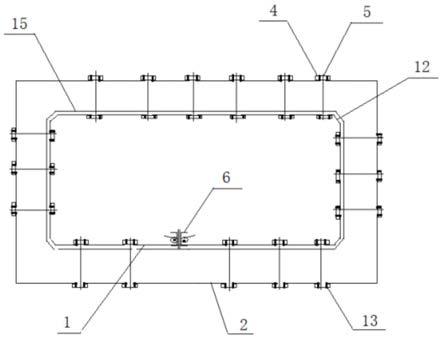
1.本发明涉及一种模板组结构和混凝土槽体结构及槽体结构的施工方法,特别涉及一种一体成型塑胶膜层防腐内衬混凝土槽体结构及施工所需的模板组和施工工法,属于建筑及设备防腐领域。
背景技术:2.随着现代工业社会的发展,设备和建筑的腐蚀成为化工、环保、造纸、冶金等众多行业必须面对的问题,每年因为腐蚀造成的损失非常巨大。而对于大型的混凝土槽体或设备,腐蚀问题尤为重要,腐蚀不仅会影响正常的生产活动,腐蚀导致的化学介质的外渗还会导致严重的环保问题,因而国家每年在防腐处理方面花费巨大。
3.通常的防腐型式均采用混凝土施工完毕后贴衬防腐层的工法,其费用高、施工周期长、施工质量难于控制、施工环境污染严重并且施工过程当中会对施工人员和管理人员的健康造成影响。
4.传统的混凝土槽体防腐施工步骤通常包括:基体处理,需要去除模板的错缝及表面的凹凸和污染等问题,打磨掉表面的浮浆。然后根据材料的不同,采用不同的黏贴和喷涂防腐材料等各种工艺。
5.显而易见,传统的混凝土储槽防腐内衬施工中存在的问题包括:
6.(1)浪费人工:基体的打磨、修补需要大量的人工。
7.(2)浪费材料:打磨去除的混凝土本身也是一种资源,另外打磨过程需要消耗电能和砂轮片及打磨设备;现场施工过程中包装桶内不可避免会有残余,施工过程当中的掉落、污染、修复以及经常出现的返工也会带来材料的浪费。通常情况下5-10%的材料富裕量是需要计算在备料中的,这些都是物料的浪费。
8.(3)污染环境:基体的打磨会造成扬尘,从而带来环境污染,现场过程中用的的底漆、涂料、胶粘剂等均会带来voc的排放。
9.(4)施工成本高:由于传统施工中的人员成本越来越高,比如10年前工人成本约100元/人日。如今则需要500元/人日。2020年之后很多防腐内衬的施工成本已经远高于材料成本。另外,愿意从事现场施工的年轻人越来越少,未来的施工人工成本也会越来越高。
10.(5)质量控制困难:由于传统的施工需要大量的人工操作,施工质量除了材料本身性能和施工性外,工人的责任心和技术水平严重影响着防腐内衬的质量,不可控因素太多。
技术实现要素:11.本发明要解决的技术问题是:如何降低基体打磨、修补所需的人工劳动力和材料,减少基体打磨造成的扬尘。
12.为了解决上述技术问题,本发明的技术方案是提供了一种模板组结构,其特征在于,包括内模板组和外模板组,外模板组设于内模板组的外圈,内模板组的底部边缘设有限位板,内模板组中至少一处设有用于夹紧膜层的双道垂直方向的膜层固定装置。
13.优选地,所述的内模板组和外模板组均由分块的垂直高度一致的模板组成,同一模板组的模板之间通过固定柱连接。
14.优选地,所述的内模板组和外模板组对应的固定柱对应成组,并设置在同一对应位置,每组对应固定柱通过设置在上部的限位连接杆固定内模板组和外模板组之间的空间。
15.优选地,所述的内模板组的转角处设有转角模板,转角模板为带有一定弧度的立柱,作为模板在转角处的连接和固定,并形成一定弧度的混凝土及膜层阴角;模板同对应的固定柱之间通过螺栓和卡箍固定连接;限位板的厚度为0.1-5mm,深度为2-5mm。
16.优选地,所述的膜层固定装置由两个开口和每个开口中间的一根夹紧装置组成,每个夹紧装置设有至少两个具有夹紧功能的夹具和作为夹紧旋钮的紧固器组成;通过夹紧装置可以将两个开口处的膜层进行夹紧固定。
17.优选地,所述的两个开口的宽度为3-5mm、垂直高度与内模板组高度相同。
18.优选地,所述的紧固器包括把手、旋杆以及与旋杆连接的偏心卡口,偏心卡口在侧边开口并可以旋出或夹紧膜层。
