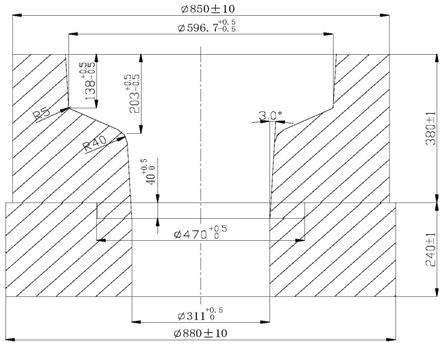
一种gh4169盘轴一体化锻件的加工方法
技术领域
1.本发明属于合金锻造领域,具体涉及一种gh4169盘轴一体化锻件的加工方法。
背景技术:2.镍基合金是指在650~1000℃高温下有较高的强度与一定的抗氧化腐蚀能力等综合性能的一类合金。按照主要性能又细分为镍基耐热合金,镍基耐蚀合金,镍基耐磨合金,镍基精密合金与镍基形状记忆合金等。
3.gh4169是一种沉淀强化镍基高温合金,在
‑
253~650℃温度范围内具有良好的综合性能,650℃以下的屈服强度居变形高温合金的首位,并具有良好的抗疲劳、抗辐射、抗氧化、耐腐蚀性能,以及良好的加工性能、焊接性能良好。能够制造各种形状复杂的零部件,在宇航、核能、石油工业及挤压模具中,在上述温度范围内获得了极为广泛的应用。gh4169合金在热加工成形过程中,由于锻造变形温度范围窄、变形抗力大等因素,且针对于盘轴一体化锻件而言,盘部与轴部横向截面尺寸变化较大,盘部与轴部最大截面面积比为6:1,盘轴重量比约为2:1,重量分布“头重脚轻”容易失稳,造成偏心,成形难度较大,导致现有的成形方法在生产盘轴件时材料利用率低、生产效率低、报废率高。
4.申请号为cn201510658047.1的专利文件公开了一种gh4738高温合金大型铸锭开坯方法,是通过多次镦拔锻造,同时辅以玻璃润滑剂及包套保温的方式开坯锻造,使得镍基高温合金铸锭晶粒变得均匀细小。但仅采用拔长的方式进行锻造,无法应用于锻造一些形状复杂的锻件。
技术实现要素:5.本发明为解决上述问题,提供了一种gh4169盘轴一体化锻件的加工方法。
6.具体是通过以下技术方案来实现的:
7.一种gh4169盘轴一体化锻件的加工方法,具体方法如下:
8.1、下料:将gh4169合金棒材原材料按相应规格进行下料,得到锻前坯料。
9.2、机加平端面:对已下料的gh4169合金棒材以最小量见光车两端面,车端面后平面度、垂直度公差为
±
0.5mm。
10.3、一次加热:将坯料两端倒圆角(r20
‑
25)mm,在坯料的任意一端包裹厚度≥50mm的石棉,坯料被包裹的长度为380
±
5mm,加热至850℃后进行保温,再加热至1040摄氏度后进行保温。
11.进一步,所述的保温,保温时间按坯料有效厚度
×
0.6min计算。
12.4、组合锻:
13.a.胎模锻:将胎模预热后将坯料上包裹的石棉撤下,并将此端作为锻件的轴部,未包套部分盖上石棉,镦粗后作为锻件的盘部,将锻件放入胎模,镦锻成形;
14.b.二次加热:将成形的坯料盘部包裹厚度≥50mm的石棉,加热至850℃并保温,再升温至1020℃后进行保温;
15.进一步,所述的保温,保温时间按坯料有效厚度
×
0.6min计算。
16.c.自由锻:将二次加热后的坯料在保持石棉包裹的条件下,将轴部进行锻压拔长至l≥595mm,终锻温度≥930℃,即得到盘轴一体化锻件。
17.综上所述,本发明的有益效果在于:本发明通过采用胎模锻和自由锻进行组合的锻造方式,显著减弱了盘与轴的偏心情况,锻件变形基本均匀,且锻件在室温下布氏硬度可达到438,断后伸长率达到19.0%,断面收缩率达到34%,锻件材料利用率得以提升,基本消除了尺寸报废的风险。
18.其中,机加平端面的控制有效保证了两端面的平面度和垂直度,基本消除下料偏斜对锻造的影响。胎模镦粗制坯过程中大头端偏心的情况显著降低,经过锻造加热过程对未变形的坯料区域进行石棉包套,保证在炉中起到很好的隔热作用,有效控制了因不可避免的空烧影响,提升了锻造成形可操作性,火次减少,变形基本均匀,锻件尺寸满足设计要求,产品组织得到保障,在满足设计要求的同时,也保证了锻件的质量要求,减少了报废率,提高了生产效率和材料利用率。
