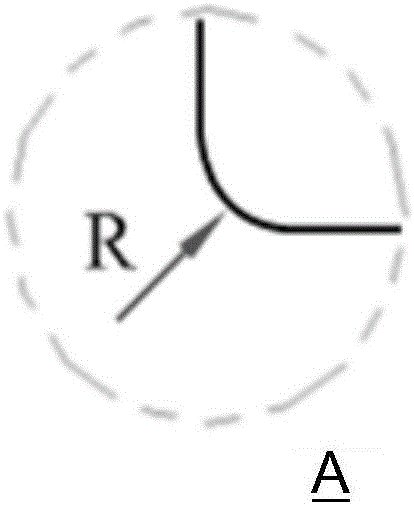
本发明涉及金属塑性加工与模具技术,更具体地说,涉及一种快速获取汽车铝板冲裁工艺参数的优化装置及其优化方法。
背景技术:
:随着汽车工业对燃油效率和尾气排放要求的不断提高,铝合金板已经代替钢板成为汽车车身覆盖件的优选材料。然而,铝合金板在落料、修边和冲孔等冲裁过程中非常容易形成毛刺并产生大量的铝屑。其中,毛刺会断裂形成碎屑,并与铝屑一同附着在工件以及模具表面,从而在最终成形的冲压件表面形成划伤、麻点、凹坑等缺陷,严重影响工件的外观质量和生产效率。因此,如何有效地抑制冲裁过程毛刺和铝屑的产生,已成为现今汽车铝板行业了亟待解决的问题。目前,解决上述的问题的主要方法有两种。其中,方法一就是改变现有修边冲裁工艺以及模具的结构,通过多次冲裁来有效提高板料的冲裁断面质量。然而,该方法会使得模具结构以及修边工序变得十分复杂,且成本高,不易实施。方法二则是通过获取最优的冲裁工艺参数来抑制毛刺和铝屑的产生。经过大量研究表明,冲裁角度、冲裁间隙以及冲裁模具圆角半径等冲裁工艺参数的选取对铝合金板修边碎屑和毛刺的产生有极大的影响,冲裁断面中光亮带大、撕裂带和毛刺小的冲裁工艺有利于减少或消除铝屑的产生。与方法一相比,方法二尽管前期需要进行大量的冲裁试验确定最优的工艺参数,但模具结构不需要有较大改动,加工成本低,可实施性强。如申请号为201010215682.x的发明专利“金属板料无毛刺的冲裁方法及模具”提出了一种新型的金属板料无毛刺冲裁方法。该发明由以下两个步骤组成:首先对金属板料背面进行冷挤压,在冲裁切口位置上形成辅助压线,产生凹形压痕;之后,再使用冲裁模具进行冲裁,冲裁间隙为板料厚度t的0.04~0.06倍。本发明对高精度的孔或产品外形的影响较小,对模具刃口锋利度的要求低。如申请号为201310005405.x的发明专利“无毛刺加工模具”,提供了无毛刺加工模具与普通模具的区别在于,模具第一次冲压的冲头安装在下模板,废料是从下往上顶起的,再由二次冲压将废料从上往下顶出,通过对产品进行二次冲压,从而使产品反面轮廓线表面无毛刺。如申请号为201210155222.1的发明专利,提供了一种无毛刺冲裁方法和冲裁系统,其冲裁工序分两步,首先在板料冲裁位置预成形一个凹槽,然后再对该位置进行冲裁,从而将工件和废料分离。采用本发明制得的工件在与凸模运行方向垂直的大平面的周边轮廓不存在冲压毛刺,且工件质量较高。综合上述现有专利分析可知,现有技术主要是通过在冲裁位置预成形出凹槽来提高金属板料的冲裁断口质量。而通过快速优化冲裁角度、冲裁间隙以及冲裁圆角半径等工艺参数来抑制铝屑和毛刺产生的相关方法还未见。技术实现要素:针对现有技术中存在的上述缺陷,本发明的目的是提供一种快速获取汽车铝板冲裁工艺参数的优化装置及其优化方法,能够在一套装置上实现汽车铝板在不同工艺条件下的冲裁试验,并快速确定各工艺参数对汽车铝板冲裁断面的影响规律,从而为不同规格不同牌号的铝板确定出最佳的冲裁工艺参数。为实现上述目的,本发明采用如下技术方案:一方面,一种快速获取汽车铝板冲裁工艺参数的优化装置,包括上模组件、下模组件和导向组件,上模组件与下模组件为相对设置;所述上模组件包括:上模固定板、垫块、上模板、凸模固定块和上模刀,上模板的上表面通过垫块与上模固定板相连,凸模固定块连于上模板的下表面,上模刀连于凸模固定块上;所述下模组件包括:下模板,设于下模板上的凹模固定块、下模刀和隔料板,凹模固定块与下模刀相固定连接,下模刀的上端面上还设有压料板,且下模刀上端面与压料板下端面与水平面成同一角度;所述导向组件包括:导柱和导套,导套设于上模板的下表面,导柱设于下模板上,且导柱和导套的位置相适配;所述的上模刀具有两组,分别设于凸模固定块的两侧,所述下模刀也具有两组,与上模刀相对应,所述隔料板设于两组下模刀之间。所述的上模刀上均设有定位销、锁紧螺栓和顶出螺栓。所述的下模刀上均设有定位块、料板定位销。