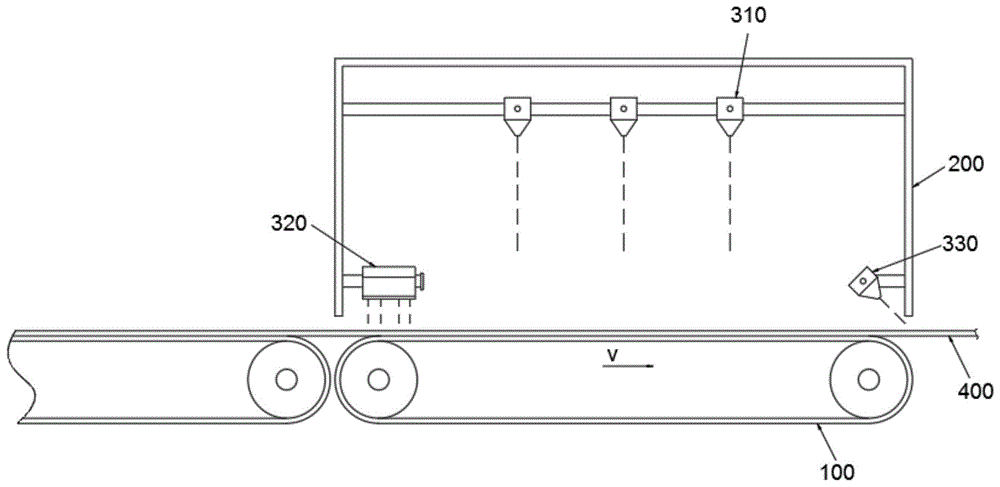
本申请涉及木质地板制造方法的
技术领域:
,具体涉及一种无醛柔性浸渍单板浸渍处理方法。
背景技术:
:薄木装饰贴面材料是一种应用广泛的贴面材料。薄木装饰贴面材料的传统生产方法是,采用单面胶带纸将数块薄木片(或单板)连结以初步使薄木片接长、拼宽后形成连续单板,再浸渍于三聚氰胺树脂中并干燥,热压复合于基材之上后,通过砂光将单面胶带纸砂除。在该种生产方法中,至少存在三个问题:(1)浸渍三聚氰胺树脂并干燥后使薄木脆化,而在热压复合工序、中转工序、或存储过程中极易发生薄木装饰贴面材料破损的现象,并由于薄木装饰贴面材料相对较脆,而增加了前述各工序的操作难度;(2)通过浸渍三聚氰胺树脂并干燥后制得的薄木装饰贴面材料,存在游离甲醛释放的问题;(3)利用单面胶带纸初步使薄木片接长、拼宽时,拼接不紧密,并会在拼接处留下较为明显的拼接缝隙,单面胶带纸痕迹难以较为有效地去除。技术实现要素:本申请的技术目的在于,克服上述技术问题,从而提供一种无醛柔性浸渍单板浸渍处理方法,其能够使浸渍后的薄木具有相对的柔性、不易破损,而使热压复合工序、中转工序、或存储过程的操作相对容易;制得的薄木装饰贴面材料无游离甲醛释放,安全、环保;且能够淡化、甚至消除相邻单板之间的拼接缝隙,提高制得的薄木装饰贴面材料外观质量。为实现本申请的技术目的,本申请公开一种无醛柔性浸渍单板浸渍处理方法,依次包括:单板软化的步骤、表面粗糙化处理的步骤、接长与拼宽的步骤、浸渍处理的步骤、冷压定型的步骤、干燥处理的步骤、收卷的步骤;其中,所述表面粗糙化处理的步骤,是在软化后的单板表面通过拉丝处理形成纤维丝层;所述浸渍处理的步骤,浸渍药剂为水性丙烯酸树脂。借由上述方法,通过使用水性丙烯酸树脂作为浸渍药剂,能够获得具有相对较好的柔性的薄木装饰贴面材料,以在一定程度上避免薄木贴面材料在热压复合工序、中转工序、或存储过程中出现破损的问题;并且水性丙烯酸树脂的使用能够解决游离甲醛释放的问题,从而制得相对安全、环保的柔性薄木装饰贴面材料。与此同时,通过在浸渍处理的步骤之前设置表面粗糙化处理的步骤,以在单板的表面形成纤维丝层,从而能够利用纤维丝层的存在,提高水性丙烯酸树脂的浸渍量,以进一步提高制得的薄木装饰贴面的韧性,避免薄木贴面材料在热压复合工序、中转工序、或存储过程中出现破损的问题。另一个方面,利用纤维丝层的存在,还能够在冷压定型的步骤中,通过整平纤维丝层而遮盖相邻单板的拼接缝隙,淡化、甚至消除相邻单板之间的拼接缝隙的同时,在一定程度上提高相邻单板之间的拼接(连结)强度。作为一种优选的实施方式,所述表面粗糙化处理的步骤,是依次通过一道0.5mm杜邦丝拉丝、一道1.0mm杜邦丝拉丝和两道0.3mm钢丝拉丝。作为一种优选的实施方式,所述纤维丝层与所述单板的本体表面通过纤维连结,且所述纤维丝层的纤维丝长度为0.5~1.5mm。在本技术方案中,将纤维丝层的纤维丝长度控制在0.5~1.5mm能够较为有效地在保证纤维丝对水性丙烯酸酯的吸收的同时,控制表面粗糙化处理的工序步骤。