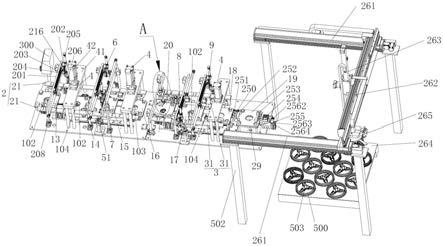
1.本发明涉及一种轮毂自动化装配设备,尤其是一种轮毂内置零件自动化安装设备。
背景技术:2.目前,对于轮毂的中心通孔内进行上轴承、下轴承、上油封、下油封及衬套的安装采用人工进行将轮毂进行上料定位后,再通过人工将上轴承安放后人工启动顶压机构进行顶压以完成上轴承的装配,然后人工将轮毂翻面后再人工安放下轴承和衬套后再人工启动顶压机构,最后进行上油封安放人工顶压,轮毂翻面再进行下油封安放人工顶压,其方式存在工作效率低下,并且装配成品合格率较低,同时装配后检测也为人工检测,因此使得装配时需要较多人工进行操作,使得人工成本和劳动强度提升。
技术实现要素:3.本发明的目的是为了解决上述技术的不足而设计的一种提升工作效率和成品合格率的轮毂内置零件自动化安装设备。
4.本发明所设计的轮毂内置零件自动化安装设备,包括:
5.工作台,其包括轮毂装配区,轮毂装配区包括轮毂抓取传送机构、以及由左至右依次相互间隔排列的第一轮毂定位工装、第二轮毂定位工装、第三轮毂定位工装、第四轮毂定位工装、第五轮毂定位工装、第六轮毂定位工装和第七轮毂定位工装;第二轮毂定位工装、第四轮毂定位工装和第六轮毂定位工装的中心孔上方分别设置有顶压机构,轮毂抓取传送机构将左侧一工装处的轮毂抓取并传送至右侧一工装处,第二轮毂定位工装通过弹性复位机构安装于工作台上;
6.下轴承输送机构和下轴承上料机构,其两者均位于第二轮毂定位工装的旁侧;下轴承上料机构将下轴承上料并放置于下轴承输送机构上,下轴承输送机构将所上料的下轴承输送至第二轮毂定位工装的中心孔下方;
7.衬套上料机构和上轴承上料机构,其两者均位于第三轮毂定位工装的旁侧;衬套上料机构将衬套上料至第三轮毂定位工装处轮毂的中心通孔内,上轴承上料机构也将衬套上料至第三轮毂定位工装处轮毂的中心通孔内;
8.上油封上料机构、下油封上料机构和下油封输送机构,其三者均位于第五轮毂定位工装的旁侧;下油封上料机构将下油封上料并放置于下油封输送机构上,下油封输送机构将所上料的下油封输送至第六轮毂定位工装的中心孔下方,上油封上料机构将上油封上料至第五轮毂定位工装处轮毂的中心通孔上端口内。
9.作为优选,还包括第八轮毂定位工装、旋转检测机构和旋转驱动机构,旋转检测机构和旋转驱动机构分别位于第八轮毂定位工装的中心孔上方和下方,且第八轮毂定位工装位于第四轮毂定位工装和第五轮毂定位工装之间。
10.作为优选,旋转检测机构包括固定于工作台上的第一架体、下压板、感应件、用于
感应感应件上的感应部的感应器、以及与第八轮毂定位工装的中心孔位置对应的下压气缸和检测轴体,下压气缸固定于第一架体上,其活塞杆上固定下压板,检测轴体旋转式安装于下压板上,感应器安装于下压板上,感应件固定于检测轴体上,且感应件与感应器的位置相互对应,检测轴体下端设置有上密封圈和下端直径小于上端直径的第一圆台体中的至少一者,旋转驱动机构包括与检测轴体位置对应的检测驱动轴、举升板、步进驱动电机和固定于工作台上的举升气缸,检测驱动轴旋转式安装于举升板上,步进驱动电机通过连接杆固定于举升板底面,步进驱动电机的转轴与检测驱动轴底端固定相连,举升气缸的活塞杆贯穿工作台的贯通区后与举升板固定相连,检测驱动轴的上端设置有下密封圈和上端直径小于下端直径的第二圆台体中的至少一者。
11.作为优选,检测驱动轴的上端直径小于下轴承的内圈内孔,检测轴体的下端直径小于上轴承的内圈内孔。
12.作为优选,还可在位于第七轮毂定位工装旁侧进行设置下料机构,下料机构包括横向位移驱动装置、垂直位移驱动装置、纵向位移驱动装置和轮毂抓取装置,纵向位移驱动装置安装于横向位移驱动装置上,垂直位移驱动装置安装于纵向位移驱动装置上,轮毂抓取装置安装于垂直位移驱动装置上。
13.作为优选,轮毂抓取装置包括与纵向位移驱动装置的底端固定相连的基板、固定于基板底面的锁紧气缸、旋转板、导向板和至少三根环形阵列分布的连杆,基板的底面中心位置固定有柱子,旋转板上设置有圆形通孔,旋转板通过圆形通孔套于柱子上,并被柱子底部的台阶限位,柱子底部的台阶底面固定导向板,至少三根连杆的一端分别与旋转板边缘销轴铰接,至少三根连杆的另一端均销轴铰接有滑块,各滑块分别插入导向板上至少三个呈环形阵列设置的滑槽内,各滑块的底面均固定有夹板,夹板的内侧设置有与轮毂外形匹配的第三弧形内凹面,锁紧气缸的活塞杆端部与一滑块固定相连,导向板和柱子的底面分别设置有位置相互对应的容置孔。
14.作为优选,还包括升降驱动机构和翻转机构,第七轮毂定位工装安装于升降驱动机构上,翻转机构包括第一夹块、第二夹块、推移装置和旋转驱动装置;第一夹块和第二夹块相互对称且间隔设置,并位于第七轮毂定位工装的上方;第七轮毂定位工装上的左右相对应两侧分别设置有第一安装架和第二安装架,第一夹块通过转轴旋转式安装于第一安装架上,第二夹块安装于推移装置上,推移装置通过转轴旋转式安装于第二安装架上;旋转驱动装置安装于第二安装架上,并与第二安装架上的转轴连接;
