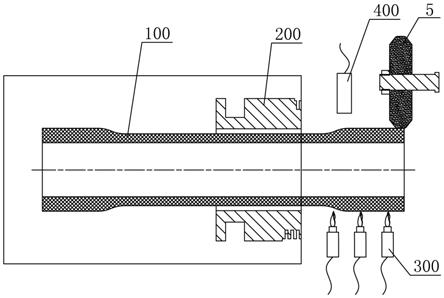
[0001]
本发明涉及氢能装备制造领域,尤其涉及一种高压氢瓶铝内胆无芯模旋压收口方法。
背景技术:[0002]
金属旋压是一种综合了挤压、锻造、弯曲、拉深、滚压和环轧的金属塑性成型加工工艺,具有无屑加工、节省原材料、成本低廉、产品质量高等优点,广泛应用于复杂曲面件高精度、轻量、高稳定性的机械加工场合。
[0003]
金属旋压技术通过利用无缝金属管制成各种回转体空心件,从根本上消除了与焊缝相关的不连续性、强度降低、脆裂和拉应力集中等问题,极大地提高了高压容器的安全性,因而广泛应用于车载高压储氢气瓶的铝内胆制造生产线中。
[0004]
在车载高压储氢气瓶的铝内胆制造生产线中,铝内胆通常由直径为350~380mm、壁厚为6~12mm的大直径薄壁铝合金管通过旋压减薄、旋压收口至两端形成直径为70~80mm的瓶嘴、以及封头结构。目前对铝合金管进行旋压收口的加工方式是利用芯模和旋压轮配合进行旋压收口的,但上述加工方式存在如下主要缺陷:
①
产品受制于芯模形状,因而生产线产品结构单一;此外随着芯模的不断磨损,同一批次旋压收口得到的瓶嘴加工精度存在差异、加工精度一致性差;
②
芯模的制造加工周期较长,且以非标定制为主,因而生产成本及使用成本较高;尤其对于用于旋压收口的进口设备,芯模更换更加困难;
③
铝内胆两端瓶嘴及封头在旋压收口成型过程中,受收口温度、收口方法等诸多因素的影响,成型后的瓶嘴内壁与封头连接处极易出现肉眼可见的裂纹,致使铝内胆报废。
技术实现要素:[0005]
本发明所需解决的技术问题是:提供一种无需采用芯模的高压氢瓶铝内胆无芯模旋压收口方法,采用该方法能减少成型后的瓶嘴内壁与封头连接处极易出现肉眼可见的裂纹的概率,提高铝内胆合格率。
[0006]
为解决上述问题,本发明采用的技术方案是:所述的一种高压氢瓶铝内胆无芯模旋压收口方法,将铝合金管端部旋压收口至瓶嘴及封头成型后,未旋压收口前的铝合金管端部的外半径与成型后的瓶嘴外半径之差为a;旋压收口方法包括如下步骤:(1)将铝合金管一端装夹于旋压收口设备的装夹装置中,对伸出装夹装置外的铝合金管端部的瓶嘴收口段和封头增厚段进行预热;预热温度为500
±
10℃,预热时间为8~10分钟;(2)预热完毕后,对瓶嘴收口段和封头增厚段进行第一组旋压收口作业;第一组旋压收口作业分为五道次进行旋压,第一道旋压为直线旋压,第二道至第五道旋压为渐进分段旋压:每道旋压的前段为直线旋压、后段为凸曲线旋压,最终得到圆锥状瓶嘴收口段和椭圆状封头增厚段;第一组旋压收口作业完毕后得到的圆锥状瓶嘴收口段的最小外半径与未旋压
收口前的铝合金管端部的外半径之差为b,b=(0.25~0.4)a;其中,每道旋压过程中的旋压轮的初始径向进给量h1均相同;每道旋压过程中、位于直线旋压段的旋压轮行走路线均为与铝合金管的轴线成夹角α的斜直线,第一道和第二道旋压过程中、位于直线旋压段的旋压轮行走路线的夹角α均为4
°
~4.5
°
,且第二道至第五道旋压过程中、位于直线旋压段的每个后道旋压的旋压轮行走路线的夹角均比前道旋压的旋压轮行走路线的夹角增加0
°
~0.5
°
;在第一组旋压收口作业中对瓶嘴收口段和封头增厚段持续进行加热,加热温度为500
±
10℃;(3)对瓶嘴收口段和封头增厚段进行第二组旋压收口作业;第二组旋压收口作业分为十二道次进行渐进分段旋压:每道旋压的前段为直线旋压、后段为凸曲线旋压,最终得到圆锥状瓶嘴收口段和椭圆状封头增厚段;第二组旋压收口作业完毕后得到的圆锥状瓶嘴收口段的最小外半径与第一组旋压收口作业完毕后得到的圆锥状瓶嘴收口段的最小外半径之差为c,c=(0.35~0.65)a;其中,每道旋压过程中的旋压轮的初始径向进给量h2均相同;每道旋压过程中、位于直线旋压段的旋压轮行走路线均为与铝合金管的轴线成夹角β的斜直线,第一道旋压过程中、位于直线旋压段的旋压轮行走路线的夹角β为4
