质量比进行混合,使用食品级碱调节ph至7.2,搅拌均匀,经离心机分离,得到大豆蛋白浸提液。
128.(2)向大豆蛋白浸提液中加入食品级酸,调节ph至4.5,搅拌均匀,经离心机分离,得到蛋白凝乳。
129.(3)将水洗蛋白凝乳破碎加水分散,使用食品级碱调节ph至6.8,并将溶液固形物含量调节至11%,搅拌均匀,得到大豆蛋白溶液。
130.(4)将大豆蛋白溶液进行杀菌和闪蒸。杀菌温度为145℃,时间为8s。闪蒸压力为-0.05mpa。
131.(5)将步骤(5)处理后的物料进行高压均质处理,压力为20mpa。然后送入喷雾干燥塔,在175℃条件下进行脱水干燥,得到大豆分离蛋白产品。
132.对比例2
133.一种低豆腥味速溶大豆分离蛋白的制备方法,具体如实施例1所述,所不同的是:步骤(2)中所述微生物活化液中微生物为植物乳杆菌,步骤(7)中所述造粒液喷涂量为0.15%,其他步骤和参数均与实施例1一致。
134.对比例3
135.一种低豆腥味速溶大豆分离蛋白的制备方法,具体如实施例2所述,所不同的是:步骤(2)中所述微生物活化液中微生物为米曲霉,步骤(7)中所述造粒液喷涂量为0.2%,其他步骤和参数均与实施例2一致。
136.对比例4
137.一种低豆腥味速溶大豆分离蛋白的制备方法,具体如实施例3所述,所不同的是:步骤(2)中所述微生物活化液中微生物为干酪乳杆菌,步骤(7)中所述造粒液喷涂量为0.3%,其他步骤和参数均与实施例3一致。
138.试验例1
139.对上述实施例和对比例方法制备的大豆分离蛋白使用气相色谱质谱联用仪进行风味分析,同时由感官评价小组(≥10人)进行风味评价。结果如表1所示。
140.表1:实施例和对比例大豆分离蛋白风味评价及关键风味物质含量变化对比
[0141][0142]
试验例2
[0143]
对市售以及上述实施例、对比例方法制备的大豆分离蛋白从溶解分散性、粉体状态及流动性等方面进行评价。具体方法为:向105g去离子水中加入7g大豆分离蛋白,用玻璃棒以3r/s速度顺时针搅拌至无干粉的时长即为分散时间。将此溶液立即用20目标准筛进行过滤,筛上物用缓慢水洗涤都105℃烘干,其净重即为分散度。以上指标均重复测试三次。市
售样品购买于山东御馨生物科技有限公司。结果如表2所示。
[0144]
表2:实施例、对比例和市售大豆分离蛋白的溶解分散性和粉体状态对比
[0145][0146]
从表1可以看出,经过微生物处理的实施例1~6、对比例2~4与对比例1相比,两种关键豆腥味挥发性物质均有不同程度的下降。进一步对比实施例1~6和对比例2~4可以发现,使用两种或两种以上菌种协同处理物料要优于单一菌种的处理效果,并且通过感官评价,实施例1~6大豆分离蛋白的基本无豆腥味。另外,实施例的大豆分离蛋白香气物质含量也有所降低,风味清淡,更加便于在后续食品加工中调香调味。
[0147]
从表2可以看出,经过造粒液进行表面喷涂的实施例1~6、对比例2~4与对比例1相比,在水中的分散速度以及分散度均有明显提高,并且实施例的粉体均无扬尘。进一步对比实施例1~6和对比例2~4可以发现,在使用同种造粒液的条件下,喷涂量更高的实施例1~6具有更快的分散速度和更低的分散度。实施例与市售样品相比,虽粉体状态相似,但是分散性方面实施例的粉体有较大优势。
[0148]
因此,本发明制备得到的豆腥味低、溶解分散性好的大豆分离蛋白能够满足生产中对风味、复溶等方面的要求。
[0149]
以上所述仅是本发明的优选实施方式,应当指出,对于本技术领域的普通技术人员来说,在不脱离本发明原理的前提下,还可以做出若干改进和润饰,这些改进和润饰也应视为本发明的保护范围。