15.作为优选,旋转驱动装置包括竖直气缸、齿条、与齿条啮合的齿轮和导向块,竖直气缸和导向块均固定于第二安装架上,竖直气缸的活塞杆与齿条的底端固定,齿条置于导向块的导向通槽内,齿轮套接固定于推移装置的转轴上;
16.作为优选,升降驱动机构包括底板、导向杆、导向套和升降驱动气缸,工作台上位于第七轮毂定位工装的下方设置有方形通孔,底板位于方形通孔的下方,并通过连接柱与工作台固定相连,导向套固定于底板上,导向杆固定于第七轮毂定位工装的定位板底面,导向杆的底端贯穿导向套,且升降驱动气缸固定于底板上,其活塞杆贯穿底板后与第七轮毂定位工装的定位板固定相连。
17.作为优选,顶压机构包括顶压气缸、顶压件和固定于工作台上第二架体,顶压气缸固定于第二架体上,顶压气缸的活塞杆与顶压件固定相连。
18.作为优选,在第四轮毂定位工装处顶压机构的顶压件包括胶块、受压浮动块和至少两根连接杆,胶块位于受压浮动块和导向体之间,连接杆的上端螺纹段贯穿受压浮动块后与导向体上的螺纹孔螺纹连接,受压浮动块被连接杆下端台阶限位。
19.作为优选,在第二轮毂定位工装处的顶压机构和在第四轮毂定位工装处的顶压机构上均设置有导向结构,导向结构包括定位杆和导向体,定位杆贯穿第二架体后与导向体固定相连,且具有导向结构的顶压机构中的顶压件与导向体固定相连。
20.作为优选,在第六轮毂定位工装的第二架体上可固定安装有自动打黄油泵。
21.作为优选,下轴承上料机构、衬套上料机构、上轴承上料机构、上油封上料机构和下油封上料机构均包括固定于工作台上的第三架体、横向位移气缸、横向直线导轨、横向位移板、升降气缸、升降板、竖直直线导轨和抓取装置,横向位移气缸和横向直线导轨均横向固定于第三架体上,横向位移板固定于横向直线导轨的滑块上,横向位移气缸的活塞杆与横向位移板固定相连,升降气缸和竖直直线导轨均固定于横向位移板上,升降板固定于竖直直线导轨的滑块上,升降气缸的活塞杆与升降板固定相连,抓取装置安装于升降板上;下轴承输送机构和下油封输送机构均包括往复平移驱动装置和安装于往复平移驱动装置上的工件定位柱,下轴承输送机构的工件定位柱位于第二轮毂定位工装下方,其通过往复平移驱动装置驱动移出第二轮毂定位工装下方后与下轴承上料机构的抓取装置位置对应;下油封输送机构的工件定位柱位于第六轮毂定位工装下方,其通过往复平移驱动装置驱动移出第六轮毂定位工装下方后与下油封上料机构的抓取装置位置对应;且下轴承上料机构的抓取装置、衬套上料机构的抓取装置和下油封上料机构的抓取装置均包括气动夹爪,上油封上料机构的抓取装置包括抓取柱体,抓取柱体的下端设置有下端直径小于上端直径的第三圆台体。
22.作为优选,上轴承上料机构的抓取装置包括抓取气缸、固定板、涨紧套、涨紧柱体和定位套,固定板固定于上轴承上料机构的升降板上,抓取气缸和定位套分别固定于固定板的上侧面和下侧面,涨紧套置于定位套的内孔中,涨紧柱体置于涨紧套的内孔中,涨紧套的顶端与固定板固定相连,涨紧套的下部设置有多个呈环形阵列并相互间隔设置的第一长形通孔,涨紧柱体下端设置有上端直径小于下端直径的第四圆台体,且第四圆台体上升后对涨紧套下部撑开使涨紧套下端部直径变大而将套于涨紧套下端部上的上轴承得到涨紧固定后抓取。
23.作为优选,在第二轮毂定位工装旁侧设置有与上轴承上料机构的抓取装置位置对应的上轴承上料台,在第三轮毂定位工装上前后相对应两侧分别设置有与衬套上料机构的抓取装置位置对应的衬套上料台和与下轴承上料机构的抓取装置位置对应的下轴承上料台,在第五轮毂定位工装的旁侧设置有与上油封上料机构的抓取装置位置对应的上油封上料台,在第六轮毂定位工装的旁侧设置有与下油封上料机构的抓取装置位置对应的下油封上料台,各上料台分别对接震动送料轨道,震动送料轨道与震动上料盘的出料口对接,且震动送料轨道的下侧面固定平振器,衬套上料台通过支撑台固定于工作台上,衬套上料台上设置有衬套放置通道,衬套放置通道上设置有端部开口和底部开口,底部开口处设置有滑动块,滑动块上位于端部开口的位置处设置有阻挡块,滑动块的底面固定有上推气缸,上推气缸的活塞杆贯穿滑动块,阻挡块的上端固定有有红外感应器,红外感应器用于检测输送过来的衬套是否到位,支撑台上固定有侧面气缸,侧面气缸的推移件与上推气缸固定相连。
24.作为优选,抓取传送机构包括第一夹取输送装置和第二夹取输送装置,轮毂装配区包括轴承及衬套装配区和检测及油封装配区,轴承及衬套装配区上具有第一夹取输送装置、第一轮毂定位工装、第二轮毂定位工装、第三轮毂定位工装和第四轮毂定位工装,检测及油封装配区上具有第二夹取输送装置、第八轮毂定位工装、第五轮毂定位工装、第六轮毂定位工装和第七轮毂定位工装。