与此同时,该长度范围的纤维丝长度能够在后续的接长与拼宽的步骤中对拼接缝提供较为有效地的结合力,并在冷压定型的步骤中被顺利地整平化而使薄木装饰贴面形成平整、光滑的装饰面。作为一种优选的实施方式,所述单板软化的步骤,是单板在软化剂中常压浸渍,后干燥至含水率25~50%。作为一种优选的实施方式,所述单板软化的步骤后,将单板干燥至含水率36~40%。在本技术方案中,发明人经过长期试验与生产实践,发现通过对单板在单板软化的步骤之后的含水率进行控制,能够影响浸渍处理的步骤中的水性丙烯酸树脂的浸渍量,以及冷压定型的步骤中的整平化处理效果。作为一种优选的实施方式,所述浸渍处理的步骤中,所述水性丙烯酸树脂通过以下工序步骤调制而成:步骤1、取丙烯酸树脂乳液100份,加入10份水,搅拌均匀;步骤2、加入耐磨颗粒;步骤3、加入7~15份水,搅拌均匀;调制而成的所述水性丙烯酸树脂的树脂浓度为80~85%;且,在所述浸渍处理的步骤中,水性丙烯酸树脂浸渍量为98~105%。在本技术方案中,通过分两次加入水,以降水性丙烯酸树脂的树脂浓度稀释至80~85%,从而能够使制得的水性丙烯酸树脂的处于涂4杯粘度为13s-19s的粘度,从而,当单板浸渍于其中后,能够达到98~100%的树脂浸渍量。在另一个方面,通过在水性丙烯酸树脂中添加耐磨颗粒,能够提高最终制得的薄木装饰贴面材料的耐磨性能;且相较于在其表面涂布耐磨油漆的方式而言,能够在薄木装饰贴面材料的整个厚度上均获得相对较好的耐磨性能。与此同时,将加入耐磨颗粒的步骤设置于两次加入水的步骤之间,则能够有利于耐磨颗粒在水性丙烯酸树脂中的均匀分散,以尽可能保证浸渍后的单板的幅面上各处的耐磨性能均匀一致。作为一种优选的实施方式,所述耐磨颗粒的添加量为30~35g/㎡。在本技术方案中,耐磨颗粒的添加量以单板在浸渍水性丙烯酸树脂后,其幅面上单位平方面积中实际的耐磨颗粒含量作为投放标准。作为一种优选的实施方式,所述接长与拼宽的步骤中,采用热固型胶线完成相邻单板间的接长与拼宽,当所述单板的厚度为0.2~0.6mm时,接长处的长度损耗为0~8mm、拼宽处的宽度损耗为0~4mm。作为一种优选的实施方式,所述接长与拼宽的步骤中,采用热固型胶线完成相邻单板间的接长与拼宽,当所述单板的厚度为1.0~1.2mm时,接长处的拼接齿的齿长为5~8mm。作为一种优选的实施方式,所述冷压定型的步骤中,采用压辊式冷压定型,压辊压力为1.5~3.0mpa。在本申请的技术方案中,借由水性丙烯酸树脂作为浸渍药剂、以及纤维丝层的设置此二项改进方案,从而本申请的无醛柔性浸渍单板浸渍处理方法,能够使浸渍后的薄木具有相对的柔性、不易破损,而使热压复合工序、中转工序、或存储过程的操作相对容易;制得的薄木装饰贴面材料无游离甲醛释放,安全、环保;且能够淡化、甚至消除相邻单板之间的拼接缝隙,提高制得的薄木装饰贴面材料外观质量。附图说明构成本申请的一部分的附图用来提供对本申请的进一步理解,本申请的示意性实施例及其说明用于解释本申请,并不构成对本申请的不当限定。