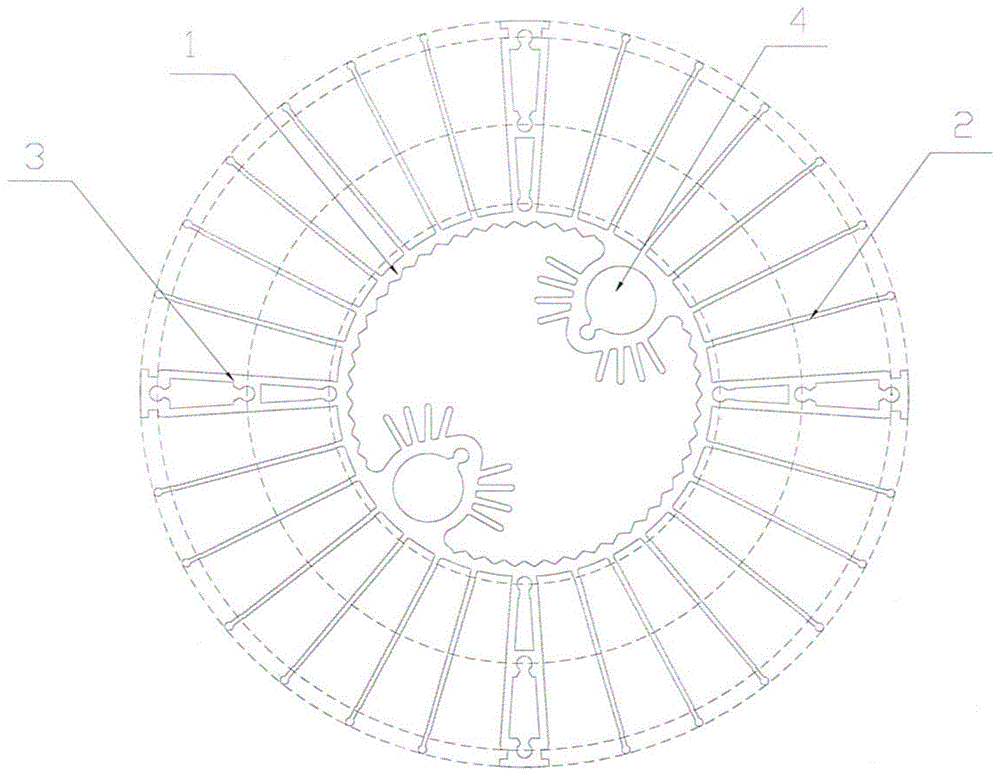
本发明属于led模组散热
技术领域:
,具体而言,涉及散热结构、用于led灯的散热器及其加工方法。
背景技术:
:目前,led光源广泛应用于新型节能光源场合,由于cob结构led光源与分立式led光源相比,具有光效高和散热结构简单等优点被广泛使用,但cob结构光源的发光效率和寿命与光源的温度严重相关,温度越高,发光效率越低,寿命也越低。led灯具的重点设计为散热设计,设法降低led光源的温度。大功率led发热量大,常规尺寸液体单相对流冷却、强制气冷、强迫对流沸腾冷却等各种传统冷却技术已无法满足高强度的散热要求,需要开发新型的散热器结构。目前用来制造散热器的工艺主要有:挤压成型、铸造、锻造、机械加工等,根据不同需要,散热器可以采用不同的成型方式,目前市场上的散热器:用以上几种工艺制造的都有。铝合金因质轻美观、良好的导热性和易加工成复杂的形状,被广泛地用于散热器材上。铝合金散热器材主要有三种类型:扁宽形,梳子形或鱼刺形;圆形或椭圆圆形外面散热片呈放射状;树枝形。它们的共同特点是:散热片之间距离短,相邻两散热片之间形成一个槽形,其深宽比很大;壁厚差大,一般散热片薄,而其根部的底板厚度大。因此给散热型材的模具设计、制造和生产带来很大的难度。散热器型材有一部分尺寸较小、形状对称的产品比较容易生产,大部分散热器型材扁宽形,外形尺寸较大,有的不对称,散热片之间的槽形深宽比很大,其生产难度较大。需要从铸锭、模具、挤压工艺几方面配合,才能顺利生产出散热器型材。技术实现要素:本发明所要解决的技术问题是针对上述现有技术提供一种led灯散热器及其加工方法,在确保散热效果的同时提高产品合格率,从而延长led灯的使用寿命。本发明解决上述问题所采用的技术方案为:一种led灯散热器,包括圆环形基座,在所述圆环形基座的外围设置有若干散热鳍片,所述散热鳍片呈放射状均匀间隔布置,在所述圆环形基座的外围等分设置有胶条安装座,所述胶条安装座沿径向设置,长度与散热鳍片一致,在胶条安装座上开设有两个型腔用于设置胶条,所述圆环形基座的内表面设置成锯齿状,以提高散热面积,在内表面上设置有一对电热管安装座,两个电热管安装座沿同一直径相对布置,所述电热管安装座上形成有安装电热管的型腔,同时在电热管安装座的外表面两侧对称设置有散热小鳍片。优选地,所述散热鳍片呈锥形结构,锥度为0.25°,由圆环形基座处向外逐渐变窄,底部宽度为1.4mm,头部宽度为1mm,长度为92mm,两侧设置成锯齿状。优选地,所述散热鳍片的端部为一球状体,球状体直径为2mm。优选地,所述胶条安装座呈锥形结构,锥度为7.5°,由圆环形基座处向外逐渐变宽,两侧设置成锯齿状。