25.作为优选,第一夹取输送装置包括位于轴承及衬套装配区前后两侧的第一顶升平移机构和安装于第一顶升平移机构上的四个第一夹取气缸,四个第一夹取气缸的活塞杆分别与第一轮毂定位工装、第二轮毂定位工装、第三轮毂定位工装和第四轮毂定位工装的位置对应,四个第一夹取气缸的活塞杆上分别固定有第一夹取块,两第一顶升平移机构均包括第一顶升板条、第一顶升气缸、第一平移板条、第一平移直线导轨和第一平移驱动气缸,第一平移驱动气缸和第一平移直线导轨均固定于工作台上,工作台上位于第一平移直线导轨的旁侧设置有第二长形通孔,工作台下方设置有第一连接架,第一连接架贯穿第二长形通孔与第一平移板条固定相连,第一平移驱动气缸的活塞杆与第一连接架固定相连,第一平移板条固定于第一平移直线导轨的滑块上,第一顶升气缸固定于第一平移板条上,第一顶升板条固定于第一顶升气缸的活塞杆上,四个第一夹取气缸分别固定于第一顶升板条上。
26.作为优选,第二夹取输送装置均包括位于检测及油封装配区前后两侧的第二顶升平移机构和安装于第二顶升平移机构上的三个第二夹取气缸,三个第二夹取气缸的活塞杆分别与第八轮毂定位工装、第五轮毂定位工装、第六轮毂定位工装的位置对应,三个第二夹取气缸的活塞杆上分别固定有第二夹取块,两第二顶升平移机构均包括第二顶升板条、第二顶升气缸、第二平移板条、第二平移直线导轨和第二平移驱动气缸,第二平移驱动气缸和第二平移直线导轨均固定于工作台上,工作台上位于第二平移直线导轨的旁侧设置有第三长形通孔,工作台下方设置有第二连接架,第二连接架贯穿第二长形通孔与第二平移板条固定相连,第二平移驱动气缸的活塞杆与第二连接架固定相连,第二平移板条固定于第二平移直线导轨的滑块上,第二顶升气缸固定于第二平移板条上,第二顶升板条固定于第二顶升气缸的活塞杆上,三个第二夹取气缸分别固定于第二顶升板条上。
27.本发明所设计的轮毂内置零件自动化安装设备,其采用自动化装配及自动成品检测,使得装配方便、快捷,大幅度提升产品装配的工作效率和装配后的成品合格率,并且仅一人即可实现批量式加工,使得人工成本和劳动强度得到大幅度的降低。
附图说明
28.图1是整体结构示意图(一);
29.图2是整体结构示意图(二);
30.图3是a处局部放大图;
31.图4是整体结构示意图(三);
32.图5是轮毂抓取装置结构示意图(一);
33.图6是轮毂抓取装置结构示意图(二);
34.图7是衬套上料台具体结构的整体设备示意图;
35.图8是整体结构示意图(四);
36.图9是轮毂装配区部位结构示意图(一);
37.图10是轮毂装配区部位结构示意图(二;
38.图11是轮毂装配区部位结构示意图(三);
39.图12是轮毂装配区部位结构示意图(四);
40.图13是上轴承上料机构结构示意图(一);
41.图14是上轴承上料机构结构示意图(二);
42.图15是检测工位结构示意图;
43.图16是旋转驱动机构结构示意图;
44.图17是第二轮毂定位工装处设置的弹性复位装置结构示意图;
45.图18是第二轮毂定位工装处设置的弹性复位装置的整体设备结构示意图;
46.图19整体结构示意图(五);
47.图20整体结构示意图(六);
48.图21整体结构示意图(七)。
具体实施方式
49.下面将结合本发明实施例中的附图,对本发明实施例中的技术方案进行清楚、完整地描述,显然,所描述的实施例仅仅是本发明一部分实施例,而不是全部的实施例。基于本发明中的实施例,本领域普通技术人员所获得的所有其他实施例,都属于本发明保护的范围。实施例:
50.如附图所示,本实施例所描述的轮毂内置零件自动化安装设备,包括工作台1、下轴承输送机构30、下轴承上料机构5、衬套上料机构7、上轴承上料机构6、上油封上料机构8、下油封上料机构9和下油封输送机构37;工作台1包括轮毂装配区100,轮毂装配区100包括轮毂抓取传送机构、以及由左至右依次相互间隔排列的第一轮毂定位工装13、第二轮毂定位工装14、第三轮毂定位工装15、第四轮毂定位工装16、第五轮毂定位工装17、第六轮毂定位工装18和第七轮毂定位工装19;第二轮毂定位工装14、第四轮毂定位工装16和第六轮毂定位工装18的中心孔102上方分别设置有顶压机构4,轮毂抓取传送机构将左侧一工装处的轮毂抓取并传送至右侧一工装处,第二轮毂定位工装14通过弹性复位机构38安装于工作台1上;下轴承输送机构30和下轴承上料机构5均位于第二轮毂定位工装14的旁侧;下轴承上料机构5将下轴承上料并放置于下轴承输送机构30上,下轴承输送机构30将所上料的下轴承输送至第二轮毂定位工装14的中心孔102下方;衬套上料机构7和上轴承上料机构6均位于第三轮毂定位工装15的旁侧;衬套上料机构7将衬套上料至第三轮毂定位工装15处轮毂500的中心通孔501内,上轴承上料机构6也将衬套上料至第三轮毂定位工装15处轮毂500的中心通孔501内;上油封上料机构8、下油封上料机构9和下油封输送机构37均位于第五轮毂定位工装17的旁侧;下油封上料机构9将下油封上料并放置于下油封输送机构37上,下油封输送机构37将所上料的下油封输送至第六轮毂定位18工装的中心孔102下方,上油封上料机构8将上油封上料至第五轮毂定位工装17处轮毂500的中心通孔501上端口内;上述中的各轮毂定位工装均包括一带中心孔102的定位板100,定位板100上设置有四个矩形阵列设置的定位块101,且四个矩形阵列设置的定位块101环绕中心孔102设置,当轮毂放置于定位板100上后,定位板100的中心孔102与轮毂500的中心通孔501位置对应,第一轮毂定位工装