图1是本申请实施例3的收卷的步骤中所采用的气力张紧系统的一种结构示意图;图2是本申请实施例3的入口气力张紧单元的一种结构示意图;在附图中:100-输送结构,200-罩体,300-气力张紧结构,310-垂直气力张紧单元,320-入口气力张紧单元,330-出口气力张紧单元,321-第一入口气力张紧元件,322-第二入口气力张紧元件,400-连续单板。具体实施方式下面将参考附图并结合实施例来详细说明本发明。实施例1:一种无醛柔性浸渍单板浸渍处理方法,依次包括:单板软化的步骤、表面粗糙化处理的步骤、接长与拼宽的步骤、浸渍处理的步骤、冷压定型的步骤、干燥处理的步骤、收卷的步骤。处理单板的规格为900mm(长)×200mm(宽)×0.4mm(厚)。一、单板软化的步骤,是将单板浸渍于软化剂中,采用的软化剂可以是现有技术中任意一种,例如包括聚乙烯醇、冰醋酸、渗透剂、去离子水等成分的木材软化剂;采用的软化处理工艺可以是现有技术中任意一种工艺方法,例如将待软化处理的单板在常温、常压下于软化剂中浸泡4~5小时,或在50~60℃、常压下于软化剂中浸泡1~3小时;将软化处理后的单板干燥至含水率低于20%。二、表面粗糙化处理的步骤,是取软化处理后且经过含水率干燥的单板,在其表面通过拉丝处理形成纤维丝层,具体来说是利用现有技术中任意一种拉丝机,在单板表面形成纤维丝长度为0.3~0.5mm的纤维丝层,并且此时,纤维丝层与单板的本体表面通过纤维连结。三、接长与拼宽的步骤,是采用热熔型胶线自动拼接设备对表面粗糙化处理后的单板进行横向拼宽、纵向接长,接长处的长度损耗为0~8mm(具体是6mm)、拼宽处的宽度损耗为0~4mm(具体是3.4mm);在本步骤中,相邻两个单板的接长处重叠3mm,因此接长处的长度损耗为6mm,相邻两个单板的拼宽处重叠1.7mm,因此拼宽处的宽度损耗为3.4mm。四、浸渍处理的步骤,将单板常温、常压条件下浸渍于现有技术中任意一种水性丙烯酸树脂中,树脂含量为50~60%,浸渍时间为5min。五、冷压定型的步骤,采用压辊式冷压定型,压辊压力为1.5~3.0mpa(具体是2.0mpa),连续单板自进入压辊通道至离开的耗时为5~7min。六、干燥处理的步骤,可采用现有技术中任意一种干燥方式,将连续单板的含水率干燥至12~16%,例如采用压辊式热压干燥,热压辊温度为120~130℃,连续单板自进入热压辊通道至离开的耗时为15~20min。七、收卷的步骤,是采用现有技术中任意一种收卷方式。特别地,由于浸渍水性丙烯酸树脂后的连续单板具有相对较好的柔性与韧性,因此,在收卷的步骤中应在收卷前对连续单板的宽度方向进行张紧,以避免收卷时大幅面的连续单板发生褶皱,影响产品质量。同时由于本实施例技术方案的连续单板在接长与拼宽的步骤中,未采用托底,且仅重叠了其幅面上相对较小的宽度与长度部分,因此,宜采用连续压辊的方式对连续单板进行张紧。实施例2:实施例2与实施例1的区别在于:在单板软化的步骤中,不对软化处理后的单板进行干燥处理,而直接进入表面粗糙化处理的步骤。在表面粗糙化处理的步骤中,将经过含水率干燥后的单板依次通过一道0.5mm杜邦丝拉丝、一道1.0mm杜邦丝拉丝和两道0.3mm钢丝拉丝,以在单板表面形成纤维丝层,纤维丝层的纤维丝长度为2.0~2.2mm。