本发明涉及一种led灯散热器的制备方法,所述方法包括产前准备、铸锭加热、挤压、拉伸矫直、定尺锯切取样、人工时效、验收与移交步骤,其中:产前准备1)铸锭选择铸锭的直径、长度及其允许的偏差在合理范围内;2)挤压模具的准备按照产品要求设计相应的挤压模具,使模具的硬度保证在hrc48~52的前提下,具有足够的韧性;完成挤压模具的制备后,在挤压前对挤压筒及模具进行加热,其中平模的模温为450℃~470℃,保温时间≥2小时,组合模的模温为470℃~490℃,保温时间≥3小时,模垫的垫温为450℃~470℃,保温时间≥1小时,挤压筒采用加温100℃保温1小时的梯温形式,保证总加热时间≥8小时;模具在炉内的时间不得超过12小时;铸锭的加热铸锭加热温度为460~480℃,保温2小时,若停止挤压超过30分钟,应将炉温降低不少于50℃;挤压空车试运行正常后,检查挤压杆、挤压筒、模具三者是否同心,对风冷淬火的制品,要在制品进入工作台前将风机启动,风冷后的制品最佳淬火温度为515~525℃,冷却速度>80℃/分钟,风冷后制品温度<200℃,沿制品全长温度差≯20℃,挤压速度:实心10—25米/分,半空心、空心10—40米/分;开始挤压前和换模具后,先按规定的上限温度挤压,挤压3~5支棒后再转入正常生产;挤压筒闭锁压力100—150㎏/㎝2,油温≤50℃,闷车时间不能超过10秒。铸锭均匀化退火不仅可以使组织和性能均匀,而且可以提高挤压性能和降低挤压力,所以要求铸锭必须均匀化退火。至于变形程度的影响,由于散热器型材的断面积一般都比较大,挤压系数一般在40以内,因此其影响较小。模具准备包括模具设计和模具热处理两步:一、模具设计模具采用h13电渣重溶钢,在设计时对于流速快的部位给予阻碍,流速慢的部位给予加快,加快金属流速的方法:1)减薄工作带,将需要加快部位的工作带用砂轮磨掉一定厚度,缩短工作带长度,加快金属流动;2)扩大型材内孔部位对应的金属分流孔面积,增加金属供给量;3)通过减小模桥入口角度从而减小了金属进入分流孔后的摩擦阻力,加快了金属进入焊合室的供给速度;阻碍金属流动的办法:1)做阻碍角,在金属流速较快的型材模孔入口侧做一个小斜面,以增加金属流动阻力,增大了摩擦面积,使金属流动时产生附加弯曲变形,延长了流动路程,阻碍角一般取3°-12°;2)通过工作带补焊,增加工作带长度从而达到增大金属流动的阻力;3)通过增大入口角度,增大了金属进入分流孔后的摩擦阻力,延缓了金属进入焊合室的供给速度;2)模具热处理因为散热器型材的模具都是许多细长的齿,要承受很大的挤压力,每个齿都要有很高的强度和韧性,如果彼此之间的性能有很大的差异,就容易使强度或韧性差的那些齿产生断裂。因此模具钢材的质量必须可靠,最好使用质量可靠的厂家生产的h13钢材,或选用优质的进口钢材。模具的热处理十分重要,要用真空加热淬火,最好采用高压纯氮淬火,可以保证淬火后模具的各部分性能均匀。但是采用纯氮快速冷却,导致模具钢内部应力过高,因此在淬火后要采取三次回火,使模具的硬度保证在hrc48~52的前提下,具有足够的韧性。这是防止模具断齿的重要条件。采用高压纯氮淬火,将钢板加热至880±10℃,保温时间2.6-3.0min/mm,适当延长在炉保温时间,钢板出炉后液氮浇淋冷却,淬火速率控制在0.1~0.8℃/s;淬火后及时入炉回火,采取三次回火,三次回火温度分别为520-640℃,保温3.0-3.5min/mm;410-520℃,保温2.0-2.5min/mm;310-410℃,保温2.0min/mm。