19.一种混凝土槽体结构,其特征在于,所述的混凝土槽体结构使用一种模板组结构一体成型,包括混凝土基体,混凝土基体设于模板组结构的内模板组和外模板组之间,混凝土基体与柔性膜层一侧粘接,柔性膜层设于内模板组与混凝土基体之间,构成一体成型塑胶膜层防腐内衬混凝土槽体结构;混凝土基体与柔性膜层一体成型。
20.优选地,所述的柔性膜层一侧复合了一层用于同混凝土基体粘接的无纺布层或纤维布层;柔性膜层上所有的拼缝部位通过不带可粘接面的柔性膜层条覆盖连接。
21.一种槽体结构的施工方法,其特征在于,所述的施工方法使用一种模板组结构一体成型混凝土槽体结构,其包括以下步骤:
22.步骤1:首先将固定柱根据设计要求固定在确定的地面位置,确保内模板组和外模板组上固定柱之间的间距满足浇筑后混凝土厚度要求;
23.步骤2:按照顺序将内模板组和外模板组已经对应的转角处的转角模板和紧固器安装就位,并连接固定;
24.步骤3:根据内模板组壁面的长度,裁切长度大于内模板组周长的柔性膜层备用,柔性膜层至少单侧具备被混凝土凝固粘结的性能;
25.步骤4:将柔性膜层放入内模板组和外模板组之间的浇筑空间,将可粘结面背向内模板组;柔性膜层的下沿放置在限位板上;
26.步骤5:将柔性膜层的两端从紧固器的开口处引出,并施适度拉力,使柔性膜层紧贴内模板组的模板,并用紧固器夹紧固定;
27.步骤6:浇筑混凝土,并按照要求向上搭设上一层模板组结构,重复上述步骤1-5的模板组结构和柔性膜层的安装,并进行浇筑;
28.步骤7:所有的施工完成后,混凝土基体上留出的缝隙采用同柔性膜层材质相同或相近的材料进行填充,对于紧固器开口处的柔性膜层端口部位,采用人工打磨,先对混凝土基体进行清理打磨,并用胶粘剂进行粘结;
29.步骤8:完成上述两个部位的热熔焊填缝和粘结后,对所有的拼缝部位再采用不带可粘接面的柔性膜层条采用热风进行焊接覆盖处理;最后形成完整的混凝土槽体结构。
30.本发明提供一种模板组结构和混凝土槽体结构及槽体结构的施工方法,其结构简单,可有效的解决传统混凝土储槽防腐内衬存在的问题,以克服现有防腐内衬施工中的不足。通过发明,避免模板的错缝及表面的凹凸和污染问题以及打磨掉表面的浮浆,仅仅只需在混凝土基体和柔性膜层的开口位置进行打磨即可。
31.混凝土槽体结构是利用模板组结构浇筑混凝土基体,并与柔性膜层粘接,构成一体成型塑胶膜层防腐内衬混凝土槽体结构,混凝土基体与柔性膜层一体成型,耐腐蚀抗渗漏;使用的模板组结构,其结构简单,施工方便,工期短,成本低。
附图说明
32.图1为一种模板组结构的俯视图;
33.图2为内模板组上的固定柱、紧固件的立面示意图;
34.图3为一种混凝土槽体结构的局部侧面示意图。
具体实施方式
35.为使本发明更明显易懂,兹以优选实施例,并配合附图作详细说明如下。
36.本发明提供了一种模板组结构,可附贴膜层并具备紧缩功能,如图1、图2所示,其包括内模板组1和外模板组2,外模板组2设于内模板组1的外圈,在内模板组1的底部边缘设有一水平的限位板3,在内模板组1中至少有一处设置了具备夹紧膜层15功能的双道垂直方向的膜层固定装置。
37.内模板组1和外模板组2均由分块的垂直高度一致的模板组成,同一模板组的模板之间设有固定柱4,固定柱4由垂直的方钢或槽钢及其他型钢制作的立柱进行固定和限位。限位板3的厚度通常为0.1-5mm,由于限位板3在安装时用来托住膜层15,防止膜层15滑落,厚度同膜层15,太厚会插进混凝土,因此,限位板3的深度依照膜层15的厚度进行设计,通常为2-5mm。本实施例中,膜层15为柔性膜层。