附图说明
19.图1为胎模锻的模具剖面示意图。
20.图2为gh4169盘轴一体化锻件的尺寸示意图。
具体实施方式
21.下面对本发明的具体实施方式作进一步详细的说明,但本发明并不局限于这些实施方式,任何在本实施例基本精神上的改进或代替,仍属于本发明权利要求所要求保护的范围。
22.实施例1
23.一种gh4169盘轴一体化锻件的加工方法,具体方法如下:
24.1、下料:将gh4169合金棒材原材料按相应规格进行下料,得到锻前坯料。
25.2、机加平端面:对已下料的gh4169合金棒材以最小量见光车两端面,车端面后平面度、垂直度公差为
±
0.5mm。
26.3、一次加热:将坯料两端倒圆角r20mm,在坯料的任意一端包裹厚度60mm的石棉,坯料被包裹的长度为380mm,加热至850℃后进行保温,再加热至1040摄氏度后进行保温。
27.进一步,所述的保温,保温时间按坯料有效厚度
×
0.6min计算。
28.4、组合锻:
29.a.胎模锻:将胎模预热后将坯料上包裹的石棉撤下,并将此端作为锻件的轴部,未包套部分盖上石棉,镦粗后作为锻件的盘部,将锻件放入胎模,镦锻成形;
30.b.二次加热:将成形的坯料盘部包裹厚度60mm的石棉,加热至850℃并保温,再升温至1020℃后进行保温;
31.进一步,所述的保温,保温时间按坯料有效厚度
×
0.6min计算。
32.c.自由锻:将二次加热后的坯料在保持石棉包裹的条件下,将轴部进行锻压拔长至l为600mm,终锻温度为950℃,即得到盘轴一体化锻件。
33.实施例2
34.一种gh4169盘轴一体化锻件的加工方法,具体方法如下:
35.1、下料:将gh4169合金棒材原材料按相应规格进行下料,得到锻前坯料。
36.2、机加平端面:对已下料的gh4169合金棒材以最小量见光车两端面,车端面后平面度、垂直度公差为
±
0.5mm。
37.3、一次加热:将坯料两端倒圆角r25mm,在坯料的任意一端包裹厚度70mm的石棉,坯料被包裹的长度为385mm,加热至850℃后进行保温,再加热至1040摄氏度后进行保温。
38.进一步,所述的保温,保温时间按坯料有效厚度
×
0.6min计算。
39.4、组合锻:
40.a.胎模锻:将胎模预热后将坯料上包裹的石棉撤下,并将此端作为锻件的轴部,未包套部分盖上石棉,镦粗后作为锻件的盘部,将锻件放入胎模,镦锻成形;
41.b.二次加热:将成形的坯料盘部包裹厚度70mm的石棉,加热至850℃并保温,再升温至1020℃后进行保温;
42.进一步,所述的保温,保温时间按坯料有效厚度
×
0.6min计算。
43.c.自由锻:将二次加热后的坯料在保持石棉包裹的条件下,将轴部进行锻压拔长至l为595mm,终锻温度为1000℃,即得到盘轴一体化锻件。
44.一、gh4169盘轴一体化锻件理化性质
45.对实施例1和实施例2所得到的锻件经过热处理后进行室温拉伸和硬度测试、高温拉伸测试、持久性能测试以及金相检验,结果如表1
‑
4所示。
46.其中,热处理的步骤为常规固溶处理和时效处理。
47.表1室温拉伸和硬度检测结果
[0048][0049][0050]
注:l1和l2是在实施例1所得锻件上切取的两段试样,l3和l4是在实施例2所得锻件上切取的两段试样。
[0051]
表2高温拉伸测试结果
[0052][0053]
注:l1和l2是在实施例1所得锻件上切取的两段试样,l3和l4是在实施例2所得锻件上切取的两段试样。
[0054]
表3持久性能测试结果
[0055][0056]
注:l1和l2是在实施例1所得锻件上切取的两段试样,l3和l4是在实施例2所得锻件上切取的两段试样。
[0057]
表4金相检测结果
[0058]