与现有技术相比,本发明的优点在于:本发明为一种圆形或椭圆圆形外面散热片呈放射状的散热器结构,通过将圆环形基座被表面,各个散热鳍片表面设置成齿形结构来提高散热面积,同时各个散热鳍片的尺寸间隔合理布置,使得散热过程有足够空间形成空气对流,确保散热效率。本发明还提供了此种散热器的制备方法,通过合理的工艺步骤和工艺参数来控制,使得此种复杂散热器的制备成功率提高,而在制备过程中对于模具处理,在设计上对于流速快的部位给予阻碍,流速慢的部位给予加快,加快金属流速的方法:1)减薄工作带,将需要加快部位的工作带用砂轮磨掉一定厚度,缩短工作带长度,加快金属流动;2)扩大型材内孔部位对应的金属分流孔面积,增加金属供给量;3)通过减小模桥入口角度从而减小了金属进入分流孔后的摩擦阻力,加快了金属进入焊合室的供给速度;阻碍金属流动的办法:1)做阻碍角,在金属流速较快的型材模孔入口侧做一个小斜面,以增加金属流动阻力,增大了摩擦面积,使金属流动时产生附加弯曲变形,延长了流动路程,阻碍角一般取3°-12°;2)通过工作带补焊,增加工作带长度从而达到增大金属流动的阻力;3)通过增大入口角度,增大了金属进入分流孔后的摩擦阻力,延缓了金属进入焊合室的供给速度;从而提高散热器的成品率。而对于模具热处理部分因为散热器型材的模具都是许多细长的齿,要承受很大的挤压力,每个齿都要有很高的强度和韧性,如果彼此之间的性能有很大的差异,就容易使强度或韧性差的那些齿产生断裂。因此模具钢材的质量必须可靠,最好使用质量可靠的厂家生产的h13钢材,或选用优质的进口钢材。模具的热处理十分重要,要用真空加热淬火,最好采用高压纯氮淬火,可以保证淬火后模具的各部分性能均匀。但是采用纯氮快速冷却,导致模具钢内部应力过高,因此在淬火后要采取三次回火,使模具的硬度保证在hrc48~52的前提下,具有足够的韧性。附图说明图1是本发明中led灯散热器的结构示意图。具体实施方式以下结合附图实施例对本发明作进一步详细描述。参见图1所示,本实施例中的一种led灯散热器,整体呈圆形结构,包括圆环形基座1,在所述圆环形基座1的外围设置有若干散热鳍片2,所述散热鳍片2呈放射状均匀间隔布置,共有24个散热鳍片2,在所述圆环形基座1的外围等分设置有胶条安装座3,相邻两个胶条安装座3之间设置有6个散热鳍片2,所述胶条安装座3沿径向设置,长度与散热鳍片2一致,在胶条安装座3上开设有两个型腔用于设置胶条,一方面可以降低散热器重量,节省材料,同时可以起到防水作用。所述散热鳍片2呈锥形结构,锥度为0.25°,由圆环形基座1处向外逐渐变窄,底部宽度为1.4mm,头部宽度为1mm,长度为92mm,两侧设置成锯齿状,以提高散热鳍片的散热面积,端部为一球状体,球状体直径为2mm,一方面提高散热面积,另一方面球状体可以防止散热器刮伤led组件中的其他元器件,所述胶条安装座3呈锥形结构,锥度为7.5°,由圆环形基座1处向外逐渐变宽,两侧也设置成锯齿状,用以提高散热面积。