°
~6
°
,且旋压过程中、位于直线旋压段的每个后道旋压的旋压轮行走路线的夹角均比前道旋压的旋压轮行走路线的夹角增加1
°
~1.5
°
;在第二组旋压收口作业中对瓶嘴收口段和封头增厚段持续进行加热,加热温度为500
±
10℃;(4)对瓶嘴收口段和封头增厚段进行第三组旋压收口作业;第三组旋压收口作业分为四道次进行渐进分段旋压:每道旋压的前段为直线旋压、后段为凸曲线旋压,最终得到圆柱状瓶嘴收口段和椭圆状封头增厚段;第三组旋压收口作业完毕后得到的圆柱状瓶嘴收口段的外半径与第二组旋压收口作业完毕后得到的圆锥状瓶嘴收口段的最大外半径之差为d,d=(0.1~0.2)a;其中,每道旋压过程中的旋压轮的初始径向进给量均为零;每道旋压过程中、位于直线旋压段的旋压轮行走路线均为与铝合金管的轴线成夹角γ的斜直线,第一道旋压过程中、位于直线旋压段的旋压轮行走路线的夹角γ为16
°
~18
°
,且旋压过程中、位于直线旋压段的每个后道旋压的旋压轮行走路线的夹角均比前道旋压的旋压轮行走路线的夹角减少4
°
~4.5
°
;在第三组旋压收口作业中对瓶嘴收口段和封头增厚段持续进行加热,加热温度为500
±
10℃;(5)对瓶嘴收口段和封头增厚段进行第四组旋压收口作业至瓶嘴及封头成型,第四组旋压收口作业为一道表面精修工序;在第四组旋压收口作业中对瓶嘴收口段和封头增厚段持续进行加热,加热温度为500
±
10 ℃;(6)将铝合金管从装夹装置中取下后旋转180
°
,将铝合金管上完成旋压收口端装夹于装夹装置中后重复步骤(1)至(5)。
[0007]
进一步地,前述的一种高压氢瓶铝内胆无芯模旋压收口方法,其中,步骤(2)、步骤(3)、步骤(4)中均采用材质为gcr15、硬度为hrc60
±
2、直径为300mm、厚度为60~80mm、圆角半径为16~20mm的旋压轮进行旋压收口作业。
[0008]
进一步地,前述的一种高压氢瓶铝内胆无芯模旋压收口方法,其中,步骤(5)中采用材质为gcr15、硬度为hrc60
±
2、直径为250mm、厚度为60~80mm、圆角半径为8~12mm的旋
压轮对瓶嘴收口段及封头增厚段进行表面精修工序。
[0009]
进一步地,前述的一种高压氢瓶铝内胆无芯模旋压收口方法,其中,步骤(2)、步骤(3)、步骤(4)、步骤(5)中,四组旋压收口作业过程中旋压收口设备的装夹装置的转速均为150~200r/min;旋压轮施加于铝合金管上的压力均为50~60kn,旋压轮转速均为550~750r/min,旋压轮轴向行进速度均为1mm/r。
[0010]
进一步地,前述的一种高压氢瓶铝内胆无芯模旋压收口方法,其中,旋压收口设备中的旋压轮带有冷却装置,所述的冷却装置的结构包括:带安装空腔的减温底座,在减温底座的前端面上开设有前后贯通的第一套管孔,在减温底座的后端面上开设有前后贯通的第二套管孔,套管穿插于减温底座的安装空腔中,且套管的前端固定搁置于第一套管孔中,套管的后端固定搁置于第二套管孔中;盘管套设于套管上,盘管的进液端和出液端分别穿过减温底座侧壁上对应通孔后伸出减温底座外;旋转轴通过轴承支撑设置于套管中,旋压轮固定于伸出套管前端外的旋转轴前端,带电机的电机支架固定于减温底座的后端面上,且电机的电机轴与旋转轴后端固定连接。
[0011]
进一步地,前述的一种高压氢瓶铝内胆无芯模旋压收口方法,其中,由金属管或塑料管制成的盘管套设于套管上,盘管的进液端和出液端位于同侧;在盘管的进液端和出液端上均设置有接头,所述的接头为卡套接头或宝塔接头中的一种。