所述的压料板均设有与料板定位销相对应的插入孔,及螺栓孔。另一方面,一种快速获取汽车铝板冲裁工艺参数的优化方法,包括以下步骤:s1.制定优化策略:确定汽车铝板冲裁优化过程中冲裁间隙、冲裁角度以及刀具圆角半径工艺参数的水平数量及水平数量对应的数值;s2.试样准备:通过切板机将试样制成条状板料;s3.上模组件、下模组件进行安装;s4.下模刀的安装:将不同倾斜角度的下模刀分别安装到相应的各个区域;s5.上模刀的安装:将不同刃口圆角半径的上模刀分别安装到相应的各个区域;s6.调节各个区域冲裁间隙到初始数值;s7.打开模具;s8.装夹板料:通过压料板和螺栓将铝板板料固定在下模刀上;s9.进行冲裁:压力机下行,完成冲裁过程,每一组工艺参数组合需重复数次试验;s10.观察铝屑产生情况以及断面中光亮带比例;s11.在凸模固定块与上模刀之间塞入垫片,从而调节各区域的冲裁间隙到下一个间隙水平数值,并重复s7~s10的操作,直至制定的优化策略中冲裁间隙的各水平均有试验结果;s12.顺时针调换上模刀位置,并重复s6~s11操作,上模刀的调换次数与所需的水平数相同,之后每调换一次都需重复s6~s11操作,从而使所制定的优化策略中所有工艺参数组合均有试验结果;s13.确定最优参数:选取最佳断面,确定所对应的冲裁工艺参数组合,若有多套工艺参数组合都达到了要求的断面质量,则比较光亮带面积,面积最大的对应参数组合为最优。所述的步骤s1中,冲裁角度的可选范围为0°~20°,冲裁间隙的可选范围为5%t~15%t,刀具圆角半径的可选范围为0.025mm~0.5mm,每个工艺参数在其可选范围内均匀分散地选取3~4个水平。所述的步骤s4中,倾斜角度与所制定优化策略中的冲裁角度相对应。所述的步骤s5中,刃口圆角半径与所制定优化策略中的冲裁角度相对应。所述的步骤s6中,若所制定的优化策略中冲裁间隙的取值有三个水平,则间隙的水平初始数值为三个水平中最小的间隙数值。所述的步骤s9中,每一组工艺参数组合需重复三至五次试验。在上述的技术方案中,本发明所提供的一种快速获取汽车铝板冲裁工艺参数的优化装置及其优化方法,还具有以下几点有益效果:1.本发明对不同牌号以及厚度的汽车铝板均具有很好的适用性;2.本发明的冲裁方式与实际修边冲裁过程保持一致,因此其试验结果对实际生产有着很好的借鉴意义;3.本发明可实现金属板料在不同冲裁工艺参数条件下的冲裁试验,从而可以研究冲裁角度、冲裁间隙、刃口圆角半径等工艺参数对于冲裁断面的影响;4.本发明结构简单,便于操作,一次冲裁可以完成四组工艺参数组合下的冲裁试验,大大缩短了工艺优化的时间;5.本发明可以在较短时间内准确获取汽车铝板冲裁的最佳工艺参数组合。附图说明图1是本发明优化装置冲裁汽车铝板时的示意图;图2是本发明优化装置的结构示意图;图3是本发明上模组件的结构示意图;图4是本发明下模组件的结构示意图;图5a是本发明上模刀的正面图;图5b是图5a的俯视图;图5c是图5b的左视图;图5d是图5c中a位置的放大图;图6a是本发明下模刀的正面图;图6b是图6a的俯视图;图6c是图6a的右视图;图7a是本发明压料板的正面图;图7b是图7a的俯视图;图7c是图7a的左视图;图8是本发明优化方法中冲裁间隙调节的示意图;图9是本发明优化方法的流程示意图。具体实施方式下面结合附图和实施例进一步说明本发明的技术方案。在为某车型发罩进行修边工序时,由于在此过程中,修边刀往往是同时触料,因此沿着修边轮廓线,材料一般不发生变形,即板料各位置均发生着垂直于轮廓线的平面应变。由于零件各位置的曲率和倾斜角度不同,因此不同修边位置处的冲裁角度、冲裁间隙以及刀具圆角半径等工艺参数均会有所差异,这也导致了板料各位置的修边断面质量存在着很大的不同,板料的修边过程可以分解为多个截面位置的二维冲裁过程。请结合图1所示,图中冲裁角度θ、冲裁间隙c以及冲裁刀具圆角半径r等参数均可以根据实际情况进行调节。当获得修边过程某一位置的修边工艺参数后,便可以通过类似的装置模拟出该位置的修边质量。