13、第三轮毂定位工装15、第四轮毂定位工装16、第五轮毂定位工装17、第六轮毂定位工装18和第七轮毂定位工装19中的定位板100通过支腿400固定于工作台上,第二轮毂定位工装14上的定位板100通过弹簧复位装置38安装于工作台1上,弹簧复位装置38包括多根导向柱体382和套于导向柱体382上的弹簧381,导向柱体382插入工作台上穿孔383中,且弹簧381的两端分别与第二轮毂定位工装14的定位板100和工作台1抵触。
51.较佳地,在第三轮毂定位工装15、第四轮毂定位工装16和第五轮毂定位工装17的中心孔102对应下方设置固定柱103,固定柱103与工作台1固定相连,其固定柱103的设置使得在顶压时下轴承得到支撑托举,防止在顶压时,下轴承由于上轴承或上油封装配的顶压而导致下轴承移位的情况发生,以提升装配的可靠性。
52.进一步地,还包括第八轮毂定位工装20、旋转检测机构27和旋转驱动机构28,旋转检测机构27和旋转驱动机构28分别位于第八轮毂定位工装20的中心孔102上方和下方,且第八轮毂定位工装20位于第四轮毂定位工装16和第五轮毂定位工装17之间,具体地,旋转检测机构27包括固定于工作台1上的第一架体271、下压板272、感应件273、用于感应感应件273上的感应部274的感应器278、以及与第八轮毂定位工装20的中心孔102位置对应的下压气缸275和检测轴体276,下压气缸275固定于第一架体271上,其活塞杆上固定下压板272,检测轴体276旋转式安装于下压板272上,感应器278安装于下压板272上,感应件273固定于检测轴体276上,且感应件273与感应器278的位置相互对应,检测轴体276下端设置有上密封圈681和下端直径小于上端直径的第一圆台体277中的至少一者,旋转驱动机构包括与检测轴体276位置对应的检测驱动轴281、举升板284、步进驱动电机285和固定于工作台1上的举升气缸283,检测驱动轴281旋转式安装于举升板284上,步进驱动电机285通过连接杆286固定于举升板284底面,步进驱动电机285的转轴与检测驱动轴281底端固定相连,举升气缸283的活塞杆贯穿工作台的贯通区287后与举升板284固定相连,检测驱动轴281的上端设置有下密封圈682和上端直径小于下端直径的第二圆台体282中的至少一者。
53.当已装配上轴承、下轴承和衬套的轮毂被抓取传送至第八轮毂定位工装20的定位板100上后,因第一圆台体和第二圆台体的最大直径和中部直径均大于上、下轴承内圈的内孔,举升气缸283的活塞杆伸出推动举升板284上升,使得旋转驱动轴281的第二圆台体282上端插入下轴承内圈的内孔内,此时下压气缸275的活塞杆下降,将检测轴体276的第一圆台体277的下端插入上轴承内圈的内孔内,以利用第一圆台体277的中部和第二圆台体282的中部分别抵触上轴承内圈的内孔口沿和下轴承内圈的内孔口沿对轮毂装夹,或者因检测驱动轴281的上端和检测轴体276的下端分别套接固定上密封圈681和下密封圈682,而检测驱动轴281的上端和检测轴体276的下端直径均小于上、下轴承内圈的内孔,此时下压气缸275的活塞杆下降,将检测轴体276下端和上密封圈681均插入上轴承内圈的内孔内,且上密封圈681与上轴承内圈的内孔过盈配合,举升气缸283的活塞杆伸出推动举升板284上升,使得旋转驱动轴281上端和上密封圈681均插入下轴承内圈的内孔内,且下密封圈682与上轴承内圈的内孔过盈配合,以利用检测驱动轴281和检测轴体276分别通过上密封圈681、下密封圈682与上轴承和下轴承可脱卸式连接,为了便于轴承内圈的内孔中插入,可在设置上密封圈681的检测轴体276下端设置第一圆台体277,可在设置下密封圈682的检测驱动轴281上端第二圆台体282。
54.此时步进驱动电机285的转轴旋转驱动轮毂旋转带动检测轴体276旋转,此时感应
器278进行检测感应件273的感应部274,检测到感应部274则与感应器278相连的plc控制器300判断为合格,在设定时间内为检测到感应部274则判断为不合格,其中感应件273为圆盘,感应部274为圆盘上的凹槽。