[0012]
进一步地,前述的一种高压氢瓶铝内胆无芯模旋压收口方法,其中,在旋转轴与套管之间的间隙中填充有导热硅胶。
[0013]
进一步地,前述的一种高压氢瓶铝内胆无芯模旋压收口方法,其中,在伸出套管前端外的旋转轴上设置有轴肩,旋压轮从旋转轴前端套入后、通过若干第一螺栓固定于轴肩上,盖板通过若干第二螺栓固定于旋转轴前端上,且盖板紧贴于旋压轮前端、将各第一螺栓封盖住。
[0014]
进一步地,前述的一种高压氢瓶铝内胆无芯模旋压收口方法,其中,所述的减温底座由公底座和母底座拼接构成,在公底座的后端面上向内开设有卡槽,在母底座的前端面上设置有向外凸出的、与卡槽对应匹配的凸台,凸台卡嵌于卡槽中。
[0015]
本发明的有益效果是:该方法无需采用芯模即可完成铝合金管端部旋压收口作业,通过合理分配旋压道次和各运动部件的进给量,并控制每道旋压的旋压轮行走路径、每组旋压收口过程中的加热温度来严格控制铝合金母料的流动,不仅能减少产生裂纹的概率,提高铝内胆合格率,还能摆脱对芯模的依赖。
附图说明
[0016]
图1是本发明所述的一种高压氢瓶铝内胆无芯模旋压收口方法的装夹示意图。
[0017]
图2是对瓶嘴收口段和封头增厚段进行第一组旋压收口作业时,每道旋压过程中的旋压轮行走路线图。
[0018]
图3是对瓶嘴收口段和封头增厚段进行第二组旋压收口作业时,每道旋压过程中的旋压轮行走路线图。
[0019]
图4是图3中a部分的局部放大结构示意图。
[0020]
图5是对瓶嘴收口段和封头增厚段进行第三组旋压收口作业时,每道旋压过程中的旋压轮行走路线图。
[0021]
图6是图5中b部分的局部放大结构示意图。
[0022]
图7是对瓶嘴收口段和封头增厚段进行第四组旋压收口作业后、瓶嘴及封头成型后的结构示意图。
[0023]
图8是带有冷却装置的旋压轮的结构示意图。
[0024]
图9是图8中各部件拆分后的爆炸图。
[0025]
图10是减温底座的分解爆炸图。
具体实施方式
[0026]
下面结合附图及优选实施例对本发明所述的技术方案作进一步详细的说明。
[0027]
实施例一为方便描述,如图7所示,将铝合金管100端部旋压收口至瓶嘴700及封头800成型后,未旋压收口前的铝合金管100端部的外半径与成型后的瓶嘴700的外半径之差定义为a。本实施例中所述的一种高压氢瓶铝内胆无芯模旋压收口方法,该方法包括如下步骤:(1)如图1所示,将铝合金管100一端装夹于旋压收口设备的装夹装置200中,对伸出装夹装置200外的铝合金管100端部的瓶嘴收口段500和封头增厚段600进行预热;预热温度为500
±
10℃,预热时间为8~10分钟;(2)预热完毕后,对瓶嘴收口段500和封头增厚段600进行第一组旋压收口作业;如图2所示,第一组旋压收口作业分为五道次进行旋压,通过五个道次将瓶嘴收口段500多余的铝合金流料分批次挤压至封头增厚段600。第一道旋压为直线旋压,第二道至第五道旋压为渐进分段旋压:每道旋压的前段为直线旋压、后段为凸曲线旋压,最终得到圆锥状瓶嘴收口段和椭圆状封头增厚段;第一组旋压收口作业完毕后得到的圆锥状瓶嘴收口段的最小外半径与未旋压收口前的铝合金管100端部的外半径之差为b,b=(0.25~0.4)a;其中,每道旋压过程中的旋压轮5的初始径向进给量h1均相同;每道旋压过程中、位于直线旋压段的旋压轮行走路线均为与铝合金管100的轴线成夹角α的斜直线,第一道和第二道旋压过程中、位于直线旋压段的旋压轮行走路线的夹角α均为4
°
~4.5
°
,且第二道至第五道旋压过程中、位于直线旋压段的每个后道旋压的旋压轮行走路线的夹角均比前道旋压的旋压轮行走路线的夹角增加0
°
~0.5
°