为了保证汽车铝板冲压零件的质量以及生产效率,铝板冲裁断面需要满足三个要求,即:无铝屑、无毛刺、大的光亮带比例,这三项要求的优先级为:无铝屑>无毛刺>大的光亮带比例。其中无铝屑最为重要,铝板冲裁过程一旦出现铝屑,则可判定该工艺不满足要求,其次是保证断口近无毛刺,最后在以上两个要求都满足以后,尽可能地提高光亮带比例。具体的评价标准如下表1所示,冲裁断面质量共分为7个等级,lv4~lv7的断口均不满足汽车铝板冲压生产的要求。表1铝板冲裁断面质量评价标准断面质量铝屑情况毛刺情况光亮带比例lv1无无50%以上lv2无无50%以下lv3无少量-lv4无多-lv5少量--lv6较多铝屑--lv7长条、大块碎屑--注:表中“-”表示不考虑该项目如上所述,在铝板修边冲孔过程中,有多个因素会影响其断口质量,而其中冲裁角度、冲裁间隙和冲裁刀具圆角半径是与冲裁断面最为相关的三个工艺参数。因此,工艺优化过程就是通过试验来确定以上三个工艺参数的最佳取值。请结合图2至图4所示,本发明所提供的一种快速获取汽车铝板冲裁工艺参数的优化装置,包括上模组件、下模组件和导向组件,上模组件与下模组件为相对设置,上模组件的上模固定板1通过螺栓与压力机固定连接,下模组件的下模板9通过螺栓与压力机固定连接。较佳的,所述上模组件包括:上模固定板1、垫块2、上模板3、凸模固定块4和上模刀5,上模板3的上表面通过垫块2与上模固定板1固定连接,凸模固定块4的上表面与上模板3的下表面固定连接,凸模固定块4的下表面上具有凸块,上模刀5具有四把,两把上模刀5为一组分别固定连接于凸模固定块4上凸块的两侧边,使得四把上模刀5前后左右对称布置,通过在上模刀5与凸模固定块4之间塞入不同规格的垫片就能够调节冲裁间隙。较佳的,所述下模组件包括:下模板9,设于下模板9上的凹模固定块7、下模刀11和隔料板8,凹模固定块7与下模刀11相固定连接,所述下模刀11也具有四把,两把下模刀11为一组与上模刀5相对应设置,下模刀11的上端面上均还连接了压料板6,且下模刀11上端面与压料板6下端面与水平面成同一角度,所述隔料板8设于两组下模刀11之间。较佳的,所述导向组件包括:导柱10和导套12,导套12具有四个,分别设于上模板3下表面的四个角上,导柱10也具有四个,分别设于下模板9的四个角上,且导柱10和导套12的位置相适配。在冲裁过程中上模刀5、下模刀11和压料板6是与板料直接接触的,所以:请结合图5a至图5d所示,所述的上模刀5主要通过位于对角线处的定位销501与凸模固定块4进行匹配定位,并通过位于中心线两端的锁紧螺栓502固定在凸模固定块4上,由于定位销501与凸模固定块4的定位凹槽是过盈配合,因此需要通过顺时针旋转中心位置的顶出螺栓503将上模刀5顶出。请结合图6a至图6c所示,所述的下模刀11主要通过位于下端的八边形定位块111与下模板9匹配连接,并通过四个料板定位销112对条形板料进行定位,压料板6可以通过位于中心线左右两端的锁紧螺栓113将板料固定。请结合图7a至图7c所示,所述的压料板6均设有与料板定位销112相对应的插入孔601,及螺栓孔602。冲裁角度、冲裁间隙和冲裁刀具圆角半径等工艺参数的调节方法如下所述:(1)冲裁角度的调节按照工艺优化的要求,加工所需倾斜角度的下模刀以及压料板,并通过更换不同倾斜角度的下模刀以及相匹配的压料板来改变本优化装置各区域的冲裁角度。(2)刀具圆角半径的调节按照工艺优化的要求,加工具有不同刃口圆角半径的上模刀,并更换不同规格的上模刀来改变本优化装置各区域的刀具圆角半径。(3)冲裁间隙的调节本发明优化装置的冲裁间隙是通过在上模刀与凸模固定块之间塞入不同规格的垫片来实现的。具体操作时,上模组件下行至下模刀刃口以下某个位置(如图8所示),将与设定冲裁间隙一致规格的塞规放在上、下模刀之间(如图8中b箭头所示方向),上模刀在水平方向先通过对角线上的两个定位销进行定位,然后松掉上模刀上的锁紧螺栓,通过在下模刀与凸模安装块之间(如图8中c箭头所示方向)塞入不同规格的垫片使上模刀向外侧移动,调节上、下模刀之间的距离,使上模刀与塞规贴紧,达到所需设定的冲裁间隙,最后锁紧上模刀上的固定螺栓。