55.在本实施例中,还可在位于第七轮毂定位工装19旁侧进行设置下料机构260,下料机构260包括横向位移驱动装置261、垂直位移驱动装置263、纵向位移驱动装置262和轮毂抓取装置265,纵向位移驱动装置262安装于横向位移驱动装置261上,垂直位移驱动装置263安装于纵向位移驱动装置262上,轮毂抓取装置265安装于垂直位移驱动装置263上。其中,横向位移驱动装置261、垂直位移驱动装置263、纵向位移驱动装置262均采用伺服滑台,利用横向位移驱动装置261、垂直位移驱动装置263、纵向位移驱动装置262的三轴位移将轮毂500抓取装置位移至第七轮毂定位工装19上将已装配完成的轮毂500抓取并输送至下料台264上放置,从而完成下料工作,plc控制器300中存有合格控制程序和不合格控制程序,合格控制程序控制横向位移驱动装置261、垂直位移驱动装置263和纵向位移驱动装置262移位将从第七轮毂定位工装19上的轮毂500抓取并放置于下料台264的产品合格放置区2641,不合格控制程序控制横向位移驱动装置261、垂直位移驱动装置263和纵向位移驱动装置262移位将从第七轮毂定位工装19上的轮毂500抓取并放置于下料台的产品不合格放置区2642,横向位移驱动装置261的底面固定有支撑架502,以使横向位移驱动装置261固定于高位;不合格品放置区,能够把安装过程中缺失的零件和上下轴承扭力不达标的零件,全部识别出来放到废料框内。
56.具体地,轮毂抓取装置265包括与纵向位移驱动装置263的底端固定相连的基板52、固定于基板52底面的锁紧气缸53、旋转板54、导向板55和至少三根环形阵列分布的连杆57,基板52的底面中心位置固定有柱子61,旋转板54上设置有圆形通孔541,旋转板54通过圆形通孔541套于柱子61上,并被柱子61底部的台阶限位,柱子61底部的台阶59底面固定导向板55,至少三根连杆57的一端分别与旋转板56边缘销轴铰接,至少三根连杆57的另一端均销轴铰接有滑块56,各滑块56分别插入导向板55上至少三个呈环形阵列设置的滑槽551内,各滑块56的底面均固定有夹板63,夹板63的内侧设置有与轮毂外形匹配的第三弧形内凹面631,锁紧气缸53的活塞杆端部与一滑块56固定相连,导向板55和柱子的底面分别设置有位置相互对应的容置孔;为了更好的夹紧轮毂,可将滑块设置为四个。
57.在本实施例中,还包括升降驱动机构29和翻转机构25,第七轮毂定位工装19安装于升降驱动机构29上,翻转机构25包括第一夹块252、第二夹块253、推移装置254和旋转驱动装置256,推移装置254采用推移气缸;第一夹块252和第二夹块253相互对称且间隔设置,并位于第七轮毂定位工装19的上方;第七轮毂定位工装19上的左右相对应两侧分别设置有第一安装架251和第二安装架255,第一夹块252通过转轴旋转式安装于第一安装架251上,第二夹块253安装于推移装置254上,推移装置254通过转轴250旋转式安装于第二安装架255上;旋转驱动装置256安装于第二安装架255上,并与第二安装架255上的转轴250连接,基于轮毂抓取装置265为需要将轮毂500的中心柱体503进行容置定位,以便于对轮毂抓取更加稳定,并且由于在装配上、下轴承、衬套和上、下油封时轮毂500的中心柱体503朝下,从而在最后装配上、下油封后的轮毂500被抓取传送至第七轮毂定位工装19后,其轮毂500的中心柱体503也处于朝下状态,此时推移装置254的活塞杆伸出使得第二夹块253推出将最后装配的轮毂500夹紧在第一夹块251和第二夹块253之间,然后升降驱动机构29驱动第七
轮毂定位工装19下降,最后利用旋转驱动装置256驱动推移装置254和第二夹块253旋转而使得被夹在第一夹块251和第二夹块253之间的轮毂500得到旋转180
°
后,轮毂500的中心柱体503朝上,升降驱动机构29驱动第七轮毂定位工装19上升对翻转后的轮毂进行托举,以便于轮毂抓取装置265来进行抓取已装配完成的轮毂500,轮毂500被抓取后第一夹块251和第二夹块253松开轮毂500,进一步地,为了第一夹块251和第二夹块253对轮毂500进行夹紧较为方便快捷,而在第一夹块251和第二夹块253的内侧均设置第一弧形内凹面257,其翻转工序的设置可以根据轮毂的实际结构进行选择性将已装配的轮毂进行翻转或不进行翻转,所以旋转驱动装置与plc控制器相连并受其控制,升降驱动机构29的升降驱动气缸294通过气泵与plc控制器相连并受其控制,因此plc控制器可根据程序进行控制旋转驱动电机和升降驱动气缸294进行动作或不动作。
58.旋转驱动装置包括竖直气缸2564、齿条2563、与齿条啮合的齿轮2562和导向块2565,竖直气缸2564和导向块2565均固定于第二安装架255上,竖直气缸2564的活塞杆与齿条2563的底端固定,齿条2563置于导向块2565的导向通槽内,齿轮2562套接固定于推移装置254的转轴250上,从而通过竖直气缸2564的活塞杆伸缩来驱动齿条2563升降来实现齿轮2562正反旋转,以进一步达到推移装置的正反180
°
旋转动作,实现将夹持在第一夹块和第二夹块之间的轮毂进行正反180
°
旋转,或者旋转驱动装置可采用齿轮减速电机,齿轮减速电机的转轴与推移装置254的转轴250固定相连,利用齿轮减速电机来控制推移装置的旋转。
59.升降驱动机构29包括底板291、导向杆293、导向套292和升降驱动气缸294,工作台上位于第七轮毂定位工装的下方设置有方形通孔290,底板291位于方形通孔的下方,并通过连接柱与工作台固定相连,导向套292固定于底板上,导向杆293固定于第七轮毂定位工装的定位板底面,导向杆293的底端贯穿导向套292,且升降驱动气缸294固定于底板上,其活塞杆贯穿底板291后与第七轮毂定位工装的定位板固定相连,其在轮毂翻转时升降驱动气缸294驱动第七轮毂定位工装的定位板下降,在轮毂翻转180