;在第一组旋压收口作业中对瓶嘴收口段和封头增厚段持续进行加热,加热温度为500
±
10℃;(3)对瓶嘴收口段和封头增厚段进行第二组旋压收口作业;如图3和图4所示,第二组旋压收口作业分为十二道次进行渐进分段旋压:每道旋压的前段为直线旋压、后段为凸曲线旋压,最终得到圆锥状瓶嘴收口段和椭圆状封头增厚段;这里通过十二个道次将瓶嘴收口段500多余的铝合金流料分批次挤压至封头增厚段600。第二组旋压收口作业完毕后得到的圆锥状瓶嘴收口段的最小外半径与第一组旋压收口作业完毕后得到的圆锥状瓶嘴收口段的最小外半径之差为c,c=(0.35~0.65)a;其中,每道旋压过程中的旋压轮5的初始径向进给量h2均相同;每道旋压过程中、位于直线旋压段的旋压轮行走路线均为与铝合金管100的轴线成夹角β的斜直线,第一道旋压过程中、位于直线旋压段的旋压轮行走路线的夹角β为4
°
~6
°
,且旋压过程中、位于直线旋压段的每个后道旋压的旋压轮行走路线的夹角均比前道旋压的旋压轮行走路线的夹角增加1
°
~1.5
°
;在第二组旋压收口作业中对瓶嘴收口段500和封头增厚段600持续进行加热,加
热温度为500
±
10℃;(4)对瓶嘴收口段500和封头增厚段600进行第三组旋压收口作业;如图5和图6所示,第三组旋压收口作业分为四道次进行渐进分段旋压:每道旋压的前段为直线旋压、后段为凸曲线旋压,最终得到圆柱状瓶嘴收口段和椭圆状封头增厚段;这里通过四个道次将瓶嘴收口段500多余的铝合金流料分批次挤压至封头增厚段600。第三组旋压收口作业完毕后得到的圆柱状瓶嘴收口段的外半径与第二组旋压收口作业完毕后得到的圆锥状瓶嘴收口段的最大外半径之差为d,d=(0.1~0.2)a;其中,每道旋压过程中的旋压轮5的初始径向进给量均为零;每道旋压过程中、位于直线旋压段的旋压轮行走路线均为与铝合金管100的轴线成夹角γ的斜直线,第一道旋压过程中、位于直线旋压段的旋压轮行走路线的夹角γ为16
°
~18
°
,且旋压过程中、位于直线旋压段的每个后道旋压的旋压轮行走路线的夹角均比前道旋压的旋压轮行走路线的夹角减少4
°
~4.5
°
;在第三组旋压收口作业中对瓶嘴收口段和封头增厚段持续进行加热,加热温度为500
±
10℃;(5)对瓶嘴收口段500和封头增厚段600进行第四组旋压收口作业至瓶嘴及封头成型,第四组旋压收口作业为一道表面精修工序;在第四组旋压收口作业中对瓶嘴收口段和封头增厚段持续进行加热,加热温度为500
±
10℃;(6)将铝合金管100从装夹装置20中取下后旋转180
°
,将铝合金管100上完成旋压收口端装夹于装夹装置200中后重复步骤(1)至(5)。
[0028]
其中,步骤(2)、步骤(3)、步骤(4)均为快速塑性成型阶段,这个阶段旋压轮5均采用材质为gcr15、硬度为hrc60
±
2、直径为300mm、厚度为60~80mm、圆角半径为16~20mm的粗旋压轮结构。
[0029]
步骤(5)为精准成型阶段,这个阶段的旋压轮5采用材质为gcr15、硬度为hrc60
±
2、直径为250mm、厚度为60~80mm、圆角半径为8~12mm的细旋压轮结构。
[0030]
步骤(2)、步骤(3)、步骤(4)、步骤(5)中,四组旋压收口作业过程中旋压收口设备的装夹装置的转速均为150~200r/min;旋压轮施加于铝合金管上的压力均为50~60kn,旋压轮转速均为550~750r/min,旋压轮轴向行进速度均为1mm/r。
[0031]
对瓶嘴收口段500和封头增厚段600进行预热及加热的方式可以采用若干加热枪300燃烧天然气来进行预热及加热,各加热枪300一字间隔排开设置。在瓶嘴收口段500和封头增厚段600区域还可以设置一组红外测温枪400,用以实时监测该区域铝合金管100母材温度,当该区域铝合金管100母材温度出现异常:过高或过低时便于操作者及时进行采取措施,避免发生铝合金管表面起皮报废等现象。