38.内模板组1和外模板组2对应的固定柱4对应成组,并设置在同一对应位置,每组对应固定柱4通过设置在上部的限位连接杆5固定内模板组1和外模板组2之间的空间,也就是浇筑混凝土的厚度。限位连接杆5的作用既可以防止撑模,又可以使模板组更加有效的定位。
39.膜层固定装置由两个开口和每个开口中间的一根夹紧装置组成,两个开口的宽度为3-5mm、垂直高度与内模板组1高度相同,每个夹紧装置设有至少两个具有夹紧功能的夹具6和作为夹紧旋钮的紧固器7组成。通过夹紧装置可以将两个开口处的膜层15进行夹紧固定。紧固器7通过连接件与其临近的模板固定,连接件的高度超出开口的高度,内模板组1上至少设置一组这样的夹具6和模板。紧固器7包括把手8、旋杆9以及与旋杆9连接的偏心卡口10组成,偏心卡口10在侧边开口并可以旋出或夹紧膜层15。
40.内模板组1的转角处设有转角模板12,转角模板12采用带有一定弧度的立柱,作为模板在转角处的连接和固定,并形成一定弧度的混凝土及膜层阴角,避免出现直角或锐角以免膜层形成较大的弯曲应力。相邻两个模板之间设有固定柱4,模板同对应的固定柱4之间用螺栓和卡箍13方式进行固定。
41.本发明提供了一种混凝土槽体结构,其使用一种模板组结构一体成型,如图3所
示,其利用一种模板组结构浇筑混凝土基体16,混凝土基体16设于模板组结构的内模板组1和外模板组2之间,混凝土基体16与膜层15粘接,膜层15设于内模板组1与混凝土基体16之间,构成一体成型塑胶膜层防腐内衬混凝土槽体结构,混凝土基体16与膜层15一体成型,耐腐蚀抗渗漏。
42.膜层15一侧复合了一层无纺布或纤维布层11,可用于同混凝土基体16粘接。
43.混凝土基体16留出的缝隙采用同膜层15材质相近的材料进行填充,对于紧固器7开口处的膜层15端口部位,采用人工打磨,先对混凝土基体16进行清理打磨,并用环氧或聚氨酯沥青胶粘剂17等进行粘结。
44.对所有的拼缝部位的膜层15通过不带可粘接面的柔性膜层条18采用热风进行焊接覆盖处理。
45.本发明提供了一种槽体结构的施工方法,施工方法使用模板组结构一体成型混凝土槽体结构。具体包括以下步骤:
46.步骤1:首先固定柱4采用膨胀螺栓14根据设计要求固定在确定的地面位置,确保内外立柱(即内模板组1和外模板组2上的固定柱4)之间的间距满足浇筑后混凝土厚度要求。
47.步骤2:按照顺序将内模板组1和外模板组2已经对应的转角处的转角模板12和紧固器7安装就位,并连接固定。
48.步骤3:根据内模板组1壁面的长度,裁切长度大于周长的膜层15备用,膜层15至少单侧具备被混凝土凝固粘结的性能,比如纬固防腐资源(上海)有限公司的winff柔性膜层。
49.步骤4:将膜层15放入内模板组1同钢筋束之间的浇筑空间(即内模板组1和外模板组2之间),将可粘结面背向内模板组1。膜层15的下沿放置在限位板3上。
50.步骤5:将膜层15的两端从紧固器7的开口处引出,并施适度拉力使膜层15紧贴内模板组1的模板,并用紧固器7夹紧固定。
51.步骤6:浇筑混凝土,并按照要求向上搭设上一层模板组结构,重复上述步骤1-5的模板组结构和膜层15的安装,并进行浇筑。
52.步骤7:所有的施工完成后,混凝土基体16上留出的缝隙采用同膜层15材质相同或相近的材料进行填充,对于紧固器7开口处的膜层15端口部位,采用人工打磨,先对混凝土基体16进行清理打磨,并用环氧或聚氨酯沥青胶粘剂17等进行粘结。
53.步骤8:完成上述两个部位的热熔焊填缝和粘结后,对所有的拼缝部位再采用不带可粘接面的柔性膜层条18采用热风进行焊接覆盖处理。最后形成完整的塑胶膜层防腐内衬混凝土槽体结构。