°
后,升降驱动气缸294驱动第七轮毂定位工装的定位板上升,以扶平轮毂,使轮毂处于水平状态,便于轮毂抓取装置进行抓取装配完成的轮毂。
60.在本实施例中,顶压机构4包括顶压气缸42、顶压件43和固定于工作台1上第二架体41,顶压气缸42固定于第二架体41上,顶压气缸42的活塞杆与顶压件43固定相连,顶压气缸42的活塞杆下降驱动顶压件43下降,以将位于轮毂500中心通孔501处的上轴承、下轴承、上油封和下油封进行顶压装配至轮毂500的中心通孔501内,以完成快速自动装配,同时,在第二轮毂定位工装14处的顶压机构4和在第四轮毂定位工装16处的顶压机构4上均设置有导向结构,导向结构包括定位杆65和导向体60,定位杆65贯穿第二架体41后与导向体60固定相连,且具有导向结构的顶压机构4中的顶压件43与导向体60固定相连,从而利用导向结构使得顶压件43在顶压时稳定可靠,以达到顶压后的上、下轴承及衬套三者同心,提升产品装配后的质量。
61.在第四轮毂定位工装16处顶压机构4的顶压件43包括胶块431、受压浮动块432和至少两根连接杆433,胶块431位于受压浮动块432和导向体60之间,连接杆433的上端螺纹段贯穿受压浮动块432后与导向体60上的螺纹孔螺纹连接,受压浮动块432被连接杆433下端台阶限位,胶块采用优力胶块,主要是在上轴承压入过程时,由于优力胶块有软压力,可
以确保下轴承先压到入轮毂的中心孔内预定装配位置后,然后在优力胶块软压力的作用下将上轴承在压入到位,由于工装表面和轮毂底面均作为装配基准,因此将下轴承先压入装配位置,使得上轴承及衬套根据下轴承作为基准进行压入装配,达到装配质量得到提升,并且装配一步到位,提升效率。
62.进一步地,在第六轮毂定位工装18的第二架体41上可固定安装有自动打黄油泵64,在当在第六轮毂定位工装18上进行上油封和下油封装配完成后可启动自动打黄油泵64进行在油封处打黄油,该操作步骤根据实际情况选择进行,因为轮毂的上、下油封,根据车型需要,有些需要在油封上注黄油,而有些不需要注黄油,增加此自动打黄油泵后,可自动切换,需要时打开会自动打黄油,不需要时关闭,所以在需要时可选择打黄油,或者在不需要时自动打黄油泵64停止启动。
63.在本实施例中,下轴承上料机构5、衬套上料机构7、上轴承上料机构6、上油封上料机构8和下油封上料机构9均包括固定于工作台上的第三架体201、横向位移气缸208、横向直线导轨203、横向位移板202、升降气缸205、升降板204、竖直直线导轨218和抓取装置206,横向位移气缸208和横向直线导轨203均横向固定于第三架体201上,横向位移板202固定于横向直线导轨203的滑块上,横向位移气缸208的活塞杆与横向位移板202固定相连,升降气缸205和竖直直线导轨218均固定于横向位移板202上,升降板204固定于竖直直线导轨218的滑块上,升降气缸205的活塞杆与升降板204固定相连,抓取装置206安装于升降板204上;下轴承输送机构30和下油封输送机构37均包括往复平移驱动装置105和安装于往复平移驱动装置105上的工件定位柱104,下轴承输送机构30的工件定位柱104位于第二轮毂定位工装14下方,其通过往复平移驱动装置105驱动移出第二轮毂定位工装14下方后与下轴承上料机构5的抓取装置206位置对应;下油封输送机构37的工件定位柱104位于第六轮毂定位工装18下方,其通过往复平移驱动装置105驱动移出第六轮毂定位工装18下方后与下油封上料机构9的抓取装置206位置对应;且下轴承上料机构5的抓取装置206、衬套上料机构7的抓取装置206和下油封上料机构9的抓取装置206均包括气动夹爪,上油封上料机构8的抓取装置206包括抓取柱体207,抓取柱体207的下端设置有下端直径小于上端直径的第三圆台体2071,在工作台1处轴承及衬套装配区11的长形孔33位置和检测及油封装配区12的长形孔33位置分别进行安装往复平移驱动装置105,往复平移驱动装置105包括沿长形孔33长度方向设置的平移直线导轨32、往复平移驱动气缸35和平移板34,平移直线导轨32和往复平移驱动气缸35相互平行设置,并均固定于工作台1上,平移板34固定于平移直线导轨32的滑块上,往复平移驱动气缸35活塞杆通过连接块36贯穿长形孔33后与平移板34固定相连,工件定位柱104固定于平移板34上,且轴承及衬套装配区11的长形孔33位于第二轮毂定位工装14的下方,检测及油封装配区12的长形孔33位于第六轮毂定位工装18的下方。