[0032]
上述旋压收口方法无需采用芯模即可完成铝合金管端部旋压收口作业,通过合理分配旋压道次和各运动部件的进给量,并控制每道旋压的旋压轮5行走路径、每组旋压收口过程中的加热温度来严格控制铝合金母料的流动,不仅能减少产生裂纹的概率,提高铝内胆合格率,还能摆脱对芯模的依赖。
[0033]
实施例二如图8、图9和图10所示,本实施例中,旋压收口设备中的旋压轮5带有冷却装置,所述的冷却装置的结构包括:带安装空腔的减温底座1,在减温底座1的前端面11上开设有前后贯通的第一套管孔12,在减温底座1的后端面13上开设有前后贯通的第二套管孔14,套管2穿
插于减温底座1的安装空腔中,且套管2的前端固定搁置于第一套管孔12中,套管2的后端固定搁置于第二套管孔14中。盘管3套设于套管2上,盘管3的进液端31和出液端32分别穿过减温底座1侧壁上对应通孔103后伸出减温底座1外。旋转轴4通过轴承支撑设置于套管2中,旋压轮5固定于伸出套管2前端外的旋转轴4前端,带电机8的电机支架7固定于减温底座1的后端面13上,且电机8的电机轴与旋转轴4后端固定连接。旋转轴4在电机8的驱动下相对于自身轴线转动,从而使固定于旋转轴4上的旋压轮5转动。
[0034]
如图10所示,本实施例中盘管3可以选择由金属管或塑料管盘制成,盘管3的进液端31和出液端32位于同侧。在盘管3的进液端31和出液端32上均设置有接头9,接头9可以采用卡套接头或宝塔接头中的其中一种。盘管3的进液端31通过接头9与带动力的冷媒介质源连通。冷媒介质可以选择温度不高于35℃的防冻液或水。
[0035]
本实施例中在旋转轴4与套管2之间的间隙中填充有导热硅胶,导热硅胶既能强化传热效果、提高盘管3中的冷媒介质与旋转轴4、旋压轮5的间接换热效率以及确保对旋压轮5均匀降温,又有助于润滑、使旋转轴4转动更加顺畅。
[0036]
本实施例中的旋压轮5由材质gcr15制成,硬度为hrc60
±
2,旋压轮5的直径为250~300mm,旋压轮5的工作圆角半径为8~20mm。在进行间接冷却降温过程中,旋压轮5的工作温度一般在350~400℃。
[0037]
如图9所示,本实施例中旋压轮5固定于旋转轴4上的固定方式为:在伸出套管2前端外的旋转轴4上设置有轴肩41,旋压轮5从旋转轴4前端套入后、通过若干第一螺栓51固定于轴肩41上,旋压轮5的前端面有向内凹进的安装槽,各第一螺栓51头部位于安装槽中。盖板6通过若干第二螺栓61固定于旋转轴4前端上,且盖板6紧贴于旋压轮5前端、将各第一螺栓51封盖于安装槽中。
[0038]
如图10所示,为便于套管2等的安装,所述的减温底座1由公底座100和母底座101拼接构成,公底座100的内部空腔104和母底座101的内部空腔拼接构成一个完整的安装空腔。在公底座100的后端面上向内开设有卡槽15,在母底座101的前端面上设置有向外凸出的、与卡槽对应匹配的凸台16,凸台16卡嵌于卡槽15中。恒温旋压轮结构通过减温底座1及若干紧固件安装于旋压机上。
[0039]
上述结构具有如下优点:无需改变旋转轴4的结构,整体结构简单、紧凑,加工及维护成本低;
②
工作时,通过输入盘管3的冷媒介质间接吸热、从而对旋转轴4和旋压轮5进行均匀降温,无需再对旋压轮5及被旋压的铝管母材浇注冷却液或润滑液,大大提高了旋压收口的合格率,改善旋压轮5的工作环境、延长其使用寿命。
[0040]
以上所述仅是本发明的较佳实施例,并非是对本发明作任何其他形式的限制,而依据本发明的技术实质所作的任何修改或等同变化,仍属于本发明要求保护的范围。