所述圆环形基座1的内表面设置成锯齿状,以提高散热面积,在内表面上设置有一对电热管安装座4,两个电热管安装座4沿同一直径相对布置,所述电热管安装座4上形成有安装电热管的型腔,同时在电热管安装座4的外表面两侧对称设置有散热小鳍片5,散热小鳍片5宽度为1.5mm,长度为9mm,电热管产生的热量先由散热小鳍片5发散出去,再通过圆环形基座1和24个散热鳍片2实现散热。本实施例公开了一种led灯散热器的制备方法,主要包括产前准备、铸锭加热、挤压、拉伸矫直、定尺锯切取样、人工时效、验收与移交。具体步骤如下:步骤一、产前准备1)铸锭选择铸锭的直径、长度及其允许的偏差按表1执行。表1单位:㎜铸锭使用时,表面不得有压入物、灰尘、油污等脏物,否则要清理干净方可投入使用。2)挤压模具的准备挤压模具的设计,按照产品要求设计相应的挤压模具,使模具的硬度保证在hrc48~52的前提下,具有足够的韧性。完成挤压模具的制备后,在挤压前对挤压筒及模具的加热制度按表2执行。表2模具在炉内的时间不得超过12小时挤压工具允许偏差按表3执行。表3单位:mm每班要用清缸垫清理挤压筒两次。步骤二、铸锭的加热1)铸锭装炉前,按机台作业指令单的要求,认真检查合金牌号、规格、熔次等是否与指令单相符,并填写好原始记录。2)铸锭加热温度为460~480℃,保温2小时。3)铸锭加热达不到规定温度不准挤压,若停止挤压超过30分钟,应将炉温降低不少于50℃,防止铸锭温度过热或过烧。4)严格控制炉温,当铸锭的加热温度高于规定的温度,应降至规定温度后再投入挤压,必须执行首料测温的规定,每生产30支棒必须测量铸锭的温度,确保挤压工艺。5)特殊情况下,需调整炉子温度或铸锭加热温度时,必须经车间主任同意并报生产部,办理有关手续后方可调整。步骤三、挤压1)生产前首先熟悉机台作业指令单的内容:型号、厚度、定尺、数量、工艺要求等。2)空车试运行正常后,检查挤压杆、挤压筒、模具三者是否同心。3)对风冷淬火的制品,要在制品进入工作台前将风机启动,风冷后的制品温度、允许制品全长温差、挤压速度等按表4执行。表44)为保证挤压产品质量,防止闷车,开始挤压前和换模具后,先按规定的上限温度挤压,挤压3~5支棒后再转入正常生产。5)挤压力1000t,800t,600t机分别不大于220、230、2230kg/㎝2,挤压筒闭锁压力100—150㎏/㎝2,油温≤50℃,闷车时间不能超过10秒。6)为防止夹渣,铸锭从加热炉夹出后,用布条擦净灰尘,方可投入挤压。7)每种规格的第一、二支制品,机手和质检员,按图纸共同对制品的表面质量、尺寸、平面间隙等进行全面检查,均符合内控标准方可继续挤压,换模后要进行同样检查。8)生产过程中,每生产10支棒,须重新对制品的表面质量检查一次,由工序自检。9)使用的手套要清洁,出料台、冷床要保持完整清洁,防止制品表面沾污、划伤。10)挤压残料(压余)的长度按表5执行。表5单位:mm11)两次挤压间的焊缝,不允许留在成品型材中(压线,盖板及非氧化的厚角除外),所以中断应在两次挤压的连接焊缝前后不大于20㎝处中断。12)严禁无挤压垫和反垫挤压,防止事故发生。13)特殊模具要使用专用模垫。