在接长与拼宽的步骤中,接长处的长度损耗为0mm、拼宽处的宽度损耗为0mm,即在本实施例中,不对接长处、拼宽处作材料重叠处理。在浸渍处理的步骤中,将单板常温、常压条件下浸渍于现有技术中任意一种水性丙烯酸树脂中,树脂含量为50~60%,浸渍时间为5min。实施例3:实施例3与实施例1的区别在于:处理单板的规格为900mm(长)×200mm(宽)×0.6mm(厚)。在单板软化的步骤中,将软化处理后的单板干燥至含水率25~50%,具体是将软化处理后的单板干燥至含水率30±2%。在接长与拼宽的步骤中,接长处的长度损耗为0~8mm(具体是2mm)、拼宽处的宽度损耗为0~4mm(具体是1mm);在本步骤中,相邻两个单板的接长处重叠1mm,因此接长处的长度损耗为2mm,相邻两个单板的拼宽处重叠0.5mm,因此拼宽处的宽度损耗为1mm。在表面粗糙化处理的步骤中,将经过含水率干燥后的单板依次通过一道0.5mm杜邦丝拉丝、一道1.0mm杜邦丝拉丝和两道0.3mm钢丝拉丝,以在单板表面形成纤维丝层,纤维丝层的纤维丝长度为0.5~1.5mm,具体是0.5~0.7mm。在浸渍处理的步骤中,水性丙烯酸树脂通过以下工序步骤调制而成:步骤1、取丙烯酸树脂乳液100份,加入10份水,搅拌均匀;步骤2、加入耐磨颗粒,例如纳米三氧化二铝颗粒,添加量为30~35g/㎡(具体是30g/㎡);步骤3、加入7~15份水(具体是15份水),搅拌均匀,调制而成的水性丙烯酸树脂的树脂浓度为80%。在干燥处理的步骤中,采用隧道式(红外加热或鼓风式加热)干燥方式,将连续单板的含水率干燥至12~16%,隧道内温度为120~130℃,连续单板自进入隧道至离开的耗时为15~20min。在收卷的步骤中,采用气力张紧系统对连续单板进行张紧处理。参考图1所示的气力张紧系统,包括接入主输送线的输送结构100、设置于所述输送结构100之上的罩体200、以及设置于所述罩体200内部的气力张紧结构。其中,输送结构100为现有技术中任意一种皮带或棍子输送线;罩体200通过输送结构100的机架或主输送线上固定梁固定安装于输送结构100之上,其下部与输送结构100的输送工作面之间具有4~5cm间隙;气力张紧结构300包括设置于罩体200内的上部的垂直气力张紧单元310、设置于罩体200内的入口处的入口气力张紧单元320、以及设置于罩体200内的出口处的出口气力张紧单元330。结合图2所示,垂直气力张紧单元310包括至少一个轴向横跨输送结构100宽度方向设置的风刀,在本实施例中是3个,其出风方向垂直于输送结构100的输送工作面,垂直气力张紧单元310通过现有技术中任意一种风刀架固定安装。入口气力张紧单元320设置于罩体200内的下部,包括沿输送结构100的宽度方向设置的一对第一入口气力张紧元件321、一对第二入口气力张紧元件322,且一对第一入口气力张紧元件321设置于一对第二入口气力张紧元件322的两侧。第一入口气力张紧元件321为轴向沿连续单板400进给方向v设置的短风刀,其出风方向朝向输送结构100的侧边,且出风方向与输送结构100的输送工作面之间形成45±1°的锐角夹角;一对第一入口气力张紧元件321沿输送结构100的轴向镜像设置。