64.在第二轮毂定位工装14旁侧设置有与上轴承上料机构6的抓取装置206位置对应的上轴承上料台47,在第三轮毂定位工装15上前后相对应两侧分别设置有与衬套上料机构7的抓取装置206位置对应的衬套上料台51和与下轴承上料机构5的抓取装置206位置对应的下轴承上料台48,在第五轮毂定位工装17的旁侧设置有与上油封上料机构8的抓取装置206位置对应的上油封上料台50,在第六轮毂定位工装18的旁侧设置有与下油封上料机构9的抓取装置206位置对应的下油封上料台49,各上料台分别对接震动送料轨道45,震动送料轨道45与震动上料盘40的出料口对接,且震动送料轨道45的下侧面固定平振器,其结构实
现自动排序上料,使得上料效率提升,其中衬套上料台51通过支撑台69固定于工作台上,衬套上料台51上设置有衬套放置通道511,衬套放置通道511上设置有端部开口和底部开口,底部开口处设置有滑动块70,滑动块70上位于端部开口的位置处设置有阻挡块701,滑动块70的底面固定有上推气缸66,上推气缸66的活塞杆贯穿滑动块,阻挡块的上端固定有有红外感应器,红外感应器用于检测输送过来的衬套是否到位,支撑台69上固定有侧面气缸67,侧面气缸67的推移件与上推气缸66固定相连,当输送过来的衬套经衬套放置通道511进入至滑动块70上后,上推气缸66的活塞杆上的插杆插入衬套上升以举升衬套,然后侧面气缸的活塞杆伸出使推移件、上推气缸、滑动块均向工装方向移动,达到滑动块处的衬套被推离所有干涉区,以便于衬套上料机构的抓取装置进行抓取衬套,也防止出现与后面输送过来的衬套发生干涉而导致取料困难的情况发生,待衬套上料机构的抓取装置将衬套抓取后,滑动块和上推气缸同时复位。
65.较佳地,基于第二轮毂定位工装14的定位板100通过弹性复位装置38进行安装配工作台1上,因此第二轮毂定位工装14上方的顶压机构4工作,顶压机构4的顶压件43下压轮毂500在弹簧复位装置38的弹簧作用下第二轮毂定位工装14的定位板100下移,以将第二轮毂定位工装14处工件定位柱体104上的下轴承与第二轮毂定位工装14处轮毂500的中心通孔501插接固定(过盈配合固定),轮毂失去下压力后,在弹簧作用下定位板自动上升复位。
66.在本实施例中,上轴承上料机构6的抓取装置206包括抓取气缸208、固定板215、涨紧套213、涨紧柱体211和定位套209,固定板215固定于上轴承上料机构6的升降板204上,抓取气缸208和定位套209分别固定于固定板215的上侧面和下侧面,涨紧套213置于定位套209的内孔中,涨紧柱体211置于涨紧套213的内孔中,涨紧套213的顶端与固定板215固定相连,涨紧套213的下部设置有多个呈环形阵列并相互间隔设置的第一长形通孔214,涨紧柱体211下端设置有上端直径小于下端直径的第四圆台体212,且第四圆台体212上升后对涨紧套213下部撑开使涨紧套213下端部直径变大而将套于涨紧套213下端部上的上轴承得到涨紧固定后抓取,其中抓取气缸208的活塞杆伸出驱动第四圆台体212上升,其活塞杆缩回驱动第四圆台体212下降达到涨紧套211的下端复位,且复位后对上轴承进行抓取的抓取力消失,上轴承被放置于轮毂500的中心通孔501上端口位置
67.在本实施例中,抓取传送机构包括第一夹取输送装置2和第二夹取输送装置3,轮毂装配区10包括轴承及衬套装配区11和检测及油封装配区12,轴承及衬套装配区11上具有第一夹取输送装置2、第一轮毂定位工装13、第二轮毂定位工装14、第三轮毂定位工装15和第四轮毂定位工装16,检测及油封装配区12上具有第二夹取输送装置3、第八轮毂定位工装20、第五轮毂定位工装17、第六轮毂定位工装18和第七轮毂定位工装19,其中将第一夹取输送装置2和第二夹取输送装置3均实现将左侧一轮毂定位工装处的轮毂500夹取并输送至右侧一轮毂定位工装上,具体地,先利用第二夹取输送装置3将第八轮毂定位工装20、第五轮毂定位工装17、第六轮毂定位工装18和第七轮毂定位工装19上的轮毂500同步抓取,然后将第八轮毂定位工装20处的轮毂500抓取并输送至空置的第五轮毂定位工装17上,将原来位于第五轮毂定位工装17处的轮毂抓取并输送至空置第六轮毂定位工装18上,将原来第六轮毂定位工装18处的轮毂抓取并输送至空置的第七轮毂定位工装19上,然后第一夹取输送装置2将第一轮毂定位工装13、第二轮毂定位工装14、第三轮毂定位工装15和第四轮毂定位工装16上的轮毂500同步抓取,然后将第一轮毂定位工装13处的轮毂抓取并输送至空置的第
二轮毂定位工装14上,将原来位于第二轮毂定位工装14处的轮毂500抓取并输送至空置第三轮毂定位工装15上,将原来第三轮毂定位工装15处的轮毂500抓取并输送至空置的第四轮毂定位工装16上,将第四轮毂定位工装16处的轮毂抓取并输送至空置第八轮毂定位工装20上(在轮毂输送过来前第八轮毂定位工装上轮毂已被抓取输送至第五轮毂定位工装上)。