步骤三、拉伸矫直1)拉伸前后要详细检查制品的尺寸,根据检查结果来确定拉伸率,拉伸温度、变形率、夹头等要求按表6执行。表6矫直温度℃变形率%夹头㎜其它要求≤500.5~2.5≯120无扭拧、弯曲、随挤压连续生产2)型材必须由步进式输送机送到拉伸矫直机旁,不允许人为拖拉,按先后顺序矫直。3)严禁一次拉伸多支型材。4)对一些横截面较大,特殊型材要用专用夹持垫,以防端头变形严重。步骤四、定尺锯切取样1)应根据机台作业指令单的定尺要求,确定好定尺限位板,锯切允许偏差按表7进行,经常检查限位板位置,确保其精确度。表7定尺长度㎜倍尺长度㎜端头允许切斜度其它要求l+10xl+20≯2°在作业指令单上注明2)锯切第一支制品后,要复检是否符合规定,达到要求后方可锯切。3)锯切制品时应整齐排列,顶紧限位板,严禁交叉,重叠锯切(小槽、压线除外)。4)锯切平台、储料台上要保持清洁,防止制品划伤和污染。5)锯切时应注意对锯切片的润滑,制品锯切口应垂直,无毛刺和严重变形,否则要更换锯片。每次锯切不得超过5支料(小料除外)。6)每次锯切不得超过8支料(小料除外)。7)锯切下的料头长度不小于30㎝,料尾不短于40㎝。8)锯切后的头、尾,不合格品要捆扎过磅,记入原始记录,然后返熔铸车间。9)切完的制品经工序检查后,抬入料筐,摆放整齐,每层之间用高温垫条间距为1000~1500㎜隔开,对断面大的制品一般用垫条4-6根,断面小的易弯曲制品可适当增加垫条数量。10)长短料同装一筐时,长料放下面;型号不同的制品同装一筐时,截面大、重量大的放下面;不同合金,一般不准放在同一筐内。11)装料高度低于料框高度10mm,料筐架要用耐高温条附垫,防止划伤。12)每筐料均需要修整锯口和刮毛刺。13)每筐料都要有工艺流程卡,挤压质检员签字后方可安排时效。步骤五、人工时效1)待时效的制品,每筐必须有经质检员确认签字的工艺流程卡方可装炉时效。2)设置专人操作时效炉,调整和控制温度,开炉期间不得离开岗位,每隔30分钟记录一次加热室温度。3)操作人员要把人工时效制品的型号、合金、筐号、规格、装炉量、入炉时间、开始升温时间、开始保温时间、热处理过程中的各次测温结果、保温终了时间、出炉时间、硬度检验值等,如实记录在《时效工艺记录》上。4)人工时效的保温时间以金属的实际温度全部达到规定的温度时,开始算起,人工时效制度按表8规定执行。表8各区定温℃制品到温后的保温时间分冷却方式200±5120出炉强制风冷5)锯切后装筐待时效的制品,停放时间不得超过2天。步骤六、验收与移交1)制品人工时效后,冷却到40℃以下,用硬度钳测量硬度。2)测量硬度,每筐制品分上、中、下最少抽查6根以上,刻度值应≥10,如有不合格品则加倍抽查,如再有不合格品则100%检查,合格品(随同工艺流程卡)吊至合格坯料堆放区,并盖好雨布,以防灰尘等腐蚀型材,等待氧化处理,不合格品则上报车间、生产部、质技部,不合格品放待处理区待分析原因,作最后判定。3)坯料区最多允许放五层料筐。除上述实施例外,本发明还包括有其他实施方式,凡采用等同变换或者等效替换方式形成的技术方案,均应落入本发明权利要求的保护范围之内。当前第1页12