第二入口气力张紧元件322为轴向沿连续单板400进给方向v设置的短风刀,其出风方向朝向输送结构100的侧边,且出风方向与输送结构100的输送工作面之间形成30±1°的锐角夹角;一对第二入口气力张紧元件322沿输送结构100的轴向镜像设置。第一入口气力张紧元件321、第二入口气力张紧元件322均通过现有技术中任意一种风刀架固定安装。出口气力张紧单元330设置于罩体200内的下部,为一个轴向横跨输送结构100宽度方向设置的风刀,其出风方向朝向罩体200的出口处(气力张紧系统的末端),且出风方向与输送结构100的输送工作面之间形成45±1°的锐角夹角。出口气力张紧单元330通过现有技术中任意一种风刀架固定安装。实施例4:实施例4与实施例1的区别在于:处理单板的规格为900mm(长)×200mm(宽)×0.6mm(厚)。在单板软化的步骤中,将软化处理后的单板干燥至含水率25~50%,具体是将软化处理后的单板干燥至含水率35±2%。在接长与拼宽的步骤中,接长处的长度损耗为0mm、拼宽处的宽度损耗为0mm,即在本实施例中,不对接长处、拼宽处作材料重叠处理。在表面粗糙化处理的步骤中,将经过含水率干燥后的单板依次通过一道0.5mm杜邦丝拉丝、一道1.0mm杜邦丝拉丝和两道0.3mm钢丝拉丝,以在单板表面形成纤维丝层,纤维丝层的纤维丝长度为0.5~1.5mm,具体是0.7~0.9mm。在浸渍处理的步骤中,水性丙烯酸树脂通过以下工序步骤调制而成:步骤1、取丙烯酸树脂乳液100份,加入10份水,搅拌均匀;步骤2、加入耐磨颗粒,例如纳米三氧化二铝颗粒,添加量为30~35g/㎡(具体是32g/㎡);步骤3、加入7~15份水(具体是10份水),搅拌均匀,调制而成的水性丙烯酸树脂的树脂浓度为83%。在干燥处理的步骤中,采用隧道式(红外加热或鼓风式加热)干燥方式,将连续单板的含水率干燥至12~16%,隧道内温度为120~130℃,连续单板自进入隧道至离开的耗时为15~20min。在收卷的步骤中,采用与实施例3中相同的气力张紧系统对连续单板进行张紧处理。实施例5:实施例5与实施例1的区别在于:处理单板的规格为900mm(长)×200mm(宽)×1.0mm(厚)。在单板软化的步骤中,将软化处理后的单板干燥至含水率25~50%,具体是将软化处理后的单板干燥至含水率38±2%。在接长与拼宽的步骤中,接长处的长度损耗为0~8mm(具体是6mm)、拼宽处的宽度损耗为0mm;在本步骤中,相邻两个单板的接长处制作齿长为3mm的拼接齿,因此接长处的长度损耗为6mm,不对拼宽处作材料重叠或开齿处理。在表面粗糙化处理的步骤中,将经过含水率干燥后的单板依次通过一道0.5mm杜邦丝拉丝、一道1.0mm杜邦丝拉丝和两道0.3mm钢丝拉丝,以在单板表面形成纤维丝层,纤维丝层的纤维丝长度为0.5~1.5mm,具体是0.9~1.2mm。