请结合图9所示,本发明所提供的一种快速获取汽车铝板冲裁工艺参数的优化方法,根据积累的铝板冲裁数据,可以确定出冲裁角度、冲裁间隙以及刀具圆角半径这三个参数的大致取值范围。其中,冲裁角度的可选范围为为0°~20°,冲裁间隙的可选范围为5%t~15%t,t为板料厚度,刀具圆角半径的可选范围为0.025mm~0.5mm。此外,针对每个参数,需要在其可选范围内均匀分散地选取3~4个水平。与其他优化问题不同,以上三个因素对于铝板冲裁质量的影响并无明显规律,且这三个因素间的相互影响也较为显著。因此,为了能够得到最优的冲裁参数组合,需要采取多因素多水平下的全面试验,而全面试验的试验量大致需要30~60次的冲裁试验,但本发明的优化方法可以在一次冲裁过程中实现铝板在四种冲裁工艺参数组合下的冲裁,有效地减少冲裁次数,从而节约优化时间。本实施例优化流程具体包括以下步骤:s1.制定优化策略:其中,冲裁间隙取0.06mm、0.12mm和0.18mm三个水平;冲裁角度取0°、10°和20°三个水平;刀具圆角半径取0.025mm、0.125mm和0.25mm三个水平;s2.试样准备:采用西南铝生产的6016汽车铝板,厚度为1.2mm,通过切板机将板料切成尺寸为300mm×70mm的条状板料;s3.上模组件、下模组件进行安装,再将上模组件、下模组件安装到压力机上;s4.下模刀的安装:将0°、10°和20°的下模刀分别安装到相应的各个区域;s5.上模刀的安装:将不同刃口圆角半径分别为0.025mm、0.125mm和0.25mm的上模刀分别安装到相应的各个区域;s6.调节各个区域冲裁间隙到初始数值,即0.06mm;s7.升起压力机横梁,打开模具;s8.装夹板料:通过压料板和螺栓将铝板板料固定在下模刀上;s9.进行冲裁:压力机下行,完成冲裁过程,每一组工艺参数组合需重复5次试验;s10.观察铝屑产生情况以及断面中光亮带比例,按照上述表1对冲裁质量进行评级;s11.在凸模固定块与上模刀之间塞入垫片,从而调节各区域的冲裁间隙分别到0.12mm和0.18mm,并重复s7~s10的操作;s12.顺时针调换上模刀位置,共调换两次,每次调换位置后均需要重复s6~s11操作,从而使27种工艺参数组合下均有冲裁结果;s13.确定最优工艺参数组合:列出每种工艺参数组合的断面质量情况,如下表2所示,比较两组断口质量为lv1的断面光亮带所占比例,其中参数组合r0.025a10c0.12(即上模刃口圆角半径为0.025mm,冲裁间隙为0.12mm,冲裁角度为10°)的光亮带占比较大,因此该参数组合为最佳冲裁工艺参数组合。表2冲裁断面质量情况工艺参数c0.06c0.12c0.18r0.025、a0lv6lv7lv5r0.025、a10lv6lv1lv6r0.025、a20lv6lv5lv7r0.125、a0lv7lv5lv6r0.125、a10lv7lv7lv1r0.125、a20lv6lv6lv5r0.5、a0lv7lv5lv7r0.5、a10lv6lv7lv6r0.5、a20lv6lv7lv7注:r表示上模刃口圆角半径,c表示冲裁间隙,a表示冲裁角度综上所述,本发明的冲裁方式与实际修边冲裁保持一致,先将板料通过压料板固定,再通过上模刀与下模刀的剪切作用实现板料分离。此外,本发明将模具均匀分成了四个区域,每一个区域都能实现不同冲裁工艺下的加工,且冲裁角度、冲裁间隙以及刀具圆角等工艺参数都是可以调节的。因此,在一次冲裁过程中可以实现四种不同工艺参数组合下的冲裁,从而有效地减少了优化过程的时间。本
技术领域:
中的普通技术人员应当认识到,以上的实施例仅是用来说明本发明,而并非用作为对本发明的限定,只要在本发明的实质精神范围内,对以上所述实施例的变化、变型都将落在本发明的权利要求书范围内。当前第1页12