68.优选地,第一夹取输送装置2包括位于轴承及衬套装配区11前后两侧的第一顶升平移机构21和安装于第一顶升平移机构21上的四个第一夹取气缸23,四个第一夹取气缸23的活塞杆分别与第一轮毂定位工装13、第二轮毂定位工装14、第三轮毂定位工装15和第四轮毂定位工装16的位置对应,四个第一夹取气缸23的活塞杆上分别固定有第一夹取块24,两第一顶升平移机构21均包括第一顶升板条216、第一顶升气缸217、第一平移板条215、第一平移直线导轨214和第一平移驱动气缸211,第一平移驱动气缸211和第一平移直线导轨214均固定于工作台1上,工作台1上位于第一平移直线导轨214的旁侧设置有第二长形通孔219,工作台1下方设置有第一连接架213,第一连接架213贯穿第二长形通孔219与第一平移板条215固定相连,第一平移驱动气缸211的活塞杆与第一连接架213固定相连,第一平移板条215固定于第一平移直线导轨214的滑块上,第一顶升气缸217固定于第一平移板条215上,第一顶升板条216固定于第一顶升气缸217的活塞杆上,四个第一夹取气缸23分别固定于第一顶升板条216上。
69.第一夹取输送装置工作时,所有第一夹取气缸的活塞杆同步伸出使得轴承及衬套装配区中每一工装处的两相对应的第一夹取块对工装处的轮毂进行夹紧,然后第一顶升气缸的活塞杆伸出,使得第一顶升板条上升,此时将工装处的轮毂进行提升而远离工装,第一平移驱动气缸的活塞杆作伸缩动作,以驱动第一平移板条进行平移,使第一平移板条向下料机构方向平移,实现将检测及油封装配区中的前一工装处的轮毂抓取并输送至后一工装的上方,然后第一顶升气缸的活塞杆缩回,使夹取的轮毂下放后放置于后一工装上,即将第一轮毂定位工装处的轮毂抓取并输送至空置的第二轮毂定位工装上,将原来位于第二轮毂定位工装处的轮毂抓取并输送至空置第三轮毂定位工装上,将原来第三轮毂定位工装处的轮毂抓取并输送至空置的第四轮毂定位工装上,将原来第四轮毂定位工装处的轮毂抓取并输送至空置的第五轮毂定位工装上。
70.第二夹取输送装置3均包括位于检测及油封装配区12前后两侧的第二顶升平移机构31和安装于第二顶升平移机构31上的三个第二夹取气缸33,三个第二夹取气缸33的活塞杆分别与第八轮毂定位工装20、第五轮毂定位工装17、第六轮毂定位工装18的位置对应,三个第二夹取气缸33的活塞杆上分别固定有第二夹取块34,两第二顶升平移机构31均包括第二顶升板条316、第二顶升气缸317、第二平移板条315、第二平移直线导轨314和第二平移驱动气缸311,第二平移驱动气缸311和第二平移直线导轨314均固定于工作台1上,工作台1上位于第二平移直线导轨314的旁侧设置有第三长形通孔312,工作台1下方设置有第二连接架313,第二连接架313贯穿第二长形通孔312与第二平移板条315固定相连,第二平移驱动气缸311的活塞杆与第二连接架313固定相连,第二平移板条315固定于第二平移直线导轨314的滑块上,第二顶升气缸317固定于第二平移板条315上,第二顶升板条316固定于第二顶升气缸317的活塞杆上,三个第二夹取气缸33分别固定于第二顶升板条316上;其中,第二夹取块34的内侧和第一夹取块24的内侧均设置有与轮毂外形匹配的第三弧形内凹面600。
71.第二夹取输送装置工作时,所有第二夹取气缸的活塞杆同步伸出使得检测及油封
装配区中每一工装处的两相对应的第二夹取块对工装处的轮毂进行夹紧,然后第二顶升气缸的活塞杆伸出,使得第二顶升板条上升,此时将工装处的轮毂进行提升而远离工装,第二平移驱动气缸的活塞杆作伸缩动作,以驱动第二平移板条进行平移,使第二平移板条向下料机构方向平移,实现将检测及油封装配区中的前一工装处的轮毂抓取并输送至后一工装的上方,然后第二顶升气缸的活塞杆缩回,使夹取的轮毂下放后放置于后一工装上,即将第八轮毂定位工装处的轮毂抓取并输送至空置的第五轮毂定位工装上,将原来位于第五轮毂定位工装处的轮毂抓取并输送至空置第六轮毂定位工装上,将原来第六轮毂定位工装处的轮毂抓取并输送至空置的第七轮毂定位工装上。
72.本发明轮毂内置零件自动化安装设备的工作原理,基于上述第一夹取输送装置和第二夹取输送装置在各工装处进行轮毂的夹取输送动作,来实现将第一轮毂定位工装处未装配的轮毂持续夹取输送并依次进行下轴承、上轴承及衬套的装配、对已装配下轴承、上轴承及衬套的轮毂检测、上油封及下油封的装配,且装配完成后的轮毂被夹取输送至第七轮毂定位工装上,最后通过下料机构的轮毂抓取装置进行抓取装配完成后的轮毂进行移位下料,并放置下料台上,其中第一轮毂定位工装处轮毂可以是人工放置,为了提升效率及自动化生产效果,亦可在第一轮毂定位工装13处进行设置皮带输送机构520进行轮毂500的输送,并将轮毂输送至第一轮毂定位工装13上。
73.另一种实施方法,基于上述工作原理在不需要装配下油封时间,plc控制器控制下油封停止上料,即下油封上料台的震动上料盘、检测及油封装配区12处的往复平移驱动装置105、下油封上料机构均停止工作,则不进行下油封的装配,而仅进行上油封的转配。
74.在上述中,其所有的固定可根据实际情况进行选择螺栓连接固定或焊接固定。
75.本发明不局限于上述最佳实施方式,任何人在本发明的启示下都可得出其他各种形式的产品,但不论在其形状或结构上作任何变化,凡是具有与本申请相同或相近似的技术方案,均落在本发明的保护范围之内。