在浸渍处理的步骤中,水性丙烯酸树脂通过以下工序步骤调制而成:步骤1、取丙烯酸树脂乳液100份,加入10份水,搅拌均匀;步骤2、加入耐磨颗粒,例如纳米三氧化二铝颗粒,添加量为30~35g/㎡(具体是33g/㎡);步骤3、加入7~15份水(具体是12份水),搅拌均匀,调制而成的水性丙烯酸树脂的树脂浓度为82%。在干燥处理的步骤中,采用隧道式(红外加热或鼓风式加热)干燥方式,将连续单板的含水率干燥至12~16%,隧道内温度为125~135℃,连续单板自进入隧道至离开的耗时为15~20min。实施例6:实施例6与实施例1的区别在于:处理单板的规格为900mm(长)×200mm(宽)×1.2mm(厚)。在单板软化的步骤中,将软化处理后的单板干燥至含水率25~50%,具体是将软化处理后的单板干燥至含水率45±2%。在接长与拼宽的步骤中,接长处的长度损耗为0~8mm(具体是8mm)、拼宽处的宽度损耗为0mm;在本步骤中,相邻两个单板的接长处制作齿长为4mm的拼接齿,因此接长处的长度损耗为8mm,不对拼宽处作材料重叠或开齿处理。在表面粗糙化处理的步骤中,将经过含水率干燥后的单板依次通过一道0.5mm杜邦丝拉丝、一道1.0mm杜邦丝拉丝和两道0.3mm钢丝拉丝,以在单板表面形成纤维丝层,纤维丝层的纤维丝长度为0.5~1.5mm,具体是1.2~1.5mm。在浸渍处理的步骤中,水性丙烯酸树脂通过以下工序步骤调制而成:步骤1、取丙烯酸树脂乳液100份,加入10份水,搅拌均匀;步骤2、加入耐磨颗粒,例如纳米三氧化二铝颗粒,添加量为30~35g/㎡(具体是35g/㎡);步骤3、加入7~15份水(具体是7份水),搅拌均匀,调制而成的水性丙烯酸树脂的树脂浓度为85%。在干燥处理的步骤中,采用隧道式(红外加热或鼓风式加热)干燥方式,将连续单板的含水率干燥至12~16%,隧道内温度为130~140℃,连续单板自进入隧道至离开的耗时为15~20min。采用实施例1至实施例6的无醛柔性浸渍单板浸渍处理方法所制得的薄木装饰贴面材料的产品性能参考表1所示。其中,甲醛释放量参考gb18580-2017中相关章节记载的检测手段进行实验;表面平整度采用肉眼、日光下观察;耐磨性能参考gb/t18103-2000中相关章节记载的检测手段进行实验,且实验对象为未经过表面漆饰处理的连续单板,实验其表面经过4000转后砂纸(180#)打磨后的磨损深度。表1.实施例1至实施例6的薄木装饰贴面材料的产品性能组别浸胶量(%)甲醛释放量(mg/m3)表面平整度耐磨性能(mm)实施例1530差0.04实施例2740差0.04实施例3980良0.02实施例41020优0.02实施例51050优0.01实施例61000优0.01由表1的实验结果可知,提高表面粗糙化处理的步骤中所形成的纤维丝层的纤维丝长度,能够较为有效地提高水性丙烯酸树脂的浸渍量;与此同时,在单板软化的步骤,将单板含水率控制在38±2%(36~40%)时,即使纤维丝的长度相对较长,也能够在冷压定型的步骤中,获得较为理想的表面平整度。以上所述仅为本申请的优选实施例而已,并不用于限制本申请,对于本领域的技术人员来说,本申请可以有各种更改和变化。凡在本申请的精神和原则之内,所作的任何修改、等同替换、改进等,均应包含在本申请的保护范围之内。当前第1页12